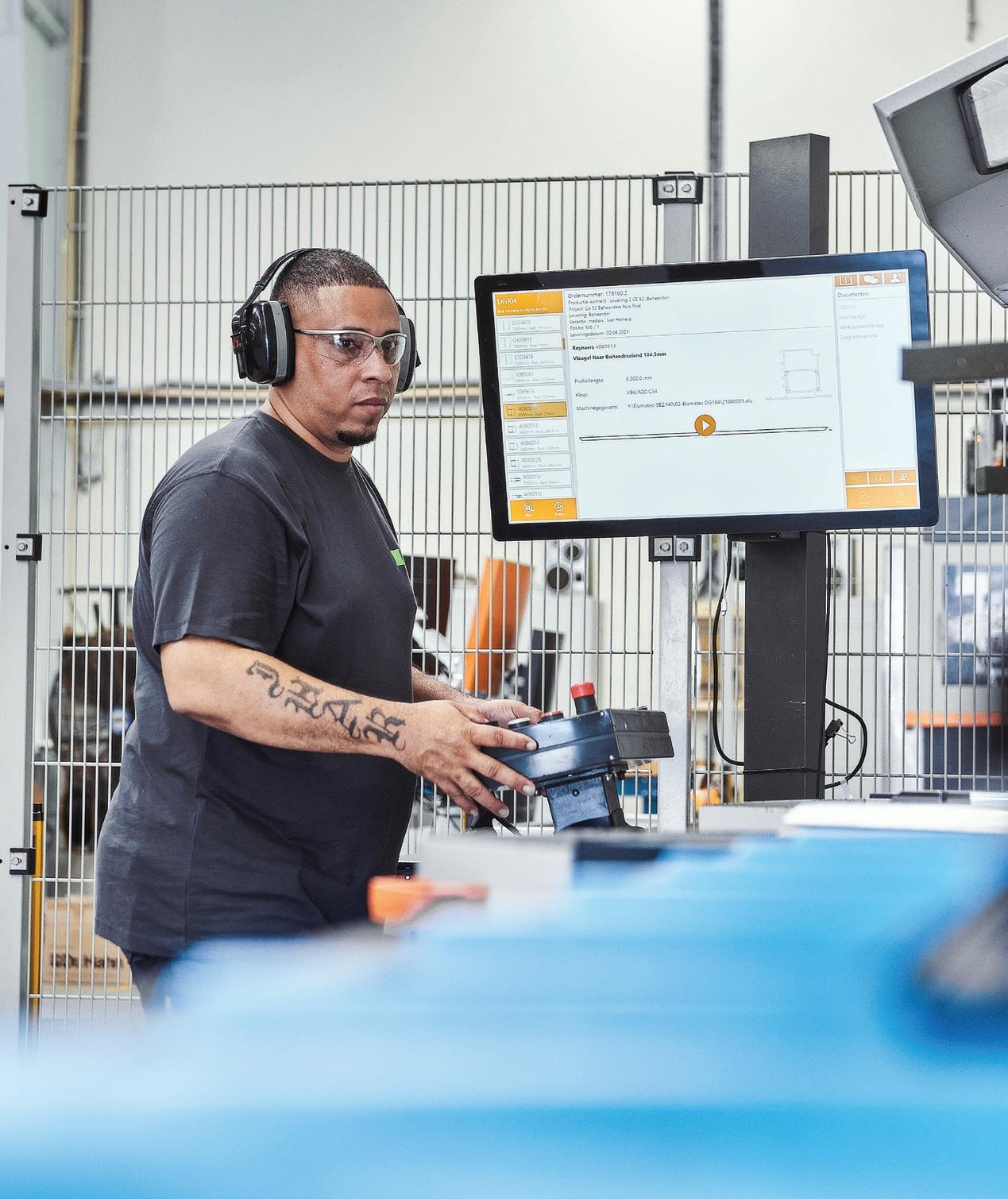
5 minute read
AUTOMATION: WHY AUTOMATION FOR MANUFACTURING WINDOWS, DOORS AND CURTAIN WALLS MATTERS
Automating your company can massively increase the productivity of tasks, processes and manufacturing lead times on the shop floor and in the office. Processes that once took a significant amount of skilled labour and time, nowadays can now rely on a standardised work process with information being available to staff at the right time and at the right moment.
Since the start of manufacturing windows and doors in Australia, the automation process has made significant steps. Just think about the introduction of the pneumatic punches, the phone, the fax, the computer, and the mobile phone.
Change is not always easy to come to terms with. Where some struggle with change, others thrive with it. The speed of technical change has rapidly gathered pace, transforming window, door and façade manufacturing beyond recognition. We are now amid the fourth industrial revolution (industry 4.0). Where some of our fellow window and door manufacturers have been able to adapt their productions lines with automated control systems, software, paperless manufacturing and CNC machines, some are still at a position where there is lots to gain.
It's important to understand the full scope of benefits that automation can bring to your company. This is especially so now that we have seen that being reliant on the international supply chain of cost-efficient window and door manufacturing is not always the best strategy. It’s worth taking stock of why automation is something to be welcomed, not feared.
1. AUTOMATION LIFTS PRODUCTIVITY
Automating your company can massively increase the productivity of tasks, processes and manufacturing lead times on the shop floor and in the office. Processes that once took a significant amount of skilled labour and time, nowadays can now rely on a standardised work process with information being available to staff at the right time and at the right moment. Just think about it. If you could save between 10%-30% of the time it took to manufacture your projects, this could also increase your productivity, making you more flexible and most importantly, manufacturing a project gets more cost efficient.
The goal is to remove any manual handling within your processes if possible. There are great ERP and Estimation software packages available that can help you to achieve this. For example, if you have multiple software packages, trying to reduce them within your business would be a great place to start. When you order products from multiple suppliers, try to avoid your staff having to adapt to different work processes each time. The fewer software packages your staff need to work with the better as this increases their efficiency, reduces software maintenance, and reduces fail cost because of constant change. Be critical about how you do things and invite your suppliers and partners over to discuss this, as they have the opportunity to share with you methods that work with other businesses.

2. AUTOMATION REDUCES COSTS
Did you know that if you improve your company processes it increase your project profit margin? When productivity increases, the cost to process a project automatically reduces. You might think, how does investing all this time and capital into new software, training and machines be financially the best choice? Let’s look at machinery for your factory, as an example. Considering that the total cost of investing in a startup package for CNC machinery equipment equals 2-3 staff members’ annual salary and equally reduces the workload of 2-3 staff members, after just one year, you have organised a massive reduction in cost to manufacture projects.
3. BE LESS RELIANT ON SKILLED LABOUR
According to the Society of Manufacturing Engineers 89% of manufacturers have reported difficulty finding skilled workers. Software can help to aid the skilled labour shortage by reducing reliance on it. In the past, manufacturers that purchased a CNC machine needed to train their staff on an engineer-level of programmer, taking weeks or even months to code the new machines with macros. This process also created a dependence on a staff member who was then hard to replace. With software though, there is no need to have an engineer working on the machine. You simply quote a job in your office software which then automatically generates all the codes for all your machines in the factory. Not only do you not need a highly trained engineer, but you also reduce fail cost because you are not depending on staff to copy that information into your machines as a standard process. In addition, it also saves approximately 30% of the time for the machine operator.
TRAIN YOUR STAFF
Most companies in Australia have an ERP system using software for quoting, ordering, and manufacturing. just installing these software products and utilising them with staff that only finished the initial training will not necessarily present you with the most efficient outcome. If you are looking to save time and therefore money, you should contact your vendor for a consultation. You will be surprised about the number of software features that you may not be currently using and about methods that you could implement to increase your productivity.
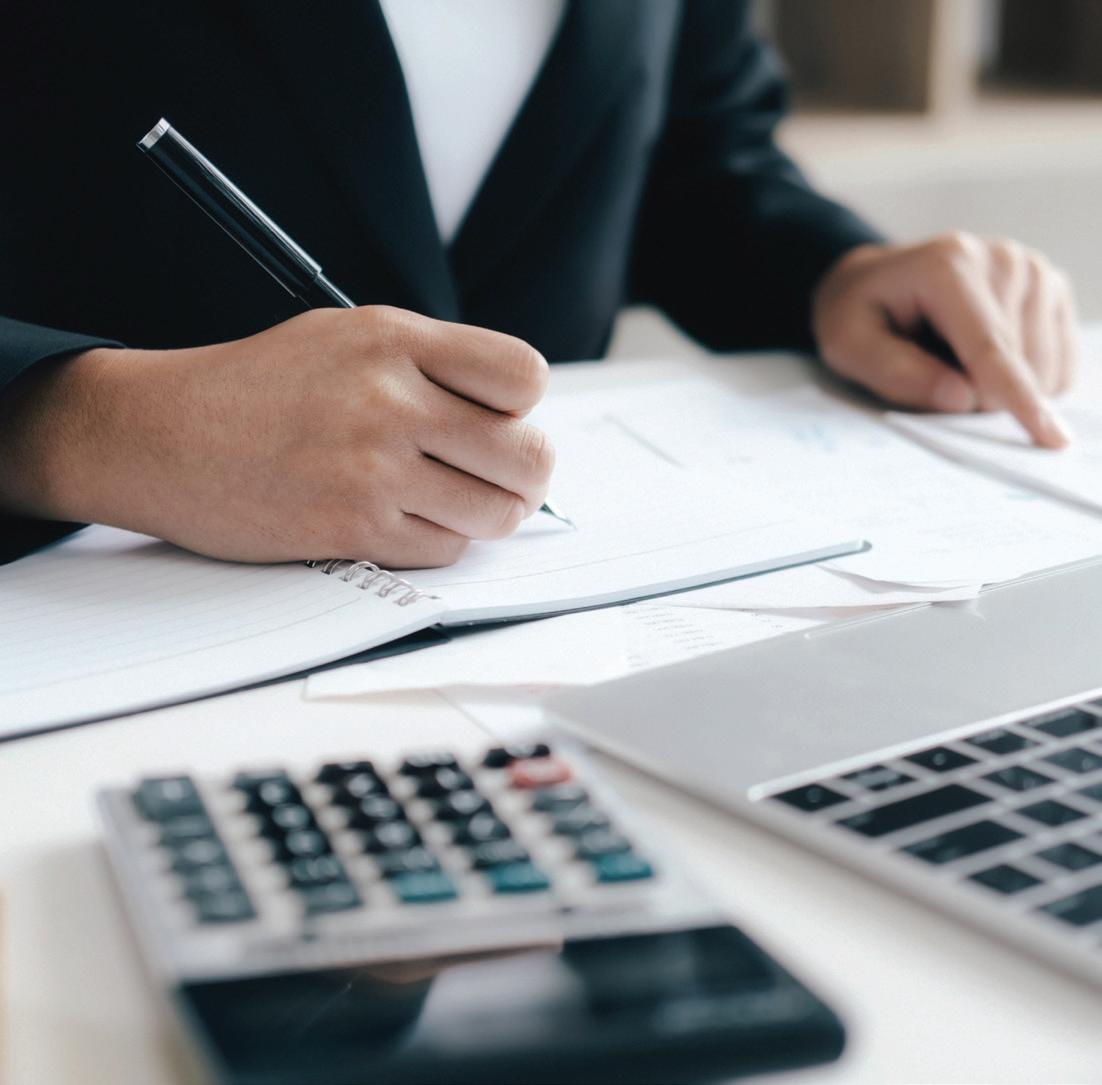