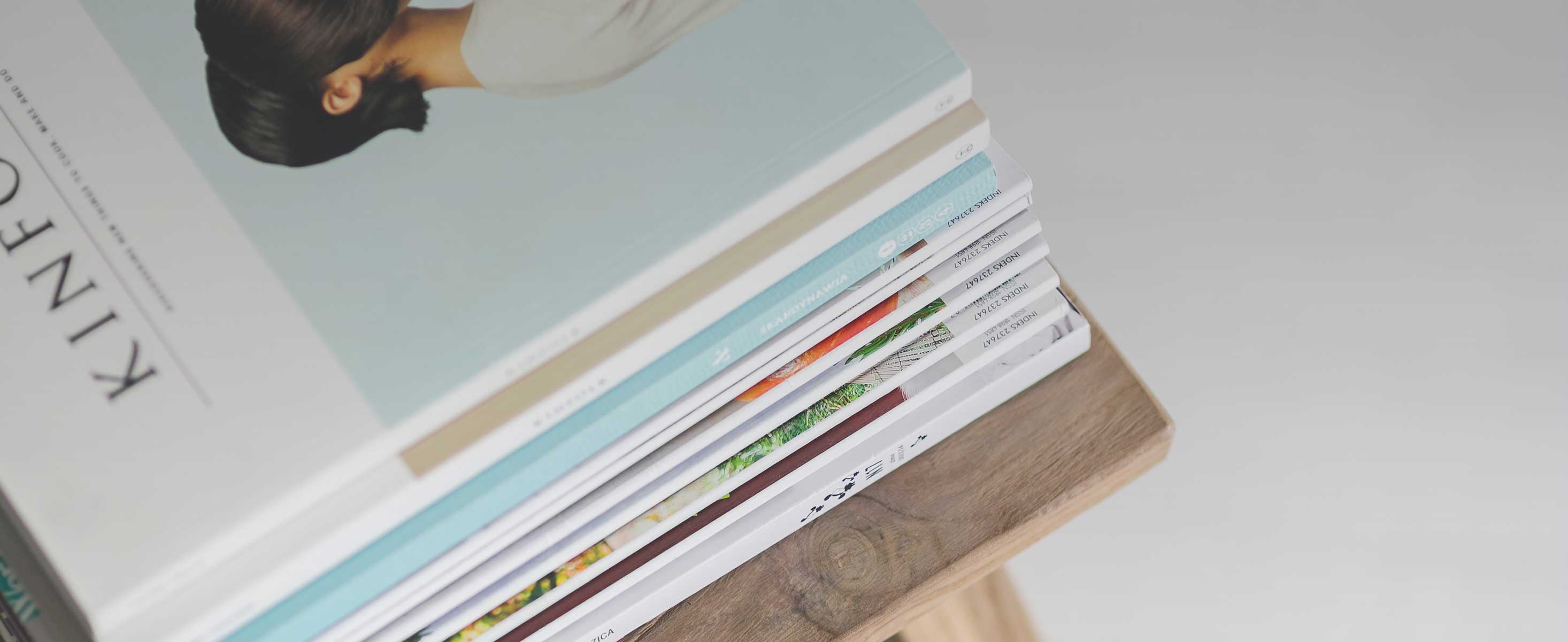
3 minute read
COMPLIANCE | Engineering Assessment of a Possible Non-Compliance Glazing Installation
POUYA ABTAHI Glass Technical Manager, Australian Glass & Window Association
AGWA is often asked what we are doing about the ‘cowboys’ in the industry. While the number of disputes and noncompliant investigations is increasing every year, members do not get the opportunity to see the work that we do to raise the standards of our industry. In what will be a new section of this magazine, we will provide snapshots of some of the content, issues and outcomes emanating from our investigations.
BACKGROUND
AGWA was informed by one of our members of a potential non-compliant balustrade installation in the auditorium/ theatre of a college.
These issues are typically triaged by the AGWA technical engineering team under the AGWA dispute resolution service, and most commonly, as in this instance, it begins with a desktop review which is often based on photographs and information supplied to us by a member or a complainant.
In the case of the balustrade in the college building, our initial review highlighted concerns around the glass thickness of the balustrade, making it non-compliant with the requirements of AS 1288 and AS/NZS 1170.1 as required for this particular application.
THE DETAILS
With the initial desktop investigation complete, we contacted the college and asked for the balustrade system’s compliance certification and engineering report to confirm our initial concerns.
As the balustrade system is located internally, wind loads were not applicable. However, imposed action loads on the balustrade system were the key focus of the assessment given the occupancy use.
The college auditorium is unusual because the lower five rows of seating can be retracted, leaving higher, usable seating that requires fall protection for the 1,655 mm drop created by the removal of the lower seating. While protection of that drop is necessary, the usage of the auditorium requires a higher protection level.
In reviewing the information provided, we learned that 12 mm thick toughened glass was used in the balustrade, which was based on the applied live load (imposed load) of C3 (0.75 kN/m). However, it should have been C5 (3.0 kN/m) as required in Table 3.3 of AS 1170.1. C3, applies to areas such as stairs, landings, external balconies, and edges of roofs, while C5 applies to places such as theatres, cinemas, grandstands, auditoriums and shopping malls.
After informing the college about our concerns, they requested an on-site inspection and expert opinion. We arranged for one of our NATA Accredited assessors to carry out a comprehensive investigation. The details are:
• The largest of the glass balustrade’s overall dimension was 1,555 mm in width and 1,200 mm high with a thickness of 12 mm.
• The handrail, which is located on top of the glass, was not part of the original design and poorly connected to the glass and adjacent wall. We considered this to be a top rail or non-load supporting handrail.
• The top rail is entirely removable in order to provide access down to the auditorium floor from the upper seating.
• The top rail was not properly connected back to the main structure.
Once the details of the site assessment were completed, with accurate dimensions of the balustrade system, AGWA undertook detailed engineering calculations and a desktop study to validate and confirm our initial assessment.
From our assessment, a compliant system would be required to have a glass thickness of approximately 25 mm, which is greater than the actual glass thickness used in this project. As previously mentioned, the whole system was therefore considered non-compliant.
A written report was provided by AGWA to the client to highlight the non-compliant installation issues and possible rectification solutions.
SUMMARY OF FINDINGS
The issues detected are summarised as follows:
1. The system does not meet the requirement of the National Construction Code because the balustrade system is rated and tested as C3 when it should be C5.
2. The entire balustrade assembly, including the top rail and removable glass panels, is highly unlikely to have been designed to be removed and replaced regularly and remain structurally adequate.
3. The top rail is more of a cap and adds little to the performance and strength of the whole system.
Ultimately, the system as designed uses a thickness of 12 mm. Our findings indicate that a compliant system requires a thickness of 25 mm.
At the time of publication, we are continuing to work with the college to provide them with a compliant outcome.
In conclusion, compliance and ensuring a level playing field is the core of our engagement in this regard and we will continue to progress this important agenda. Your ongoing assistance to raise concerns on installations like this is highly valued so we can work to protect our industry from the cowboys profiting from non-compliance and nonconformance.