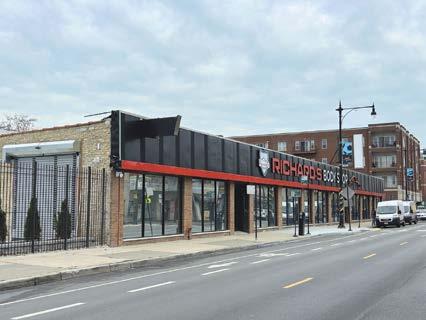

3D International 4-5
Byers Collision Center Columbus, OH
3M 6-7
Painters Collision Centers Queen Creek, AZ
AirPro Diagnostics 8-9 Key Collision Rochester, NH
AkzoNobel 10-11
Coatings Columbus Body Works Columbus, GA
asTech 12-13
22-23
KECO Body 24-25
PPG 28-29
Bob's Auto Re nishing Kahului, HI
Driven by Repairify
Axalta 14-15
Coating Systems Har vey's Collision Centers Dallas, Mesquite and Allen, TX
Blowtherm USA 16-17
Tag's Auto Inc. Clintonville, WI
Car-O-Liner 18-19
K&M Collision Hickor y, NC
Equalizer 20-21 Star Body Works Medford & Grants Pass, OR
Pro Spot 30-31
International Mike's Collision Center Bloomington, IL
SATA 32-33
Mercedes-Benz of Cutler Bay Cutler Bay, FL
Solidus 34-35
JDM Collision Thor ton, IL
Spanesi 36-37
Americas Richard's Body Shop Chicago, IL
USI of 38-39
Nor th America
Mopper t Brothers Collision
Services Group Morton, PA
Autobody News published its first Shop and Product Showcase in June 2011, the brainchild of one of our longtime writers, Ed Attanasio. He thought it could help our readers increase profits in their own shops by learning, peer to peer, why certain products and services have been successful for other shops.
The June 2024 issue is our 27th edition. A lot has changed in the industry since those first nine testimonials were published 13 years ago. As vehicles have become more technologically advanced, so too have the processes and tools needed to bring them back to pre-loss condition.
Some of the shops in this issue told us about the tools they use to research OEM procedures, perform pre- and post-scans and recalibrate cameras and sensors for what used to be relatively simple repairs. Of course, they’re also still using much of the same equipment and materials as they did in 2011 – paint, spray guns and booths, frame machines and welders – and sang the praises of the ones that work for them.
Part of what makes these testimonials special is learning about the history of the shops and people themselves. Reading through previous issues, and then editing the testimonials for this one, it’s clear one thing has never changed – how seriously collision repairers take their responsibility to perform a safe, proper repair, that also makes the customer say, “Wow, it looks like the accident never even happened.”
Enjoy the June 2024 Shop and Product Showcase. We’ll be back with the next edition in October.
“It’s the first thing the customer sees. They may not understand the structural repair of their car, but they understand color match.”
– Jeff McFadden Harvey’s Collision Centers
“We save so much time by doing calibrations ourselves. Anytime we can keep the vehicle on our premises and do this work ourselves, it greatly improves our cycle time.”
– Mike McNulty Key Collision
“I truly do believe if you’re going to buy a front-end alignment system, it absolutely makes sense to invest in ADAS calibration, because it needs to be done if it has a forward-facing camera.”
– Mike Watson Golden State Paint & Body Inc
“I really believe equipment is important. My commitment to my staff is to give them the best tools to do the best job.”
– Mike Mavec Mike’s Collision Center
“If you don’t match the look and depth, the repair is no good. If you can tell it’s been repaired, the repair is no good.”
– Tag Tagliapietra Tag’s Auto Inc.
Achieve unmatched results with less product ® and less time. Plus, 3D ACA contains no fillers, vir tually eliminating comebacks from reoccurring swirl marks.
Tr y the 3D ACA system today.
BODY SHOP SAFE
Byers Auto Group began in Columbus, OH, in 1897 and has expanded to 15 dealerships with 13 brands. The Byers family owns the franchise, including Byers Collision Center, which opened in 1985.
Over the years, Byers Collision Center has expanded to 60,000 square feet on 16 acres of land.
Autobody News asked Andrew Gallo, an automotive refinishing technician who has been with the company for 13 years, what makes the automotive business stand out.
“They still operate as a familyowned dealer and body shop, which is hard to find nowadays,” he said. “The company is very easy to relate to, as far as interactions with the family go, and they treat us very well.”
Gallo added the GM-certified collision center is new and in excellent condition.
“We have some of the best equipment out there currently,” he said. “It’s an all-around easygoing, good workplace that moves a lot of volume.”
Autobody News asked what products have helped the I-CAR Gold Class body shop find success. Gallo said they began using 3D Alpha Ceramic Alumina (ACA) polishes, compounds and spider pads from 3D International about five years ago.
“When I started as a technician, we were using a lot of the olderstyle compounds and pads from a competitor company, which, in my opinion, made a heck of a mess,” he explained. “It was very messy for the car and the cleanup process.”
Gallo said Tom Payne , 3D International’s national sales director, came to them with a demo, and he “fell in love” with the products.
“I love that the 3D ACA polishes and compounds work; it cuts very well,” he explained. “It doesn’t make a mess on the vehicle and comes off very easily.”
Gallo added that from what he has seen, no fillers are involved in the compounds and polishes.
“What you see is what you get,” he said.
Gallo said he likes the 3D International spider pads because they don’t break down quickly.
“You get quite a bit of use out of the pad itself,” he said. “But the main reason I wanted to switch and use these products is that they cut and do the job extremely well, and there is minimal cleanup with the compound.”
Gallo said the 3D ACA “doesn’t sling a lot” and “doesn’t break down and throw crumbs across the hood of the car.
“It’s a good, clean product,” he said. “You don’t need a ton of compound to do what you’re doing.”
Gallo added the 3D ACA and spider pads also save time.
“With the correct sanding procedures, the denibbing process takes minimal time to polish up the spot you denib,” he explained.
Gallo said Byers Collision Center tried many other compounds, and after a wash or two, “a lot of the sanding scratches from the denibbing would come back,” which is not the case with the 3D ACA.
“We have greatly reduced our comebacks since using 3D and our customers are happier,” Gallo said.
“So far, I have not found
Byers Collision Center Columbus, OH
614-914-6720
www.byerscollision.com
Company At A Glance...
Type: Collision Repair
Facility Employees: 25
In Business Since: 1985
Number of Locations: One
Production Space: 60,000 square feet
anything I like better than the 3D International products,” he said. “They’re what I use on my vehicles daily.”
Gallo said he has referred many people to these products because of what customers get for the price point.
“It’s unbeatable,” he added.
Gallo said Byers Collision Center has an “awesome” relationship with its 3D International rep.
“Anytime I reach out to anybody I need to speak to, I normally either get an answer or a call back in a timely fashion,” he said. “The training is good, and if you ever have any problems, Tom is normally right out there to assess anything that might be happening.”
Autobody News reached out to Payne about his experience with Byers Collision Center.
“Byers has always been and will continue to be an exceptional organization to work with,” said Payne. “The complete Byers Collision staff has been outstanding, and the paint team has been very professional!”
Payne added 3D International’s overall goal is to help auto body shops reduce comebacks and improve customer satisfaction.
“Secondly, we want shops to realize the savings by getting to a finished product with less product and less time,” he concluded.
Gallo, automotive refinishing technician at Byers Collision Center, said 3D International products “do the job extremely well” and require “minimal cleanup.”
3D International, LLC
661-250-2020
Todd Mason, VP of Marketing 3dproducts.com
Facebook: @3dproducts
Instagram: @3dcarcare
YouTube: @3DCarCare
James Huard’s impact on the automotive repair industry spans more than four decades. After getting his start at 15, he performed different roles within shops across the country, culminating in his ownership of Painters Collision Centers in Arizona. Each chapter of his career contributed to his understanding of the industry, laying the groundwork for Painters, which grew into three mega-volume body shops and a calibrationspecific facility, to become a leader in its region before being acquired in early 2024.
At the core of Painters Collision Centers’ reputation was a commitment to quality and close attention to detail under Huard’s leadership. Painters’ facilities operated under a strict regimen to ensure every vehicle underwent thorough scrutiny before leaving, complemented by a robust documentation system, where each step of the repair process was recorded and archived.
Central to Painters’ success was staying abreast of the latest advancements in software technology. In mid-2021, Huard engaged in discussions with Joel Skaar, a 3M representative specializing in collision repair, about 3M™ RepairStack™ Performance Solutions, an innovative hardware and software system designed to revolutionize inventory management, streamline blueprinting and billing processes, and provide real-time business performance analysis. Recognizing the potential of 3M™ Repairstack™ to optimize operations and drive growth, Huard embraced the partnership with 3M.
“I wanted to provide my technicians and painters with the best products available, and I believe 3M delivers just that,” Huard affirmed. By implementing 3M™ Repairstack™, Painters could equip their team with superior products while minimizing waste and maximizing efficiency. The promise of cost savings and operational enhancements made 3M™ Repairstack™ an attractive proposition.
However, Huard sought
reassurance from 3M, having encountered numerous vendors and their promises over the years.
“I’m really big into promises kept. I’ve been in this industry so long, everybody makes me a promise that they can’t fulfill.” From the beginning of the process, Skaar sought a deep understanding of how Painters operated, which gave Huard confidence in the partnership.
By the end of 2021, all three Painters locations were equipped and operational with 3M™ Repairstack™. In their approach, they designated their parts managers as the gatekeepers, centralizing control over inventory. They meticulously managed every item. This level of detail allowed them to precisely allocate resources, down to a single piece of sandpaper. The software they implemented facilitated this granular level of tracking and accountability. With this system in place, they were able to operate with unprecedented precision and efficiency, enabling them to focus on the task at hand of repairing more vehicles.
“The biggest promise kept was that they would save me money, and they did,” Huard acknowledged. By leveraging the 3M™ Repairstack™ Performance Solutions advanced inventory management capabilities and superior products, Painters achieved about a 1.5% increase in the top line sale on average, significant for any business over
Painters Collision Centers Queen Creek, AZ 480-987-7968
Company At A Glance...
Type: Collision Repair
Facility Employees: 100+
In Business Since: 2021-2024
Number of Locations: Three
time. Furthermore, 3M’s unwavering support and commitment to customer satisfaction and use of the tool further solidified the partnership.
In addition to the tangible benefits, Painters also derived value from creating a gamified approach to reporting facilitated by 3M™ Repairstack™. By integrating analytics and sales numbers into a competitive framework, Painters fostered a culture of continuous improvement and accountability among its employees. The weekly analytics/reporting email, shared among the three shop GMs, served as a motivational tool, driving sales to higher levels. If a shop wrote $100,000 worth of repairs, but only sold $200 of 3M product, it was clear this was an area of opportunity to discuss with the GM.
The “winning” GM would receive a prize or bonus.
Huard’s visionary leadership and strategic partnership with 3M helped propel Painters Collision Centers to unparalleled heights of success. By prioritizing quality, efficiency and employee satisfaction, Painters set a new standard of excellence in the automotive repair industry. As Huard aptly puts it, “I recommend [3M™ Repairstack™] to shop owners. I recommend it to corporate collision. I recommend it to everybody. If you want to be efficient, you want to have control of your products and you want happy technicians, it’s the way to go.”
A weekly analytics/reporting email generated by the Performance Analytics Dashboard, shared among the three shop GMs, serves as a motivational tool, driving sales to higher levels.
Parts managers are able to meticulously manage every item, down to individual units, allowing them to precisely allocate resources, even down to a single piece of sandpaper.
3M Automotive Aftermarket Division
877-666-2277
www.3MCollision.com
Facebook: @3MCollision
Instagram: @3MCollision
YouTube: @3MCollision
Remote Diagnostics and ADAS Calibrations by on-demand Brand Specialists • We roll up our sleeves and support your
• Coverage on 98% of all vehicles, including 2024 models
$0 down plan
Industry-leading Response Time of under 90 seconds
Evergreen Tool Warranty
Key Collision started out as a small body shop in a dealership in 1992, but by the time Chief Operating Officer John Stolz began working with the company in 2019, it had grown to six shops in New Hampshire.
Since then, the company has expanded to 11 shops in five states — with ambitions to expand nationwide. When asked how Key Collision stands out, Stolz, who previously worked in the insurance industry for 35 years, emphasized the company’s dedication to working closely with both customers and insurance companies.
“Probably our biggest advantage is that we have a unique understanding of what insurance companies want out of their repairs,” said Stolz. “We’re very customer service based, but to coordinate top quality repairs with the expectations of the insurance companies has really made a great product for our customers.”
In 2023, Stolz and Key Collision’s Director of Compliance Mike McNulty became interested in AirPro Diagnostics after seeing a product demonstration. Intrigued by what they saw, McNulty and Stolz flew to Florida to learn more at the company’s corporate office and manufacturing facilities.
According to Stolz, “In Florida, they gave us a great tour and the equipment was really impressive — but we also liked the company culture and their dedication to making sure that cars were safe for customers.”
Key Collision has since purchased a full suite of AirPro products and services, which includes AirPro-employed embedded technicians in some of their shops. From the beginning, Stolz said AirPro products stood out for their ease of use.
“At first I looked at the Auggie [AirPro’s digital FFC targeting system] and I thought, ‘Oh, we’ll never be able to use this thing.’ And then we mastered it in 10 minutes. So, although it may look intimidating, we were blown away by the ease of use,” Stolz said.
McNulty agreed the intuitive design of AirPro tools makes them extremely easy to learn.
“AirPro has been great when it comes to the pre- and postscanning of vehicles,” he said. “The interface that they use makes it very simple to navigate, so training new technicians doesn’t take a lot of time. Usually, I only have to show somebody how to do it a few times before they’re flying on their own.”
AirPro’s scanning technology has helped the company ensure insurance companies are reimbursing them for everything they do on a car.
“The great thing about AirPro is that once that vehicle is scanned, it will tell us exactly what DTCs are present in the car — as well as how long that code has been stored,” McNulty said. “So we know right off the bat if that DTC is related to the loss or if it’s prior damage. We share that information with the insurance company to justify a lot of our repairs.”
When it comes to customer care, both Stolz and McNulty agree it’s hard to compete with AirPro.
“When we initially do a prescan on that vehicle, the AirPro technician on the other line will say, ‘Hey, this vehicle is equipped with a forward-facing radar. If you do X, Y and Z, you’re going to have to do this calibration at the end of the repairs,’”explained McNulty. “So we can build that into our repair plan from the very start, and there’s no surprises at the end.”
Part of what speeds up the process is the fact AirPro’s technicians are specialists.
“All AirPro technicians specialize
in one manufacturer,” McNulty said. “So if I call somebody and I have an F-150, the person I’m speaking to on the other end is most likely a certified Ford mechanic. So he can move around very quickly, and their response time is much quicker than anything else we’ve experienced.”
Key Collision has built a strong working relationship with AirPro, in particular with Tom Deacon, national director of strategic growth, who has provided exceptional support.
“Tom Deacon has been our point of contact from day one. We have biweekly phone calls with him to make sure that any issues that we have are addressed – and any one of the managers can call him anytime if there’s a problem or question,” Stolz said.
Working with AirPro has greatly benefited Key Collision by keeping the calibration work inhouse.
“We save so much time by doing calibrations ourselves,” McNulty said. “Anytime we can keep the vehicle on our premises and do this work ourselves, it greatly improves our cycle time.”
Between the intuitive technology and customer care, Key Collision sees AirPro Diagnostics as a huge benefit to its business and has no intention of looking elsewhere for ADAS equipment.
“AirPro Diagnostics has really exceeded our expectations. We look forward to growing with them as they get involved in new vehicles and new systems. We’re their biggest proponent,” Stolz said.
Company At A Glance...
Type: Collision Repair
Facility Employees: 197
In Business Since: 1992
Number of Locations: 11
Combined Production Space: 225,000 square feet
AirPro Diagnostics tools have dramatically improved Key Collision’s cycle times by keeping calibrations in-house.
Facebook: @AirProDiag
Instagram: @airprodiag
LinkedIn: @airpro-diagnostics
YouTube: @airprodiagnostics1282
“When
Philip Wynn - Columbus Body Works
In 1918, Woodrow Wilson was president, World War I was drawing to a close, and Philip Wynn’s family established an auto body shop in downtown Columbus, GA.
Now known as Columbus Body Works, the shop has grown and changed over the years –even moving location a couple of times into bigger and more sophisticated facilities – but it has remained in family hands. With that kind of long history, you might think Wynn would take a more laid-back approach to business, perhaps resting a bit on the family laurels. But you would be wrong.
Instead, when it was Wynn’s turn to take over the reins of the business in 1992, he decided to take the shop to a new level.
“Until I joined the company, we were just a one-shop, momand-pop business. But I had a little further ambition and wanted to grow the business. So I went after some dealerships and started working with them and was able to open up a second store on my own in 1998.”
It hasn’t all been smooth sailing over the decades, but under Wynn’s leadership, Columbus Body Works went from being a “mom-and-pop” shop that brought in less than $100,000 per month to two shops bringing in close to $15 million in 2023. According to Wynn, the business currently repairs around 400 cars per month.
Wynn noted the company wouldn’t be where it is without its commitment to customer service and high-quality workmanship. And he said the team made a decision early on to use the best products they could find. When it comes to paint, that means AkzoNobel’s Sikkens product line.
“We were one of the first companies in the U.S. to start working with AkzoNobel back in 1986. Everyone was a little nervous with it coming out of Holland, but we had a friend that was using it out in Texas and we decided to give it a shot.”
According to Wynn, Sikken’s color-matching and ease of application are just a couple of the reasons he is so dedicated to the product and his employees feel the same.
“When anyone comes to apply for a job, if they find out we use Sikkens, they get excited. They’re glad to see that we’re willing to use Sikkens and not a cheaper brand. It’s a simple, high-quality product that is easy to use.”
Wynn has been continuously impressed with how uncomplicated AkzoNobel has kept the Sikkens line over the decades and how well-tested every Sikkens product is.
“Each time they’ve come out with a new product, they’ve made it easier and by the time we get it, it’s already been put through the wringer so we know it works in the field. They’re always trying to solve problems like how to get the clear to dry faster, how to get it hard, how fast you can get any kind of imperfection out.”
Wynn has also taken full advantage of AkzoNobel’s continuing education, and he credits that training with giving him the business acumen that has helped him grow the business to where it is today.
“That training has probably been one of the biggest things that’s helped me learn to run the shop like a business. I started using
Columbus Body Works Columbus, GA 706-322-0676
columbusbodyworks.com
Company At A Glance... Type: Collision Repair
Facility Employees: 60
In Business Since: 1918
Number of Locations: Two
Combined Production Space: 60,000 square feet
their 20 Groups, which taught me how to grow this business. And they had consultants that worked for Sikkens that would come in and show you how to put these management systems in place and how to run your shops with them.”
At one point, Wynn decided to try out a different paint line. But when it comes to product quality and customer care, Wynn has found other companies can’t compete with AkzoNobel and the relationships he’s built with Sikkens representatives over the years.
“It’s the shop tours. It’s the shop follow-ups. It’s having people that you know coming in and out of your business checking in on you, keeping your numbers up to date, and keeping you informed versus just letting you run up a big bill. They will pop in on us and do a can test to see how much waste we have in the back, making sure we’re not over-pouring.”
Wynn is on the cusp of opening a large new facility, the third branch of Columbus Body Works. The business has come a long way from its humble beginnings as a small shop on Columbus’ Front Avenue. But as it grows, some things won’t change for this family business, and one of those is its relationship with AkzoNobel.
“We’re 100% committed to Sikkens,” said Wynn.
AkzoNobel Coatings 800-618-1010
www.SikkensVR.com/us-en
A pre-scan can tell you if there are any codes, but asTech® insights can tell you how to repair them.
Using our data from millions of repairs and DTCs, we’ve built the industry’s first automotive intelligence platform for repair planning. asTech® insights analyzes the results of your pre-scan and automatically generates custom collision repair recommendations so you can build your repair plan in a matter of minutes.
Kendrick Paint & Body was founded in 1952 by James Kendrick, as a single-stall repair shop in Augusta, GA. The company expanded with the city, which is now home to industries ranging from health care to the military and federal government, which all bring in a lot of people — and vehicles that get into accidents.
Seventy-two years later, it has grown to nine auto body shops — five in Augusta, where its corporate headquarters are located, one each in the neighboring towns of Evans and Martinez and two more in Aiken, SC — with plans to open a 10th in 2024.
When James retired, his sons, Jimmy and Steve Sr., took the reins. Now, Steve Sr.’s son, Steve Jr., is running the show. His daughter, Ansley, graduated from college in 2022 and is now working in an operational role, learning the ins and outs of the company to one day step up and become the fourth generation — and first woman — to run it.
All Kendrick shops are I-CAR Gold Class certified, and several employees have achieved Platinum certification. The business also has 14 OEM certifications, including Tesla, BMW, Nissan/Infiniti, Ford, GM, Honda/Acura, Kia, Hyundai, Volvo and Volkswagen.
Investing in new equipment and procedures has been a priority for Kendrick as the amount of technology in all cars has skyrocketed.
David Clark, CEO of Kendrick, said asTech is a crucial partner in correctly repairing vehicles equipped with ADAS features — currently about 70% of the 950 vehicles it repairs monthly, and growing every year.
All Kendrick shops use asTech to conduct pre- and post-scans, and Kendrick’s specialty division, Blue Automotive, uses asTech devices paired with the John Bean TruPoint system to complete static and dynamic calibrations.
Clark said Kendrick has tried similar tools from other manufacturers, but asTech’s focus on building an unrivaled database of OEM and OEM-compatible scan tools sets it apart. It is now the only tool used company-wide.
“In order to provide the most
Kendrick Paint & Body Augusta, GA
706-724-4071
kendrickbodyshop.com
Type: Collision Repair
Facility Employees: 200
In Business Since: 1952
Number of Locations: Nine
Combined Production Space: 250,000 square feet
high-quality scan, asTech offers the ability to use OE scan tools,” Clark said. “It just made more sense for us to partner with asTech to make sure we were giving the highest level of quality to the customer.”
Having access to the right tool for every manufacturer means Kendrick’s technicians can scan every module in a vehicle. An aftermarket tool may not have access to all of those modules, particularly in newer models with a more secure “gateway” to data, meaning those tools may not be able to identify everything wrong with the vehicle. “That leaves you with an incomplete repair,” Clark said.
Choosing asTech for scanning and calibrations has several advantages beyond being able to control the quality of repairs.
“There’s increased efficiency, because there’s no delay on having to take a car to a dealership or wait for a sublet provider to come to one of our shops,” Clark said. “We’re seeing a one- or two-day decrease in cycle time from before.”
Time is also saved thanks to the link between asTech and Kendrick’s estimating system, CCC, which allows the asTech device to automatically drop pre- and postscan documents into CCC, meaning parts department employees and estimators no longer have to enter that information, or wait for a thirdparty vendor to email it. “All of that has been sped up with asTech,” Clark said.
asTech also provides detailed reports and invoices, so Kendrick can provide detailed documentation
to both the customer and insurance carrier.
“That’s one of the biggest things that I have liked about the asTech,” Clark said. “It really lays out everything that’s on there, and tells everything that needs to be done.”
Sometimes, asTech’s scans find codes not related to the loss, but Kendrick can also provide that information to the customer and recommend a solution.
The documentation provided by asTech also creates transparency, which builds trust between the shop, customer and insurance carrier.
“We can say, ‘Here’s all the information on what we did,’ as opposed to just taking our word for it,” Clark said.
Finally, performing scans and calibrations in-house assures Kendrick they’re done correctly.
“At the end of the day, we have a liability for whoever we use, whether it’s a sublet vendor or we do it internally,” Clark said. “There’s definitely a bigger peace of mind knowing we can control that quality.
“It’s no different than replacing a bumper on a car; we know who replaced that bumper, who painted it. Now we can understand who did the scan and who did the calibration,” he added.
Clark said asTech’s support staff has been “tremendous at every level,” providing training on its calibration tools on-site at the Blue Automotive facility.
“They are constantly checking in on us, making sure if there is something we need, they’re getting us that information,” Clark said.
About 70% of the 950 vehicles Kendrick repairs monthly have ADAS features that require preand post-scans and calibrations.
asTech® Driven by Repairify™ 888-486-1166
astech.com
Facebook: @astechdrivenbyrepairify
Instagram: @astech_official
LinkedIn: @astechdrivenbyrepairify
Why do so many shops choose Cromax® XP? Maybe it’s because they can achieve a premium finish in as few as two coats. Or that it’s easy to mix, match, and apply. It could also be having access to the most innovative digital color match tools. But we’d like to think it’s all of it.
See what sets Cromax® XP apart from the competition. axalta.us/xp
Harvey’s Collision Centers was founded in 1956 by William J. Harvey, who started the business on Cedar Springs Drive before moving to the current location on Maple Avenue in Dallas. He and the next two generations of his family kept the single-location body shop thriving, largely due to their reputation for outstanding service.
In early 2018, Harvey’s grandson and third-generation owner, Johnny Harvey, sold the business to Jeremy Lennox
Lennox had a lifetime of experience in the collision repair industry — his father founded Service King, and Lennox worked for his dad’s company for 24 years, before leaving in 2017 to strike out on his own.
Lennox said he bought Harvey’s because it had such a stellar reputation and was in a prime location, near one of the city’s major arteries.
“Mr. Harvey had a really good brand,” Lennox said. “I knew that the Harvey’s reputation in Dallas was something I could build a business out of.”
Lennox got right to work building out the business, buying a former NAPA Auto Parts store on Commerce Street in Dallas and converting it into the second Harvey’s location.
In July 2023, Jeff McFadden joined Harvey’s as an equal partner in the business and the company’s CEO, bringing decades of experience in the industry, including 34 years as a Service King teammate, 10 of those as president.
The same day McFadden joined, the company closed on a new location in Mesquite, TX, which became Harvey’s third, and then opened its fourth location, in Allen, TX, on Central Expressway, in a 21,000-square-foot former furniture store. The company has plans to open a fifth location by the end of 2024, and several more by the end of 2025.
McFadden said coming from a large MSO to a family-owned business was an exciting opportunity to do something special and build a unique brand that differentiates Harvey’s from the competition.
Harvey’s paint partnership was one of the first things McFadden
Harvey’s Collision Centers was a single-shop operation in Dallas, TX, for more than 60 years until new owners began expanding its presence in 2018. It now has four locations, and there are plans for several more.
looked at. He had been a part of converting all 350 Service King locations to Axalta in 2014, so he did not hesitate to reach back out to Axalta — with whom he’s had a lot of success in the past.
“Axalta championed the cause; I was treated the same as when I was talking about converting 350 shops,” McFadden said.
McFadden turned to English Color & Supply, a Dallas-based distributor he has worked with his entire career, to install paint booths, support Harvey’s painters in learning the Axalta system and keep all four locations stocked.
“They converted all three existing locations at the time in three weeks — the equipment, training, time in the paint booths, follow up training,” McFadden said.
“They’re just really good people,” McFadden said. “We ended up with two great partners [in Axalta and English.] English’s CEO Robert Burns is just a great guy that gets the job done with epic support.”
Harvey’s started using Axalta’s Cromax XP line, a solventborne base coat that delivers a high-quality finish in an easy-to-use system.
“It’s their best solvent product,” McFadden said. “It’s where their R&D goes for solvent, so we’re shooting the latest technology.”
McFadden said the Cromax XP line averages two coats, rather than five to seven like some other vendors’ products, which increases efficiency and reduces materials costs. It also lays down clean and has a consistently superior color match.
The painters at Harvey’s were quick to adapt to Axalta’s system.
“We went to the painters and asked if they would be OK with
switching [from the former vendor],” McFadden said. “They said they’d heard great things about Axalta or had worked with it before at other shops and liked it.”
McFadden said learning a new manufacturer’s paint system can be tricky — like getting in one automaker’s vehicle after driving another your whole life and finding different controls — but the training and support from English Color & Supply and Axalta made for a smooth transition.
“[The painters] were very satisfied with the training, as well as with the product they got at the end of the day,” McFadden said.
Customers also appreciate the color-matching quality of Axalta finishes.
“It’s the first thing the customer sees,” McFadden said. “They may not understand the structural repair of their car, but they understand color match.”
Switching to Axalta helped Harvey’s realize the true potential in profitability in its paint shop.
“You get there via technology, the best product and adjacent partnerships, along with the training they provide,” he said. “Axalta and English Color & Supply really have all the bases covered.”
Harvey’s uses Axalta’s PBE Exchange, a smartphone app, available on both Apple and Android phones, that allows online ordering while helping shops track product use and efficiency.
“[Switching to Axalta] was one of the easiest decisions that I’ve made in the nine months I’ve been here,” McFadden said. “The confidence I have in the Axalta team is really second to none.”
Harvey’s Collision Centers
Dallas, Mesquite and Allen, TX 214-526-1363
harveyscollisioncenters.com
Company At A Glance...
Type: Collision Repair
Facility Employees: 70
In Business Since: 1956
Number of Locations: Four
Combined Production Space: 65,600 square feet
Collision Centers uses Axalta’s Cromax XP line because it provides superior color-matching and requires fewer coats, increasing efficiency and reducing materials costs.
www.axalta.us
Facebook: @AxaltaNArefinish X: @axalta
Instagram: @axaltarefinish
LinkedIn: @axalta
YouTube: @axalta
•
•
•
•
•
When Don “Tag” Tagliapietra graduated from high school with experience as a mechanic, he wanted to open his own auto repair shop. However, his 1-A status meant he would likely be drafted by the military, so he enlisted in the U.S. Army. In 1961, at the age of 21, Tagliapietra was discharged from the Army and he could finally establish Tag’s Auto Inc. in his hometown of Clintonville, WI.
He may have gotten his business off the ground a few years later than intended, but Tagliapietra has more than made up for lost time 2024 is his 63rd year running his shop, and he has no plans to retire.
“I love what I do,” Tagliapietra said. “I have an unbelievable business and an impeccable reputation, and it means the world to me. Most people my age are retired but that’s the last thing I want to do.”
Tag’s Auto started out doing mechanical repairs only, but now it also offers used vehicle sales, 24hour towing and collision repair. It operates out of a 7,200-square-foot building it relocated to in 1972, and employs an office manager, mechanic and two collision repair technicians.
In 1996, Tagliapietra decided it was time to invest in a downdraft paint spray booth, so he attended the National Autobody Congress and Exposition (NACE) in Orlando, FL, to do some research.
After seeing and comparing all the popular spray booths set up and running on the show floor, Tagliapietra chose a Blowtherm Ultra Prep station and Ultra 2000TM Booth.
Both were installed that same year, and today — nearly 28 years later — Tag’s Auto has put 1,030,734 actual hours on the booth and 638,622 on the prep station, all with stellar results and minimal maintenance.
“This was probably the higherpriced one of everything I looked at, but I could see the quality of this spray booth,” Tagliapietra said.
“The Blowtherm booth is truly unbelievable quality,” Tagliapietra said, pointing out the amount of money he’s saved on maintenance over the years as proof positive of that.
Proper maintenance has kept this 1,700,000-hour Blowtherm spray booth and prep station combination running like the day it was installed at Tag’s Auto Inc. in Clintonville, WI.
“That spray booth is used every day; I don’t know what I would do without it,” he said. “And it never breaks.”
For Tagliapietra, the biggest initial draw was the fact the booth’s intake and exhaust fans are directly driven off electric motors, with no belts involved.
“That is a huge advantage, for not having to do repairs,” Tagliapietra said. “Both pieces of equipment have their original 7.5-horsepower electric motors.”
Tag’s Auto keeps its Blowtherm equipment running smoothly by changing the floor filters every month and stack filters every two months, and cleaning the blower fans and housing once a year.
“This is an incredible system,” Tagliapietra said. “It works every time we turn the switch on.”
But in the nearly three decades the Blowtherm prep station and booth have been running flawlessly in his shop, Tagliapietra said, the quality of the finishes produced is the real standout feature.
“Everything is base and clear coat, and it puts out awesome finishes that match the OEM quality,” Tagliapietra said. “It takes a quality piece of equipment to do that. If you don’t match the look and depth, the repair is no good. If you can tell it’s been repaired, the repair is no good.
“Without a good downdraft
Tag’s Auto Inc. Clintonville, WI
715-823-4192
tagsauto.net
Type: Collision and Mechanical Repair, Vehicle Sales
Facility Employees: Four In Business Since: 1961
Number of Locations: One
Production Space: 7,200 square feet
spray booth, it’s impossible to match a factory finish,” he added.
Outside of regular maintenance, the only service Tag Auto’s Blowtherm Ultra 2000 booth required was in early 2023, when it needed a replacement control module. The service technician contacted Mark Miller, vice president of sales and marketing for Blowtherm USA, to get the part.
Tagliapietra was surprised to hear the name — in 1996, Miller was the sales representative who spoke to Tagliapietra at NACE and sold him the booth and prep station.
“I liked talking to Mark Miller [at NACE] because he was extremely informative,” Tagliapietra said. “I couldn’t believe he was still with the company [after all these years.]
“He knew I was 80 years old or better and couldn’t believe I was still doing business,” he added with a laugh.
The Blowtherm Ultra 2000 has been in use at Tag’s Auto for so long, it’s now branded as the Blowtherm World line of products. But the World boasts the same craftsmanship, performance and near-limitless lifetime of use as the equipment Tagliapietra bought all those years ago.
“It’s truly quality,” Tagliapietra said. “The old saying is ‘You get what you pay for,’ and this Blowtherm spray booth is absolutely, truly what that means.”
Tag’s Auto Inc. has upheld a lifelong reputation for superior collision repair workmanship and quality finishes since 1961. Blowtherm USA & Training Center
855-463-9872 or 262-269-6265
www.blowtherm-usa.com
sales@blowtherm-usa.com
K & M Collision in Hickory, NC, is a family owned and operated business that prides itself on processes, quality and the staff who make it possible.
“We’re highly consumer and certification driven,” said Vice President of Operations K. Michael Bradshaw
Bradshaw added K & M Collision partners with more than 30 OEM certifications. The body shop adopted top-tier equipment and technology from Car-O-Liner® 15 years ago to repair various makes and models correctly.
“Car-O-Liner® has a lot of OEM approvals, so as a certified repair facility, that’s something we’re looking at when we purchase equipment,” Bradshaw explained. “It is not just a matter of the equipment being efficient or innovative or what we need to get the job done; it is also knowing the OEMs have confirmed that this equipment meets their standards and criteria for repairs.”
Bradshaw said once K & M Collision tested and implemented their first Car-O-Liner® products, their success drove the shop to introduce more equipment into their offerings and repair processes.
When Autobody News asked Bradshaw to name the Car-O-Liner® products used by the collision center, he said, “There’s not much from CarO-Liner® that we’re not touching.”
K & M Collision incorporates several BenchRack™ systems, the first product they purchased from Car-O-Liner.
“The Car-O-Liner® BenchRack™ has been a game changer for us, allowing repairs on both unibody and full-frame vehicles with precision,” said Bradshaw. “This has not only aligned our work with OEM standards, but also improved our operational efficiency.”
For aluminum repair, K & M Collision uses the Car-O-Liner® CMI™3000 II Pulse.
“The CMI™3000 II Pulse has allowed us to meet the stringent OEM requirements for aluminum welding, enhancing the quality of our structural repairs,” Bradshaw explained. “Its adoption has been pivotal in elevating our workshop’s reputation for specialized aluminum repair.”
The Car-O-Tronic® Vision2 X3 and the Car-O-Liner® PointX® II are K & M Collision’s choices for vehicle
The Car-O-Tronic® Vision2 X3 and Car-O-Tronic® on the BenchRack™ help K & M Collision technicians return a Range Rover to pre-accident manufacturer regulations.
measuring.
“Employing the Car-O-Tronic® Vision2 X3 has perfected our ability to document and correct structural deviations, ensuring every vehicle is returned to its factory specifications,” said Bradshaw. “This rigorous approach has significantly boosted customer confidence in our repairs.”
Bradshaw added K & M Collision pre-measures every vehicle they repair and the Car-O-Liner® PointX® II has helped immensely with that process.
“Every technician here uses the Car-O-Liner® PointX® II to measure the front and rear structure of a vehicle within their repair bay versus having to run the vehicle up on a frame machine to set it up and measure it,” he explained. “So, for a diagnostic measuring application, the Car-O-Liner® PointX® II has solved many problems within our facility by allowing us to measure every vehicle efficiently.”
Bradshaw said he feels all body shops should pre-measure vehicles for safety and as an additional profit center.
“It’s a matter of doing it properly with the correct tools, which Car-O-Liner ® provides,” he added.
K & M Collision also implements manufacturer-specific tools from Car-O-Liner®
“For the CTR 12000, we have the branded version with the required software for repairing Volkswagen, Audi and Porsche,” Bradshaw said.
Bradshaw said their body shop also houses the Car-O-Liner® EVO™ 1, 2, 3 Anchoring and Holding with manufacturer-specific attachments for the anchoring points.
“The EVO™ systems from Car-O-Liner® have equipped us with advanced anchoring and fixturing capabilities, crucial for adapting to new vehicle designs and repair techniques,” Bradshaw said. “This adaptability has kept us ahead in the industry, ensuring high-quality repairs across a variety of vehicles.”
Bradshaw said the service side is the next important factor contributing to their longstanding partnership.
“Anytime there has been an issue, our Car-O-Liner® distributor has been able to solve the problem or get us a replacement while a piece of equipment gets serviced,” he said.
Bradshaw said when equipment like this goes down, it can create a massive problem in the production flow.
“Having the ability to know if that happens, somebody is going to be here promptly to make sure we can get it corrected as quickly as possible has also been a big emphasis for us,” said Bradshaw. “This level of reliability is not the case with many of the equipment vendors we deal with, especially with the in-the-frame equipment business.”
Bradshaw concluded by sharing his satisfaction with the training his team has received from Car-O-Liner®
“The Car-O-Liner® comprehensive training programs have been invaluable, ensuring our technicians are not only skilled in using the equipment, but also deeply understand the repair processes,” he said. “This depth of knowledge has led to more efficient repairs and heightened customer satisfaction.”
K & M Collision Hickory, NC 828-569-1275 kandmcollision.com
Company At A Glance... Type: Collision Repair Facility Employees: 35 In Business Since: 1991 Number of Locations: One Production Space: 35,000 square feet
K & M Collision uses the Car-O-Liner CMI™3000 II Pulse, EVO™ 1, 2, 3, Car-O-Tronic ® Vision2 X3 and Car-O-Tronic® on the BenchRack™
The CMI™3000 II Pulse, Car-O-Tronic® Vision2 X3, Car-O-Tronic® on the BenchRack™ and EVO™ 1, 2, 3 have been “game changers” for the family owned and operated facility.
info@car-o-liner.com car-o-liner.com
LinkedIn: @car-o-liner-hq
When Star Body Works, a fourshop regional MSO in Southern Oregon that also has a suspension calibration shop and a towing business, decided to expand its repertoire to include auto glass services, General Manager Jake Jennings asked around for recommendations on the best way to do it.
“They all said, ‘Hands down, Equalizer,’” Jennings said.
Jennings and three other Star Body Works employees have since completed Equalizer’s oneweek, 40-hour course at its Auto Glass Academy in Round Rock, TX, taught by Global Education Director Gilbert Gutierrez. After hiring another employee who already had experience in auto glass, Star Body Works can now keep all its collision repair facilities’ glass work in house—saving money and cycle time.
Star Body Works repairs an average of 450 cars per month between its four I-CAR Gold Class locations in Medford and Grants Pass, OR. The shops hold numerous OEM certifications, including Tesla, Subaru, Honda, Acura, Nissan, GM, Ford, Volvo, Chrysler, Kia, Hyundai and Mazda, and is close to achieving Mercedes-Benz.
Jennings said the shops pull away all glass from any panels being painted, for a factory-like finish that doesn’t expose paint lines to UV rays. “That’s almost every car if we’re doing a quarter panel, lift gate or pillar,” Jennings said.
Before, Star Body Works sublet that work to a mobile glass company that visited all four shops nearly every day. Now, it has its own van, staffed by its employees, who can do all the glass work themselves.
Jennings said bringing glass work in-house has several advantages.
First, the shop can make a bit of a profit off glass work now. When it was subletting the work, insurance companies would not allow Star Body Works to charge them any more than Star paid the mobile glass tech. “If I keep that in house, now I pay a labor cost, but I can
Star Body Works
Medford and Grants Pass, OR 541-779-5621
starbodyworks.com
Company At A Glance...
Type: Collision Repair, Glass Replacement
Facility Employees: 65 In Business Since: 1948
Number of Locations: Four
Combined Production Space: 65,000 square feet
make a profit off of it,” Jennings said.
Second, the shop has more control over scheduling repairs and replacements. “The glass industry is stretched so thin with how much work is out there,” Jennings said. “Two years ago, we could get (the sublet company) in same day (to do glass work.) Now, it’s two to three days minimum.”
Jennings said that is only going to get worse, as several glass companies are leaving the collision repair industry because insurance companies are putting pressure on how much shops are allowed to charge for the work. The 30-squaremile area of Oregon where his shops are located is down to only one such company.
Third, Star Body Works can ensure calibrations are correctly performed on its customers’ cars, which is becoming increasingly important in glass work.
“People who’ve been doing (auto glass) for 20 years don’t understand the importance of recalibrations, and it’s putting lives in danger,” Jennings said. “That’s the shadow lurking behind the windshield business.”
Jennings said he reached out to Shannon Kern, education program director at Equalizer, to find out what it would take to get trained. Soon after, he and another employee went to Texas for the one-week course. Jennings, who started in the collision repair industry with a high school internship more than 20 years ago, said the course “was a lot more
than people anticipate,” but he saw students who started with no knowledge of the industry build their skills as quickly as people who already had years under their belts.
Over the five days, the students learned about laws related to glass repair and replacement and were taught—both in the classroom and in a hands-on shop—how to correctly prepare a vehicle, including pre-scanning ADAS features, and perform the work. The course was capped off by a final written test and a handson replacement observed by instructors.
When the students passed the final, they were certified by Equalizer and eligible to take the national certification test, which Jennings also passed.
Equalizer also gives students a tuition credit to purchase tools, which Jennings took full advantage of. He said Star Body Works uses the Viper and Raptor cord and wire glass removal tools, as well as Equalizer’s glass stands, knives and chip and crack repair tool.
“I like the tools and the way they work,” Jennings said. “You know they’re going to have the tool that works the best. All their tools work together.”
Jennings said he has only had to send back one tool to be repaired, which Equalizer did, under warranty, and returned in two days.
“We get really good support,” Jennings said. “I’m constantly ordering stuff from them. They know me and answer with ‘Hey Jake.’”
Bringing glass services in-house allows Star Body Works to make money, better control cycle times and ensure recalibrations are properly completed.
www.autoglassacademy.com
Facebook: @equalizertools
X: @equalizertools
Instagram: @equalizertools
YouTube: @equalizervideo
Clear, on-screen step-by-step instructions
On-screen direction walks techs through calibrations for millions of vehicles
Comprehensive pre- and post-scans of installed systems and codes
Full diagnostic capabilities reveal trouble codes and other vehicle information
Secure gateway and gap coverage
Code/pair new parts to the vehicle after installation
Follow guided processes to calibrate required systems after a collision
Golden State Paint & Body was founded in 1987 in Porterville, CA, by Dennis Watson Sr., after he borrowed $1,500 from a buddy and his dad’s toolbox. Following his vision for his company to “be the best at what we do,” he worked hard to build a reputation through high standards and word-ofmouth advertising.
Nearly four decades later, the company has achieved I-CAR Gold Class status and ASE certifications, added a second shop in Tulare, and repairs about 360 vehicles a month. It offers high-quality collision repair services, as well as 24-hour towing and glass tinting and replacement.
It’s also a “family affair,” according to Dennis’ son, Mike Watson — he and his three brothers all work for Golden State. Mike is the CFO of the Tulare location, while Dennis Jr. manages the Porterville location, Martin is a glass technician and Doug a body technician.
Mike said he graduated from high school in 1986, and when his dad started the business a year later, he joined.
“My dad decided very early on that we wanted to do repairs that were ‘invisible,’” Mike said. “When you have a customer say, ‘I can’t tell anything ever happened,’ that is a joy.”
Over the years, the team at Golden State has seen cars evolve. Air conditioning, power windows and backup cameras have gone from pricey options to standard features on even the most basic new car. Now automakers are equipping most new vehicles with ADAS features like automatic emergency braking (AEB), all guided by a slew of cameras and sensors.
“Cars were very simple when we started,” Mike said. “Now you have to calibrate. There’s more precision on newer cars, they’re more technical.”
To keep up with those advancements, Golden State has been investing in Hunter Engineering equipment.
Mike said the first product purchased was an alignment machine. Before, Golden State sublet that work to a local dealership. Then the shop purchased a tire
mounting and balancing machine, so it could also start doing that work in-house.
But the “biggest game changer,” Mike said, was purchasing Hunter’s ADASLink® and DAS 3000 ADAS static calibration tool, which uses built-in cameras and rear wheelmounted targets to position the fixture, to do that work in-house as well.
Performing some calibrations requires extra space, and a level floor with no metal objects and the right lighting, but Mike said making those adjustments and buying the Hunter ADASLink® and DAS 3000 paid for itself in six months.
“That is the No. 1 best investment I’ve ever made in collision repair equipment,” Mike said.
Any shop that replaces windshields or does alignments as part of the collision repair process needs to recalibrate the cameras and sensors that guide AEB systems every time, Mike said.
Being able to do that work in-house with Hunter’s ADASLink® and DAS 3000 saves Golden State money, as it no longer has to pay a third-party provider; saves time, as it can get the work done faster and return the vehicle to the customer sooner; and gives the team peace of mind knowing for sure it was performed correctly.
“Our customers trust us with their car from start to finish, and I want to make sure I know it was done correctly and that car is going to respond the same [as before the collision],” Mike said.
“I had an instance in the past where we took a car to
the dealership, and they said it wouldn’t calibrate because a sensor was in the wrong spot,” he said. “But we knew it was in the right spot, so we took it to a different dealership, and it calibrated. If a dealership can make a mistake, do you trust them in the future? I trust our guys, who we trained, that they’re going to do it correctly.
“You’re responsible for your subletters, so if they do it incorrectly, we’re still responsible,” Mike added.
Mike said his shop in Tulare was the “guinea pig” that got the first Hunter ADASLink® and DAS 3000 in 2021. The Porterville shop sent its recalibration work to Tulare briefly, before the company invested in a second system for that location.
“Both shops also do glass, and we calibrate in-house after each replacement,” Mike said. “That keeps the profit in-house, and we have control to make sure that it’s done correctly.”
Mike said Hunter offers training on all of its equipment, both on-site in shops and in its own training facility.
“The No. 1 thing with Hunter is the service,” Mike said. “Any issues at all, I can call, and they will help me figure it out. It’s been an amazing relationship.
“I truly do believe if you’re going to buy a front-end alignment system, it absolutely makes sense to invest in ADAS calibration, because it needs to be done if it has a forward-facing camera,” Mike added.
Golden State Paint & Body Inc.
Tulare and Porterville, CA 559-687-3222
gspbinc.com
Company At A Glance...
Type: Collision Repair
Facility Employees: 72
In Business Since: 1987
Number of Locations: Two
Combined Production Space: 80,000 square feet
Mike Watson, CFO of Golden State Paint & Body’s Tulare location, called purchasing Hunter Engineering’s ADASLink® and DAS 3000 ADAS static calibration tool the “biggest game changer.”
The shop’s first purchase from Hunter Engineering was an alignment machine.
Hunter Engineering Co. 314-731-0000
www.hunter.com
contact.hunter@hunter.com
Facebook: @hunterengineeringcompany
Instagram: @hunterengineering
LinkedIn: @hunter-engineering
YouTube: @HunterEngCo
Michael Giarrizzo has decades of experience under his belt. He’s a third-generation automotive repair professional, having followed in the footsteps of his dad and grandfather. Now president and CEO of DCR Systems, headquartered in a 35,000-square-foot facility in Mentor, OH, he oversees a network of collision repair centers that stretch from the Midwest to the East Coast.
His family’s roots trace to a humbler setting: his grandfather’s two-bay mechanic shop, founded in 1946. During the 1960s, his father, Michael, opened a 5,000-squarefoot mechanic and collision repair shop, where a young Giarrizzo performed odd jobs while learning to buff and prep.
After graduating from St. Bonaventure University in 1984 with a degree in business marketing, he joined the family business. Over the years, the company experienced a growth spurt. They opened three new locations and changed the name from Johnny’s Service Inc. to JSI Collision Specialist. “My dad’s role was to open new locations and I took over operations for the company,” recalled Giarrizzo.
In 1999, during an early wave of consolidations, the business was acquired by Sterling Autobody “We were the first organization to be acquired as a market. Most of the others were single store acquisitions,” said Giarrizzo. He was hired as the Ohio regional director and appointed COO in 2001. He left Sterling in 2004. Following a brief stint as a lead consultant for Sherwin Williams, Giarrizzo opened DCR Systems in 2005. The company now has seven locations, four in Ohio and one each in New York, Massachusetts and North Carolina. DCR holds 16 OEM certifications companywide, but which vary from shop to shop.
From its inception, DCR has had a unique business model. Essentially it provides a seamless turnkey-repair experience that ensures a dealership receives a safe and proper repair based on time-tested standard
DCR Systems Mentor, OH 888-327-9902
www.dcrsystems.com
Company At A Glance...
Type: Collision Repair
Facility Employees: 100 In Business Since: 2005
Number of Locations: Seven Combined Production Space: 104,000 square feet
operating procedures.
Each location has a strategic relationship with a local auto dealership either through a managed or a licensed model. “We are a pure independent, but through our manufacturer certifications we partner with dealers,” said Giarrizzo. “We take pride in being a certified repair center. We use only original parts and manufacturer-specific calibration software.”
Giarrizzo also takes pride in Collision Clarity, an in-house quality-control software, which documents every step of every repair. “It provides a complete pictorial storyboard of each claim, the damage, what it’ll take to fix properly and validates the process with photos that show the repairs were performed correctly.”
DCR’s patented lean production system — comprised of best practices — helps streamline repair processes, reduce waste and results in increased productivity and higher quality repairs. Which, said Giarrizzo, is what makes the KECO Glue Pull Repair System a good fit.
“We’re so excited about KECO Glue Pull. Using the technology of Glue Pull allows us to repair panels more precisely and efficiently without rework or compromising the integrity of the metal, versus a more invasive traditional repair.
“Instead of welding on a tab, pulling out the metal, cutting off the tab, grinding off the paint and
coating with body filler, which is porous — almost guaranteeing a corrosion situation down the road — we are able to avoid all that with Glue Pull.”
Giarrizzo also noted Glue Pull does not affect the factory e-coat and can be used on both aluminum and steel panels. Additionally, he pointed out a technician can use Glue Pull to significantly reduce the size of the damaged area, thereby reducing the need to blend into an adjacent panel, resulting in a topnotch repair.
While acknowledging there was a transition period as technicians adapted to Glue Pull, Giarrizzo said entry-level support staff were quick to “really embrace the cutting-edge technology” — which he points out to students at a local trade school, where DCR provides input and guidance for a collision repair training program.
A believer in a learning culture, Giarrizzo helped integrate Glue Pull into the school’s curriculum. “When I address these students, I speak to them about having gluepulling skills. This is the technology of the future. We already have a technician shortage, so we need to create our own workforce. If these students apply to work at a shop and have glue-pulling skills, think about how attractive that will be to the owner. That’s why the KECO Glue Pull skill sets are so important.”
KECO Body Repair Products 888-532-6822
Company Contact: Scott Stayton www.kecotabs.com
Facebook: @KECOBodyRepairProducts
X: @kecotabs
Instagram: @kecodentrepair
LinkedIn: @keco-body-repair-products
YouTube: @KECOBodyRepairProducts
Brandon Miller may be a new business owner, but he isn’t new to ADAS calibration. Miller, who opened his own mobile ADAS calibration business in 2023 in his hometown of Collinsville, IL, spent years as a technician and location manager, doing ADAS calibrations for a local business. He then spent several years on the road working in sales, tech support and on-site training for a glass distributor.
According to Miller, a big part of that job was training businesses on the importance of performing recalibrations.
“I traveled the country teaching people how to use the equipment and the responsibilities that they have for performing recalibrations — that calibrations are not just a revenue stream. ADAS is 100% a liability issue and it needs to be done properly, per the manufacturer’s specs.”
Those years of traveling gave him both experience as an educator and a deep knowledge of ADAS calibration equipment. But he knew he didn’t want to spend his whole life on the road, so in 2023, he opened Miller ADAS Solutions and began serving local auto body shops with a mobile ADAS calibration unit.
After years of working in the field, Miller had used just about every ADAS tool on the market. So when it came to buying his own tools he knew exactly what he wanted — and who he wanted to work with.
He had established a solid working relationship with Launch Tech USA over the years and had even helped the company design its unique 3-in-1 Radar Kit, which proved to be perfect for his mobile business.
In Miller’s experience with the ADAS market, he found most packages are designed by sales executives who have very little experience in handson recalibrations. For customers, this means they often have only two or three packages to choose from and little information on what might be missing from the lowerend package. Miller said this puts
Miller ADAS Solutions Collinsville, IL
brandon@milleradassolutions.com
Company At A Glance...
Type: Mobile ADAS & Diagnostic Service
Facility Employees: One
In Business Since: 2023
Number of Locations: One, with one mobile unit
Production Space: 2,500 square feet
pressure on customers to buy more than they need.
“That customer would end up purchasing the higher-end package just to complete radar calibrations, and within a year they realize their business only needs three or four pieces of the 40-piece package. If you’re in the collision realm, your primary ADAS needs are radar recalibrations after collision repair.”
Miller, who has a passion for R&D and design, worked with Launch Tech USA to design and field test a 3-in-1 Radar Kit which contains, in Miller’s words, “everything you need, nothing you don’t.”
Miller said for a business like his, the kit stands out from anything else available in the field in that it gives collision centers a startingoff package that includes all the standard implements they will use every day, consolidated into two carrying cases.
“The 3-in-1 Radar Kit is pretty much one of the only ones in the industry that can implement all radar recalibrations by just using one stand. With any other product, you have to have multiple stands — one for just your Hondas, just your Toyotas, and then another one for your Volkswagen blind spots — your Doppler radars. This puts it all in one, which is a lot more convenient.”
Miller said his Launch Tech USA scan tool also features a similar level of versatility.
“For my scan tool, I use the
Launch Tech Throttle III, which is a professional-level scan tool. I like it a lot just because of the flexibility it provides. I could add a four channel oscilloscope, TPMS programmer or battery tester to the scan tool with the appropriate accessories. The SmartLink C is a very capable J-Box for module programming as well.”
But Miller said one of his favorite aspects of using Launch Tech USA’s tools is the seamless reporting.
“When it comes to reporting, Launch Tech USA makes it very easy. I utilize the Google Cloud for my business, so all the reports for my different customers are all shared in different folders and I can just literally pull up Google Drive, drag and drop, put it right in my invoice, and I’m done. That’s my favorite part.”
Miller, who operates one unit out of a small rented space in addition to his mobile unit, is still very much in the process of building his business. But he’s happy to be off the road, putting down roots as a local businessperson and serving his community by performing an essential service.
“It was something that I was really looking to do for a long time. My father really pushed me to start thinking more about owning my own business instead of teaching. And when he passed about two years ago, that was definitely the kick in the butt that I needed to get out there and make it happen.”
Miller said Launch Tech USA offers great versatility for his mobile business.
Miller ADAS Solutions serves local auto body shops in Collinsville, IL.
www.launchtechusa.com
Facebook: @launchtechusa
Instagram: @_launchtechusa
LinkedIn: @launch-tech-usa
YouTube: @LaunchTechUSA
Bob’s Auto Refinishing is a wellrespected, long-established familyowned and operated collision repair shop, located at 314 Ho’ohana St. in Kahului, HI. It has been in business since 2007 and offers top-of-theline painting and collision repair as well as world-class, responsive customer service.
The team includes highlyskilled technicians who are unibody and frame repair experts. The shop specializes in both, making it the goto collision repair shop in the area. It features hydraulic machine work, state-of-the-art equipment, bumper and fender repair, and much more. Insurance work is accepted. Impeccable honesty and reliability are guaranteed on every job.
Vehicle painting is considered an art form by the team, and a specialty of the shop. Whether a customer’s vehicle needs dents repaired, or dings and scratches repaired and painted, the shop takes excellent care of them. Top-quality paintless dent removal, full body paint jobs and paint touch-ups are offered.
The shop recently converted from a competitor solvent to the PPG Deltron® NXT™ paint system. Since then, results have been a significant game changer for the shop. The shop reported to PPG’s staff their team was “absolutely blown away” by switching to PPG’s digital color-matching tools and using PPG’s DIGIMATCH™ Spectro and VISUALIZID™ 3D visualization software.
The software identifies the best color match quickly and easily, a big reason why many believe it to be the leader in the collision repair industry. The shop also reported to PPG’s staff that employees absolutely love the quality and color match of the Deltron® NXT™ base coat.
Jacob Tiu and his sister, Brittany, are in the process of taking over Bob’s Auto Refinishing from their father, Robert. Robert, the current owner and manager, has been in the collision repair business for 25 years, 17 of them as owner of Bob’s.
“The quality of the paint is amazing,” Tiu said. “The Deltron® NXT™ colors are much more vibrant than
any other solvent-based paint line I have ever used.”
Tiu said he was happy to increase the shop’s production speed making the change. “Since switching over to PPG, I would say we average an additional five to six more cars a week.”
Tiu called PPG’s products user-friendly, and said that has also increased productivity at the shop since switching from a competitor brand. “The PPG Deltron® NXT™ line is very user-friendly, and it lays down really well in terms of coverage and flatness. Some paint codes took us four to five coats to get coverage, but we are now able to do it in two coats with the new system.”
Tiu also praised the blendability of the Deltron® NXT™ line, which he said is easier to blend than competitors’ products. “Not only is the Deltron® NXT™ line great with coverage, but by using the right mix ratio and reducers, the system is very easy to blend without having any mottling.”
PPG’s Deltron® NXT™ refinish system is engineered explicitly for collision centers, prioritizing supreme color accuracy and workflow efficiency. This next-generation system is tailored to meet the challenges posed by the continuous evolution of sophisticated OEM finishes. By integrating the latest advancements in toner pigments, state-of-the-art liquid pearls, and the dynamic hues afforded by XIRALLIC® and COLORSTREAM® effects, the Deltron® NXT™ system ushers in an
Bob’s Auto Refinishing
Kahului, HI
808-986-8001
www.bobsautorefinishing.com
Company At A Glance...
Type: Collision Repair
Facility Employees: 12
In Business Since: 2007
Number of Locations: One
Production Space:
6,000 square feet
era of unparalleled color-matching precision.
This system doesn’t just promise an exact match; it delivers, leveraging PPG’s extensive, globally recognized database that boasts more than 5 million prime and variant color formulas. Updated daily and accessible via the internet, this resource, combined with cutting-edge digital and print color matching tools, ensures finding the perfect match for any customer’s vehicle becomes a streamlined and accurate process.
As a global leader in the manufacture and supply of paints, coatings and surface solutions, PPG takes pride in creating worldclass products to support a variety of industries and end users. PPG’s commitment to innovation and quality is reflected in its comprehensive product lineup. PPG’s paints, coatings and colormatching technology — coupled with its auxiliary products and sundries — are meticulously designed to facilitate the preparation, painting and delivery of a high-quality finished product. Achieving excellence in every project, PPG’s solutions are developed with the end-user in mind, ensuring durability, aesthetics and superior performance across all applications.
For those collision centers that prefer a premium-quality, solventbased refinish system, PPG’s Deltron® NXT™ refinish system offers new levels of premium colormatching capability.
PPG 440-572-2800
ppgrefinish.com
Facebook: @PPGRefinish
X: @PPGRefinish_NA
Instagram: : @ppgrefinish
YouTube: PPGRefinish (USA/Canada)
Growing up in Joliet, IL, as one of six siblings whose parents emigrated to America from Slovenia, Mike Mavec had little interest in cars. A high school athlete, he enjoyed running track and hanging out with friends. “I was a jock and cars were the furthest thing from my mind,” he recalled.
Like many teenagers, however, he needed a summer job. As luck would have it, his track coach’s brother-in-law ran a body shop and Mavec was offered a job as a detailer. “I didn’t want to work in a body shop, but out of respect for my coach, I said I’d do it for the summer,” said Mavec. It was an eyeopening experience.
“I was blown away by the artistry of those technicians, their knowledge of how to take something apart, fix it and put it back together. I knew immediately this was very cool.”
Smitten by the work, Mavec continued to hone his skills during summer breaks and while attending Joliet Junior College. “At the time, I didn’t know what I wanted to do in the future, but I was progressing in the industry and had a knack for painting.”
A semester before graduation, Mavec decided to drop out and work full time at the body shop. “My parents hit the roof,” he said. “All of my siblings went to college. My parents saw education as the means to success.” Determined nonetheless to give it a go, he soon was promoted to head painter and by age 21 became shop foreman. Three years later, in 1994, he went into partnership with the owner at a second location in Bloomington, where he remained until 2003.
Flash forward to 2005. Mavec and his wife, Stacy, broke ground on a 10,000-square-foot facility. Mike’s Collision Center opened in early 2006. Over the years, the company has earned a reputation as a top-tier repair center.
The family-owned business churns out more than 100 vehicles monthly. The shop holds
in 2006, the
certifications from Acura, Honda, Rivian, Subaru and Tesla, and has earned I-CAR Gold Class certification.
Mavec believes his commitment to continuing education is central to the company’s success and has invested heavily in technician training. The six body men he employs are all I-CAR Platinum certified as well as I-CAR welding certified in all levels.
“Not every shop makes this investment — it’s very expensive,” said Mavec. “A lot of shops have one person who’s weld certified. I look at it differently. If a shop only has one person who’s welding certified, I have to assume there are others welding on cars who aren’t certified.
“We back every repair with our lifetime guarantee. When we return a car to a customer our goal is to [ensure] we meet OEM criteria for a complete, safe and quality repair.”
While having skilled technicians is essential, Mavec believes top-notch equipment is equally important. To give his techs a leg up, the shop relies on two Pro Spot welders: the i5 SMART Spot Welder and the SP-5 DP MIG Welder.
“The i5 is a squeeze-resistant welder. It’s the most efficient way to join two metals together,” said Mavec. “The i5 speeds the process and improves the repair quality. It gives us the capability to ensure the weld is as good as factory.”
Mike’s Collision Center Bloomington, IL
309-662-7777
mikescollisioninc.com
Company At A Glance...
Type: Collision Repair
Facility Employees: 18
In Business Since: 2006
Number of Locations: One
Production Space:
10,000 square feet
He said the i5 also eliminates human error by automatically delivering the correct weld power regardless of metal type. “All body men can weld but the quality level will differ.
“Some are very good welders; others shouldn’t be welding. With the i5, an audible sound verifies the weld was done precisely and gives us the assurance it’s a safe and proper repair.”
Given that many of today’s vehicles incorporate multiple types of metal, Mavec said having one piece of equipment that can weld aluminum, mild steel and ultra-high tensile steel is a boon to his shop.
“The SP-5 DP is dynamic. It’s a multi-head welder with three torches, an aluminum wire and two metal wires. So, on a Honda, for example, I can weld an aluminum outer panel, weld a mild steel outer pillar and MIG braze the UHSS inner structure. It allows one machine to do three levels of welding on one particular vehicle. That’s innovative and a good return on investment.
“I really believe equipment is important,” he added. “My commitment to my staff is to give them the best tools to do the best job. Being able to partner with a company like Pro Spot gives staff the best opportunity to use their skills to do the best job for the customer.”
Pro Spot’s three-torch SP-5 DP MIG Welder is capable of welding multiple types of metals on a particular vehicle. Technician Alex Crippen is shown programming the welder.
Tyler Stauffer programs and uses Pro Spot’s i5 SMART Spot Welder to achieve a high-quality, safe and proper repair. Both Stauffer and Crippen are I-CAR Platinum certified and I-CAR welding certified in all levels.
Pro Spot International
760-407-1414
prospot.com
Facebook: @prospotinternational
Instagram: @prospotwelding
X: @prospotwelding
LinkedIn: @prospot
YouTube: @prospotwelding
The amount of work caused by a wrong decision and the associated high costs of repainting the area leave no room for compromise when it comes to choosing the light quality.
In order to ensure that the correct color variant is selected during refinishing and the associated color shade can be determined, a light source that reproduces the entire color spectrum of visible light (daylight) as far as possible must be used. The specially developed SATA trueSun facilitates professional color retrieval and identification, even inside the bodyshop.
Best possible close to daylight reproduction of different color shades
Homogeneous light distribution across the entire illuminated area
Approx. 70 minutes at full light intensity
Uniform light intensity - independent from the battery's level of charge
Charging cycle time of only 50 minutes
Infinitely adjustable light intensity
www.sata.com/truesun
800-533-8016 E-mail: satajet@satausa.com www.satausa.com
On its main website, MercedesBenz summarizes its business philosophy as follows: “At Mercedes-Benz, our employees and communities are at the heart of everything we do.”
That is evident at MercedesBenz of Cutler Bay in Florida, which was named once again as the “Best of the Best” dealership for 2023 — an honor only given to the top 15% of Mercedes-Benz dealerships in its retail network.
Its body shop began in 2008 and quickly doubled in size within 10 years. Mercedes-Benz of Cutler Bay repairs 125-150 cars monthly at its 50,000-square-foot facility.
Scott Woodard, body shop director, has been with the company for 25 years and said the body shop stands out for two reasons: “It’s always about the customer and we repair it one way — the right way.”
Woodard said representing one of the leading luxury brands like Mercedes-Benz is a challenging feat. His team relies on quality tools and training to deliver an exceptional vehicle to customers every time.
“To this day, it’s still cool to see customers’ reactions when they pick up their car [after a repair],” he says. Striving for excellence, Woodard said their goal with every paint job is to replicate the manufacturer’s original finish.
An exceptional SATA spray gun is critical to a flawless and perfect application. “SATA is the best,” he said. “SATA takes ‘good’ painters and makes them ‘great’ painters.”
Woodard said the SATA spray guns are beautiful to behold and super user-friendly. His paint techs like how easy they are to work with and load. Mercedes-Benz of Cutler Bay has used SATA guns ever since they appeared in the U.S. market. Woodard discovered them through his PPG paint rep, who recommended them. SATA spray guns are the only ones he will use now because they help deliver an
Mercedes-Benz of Cutler Bay Cutler Bay, FL 305-661-9666
www.mbcutlerbay.com
Company At A Glance...
Type: Collision Repair
Facility Employees: 40
In Business Since: 1990 (Body Shop)
Number of Locations: One Production Space:
40,000 square feet
excellent application and reduce cycle time.
Cutler Bay is a community of about 45,000 people in MiamiDade County in south Florida. Despite intense competition from other body shops in the area, Mercedes-Benz Cutler Bay owns the market, attributing its “Best of the Best” success to its exceptional care of its customers and their vehicles.
SATA training through the local PPG offices supports Woodard’s four paint technicians. His techs love using the SATA guns, and having such quality equipment is one of the many standouts in working at the body shop.
One of the perks of working at Mercedes-Benz of Cutler Bay is that after reaching their second anniversary, the technicians get to keep the spray guns. To say his techs love using SATA’s spray guns would be an understatement.
Mercedes-Benz of Cutler Bay uses the SATA Jet 5500 RP and the SATAJet 5000 B RP. It’s easy to see why Woodard’s painters love the SATA spray guns. These ergonomically designed spray guns were developed with Porsche Design Studio. They are also lightweight, making it easy to maneuver and provide outstanding coverage. Painters also appreciate that the inlet pressure and painting distance are easy to adjust based on the specific paint used, climatic
conditions and their working style. Customizing the settings to the unique working style of each painter is an impressive selling point.
In addition, the SATA Jet 5500 RP spray guns are extra fast for maximum working speed and optimized high-pressure technology and low overspray. Both guns can be optimally used with waterborne paints and the 5500 can meet the highest demands on the painting result and clearly exceed the transfer rates of 65% required by the VOC directive.
Another great feature is they are easy to clean, reducing the clean-up time so a tech can finish the job or start another quickly and efficiently, maximizing productivity and workflow efficiency.
Not only do SATA guns decrease cycle time for each job, but they also create a consistent application and finish quality. Another plus? The guns last a long time — as long as 10 years or more. SATA has a strong ROI.
Having been with MercedesBenz of Cutler Bay for 25 years, Woodard sees multiple generations of family members through its doors. That loyalty is built on caring for their customers’ vehicles as if they are their own. Finding exceptional partners like SATA is crucial in maintaining their customers’ confidence levels— both now and for the next generation.
Paint technicians at MercedesBenz of Cutler Bay love the SATA spray guns because they are easy to load, use and clean. This allows them to be fast and efficient with every job, reducing cycle time.
SATA Spray Equipment
800-533-8016
www.satausa.com PO Box 46 Spring Valley, MN 55975
Facebook: @SATAUSA
Instagram: @satausainc
YouTube:@SATAUSAInc
Multifunction spot welding machine in the premium class with complete software package for worr y-free automotive repair. A fully automatic smar t welder designed to meet OEM specs allows for quick, easy welds on a wide range of steel strengths, layers, and thick nesses
This Multi-Use Table and mobile lifting car t is designed for dismantling and xing electric vehicles, as well as engines, gearboxes, drive axles, fuel tanks, suspensions and chassis components of traditional vehicles The MLT-3 rotates and adjusts to speci c needs. Options include positioning and jigging components with specialized xtures
This versatile 3-torch system can be set up with steel, silicone bronze, aluminum, or any combination. The multi-function synergic power source has full digital control, and o ers premium welding quality in MiG, Pulsed and Double -Pulsed MIG on all materials.
This multi-purpose bench is designed to handle all types of LIGHT, MEDIUM and HEAVY collision repair The most unique feature of SMART RHONE is “QUICK ANCHORING.” The vehicle can be anchored and ready to per form pulling operation in less than 15 MINUTES.
Solidus o ers a full line of prep stations, mix rooms and spray booths custom built to meet your needs in the paint shop.
John Melendez has spent his entire life in auto body shops, and he knows the auto body industry is changing fast. But if you want a template for what it means to future-proof a business, Melendez is a person to watch.
Melendez grew up around cars, working first in his dad’s body shop and then in dealerships, where he moved into management positions. His journey as a business owner, however, didn’t begin until 2005, when he bought a body shop, and renamed it JDM Collision, using his initials.
Melendez has seen ups and downs as a business owner, but the relentless pursuit of education has been a throughline of his entire career. He’s a certified GM master technician and mechanical technician, and he is chairman of I-CAR for Northwest Indiana, an organization he speaks passionately about.
When it comes to thriving in the collision repair industry, Melendez also emphasizes the importance of holding certifications — JDM Collision is a certified GM repair center and holds I-CAR Gold Class recognition. The company is on the cusp of opening a new, advanced calibration center, and as he reflected on his competitive advantage locally, this is a strong theme.
“I’m one of the very few technicians in my area that carries 100% status as a master GM tech, so I’m on the rosters of three different GM dealerships,” Melendez said. “That’s a huge advantage, considering the demographics of the area — and I’m continuing my education and certifications to the present day. Couple that with our I-CAR recognition, it just puts my business on a completely different level.”
That heart for education was what led Melendez to Solidus, which has been a transformative business partnership for JDM Collision. Melendez was representing I-CAR at a student career day when he met Julie Lombardo, head of AASP-Illinois. She invited Melendez to their annual meeting and trade show, where he met Mike Hildebrand, owner of Solidus. He was initially intrigued by
the company, but skeptical.
“I was like, all right guys, it sounds good. But as a business owner I’m apprehensive because after the sale, it’s like pulling teeth to get a company to come out when a piece of equipment breaks down,” Melendez said.
It wasn’t until Solidus invited Melendez to come to Kansas City to help judge a welding competition that Melendez began to see what sets Solidus apart. Working alongside Solidus at that competition convinced him the company wasn’t selling empty promises.
“That’s when I went, ‘My God, these are car guys!’ They’ve all been in the industry from the get-go. And how they talk to and treat people who are our future customers, how they actually could perform the workmanship and truly stay behind the product they sell, that sold me,” Melendez said.
Since then, Melendez has been all in with Solidus, purchasing, among other equipment, multiple Celette benches, the NAJA electronic measuring system and Solidus 300 amp welders approved for multiple manufacturers—and, crucially, by JDM’s 20-year-veteran welder.
Melendez is especially excited about the company’s new Solidus medium-duty spray booth, which was being installed at the time of this interview.
“It has the latest in robotic curing by Infrarr to accommodate the electronic platform, and the size means we’ll be able to take larger electric vehicles, like Rivian,” he said. “I emphasize the technology
because the average shop is not going to be able to do the less invasive repair that electric vehicles need.”
Melendez said using Solidus equipment gives his business what it needs to serve the cars of the future. “Equipping my shop with Solidus equipment means that I’m not going to be limited — so I can pursue Rivian certification, for example, and we’re going to be set up to take on those cars.”
Melendez also had much to say about the quality of customer care at Solidus. He’s been deeply impressed by employees like Jim Korous, Chris Scanga and John Pankau, who are kindred spirits in their commitment to excellence and advancing the industry.
“I can’t emphasize enough their service team. I was just floored seeing how these guys are truly 100% quality-minded. They always follow through,” Melendez said. “This is the first time I’ve been treated this way by any outside vendor that is supplying me. I just never expected this level of service and commitment. Our shop is being treated as if it’s their shop, and it’s hard to find that type of value today.”
Melendez is very busy these days, taking JDM Collision through its imminent expansion, and readying his business to take on whatever the future brings.
“I hit a home run by going with Solidus because they’re able to help equip this shop to be the most advanced in South Side Chicagoland and all of Northwest Indiana,” he said. “I couldn’t be happier to be working with them.”
JDM Collision Thornton, IL 708-877-7300
Company At A Glance...
Type: Collision Repair
Facility Employees: 16
In Business Since: 2005
Number of Locations: Two Combined Production Space: 13,000 square feet
is especially
Melendez said using Solidus and Celette equipment gives his business what it needs to serve the cars of the future.
Solidus
636-405-2800
solidususa.com
www.shopsolidususa.com
Info@solidususa.com
Facebook: @SolidusUSA
YouTube: @solidusequipmentsystems6572
Richard Zipperstein launched his venture into the automotive world as a humble mechanic, a role that soon evolved due to customer demand for a reliable place to have collision repairs done. This push led to the birth of Richard’s Body Shop in 1985, a move narrated with pride by his son, Eddie Zipperstein
Fast forward to today, transformed under Eddie’s stewardship, Richard’s Body Shop sprawls across a 50,000-squarefoot campus of multiple buildings for mechanical, body, structural and refinish. The body shop also boasts an impressive array of OEM certifications, including prestigious names like Tesla, Jaguar, Range Rover, Volvo and Rivian. A significant chunk of their work, about 85%, caters to Tesla vehicles, a testament to their expertise and market demand.
Eddie attributes the shop’s standout quality to its remarkable cleanliness, a feature so pronounced that he boldly claims, “It’s so clean you can eat off the floor.”
This commitment to excellence has seen the shop through transitions, including the retirement of Eddie’s parents and the entry of his son, Isaac, into the business. This imminent addition heralds the dawn of a third-generation legacy at the collision center, with Isaac bringing a fresh perspective through his computer science and business studies, especially in areas like social media and operational flow.
A pivotal partnership in the shop’s journey has been with Spanesi Americas, particularly highlighted by their custom paint booth project. Initially encountered at the Las Vegas SEMA trade show, Spanesi caught Eddie’s eye, marking the beginning of a fruitful collaboration. Their offerings, celebrated for being compact, clean and efficient, have significantly enhanced the shop’s operational capabilities. The collision center now houses three custom designed spray booths, tailored for the massive Rivian Amazon electric delivery vans, reflecting
Richard’s Body Shop in Chicago was founded in 1985 and has since grown to encompass 50,000 square feet between multiple buildings, each dedicated to a particular step in the repair process.
both innovation and foresight in accommodating larger vehicles.
Eddie’s engagement with Spanesi transcends more than mere transactions; it’s built on responsive and reliable support. The team always provides invaluable assistance a mere text away.
“Spanesi was able to build oversized booths in a building that had several obstacles because of its design and age. Then they made adjustments on site to get past roof joists and walls that were not square and true; you would never know looking at the finished product,” Eddie said.
When it was time for Richard’s to expand, Spanesi was right there to aid in adding additional equipment, as well as insights into the flow of production in the shop. Extending beyond mere implementation, Spanesi conducted assessments of multiple areas of Eddie’s business, culminating in a custom recommendation to optimize performance and efficiency.
Richard’s needed a better work flow, which was solved by the addition of Spanesi Multibenches in the body and refinish areas. Thanks to the Multibenches, technicians can stand when performing their jobs instead of working off the floor or constantly bending over. This improves employee efficiency and productivity for all processes. “There was a noticeable production difference right away after adding these benches,” Eddie said.
The relationship between Spanesi and Richard’s extends beyond the equipment currently in
production. “Spanesi creates custom made equipment prototypes that they then bring here for us to try out,” said Eddie. “They’re currently developing a portable spray station, almost like a spray booth.”
Eddie said the portable spray booth will come in handy for a variety of situations. “Let’s say you’re doing a core support, and you want to paint the vehicle before and not have to go back and forth to the spray booth,” he explained. “They’re meeting a need we have, and we’re excited to see if the product is a good fit for our business.”
The shop’s positive trajectory has also resonated with the community. Recent renovations have transformed a once-dilapidated building into a neighborhood gem, contributing to local pride and community engagement through events like the “Lot Jam” Block Party. Furthermore, Richard’s Body Shop has taken proactive steps in nurturing future talent through a paybased internship program for local high school students, emphasizing hands-on learning and career development in the automotive repair industry.
Eddie’s narrative is not just a story of business growth but a testament to community involvement, innovation and using the right equipment. After all, it’s his deep-seated commitment to quality and efficiency, as well as his principles, that have propelled Richard’s Body Shop into a realm of exceptional service and community trust.
Richard’s Body Shop Chicago, IL 773-588-3301
richardsbodyshop.com
Company At A Glance...
Type: Collision Repair and Mechanical
Facility Employees: 50
In Business Since: 1985
Number of Locations: One
Production Space: 50,000 square feet
Among the Spanesi equipment at Richard’s Body Shop are three custom designed spray booths, tailored for large vehicles like Rivian’s Amazon electric delivery vans.
Richard’s Body Shop counts on equipment from Spanesi Americas Inc. to improve workflow and productivity.
Spanesi Americas Inc. 224-SPANESI (224-772-6374)
www.spanesi.us
Facebook: @spanesiamericas
X: @spanesiamericas
Instagram: @spanesiamericas
LinkedIn: @spanesi-americas
YouTube: @spanesiamericas_official
Moppert Brothers Collision Services Group is a third-generation familyrun business that has been serving southeastern Pennsylvania and southern New Jersey for nearly half a century, now managed by Harry Moppert Sr. and his sons, Harry Jr. and Douglas. Their team of skilled technicians can handle everything from a small paint chip to a major collision repair.
Harry Sr. said when the company built its location in Northfield, NJ, just outside Atlantic City, they wanted the 17,000-square-foot building to be a first-class operation, like the rest of their locations.
“We really did a lot of work to make sure it was state-of-the-art in every way possible,” Harry Sr. said.
The team reviewed the spray booths already installed in their other facilities, made by five different manufacturers.
“Some had good qualities, some had bad, some worked well, some lasted longer,” Harry Sr. said. “When we looked at [the USI Italia] booth, we saw instantly the quality with which it was made and all the new features. There’s a lot of good stuff here. It was an easy decision for us to purchase those booths.”
Moppert Brothers purchased two booths and a paint mixing room from USI Italia for its Northfield location. Harry Sr. praised the features on the USI Italia booth that make it a snap to work with newer waterborne paint systems.
“The panel itself has so many features for waterborne paints with the new technology,” Harry Sr. said. “There’s a masking mode, spray mode, dry mode for waterborne, bake mode, all incorporated into running the booth and spraying a car. Other booths we had in the past didn’t have any of those features.”
The booth’s variable speed drive automatically changes the speed of the motors for different modes, ensuring the airflow is optimum for every step of the process, increasing efficiency and minimizing energy costs to run it.
It also saves money because it has features for drying, meaning Moppert Brothers did not have to
Moppert Brothers Collision Services Group
Morton, PA 610-544-4444
www.moppertbros.com
Company At A Glance...
Type: Collision Repair
Facility Employees: 47 In Business Since: 1976
Number of Locations: Three
Combined Production Space: 42,000 square feet
purchase additional equipment for that step.
“These are features I’d never seen built into a booth,” Harry Sr. said.
The shop’s two booths are connected to the paint mixing room, so everything is contained.
“It’s fantastic as well,” Harry Sr. said.
As for the finish produced by the USI Italia system, Harry Sr. is consistently impressed by that too.
“I’ll say it in one word — absolutely amazing. OK, that’s two words,” he said with a laugh.
“The finish is perfect; [the booth] duplicates exactly factory textures, so the appearance of the film looks exactly like it should,” Harry Sr. said. “I’m very pleased with it.
“You can do high production work, custom work, whatever you choose,” he added. “It has the versatility to do whatever you’re looking to do.”
Harry Sr. said the Northfield location was built with MercedesBenz clients in mind. Moppert Brothers has Mercedes-Benz and Tesla certifications at its other locations, and is working on completing both, as well as its BMW certification, at the Northfield location. It also holds a Honda and Acura certification.
“We do have an upper end customer base so to speak, and the vehicles to go with that, but our intention is to be able to paint higher end cars as well as regular cars,” he said.
Moppert Brothers worked with
Centerline Collision Equipment, a USI Italia distributor.
“They did a fantastic job with the presentation and working with us to lay it out at the shop,” Harry Sr. said. “They were the best vendor we’ve ever used for purchasing a spray booth.”
Centerline also provided the training for Moppert Brothers’ painters, showing them how to operate the booth to produce the best results.
“We had two painters, and they argued over who was going to get to paint the next car in the booth,” Harry Sr. said. “The painters love it.”
Moppert Brothers was so pleased with its USI Italia system, it purchased a booth for its original shop. Centerline was able to custom build the cabin to fit in the location of the shop’s previous booth, allowing it to fit “like a glove” around existing columns and poles.
“We just recently completed installation, and it’s a night and day difference over the booths that were in there before,” Harry Sr. said.
Moppert Brothers is also planning to add a second USI Italia booth to one of its locations, and is building a 7,000-square-foot addition at yet another location so it can install a USI Italia booth there as well. In the end, it will have a total of five USI Italia booths at three locations.
“In the past two weeks, we did 52 cars in one [USI Italia] booth,” Harry Sr. said. “It was an excellent choice.”
The Northfield location’s 17,000-square-foot building houses a first-class operation. USI of North America 201-405-7760
Company Contact: Stefano Moretto s.moretto@usius.com www.usius.com
Facebook: @USI-of-North-America
Instagram: @usiitalia