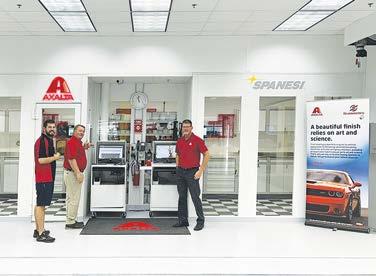
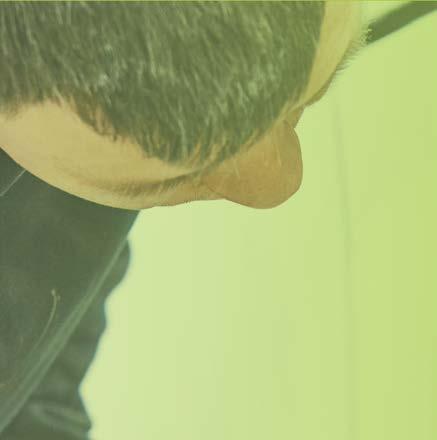
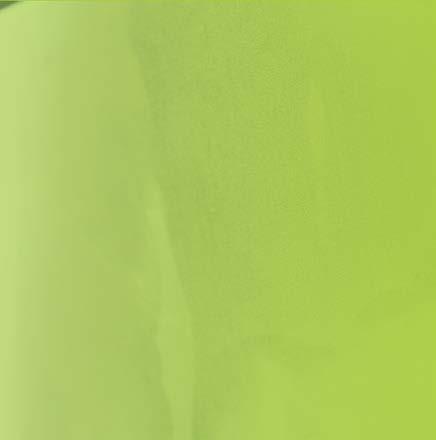
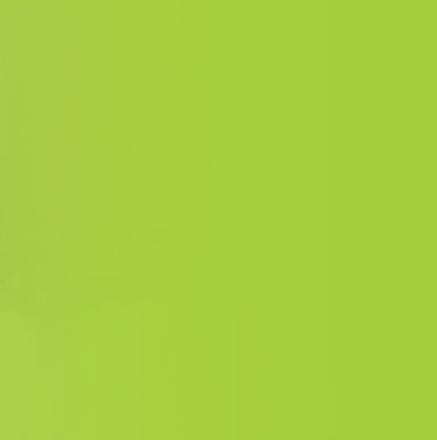

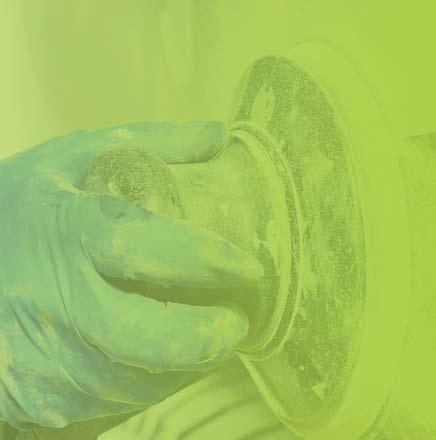
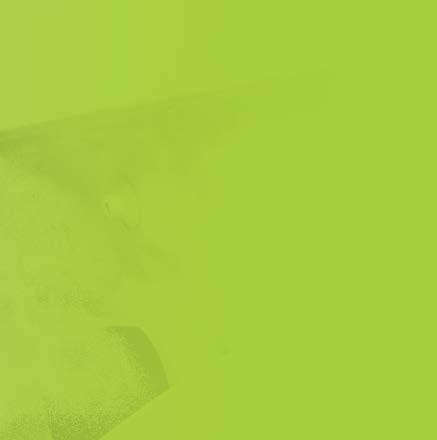
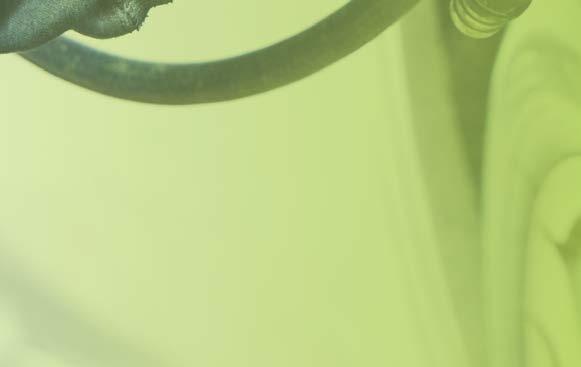
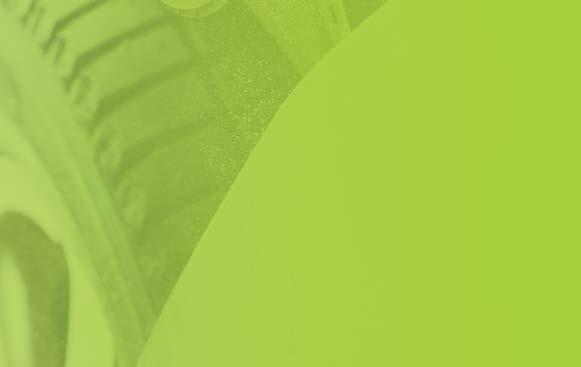
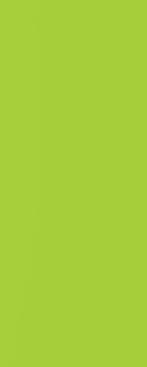
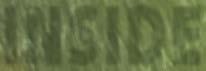
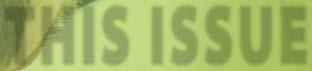
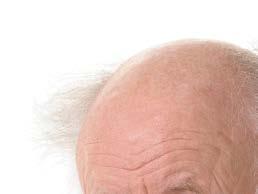
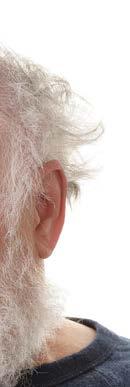


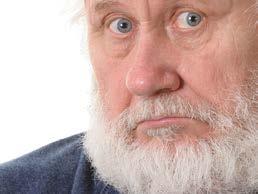
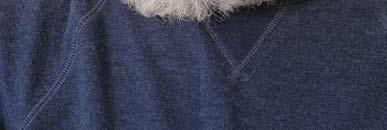
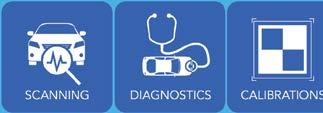
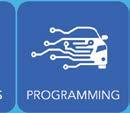
Since opening its doors 47 years ago, Moppert Brothers Collision Services Group has focused on providing quality repairs by friendly staff and delivering vehicles on time to customers so there are no surprises. The third-generation family business has locations serving southeastern Pennsylvania and southern New Jersey.
Harry Moppert Sr. and his sons, Harry Jr. and Douglas, have managed the company together since 2012.
As an I-CAR Gold Class Shop, the Moppert Brothers team understands the importance of training technicians and having inhouse experts complete safe and proper repairs.
Over the years, the company has obtained OEM certifications for several brands, including Mercedes-Benz Elite Certified, BMW, Tesla, FCA, Ford, GM, Honda-Acura, Hyundai, Kia, Nissan and Subaru.
“OEM certifications enable us to obtain the right information to repair the cars properly,” said Harry Sr. “The industry and consumers recognize that a shop that has certifications is going to do the job right and the motoring public are the ones that benefit from that.”
He said the business has always been on the leading edge of the latest equipment and technology in the collision industry.
An important part of that is the company’s reliance on AirPro Diagnostics’ services. Harry Sr. has known Michael Quinn, chief global development officer at AirPro Diagnostics, for many years, and was impressed with the company’s scanning, diagnostics and ADAS calibration solutions. As a result, the company has been using their services for a long time.
Moppert Brothers’ technicians can connect an AirPro device to a vehicle with OEM-licensed software and multi-brand diagnostic applications that are resident. Then, a remote brand specialist technician performs a full scan and thorough diagnostics. The findings are recorded and stored on ORION, a cloud-based diagnostic management platform, and a complete report is available on the user portal and through email.
“It’s a convenient and simple process,” said Harry Sr. “We have been able to cut out a lot of wasted time scheduling an appointment with third-party vendors to come in or setting up an appointment with an outside vendor that tells us it will be ready tomorrow and they don’t look at it for three days.”
Instead, he said technicians can connect on the spot when they are ready and dial in to AirPro to do the job. AirPro services 40 automotive brands and offers a pledge to work on a vehicle within 10 minutes of requesting service.
Moppert Brothers has found the price is reasonable for the services offered and the company updates their equipment when appropriate.
“The equipment works well and has been accurate, reliable and easy to use,” Harry Sr. said. “The AirPro techs are very knowledgeable and helpful and you can speak to them anytime.”
Harry Sr. said his technicians have found the AirPro Diagnostics training very helpful, whether it is in person, over the phone or through Zoom.
“We’ve made the right choice for the company to choose AirPro as a partner,” he said. “They do everything that we can’t do inhouse and we’ve had a lot of success with them.”
When AirPro introduces additional services to the industry, such as ADAS calibrations equipment and services, Moppert Brothers has reviewed how the offerings will best support their business.
“We are currently evaluating
the Auggie since it works so well for so many vehicle applications,” said Harry Sr.
The Auggie is AirPro Diagnostics’ patented forwardfacing camera (FFC) device, designed to serve the automotive service sectors with quick, mobile and safe recalibrations. It is a wireless, compact solution that saves time and increases efficiency, rendering the ADAS targets and lighting conditions in a theater-like environment to precisely perform FFC calibrations.
Excellent customer service is a top priority at Moppert Brothers and AirPro products have helped the business deliver cars on time. Moppert said this has earned them a reputation for meeting customers’ needs.
The business also supports the community in which they live and work. “We’re not a big conglomerate; we’re a familyowned business that gives back to the community,” said Harry Sr.
This includes participation in the National Auto Body Council (NABC) Recycled Rides vehicle gifting program, sponsoring Little League baseball teams and participating in local fundraisers and organizations. They also support trade schools and industry training for employees and encourage staff to be active in local organizations like Rotary Clubs, Kiwanis, the Chamber of Commerce and local church groups.
“From sponsorships to fundraisers, we get involved,” said Moppert. “We pride ourselves on being a good neighbor and the community recognizes it.”
Morton, PA
610-544-4444
www.moppertbros.com
Company At A Glance...
Type: Collision Repair
Facility Employees: 47
In Business Since: 1976
Number of Locations: Three
Combined Production Space: 42,000 square feet
Excellent customer service is a top priority at Moppert Brothers and AirPro products have helped the business deliver cars on time.
AirPro Diagnostics
904-717-1711
airprodiagnostics.com
Facebook: @AirProDiag
Twitter: @AirProDiagnost1
Instagram: @airprodiag
LinkedIn: @airpro-diagnostics
YouTube: @airprodiagnostics1282
“I’ve
incredible. The gloss and shine
clear
Marvin Dawson Fixed Operations Director Campbell Ford
When Marvin Dawson first took on the role of fixed operations director at Campbell Ford in Niles, MI, three years ago, he knew that getting the collision shop on its feet was going to take some work. He was excited, though, to be moving into a second-generation family-owned dealership.
The majority of Dawson’s career has taken place in familyowned operations, but after his previous workplace was sold to a large company, Dawson got a taste of a corporate-run business.
“The people that put the blood, sweat and tears into the business were just not appreciated anymore,” said Dawson. “They’re a number on a payroll list. That’s not me. That’s not who I am. So I was glad to have the opportunity to come up and work with Doug Campbell.”
With no trained estimator at Campbell Ford Collision Shop, and only one painter and one body man, Dawson knew he had a massive challenge cut out for him. But he also knew the ownership was all in.
“You could see that that they wanted to make things happen,” said Dawson. “They wanted to make it work, and they’d put their money in those directions. So I knew if I put the effort in to turn the culture around and put the business back together, we’d have something.”
Soon after arriving, Dawson made the decision to partner with AkzoNobel Coatings, after a trusted vendor recommended the company. He quickly found the AkzoNobel team was as committed as he was to making the shop a success.
“So many people have told me stories about the collision industry where, you know, they’re courted by a company, then once they sign the contract, it’s just crickets,” said Dawson. “But with AkzoNobel, the relationship flourished more after I signed the deal than before I signed. They review KPIs for me religiously and look for ways for me to improve my business. I’ve not had that in 30-some years in
the business.”
In fact, Dawson found AkzoNobel embodied the kind of culture he was striving to build at Campbell Ford.
“They’re constantly looking at ways to help me improve. Ryan Kerr is my local rep. I think he lives about three hours away from me, and if I had a problem, he’d be here. I feel like I’ve created a relationship with them that’s almost like a family feel where I know they’re watching out for me.”
The AkzoNobel products themselves are just as easy to work with, according to Dawson, who went through AkzoNobel’s training program when Campbell Ford made the switch to their products.
“I’ve not seen a better color match in the industry,” he said. “The ease of application is incredible— the product is forgiving and easy to repair on the fly. The gloss and the shine of the clear products is showstopping.”
While transitioning to a new product can be difficult, Dawson rated AkzoNobel’s training as second-to-none, and said his employees are thrilled with the results that they get when working with the products.
“They’re prideful on it. We like the product that we put out there. They’re very happy with the amount of time it takes to color match, to blend, to clear. It is a time-saving product.”
Three years since Dawson’s arrival, things have changed significantly at Campbell Ford,
even though the area continues to be a crowded collision repair market.
“I now have five body guys, a painter, a prepper and two estimators,” he said. “I have a fully certified team of collision repair professionals, and we’re doing very, very well actually.”
Dawson credits the turnaround to a shift in culture at the shop.
“What I think COVID has done is it made us realize that people just didn’t want to go back to work for a paycheck. They wanted to go back to work in a place where they felt truly appreciated, truly recognized, and where things are done right—or they weren’t going back.”
Going forward, Dawson sees growth in business happening organically, from the word-ofmouth recommendations that result when you take care of customers, rather than “breaking his neck” looking for direct repairs.
The company has a strong relationship with local Enterprise car rental branches, and owner Doug Campbell has taken the step of building the first EV charging station in Niles.
It’s clear that, at Campbell Ford, service is the key to growth.
“We’re supporting the EV industry and our local community here,” said Dawson. “My service manager and I sit on the board for three different high schools’ CTE programs. To us, everything’s about our brand and it’s about community. We’re a very proud store.”
Campbell Ford
Niles, MI
269-684-8300
www.campbellfordniles.com
Company At A Glance...
Type: Collision Repair
Facility Employees: 10
In Business Since: 1977
Number of Locations: One
Production Space: 10,000 square feet
AkzoNobel Coatings
800-618-1010
www.SikkensVR.com/us-en
Facebook: @AkzoNobelNARefinish
Twitter: @AkzoNobel_AACNA
Instagram: @AkzoNobelRefinish
LinkedIn: @AkzoNobel
YouTube: @AkzoNobel Refinish
Auto Beauty Center in Independence, MO, started out offering quick services like alloy wheel restorations and paintless dent repair. It later bought a mobile business offering detailing and minor collision repair, and brought those services into its retail location, along with mechanical repair.
Owner Brett Starr knew he was on to something. With a background in sales and marketing, he knew business is all about relationships. He also knew from his research that most shops pull in customers from a 6-mile radius and usually only see their regulars once every five years.
But his shop offers so many services in one place—including its own fleet of rental cars—making it so easy to keep a vehicle looking and running like new, it was drawing customers from all over the Kansas City metro area, and they were returning more frequently, allowing Auto Beauty Center to build a loyal customer base that trusted it.
“There’s a certain amount of the population that likes to keep their cars looking really nice, and we just make everything super convenient,” Starr said.
It wasn’t long before some of those regular customers needed more extensive collision repair services, the kind of jobs big enough to involve insurance companies.
“We did one or two [jobs], and thought we had to go full speed into this, because it’s a great opportunity,” Starr said.
However, one skillset not in Starr’s background was collision repair.
“I was nervous, never having worked in a shop as painter or body tech, but I wanted to make sure that we were following all the proper procedures,” Starr said.
Starr said he got to work putting together a plan to get into collision repair—including the tools he needed. His CCC representative recommended ALLDATA, because it automatically syncs with CCC’s estimating software, which the shop was already using. Starr said that turned out to be the right move.
“ALLDATA has played a big
part in our growth,” Starr said.
The shop now uses ALLDATA Repair software and ALLDATA Diagnostics, which turns a tablet into a scan tool to pull trouble codes and works with the software to look up OEM repair procedures for any vehicle that comes into the shop.
ALLDATA helps the shop repair vehicles quickly and accurately, which Starr said keeps cycle times down and customers happy as the shop processes about 300 vehicles per month, between all of the services offered.
“It’s impossible to know everything about every vehicle out there, especially as things are changing rapidly on cars, with more ADAS and more electronics,” Starr said.
ALLDATA enables the shop’s crew to pull up repair plans and schematics, as well as information about any special tools needed to complete a job.
“It just helps with the guessing game,” Starr said. “This car’s gotta be safe, and the only way to know is to print out the repair plan, go over it with the technicians and take in-process pictures along the way to make sure everything is done according to that plan.”
If one of the shop’s technicians runs into a problem, ALLDATA has master technicians on call through its Tech-Assist hotline service who can connect remotely to look at the vehicle, to either immediately identify the issue and how to fix it or do more research and call back with the solution. “Instead of my technician
having to do that research, he can go work on another car,” Starr said
“The support is outstanding,” Starr added. “Being able to just pick up the phone and call another master tech who specializes in Subarus or Mercedes-Benz or whatever vehicle is priceless.”
Technicians can also make a “Library Request” if they can’t find repair information for a particular vehicle, which sometimes happens on older or more rare models. ALLDATA quickly finds the answer and returns it.
ALLDATA also syncs with the shop’s QuickBooks software to upload estimate invoices directly, freeing up an employee who used to type in invoices to instead help customers, and keeps track of the shop’s inventory, alerting it when it’s running low on frequently-used supplies.
“It just simplifies our whole operation,” Starr said. “It helps us try to make repairing a vehicle more affordable for our customers.”
Starr said he also appreciates how proactive ALLDATA is.
“They’re always telling me about new things they’re working on,” he said. “I can tell them about pain points and they’re already working on it. They are always looking ahead, asking how can we make our system better and more efficient.”
Starr said he thinks of his vendors as strategic partners. The right ones can help the shop be more successful.
“ALLDATA is definitely one of those companies I rely on to help us be successful,” Starr said.
Auto Beauty Center
Independence, MO
816-252-1978
autobeautycenters.com
Company At A Glance...
Type: Collision & Mechanical Repair
Facility Employees: 18
In Business Since: 2016
Number of Locations: One
Production Space: 25,000 square feet
ALLDATA
916-478-3255
Company Contact: James Loveridge
Marketing Manager (916) 478-3255
james.loveridge@alldata.com
www.alldata.com
Facebook: @yourALLDATAteam
Twitter: @ALLDATA
Instagram: @youralldatateam
LinkedIn: @alldata_2
YouTube: @YourALLDATATeam
Cromax® EZ, an easy to mix, easy to match and easy to apply waterborne basecoat system that always delivers.
See how easy waterborne can be.
axalta.us/ez
Joining a franchise can sometimes mean signing on with a substandard vendor. Fortunately, that was not at all the case at ProColor Collision Montclair in Montclair, CA. Owner Carlos Flores has never been more satisfied with his paint system, thanks to the product and support he has gotten from Axalta after becoming part of ProColor.
“I’m very happy with the product and the manufacturer,” said Flores.
Flores said his path to becoming an auto body shop owner was different from many others.
“I’ve met a lot who are owneroperators,” Flores said. “They know the trade. They have been body men or painters, or in the insurance industry. I’ve done none of that.”
Rather, Flores got a business degree and an accounting certification, and worked as an accountant until the Great Recession hit in 2008. He joined his mother in her restaurant business for a few years, and then, in 2011, he and a friend opened their first body shop in Los Angeles, Evergreen Auto Body Specialists
Flores’ friend was the one who had the industry experience, while Flores brought the bookkeeping and administrative knowledge. The business partnership didn’t work out in the long run, but in the two years Flores worked with his friend, he learned a lot—enough to open his own shop.
In 2013, he did just that, opening what was originally known as Montclair Auto Collision
“That’s how I came to own my own business without picking up a piece of sandpaper or anything of the sort,” Flores said with a laugh.
In 2021, an Axalta representative visited Flores’ shop. Flores mentioned he’d been considering joining a franchise, and the Axalta rep recommended he consider ProColor Collision, which was just beginning to branch out into California.
Flores liked what ProColor had to offer and spent the rest of the year checking off all the tasks necessary to join—among them changing the name to ProColor Collision Montclair, earning I-CAR Gold certification and picking a new paint vendor, as the shop’s original vendor was not one contracted with ProColor.
After observing a product demonstration at Axalta’s training center in Pomona, CA, Flores chose to partner with Axalta. His shop has been using the Cromax EZ waterborne system since it officially started doing business as part of the ProColor Collision franchise in February 2022.
The Cromax EZ system of primers, sealers, base coats and clear coats is easy to mix, easy to match and easy to apply.
“We found out the primers and sealers work very, very well,” Flores said. “They give us great coverage. The sealers are just a great product to use.”
Flores also praised the base coats for their superior color match and coverage—especially compared to his shop’s former vendor.
“They just didn’t have the same coverage,” Flores said.
“Using Axalta means less material and more profit for the paint department.
“The clear is just phenomenal, just a great clear,” he added.
In addition, Axalta provided training for Flores’ head painter,
Alfredo Murillo, making him proficient at using the Cromax EZ system as efficiently and effectively as possible, to produce the best results while saving money on materials.
“He uses the entire Cromax system, which has led to bigger profit margins,” Flores said. “He’s our in-house expert.”
Flores said the customer support from Axalta has been topnotch since the first day.
“The customer support has been excellent so far; I have had zero complaints,” Flores said. “I am extremely happy with the support from Axalta and the team here in Southern California: Joel Sanchez and Carlos Lopez.”
ProColor Collision Montclair’s production increased easily between 25% to 30% per month, offering collision repair, painting services and computerized color matching, as well as a lifetime warranty on all insurance repairs. They are also working on their Tesla certification. “That’s very important to us,” Flores said.
Flores said Axalta will be a valued vendor partner for many years to come.
“Everybody from the top of the food chain to the very bottom has been very helpful, very supportive, and very encouraging every step of the way,” Flores said. “I’m very pleased with what Axalta has brought to my business, and what they continue to bring to the table.”
ProColor Collision Montclair
Montclair, CA
909-621-1052
procolor.com/en-us/shop/ montclair/
Company At A Glance...
Type: Collision Repair
Facility Employees: Nine In Business Since: 2013
Number of Locations: One Production Space: 9,000 square feet
Axalta Coating Systems
1-855-6-AXALTA axalta.us
Facebook: @AxaltaNArefinish
Twitter: @axalta
Instagram: @axaltarefinish
LinkedIn: @axalta
YouTube: @axalta
Offering collision repair in addition to mechanical repair and snowplow sales services, Shannon’s Auto Body’s two locations in Brainerd, MN, stay busy all the time. In July, they added a new, modern and upgraded location. At the same time, they switched to Axalta for their paint and accessories. The business has been using Spies Hecker Permahyd Hi-TEC for more than a year and couldn’t be more pleased with the results.
It’s an exciting time for owner Shannon Christian and his 40plus employees. He built his “dream shop” and needs to fill it with techs, estimators and support employees. “We have 43 people here now, but by the time we are fully staffed, we’ll have more than 50 people working for us,” Christian said. “We’ve come a long way from working out of a single-stall garage in 1996. This new 40,000-square-foot facility shows how far we’ve come.”
With windows everywhere, customers can see their vehicles getting repaired if they desire.
“We are all about full transparency,” he said. “Customers get to see us blueprinting and painting, with our paint booth in the middle of the shop floor. We made sure to install huge windows, so that they can see it all—calibrations, repair planning and paint application—it’s an educational tool for us. We’re running the paint production on a track system, with all taping and prepping happening outside the booth. It has been a big change and a real plus for our overall production.”
Christian received his initial education about the collision repair industry when he attended a local trade school, and hit the ground running.
“I was working for a shop while still attending school,” he said. “A car dealership hired me and I did everything I could to learn as much as possible. Four years later, I decided to start my own shop, so I took a leap and put everything on the line. We started with 2,000 square feet and expanded three times. Work was spread out between three buildings with a combined 17,000 square feet of workspace.
“The location wasn’t great; we were out of town without any drive-by traffic—we were known as
a ‘destination’ location. We kept the facility for mechanical repairs and snowplow sales and repairs. We also plan to use that space to expand our marine and RV repairs.”
Today, Shannon’s Auto Body is serving second-generation customers and developing a healthy mix of consumer and car dealership business.
“Quality work and customer service are key, and we’ve made it a priority since the very first day,” Christian said. “Our dealership customers rely on us to get their vehicles back and in top-notch condition, and we work hard to achieve it.”
Shannon’s Auto Body features ASE-certified and Platinum I-CAR technicians; Christian said he is proud to be an I-CAR Gold Class Shop. The business is also proud to use waterborne paint to reduce the impact on the environment, and are active members of the Society of Collision Repair Specialists (SCRS) and the Alliance of Automotive Service Providers Minnesota (AASP-MN).
In July 2022, Shannon’s Auto Body signed on the dotted line with their jobber, Blue Rock Refinishing Solutions, which was a big part of the reason for changing paint lines.
“We weren’t looking for a new paint vendor, but the people from Blue Rock came to us and we liked what they were saying,” Christian said. “They have played a major role in every aspect of the design we went with. They showed us what they had to offer and wowed us. The Spies Hecker Permahyd Hi-TEC line is a great product, but what is truly important is Axalta’s support and
knowledge. We trust the people at Blue Rock and our employees feel the same.”
Christian is enamored with the finished product and the process of using Axalta’s waterborne paint. “The Spies Hecker Permahyd HiTEC basecoat is fast and we have definitely increased our productivity since we began spraying it,” he said. “The color matches have been excellent and the cars are coming out of the booth looking perfect. We have also succeeded by referrals and word of mouth, and Axalta’s quality gives us a finished product that we can all stand behind.”
With one painter and two backup painters who can step in when needed, the training for applying the products was easy and drama-free. “First, we went to the Axalta Customer Experience Center in North Carolina to demo the product, and then about two months later, I sent my painter there for training,” Christian said. “He was up and running from day one and he has gotten even better over the course of the year. Our Blue Rock representatives come to the shop all the time for ongoing training, and that has helped us a lot as well.”
Operating out of a brand new facility with Axalta onboard and performing beautifully, Christian is psyched about the future at Shannon’s Auto Body. “To be successful, we need to align with companies like Axalta Coating Systems and Blue Rock Refinishing Solutions. They will help us grow and provide a consistently excellent product while saving us time and money.”
Shannon’s Auto Body
Brainerd, MN
218-829-6764
shannonsautobody.com
Type: Collision Repair
Facility Employees: 43
In Business Since: 1996
Number of Locations: Two Combined Production Space: 57,000 square feet
At Shannon’s Auto Body’s new 40,000-square-foot facility, quality work and customer service are key.
Axalta Coating Systems
1-855-6-AXALTA
axalta.us
Facebook: @AxaltaNArefinish
Twitter: @axalta
Instagram: @axaltarefinish
LinkedIn: @axalta
YouTube: @axalta
Payne Auto Group has been serving Southern Texas since 1949, with 15 new and used car dealerships throughout the region. In 2022, the auto group decided to add its second collision repair center in Pharr, TX.
General Manager Louie Solis was hired to run Payne Pharr Collision Center. Solis said he had researched paint booths in the past, ultimately choosing Blowtherm because they are reportedly efficient, capable and reliable.
“That all turned out to be true,” Solis said. “I was impressed.”
So when he joined Payne Pharr Collision Center to help outfit the repair center with top-of-theline equipment, there was only one choice. In February 2023, the shop installed a Blowtherm World extended height spray booth, along with a mix room and prep station.
“It’s like the Cadillac of paint booths,” Solis said.
The extended height Blowtherm booth’s interior measures 29’ 6” long, 13’ 6” wide and 11’ 6” tall—which is 2’ 6” taller than a standard booth, meaning it can accommodate the growing number of commercial vehicles in most any area of the country, including SUVs, crossovers, vans and pickup trucks. Solis said his shop is now one of the only shops in the area capable of servicing medium-duty commercial vehicles, a clear competitive advantage.
It fit in with other equipment the shop purchased to be able to work on larger, heavier vehicles, including lifts, frame machines and alignment machines.
“We designed the shop around being able to work on heavier vehicles and extended length and height vehicles,” Solis said. “That was one of the visions that brought us to the Blowtherm extended height booth. The shop is prepared to work on any size vehicle that comes through the door.”
In addition, if the shop switches to a waterborne paint system in the
future, Solis said it won’t have to replace its Blowtherm equipment, due to the spray booth’s flexibility and massive air movement.
Of course, just having the equipment doesn’t mean much if the finished product doesn’t look good, but Solis said that is never an issue with Blowtherm. Vehicle parts are always sprayed evenly and consistently, Solis said, resulting in a high-quality finish every time.
“We have one painter and two preppers, and they love everything about Blowtherm,” Solis said.
The spray booth’s direct-fired gas burner, with its fast response to set temperatures, and heating recuperator are also big selling points, Solis said.
“It has, I think, 90% recirculation when it’s in the bake cycle,” Solis said. “That’s one thing that really set it apart; it has massive air movement. That means shorter operating cycles, which helps get vehicles through that part of the process quicker.
“Everything is reduced—cycle times and labor costs,” Solis said.
Solis also appreciates the booth’s LED lighting, and how the booth’s door locations are customizable to make sure they fit in with any shop’s layout.
“The appearance of the equipment is very nice,” Solis added. “You can tell just by looking at it that it’s very well built.”
The reliability is also top-
notch, Solis said.
“It’s just a reliable piece of equipment,” he said. “As long as you keep up with maintenance on a regular basis, it gives you something reliable. I’ve worked with booths before that were always breaking down.”
Solis said he has received outstanding support from his Blowtherm distributor and authorized installer. “We’ve always gotten quick answers,” he said.
Blowtherm USA has a nationwide network of authorized, trained sales and service experts. To find your local distributor, call 1-855-463-9872 or email sales@ blowtherm-usa.com.
Comprehensive spray booth, prep station and mix room equipment information can also be found at www.blowtherm-usa.com.
Existing owners who have had Blowtherm systems for decades are thrilled with the new Technical Spare Parts reference guide on the web, making ordering parts for Blowtherm equipment easier than ever. The guide can be accessed at www.blowtherm-usa.com/ Technical-Parts.
Payne it forward! Payne Auto Group is also known for its robust community service program, “Payne it Forward,” giving thousands of dollars over the past six decades to student scholarships and several charities across the Rio Grande Valley.
Payne Pharr Collision Center
Pharr, TX
956-601-1080
www.payneautogroup.com/ payne-collision-center
Company At A Glance...
Type: Collision Repair
Facility Employees: 15
In Business Since: 2022
Number of Locations: One
Production Space: 17,000 square feet
Blowtherm USA & Training Center
855-463-9872 or 262-269-6265
www.blowtherm-usa.com
sales@blowtherm-usa.com
Brothers and co-owners Dan and Rich Schwartz combined their first names to form DANRICH Collision in 1980 in Homer Glen, IL. Since then, the body shop has changed to CARSTAR DANRICH, acquired a second location, earned a Tesla certification and had more family members join the team. Dan’s son Clarke is the general manager, while his nephew Danny is a painter.
“My brother and I are the third generation in the auto repair business,” said Dan. “My father was a technician, my grandfather was a technician and with my son and nephew working here, that makes four generations.
“Compared to the big MSOs, we’re still a small family operation and we treat our customers like family,” he said. “My brother and I still work on the floor, will repair cars when our team needs an extra hand, and my brother handles the parts department right now, too.”
During the pandemic, Dan and Rich bought a second location in Des Plaines, IL, that they’re currently remodeling.
“It now serves as Tesla parts storage,” said Dan.
CARSTAR DANRICH holds a Tesla manufacturer certification and is in the process of becoming BMW and Volkswagen certified.
Switching to Car-O-Liner® equipment over a year ago has helped CARSTAR DANRICH in earning OE certifications.
“Car-O-Liner® is approved by many of the OEMs we want to be certified by,” Dan explained.
“I remember when they wanted the Tesla certification, and now whenever I go in there, they are loaded with Tesla repairs,” recalled Chris Cooling, who works for Wakeman Equipment, a proud distributor of Car-O-Liner® that enjoys helping body shops such as CARSTAR DANRICH grow their business and earn OEM approvals. “There’s always one sitting on the Car-O-Liner® bench. So, I think the equipment has driven new business.”
Dan added that Car-O-Liner’s® sales and support team was also a
significant factor in choosing the vendor.
“The company stands behind their equipment,” Dan said. “If you have an issue with anything, they come in and are there for you.”
Dan recalled that when he purchased the Car-O-Liner® Quick42™, there was a shortage of clamps due to the pandemic.
“They worked well with me, and as soon as the salesman got one of the clamps in, he brought it out to us,” he said.
Dan added the sales team has been “easy to work with.”
“They’ve made purchasing Car-O-Liner® equipment seamless,” he said. “Chris comes here and sets everything up and spends two days training the employees.”
Dan added that when CARSTAR DANRICH hires a new employee, he calls Car-O-Liner® to make an appointment and a rep is there promptly to train the technician on their equipment.
In addition to the frame rack and measuring system, CARSTAR DANRICH also purchased the EVO™ Universal Anchoring and Holding System components from Car-O-Liner®
“Let’s say a vehicle doesn’t have pinch welds for clamping vehicles the traditional way,” said Cooling. “They now have all the equipment needed to properly anchor the vehicle and fixture parts in place to repair the vehicle per OEM procedures.”
CARSTAR DANRICH also purchased a CTR™9 Resistance
Spot Welder. The CTR™9 is a fullyautomated resistance welder designed to replicate factory OEM welds, explained Cooling. “This welder will measure the thickness and density of the metal and automatically establish the required settings to generate a proper weld nugget; the welder does all the work for you.”
Cooling said newer model vehicles contain several types of complex metals such as high strength and ultra-high strength steels.
“So, with the equipment they purchased, they can feel confident that no matter what metals they are working with, the vehicle will be repaired to OEM specifications,” Cooling said.
Cooling is introducing a new product to CARSTAR DANRICH, the CDR™1 Dent Repair Workstation.
“It’s an all-encompassing dent station for steel, aluminum, glue pulling and more,” Cooling said. “So, I provided them with the equipment for a month, as we continue to work together to learn all the applications for the product.”
Cooling concluded, “They’re a good family-owned business and I respect their hard work.
“I enjoy working with these kinds of clients,” he added.
Dan said his customers also appreciate the culture, environment and repair quality generated by their family-owned and operated body shop.
CARSTAR DANRICH
Homer Glen, IL 708-301-1250
www.carstar.com/locations/il/ homer-glen-15340
Type: Collision Repair
Facility Employees: 11
In Business Since: 1980
Number of Locations: Two
Combined Production Space: 18,000 square feet
CARSTAR DANRICH uses several Car-O-Liner® OEM approved products, such as the Volkswagen 6528 Measuring and Alignment System, to repair damaged vehicles.
North America
800-521-9696
info@car-o-liner.com
www.car-o-liner.com
LinkedIn: @car-o-liner-hq
AC Automotive Inc. was founded in West Hartford, CT, in 1985 by Aldo Carducci Sr. as a small Mobil gas station and three-bay mechanical repair shop.
As Aldo Sr.’s two sons, Guy and Aldo Jr., grew up and became more involved in the business, they added a 24-hour towing service, which brought in a lot of collisiondamaged vehicles. The family started to perform some of that body work themselves.
Eventually, the shop needed to replace its gas tanks per state regulations, at which point the family decided to get out of the gas business altogether and focus on mechanical and body repair.
“That’s when we put a big addition on our building,” Aldo Jr. said. “We added another 6,000 square feet to offer more body repairs. As time continued, we had so much success, we decided to get out of towing completely and focus our attention on collision.”
Today, Guy and Aldo Jr. own AC Automotive, and no longer offer towing or mechanical repairs unless it’s tied to the collision repair. In 2021, they opened a second location in New Britain.
The I-CAR Gold and ASEcertified shops hold certifications from Nissan, Infiniti, Hyundai, Kia, Alfa Romeo, Subaru, FCA and Mazda, offering full body repair and refinishing, paintless dent removal, headlamp renewal and windshield replacement. Between both locations, AC Automotive repairs about 200 vehicles per month.
Aldo Jr. said the business has used CCC Intelligent Solutions’ estimating platform, CCC ONE, “since the beginning of time,” and has since added more of CCC’s tools.
“We just kept adding each product that they offer as we went along,” Aldo Jr. said. “Their product is very intuitive, easy to work with and self-explanatory. They have a lot of nice features between scheduling and photo estimating. Really, it’s the whole package, so it makes running an auto body shop pretty easy.”
This summer, AC Automotive participated in a test of CCC’s newest offering: Repair Cost Predictor, part of the CCC Engage digital marketing tool, designed to accelerate lead generation. The feature was made available to all shops with CCC Engage, at no extra charge, in mid-August.
Repair Cost Predictor helps shops spend less time writing estimates that may not result in work. A potential customer, using their phone, can add images of their vehicle to a chat with the shop, and CCC’s AI-powered tool generates a predicted range for the cost of repair in seconds. The customer is then prompted to either get a full estimate or book a repair appointment. If the customer asks for an estimate or appointment, shops also receive these photos and the predicted range right into CCC ONE.
“My initial take is that I’m very happy with it,” Aldo Jr. said.
“One of my concerns was that the predictor would be off,” he said. “In this day and age, we are getting used to AI and new technology and how reliable it will be. I was thinking it would be on the low side for the cost predictor, but it’s actually pretty accurate. I’ve been very surprised and happy to see how accurate the predictor is.”
Customers have also been pleasantly surprised by the speed with which they can get an idea of how much a repair might cost.
“They’ve commented on how quickly they were able to get a response, which gave them some guidance,” Aldo Jr. said.
The Repair Cost Predictor allows AC Automotive to get the ball rolling on a potential repair in a relatively simple manner without tying up a staff member on writing estimates that may not go anywhere, Aldo Jr. said.
“This is just another way for us to control costs without having someone simply dedicated to writing estimates all day long,” he said. “It allows my staff to be freed up to do some other important tasks throughout the day.”
Giving customers an immediate estimate also “weeds out” those who aren’t serious about getting a safe and proper repair done on their vehicle, further saving the shop time, Aldo Jr. said.
“Once they get the lead, the ones that follow through are the ones who want their cars back to OEM specifications,” he said. “The ones looking to cut corners usually won’t follow through after the cost predictor.”
After participating in the test, Aldo Jr. said his shop’s two locations would absolutely continue using the Repair Cost Predictor.
“A customer calls, we can offer the feature and get the process going. People are used to instant gratification, so if you’re not immediate, you’re behind,” he said.
AC Automotive Inc.
West Hartford & New Britain, CT 860-236-5020
ac-auto.com
Company At A Glance...
Type: Collision Repair
Facility Employees: 23
In Business Since: 1985
Number of Locations: Two
Combined Production Space: 14,000 square feet
CCC Intelligent Solutions
877-208-6155
www.cccis.com
Facebook: @CCCIS
LinkedIn: @ccc-intelligent-solutions
For more than 20 years, CIV Car Care Center owner Carlos Reyes has combined his passion for automobiles with his commitment to the community.
Born and raised in Boston, MA, Reyes opened his first body shop, C&J Auto Body, in 1991 in Boston, which was eventually sold. In 2019, he established CIV Car Care Center in Hyde Park.
The body shop prides itself on providing exceptional automotive repair services and ensuring customers’ needs are met with professionalism and expertise.
Branden Naraine, body shop manager, said Reyes has built a reputation for offering top-notch service in the Greater Boston area and runs the business based on his love for cars and care for people.
“He is very generous and volunteers his time in the community,” said Naraine. “It’s something that is near and dear to his heart.”
Reyes supports a variety of local charities and youth organizations in the Boston area, such as the Boston Raiders Pop Warner Football Team and YMCA Greater Boston.
“He wants to give back to the community where he was raised and helped make him the man he is today, which is a pillar in the community,” said Naraine. “The positive impact that he has will ultimately change the lives of some of the youth in our city.”
Since joining the shop in April 2023, Naraine has found Reyes considers his employees and customers family.
“That’s what’s most important to his business,” he said. “We have a family atmosphere at the shop and when customers come in, they are treated like a family member.”
Part of taking care of employees and customers is ensuring a safe environment in the shop.
“When a vehicle is hit in the front and you have to change the condenser and AC unit, it has to be safe for the technicians to take those parts off,” explained Naraine.
“It’s essential to our business that we’re able to be sure they are safely depressurized.”
The shop purchased its first refrigerant management system from CPS Products in November 2022, the MAXXAIR™ MX3030 Refrigerant Management System.
The dual refrigerant unit provides full YF compatibility and was designed to efficiently recover, recycle and recharge automotive A/C systems, serving all refrigerant types. It is compatible with both electrical and traditional engine-driven compressors and is constructed of a durable welded steel frame to withstand shop environments.
It can also quickly convert from an R-1234yf model to an R-134a to service an increase in demand or replace a non-working R-134a machine.
The patented motor-controlled ball valve was created to open wider than traditional valve configurations for increased flow. With many compressors failing due to varying amounts of oil, the patented compressor is oilless. The product has an interactive touchscreen LCD display compatible with a WiFi printer and can integrate with Bluetooth wireless adapters for service checks.
Serving multiple industries, CPS Products develops and manufactures specialty tools and equipment for service technicians to “work smarter, win more business and make more money.”
Established in 1989 and based
in Florida, the company invests heavily in industrial design and builds its products to be easy to use. The CPS development team includes electrical, mechanical, software and chemical engineers.
The company’s distributor, Kwik, recommended CIV Car Care Center purchase the high-quality MX3030 Refrigerant Management System for the facility.
“When recharging the air conditioning system in vehicles, you need to think about how you store these chemicals and make sure they don’t leak,” said Naraine. “The MX3030 is really going to help keep our technicians safe.”
Working with a pressurized system, the CIV Car Care Center team wanted to ensure they had a good understanding of how to use the machine. After seeing a demo and receiving training, Naraine said they have been impressed with how easy it was to use.
“The gauges let you know if pressure is getting too high,” said Naraine. “The machine lets you know what to do and really doesn’t allow you to make a mistake.”
Naraine said once the car has been repaired and put back together with a new condenser, the MX3030 ensures it is recharged accurately with the amount of refrigerant required.
Since purchasing the unit, Naraine said it has become an essential piece of equipment in the shop and they have been impressed with the customer service provided by CPS Products.
CIV Car Care Center
Boston, MA
617-272-3221
civcarcare.com
Type: Collision Repair
Facility Employees: Six
In Business Since: 1999
Number of Locations: One
Production Space: 10,000+ square feet
CPS Products’ MAXXAIR™ MX3030 Refrigerant Management System has become an essential piece of equipment at CIV Car Care. Technicians Alex and Alberto are pictured.
CPS Products
305-687-4121
cs@cpsproducts.com
Facebook: @cpsproductsinc
Twitter: @cpsproductsinc
Instagram: @cpsproductsinc
LinkedIn: @cps-products
LIGHTWEIGHT, LOW PROFILE precision balanced design delivers superior control
DUAL RUBBER SUPPORTS provide incredible stability when the machine is not in use
20' SWIVEL CORD
RUBBERIZED DYNAGRIP delivers reduced vibration and increased insulation resulting in greater operator comfort and reduced fatigue
TOOL CAN RUN 5" OR 6" PADS
#RespectTheFinish
Follow us on Instagram: @dynabrade_auto
SINGLE-ACTION LOCK TRIGGER
ERGONOMICALLY-DESIGNED EXTENDED HANDLE for increased operator comfort during use
2 TOOLS - IN -1
Cuts like a rotary, finishes like a DA!
In 1979 at the age of 13, Renny Doyle started detailing aircraft to help get his mom and grandmother off welfare. Later that summer, he detailed his first car.
“From there, the company just kept growing,” Doyle said.
Business continued to grow, but in 2005 it skyrocketed shortly after he and his team detailed the first ever jet-powered Air Force One, known as SAM 970.
“It hit the news, and with the internet coming along rapidly, we started getting requests from people who wanted us to train and coach them,” Doyle explained. “So, in 2005, I said, ‘We’ll give it a shot,’ so I put my first class on, and it took off.”
Doyle then sold his detailing shops and fully committed to coaching detailers.
Doyle’s current company, Detailing Success, which he runs with his wife, has headquarters in Big Bear, CA, with five other locations in New Jersey, Texas, Oregon, Florida and Northern California.
“We do advanced five-day courses and extreme one-day training here in Big Bear, while our other locations focus solely on our extreme one-day classes,” he explained. “We have three fulltime employees in Big Bear. The technicians and entrepreneurs who run our other locations are trained and coached by us first.”
Doyle added, “So our five other locations are independent businesses with their own training, like a licensing program.”
Autobody News asked Doyle why his business stands out in the industry.
“We’ve been detailing for a long time; it’s a low-entry-cost business,” he said. “So, we knew many detailers creating fairly wellpaying jobs, but not businesses.”
Doyle said when he and his wife started Detailing Success, they wanted to do it differently.
“We educate the people we engage with at high technical levels, so their skill sets are high, and, most importantly, we tie everything back to profits,” he explained. “It always comes back to running a legitimate business, earning as much as possible, and having a good life while doing it.”
Recently, Doyle embarked on another venture, creating a
polishing tool with Dynabrade. He started using Dynabrade tools 20 years ago, but met with the company’s California rep, Matt Denney, a few years ago.
“We built up a great friendship and colleague relationship,” he said. “I started getting more involved with Dynabrade and seeing what they’re doing.”
He said Dynabrade started creating liquid products, compounds and polishes around that time.
“We have our line of detailing products, but we’re pretty Switzerland,” Doyle explained. “We believe that if everyone is doing better, we’ll do better.”
So, Detailing Success and Dynabrade started collaborating, creating a “great opportunity” to sell their wares.
At that point, Doyle said, he had wanted to develop his own tool for the past four or five years. He said he asked himself who he could trust to help him with this dilemma, and Dynabrade was the answer.
“It’s a revolutionary polisher,” he said. “And it has been designed by people who touch tools to paint: body shops, detailers, dealerships, even a fire department; they’ve all been in the testing and development stage.”
Doyle said he’s proud to have built an ergonomically correct tool.
“It’s called a GDA—geared dual action tool, which is unique. It brings a lot of qualities to the table,” he explained. “Normally, where the internals are steel, many of ours are composites, which absorb and dissipate heat better and lighten the tool.”
He added the tool has a low profile, so people using it on paint
found it easy to handle.
“It’s a tough tool, and it goes through everything, so during testing, we started calling it the Warthog,” he said. “We’ve done drop testing and really beat this thing up.”
In July, Doyle and his team commemorated the 20th anniversary of The Detailers of Air Force One by once again tackling the massive project at the Museum of Flight in Seattle, WA.
“During the project, we introduced the tool to the public,” he said. “From July 9-18, we put hundreds of hours on these tools. It was the first time the tools were used en masse.”
Doyle’s team detailed 17 aircrafts over eight days.
Autobody News asked Doyle what body shops would benefit from using this tool.
“One of the weakest links in all of our businesses, especially body shops, is skilled personnel,” he explained. “And this tool does all, so you’ll get better work with less training.”
Doyle referred to the tool as “the Apple iPhone of polishers.”
“We’ve simplified it: You can cut with it, you can finish with it, it’s durable, and it’s not confusing to learn,” he explained. “So, the chance of damage is lessened greatly.
“It’s a modern-day machine,” he added.
“You can put it in the hands of a body shop owner or manager, and they’ll be able to develop their skillbased technicians much quicker,” Doyle said. “And if you lose people or there are shifts in personnel, there’s no big hang-up trying to get somebody up to speed. It’s a relatively easy tool to learn.”
Big Bear, CA 909-366-0909
detailingsuccess.com
Company At A Glance...
Type: Mentoring/Training for Detailers
Facility Employees: Three In Business Since: 2005
Number of Locations: One Production Space: 5,000 square feet
Doyle teaches detailers across the country how to not only develop a high skill set, but also create a profitable business.
Dynabrade
800-828-7333 x536
ron.veiders@dynabrade.com
www17.dynabrade.com
Facebook: @Dynabrade
YouTube: @DynabradeInc
Instagram: @dynabrade_inc
When Star Body Works, a fourshop regional MSO in Southern Oregon that also has a suspension calibration shop and a towing business, decided to expand its repertoire to include auto glass services, General Manager Jake Jennings asked around for recommendations on the best way to do it.
“They all said, ‘Hands down, Equalizer,’” Jennings said.
Jennings and three other Star Body Works employees have since completed Equalizer’s oneweek, 40-hour course at its Auto Glass Academy in Round Rock, TX, taught by Global Education Director Gilbert Gutierrez. After hiring another employee who already had experience in auto glass, Star Body Works can now keep all its collision repair facilities’ glass work in house—saving money and cycle time.
Star Body Works repairs an average of 450 cars per month between its four I-CAR Gold Class locations in Medford and Grants Pass, OR. The shops hold numerous OEM certifications, including Tesla, Subaru, Honda, Acura, Nissan, GM, Ford, Volvo, Chrysler, Kia, Hyundai and Mazda, and is close to achieving Mercedes-Benz.
Jennings said the shops pull away all glass from any panels being painted, for a factory-like finish that doesn’t expose paint lines to UV rays. “That’s almost every car if we’re doing a quarter panel, lift gate or pillar,” Jennings said.
Before, Star Body Works sublet that work to a mobile glass company that visited all four shops nearly every day. Now, it has its own van, staffed by its employees, who can do all the glass work themselves.
Jennings said bringing glass work in-house has several advantages.
First, the shop can make a bit of a profit off glass work now. When it was subletting the work, insurance companies would not allow Star Body Works to charge them any more than Star paid the mobile glass tech. “If I keep that in house, now I pay a labor cost, but I can
make a profit off of it,” Jennings said.
Second, the shop has more control over scheduling repairs and replacements. “The glass industry is stretched so thin with how much work is out there,” Jennings said. “Two years ago, we could get (the sublet company) in same day (to do glass work.) Now, it’s two to three days minimum.”
Jennings said that is only going to get worse, as several glass companies are leaving the collision repair industry because insurance companies are putting pressure on how much shops are allowed to charge for the work. The 30-squaremile area of Oregon where his shops are located is down to only one such company.
Third, Star Body Works can ensure calibrations are correctly performed on its customers’ cars, which is becoming increasingly important in glass work.
“People who’ve been doing (auto glass) for 20 years don’t understand the importance of recalibrations, and it’s putting lives in danger,” Jennings said. “That’s the shadow lurking behind the windshield business.”
Jennings said he reached out to Shannon Kern, education program director at Equalizer, to find out what it would take to get trained. Soon after, he and another employee went to Texas for the one-week course. Jennings, who started in the collision repair industry with a high school internship more than 20 years ago, said the course “was a lot more
than people anticipate,” but he saw students who started with no knowledge of the industry build their skills as quickly as people who already had years under their belts.
Over the five days, the students learned about laws related to glass repair and replacement and were taught—both in the classroom and in a hands-on shop—how to correctly prepare a vehicle, including pre-scanning ADAS features, and perform the work. The course was capped off by a final written test and a handson replacement observed by instructors.
When the students passed the final, they were certified by Equalizer and eligible to take the national certification test, which Jennings also passed.
Equalizer also gives students a tuition credit to purchase tools, which Jennings took full advantage of. He said Star Body Works uses the Viper and Raptor cord and wire glass removal tools, as well as Equalizer’s glass stands, knives and chip and crack repair tool.
“I like the tools and the way they work,” Jennings said. “You know they’re going to have the tool that works the best. All their tools work together.”
Jennings said he has only had to send back one tool to be repaired, which Equalizer did, under warranty, and returned in two days.
“We get really good support,” Jennings said. “I’m constantly ordering stuff from them. They know me and answer with ‘Hey Jake.’”
Star Body Works
Medford and Grants Pass, OR 541-779-5621
starbodyworks.com
Company At A Glance...
Type: Collision Repair, Glass Replacement
Facility Employees: 65
In Business Since: 1948
Number of Locations: Four Combined Production Space: 65,000 square feet
Equalizer® Industries, Inc. 512-388-7715
www.Equalizer.com
www.autoglassacademy.com
Facebook: @equalizertools
Twitter: @equalizertools
Instagram: @equalizertools
YouTube: @equalizervideo
Clear, onscreen step-by-step instructions make the ADASLink® diagnostic scan tool your gateway to ADAS calibrations.
Onscreen direction walks techs through calibrations for millions of vehicles
Comprehensive pre- and post-scans of installed systems and codes
Full diagnostic capabilities reveal trouble codes and other vehicle information
Secure gateway and gap coverage
Code/pair new parts to the vehicle after installation
Follow guided processes to calibrate required systems after a collision
Ricky Ragle opened Canton Paint & Body in 1993 after “getting tired” of his one-hour work commute from Dallas, TX, recalled his son, Corley Ragle
“My mom was also traveling back and forth, working for the City of Sunnyvale, and started realizing, ‘We can make some money at this, Dad is really good at this,’” Corley Ragle said. “So, she gave her notice at that job and came over to the body shop and worked with Dad.”
Ragle said the two worked side by side, building the business together.
About 18 years ago, Ragle joined his mom, Sue Ragle, to run the body shop in Canton shortly after his dad retired in the early 2000s.
However, this past year, Ragle became the sole owner of Canton Paint & Body following back-to-back tragedies. During the pandemic, he lost his father to COVID, and in March 2023, his mother lost her battle with Stage 4 breast cancer.
“God threw a lot at us all at once,” he said.
Ragle added it has been difficult finding someone with his mother’s work ethic, as she “could do 20 people’s jobs.”
To adjust to this significant loss, personally and businesswise, Ragle made major shifts at his collision repair center.
“We wanted to invest money back into the shop, and we had already expanded our main building to 30,000 square feet,” he explained. “Plus, we had acquired several buildings next door so our customers can access Enterprise rental cars onsite and for additional workspace.”
In total, the body shop now has 40,000 square feet of workspace.
“We never imagined that we’d get this big for a small town,” said Ragle.
Ragle said they got tired of subletting jobs that required ADAS technology and alignment equipment. They were risking quality with offsite mechanics who wouldn’t take ownership of their work. So, he reached out to a trusted local mechanic, who
had owned an auto repair shop 20 years before retiring, and told him his dilemma. Ragle said his friend referred him to Hunter Engineering, saying the company was “the best.”
“I looked them up and reached out to a gentleman named Joe Yoder,” Ragle explained. “Mr. Yoder came down and met with me the same week. Next thing you know, we got three brand new alignment machines, along with the full ADAS system to recalibrate object sensors and parking sensors, distance control for your adaptive cruise control, and more.”
Ragle said having Hunter Engineering equipment “has made things a million times better and stress free.”
“Now we’re not subletting our stuff across town,” he said.
“I have one in-house mechanic, and we just drive it from one of our buildings to the other. We do everything here, so we can control the quality, and keep all the money in house.”
Ragle added Canton Paint & Body can also “mark things up properly now.”
He also shared insight for body shops reluctant to incorporate ADAS technology.
“I’m sure there’s a lot of small shops debating getting into ADAS,” he said. “I highly recommend it because obviously more and more computers are getting put into cars every day and they’re getting smarter and smarter. So, you have to evolve with the technology you’re given.”
During the past year or so working with Hunter Engineering, Ragle reported the equipment is “great, user-friendly, and the ADAS
software is always up-to-date.”
“Getting the updates is huge for us; it’s a concern for a lot of shops,” he said. “Out of 300 cars, we’ve only come across two instances where the update wasn’t released by the manufacturer yet on ADAS.”
Ragle said his relationship with Hunter Engineering sales reps has been “awesome.”
“Mr. Yoder is the best salesman and I’d say he’s a technical guy too,” he said. “If you call him on his cell, I mean call any time, he’ll answer a call or text and he always has the answer, and in the rare occasion where he doesn’t have the answer, I promise you, he will have that answer here shortly. So, that’s one thing I love about him; he’s real persistent.”
Ragle added Hunter Engineering also offers classes to customers. In addition to classroom training, Canton Paint & Body works with Tim Sowers, a dedicated technical and training representative from Hunter. He installs and maintains the equipment and does on-site training with the technicians when needed.
Ragle said Sowers is “leagues above anybody I’ve dealt with [from other vendors] as far as customer service and knowledge.”
“We need more of him at several other companies,” he said. “You can call him, text him, and he’ll answer you, which is nice.”
As far as customer relations, Ragle said, “We’re a small town and we treat everybody like family. We know nobody wants to be here after they’ve been in a wreck, so we always try to make it as easy as possible for them.”
Canton Paint & Body
Canton, TX 903-567-2500
Company At A Glance...
Type: Collision Repair
Facility Employees: 21
In Business Since: 1993
Number of Locations: One
Production Space: 40,000 square feet
Hunter Engineering Co. 314-716-0469
tmaitz@hunter.com
Facebook: @hunterengineeringcompany
Instagram: @hunterengineering
LinkedIn: @hunter-engineering
YouTube: @HunterEngCo
As a child, John Melendez spent much of his time at his father’s body shop, John’s A1 Body Shop in East Chicago, IN. In 1996, Melendez began working at a multi-line dealer with 19 stores in Park Forest, IL. He purchased the dealership’s body shop in April 2005, and renamed it JDM Collision, incorporating the initials of his name, John David Melendez. Later, the facility moved to Olympia Fields and was sold in 2015.
Melendez bought a second collision repair facility in Lansing, IL, in 2010, which was moved five years later to a more modern, updated center in Thornton, IL. The company currently operates the one location in Thornton and prides itself on staying educated about the latest technology and repair methods to fix cars properly.
The business owner attributes his success to focusing on continuous training and improvement.
“What helped get me in the position I’m in today is education,” said Melendez, a certified GM technician and mechanical technician.
A key element of the education is provided by I-CAR, the InterIndustry Conference on Auto Collision Repair. The international nonprofit organization is dedicated to providing information, knowledge and skills required to perform complete, safe and quality repairs.
Melendez began attending live I-CAR courses in 2015.
“I took a liking to it and then became serious over the years,” he recalled. The business achieved I-CAR Gold Class® recognition starting in late 2018 and continuing into 2019. At the same time, JDM Collision was recognized as a certified GM repair center.
Since taking his first I-CAR class, Melendez has noticed I-CAR always seems to provide the latest training and development for the collision industry. This includes a portfolio of more than 300 online, live, virtual and in-shop courses.
Whether an employee is focused on becoming an ADAS or non-structural technician or estimator, or taking on another role in the shop, such as production management, there is a path available through
I-CAR. A variety of programs are also available, including Hands-On Skills Development™, vehicle and technology classes and welding certification.
“Our employees are learning as we go along,” he said. “It has been fun and interesting and keeps you sharp.”
Since the pandemic, many technicians have become accustomed to taking online courses.
“Technicians can now complete online courses during a workday, and I’m not taking away their personal time,” explained Melendez. “That has really helped my business grow and become more efficient.”
As an I-CAR Gold Class facility owner, Melendez has prioritized training for himself and employees.
The Gold Class® recognition, which started in 1990, is the highest role-relevant training achievement recognized by the collision repair industry.
Having I-CAR Gold Class status has helped JDM Collision employees learn what is needed to complete safe and quality repairs. It has also helped the business acquire OEM certifications.
“OEMs want you to be trained and make sure you are following the correct repair procedures,” he said. “That has led us to continue getting trained by I-CAR.”
Their current path and dependence on I-CAR training will help the team at JDM Collision gain OEM certification for Ford, Nissan, JLR, Hyundai and Kia, and become one of GM’s only certified centers equipped to handle the new EV platforms.
“Being I-CAR Gold Class will make it easier for us to acquire these
OEM certifications,” said Melendez. “Honestly, we wouldn’t have been able to acquire them if we didn’t have I-CAR Gold Class recognition under our belt.”
The shop’s purchase of a building down the street is being set up as an advanced calibration center called JDM CALIBRATION Center. In addition to focusing on calibrations, alignment and EV mechanical repair center, it will also do body and aluminum repair.
When the facility opens, they plan to use tow trucks to transport vehicles to and from their existing shop. The new center will offer service to other collision repair centers in the Chicagoland and Northwest Indiana area.
“We’re going to be a one-stop shop for consumers,” he said. “It is so exciting to be able to operate with this type of status, and the repairs coming to our door are not driven by any insurance company.”
Melendez is also looking forward to dealing with other EV manufacturers when the training paths are completed.
With a passion for industry training, Melendez has volunteered as the Northwest Indiana I-CAR Committee chairman for the past four years. In this role, he provides information to local shops about the options available.
He stresses the importance of technicians taking the time to stay up to date with new technology and repair methods.
“My advice to other shops that want to stay in the collision industry is to not be intimated by the complexity of the cars on the road today,” he said. “The information is out there, and any individual who doesn’t take advantage of that should not be fixing cars.”
JDM Collision
Thornton, IL 708-877-7300
Company At A Glance...
Type: Collision Repair
Facility Employees: 10
In Business Since: 2005
Number of Locations: One
Production Space: 13,000+ square feet
I-CAR 800-I-CAR-USA
www.I-CAR.com/GTGC
Facebook: @icareducation
Twitter: @I_CAR_Education
Instagram: @icareducation
LinkedIn: @company/i-car
YouTube: @user/icartraining
The Inductor® Pro-Max uses high frequency magnetic fields to generate Invisible Heat® in metallic car parts without the collateral damage of an open flame to nearby parts. Quickly and easily remove vinyl graphics, moldings, auto glass, windshields, mechanical and suspension parts.
Applications:
> Back Glass
> Door Dings
> Graphics & Decals
> Nuts & Bolts
> Seam Sealers
> Spray-in Bedliners
> and 100’s more!
This tool is manufactured in the USA with genuine OEM parts. Available through your local tool distributor.
Follow Us On Social Media:
Kijana Noel, owner and operations manager of G&B Collision Center in Brooklyn, NY, is carrying on a long family tradition in the automotive repair industry.
Noel’s grandfather opened a shop in Grenada more than 60 years ago. All five of his children grew up to work in the industry, either on the mechanical or auto body side.
One of his sons—Noel’s uncle—and a friend started working on friends’ and family’s cars in Brooklyn, NY, out of a two-car garage behind a house in the early ‘90s, on evenings and weekends. Buzz grew by word of mouth, and eventually his uncle felt he had enough steady work to move the operation into a 5,000-square-foot facility in 1998.
“The climb was slow, but we got rolling,” Noel said.
Meanwhile, after high school, Noel attended the diesel mechanic program at Ohio Technical College, then came back to New York to work for his uncle, joining the team in 1999. He is now a co-owner of the shop and oversees operations.
“It’s kind of a family trade,” Noel said.
Today, G&B Collision Center has grown into an 8,000-squarefoot space. The I-CAR Gold Class facility repairs about 90 vehicles per month, offering heavy collision repair, minor dent repair, paintless dent removal, wheel repair and car lease return pre-inspection services.
Noel said the family-run business has always kept an eye out for cutting-edge technology. “We love tools,” he said. “That’s another thing that’s ingrained in our DNA—we love new fascinating tools that make our job easier and cleaner.”
That’s why they purchased their first induction heating tools from Induction Innovations not long after the company started offering them. Founder and President Tom Gough developed the first Inductor Series model in 2000, inspired by his 28 years in collision repair, seeing the many time-consuming processes.
G&B Collision Center has been using a full-size Inductor Series
model and a Mini-Ductor Venom for about two decades, Noel said, and the technicians all prefer them to open-flame torches when they need to remove any adhesive from metal, including sealers, under coatings, glass or tape, or heat up corroded or seized bolts.
“It would be hard to get them to go back to an oxy-acetylene torch,” Noel said, as the induction heating tools are safer, cleaner and more versatile.
Noel said he prefers the induction heat used by Induction Innovations because “anything can happen” when using an open flame.
Noel recalled seeing a car’s interior catch fire while a technician used a torch to heat up seam sealer underneath the car. Before anyone realized what was happening, the fire spread, burning 60% of the interior before it could be extinguished.
“That was enough for me, just seeing that,” Noel said. “You just have a lot more control with the inductor versus the open flame.”
Induction heat also does the job more cleanly.
“We use the Inductor Series when we’re changing panels and have to remove sealer, or under coating,” Noel said. “When we take off moldings attached with two-sided tape, it comes off a lot cleaner. We use it a lot day to day.”
According to Induction Innovations, the Inductor and MiniDuctor both use high frequency magnetic fields to heat ferrous
metals without the collateral damage to nearby plastic parts torches can cause.
Noel said the Mini-Ductor Venom is great for gaining access to smaller, tighter spaces the fullsize model can’t reach. Using one of the included coils that can flex around corners a flame cannot, the Mini-Ductor heats a 3/4” nut red hot in seconds.
Induction Innovations also notes using their tools can save shops money by allowing them to re-use some parts that might otherwise be discarded and save on consumables.
G&B Collision Center purchases its Induction Innovations tools from Collision Equipment Consulting, Inc., Noel said, and is very happy with the support it receives from owner Ted Dinnela
“We’ve only had one issue ever, with the Venom. It was under warranty and we got a new one. The service has been so far, so good,” Noel said.
He said the Induction Innovations tools are also easy to use and don’t require any extensive training.
“The techs love it,” Noel said. “You can do a lot with it. Once they get the hang of it, they prefer it.”
Of all the advantages the G&B Collision Center team enjoys using Induction Innovations tools, the safety is the biggest one.
“This industry can be very dangerous, and anything that makes it safer is definitely a plus,” Noel said.
Brooklyn, NY
718-230-9793
gbcollisioncenter.com
Company At A Glance...
Type: Collision Repair
Facility Employees: 12
In Business Since: 1998
Number of Locations: One
Production Space: 8,000 square feet
Annand Gaul uses Induction Innovations’ Inductor Max. Noel said his once his shop’s employees get the hang of induction heating tools, they prefer them to openflame torches.
Noel said the induction heating tools from Induction Innovations are cleaner, safer and more versatile than traditional torches.
877-688-9633
www.theinductor.com
Facebook: @InductionInnovations
Twitter: @invisibleheat
Instagram: @induction_innovations
LinkedIn: Induction Innovations, Inc.
YouTube: Invisible Heat by Induction Innovations
The new Talon is a portable, gas-catalytic, medium-wave infrared curing unit that incorporates the same unique emitters as larger, in-booth US Autocure systems.
Dabler Auto Body has maintained its reputation as a toptier collision center for decades. Founded in 1967 by Chuck Dabler inside a Volkswagen dealership, the 16,000-square-foot standalone Salem, OR, facility is now owned by Dabler’s son, Dennis, and Mike Brockway
Their high-volume shop, which turns out 100 vehicles monthly, boasts certification credentials from Subaru and the Certified Collision Group, which maintains a nationwide network of OE certifications. To further establish the business as a best-in-class body shop, the company focuses on a narrow vehicle demographic, primarily specializing in highend German marques as well as Subarus, which are popular in the Northwest.
“We’ve always wanted to be an elite repair facility,” said Brockway. While acknowledging it took time to shift from working on any vehicle no matter the make, model or vintage, they now only service passenger cars from 2010 or newer. “This is our niche. We had to be selective, pick a lane and go fast. We hired additional techs and invested in ADAS equipment, training and the latest tools. This is a volume game, so we have to be very efficient and streamlined to achieve the most success.”
Their success is also linked to a long-standing relationship with Industrial Finishes & Systems. “Our experience with Industrial has always been amazing,” said Brockway, who first worked with Industrial while employed as head painter at Dabler in the early 2000s. He later served as Industrial’s BASF tech rep and business development manager during the firm’s transition from distribution center to a multifaceted resource for business services and solutions.
“Industrial excels at building relationships,” he added. “They not only provide excellent service, but also excellent support and training
on how to use the products and make money with them. Any time I need to know something, the response is always ‘I got a guy’— they always have the solution. That’s a huge part of our success.”
Brockway pointed out Industrial is also a source of cuttingedge technology to help shops be more efficient and productive.
“They’ve always been innovative and bring new products for us to beta test.”
Case in point: Dabler Auto Body is currently beta testing a mobile infrared curing system, which significantly reduces cure time. The mobile system, known as Talon—a version of a fixed unit that works with paint booths—can be operated from a local terminal, computer or smartphone.
“It’s cutting-edge technology and it’s changing the way we look at production,” said Brockway. “We use BASF’s UV primer and Bondo. It’s why we can paint five cars a day, 25 cars a week and 100 cars a month through one paint booth. Without the accelerated dry times and those products, we wouldn’t be able to do that. It’s truly innovative.”
In reflecting on his decadeslong career, Brockway also credited Industrial for the experience he gained as their employee. “I was
a journeyman painter and knew how to run a shop, but as business development manager I learned the nuts and bolts of running a business and how to operate profitably. It was a career-building experience.”
It also served as a springboard for Brockway to join forces with Dennis Dabler as the company’s CFO in 2015. “Even when I was in college, I knew I’d own a successful body shop at some point,” he said.
In the years since, the duo has made significant strides. Starting with six employees, there are now 21. Annual revenues have grown dramatically year after year, from a modest $800,000 in sales to nearly $5 million this year.
“We are about 30% DRP and 70% non-DRP, though we still facilitate the claim through the customers’ insurance, just without the contracts,” he noted. “Our web presence is driving that work—our company name, our reputation and our repeat customers.
“Dennis and I complement each other well. We both do a little bit of everything, but he excels with customer service and has that human touch. I’m more of a computer and analytics guy. The most important thing for us is to preserve Chuck’s name, his reputation and his legacy.”
Salem, OR 503-585-8066
dablerautobody.com
Type: Collision Repair
Facility Employees: 21
In Business Since: 1967
Number of Locations: One
Production Space: 16,000 square feet
Industrial Finishes and Systems
800-531-1305
www.industrialfinishes.com
Facebook: @industrialfinishes
Twitter: @indfinishes
Instagram: @industrialfinishesandsystems
LinkedIn: @Industrial Finishes and Systems, Inc.
YouTube: @IndustrialFinishesTV
Since opening its doors 40 years ago, Osage Ambulances has been committed to producing the best value ambulances for customers. Based in Linn, MO, the company is a full-service custom ambulance manufacturer, offering Type I, II and III ambulances on-site, as well as remount and repair services.
Kenny Fick, plant manager, said the privately held business is dedicated to putting quality, employees and customers first.
“It has always been our goal to create high-quality custom ambulances for communities across America,” said Fick.
Established in 1983, the business started as a van conversion manufacturer that sold to dealerships in the central U.S. In 1985, it was asked to build an ambulance for the city of St. Louis, MO. The business built vans and ambulances for the next 16 years, until management decided to only focus on ambulances. Since then, it has worked with a network of dealers nationwide to help customers place orders.
Fick attributes the company’s success to its focus on employees.
“A lot of the other companies in our industry are looking at the bottom line more than anything,” he said.
Osage Ambulances takes a different approach and concentrates on keeping employees happy. As a result, the average tenure is about 20 years.
“From services and sales to design and detailing, the team has one common goal: 100% customer satisfaction,” Fick said.
When the company started, Fick said it was purchasing aluminum bodies from a company that was also painting them. In 2002, Osage Ambulances moved the painting operation in-house.
“We were spraying in a couple of manufactured booths that were plywood and lined with sheet metal,” he recalled. “It was pretty primitive at the time and they didn’t have much airflow.”
He realized they needed a spray booth that was bigger and better with good airflow.
After researching some options, Fick learned about KAYCO Spray Booths and found the product line offered a variety of spray booth configurations at
an affordable price. Soon after, Osage Ambulances made its first purchase.
“Probably the biggest asset with KAYCO is that they built the booth custom for us,” said Fick. “They met all of our needs and requirements.”
Since then, Osage Ambulances has purchased four additional booths through its dealer, Auto Body Color, in Saint Joseph, MO. The booths are 18 ft. wide, 32 ft. long and 15 ft. tall.
Over the years, Fick said his staff has found the booths reliable and easy to use.
“Except for occasionally changing the filters, the products are mostly maintenance-free,” said Fick. “The products are very good quality and KAYCO is a very easy company to work with.”
Similar to Osage Ambulances’s focus on paying close attention to customers’ needs, Fick has found KAYCO Spray Booths has a similar business outlook.
Started in 1978 by Bill and Kay Fowler, KAYCO Spray Booths is a family company, owned and operated by their son-in-law and daughter, Chuck and Carol Koenen
The company prides itself on manufacturing its products using high-quality materials and hardware. The KAYCO line of products offers a standard line of equipment, such as spray booth configurations, paint mixing rooms, limited finishing stations and accessories for automotive and industrial applications. This includes cross-drafts, down-drafts, filter booths and truck booths.
KAYCO also offers build-toorder products, which allows the company to determine the style
and size of booth that will fit the application best.
“If a customer had a product that is unique in size, we can build the booth to accommodate that,” said Chuck Koenen. “With Osage, for example, the ambulance bodies are a little larger than the typical automotive booth dimensions can fit and we were able to design and build the booth to those dimensions.”
The newest booth is a side exhaust down draft configuration. Osage’s building layout required the heater to be mounted behind the booth. Koenen said this flexibility made fitting the booth into the existing space possible.
As a production facility, Fick said Osage Ambulances probably sprays more paint in a day than a body shop will in a month because of the size of the ambulance bodies and many customers requesting striping on their custom ambulances. Typically, the booths are used four days a week, 10 hours a day.
“In that time period, just with the bodies that we’re painting, we’re running through probably 20 bodies a month,” said Fick.
He and his employees have been very impressed with the dependability of the spray booths, which has helped them stay on track with deliveries.
By working with a professional company like KAYCO Spray Booths, Fick said it enables Osage Ambulances to provide a highquality product to customers across the country that is second to none.
“In the process, we keep our dealers and customers happy, which sets us apart from our competitors,” he said.
Osage Ambulances
Linn, MO
573-897-3634
www.osageambulances.com
Company At A Glance...
Type: Ambulance Manufacturer
Facility Employees: 125
In Business Since: 1983
Number of Locations: One
Production Space: 110,000 square feet
The dependability of KAYCO spray booths has helped Osage Ambulances stay on track with deliveries.
KAYCO Spray Booths
800-529-2640
La Vernia, TX
kaycospraybooths.com
Facebook: @Kayco-Spray-Booths
Twitter: @KaycoSpray
Instagram: @kaycospraybooths
YouTube: www.youtube.com/
@kaycosprayboothsinc.8058
The KECO GPR system is not an add-on to a stud welding system it is a complete replacement for stud welding.
www.kecotabs.com
In the seven years since Kenny and Amanda Allen opened their Oklahoma City, OK, collision center, Allen Auto Body has become a go-to destination for customers seeking top-quality repair services. As a testament to their culture of excellence, the I-CAR Gold Classcertified shop offers a lifetime workmanship warranty, holds OEM certifications from Nissan, Infiniti, Hyundai, Kia, Chrysler, Jeep and Dodge, and has been named one of three best-rated body shops in the city.
“Amanda and I have been in the industry more than 30 years,” said Kenny, whose career as a painter was inspired by a high school shop class. “She started as a parts delivery driver and then managed an independent shop. We met at the Ford dealership where I was the shop manager and she was the estimator. Later on, I was a paint rep for DuPont. She was a field appraiser for an insurance company. Then came the opportunity to buy this shop. With her skills and my background, we make a good team.”
Kenny oversees the shop. Amanda serves as estimator and back office administrator. They employ two I-CAR-certified body techs and a painter. Their daughter Hope doubles as receptionist/ customer service rep and handles parts intake. The 9,250-squarefoot facility churns out 25 to 30 vehicles monthly. Most vehicles are less than seven years old.
From the get-go, they opted to work directly with consumers rather than through a direct repair program. “Our initial approach was to be a DRP, but the guidelines didn’t meet what we wanted to do as a business,” said Kenny Allen. “We saw a greater need to work directly for the customer, not the insurance companies. It’s paid off; most of the time we get our door rate.”
Their approach to training, technology and tooling has paid off as well. “We’ve always wanted to be the best shop in town and invest as much as we can to stay up to date,” said Allen.
Through participation in the Assured Performance network, the shop secured its OEM certifications and earned the Assured Performance Certified designation. To assure compliance with OEM repair guidelines, including calibrations, the team relies on ALLDATA and RepairLogic’s OEMspecific software procedures.
To sharpen skills, techs participate in off-site training. Both owners also attend managementtraining classes. To stay abreast of legislative and regulatory issues, Amanda serves on the board of the Oklahoma Auto Body Association (OKABA.)
Staying up to date also means having the latest in tool technology. Like many automotive techs, Allen is enamored of tools and gadgets to improve efficiency, workflow and profitability, which is why he firmly believes the KECO Glue Pull Repair System is an asset to his shop.
When using the GPR System, Allen noted a significant difference from invasive old-school repair techniques. “Not having to grind a panel and sand body filler is a benefit. Employees aren’t breathing in as many hazardous materials. Because we don’t grind off the paint, the factory corrosion protection isn’t compromised and, with less dust and cleanup, there’s a faster turnaround.
“Before KECO GPR,” he added, “it seemed faster to beat the panel, grind it off and put on body filler. At first there was a learning curve with the KECO system. But now,
it’s the first thing the techs turn to. Watching them use KECO GPR, I see new talents develop.
“With the paint still intact, they’re able to see whether the panel needs Glue Pull Repair or knock down. Once straightened, very little filler is needed. With GPR, they can work out the dent and make a less invasive repair. This has reduced our body filler and primer consumption, and the need to sometimes blend adjacent panels.”
KECO GPR has also created an opportunity to repair minor damages to an EV. “Before GPR, if an EV showed up, we couldn’t repair it,” said Allen. Noting the GPR system complies with OEM guidelines, he said “it has opened a door for us. If it’s a cosmetic repair to the sheet metal, we can repair it with the KECO system.”
Training also plays an essential role. “At Allen Auto Body, training through KECO is a must,” said Allen, whose shop is close to KECO headquarters. “I was able to attend one of the very first training classes. I was amazed and excited to see all the possibilities the new systems were going to offer, and I’m still amazed at the possibilities. KECO is constantly coming out with new ways to help the industry.
“To stay up to date, you must invest in your equipment, training and new technology. If you’re not using KECO GPR, you’re going to fall behind. It’s a faster turnaround, it reduces material costs, it keeps your shop cleaner and you make more money. It’s a win-win.”
Allen Auto Body
Oklahoma City, OK
405-948-1315
www.allenautobody.com
Company At A Glance...
Type: Collision Repair
Facility Employees: Five
In Business Since: 2016
Number of Locations: One
Production Space: 9,250 square feet
Repair technician Scott Burleson uses KECO’s K-Beam to reshape the wheel opening body line. Prior to using the KECO GPR system, the technician would use stud welders to pull the dents, which could compromise the factory corrosion protection, or drill the panel, which could affect the vehicle’s structural integrity.
KECO Body Repair Products
405-745-2145
Company Contact: Scott Stayton
www.kecotabs.com
Facebook: @KECOBodyRepairProducts
Twitter: @kecotabs
Instagram: @kecodentrepair
LinkedIn: @keco-body-repair-products
YouTube: @KECOBodyRepairProducts
Large, bright touchscreen for rapid navigation between functions. Designed and built by Opus IVS in the US
QuickADAS allows you to do your own calibrations right on the tool
We are the only company that makes OEM tools for dealerships and meets all OEM cer tification requirements for collision repair.
Hundreds to ASE Cer tified technicians to get the job done right. Programming, Scanning or you’re just stumped - we’ ll get the repair completed with you
Highly accurate aftermarket scans in 1-2 minutes, fastest in the industry
O’Hare Auto Body in Bensenville, IL, proudly boasts it has been the “premier auto body and service shop in the Chicagoland area” since it opened in 1985. Certified by a wide range of OEMs, including Ford, GM, Mercedes-Benz, Porsche, Lucid and Tesla, the busy shop repairs about 120 vehicles per month.
Lee Serling is O’Hare Auto Body’s lead ADAS/scan technician, joining in 2019, coming from a background in information technology.
Serling said he first learned about Opus IVS and its DriveSafe scan tool from a webinar in November 2020. The DriveSafe scan tool is the “one collision solution that does it all,” offering OEM and aftermarket scanning, ADAS calibration, programming and live expert support, all in one tool.
When management found out DriveSafe integrates with CCC Intelligent Solutions’ estimating software, which the shop was already using, they reached out to Opus IVS to set up a demonstration.
After a multi-day demonstration showing the capabilities of the tool, O’Hare Auto Body was sold, and the Opus IVS DriveSafe unit has been the shop’s primary OE scan tool since 2021.
Serling said using the DriveSafe tool has reduced the shop’s cycle times by helping the crew write accurate repair plans quickly and giving them instant access to highly-skilled remote experts when help is needed, which has all contributed to increased customer satisfaction.
“After doing the demo, I was most impressed with the level of support from the technicians on [Opus’s] staff,” Serling said. “I like to ask a lot of questions, almost to the point where it would make an ordinary technician on the other end of the line angry, but the Opus technicians happily address any questions or concerns that I might have about repairing the vehicle. They’re not just clearing codes.
“As far as extracting info from scan reports, before [with other scan tools], it was just ‘here’s the scan report, good luck,’” Serling said. “Now, Opus’ technicians can discuss over the phone what may
be related and how to address it, because they have years of experience.”
Serling said Opus IVS hires high-caliber technicians, and then is able to retain them.
“We’ve been working with the same [technicians] since we bought the Opus tool,” Serling said. “It seems like the people who work there like working there, because they’re not being pressured to just get [codes] cleared. They can focus on quality.”
As an example of the level of support O’Hare gets, Serling remembered when the shop was replacing a Land Rover’s blind spot module.
“Jaguar/Land Rover vehicles are finicky,” Serling said. “I was really impressed with the [Opus] tech’s foresight to make sure everything was correct before the scan. He noticed the battery voltage wasn’t right, so we got that adjusted, and got the module programmed.
“The [local Land Rover] dealer wouldn’t have been able to take it in for five days, so the customer got the car back a lot sooner,” Serling said.
“Programming modules is a big one,” Serling added. “The convenience factor is something that really sticks out, just with the volume [of vehicles we repair.]”
Serling said another selling point was that Opus IVS can do dynamic and static calibrations remotely for shops using DriveSafe, which can be a lifesaver. So many shops---O’Hare included--don’t always have the necessary space to properly complete them.
“The partnership with Opus helps to plan for each unique calibration and determine if we can do it onsite with Opus,” Serling said.
The feature that initially piqued the shop’s interest in Opus IVS—the integration with CCC estimating software—has also more than proven its value, Serling said.
“The scan report uploads immediately to CCC’s attachments, and CCC generates the invoice, so it makes our accounting staff happy,” Serling said. “It’s nice and seamless; we don’t have to go searching for something to download from a portal.” It also shows up for insurers as a verified scan.
Serling said he would recommend the Opus IVS DriveSafe scan tool to any shop that “takes scanning and calibrations seriously.”
“It’s a commitment,” he said. “You need somebody who will take the responsibility of extracting info and passing it along to the estimator or technician, because it will save you time and money in the long run. Even if you can’t do all the calibrations in house, it will help you plan for the ones that will need to be [sublet] after a repair.
“You can try to problem-solve with the [support] tech on other end, which means you will learn a lot and add to your knowledge base at the shop,” Serling added. “Taking advantage of all the resources available makes for a better experience for everyone.
“There’s peace of mind in having Opus as an option,” Serling said.
O’Hare Auto Body
Bensenville, IL
630-766-6668
ohareautobody.com
Company At A Glance...
Type: Collision Repair
Facility Employees: 30
In Business Since: 1985
Number of Locations: One
Production Space: 18,500 square feet
Opus IVS
877-945-6442
www.opusivs.com
7322 Newman Blvd., Bldg #3 Dexter, MI 48130
Facebook: @OpusIVS.US
LinkedIn: @opus-ivs
YouTube: @AutologicTV
Before Dave Niestroy opened 3D Auto Body in West Chester, PA, in 1981, he spent free time in high school doing repairs in his parents’ garage. Now, 3D Collision Centers spans three counties in southeastern Pennsylvania, with seven physical locations and one satellite location at a Subaru dealership.
Patrick McCready, operations manager, said 3D stayed at one location until the late ‘90s, and then began opening two at a time every few years until the most recent addition in 2017.
“Dave worked closely with insurance partners to find markets that needed a strong, DRP-friendly shop,” McCready said.
McCready said 3D Collision Centers has always believed in developing talent.
“We make a point to engage young people by promoting them from within and investing in them, whether it’s through education, special training or promotions,” he said. “Our greatest asset is our team members, and with today’s challenges, rather than placing ads and hiring people, I think it’s more important to make sure we’re paying a fair wage, that our relationships with insurance partners stay strong, and giving everyone a friendly, nice area to work, along with excellent benefits.”
McCready explained 3D Collision Centers’ success also comes from continual investment in new, updated technology. Since 2014, it has used PPG’s ENVIROBASE® High Performance waterborne system.
“We were transitioning from solvent to a water-based product to get ahead of regulations and be compliant,” he said. “So, from everything we looked into and tried, we felt that PPG Envirobase was by far the most superior waterbased product on the market from a production standpoint.”
McCready said 3D Collision Centers was also investing in OEM certifications at the time, so finding a paint distributor that aligned with this goal was crucial.
“Out of the competitors, we felt PPG had the best coverage as far as OEM certifications,” he explained.
In 2016, PPG also helped 3D Collision Centers build one of the
first fully-equipped Symach shops in the country.
“The technology started in Italy and it bakes a vehicle within minutes, as opposed to a traditional downdraft paint booth,” McCready explained. “It has helped us improve our cycle times and allows us to paint 15 to 20 cars a day.”
McCready said PPG provided “great support” when bringing Symach to the Conshohocken, PA, location.
“PPG saw the future in drying technology and sent chemists out in the first few months to adapt a clear coat that would pass United States drying regulations,” he said. “Now, that shop alone is 30,000 square feet, producing on average $800,000 to $1 million a month in gross sales.”
3D Collision Centers also recently started using the new PPG VISUALIZID ™ 3D color rendering software and DIGIMATCH™ spectrophotometer.
“The VisualizID 3D color rendering software is easy to use,” said Jake Vogel, painter. “All the jobs are signed ROs from the office; they could put the paint code in that software and it’s already on that job.”
Vogel said this goes hand in hand with the DigiMatch spectrophotometer.
“A painter, prepper or anybody can go out in the morning and take a spectro reading of every car in paint and assign it to that RO from the device itself,” he explained. “So, when you download the reading into the PaintManager XI software, it’s already all labeled in the ROs, and all you have to do is
click on it and go.”
Vogel said he appreciates how the RO shows the estimated material cost, so he knows where he wants to be as far as selecting the right amount of base or clear coat.
He said the new DigiMatch spectrophotometer works in conjunction with the VisualizID software, which “has a 3D visualizer that shows you a computergenerated spray out of your spectro reading compared to one from PPG themselves, so you see all angles before you go and do a spray out to guarantee the match.”
McCready added the new VisualizID technology shows how a color will flop with sunlight.
“If Jake is painting a bumper only, it gives him a visual,” McCready said. “It may not be the exact color on the screen, but rather than walking out with a paint swatch or a spray out, it’ll show him how this color will look under certain light to human eyes, which drastically reduces the struggle of matching paint in different lighting.”
McCready also explained how the PaintManagerXI software has developed to integrate with body shop management systems.
“The painter can see the amount written for materials when he starts to mix the color,” he said. “So, if there is a special toner required or anything along those lines, we will see the paint cost immediately, and we are able to supplement accordingly in real time.”
McCready concluded that 3D Collision Centers has noticed a more consistent gross profit thanks to the technology that PPG offers.
3D Collision Centers
West Chester, PA 610-692-7776
www.3Dbodyworks.com
Company At A Glance...
Type: Collision Repair
Facility Employees: 135
In Business Since: 1981
Number of Locations: Seven
Combined Production Space: 90,000 square feet
PPG
440-572-2800
rusnak@ppg.com
www.ppgrefinish.com
Facebook: @PPGRefinish
Twitter: @PPGRefinish_NA
Instagram: : @ppgrefinish
YouTube: PPG Refinish (USA/Canada)
SATA® RPS® Multi-purpose Cups save not only time, but paint and cleaning materials too.
The SATA RPS cups have a unique venting system that plays into the efficiency of the overall SATA system. The vents allow for an even flow rate through the cup—so, whether the cup is entirely full, half full, or just has a couple ounces in it, the flow rate will stay the same. The vented RPS cups allow for ALL of the paint and other materials to be sprayed from the cup, with a constant color match and film build. No costly ounces of left over unused material. Mix only what you need, and spray it to the last drop.
BENDABLE
RPS cups have a built-in flexibility of the cup lid “neck” which allows painters to tilt the cups forward or side to side to spray at many different angles, on parts, rocker panels, and bumper covers. This flexibility assists in making the RPS a great solution for more difficult paint jobs. Excluding the 0.3 L minijet version.
With SATA RPS, removing the cup from the spray gun becomes a clean and safe process. When the paint job is finished, squeeze the RPS cup and close the vent cap on the bottom of the cup to create a vacuum inside. Now turn the spray gun upside down and pull the trigger to empty the material passage ensuring easy gun cleaning and a tidy workplace.
The exclusive independent distributor of SATA products in the US and Puerto Rico
#03
Occasionally during the paint process the material cup may accidentally knock into the vehicle or panel stand. Due to the robust threaded connection between the cup and the lid, any chance of the cup becoming detached is avoided, as is the chance to spill paint.
Refilling paint during the application process is sometimes necessary. The design of the cup allows the simple and clean topping off and the easy exchange of the material filter, if required.
Phone: 800-533-8016 www.satausa.com
E-mail: satajet@satausa.com
SATA, SATAjet and/or other SATA products referenced herein are either registered trademarks or trademarks of SATA GmbH & Co. KG in the U.S. and/or other countries.
As JD Burdge of Springfield, TN, watched his shop burn to the ground Jan. 9, 2020, he knew he was going to lose everything.
After 25 years of business in Springfield and decades of accumulating tools and equipment, the collision shop represented a lifetime of hard work. To Burdge, B&J Automotive & Collision was his means of both making a living and serving his community.
The scariest part of watching his shop burn was knowing insurance would not be able to cover the loss. He had let the insurance briefly lapse to help a family member pay for urgently needed medical care.
Cars are a lifelong passion for Burdge, and he has been working on them since he was 9 years old, growing up on a farm in New Jersey. He later built a business there but moved to Springfield in 1995, when his hometown started feeling too crowded for him.
Burdge has been an active member of the Springfield community from the day he opened up shop there.
“I love my customers,” Burdge said. “Of course, you’ve got to make money. But there are a lot of people out there that have gone through hardships and need help. And if they don’t have the money, well, we’ll work on that. You’ve got to have a vehicle to go back and forth to work, right?”
All told, after 25 years in business, the fire destroyed about $650,000 in tools and $300,000 of equipment, not to mention the loss of the building. Looking at the ruins, Burdge didn’t know if he’d be able to build back.
But the people around him weren’t going to let him down. Burdge had always been known as the first in line to give and, while it was hard for him to make the shift, his pastor helped bring him to the point where he could receive.
The community organized a GoFundMe, and a business down the road opened its doors to him
so he could get back to work as quickly as possible. Single Source Paint generously donated paint and equipment, and another business donated a spray booth.
“So I said, ‘Great. All right, now what do I do? I’ve got body work coming in and I’ve got no paint guns,’” said Burdge.
Burdge started painting with a SATAjet 90 in the 1980s and was devoted to SATA products. He got in touch with the company directly and, after hearing his story, SATA’s importer, Dan-Am Company, immediately sent him a gun and a cabinet so he could start working again.
Burdge said SATA quality is very valuable to him.
“SATA is unsurpassable,” says Burdge. “Not only are the guns quieter, they work on less pressure, and they’re designed for superior spray. They put product on the vehicle, not in the air. They just break the paint up professionally and lay it down. I’ve sprayed with a lot of guns, but there’s really only one top gun. And that’s SATA.”
He sees investing in SATA equipment as a cost- and timesaving measure in the long run.
“Look, you’re going to pay more for SATA. But you’re not paying for a name,” Burdge said. “You’re paying for years of experimentation and it shows when you pick up the guns. It’s unbelievable. The balance, the light weight, the way they atomize
upside down. What takes a quart of paint to do with some guns, SATA will do with half a quart. So there’s time and material savings there. And they’re constantly improving.”
Burdge has received ongoing support from SATA, and over the last three years, he has built up a full line of guns. On top of that, he has built a relationship with his SATA rep that continues to this day.
“I can call him up now if I’m having a problem, and he’s right there on the phone to help,” Burdge said. “The support is always there, and if I needed anything to this day, I could call him.”
Burdge is working out of his own shop again, thanks to the generosity of local businessman Mac Baggett, who rented out a warehouse to him on condition that he pay back the rent after his first year in business.
“Without SATA and so many others, I could not have done it,” Burdge said. “Talk about community service or good faith in the industry—to help a man that’s gone through a tragedy.”
Burdge’s customers continue to come back to B&J Automotive, and he is deeply grateful for the opportunity to be working in his own shop and able to give back to his community.
“You know, I’m not out yet,” said Burdge. “But I’ll tell you this. I’m turning dollars. I’m able to take care of people. God has been good.”
B&J Automotive & Collision
Springfield, TN
615-382-9990
Type: Collision Repair
Facility Employees: Three
In Business Since: 1995
Number of Locations: One
Combined Production Space: 6,000 square feet
Dan-Am Company
800-533-8016
www.satausa.com
PO Box 46
Spring Valley, MN 55975
Facebook: @SATA by DanAm Company
Twitter: @SATA_DanAm
Instagram: @sata_by_dan_am
LinkedIn: Dan-Am Company/ SATA Spray Equipment
With an avid interest in cars, Shannon Christian started in the automotive industry in 1992, when he began working at a GM dealership in Brainerd, MN. Christian was finishing a two-year degree at the tech college and employed at another shop when the dealership recruited him. Four years later, he opened his own shop, Shannon’s Auto Body, five miles out of town in a 2,000-square-foot horse barn in his backyard. The shop specialized in restoration and collision repair. As business grew, Christian realized the need for space and ultimately added a second and third garage on the same property.
In addition to operating his original 17,000-square-foot facility, Christian opened a second location in July 2023, about five miles from the shop. The 40,000-squarefoot facility has better visibility and a layout designed to better accommodate collision repairs.
Christian and his team pride themselves on providing outstanding customer care and quality repairs in the Brainerd Lakes area in Minnesota. The business services nearly every make and model.
“We utilize the latest repair technology and are committed to fixing vehicles safely and correctly to their pre-collision condition,” said Christian. “We want to put customers back on the road in a safe vehicle.”
Vehicles often come in that have been previously repaired incorrectly at other facilities. Christian and his team do post-collision inspections and fully blueprint the car to write a complete repair plan per OEM requirements and determine the calibrations required.
Christian said they are proud to be an I-CAR Gold Class shop and active members of the Society of Collision Repair Specialists (SCRS) and the Alliance of Automotive Service Providers of Minnesota (AASP-MN). As an AASP-MN board member, Christian is dedicated to improving the industry and educating other shops.
Educating employees is also a priority. “We are constantly training staff and updating our procedures to keep up with industry changes,” said Christian. Several of the Shannon’s Auto Body staff are I-CAR Platinum and ASE-certified technicians.
The education process includes bringing estimators and technicians to the SEMA Show in Las Vegas, NV, to learn new repair methods and see the latest equipment and tooling.
About six years ago, Christian was looking for a paint booth to purchase while attending SEMA.
“I just fell in love with Spanesi’s full glass doors and touch panels,” he said. “It was like comparing a Ferrari to a Ford.”
Christian was drawn to Spanesi’s high-quality Italian products.
“It set them apart from everybody else,” he said.
As part of a performance group Christian belongs to through the company’s paint manufacturer, he toured other shops and noticed they used the Spanesi Touch. After testing it, he realized how quick and easy it was to set up and do the measurements.
“That really interested me,” he said. At the 2019 SEMA Show, the team looked at frame equipment and priced out a Multi-Bench and a Touch Measuring System. While attending a team bonding experience, Christian discovered they had won the Spanesi Touch as part of an SCRS contest the equipment provider was holding. In 2022, the shop won the contest again and received a Spanesi Q5.2 welder.
Christian was impressed with Spanesi’s 360-Degree Concept, which includes all equipment needed to outfit a body shop for a complete repair. This consists of a spray booth, measuring system, pulling benches, welders, vacuums and sanders.
With the addition of a second shop, Christian worked with Tim Morgan, Spanesi Americas’ COO, and the Spanesi team to lay out the shop most effectively. Morgan visited multiple times to ensure
everything was set up correctly and working properly.
Since then, the shop purchased an additional Spanesi Touch, six Multi-Benches, a double and single spray booth and a welder for the new location.
Christian said the equipment has provided the business versatility, which has helped with shop flow and efficiency so vehicles are delivered on time.
“Spanesi equipment is state-ofthe-art,” he said. “The Multi-Benches are very versatile, the spray booths are large, utilize a side load track system and full glass doors, have excellent lighting and airflow is as good as it gets. The mix room was custom-built with full glass windows, tiled floor and cabinets. It is a painter’s dream to work with this equipment.”
Christian is impressed with the training and support his team has received. In addition to Spanesi’s inshop training, technicians travel to Chicago, IL, for classes.
Having modern, up-to-date equipment has helped when hiring new technicians.
“Any technician who comes in and sees the equipment wants to work here,” said Christian. “We’ve never had such a high volume of employees to pick from just by having the Spanesi equipment.”
Christian said many shops have been repairing vehicles the same way for 30 years and don’t realize the importance of staying current with the changes on cars.
“We always hear about ‘industry standard,’” he said. “We want to set the bar and show the industry what the standard should be.”
A key element is researching OEM repair procedures and having dependable equipment, such as Spanesi’s.
Shannon’s Auto Body
Brainerd, MN
218-829-6764
shannonsautobody.com
Company At A Glance...
Type: Collision Repair
Facility Employees: 43
In Business Since: 1996
Number of Locations: Two
Combined Production Space: 57,000 square feet
Spanesi equipment has helped Shannon’s Auto Body with shop flow and efficiency, so vehicles are delivered on time.
Spanesi Americas Inc.
224-SPANESI (224-772-6374)
www.spanesi.us
Facebook: @spanesiamericas
Twitter: @spanesiamericas
Instagram: @spanesiamericas
LinkedIn: @spanesi-americas
YouTube: @spanesiamericas_official
Robert Lloyd Sr. founded Lloyd’s Collision & Paint Center in Santee, CA, in 1984. Since then, he and his sons, Robert Jr. and Michael, have built the business into one renowned for providing reliable, quality collision repair services. In 2012, the family opened a second location in Lakeside, CA, which has since undergone an expansion.
Robert Jr. worked in his dad’s shop throughout high school, on summer breaks and then as part of a work study program his senior year, sweeping floors and cleaning cars, eventually moving up to helping the auto body technicians. After graduating, he started working full time on body work. He and Michael, who gravitated toward the painting side of the operation, now manage production and quality.
Today, the family-run shop’s two I-CAR Gold Class locations repair about 200 vehicles per month. Lloyd’s Collision & Paint Center also has earned several OEM certifications, including Ford, GM, Tesla and Fisker—a newcomer to the U.S. market that just delivered its first two all-electric SUVs to customers in California earlier in 2023.
With so many vehicles coming through, Robert Jr. said Lloyd’s has tried just about every platform available to look up OEM repair procedures, including the OEMs’ websites.
“One thing they had in common is they’re all very difficult to navigate,” Robert Jr. said. “They use different terminology for different makes and models. It makes it hard to train, hard for techs to understand how to read them if every manufacturer uses different terms, diagrams and processes for looking them up.”
Several years ago, Lloyd’s found the exception to that rule— SUN Collision Repair Information.
“We got an opportunity to demo SUN Collision, and the one thing we love about it is it’s very user friendly,” Robert Jr. said.
“SUN Collision gives you the ability to input basic keywords and generates the [repair] information based on that almost instantly— there’s no searching, digging for the information,” he added.
“If you’re looking up quarter panel procedures, just put in the VIN or license plate number of the car, put in ‘quarter panel,’ and it’ll populate all the options for the quarter panel, whether you’re replacing it or repairing it,” Robert Jr. said. “So, you’ll be able to find that really quick, print it, email it, whatever you need to do.”
The repair information is webbased so the shops’ technicians all have access on their laptops.
“Instead of having to print everything out, we just tell them what they need to research,” Robert Jr. said. “It saves a ton of time in the research process.”
SUN Collision software provides answers for every type of repair, from ADAS diagnostics and recalibration to diagnostic trouble codes and technical service bulletin issues related to a vehicle.
Robert Jr. said all of that information helps his staff write complete estimates the first time, with all the documentation needed to prove to insurance companies that every line item is required to complete the repair properly.
“That’s saving us a ton of time, and creating revenue in return, as far as getting paid to perform all the necessary procedures,” he said. “We were getting this information [before] from other avenues, but it was frustrating. This has made it very simple.”
The shops’ crew looks up repair procedures before every single job, Robert Jr. said.
“Knowing we’re getting the most current information to do the repairs makes us feel like we’re
doing the correct repair every time,” he said.
That also gives customers peace of mind.
“Obviously, every customer values their vehicle, and when they’re in a collision, they’re not happy,” Robert Jr. said. “So when we’re able to explain to them that we’re fixing the car to OEM standards and doing everything we can to get it back to pre-accident condition, that definitely makes them feel better about the repair process.”
Most recently Lloyd’s also helped SUN Collision test and develop a newly launched Repair Package feature that streamlines the blueprinting process for his estimate writers. The feature produces a comprehensive repair package that includes all the relevant information about a job—including repair procedures, illustrations along with OEM part numbers—and maps the data to the shop’s estimating platform.
Robert Jr. also praised SUN Collision’s wiring diagrams that help his techs diagnose electrical problems—as well as reset procedures for systems like tire pressure monitors, and suggested fixes for a particular vehicle’s known common issues.
“We could talk about [SUN Collision] for another few hours,” he said.
SUN Collision is a member of Snap-on’s Total Shop Solutions, which also includes sister brands Mitchell 1, John Bean®, Car-OLiner® and Hofmann® products. To request a free demo, please visit suncollision.com.
Santee, CA
619-448-8768
www.lloydscollision.com
Company At A Glance...
Type: Collision Repair
Facility Employees: 40
In Business Since: 1984
Number of Locations: Two
Combined Production Space: 75,000 square feet
SUN Collision
877-840-1973
info@SUNCollision.com
suncollision.com
Facebook: @SUNCollisionRepairInformation
Twitter: @SUN_Collision
Instagram: @suncollisionrepairinformation
YouTube: @suncollision3830
Edwards Collision Studios in Rocklin, CA, was established in 2014 as a Porsche restoration shop by father and sons Dave, Cole and Joe Wolcik, who chose to name it after their shared fifth-generation middle name.
“No one can pronounce Wolcik,” Joe said with a laugh.
“We had a passion for Porsche,” Joe said of the reason the family started the Porsche restoration shop. “We still do. We have a clientele that we’ve built based on friendships and cars. We go to local Porsche shows, and it’s kind of a network of Porsche people.”
Several of the Porsches that came into the shop had minor collision damage. Due to their extensive experience in the automotive repair industry—Dave has 40 years, Joe has 20 and Cole has experience as a paint technician representative—the Wolciks already had relationships with insurance companies and dealerships, so they started taking on claims.
Today, Edwards Collision Studios repairs about 55 vehicles per month, with a crew of ASEand I-CAR-certified technicians, offering complete collision repair. The family-run business—which also includes sister Crystal, the CFO—recently leased a neighboring building to double production space, so they could break down the repair process into separate departments: disassembly, structural, paint and reassembly, making it possible to fine tune the quality in each department and place technicians in the departments where they shine best.
Joe said though the shop repairs all makes and models, it tends to attract owners of high-end luxury cars—Porsches still make up about half of the shop’s repairs.
“Our slogan is ‘perfecting the art of collision repair,’ because that’s the way we look at it; we think of vehicles as works of art,” Joe said. “We came up with ‘studio’ in the name because our European-style workshop tailors every customer’s requests to their repair needs. One customer is adamant about OEM parts while another is completely
adamant about metal finishing and no fillers, another about the color match with no blending to keep thickness consistent with the rest of the vehicle. We tend to take our time and tailor the repair process.”
To achieve the results demanded by their clientele, the Wolciks looked for the best paint booth they could find, ultimately investing in a USI Italia Chronotech booth, installed in May.
“We had three booth companies in here, what we thought were the top three, and USI outshined all the others,” Joe said.
Joe said he was most impressed by the USI Italia booth’s electronic control management system.
“We were impressed with how it tracks repair orders, the efficiency and heat control,” Joe said. “We’re able to look at all that and fine tune it to what we need.”
Many of the cars that come to Edwards Collision Studios are exotic, made of different materials like carbon fiber, with an array of different composites requiring specific heat cycles.
“We are able to fine tune these heat cycles to the manufacturer recommendations,” Joe said. “For example, Ferrari wants its cars baked at 100 degrees, because it doesn’t want the resins to release on its parts.”
Joe said the booth also heats up quickly. “We’re also able to ramp it up to 202 degrees in three minutes, which has improved cycle time in the paint department tremendously, double to be
exact,” he said. “That allows us to grow in other departments because we no longer have a bottleneck in the paint shop.”
The USI Italia booth allows the shop to duplicate factory texture, Joe said, which also helps cycle time because the painter doesn’t have to try to do so in the polishing stage.
In addition, the booth’s filtration system “is amazing,” Joe said. “It’s moving 20,500 CFM of filtered air and any dirt that does somehow get through is so microscopic, it takes little time or effort to sand it out.”
All of this adds up to returning pristine cars to customers faster than ever.
“Customers like having their vehicles back quicker,” Joe said. “What used to take three days, we’re doing in one day now.”
Joe praised his booth’s installer, CleanRoom Paint Shop. “They came out for the demo, training and tech support,” he said. “They were here once a week after the initial install helping us fine tune this thing, which is impressive service.”
Joe said over the years, he has learned no matter what goals a customer has for their car’s repair outcome, they all have one expectation in common---for the car to look like it was never repaired in the first place. The USI Italia booth absolutely helps Edwards Collision Studios achieve that every time.
“We focus on the quality of the repair over price, timelines or anything else,” he said.
Edwards Collision Studios
Rocklin, CA
916-899-7661
edwardscollisionstudios.com
Company At A Glance...
Type: Collision Repair
Facility Employees: 12
In Business Since: 2014
Number of Locations: One
Production Space: 9,600 square feet
USI of North America
201-405-7760
Company Contact: Stefano Moretto s.moretto@usius.com www.usius.com
Facebook: @USI-of-North-America
Instagram: @usi_refinish