
9 minute read
Audi Wholesale Parts Dealers
Though the California Bureau of Automotive Repair (BAR) www. bar.ca.gov does not have jurisdiction over auto body shops beyond the more than 4,000 in the Golden State, some information shared by BAR Chief Patrick Dorais in a recent webinar could be instructive to shops elsewhere as well.
Dorais said his agency, which also oversees about 31,000 dealerships, mechanical shops and smog check stations, receives about 17,000 consumer complaints a year―though not surprisingly, many fewer this past year during the pandemic. Generally only about 1,000 of those involve body shops, Dorais said.
Advertisement
“In about a third of those complaints in the auto body area, consumers are alleging either that the shop made false or misleading statements, or they failed to obtain the customer’s authorization,” he said. “Consumers are commonly reporting to us that they feel misled about the length of time for the repairs, and not having any understanding of what was being done to their vehicles. Those are the kinds of things we commonly see in our complaints.”
Though few states have a regulatory body like the BAR overseeing the industry, most have consumer protection laws requiring customer authorization for repairs, so ensuring such authorizations are well documented could reduce―or at least counter― many consumer complaints.
The BAR’s “Write It Right” guide (https://www.bar.ca.gov/pdf/ WriteItRight.pdf) for shops was updated two years ago to indicate electronic authorization is permitted, even offering a screenshot of what a text authorization should look like.
Status updates sent to customers via email or text can also provide good documentation―provided they are saved by the shop―to counter many consumer complaints.
“We may come to you, saying the customer is saying this, here’s what they’re alleging,” Dorais said during the webinar. “As a shop owner or manager, you can say, ‘No, we’ve got something that tells a different story, and here’s my proof.’ That’s really important to preserve that document.”
Those outside California might also take note of the BAR’s prohibition on page 7 of the “Write It Right” document on the use of such part descriptions.
“Each new replacement crash part listed in an autobody or collision repair estimate must be an OEM crash part unless specifically identified as a non-OEM aftermarket crash part,” the document dictates. “Descriptors like Opt-OEM, Alt-OEM, OEM-Surplus, Like Kind Quality, Quality Replacement Part and similar designations do not satisfy this requirement.”
The ambiguity of those parts descriptions are something a Collision Industry Conference (CIC) committee has been working to address. During CIC in mid-2020, the committee showed how the list of parts categories varies among parts platforms and estimating systems. The committee showed several flowcharts demonstrating how all these variations in parts categories can result in the exact same part being described two different ways on estimates.
In one example, a vendor selling OEM parts outside of the authorized OEM channel enters those parts into a platform that uses the “OEM Surplus” category for such parts. That platform feeds into an estimating system that uses the “Optional OEM” label for those parts. That runs up against the BAR’s prohibition on the use of the “Opt-OEM” label.
“So while that part can go into the estimating platform as ‘OptOEM,’ the end-user is required to choose what they are going to call it on the estimate,” said Aaron Schulenburg of the Society of Collision Repair Specialists, who co-chairs the CIC committee. “You then have a situation where a shop repair plan, and an insurance company estimate, may each potentially choose different nomenclature for the exact same part. One may identify that as an aftermarket part, and one may identify it as an OEM part, and you have an estimating platform that allows for that choice.”
Order Audi Genuine Parts from these select dealers.

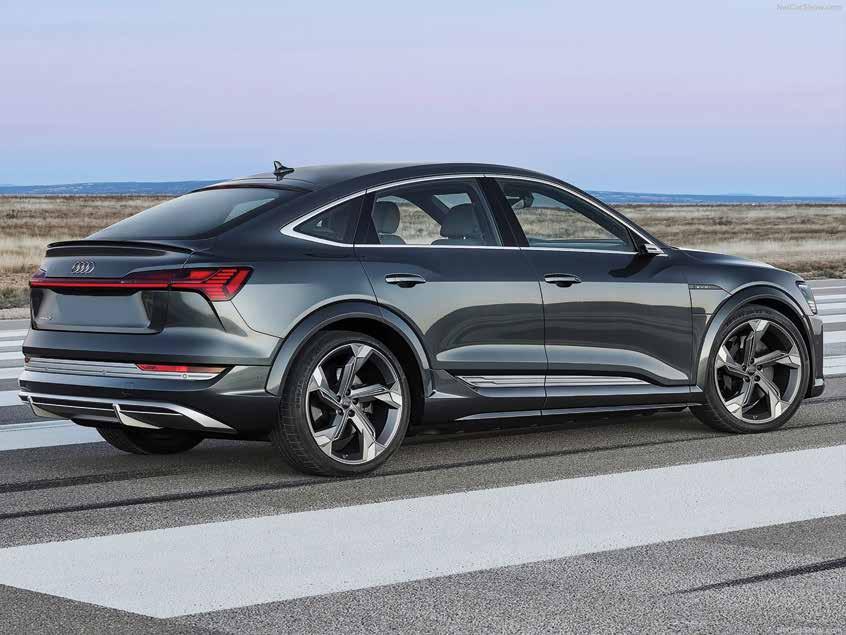
Audi dealers strive to make you an Audi Genuine Parts fan. ILLINOIS Audi Exchange
Highland Park 847.432.5880 847.432.5708 Fax gorejel@audiexchange.com
MISSOURI Kansas City Audi
Kansas City 866.949.9500 Toll Free 816.941.4969 Direct 816.942.3156 Fax M-F 7am-6pm Sat 8am-5pm cfowles@molleaudi.com
WISCONSIN Audi Milwaukee
West Allis 414.543.3000 414.543.5150 Fax M-F 7:30am-5:30pm parts@iamilwaukee.com
Audi North Shore
Brown Deer 414.371.2277 414.355.9815 Fax M-F 7:30am-5:30pm rfritsch@audinorthshore.com
Regardless of the age of your customer’s Audi, Audi dealers have access to over 200,000 part numbers and are supported by a nationwide network of distribution centers to help ensure non-stocked parts are delivered the next day.
On March 25, the Tennessee Collision Repairers Association (TCRA) hosted an evening of training, featuring Lee Rush from Sherwin-Williams, who explained “Why Ignoring Quality Control Will Cost You Profits and Sales.”
Rush promised to deliver an informative presentation on quality control as well as a demonstration of a new QC product.
TCRA President JMark Smith welcomed attendees from the Carolinas Collision Association (CCA) and the Mississippi Collision Repair Association (MSCRA), and noted, “QC is an important part of our business, and as a member of TCRA, quality repairs are something we place a lot of emphasis on because we want repairs done correctly.”
Beginning by sharing some details about his background and experience, predominantly as part of an operations team, Rush offered insight into how to implement processes in multiple locations with multiple variations.
“Over the years, in-process quality validation proved to be challenging,” Rush said. “The industry needs methods and procedures to evaluate quality throughout the process instead of figuring out what needs to be reworked once the repair is completed, or worse―having the consumer find the quality issues!”
After chasing a better method for quality validation and verification for years, Rush joined Sherwin-Williams, where he works with shops on developing and improving the business model, allowing him to educate those shops on why ignoring QC and technology costs profits and sales.
His goal for the presentation was to provide enough insight to begin to change the shops think about quality validation.
“The first part of this is just changing how we think and beginning to move away from tradition into a new business model,” he said.
“Technology is our friend when it comes to quality validation,” Rush continued. “The industry is finally catching up with regards to applications that improve our ability to better manage, lifting the burden and allowing us to focus ON business instead of being crazy IN the business.”
While the industry has long known there is a need to validate quality, the real challenge has always been determining how to do it.
“We need to validate quality prior to the consumer validating it,” Rush stressed. “Over the years, we’ve tried many methods with limited―or no―success, but QC validation continues to be a universal challenge for
the collision industry. This industry is a high variation business model, and all that complexity from vehicle to vehicle adds complexity.
“Quality is a pain point on every production floor, plus it presents a huge liability risk that won’t be defendable with a pencil and paper checklist going forward.”
Rush also addressed how quality issues cost every shop profits and sales, both in materials costs related
to reworks as well as by preventing the shop from creating new revenue.
“We’ve grown tolerant to this disruption in production, and we need to focus now on improving our labor utilization,” he said.
Shops face increased liability and risk due to vehicle complexity and required repair methods related to ADAS, complex steels, aluminum, carbon fiber, electronic components and new bonding technologies.
“These increase our liability and risk, which is getting steeper and steeper for collision operators every day,” Rush said. “Change is constant; make sure quality is constant, too.”
The need for in-process QC validation is even greater due to insurer demands related to DRP service level agreements, including varying insurer needs, virtual claims, approval process, inconsistent appraisals, customer handling process, parts usage and authorizations, and supplement authorizations.
“The market hadn’t produced any real technology to help and assist shops as they verify quality with their techs. It’s contingent on us to remind people and ensure we remain compliant from program to program,” Rush said. “Now, there’s technology to assist us with this, and it can easily be managed through a phone application to ensure each claim is handled according to that carrier’s expectations and requirements.”
QC validation is also a relevant component of customer satisfaction, and citing a study that showed 82% of consumers are less likely to use a business after seeing a negative review, Rush identified causes of those: missed delivery times, defects on delivered vehicles and poor internal communication.
“Our current internal communication method is ‘stop and tell someone,’ but that’s disruptive because it negatively impacts labor utiliza-
tion,” Rush pointed out. “It’s a bad system, but we’re going to rectify that with technology and in-house quality validation.”
Poor quality costs shops in reworks, increased cycle time, wasted production time, inefficient communication processes and recurring unaddressed issues with parts, equipment or skills.
“It’s cumulative, so we’re all desensitized to it. But we have to take care of it. The reality is when we stop, reverse or rework, cumulatively, this replaces a lot of potential labor we could have produced and sales that could have followed,” Rush said. “If you calculate it, you’ll be shocked at the amount of profit, cost and sales impacts.”
Traditionally, shops perform QC during a visual post-repair inspection, but the only items that can be seen post-repair are fit, function and finish.
“Post-repair inspections don’t tell us about the unibody or frame, if the suspension measurements are within tolerance or if the structural components are welded correctly,” Rush noted. “There’s no validity with a paper checklist, and no method to recall or review the data. There are a lot of challenges with the traditional QC methodology, and the industry has a real need for a consistent QC validation method.”
The average collision repair requires a 20-step process, according to Rush, as well as an average of 75 individual operations, 23.6 labor hours and 10 new parts replaced.
“Vehicle damage repair is a highly variable practice; I believe the automotive industry has the highest degree of variability in any industry,” Rush said. “The average vehicle will go through five different practice repair phases, and eight to 10 individuals can be a part of each repair order. Given the massive amount of variation, a paper and pencil checklist does not meet the need of today’s repair cycle complexities; it demands a better solution.”
Rush suggests a method that uses quality validation technology to ensure shops are verifying and validating quality as the vehicle cycles through the repair process.
He believes the industry needs a “digital tool, designed to be used with any tablet or handheld that doesn’t require special purchases. It should use imported repair order data, identify non-compliance using photo triggers and enhance communication, while also providing fully customizable, dynamic SOPs.
“It must allow us to inspect quality in-process regardless of the vehicle, the insurer, the OE requirement and the number of handoffs, or why use the application?”
Sherwin-Williams developed the Collision Core Quality application to meet these needs.
“Conducting in-process quality
On March 25, the Tennessee Collision Repairers Association (TCRA) hosted an evening of training, focused on QC validation methods