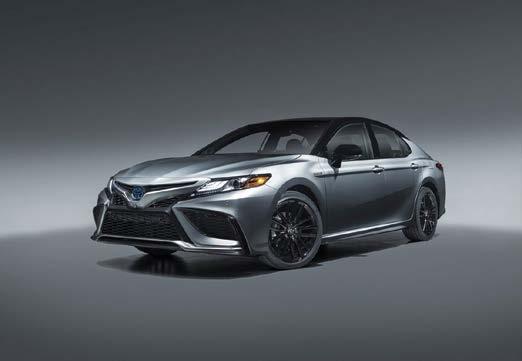
9 minute read
Toyota Wholesale Parts Dealers�����������������������
Axalta Coating Systems, a leading global supplier of liquid and powder coatings, on Aug. 30 announced Mark Garrett has stepped down as a member and chair of its Board of Directors, effective Aug. 26, due to his increasing professional commitments in Europe.
The board has appointed William M. Cook as its new chair, effective upon Garrett’s resignation.
Advertisement
Cook joined Axalta’s board in 2019. He previously served as executive chairman of Donaldson Company, Inc. until 2016, and prior to that served as chairman, CEO and president of Donaldson for more than 10 years. During his 35-year career at Donaldson, Cook held various roles of increasing responsibility, including senior vice president, international, CFO and senior vice president, commercial and industrial. Cook also brings to the board strong public company board experience.
Source: Axalta Plaintiffs in the Takata Airbag Product Liability Multidistrict Litigation on Sept. 1 filed a class action settlement agreement resolving claims against Volkswagen Group of America, Inc. and Audi of America, LLC, and its affiliates that will accelerate the removal of dangerous airbag inflators from approximately 1.35 million affected vehicles while also compensating consumers for their economic losses.
The proposed $42 million settlement will provide numerous benefits to current and former owners and lessees of the affected vehicles, similar to agreements previously announced with Toyota, BMW, Mazda, Subaru, Nissan, Honda and Ford. The agreement was filed in the U.S. District Court for the Southern District of Florida, Miami Division, as part of the multidistrict litigation being overseen by Judge Federico A. Moreno.
“We are pleased that after three years of hard-fought litigation we have reached a settlement with Volkswagen that will bring significant monetary and other relief to more than a million class members,” said Peter Prieto, court-appointed plaintiffs’ chair lead counsel, who, along with other members of the plaintiffs’ leadership, negotiated the settlement on behalf of consumers. “This agreement will not only expand awareness of the Takata recalls and improve driver safety by accelerating the removal of defective airbags from our roads, but will provide compensation to affected VW and Audi consumers,” Prieto said. “We will continue to vigorously prosecute our claims against Mercedes Benz, General Motors and FCA to ensure that our clients obtain the relief they deserve.”
Among the benefits provided for in the settlement is an outreach program overseen by an independent settlement special administrator that enhances and expands upon VW’s and Audi’s outreach efforts to significantly increase recall remedy completion rates. The program will regularly contact class members through direct mail, phone calls, email, internet ads and social media to educate them about the settlement and incentivize them to receive the recall remedy and exercise their rights under the settlement agreement.
The settlement also provides compensation to class members for their economic losses resulting from the recall in the form of reimbursement for reasonable out-of-pocket expenses, a possible residual distribution payment of up to $500, requirements to provide rental cars to class members while they wait for their recall remedies and the provision of a customer support program for repairs and adjustments on the replacement inflators, including an extended warranty.
This settlement is subject to court approval. If preliminary approval is granted, class members will receive more information about the terms of the settlement. The benefits of the Enhanced Rental Car Loaner Program will be provided no later than the date of preliminary approval.
When and if the court grants final approval, the claims process will open to eligible class members pending any appeals that are filed. Personal injury claims related to the Takata Airbag Litigation are not covered by this settlement.
Source: Schwartz Media Strate-
gies
Do it Do it Right!Right! Use Use
These Dealers are Genuine Wholesale Parts Specialists.
Colorado Stevinson Toyota East
AURORA 800-332-5877 303-341-2396
303-360-7881 Fax
M-F 7-6; Sat 8-5 bhimelstieb@stevinsonauto�com
Louisiana Price LeBlanc Toyota
BATON ROUGE 800-960-1157
225-408-1249 Fax
Texas Sterling McCall Toyota
HOUSTON 800-231-1440
713-270-3942 Fax
M-F 7am-7pm; Sat 7am-4pm
Toyota of Laredo
LAREDO 888-818-5176
956-718-4259 Fax
M-F 7:30am-6pm; Sat 8:30am-5pm www�toyotaoflaredo�com
Vic Vaughan Toyota of Boerne
BOERNE 210-870-1809
210-870-1802 Fax
M-F 7am-7pm; Sat 7am-5pm tobparts@toyotaofboerne�com
Since the early 20th century, steel has been the material of choice by auto manufacturers worldwide. Almost every vehicle model has been designed using steel due to its strength, cost-effectiveness, workability and availability.
“Automakers are now moving away from the use of mild steel, which was a core substrate used for automotive construction for a long time,” said Ryan Mandell, director, Claims Performance, Auto Physical Damage Solutions for Mitchell International.
Instead, OEMs are increasingly using lightweight materials such as aluminum, high-strength steel, ultra-high-strength steel and plastic.
Mandell has worked in a variety of industry segments over his career. He joined Progressive Insurance as an adjuster after graduating college in 2004 and then worked for a medium-size MSO, Precision Collision Auto Body, based in Washington. Before he was hired by Mitchell in 2017, he was in charge of five wrecking facilities owned by B&R Auto Wrecking in the northwest for four years.
Autobody News talked to Mandell about the use of lightweight materials in current and future model vehicles and how this shift will impact collision repairers.
Q: Why are automakers moving away from the use of mild steel and using lightweight materials?
A: Manufacturers are moving away from the use of mild steel for a couple of reasons. First, they want to improve fuel economy in response to the National Highway Traffic Safety Administration (NHTSA)’s Corporate Average Fuel Economy (CAFE) standards, which regulate how far vehicles must travel on a gallon of fuel. The current requirement is for automakers to raise the average fuel efficiency of new cars and trucks to 54.5 miles per gallon by 2025.
With an increased focus on manufacturing electric and hybrid vehicles, lightweight materials are being used to offset the weight of the batteries. Many people believe electric cars are lightweight because they don’t have an engine, but lithium-ion batteries are really heavy.
According to a study conducted by a global transportation company named Kar-Tainer, the company found that if you look at the average weight of an internal combustion vehicle versus an electric one, the electric vehicle on average was a little over 400 pounds heavier.
Lithium-ion batteries have a low energy density ratio. In order to produce the kind of range and performance and be competitive in the market, you have to have a large battery. Until we get to the point
where we’re using solid-state battery technology with a higher energy density, this will be the case for some time.
The shift away from steel is also about improving crashworthiness. A university study compared structural aluminum to mild steel, which has been used in structural applications for an extended time. They found that aluminum absorbed twice the crash energy than steel.
Q: Can you tell us about the trend toward lightweight materials and if it’s expected to continue in the future?
A: The use of lightweight materials has ramped up over the last decade. When I worked in a body shop in 2008, the incidents of aluminum in our facility were minimal. By the time I left in 2012, it was becoming more common.
Looking at Mitchell data from our estimating customers, we see a couple of percentage points growth every year in terms of the major component parts constructed of these types of materials.
Looking ahead, it is predicted that this trend will continue to evolve. A study conducted by IHS Markit showed that over the next 10 years, we’re going to see highstrength steels have higher percentage content in vehicles than mild steels. Higher tensile strength steels are fired at higher temperatures, which produces more rigidity, so the material is not only lighter, but also stronger.
Q: How is this shift expected to impact collision repairers?
A: As manufacturers continue to use more non-traditional materials, it will ultimately impact collision repairers. When Ford manufactured the all-aluminum F-150 in 2015, there was much discussion around the use of this material. As a result, some collision repairers have already set up their facilities to accommodate aluminum repair with a clean room and dedicated tools, dust evacuation systems, etc.
In addition to aluminum and lightweight steel, I think we’ll also see a shift in the use of composite plastics. All these changes are likely to affect the repair versus replace decision-making process. Certain materials are simply going to create a different pattern of damage than steel.
With some parts of the car comprised of ultra-high-strength steel, for example, a repair is prohibited because it will ruin the vehicle’s structural integrity. Other parts, such as composite plastics and even carbon fiber, can be repairable in certain instances but this is rarer than if the panel was comprised of mild steel.
The properties of the metal in the vehicle dictate how it will respond in an accident. Because aluminum becomes more brittle when impacted, it’s more likely that it will crack versus deform. When mild steel is impacted, it dents. It deforms the energy and continues to travel through the rest of the car because that energy hasn’t been dispersed quickly enough.
When you have something that cracks, that energy disperses much more efficiently. If you have a fend-
er with a dent, it might be repairable; however, it probably can’t be fixed if it has a crack.
Take the 2018 Audi A3. There’s an A3 with a gas engine and an Audi e-tron, the plug-in electric vehicle. With the gas engine version, the fenders are made of mild steel. The fenders on the plug-in version are aluminum. The front ends look identical and there is no difference cosmetically.
However, when those cars are in an accident and subjected to impact, the fenders are going to respond very differently. There will be different patterns of damage simply due to the materials. That’s at the core of why this is important.
The chief engineer of the Ford Explorer, Bill Gubing, said that weight was a factor in every decision they made on the 2020 Explorer, according to FordAuthority.com. The engineering team looked at every part and how they could achieve weight savings and still achieve the same type of performance or better in a crash test. Ford uses aluminum in the 2020 Explorer, but it also uses steel, magnesium and plastic.
This is a great example of how automakers are looking at all the components in the vehicle to de-
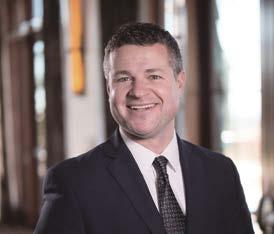
Ryan Mandell, director, Claims Performance, Auto Physical Damage Solutions for Mitchell International�
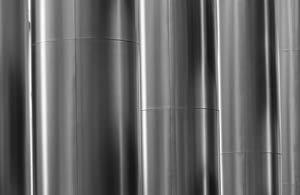
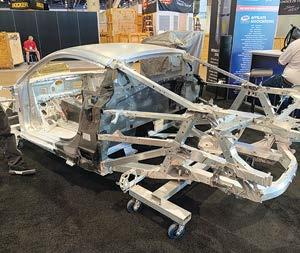
This Audi structure at the SCRS booth during SEMA consists of stamped and extruded aluminum with carbon fiber reinforcements� Credit: Tim Ronak