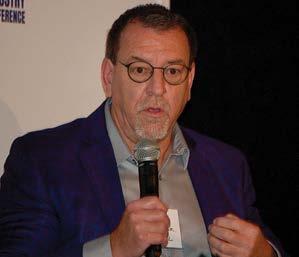
5 minute read
Plant in Oklahoma: Report
“In fact, they’re becoming far more specific about what is a paint material, and creating invoices and documentation for that,” Ronak said. “They’re taking some of the things that used to be called materials, like panel bonding adhesive and seam sealers, and billing for those independently on a per-job, docu-
mented basis.”
Advertisement
He said “knowing your numbers” is even more crucial for shops in inflationary periods.
“Be able to break down how you look at your business, rather than just sales versus a pile of costs,” he recommended. “You need to truly understand job-costing. The transformative moment for most shops that I’ve worked with in all the years I’ve been doing this is when they understand job-costing and they stop doing the things that take money away. That’s typically all you need to do: Stop doing the stuff that costs you money, and start doing more of the things that make you money.”
Ewing, a performance group manager for BASF, said shops using the Mitchell Refinishing Materials Calculator, PMCLogic from Computer Logic or their paint scale to more accurately track and invoice for the actual materials used will see two otherwise identical jobs may have different paint costs just because of the color. Charging based on paint labor hours doesn’t take into account so many factors like that, he said.
“You may have a weak estimator who writes lower hours than should be expected for that repair, or may have missed something during the estimating process,” Ewing said. He said paint and materials documentation and invoicing will continue to become more detailed over the long term, just as estimates themselves were once as basic as “replace and paint fender for $xxx.”
Shorter-term, he said, shops need to work with the manufacturer of the paint they are spraying “to really understand how to be profitable with their products,” and then “learn how to document and communicate that” to whoever is paying the bill for repairs.
Tim Ronak of AkzoNobel said collision repairers really need to be on top of their numbers during inflationary periods
Addressing Costs with Insurers
An insurance company representative on the panel said, like shops, insurers are seeing their costs rise quickly. Dan Tessadri, auto physical damage business consultant for CSAA Insurance, said at least in some states, there can be a long lag time before insurers can reflect their higher costs in premiums.
In California—and some other states—insurers must get the premium increases approved in advance. Between the process of determining the increases needed and getting approval, he said, it can take up to two years to see the increase reflected in premiums.
“That’s a little different than what [a paint company CEO said in a news clip played at the meeting] where every quarter they look to adjust prices,” Tessadri said.
Tessadri was asked about shops’ approach in seeking rate increases.
“There is an incredible difference in the documentation, in the communication, in the overall sort of understanding of the impact inflation is having on their store,” Tessadri said.
The most effective way he sees for a shop to start that conversation?
“From my perspective, it’s understanding that you’re not operating in a vacuum. We’re not all in the same boat, but we’re in the same storm,” Tessadri said.
Work for some open discussion, he recommended.
“‘This is what I want, but this is what I could potentially live with,’” Tessadri suggested. “Those are the discussions that end up probably more successful. I’m a data guy. So I do sort of enjoy seeing [someone who has] gone to the length of crunching that information to explain it to me.”
Panasonic Looking at Potential EV Battery Plant in Oklahoma: Report

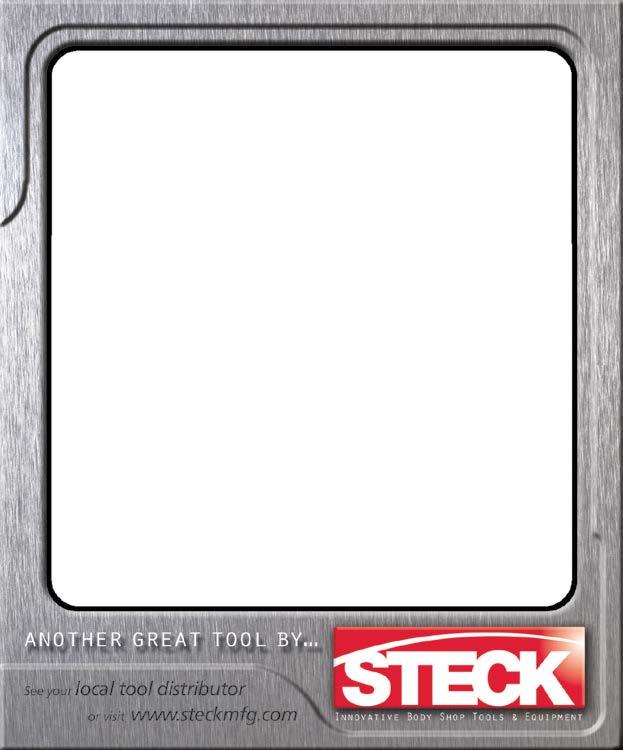
by Simon Alvarez, Teslarati
Oklahoma may have lost to Texas and Kansas when Tesla and Panasonic were looking for a new U.S. factory site, but the Sooner State’s efforts might finally be paying off. As per recent reports, Tesla supplier Panasonic is reportedly in discussions to build another battery factory in the U.S., and it would be worth about $4 billion. Prior to Panasonic’s decision to build a battery factory in Kansas, reports suggested the Japanese company was considering both Kansas and Oklahoma as potential sites for its new facility. Panasonic’s Kansas plant is expected to produce 4680 cells for Tesla’s Gigafactory Texas, which is producing popular vehicles like the Model Y and, in the near future, new products like the Cybertruck. Citing individuals familiar with the matter,The Wall Street Journalsaid Panasonic is now looking at Oklahoma as the location of a new battery plant. The publication’s sources, however, said there is no guarantee yet an agreement will be reached.
People allegedly familiar with Panasonic’s plans have described two U.S. plants as “twins” with similar capacities. This suggests the Oklahoma site may also be tapped to supply Tesla. A spokesperson for Oklahoma Gov. Kevin Stitt has so far declined to comment on the matter.
Oklahoma has been fighting hard to secure a deal with key companies involved in the development of electric vehicles—and it has come close. The state was shortlisted by Tesla when the EV maker was searching for the site of its Cybertruck factory, to the point CEO Elon Musk met with state officialsto see if a deal could be reached. Ultimately, Oklahoma lost to Austin, TX, to be the site of Tesla’s Giga Texas. Oklahoma was also reportedly shortlisted by Panasonic when it was looking for a new U.S. battery factory site. But despite putting together an beneficial incentive package for Panasonic, Oklahoma lost to Kansas. If the WSJ’s sources prove accurate, perhaps Oklahoma’s efforts will finally bear fruit, and the state could be one of the key players in the U.S.’ electric vehicle revolution.
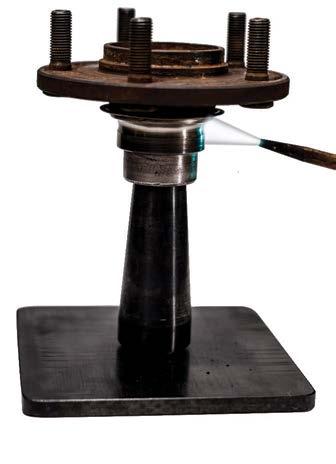