
1 minute read
Autonics Stepper Motors & Drivers
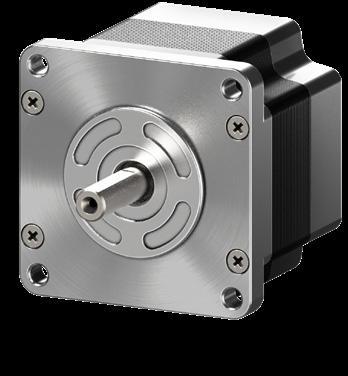
1. Available Open Loop Control with Digital Signals
Advertisement
With PLC, open loop control is available with pulse input (digital) and separate position detection devices are not required. In addition, gain tunning is not required and circuit configuration is simple.
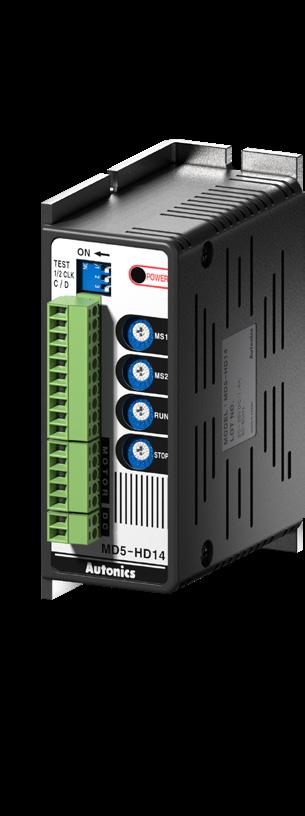
2. Simple and Accurate Control
Stepper motors can rotate at a certain angle per step and stop with high accuracy. 5-Phase Stepper motors optimized by pulse input signal are available to control the rotation angle and speed easily.
0.72˚
5-Phase Stepper Motors
3. High Accuracy Position Control
Since 5-Phase stepper motors have a rotation angle of 0.72˚ (Full step) per step and have no accumulation of stopping errors, repeatability is accurate.

4. High Response and Self-Holding
Since the stepper motors rotate synchronously with the input pulse, response in starting, stopping, and reversing is high. In addition, stepper motors have a high holding torque which makes them hold a stop position without mechanical break or control signal.
5. Various Lineup
5-1. 5-Phase Motor Lineup
5-phase stepper motors rotate by 0.72˚ per pulse. When using micro step drivers, more precise control is available with rotating 0.00288˚ per pulse.
5-2. Various Motor Frame Sizes and Types
Various motor frame sizes (24 / 42 / 56 / 60 / 85 mm) are provided. Users can apply various motor types (standard type, built-in brake type, hollow shaft type, geared type, built-in rotary actuator, etc.) in different environments.
* Motor frame sizes may vary by type.
5-3. Various Stepper Drivers Lineup
Various lineup of drivers (micro step type and intelligent type) is provided. Users can customize with flexibility.
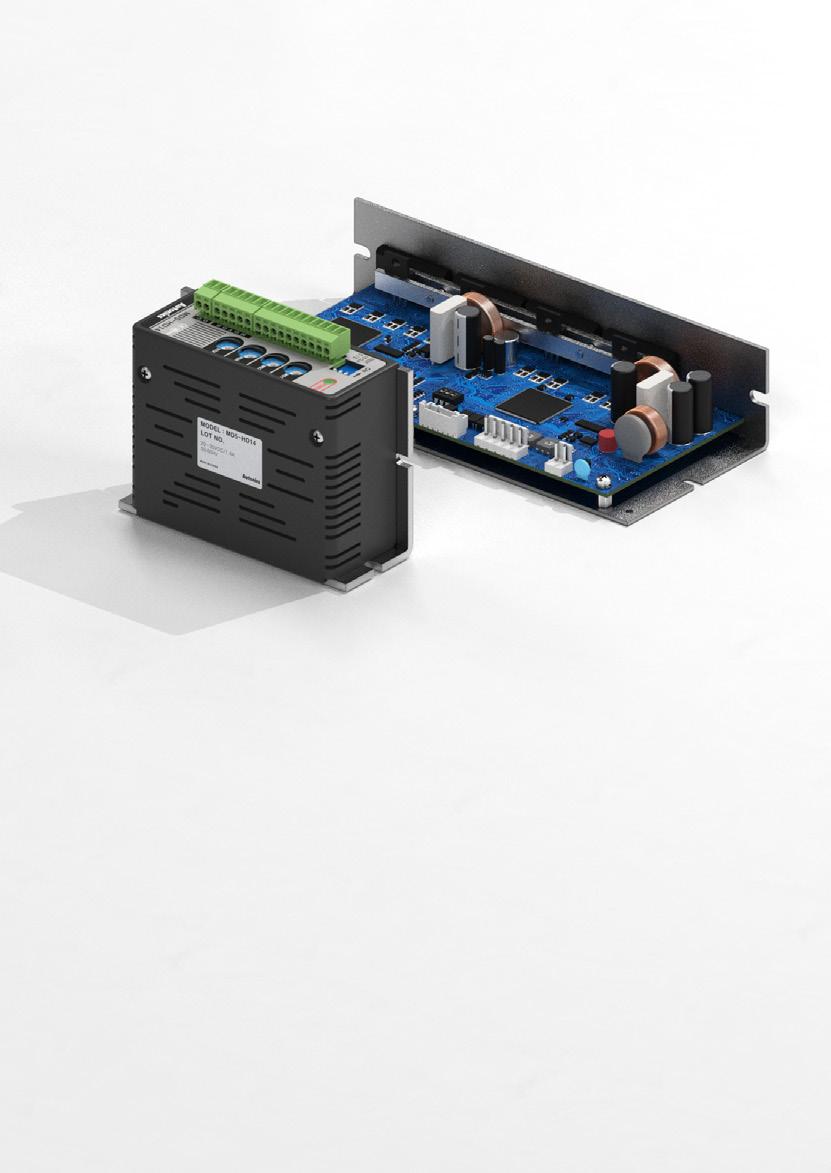