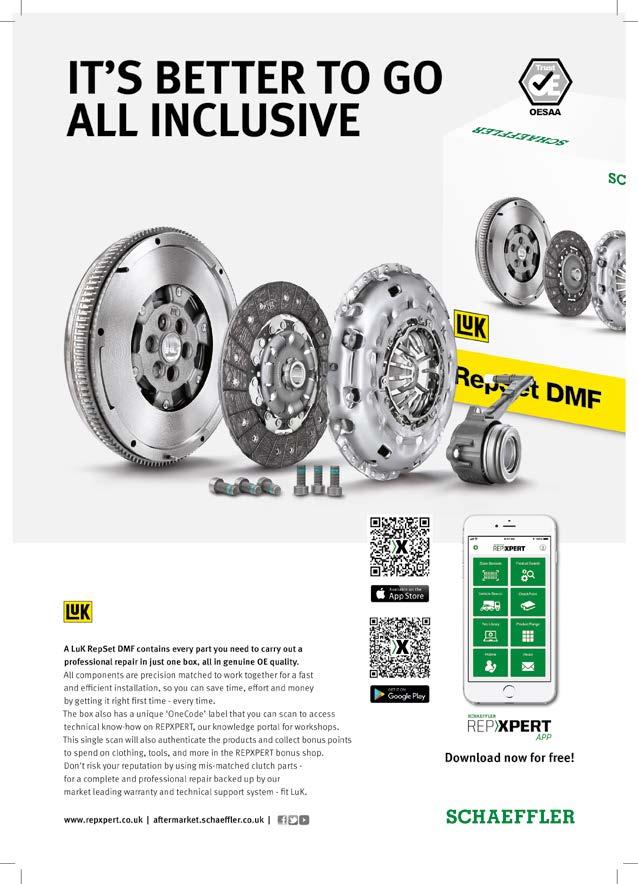
4 minute read
THE HOT CLUTCH
As good as modern clutches might be, heat remains a formidable enemy, as Rob Marshall finds
Ever since carriages became powered by engines rather than horses, engineers had to solve the challenge of transmitting power from a rotating crankshaft to stationary wheels. It was found almost immediately that a friction clutch was the most effective method, let down severely by the materials available at the time. They discovered fairly quickly that leather and cork were not the most heat-resistant of materials... Being immensely durable and heat-resistant, asbestos was ideal, but the health risks discovered later led to it being banned from not just clutches and brakes but also engine gaskets. Since then, engineers have been forced to develop suitable replacements that do not dissolve technicians' lungs. This has been far from easy, considering that clutches have had to become more sophisticated and lighter, while cars have become heavier and more powerful.
Keeping up to date
While the diaphragm spring friction clutch has remained relatively unchanged for decades, you should not be complacent. Updating your training is still worthwhile, to discover how and why the latest developments have been introduced, such as self-adjusting clutch covers. Yet, a clutch still produces the majority of its heat, when the friction plate slips against the flywheel and clutch cover, as the vehicle takes up drive.
When examining a clutch, check the metal parts for colour changes. Yellowing, or bluing, indicates severe overheating has occurred.
Unfortunately, as is so often the case in engineering, final specifications are a compromise. Sachs reports that OE suppliers work closely with car manufacturers to develop clutch friction material that provides the best compromise between long life and comfort under normal road conditions. A long-life lining might have excellent heat-resisting characteristics but, if violent and uncomfortable judder is the price, the carmaker will reject it. This also explains why OEMs do not use race clutches, even in high-performance road cars, due to their very unprogressive 'on-off' bite points.
Over-slip
When leading ZF Group UK's clutch training courses, its Technical Training Manager, Wayne McCluskey, tells delegates that drivers tend not to realise that the maximum clutch slip time should not exceed several seconds. Any longer than this risks creating potentially damaging quantities of heat.
Check the metal parts for evidence of glazing, indicating that contamination (usually oil) is entering the clutch unit. First Line says to also use your nose – the acrid, burning smell of vapourised linings will linger on the removed parts.
This poses a problem, Sachs explains, because excessive heat causes the binding resin within the friction lining to break down. As these temperatures increase, the fibres within the lining material separate. Should the temperature rise even more, the lining will disintegrate.
Valeo says that you can suspect clutch overheating, because excessive temperatures change the lining material's friction characteristics. This can result in not just clutch judder but also clutch plate distortion, a situation that promotes uneven flywheel contact, causing hot spots to develop and increasing the overheating risk. These perils increase as the clutch ages, Valeo finds that, as the clutch friction plate wears, its heat dispersant abilities reduce as well.
Who is to blame?
Poor driving tends to be the main culprit, especially as it is possible to burn a clutch out completely within seven minutes, whereas one fitted to a vehicle that has been driven with a modicum of mechanical sympathy can last well over 70,000 miles. Valeo explains that the clutch is designed to be either engaged, or disengaged completely, meaning that the clutch pedal should either be depressed fully, or left untouched. Therefore, problems occur when the clutch is 'ridden' - i.e. when the clutch pedal is depressed partially. As most technicians appreciate, apart from increasing release bearing/CSC wear, the pressure applied by the pressure plate/ clutch cover is insufficient to clamp the friction disc firmly against the flywheel, causing it to slip and generate heat. Therefore, educating the driver sensitively about mechanicallysympathetic driving techniques will help. These include not using the clutch pedal as a footrest, avoiding slipping the clutch to compensate for selecting too high a gear, not holding the car on an incline with the clutch instead of the hand brake and, of course, resisting racing getaways.
Even so, First Line, Sachs and Valeo find that technician error can also be responsible for reduced clutch life. The most common reason why a new part fails prematurely is contaminated friction lining. As lubricant from either the engine, or transmission, can cause this, not attending to weeping oil seals is a false economy and will prejudice any clutch warranty – a fact that is worth highlighting to the customer, should you meet any resistance about the extra cost of attending to worn ancillary items that are not related directly to the clutch.
Even so, overgenerous application of grease to the gearbox splines remains the most common workshop error. This lubricant is flung from the input shaft and finds its way onto the clutch linings as soon as the car embarks on its first postclutch replacement trip. The resultant contamination will shorten the new clutch's life, by modifying its lining's friction characteristics, causing more slip and, therefore, enhancing the overheating risk still further. The customer may also experience juddering and may return angrily for an explanation.
Consequential damage
Once you have removed the clutch and your subsequent checks confirm that it has overheated, suspect damage to related parts. The dual-mass flywheel is the most vulnerable item in this respect. While you cannot dismantle it, you are justified in suspecting internal damage if you notice either blue, or yellow, colours on the contact faces, indicating that it has experienced temperatures over 400 degrees Celsius. Sachs explains that the DMF is filled with grease, which can solidify, should it encounter higher than designated temperatures. Certain DMFs contain nylon parts, such as spacers, which can melt. Understandably, should it contain solidified grease and melted components, the DMF cannot function correctly. Sachs highlights also that the DMF's secondary mass is relatively thin, meaning that it can also distort if overheated.
Valeo concurs that, as the DMF is an enclosed mechanical assembly, it is harder for it to cool. Therefore, if you suspect overheating, inspect the assembly for cracks, which indicate that the part has exceeded its designed shock value specifications. Clearly, a cracked DMF must be replaced. Should you suspect that how the vehicle is being used results in excessively high temperatures, Valeo suggests that its KIT4P solid DMF conversion kit might be a worthwhile consideration, owing to the single mass unit not having to dissipate internal friction energy.
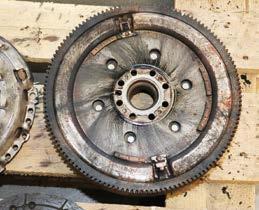