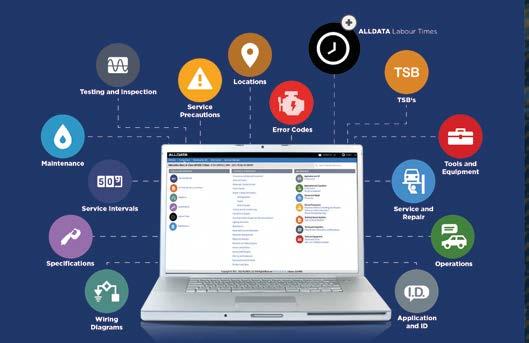
6 minute read
alldata repair: Vital OEM data and support for every task
ALLDATA Repair puts the latest, original OEM repair information right at your fingertips, covering more than 91,950 unique vehicle combinations – 95% of all vehicles on the road today
ALLDATA Repair subscribers can now obtain original OEM repair information from Dodge, Ram and Jeep after ALLDATA secured the right to republish technical repair data from these vehicle manufacturers for Europe. This increases the number of vehicle manufacturers data available to ALLDATA Europe’s customers to 32.
The repair information for Dodge, Ram, and Jeep is currently accessible via the ALLDATA Info Centre Service. The Info Centre Service is an additional support resource for automotive and bodyshop professionals searching for technical information within the ALLDATA Repair portal. It complements a library of 91,950 vehicle combinations, which equates to over 95% of vehicles being driven on roads today.
For all other (29) vehicle manufacturers, vital information is available in the ALLDATA Repair Portal. The ALLDATA Repair portal contains Technical Service Bulletins (TSBs), diagnostic trouble codes (DTCs), and more than six million technical drawings and wiring diagrams – including electrical connector views – all available in five languages. The portal contains 75 million articles. ALLDATA Europe is committed to continuously strengthening its flagship repair product for the benefit of the company’s 12,000 European subscribers.
OEM Labour Times
In February this year, ALLDATA Europe announced a new add-on product for ALLDATA Repair that provides quick and easy access to OEM labour times. Now, with just one click, subscribers can see accurate OEM labour times that correspond to repair information – both mechanical and body.
These examples, along with the exciting news of yet more vehicle manufacturers being integrated into ALLDATA Repair, demonstrate ALLDATA Europe’s determination to continue its evolution, according to ALLDATA President Satwinder Mangat.
“We have a continual program of development for ALLDATA Repair worldwide, which means the product we had a year ago is now even better and the product purchased today by the customer will be updated and enhanced on a regular basis,” said Mangat.
This commitment was echoed by ALLDATA Europe’s General Manager and Managing Director Karol Englert. “There is a customer and employees feedback loop that we are constantly reviewing, which gets fed into our product development roadmap,” he said. “We aim to keep the same user experience that our customers have become familiar with, but always look for ways to improve our product as well. In the next 12 months alone, the roadmap is full of improvements and additions that have come about as a direct result from that feedback.”
Can’t find what you’re looking for? The Info Centre Service will sort it!
The Info Centre Service provides additional support for workshops searching for technical information in the 72 million documents available within the ALLDATA Repair portal.
ALLDATA Europe Managing Director, Karol Englert, revealed how subscribers can use the value-added service: “Users can access the Info Centre Service via the ALLDATA Repair portal. If we have published data for the vehicle but they simply can’t find what they are looking for, they can put in a request to us. We will assist subscribers by providing the location of the data. This will enable them to become familiar with the portal and increase their confidence for next time.”
Some repair data, however, is not published and is only accessible on demand via the Info Centre Service, as Karol explained: “For example, service interval check sheets are unique to each vehicle on the road, depending on age and mileage covered and are, therefore, only available on request.
“Alternatively, it may be because we have just signed a new agreement with a vehicle manufacturer and are still processing the repair information and getting it ready to publish into the ALLDATA Repair portal.”
Irrespective of the request and whether the data is readily available on ALLDATA Repair, one of ALLDATA Europe’s 11 qualified and experienced technical support specialists will respond quickly.
The Info Centre Service team has a targeted response time of four hours but can often fulfil requests in less than two, depending on demand and the type of enquiry received. The user is then able to carry on with their job safely and accurately, rather than guessing or having to turn work away.
ALLDATA Repair in action: Inside Intelligence
ALLDATA Repair offers solution after receiving customer enquiry about a 2018 Jaguar F-Pace, which had left the technician puzzled!
Providing safe, accurate vehicle repairs and getting customers back on the road quickly means starting with the right tools: ALLDATA Repair offers exactly that by providing up-to-date OEM mechanical/body repair information and procedures for 91,950 unique vehicle combinations – more than 95% of all vehicles on the road today.
The portal comprises of six million technical drawings and wiring diagrams, including electrical connector views, which are available in five languages.
Query
Independent workshops and bodyshops rely on ALLDATA Repair; as such, it recently came to the assistance of a customer that was recently working on a 2018 Jaguar F-Pace, which had been experiencing issues which left a technician puzzled and scratching their head.
The lights, indicators and the wash wipe system worked intermittently. The technician scanned the vehicle’s systems, but no trouble codes were present – it was very odd and frustrating, as it was proving difficult to solve. Step forward, ALLDATA Repair!
Solution
Thankfully, ALLDATA Repair’s experts had come across this issue before and, indeed, it was tricky to solve. The root cause of the problem was down to a poor connection on the connector mounted on the PCB board within the lighting and/or wiper control switch.
The technician removed the control switches (highlighted below); in the example, it shows the left-hand control switch, but the right-hand side is the same.
Upon doing so, the technician connected and reconnected the control switches at least twice to clean the electrical contact points. They obtained some NyoGel electrical contact lubricant – a suitable equivalent is fine – and applied it to the connector on the PCB. For future reference, it’s vital that it’s not directly applied to the control switch connector.
Finally, they removed excess lubricant and refitted all components as required. The same method can be used, if required, to the right-hand control switch. This solved the issue and allowed the technician to complete a professional, correct and efficient repair, which meant a happy customer!
KTS Diagnostics: Lesson 4
Identifying Known Fixes With Experiencebased Repair
Welcome to the fourth bitesize guide in our series of useful tips to help your workshop maximise the potential of your Bosch ESI[tronic] 2.0 software
Identify And Remedy Known Fixes Faster
Last time, we delved into the time-saving potential of our ‘Service Tasks’ tool. By putting all the tasks your workshop team need to complete right at their fingertips – in seconds –‘Service Tasks’ gives your engineers a head-start on the work at hand. While our Experience Based Repair (EBR) – Known Fixes feature helps them take efficiency to the next level.
FIXES YOU CAN TRUST, IN ONE CONVENIENT PLACE
With the online knowledge exchange growing by the day, many workshops are turning to Google for their repair instructions. While the internet is a huge data source, many results are unvetted and unverified. Leaving a lot of timeconsuming legwork for your team, even if the initial search goes smoothly.
By aggregating knowledge from across a worldwide diagnostic community of 75,000 experts, EBR - Known Fixes cuts out potential hours wasted searching the web.
From the technical hotline and internet forums to trending Google searches – the EBR-finder utilises an innovative algorithm to identify common problems from across a wide variety of sources and alert our experienced ESI[tronic] SIS authors of any emerging challenges being experienced in the field. This expert team then check the entries for plausibility and validate the data to create Bosch-quality content to guide you through the fix.
ACCESSING EBR – KNOWN FIXES
Found under the Known Fixes tab, EBR – Known Fixes allows you to find the right solution in seconds.
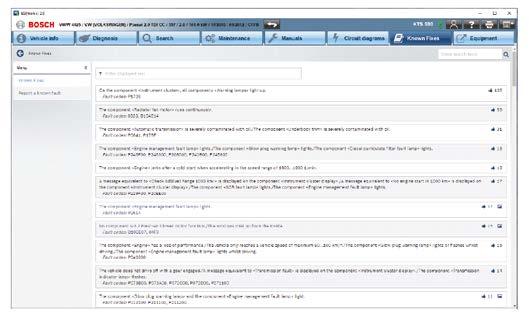
Once registered, you can freely type any text into our search agent to find common fixes by fault code, symptom, component or keyword.
Ranked By Likes
Find our most popular fixes, fast. Thanks to the feedback feature we’ve made it easy for technicians on the ground to rate a fix – helping you to easily see the industry’s best-ranked solutions, see Figure 1. It also enables you to have your say on how useful you found a particular fix.
Search Bar
You can quickly and easily search our database of fixes by keyword. Just like you would if you were relying on traditional search engines. The biggest difference? Every result is Bosch approved, see Figure 2
FOR CONSISTENCY AND RELIABILITY, EVERY BOSCH APPROVED FIX FOLLOWS THE SAME FORMAT, SEE FIGURE 3.
COMPLAINT
A brief summary of the issue
GENERAL CONDITIONS
A list of any relevant symptoms
POSSIBLE CAUSES
The most common reasons why this fault may occur
REMEDY www.bosch-training-solutions.com
The known fix for these challenges.
Quick and reliable repairs are the foundation for excellent results and satisfied customers. With more than 1,500,000 real life use cases – and growing – it’s never been easier to find the right solution for your problem. Fast.
As on online service that is updated automatically, EBRKnown Fixes will always bring you the very latest repairs and adaptations from our ever-growing database.
Join us for our next lesson to discover how our Service Information System – or SIS for short – can guide you from symptom detection and associated trouble code to root cause and rectification, step-by-step.
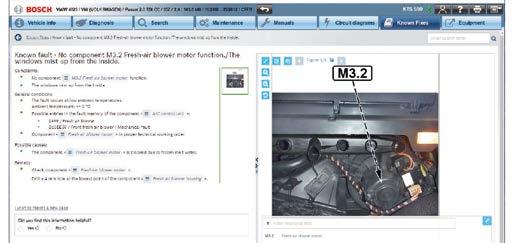
