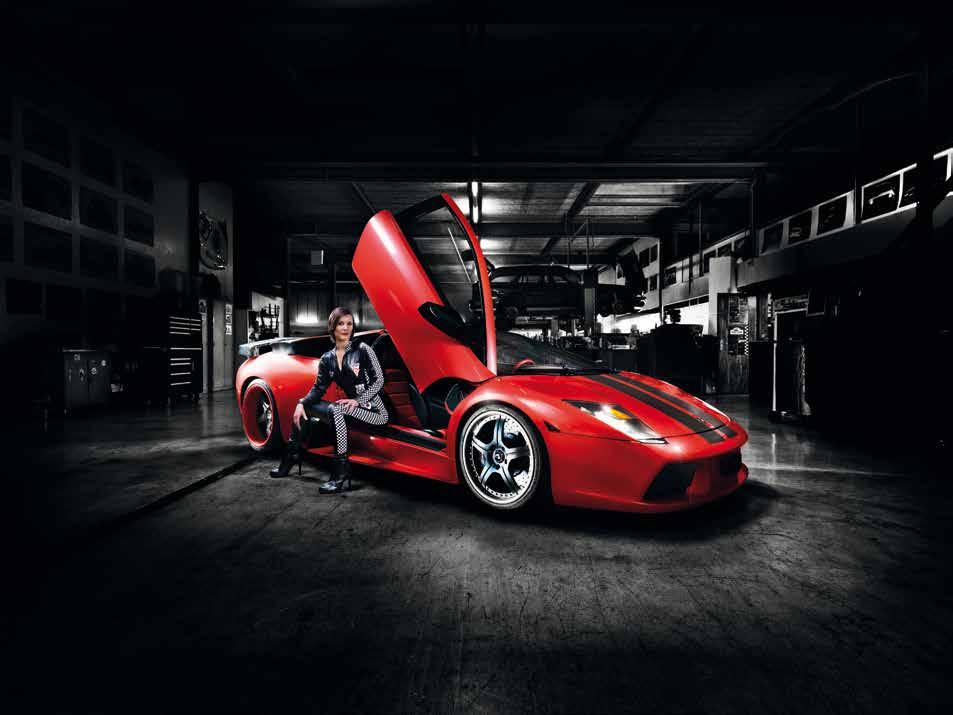
10 minute read
PLATTFORMIDEE IM RÄDERBAU
from A&T 04/2023
BBS stellt mit der neuen Unlimited-Serie eine Radgeneration vor, welche eine noch grössere Individualisierung ermöglicht. Um ein Rad für ein Fahrzeug auszuwählen, kann im Baukastensystem alles Mögliche zusammengebaut werden. Zuletzt muss der Fahrzeughalter aber wissen, was für sein Fahrzeug vom Gesetz erlaubt ist. Text: Andreas Lerch | Bilder: BBS, Lerch
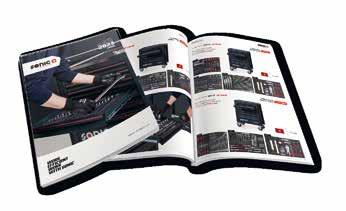
BBS heisst nach den Anfangsbuchstaben der Firmengründer und dem Produktionsstandort Baumgartner, Brand und Schiltach. Heinrich Baumgartner war ein rennsportbesessener Automechaniker mit guten Ideen und geschickten Händen. Er verbreiterte seine Autos so gut, dass er einen Werksauftrag erhielt, welchen er in der leerstehenden Textilfabrik seines Freundes Klaus Brand in Angriff nahm. Neben den Verbreiterungen hatte Baumgartner schon lange das Problem der ungefederten Masse erkannt, und 1970 gelang es ihm, ein leichtes, dreiteiliges Rennrad zu entwickeln. Damit war der Grundstein für den Erfolg gelegt. 1980 wurden täglich 1000 Räder gebaut, 1995 waren es bereits 3000 Räder. Das Mitte der 1990er Jahre entwickelte

RC-Rad war optisch dem aktuellen CI-R-Rad nicht unähnlich und erfreute sich einer 25-prozentigen Masseersparnis gegenüber herkömmlichen Leichtmetallrädern.
2007 stellte die BBS Kraftfahrzeugtechnik AG Insolvenzantrag. Nach mehreren Handänderungen, Aufsplittungen und weiteren Insolvenzanträgen wurde BBS 2021 von KW Automotive übernommen. So kam das arg gebeutelte Unternehmen vor zwei Jahren wieder in ruhigere Gewässer. Und der Elan der alten Erfolgsgeschichte scheint wieder Fahrt aufzunehmen, denn eben hat die Firma die neue Entwicklungsrichtung BBS Unlimited vorgestellt.
BBS Unlimited
Die neue Rädergeneration scheint so aufgebaut zu sein, als hätten die
BBS-Entwickler bei den OEMs die Plattformtechnologie übernommen und auf die Radproduktion angepasst. Während früher ein Rad mit der Grösse 10 J x 20 H2 für jedes bestehende Fahrzeug, das diesen Radtyp im Typenschein aufgeführt hat, einzeln gegossen und hergestellt werden musste, wird es heute nur noch in maximal vierfacher Ausführung gebaut. Der fahrzeugspezifische Lochkreisdurchmesser und die vorgeschriebene Einpresstiefe können problemlos mit festverschraubten Adapterscheiben angepasst werden.
Auch für den Wiederverkäufer werden die Lagerhaltungskosten viel kleiner, da er die voluminösen Räder nur noch in kleiner Anzahl lagern muss. Die Distanzscheiben, über welche die fahrzeugspezifischen Anpassungen erfolgen, nehmen im Lager nicht sehr viel Platz weg; und so sind die Räder immer lieferbar, während sie früher in der Regel bestellt werden mussten.
Radaufbau
Ein Fahrzeugrad besteht aus der Felge und der Radschüssel. Diese Terminologie unterscheidet sich von der Werkstattsprache. In der Werkstatt wird als Rad in der Regel das Gesamtrad mit Radschüssel, Felge und Reifen verstanden.
Die Felge schliesst den Reifen pneumatisch ab und hält ihn in seiner Position. Das ergibt sich durch die geometrisch definierten Formen von Felgenhorn (1 in Bild 3) und Hump (2). Dazwischen liegt die Felgenschulter (4), auf welcher der Reifenwulst aufliegt: Auf diese Weise können die Dichtheit, der Rundlauf und der Planlauf garantiert werden. Das vertiefte Felgenbett (3) ermöglicht die Montage und die Demontage der
Reifen. Da der Wulst mit einem stählernen Drahtseil (Wulstkern) versteift ist, kann der Reifenwulst im Durchmesser nicht vergrössert werden und ist auch nicht elastisch. Deshalb muss die Montage durch einen Trick ermöglicht werden. Wenn der Reifenwulst auf der einen Felgenseite über das Felgenhorn gestülpt werden soll, muss er auf der anderen Seite in der Vertiefung, eben im Felgenbett liegen. Auf diese Weise geht es mit dem Wulstdurchmesser wieder auf und der Reifen kann montiert werden. Am Schluss wird der Wulst beim Pumpen über die Humps gestossen. Dazu lässt sich der Wulstgummi genügend elastisch zusammendrücken.
Die Radschüssel oder der Radstern wurde früher bei Stahlrädern eingeschweisst, bei Leichtmetallrädern werden Felge und Radstern zusammen gegossen oder geschmiedet. Exklusiv können sie auch miteinander verschraubt werden. Der innere Teil des Radsterns stellt die Verbindung mit dem Fahrzeug dar und muss deshalb auf dieses abgestimmt sein. Die Abstimmung betrifft die Schrauben- bzw. Bolzenanzahl, den Lochkreisdurchmesser (6), also den
Bild 3. Radbezeichnungen und wichtigste Masse: 1 Felgenhorn – 2 Hump –3 Felgenbett – 4 Felgenschulter – 5 Lochdurchmesser – 6 Lochkreisdurchmesser –7 Nabendurchmesser – 8 Felgendurchmesser, Reifeninnendurchmesser –9 Einpresstiefe – 10 Maulweite.
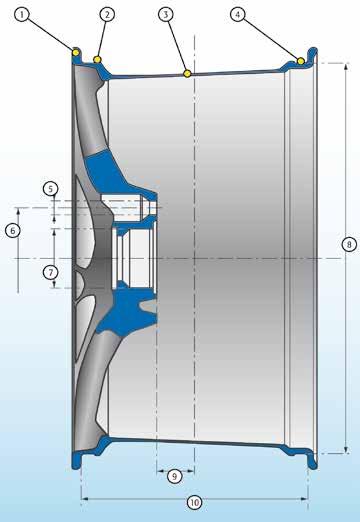
Kreis, auf welchem die Bohrungen für die Radschrauben gebohrt werden, den Durchmesser für die Radschrauben (5) und den Nabendurchmesser.
Typenscheindaten
Es dürfen nicht alle beliebigen Räder, welche an ein Fahrzeug geschraubt werden können, auch montiert werden. Der Fahrzeughersteller hat bei der Typenprüfung bestimmt, welche Dimensionen von Reifen und Rädern zu einem bestimmten Fahrzeug passen (Bild 4). Diejenigen Dimensionen, welche im Typenschein aufgeführt werden, können problemlos montiert werden und werden von der
Motorfahrzeugkontrolle auch nicht beanstandet. Werden jedoch andere Räder montiert und weicht dabei die Gesamtspurweite um mehr als 2 % von dem Mass aus der Typengenehmigung ab, sind die Räder prüfungspflichtig.
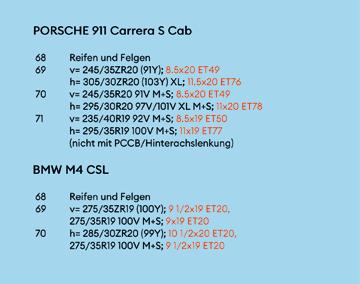
In der VTS Art. 34 «Ausserordentliche Prüfungspflicht» steht unter Absatz 2: Der Halter oder die Halterin hat der Zulassungsbehörde Änderungen an den Fahrzeugen zu melden. Geänderte Fahrzeuge sind vor der Weiterverwendung nachzuprüfen. Namentlich betrifft dies: […] b. Änderungen der Abmessungen, […], der Spurweite, […]; f. nicht für den Fahrzeugtyp genehmigte Räder.
Übrigens: viele Sonic-Produkte können Sie auch in unserem Showroom in Entlebuch entdecken. Vereinbaren Sie einen Termin mit uns!
So kann in der offiziellen Typengenehmigung neben der Radbreite (= Maulweite, 10 in Bild 3), dem Raddurchmesser (8) und der Einpresstiefe (9) auch das Material und/ oder der Hersteller definiert werden.
Räder, welche nicht diesen Anforderungen genügen, müssen geprüft werden. Weicht die Spur dabei weniger als 2 % von der in der Typengenehmigung aufgeführten Spurweite ab, reicht eine Eignungserklärung vom Schweizer Importeur, eine Bestätigung des Felgenherstellers oder die Garantie des Fahrzeugherstellers. Existiert ein ASA-Prüfbericht, ist dieser auf der Typengenehmigung hinterlegt und muss nicht im Fahrzeug mitgeführt werden.
Wird die Spurweitenvergrösserung grösser als 1 % pro Rad (ASA 2a, 4.5.2.2 b), so sind die Räder nur zulässig, wenn eine Garantie vom Fahrzeughersteller oder vom Umbauer vorliegt, welche zum Beispiel auf einem Bericht des DTC (Dynamic Test Center, Vauffelin) basiert.
Spurweite und Einpresstiefe
Die Spurweite stellt das Mass zwischen den Laufflächenmittelpunkten zweier Räder der gleichen Achse dar. Grundsätzlich kann sie durch eine Veränderung der Radbreite beeinflusst werden. Es kommt aber noch eine zweite Grösse dazu: die Einpresstiefe. Diese misst von der Anlagefläche des Rades zum Radaufhängungsflansch bis wiederum zur Radmitte (Bild 3, Position 9).
Mit der Einpresstiefe wird die Lage des Rades im Radkasten direkt beeinflusst.
Soll die Einpresstiefe messtechnisch kontrolliert werden, wird das Rad so auf eine ebene Fläche gelegt, dass das Felgenhorn waagrecht auf der Messfläche aufliegt. Die Felgenbreite müsste theoretisch korrekt innen am Felgenhorn gemessen werden. Da beide Felgenhörner in den meisten Fällen die gleiche Geometrie aufweisen, genügt es in der Praxis, wenn quer über das Rad ein gerader Massstab gelegt und der Abstand zur Auflagefläche gemessen wird (Aussenbreite B). Die zweite Messung erfolgt von der Nabenfläche bis zur Kante des über das Rad gelegten Massstabes (Mass C). Die Einpresstiefe (ET) kann nach der folgenden Formel bestimmt werden:
Mit Werkzeugeinlagen von CLEVERSYS GmbH haben Sie Ihr Werkzeug im Griff. Massgeschneidert und kostengünstig.
Bild 5. Schnittdarstellung der Radverbindung: 1 Rad – 2 Radschraube –3 Verdrehsicherung – 4 Einpresshülse – 5 Bremsscheibentopf – 6 Zentrierring Adapterscheibe an Radaufhängung – 7 Nut für Klicknasen – 8 Zentrierring Adapterscheibe an Rad – 9 Radnabe – 10 Kurzkopfschraube zur Verbindung Adapterring mit Radnabe – 11 Adapterscheibe.
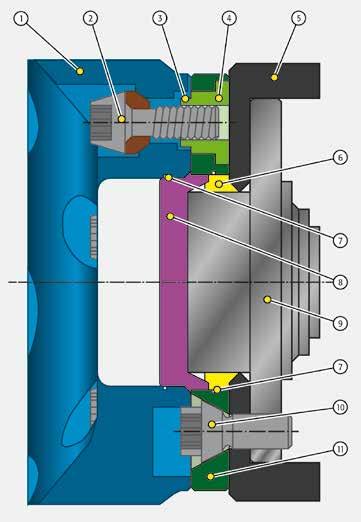
Einfluss der Einpresstiefe
Der Nabenflansch der Radaufhängung verändert seine Position nicht. Beträgt die Einpresstiefe 0 mm, ragt die halbe Radbreite von der Radnabe gegen innen ins Radhaus, während sich die andere Hälfte gegen aussen ausdehnt. Wird die Einpresstiefe positiv, wird ein grösserer Teil des Rades gegen innen verlegt. Ist die Einpresstiefe negativ, wird das Rad nach aussen gerückt. Damit vergrössert sich die Spurweite und es steigt die Gefahr, dass der Reifen beim Einfedern am Kotflügel streift. Bei zu grosser positiver Einpresstiefe wird die Spurweite kleiner und die
Konkavität des Rades
Ein Leichtmetallrad soll grundsätzlich eine geringe Masse aufweisen. Aus diesem Grund sind die BBS-Räder aus der Aluminiumlegierung AlSi7Mg gefertigt. Ebenfalls aus Masseüberlegungen haben sich die Leute bei BBS entschieden, nicht eine Grundform eines Rades zu machen, sondern deren vier. Die im Niederdruckgiessverfahren gebauten Räder sind bei der Unlimited-Reihe so geschaffen, dass ihre Naben nur mit den speziellen Adapterscheiben an die Radaufhängung geschraubt werden dürfen und können. Das Rad weist einen Lochkreisdurchmesser von 117.5 mm auf, welcher momentan bei keinem Hersteller Verwendung findet.
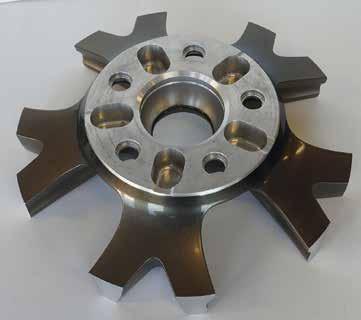
Damit die Adapterscheiben nicht allzu dick und schwer werden, gibt es meist drei unterschiedliche Räder mit der gleichen Dimension, aber eben mit verschiedenen Basiseinpresstiefen. Die Konkavitäten (Bild 2) sind von der Klasse 0 bis zur Klasse 3 eingeteilt. Bei den schmäleren Rädern – bis etwa 9.5 Zoll Maulweite – werden die Konkavitätsklassen 0 bis 2 angeboten, bei den breiteren Rädern die Klassen 1 bis 3. In Bild 2 sind drei Varianten übereinandergelegt und mit blau, grün, braun gekennzeichnet. Beim beispielhaften Rad (10 J x 20 H2) sind die Messwerte folgendermassen abgestuft:
Das Rad mit der Konkavitätsklasse 0 wird bei dieser Maulweite nicht angeboten, jenes in der Klasse 1 hat eine Basiseinpresstiefe von 71.5 mm. Die zehn angebotenen Adapterscheiben weisen Dicken von 14 mm bis 50 mm mit unterschiedlichen Abstufungen auf. Im Beispiel der Klasse 1 liegen die Einpresstiefen zwischen 57.5 mm (71.5 mm Basiseinpresstiefe – 14 mm Adapterscheibendicke) und 21.5 mm. Das Rad der Konkavitätsklasse 2 weist eine Basiseinpresstiefe von 58 mm auf. Auch hier können wiederum die gleichen Adapterscheiben eingesetzt werden. Damit liegt der Spielraum der einbaufertigen Einpresstiefen zwischen 44 mm und 8 mm. Bei der Konkavitätsklasse 3 ist die Basiseinpresstiefe 46 mm. Mit der dicksten Adapterscheibe ergibt sich eine negative Einpresstiefe von 4 mm.
Bei allen Raddimensionen können die gleichen Adapterscheiben eingesetzt und die Räder auf diesem Weg den Kundenbedürfnissen angepasst werden.
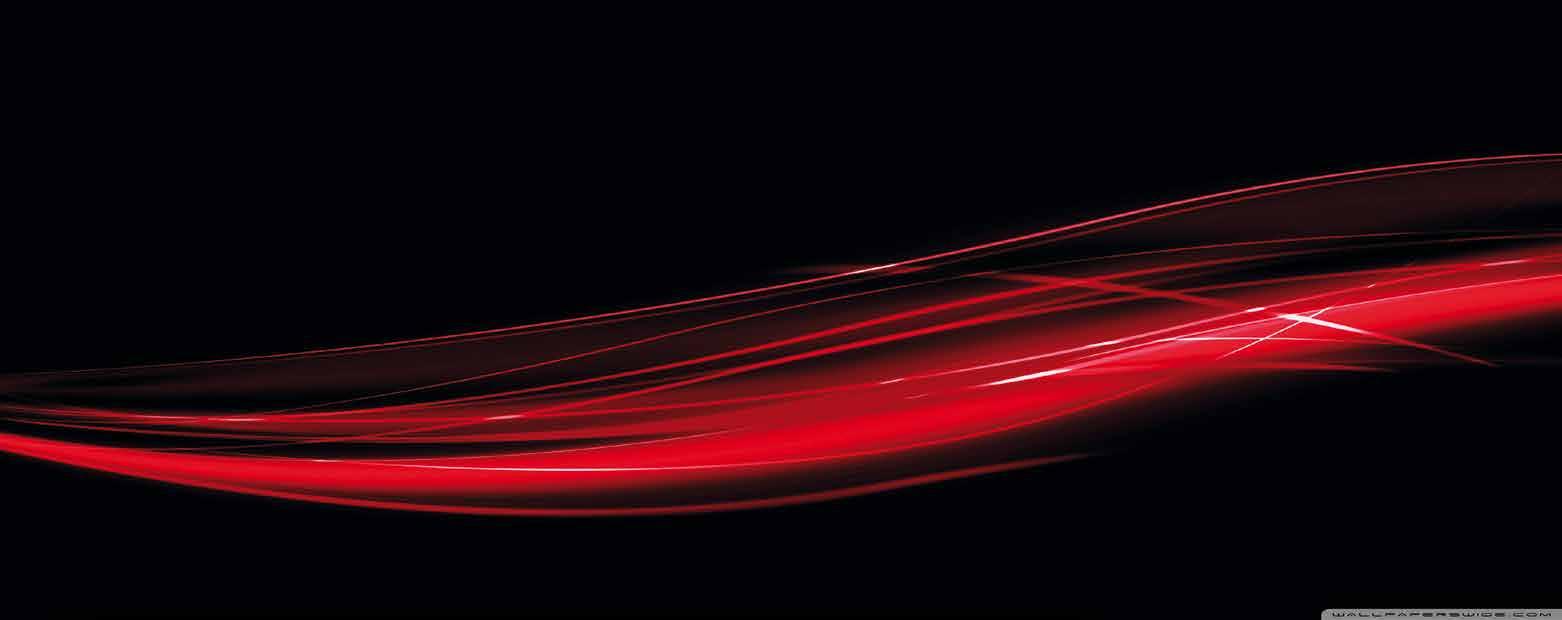
Adapterscheiben
Die Adapterscheibe bestimmt mit ihrer Dicke die Einpresstiefe des Rades. Daneben muss sie die Kräfte vom Rad auf das Fahrwerk übertragen. Dafür wird sie einmal mit der Fahrzeugnabe verschraubt und auf der anderen Seite mit dem Rad. Die Nabenbohrung muss gegen
Unlimited-Räder nur für Fünflochräder vorgesehen sind, werden die fünf fahrzeugspezifischen Bohrungen mit dem entsprechenden Lochkreisdurchmesser in die Adapterscheibe gebohrt und für die speziellen BBS-Schrauben (Kurzkopfschrauben mit den fahrzeugspezifischen Gewindeabmessungen) angesenkt. Momentan sind zehn Lochkreise ausgewählt, damit sind auch die Fahrzeuge definiert, welche mit Unlimited-Rädern ausgerüstet die entsprechenden Radaussparungen (Bild 6). Die fünf Einpresshülsen weisen ein Innenfeingewinde M14 x 1.5 auf und liegen auf dem Lochkreisdurchmesser 117.5 mm.
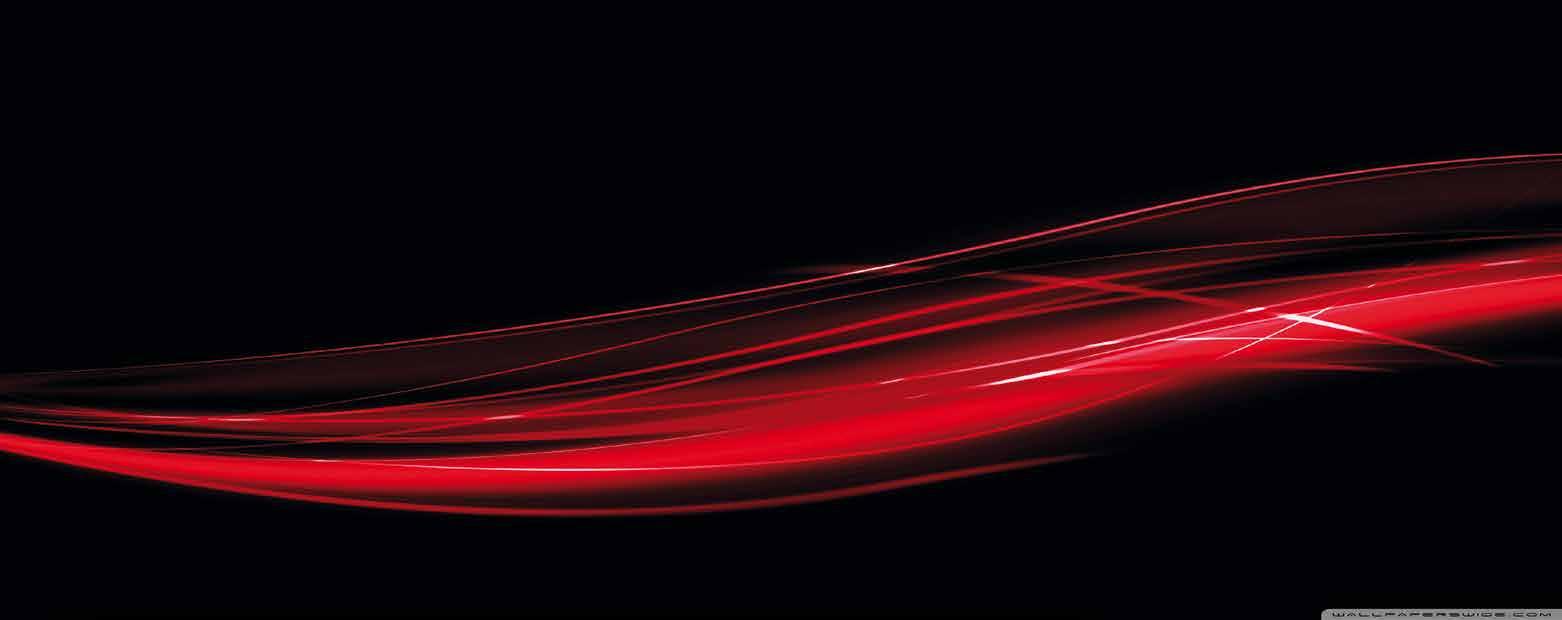
Zentrier- oder Adapterringe
Die Zentrierringe aus Kunststoff sind von vielen Leichtmetallrädern bekannt. Wenn Metall auf Metall passgenau stimmen soll, kann an den Berührungsstellen Korrosion entstehen, die beiden Flächen können zusammenoxidieren. Kunststoff eignet sich sehr gut, da die Zentrierbelastung nur während der Montage auftritt. Sobald die Schrauben festgezogen sind, werden die Adapterringe nicht mehr belastet. Die zylindrischen Teile der Ringe sind zur Zentrierung leicht konisch ausgeführt und mit Toleranzausgleichsnoppen versehen. Die Toleranzausgleichsnoppen (rote Kreise in Bild 8) stellen bei der Montage (= Zentrierungsaufgabe) einen Widerstand dar und nutzen sich ab. Deshalb müssen die Zentrierringe nach einigen Montageprozeduren ersetzt werden.
Die Ringe für die Zentrierung mit der Fahrzeugnabe (Bilder 5 und 9) bestehen aus einem bis 240 °C temperaturbeständigen faserverstärkten Polyamid-Verbundwerkstoff. Die Rin-
Zentrierlänge beträgt 6 mm. Adapterscheibenseitig ist der Durchmesser immer gleich (77 mm), weil die Adapterscheiben auch gleich gebaut sind. Radseitig ist der Zentrierdurchmesser etwas kleiner und beträgt 70 mm.

Zubehör
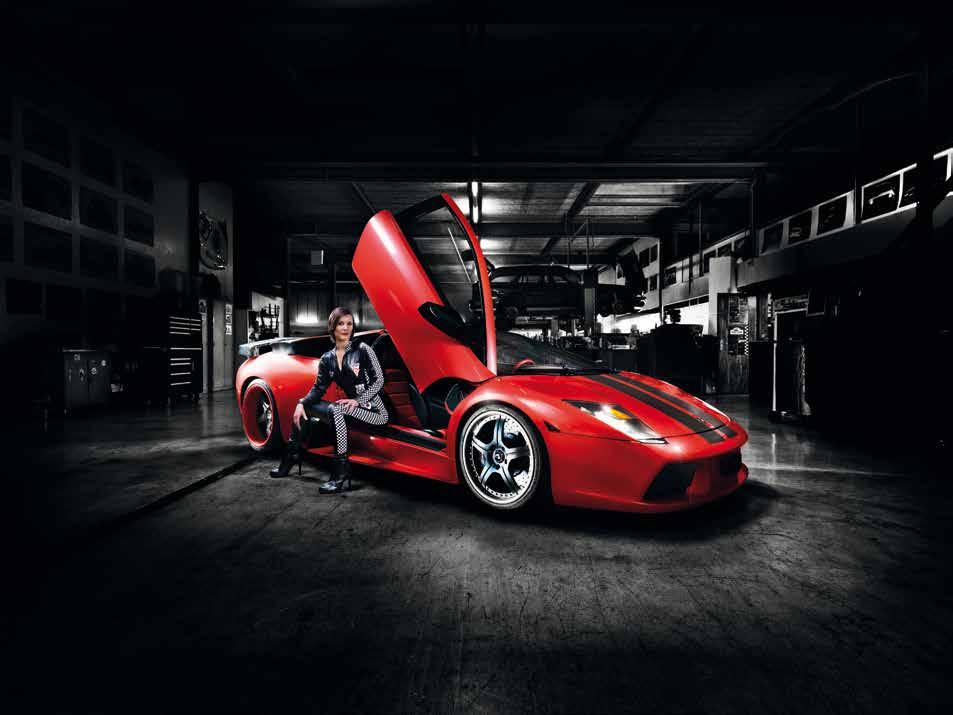
Nicht nur die Gesamträder können verschiedenfarbig geordert werden, auch die auf die äusseren Felgenhörner geklebten Anfahrschutzringe aus Kunststoff und die Ventildeckel sind verschiedenfarbig lieferbar. Bei den Nabendeckeln kann aus verschiedenen Farben ausgesucht und das BBS-Logo kann in 2D- oder 3D-Optik ausgewählt werden. Zusätzlich sind Rotationsdeckel erhältlich, bei denen der BBS-Schriftzug bei stehendem Fahrzeug immer waagrecht steht. Bei den Radschrauben kann zwischen Stahl- und Titanschrauben gewählt werden. Alle BBS-Radschrauben benötigen einen speziellen zehnzackigen sternförmigen Schlüssel.
1. Woraus besteht ein Gesamtrad?
2. Aus welcher Legierung wird ein BBS-Rad hergestellt?
3. Um wie viele Millimeter verändert sich die Gesamtspurweite von 1786 mm, wenn die Reifen 285/35 R 20 von den originalen Rädern 10 J x 20 H2 ET40 auf Räder 10 J x 20
Alterungszustand von Batterien
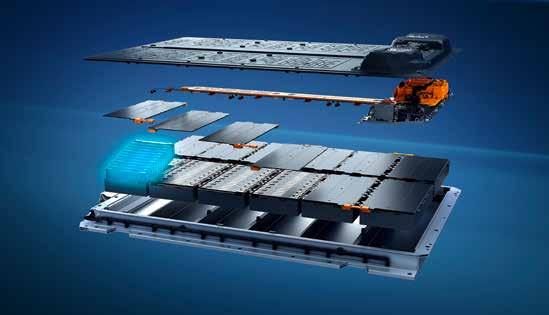
FIT BIS INS HOHE ALTER?
Zwei neue, unabhängig voneinander entwickelte Verfahren zur möglichst genauen Ermittlung des Alterungszustands von Batterien beziehungsweise einzelner Batteriezellen versprechen eine einfachere Einbindung in die Kreislaufwirtschaft (etwa bezüglich Refabrikation von Batteriepacks). Durch Implementierung in das Batteriemanagementsystem lassen sich zudem genauere Prognosen der Batterielebensdauer stellen. Text: Stefan Gfeller | Bilder: BMW, Fraunhofer IFAM, Mercedes-Benz, UBT
Im Rahmen der Kreislaufwirtschaft gelangen «verbrauchte»
Traktionsbatterien in der Regel zunächst in die Wiederverwendung, beispielsweise als stationäre Stromspeicher in Ladeanlagen, bevor sie schliesslich recycelt werden. Im Ersteinsatz und auch bei allfälligen Wiederverwendungen ist es natürlich wichtig, den Alterungszustand einer Batterie oder sogar jeder einzelnen Zelle möglichst genau zu kennen, um Vorhersagen zur verbleibenden Lebensdauer machen zu können oder um zu bestimmen, ob und wie der Akku allenfalls weiterverwendet werden kann. Dazu wurde nun sowohl von der Universität Bayreuth als auch vom Fraunhofer-Institut für Fertigungstechnik und angewandte
Materialforschung IFAM jeweils ein neuer Ansatz / ein neues Verfahren vorgestellt.
Abweichendes Alterungsverhalten einzelner Zellen Wenn eine Batterie ihr vermeintliches Lebensende erreicht hat und beispielsweise nicht mehr weiter als Traktionsbatterie verwendet werden kann, ist es zunächst einmal dienlich, festzustellen, ob allenfalls nur eine einzelne Zelle und nicht die komplette Batterie an ihrem Lebensende ist. Schliesslich könnte man in diesem Fall nur die defekte Zelle statt des ganzen Akkupacks ersetzen. Diese Ermittlung war jedoch bislang sehr aufwendig, wie Tom Rüther, Wissenschaftlicher Mitarbeiter am Lehrstuhl Elektrische Energiesysteme und am
Bayerischen Zentrum für Batterietechnik «BayBatt» der Universität Bayreuth, erklärt: «Die Entscheidung für die beste kreislaufwirtschaftliche
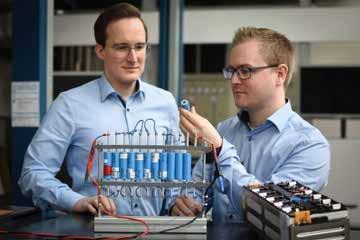
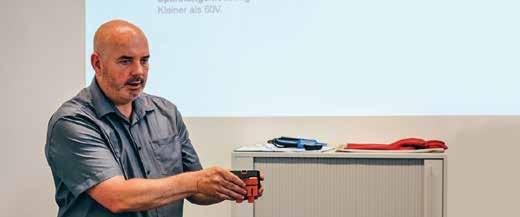
Option für gealterte oder defekte Akkupacks – das heisst zunächst die Reparatur, Wiederaufbereitung zur Weiterverwendung anstelle einer nachfolgenden stofflichen Verwertung – erfordert bisher umfassende Messungen, Analysen und eine entsprechende Datengrundlage.» Er hat jetzt gemeinsam mit Kollegen unter der Leitung von Prof. Dr-Ing. Danzer eine Alternative vorgelegt und die Erkenntnisse darüber im Fachjournal «Applied Energy» veröffentlicht. Aber von Anfang an; in Bayreuth arbeitet man nämlich innerhalb des BMBF-Projekts «ReDesign» des Kompetenzclusters «greenBatt» an Verbesserungen hin zur Kreislaufwirtschaft im Batteriebereich, wobei es vor allem um die Refabrikation von Akkupacks geht. Dabei werden einzelne (Teil-)Module oder Zellen ausgetauscht, die defekt sind oder ein abweichendes Alterungsverhalten im Vergleich zum Rest der Batterieeinheiten aufweisen. Allerdings konnte bisher eben nur anhand aufwendiger Messungen erkannt werden, ob eine signifikante Ungleichheit im Zustand der Akkus vorliegt oder ob alle Zellen gleich gealtert sind.
Neuartiger vergleichender Analyseansatz
Und genau diese aufwendigen Messungen am vermeintlichen Lebensende der Batterie werden nun durch
Digitalisierung obsolet. Dazu werden virtuelle Batteriemodule auf der Grundlage der Messung von einzelnen Zellen desselben Typs erstellt, die Schwankungen von Zelle zu Zelle werden zu Beginn der Lebensdauer bestimmt. Daraus resultiert eine Art «idealtypisches Batteriemodul» unter Berücksichtigung von statistischen Schwankungen.
Für die quantitative und qualitative Analyse sei das ein neuartiger vergleichender Analyseansatz. Die Merkmale der in Serie verbundenen Zellen werden dabei untersucht und mit denen einer ungleichmässig gealterten Verschaltung verglichen. Für die vielversprechendsten Merkmale wird eine detaillierte Empfindlichkeitsanalyse durchgeführt, bei der der Einfluss der Zell-zu-Zell-Variationen, der Alterungsbedingungen und des Alterungsmechanismus untersucht wird. Das Merkmal mit der höchsten Empfindlichkeit, das sogenannte niederfrequente Minimum, ist in der Lage, einzelne Ausreisser innerhalb einer grossen Anzahl von seriell verbundenen Zellen zu erkennen.
Somit würden erstmals gezielt Unterschiedlichkeiten innerhalb eines Akkupacks entdeckt, erklärt
Tom Rüther: «Wir haben damit eine Methode gefunden, um ökonomisch weniger aufwendig als bisher herauszufinden, ob ein Batteriemodul ungleichmässig gealtert ist, was uns neue Handlungsmöglichkeit bei der Bewertung von unterschiedlichen Kreislaufwirtschaftsoptionen gibt.»
Alterungszustand einzelner
Zellen der Batterie
Zur Untersuchung respektive Bestimmung der Gesamtlebensdauer der Batterie wäre es natürlich dienlich, wenn man die Lebensdauer bzw. den Alterungszustand jeder einzelnen Zelle kennen würde. Für die Alterung von Batteriezellen sind jedoch viele Faktoren entscheidend. Neben der kalendarischen Alterung, die hauptsächlich durch Lagerungstemperaturen und den Ladezustand während der Lagerung bestimmt wird, ist vor allem die Historie aller Lade- und Entladevorgänge mit den dabei jeweils aufgetretenen Strombelastungen und Temperaturen massgeblich. Die genaue Bestimmung des Alterungszustands ist deshalb komplex und bisher mit erheblichem Aufwand verbunden.
Bestehende Ansätze basieren entweder auf Simulationen, die eine vereinfachte Beschreibung des Batteriesystems und des Zersetzungsprozesses darstellen, oder auf experimenteller Extrapolation der Zyklenlebensdauer der Batteriezellen – wobei der empirische Zusammenhang zwischen