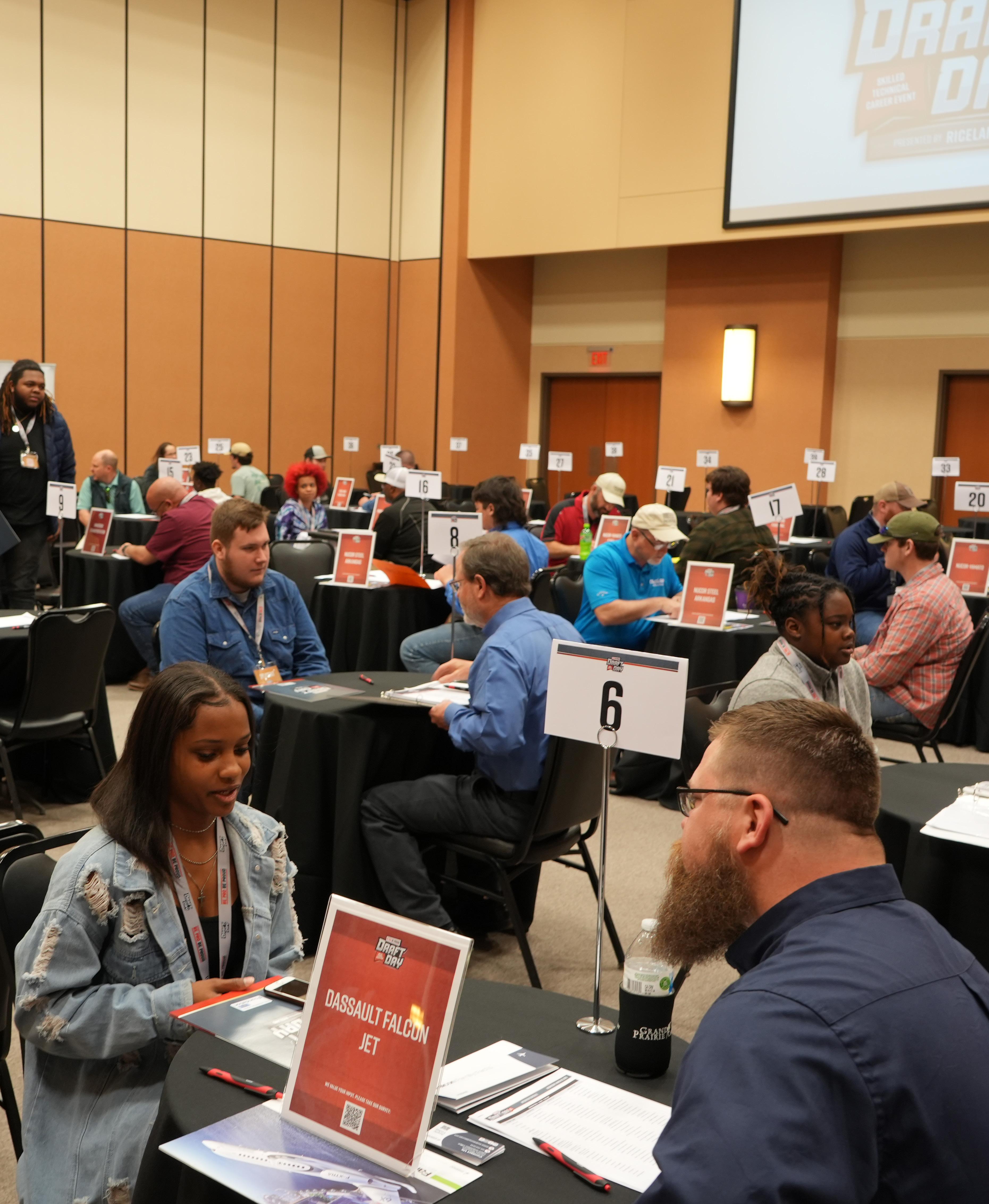
10 minute read
CallingBackupfor
In Arkansas and beyond, trade workers desperately needed
By John Callahan
Be Pro Be Proud’s Draft Day helps connect students with potential employers.
(Photos provided)
There are many unsung heroes that keep our economy rolling and make our way of life possible in the first place.
Many are the hard-working, blue-collar workers who quite literally keep the gears turning: mechanics, carpenters, millwrights, welders, electricians, plumbers and more besides. For all the good work they do, however, there simply aren’t enough hands on deck. Arkansas’ trade workers are calling for backup, and institutions across the state are moving full steam ahead to fill their ranks with new recruits.
“I would call it a crisis,” said Randy Zook, president and CEO of the Arkansas State Chamber of Commerce. “We have, depending on the source of information, somewhere between 75,000 and 100,000 open jobs in Arkansas. It’s a stunning number, sort of shocking when you hear it, but it’s true nationally. We’ve got about 10 million open jobs in America and only about 6 million people who are categorized as officially unemployed, so it’s nearly a 2-to-1 ratio of open jobs to people in the marketplace who are looking for these jobs.”
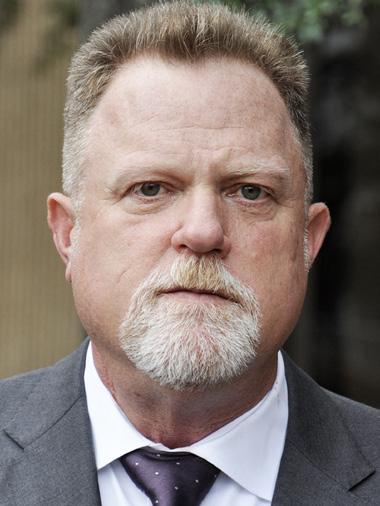
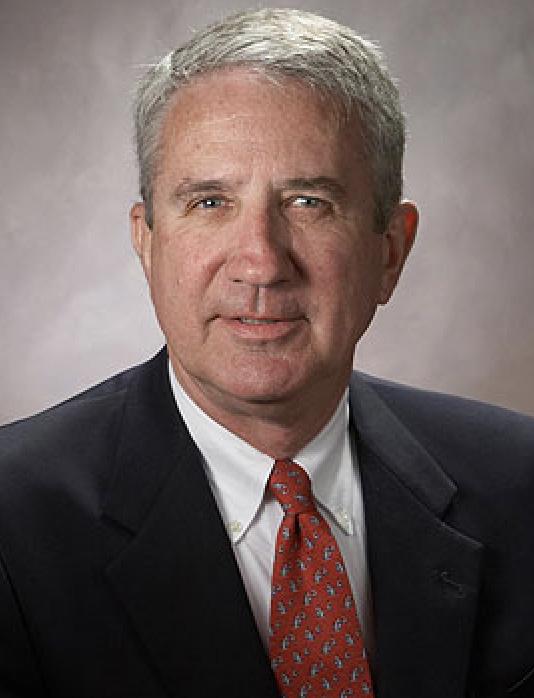
Nor is this crisis limited to any one industry. It runs the gamut from health care to construction, manufacturing to hospitality, the military to service industries. And as much as each of these industries has a need for its own type of skilled technician, there are trades such as plumbing that they all rely on in some form or another.
This lack of workers, both in sufficient quantity and quality, creates a significant bottleneck for growth across businesses of all types. For companies that deal directly in these trade jobs, they are unable to recruit and grow in response to the massive demand they face, while other industries may find their projects and expansions delayed for want of enough workers to get the job done.
According to Bryan Spradley, training director for the Arkansas Oklahoma Carpentry Apprenticeship, there are individual construction projects happening right now in Arkansas in need of 100 carpenters or more. Such shortages translate into lower profits, slower economic growth and lower tax revenue for government at all levels.

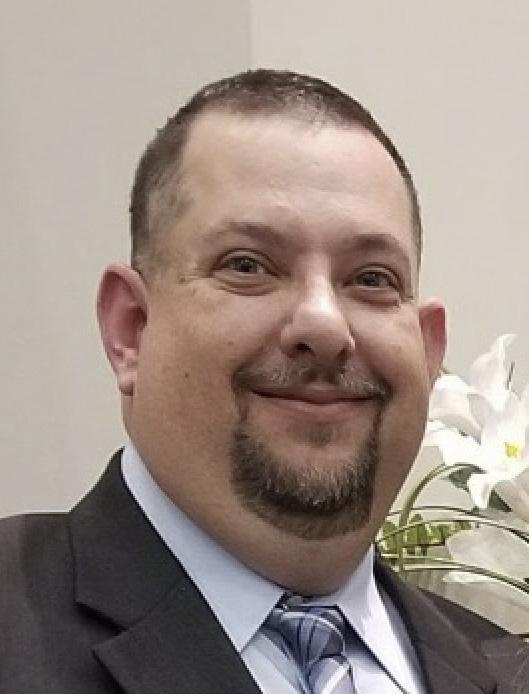
“Each week, we get a phone call from one of our local companies that says, ‘We need this skill set, can you help us?’” said Kendall Ross, executive director of the Center for Economic Development at the University of Arkansas at Fort Smith. “The truth is, there are not enough workers to go around to everyone who needs them. You can drive around town and pretty much see help wanted signs everywhere. So, I think the goal here now is, how do we help people get the skill sets they need in whatever position it is they’re trying to get into?”
Not only would an influx of new trade workers break open the bottleneck, but the potentially thousands of well-paying jobs with good benefits would be a strong economic stimulus of their own.
“You’d have more people able to improve the quality of their lives, you’d have more people able to support their families at the levels that include more and better choices,” Zook said. “Everything from what you eat to where you live, to what you drive and what you do with your time. It would make a larger economic pie in whatever area you’re talking about, whether it’s Arkansas or the country as a whole. We’d be more competitive, more attractive and life would be better.”
Of course, building a new workforce is easier said than done. Even if finding enough willing candidates was a quick process, training them would not be. Combine that with a declining birth rate and the fact that the baby boomer generation is rapidly retiring, and finding new workers is as much a race to replace old ones as it is to actually grow their numbers. Luckily, there are numerous programs across the state to help recruit and train the next generation of working-class heroes.
Among the most prominent and successful of these programs is Be Pro Be Proud, an effort launched in 2016 through the Arkansas State Chamber of Commerce to change perceptions around skilled professions and show that they can be a career of first choice, rather than a backup to a four-year degree path.
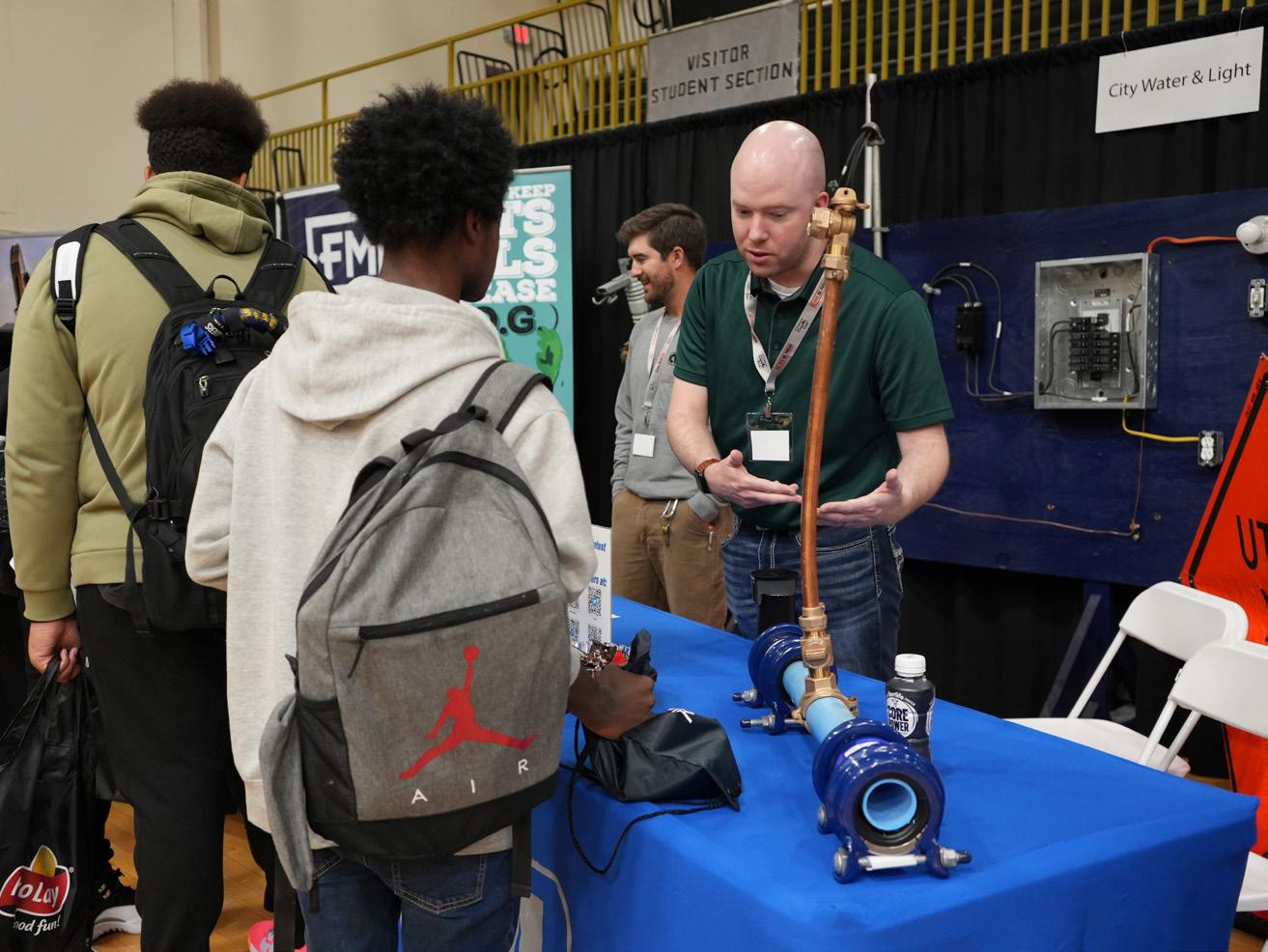
“We let our technical education capacity degrade over a long period of time,” Zook said. “[We thought] everybody’s supposed to go to college; well, that just hasn’t worked out very well. A lot of people don’t have to pursue a four-year degree, they can find above-average, high-demand wage jobs that don’t require that kind of preparation.” out of the approximately 175-day school year that they are on school campuses across the state. Roughly 20,000 students participate in the workshops annually, with Be Pro estimating that they’ve interacted with some 175,000 students in total.
Be Proud works to spread awareness of that idea, especially to middle- and high-school students, through two primary means. The first is Be Pro’s website, which shows students detailed information about a wide array of skilled professions, such as the responsibilities a profession entails, its average income in the first five years, average annual job openings and how long the training takes, as well as program resources, surveys and more. The second approach is, more fittingly, hands-on.
Once a student’s interest has been captured, Be Pro invites them to continue the conversation and get involved in technical training courses, as well as sharing their contact information with post-secondary training programs and employers. Be Pro provides them with workshops to prepare them for job interviews and prepairing resumes, which culminates in Draft Day, an event that directly matches students with prospective employers, setting them on an immediate career path after graduation. Of 771 seniors who participated in Draft Day last spring, 40 percent were offered jobs or invited back for follow-up interviews. In fact, Be Pro has been so successful that its operations have spread beyond Arkansas to Georgia, North Carolina, South Carolina, Tennessee and New Mexico.
“We have two mobile workshops: custom 53-foot, double-expandable commercial tractor trailers that have about 14 simulator stations on-board,” said Andrew Parker, executive director of Be Pro Be Proud. “They are virtual or fully immersive simulations that allow a student to experience what it would be like to train as a lineman, diesel technician, in robotics, welding, construction, CAD/CAM design, heavy equipment operation. We have a team young enough that they’re relevant to the students they’re talking to, but also have had some experience that makes them reliable for the information they give.”
These mobile workshops see plenty of use: 150 days or more
But just finding a prospective trade worker isn’t enough; they also need to be taught the skills necessary to get the job done right. A good place to start is one of the many educational institutions across the state, such as UAFS and its Center for Economic Development.
Established in May 2022, the center is actually a combination of three other centers: the Family Enterprise Center, a regional office of the Arkansas Small Business and Technology Development Center and the Center for Business and Professional Development. Overall, the center focuses on establishing an entrepreneurship ecosystem in the River Valley region through a variety of programs, including noncredit technical courses in fields such as advanced manufacturing, hydraulics, programming and robotics. Alongside these specialized
“hard skills,” the center also teaches more widely applicable “soft skills” useful in any profession, such as communication skills, emotional intelligence, work-life balance, ethics and integrity.
“We have a class called industrial electricity that’s happening right now,” Ross said. “We have a morning class and an evening class to help those people that might work in first shift or second shift to give them the opportunity to be trained at a time that’s more feasible for them. There are some lectures, but they are mostly hands-on in the classroom. We provide that training here on campus, but we also provide it at a local manufacturer if someone is interested in that. We’re in the middle of our welding upskilling workshop; it’s a workshop designed to take someone with no skills to be able to weld fairly well in just 40 hours.”
A growing number of two-year institutions have been improving the quality of their training programs in response to the industry’s demand, as well as working with other organizations to establish new apprenticeship programs that bring in more participants. Take, for example, the Russellville Training Center of the Arkansas/Oklahoma Carpenters Apprenticeship and Training Trust Fund, which is part of the Southern States Millwrights Regional Council of the United Brotherhood of Carpenters and Joiners of America (UBC).
The UBC has maintained a training center in Russellville for roughly a century, but a new location was constructed in 2021 to accommodate growth and provide for more advanced technology. Spanning 35,000 square feet, with 20,000 square feet of shop space, the new training center has earned visits from politicians on both sides of the aisle at state and national levels, such as U.S. Sen. John Boozman (R-Arkansas).
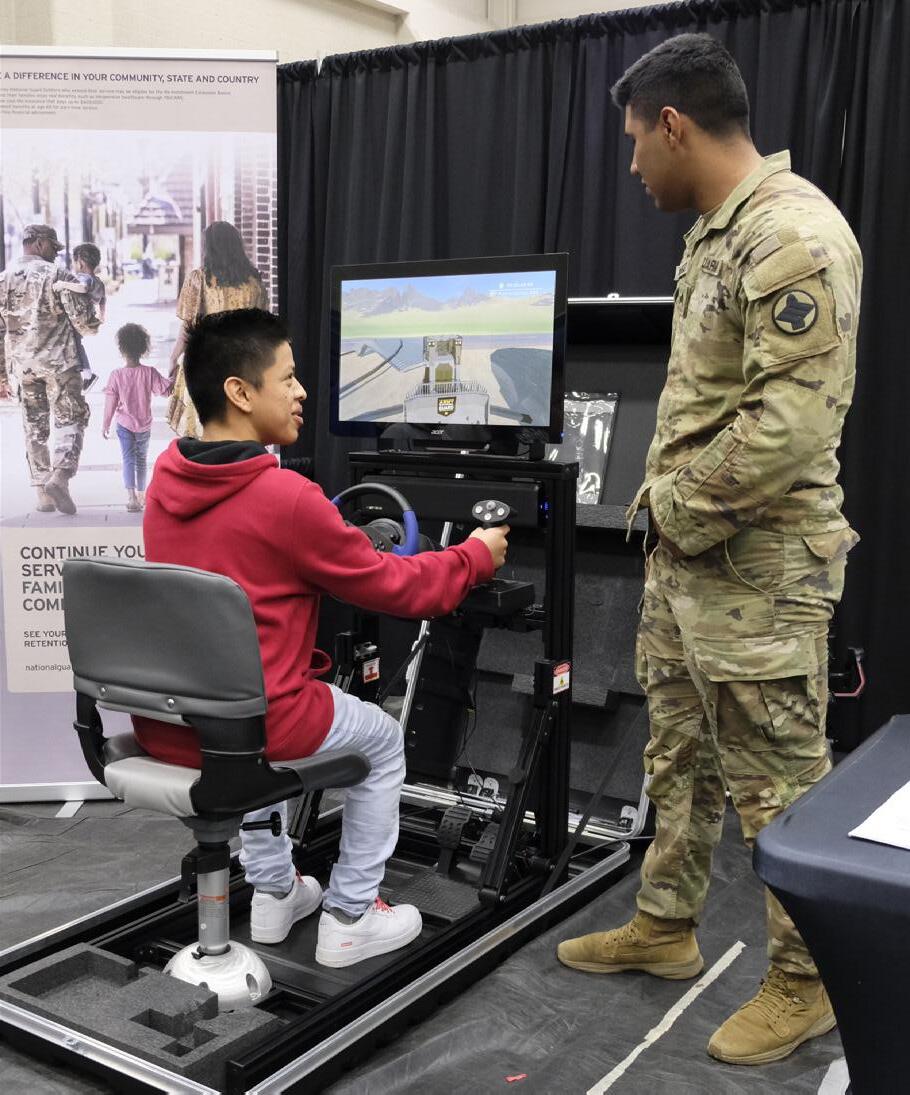
“We have a four-year apprenticeship program, and we train both carpenters and millwrights,” said Spradley. “For carpenters, we can teach anything from scaffolding to concrete forms to interior systems, which encompasses metal studs, drywall, ceiling grids and ceiling tiles, to how to read blueprints. We also have a medical aspect called ICRA, Infection Control Risk Assessment, where we can train our members, apprentices and journeymen to be able to go into a hospital and build containments during construction, ensuring minimal risk of infections, particulates and dust spreading throughout the facility.”

(Clockwise from top left) At Draft Day, students can visit company booths to find out more about what a career might entail; students from Watson Chapel operated a simulator on one of Be Pro’s mobile workshops; Gov. Sarah Sanders even tried her hand; the mobile workshops provide students the chance to get a taste of what it would be like to drive a truck, operate heavy machinery or perform many other jobs.
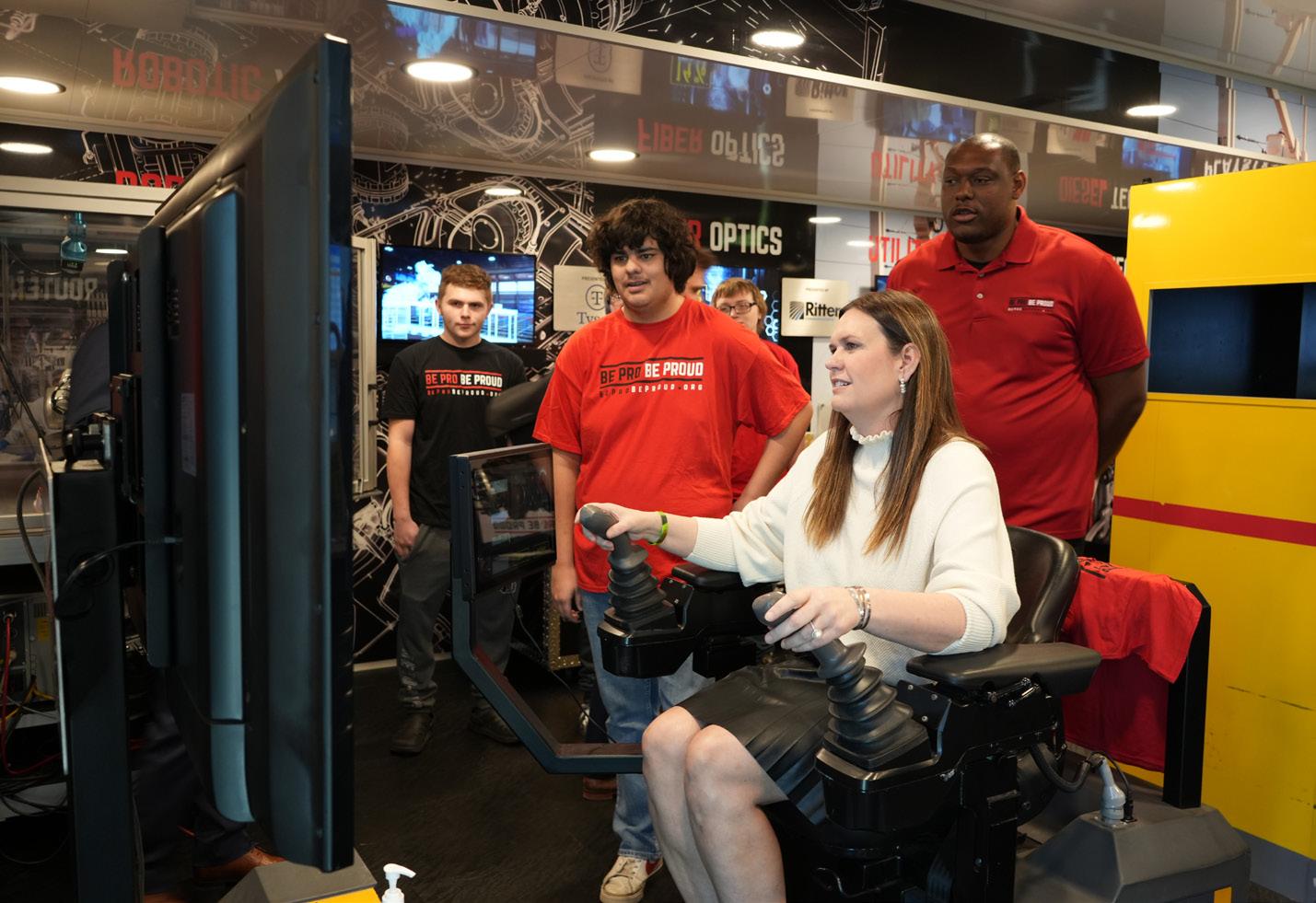
Just about anything a carpenter might need to know, the Russellville Training Center can teach, including OSHA safety standards, equipment training and first aid. Millwrights go through a similar program, learning how to weld, read blueprints and align or repair machinery used in everything from factories to nuclear power plants. The carpenter apprenticeship requires 576 classroom hours, with 800 for millwrights and a requirement of 5,200 work hours for both. Should one of the Regional Council’s 279 partner contractors require skills not covered by the standard apprenticeship, they can contact the training center to set up classes to teach them.
“I hate to say the word ‘train,’ because you train dogs, you educate people,” said Rick Halford, political director for the Southern States Region Council. “I like to call this an educational center, because we get them in here and educate them on the apprenticeship side, we educate them on the union side, teach them soft skills, educate them on their benefits and everything they need when they get out there.”
The Arkansas/Oklahoma Carpenters Apprenticeship is actively working to get people in the door, visiting career fairs, high schools and vocational technology centers. They also work with a UBC program called Career Connections, a curriculum that gives high school students a major head start in a carpentry career by providing firsthand experience before graduation, as well as teaching skills valued by employers such as teamwork, goal setting and taking the initiative. The UBC has even established training centers on some military bases, giving veterans a career path once they leave the military.
It’s clear that our society needs trade workers, but what incentive is there for an individual to choose a trade career? Beyond the simple satisfaction of a job well done, Halford and Spradley can vouch that it’s a well-rewarded career path.
“The average man hours per year per member in the 11 states in the Regional Council is 18,000. A 40-hour work week is 2,080 a year, but they’re working 18,000 hours a year,” Halford said. “A lot of that is overtime, so they’ll get paid time-and-a-half over 40 hours, depending on which contract, automatically time-and-ahalf on Saturdays in some places. There’s double-time on Sunday and holidays, so they make a good, substantial living. We have some apprentices that make over $100,000 a year; we’ve got some journeyman millwrights in certain areas that make over $200,000 a year.”
In addition to good pay, a worker with the UBC gets a suite of benefits like health care, a pension and an annuity, none of which come out of the worker’s wages. They are also largely able to choose how much or how little they want to work, though there is a minimum number of hours required to qualify for health care. Another plus is the near-certainty of demand; the need for skilled professionals will not end anytime soon, and even if work happens to be slow in Arkansas at any point, UBC carpenters or millwrights can find work anywhere else in the nation and keep their benefits.
If starting a trade career is starting to sound appealing, but you aren’t quite sure, it’s worth remembering that no career has to be life-long.
“Trades are solid work, but I would remind people that the average number of jobs people have is 12,” Ross said. “So, over the course of our lifetime, we’re probably going to have 12 different jobs that are going to look a lot different. So, I would always encourage someone who’s going to decide to do a trade, consider perhaps taking some classes in the evening or during the day when they’re not working so they can go ahead and get that degree. Perhaps later in life, they may want to change directions and then they’re well prepared to do that.”
The other side of the coin can also be true: perhaps you’ve started down a different career path and found it wasn’t what you thought it would be. If you feel like the life of a trade worker is calling to you, it’s not too late to make that change.
Though there are far more organizations and programs in Arkansas dedicated to recruiting and training tradesmen than are listed here, the great shortage of workers is proof that more needs to be done.
“I think you’re going to see a push for more public-private partnerships, that is, government, private sector and educational institutions working together. That would help all of us understand our needs, and we can design programs specifically for industry requirements,” Ross said. “I think Arkansas is doing a really good job in supporting workforce development, but I would love to see more financial incentives for businesses that are participating in workforce development programs. Any grants or tax credits to encourage more investment in training and hiring local talent would help keep people in the River Valley.”
“The bottom line is, we’ve got to do this in order to give our kids and our grandkids the level of opportunity they deserve and the level of opportunity that is required to continue to be competitive on a global scale,” Zook said. “We’re in a global contest for economic development. And the countries, communities, states and the people who prepare and make the right kinds of choices are the ones that are going to prevail. And we want to make sure that’s us.”