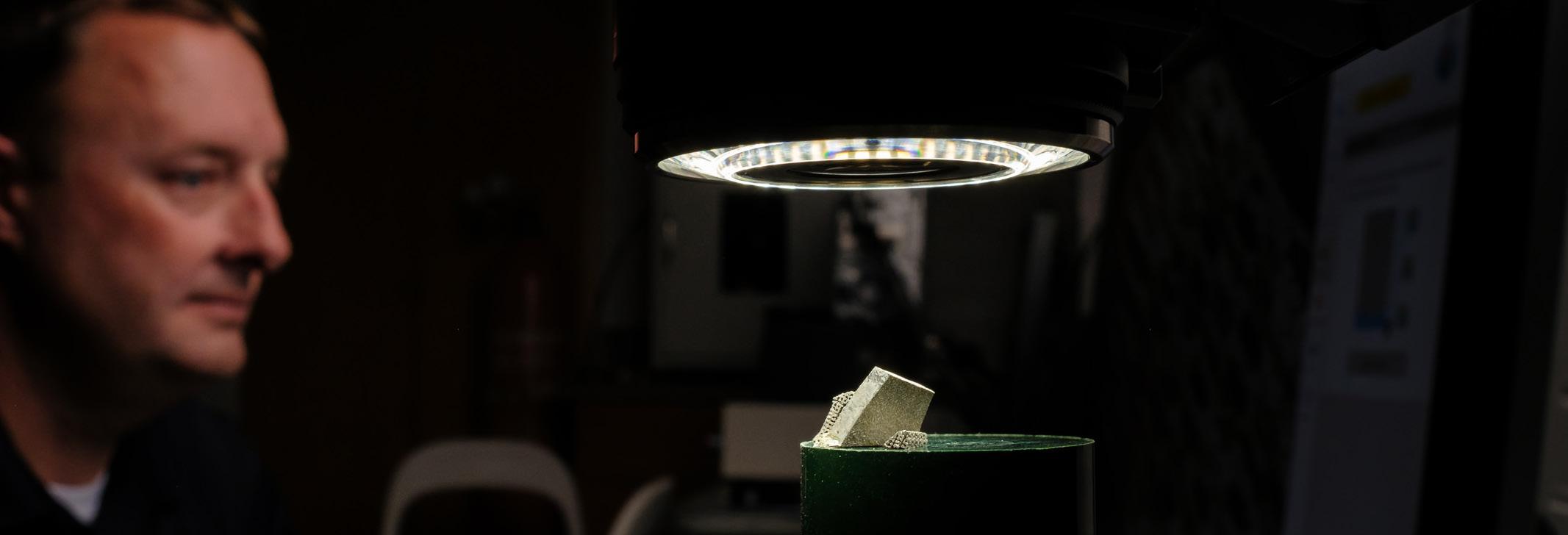
1 minute read
University Expands National Prominence in Hypersonic Flight Research
that are so nonlinear that they are not fully understood, and that we need to characterize if we want to design systems that work under these conditions.”
Consider how, when a car is moving at 80 mph, a one-second delay in the driver’s decision making can have catastrophic results. Hypersonic vehicles, which travel thousands of miles per hour and face additional factors such as shockwaves and extreme heat, have even less room for error.
To train hypersonic systems to navigate and react to extremely complex, highspeed situations on their own, the team – which includes researchers in engineering and the Space Systems Engineering Laboratory – is using a type of machine learning called metareinforcement learning.
“With meta learning, we can train it not only on one scenario, but on many scenarios,” Furfaro said. “By enabling this continuous learning, we are basically able to have a system that continually adapts.”
$1.2M to 3D-Print Parts for Hypersonic Vehicles
“Many conventional systems are designed using linear theory and are not designed to fly or intercept at that speed,” Furfaro said. “There are a lot of things happening in hypersonic flow
Not every material, or every shape, can withstand traveling at hypersonic speeds. UA professors are creating novel metallic alloys optimized both for the additive manufacturing, or 3D-printing, process and for the high temperatures and stress levels of hypersonic flight.
A $1.2 million grant from the Office of Naval Research’s Defense University Research Instrumentation Program will fund a suite of new equipment to support the work of Sammy Tin, department head of materials science and engineering, and Andrew Wessman, an assistant professor in the same department.
3D printing, or additive manufacturing, offers much more design flexibility than traditional manufacturing, allowing the creation of precise geometries that aren’t otherwise possible. It offers a new world of possibilities for the field of hypersonic flight, such as incorporating cooling pipes directly into the structure of a vehicle. Until now, most metal additive manufacturing specialists have used metal alloys that were originally developed for traditional manufacturing processes.
“If you try to take that same material, you can make it into a powder and then print with it,” Wessman said. “And it prints OK, but it’s not really optimal.”
The grant will fund the purchase of an array of instruments, including a powder bed fusion system, a gas atomization system, a vacuum furnace and an X-ray diffractometer.
“Combining all these pieces will give us a unique capability in terms of the infrastructure for advanced manufacturing,” Tin said.