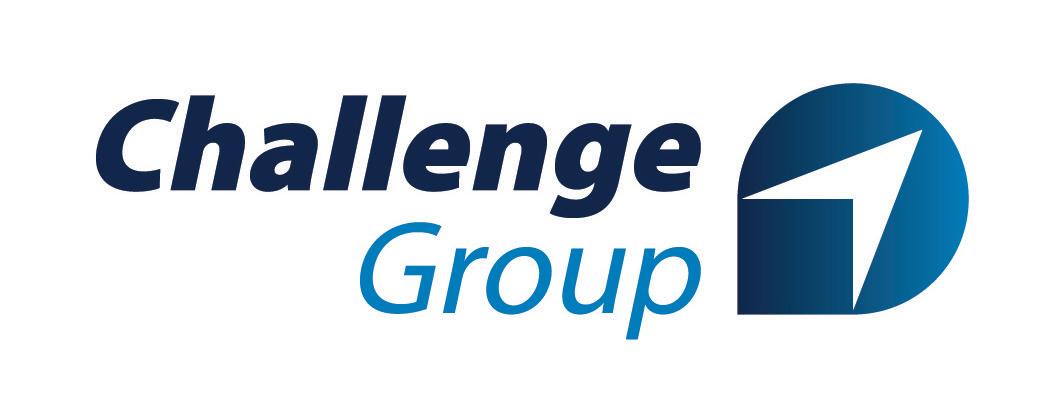
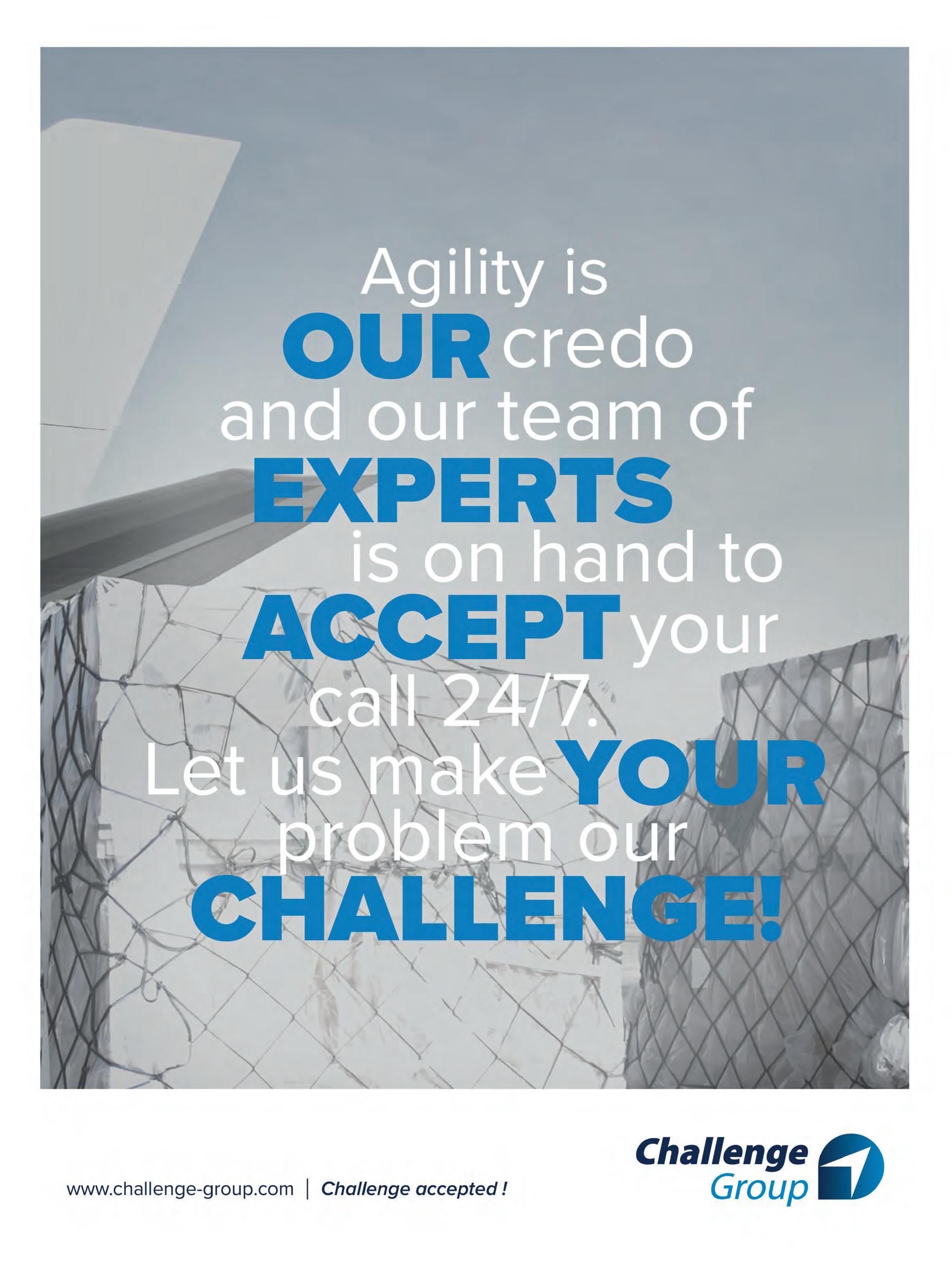
Your guide to the latest developments in the international airfreight industry

HANDLERS HELPING TO TURN THE APRON GREEN
HANDLING THE JOURNEY OF A PIECE OF CARGO
ALWAYS UP FOR A CHALLENGE
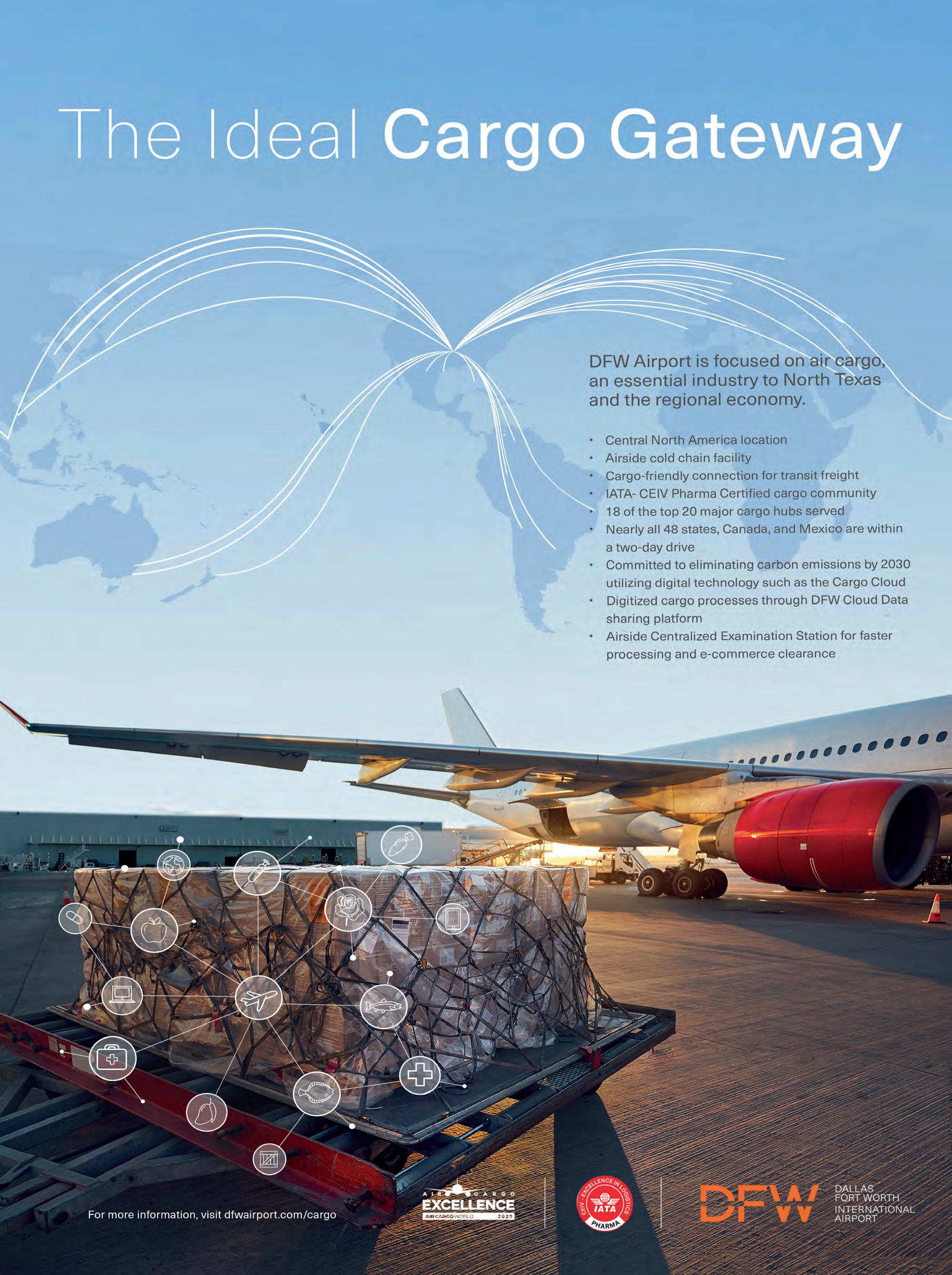
Your guide to the latest developments in the international airfreight industry
HANDLERS HELPING TO TURN THE APRON GREEN
HANDLING THE JOURNEY OF A PIECE OF CARGO
ALWAYS UP FOR A CHALLENGE
Witness the journey of a singular cargo unit as it embarks on its global transit. The orchestration of cargo operations unfurls through the concerted efforts of countless adept handlers dispersed across myriad airports spanning the globe. A paramount directive for ensuring an impeccably smooth operation and handling process comes from adherence to the industry-sanctioned Master Operating Plan (MOP).
Central to the intricate tapestry of the air cargo supply chain, cargo handling operations stand as its linchpin. Operational efficiency, epitomised within warehouse protocols, forms the bedrock of the sector’s work. Meticulous directives governing the acceptance and treatment of cargo delineate the pathway toward excellence. The safe manipulation of Unit Load Devices (ULDs), tantamount to integral aircraft components, is assured.
Architectural intelligence is tendered through recommendations aimed at the development of superlative cargo facilities. Propagating clarity on our operational capacities, we consecrate transparency, in turn enriching the panorama of customer interaction.
In the world of air cargo logistics, the loading and unloading procedures require a streamlined efficiency. Nonetheless, it is imperative to underline that an intricate web of rules and regulations binds the actions of cargo and ground handling personnel. A meticulous adherence to ramp safety protocols not only mitigates potential accidents but also plays a pivotal role in maintaining optimal aircraft turnaround times.
With the insights of the International Air Transport Association (IATA), the sphere of cargo handling constitutes a pivotal node within the broader supply chain fabric. This critical segment orchestrates the seamless transition of goods from landside to the cargo facility. From the inception of cargo at the originating airport through its preparatory phases for flight loading, to the eventual discharge at the destination and its transfer to the consignee or freight forwarder, the multifaceted aspects of cargo handling bear scrutiny. The orchestration of these interconnected steps is of importance to ensure the secure and punctual delivery of shipments.
The inception of the cargo handling process unfurls with the strategic booking and meticulous planning of shipments. This preliminary phase encompasses an array of pivotal tasks that must be meticulously executed prior to the actual departure of the cargo from the facility. The formulation of a robust action plan is the cornerstone upon which smooth booking operations are made. Such a plan prevents the emergence of complications downstream in the sequential cascade of events.
Upon the acceptance of shipments slated for transportation, dedicated personnel responsible for airport cargo and ground handling embark on the preparatory journey of readying air cargo for
its impending flight. An obligatory reiteration of security clearance for goods in transit ensues. Items retained within the aircraft during transit are classified as such, warranting comprehensive security checks by cargo and ground handling services. This rigorous assessment encompasses both x-ray examinations and the deployment of Explosive Trace Detection (ETD) screening mechanisms. An exhaustive evaluation encompassing the electronic Air Waybill (e-AWB), cargo integrity, and piece enumeration is subsequently undertaken. Upon the receipt of pre-plan specifics from the carrier, the meticulous preparation of a build-up plan ensues, serving as a roadmap for the assembly of air cargo to be embarked upon the flight. These salient particulars are communicated to the warehouse, thus facilitating coordinated actions.
Subsequently, strategically loaded ULDs are ushered into a secure flight holding area. This becomes a strategic juncture demanding utmost vigilance towards sensitive variables such as temperaturecontrolled consignments and hazardous goods. Adhering to a punctual and organised procession, ULDs are carefully aligned in an order conducive to subsequent ramp transportation arrangements. Throughout this meticulous manoeuvre, rigorous compliance with ramp safety protocols remains non-negotiable. The significance of this regimen is accentuated by the imperative need to mitigate accidents, a feat achievable solely through the unwavering awareness of all ground support equipment.
At this juncture, custodianship of air cargo transitions from the purview of the warehouse operator to the ramp handler. The seamless transference of goods from the cargo terminal to the aircraft is a multifaceted endeavour that finds its most cogent guidelines within the comprehensive repository of the IATA Cargo Handling Manual (ICHM). By assiduously adhering to the precepts, the loading of the aircraft follows with a meticulous load plan, duly considering the accommodation of special cargo. Upon the completion of this pivotal step, any disparities encountered necessitate swift rectification, culminating in the updated electronic flight manifest. This marks the threshold of the aircraft’s departure, underscoring that the culmination of the cargo loading procedure remains contingent upon the despatch of the flight manifest, the loading specifics and the carriage particulars.
Summing up, it is evident that the loading and unloading procedures within the realm of air cargo administration are notably succinct in comparison to the intricacies observed during the shipping processes. However, it is paramount to recognise that the panorama is fraught with a labyrinthine array of rules and regulations that demand scrupulous observance by cargo and ground handling personnel. The bedrock of this operational domain hinges upon an unwavering commitment to ramp safety protocols, executed with a methodical precision that removes accidents and bolsters the stipulated aircraft turnaround timelines.
Editor: James Graham
Associate Editor: Chris Lewis
Director of Operations: Kim Smith
International Sales Director: Rosa Bellanca
International Sales Executive: Zainab Khalid
Finance Manager: Rachel Burns
Video Director: Michael Sales
Design & Production Manager: Alex Brown
Production Supervisor Kevin Dennis
Website Consultant: Tim Brocklehurst
The views and opinions expressed in this publication are not necessarily those of the publishers. Whilst every care is taken, the publishers cannot be held legally responsible for any errors in articles or advertisements. No part of this publication may be reproduced, stored in a retrieval system or transmitted in any form or by electronic, mechanical, photographic or other means without the prior consent of the publishers. USA: The publishers shall not be liable for losses, claims, damages or expenses arising out of or attributed to the contents of Air Cargo Week, insofar as they are based on information, presentations, reports or data that have been publicly disseminated, furnished or otherwise communicated to Air Cargo Week.
INTERNATIONAL AZ URA
Twenty-five years ago, in the last years of the 20th century, many Cold War artefacts and locations throughout Western Europe were seeking new roles. An abandoned Belgian airfield outside Liège now plays an important role in the airfreight supply chain as the base of Challenge Handling.
Challenge Group’s strong presence in Belgium, particularly in Liège, is not just a testament to its strategic advantages but also a story of vision and growth. That is the opinion of David Alexis, general manager for Challenge Handling.
He says: “Challenge Group was the pioneer, believing in Liège Airport’s potential when it was an abandoned military base 25 years ago. Today, Challenge Handling, as part of Challenge Group, stands as the largest GHA at Liège Airport and our facilities cover an expansive 42,000 sq m,”
The facility houses over 700 dedicated professionals and a stateof-the-art ‘horse inn’. Moreover, Liège’s central location within the golden triangle of Frankfurt, Paris, and Amsterdam provides a pivotal advantage. In the past five years alone, Challenge Group has seen “an astounding increase” in handled tonnage, surging from 78,000 tonnes in 2012 to “an impressive” 282,000 tonnes in 2022.
Online and offline warehousing
Challenge Group has ‘online’ warehousing which are facilities located directly on Liège Airport’s apron where aircraft are parked right in front of the warehouse. In the south part of the company’s operations at B76, the handler provides services to third-party carriers and business partners. In the brand-new facility in the north side at B26, the handler deals with Challenge Group operations. ‘Online’ warehousing is optimised for immediate access to aircraft, ensuring efficient cargo transfer between the warehouse and the aircraft.
In contrast, ‘offline’ warehousing is situated outside the airport, typically at a distance, as is the case with the second line located approximately a kilometre away from the airport in the Liège logistics area. This is adjacent to the railway services that connect the EU with China. Here, all inbound cargo is handled and offered a comprehensive range of ancillary services as part of an end-to-end solution. ‘Offline’ warehousing is ideal for handling cargo that does
not require immediate proximity to aircraft. This solution allows for a more diverse set of services to be provided, considers Alexis.
An important key to the success of the operation at Liège is its 900 sq m of temperature-controlled storage. This is the thought of Alexis. He says: “Our temperature-controlled storage facility spans an area of 900 sq m and maintains a uniform height of five metres in both our online facilities. This space is meticulously designed to ensure optimal temperature and environmental conditions to safeguard the quality and integrity of temperature-sensitive cargo.
“Additionally, we have a dedicated fast lane in B76 that can accommodate two B747 freighters simultaneously. This specialised lane is particularly efficient in handling shipments, typically arriving from Africa, which are laden with perishable goods, including fruits, vegetables and fresh flowers. These goods are promptly processed and distributed to various key markets across Europe, maintaining their freshness and quality throughout the logistics process.
“Our cold-storage facilities are incredibly versatile, catering to a diverse range of cargoes. From pharmaceuticals, fresh fruits, vegetables, and delicate flowers to meat products, our temperaturecontrolled storage ensures that these goods maintain their quality and integrity throughout their journey. Moreover, our facilities are not limited to just perishable items; we also provide a secure and controlled environment for high-tech cargo like semiconductors and data centre equipment, safeguarding their functionality and performance. Whatever your cargo, we have the capabilities to store and manage it effectively to meet your specific needs.”
Within each of the Challenge Group facilities, the handler offers two floors of office space, providing a dedicated and efficient workspace for staff. These offices serve as the nerve centre for operations, allowing our dedicated teams to manage various aspects of cargo handling and logistics. In addition to office space, Alexis is only too aware of the importance of providing comfortable and functional staff facilities.
Europe’s largest capacity high loader
Possessing Europe’s largest capacity high loader, capable of handling up to 52 tonnes, provides Challenge Group with a
“an astounding increase” in handled tonnage, surging from 78,000 tonnes in 2012 to “an impressive” 282,000 tonnes in 2022”
“significant advantage” in the industry. “This powerful equipment is indispensable,” notes Alexis, “for loading large and heavy cargo, such as turbines and tools for the oil and gas sector. It becomes a compelling selling point, especially for charter flights and 40 ft ULDs, which are a common feature of our operations. This unique capability underscores our expertise in managing complex verticals, setting us apart in the market. While the advantages of this loader are substantial, one unit is sufficient for our needs. Maintaining and operating such specialised equipment requires specific training and dedicated maintenance: it’s worth noting that this particular high loader is no longer in production.”
The labour market in Belgium is currently shaped by a complex interplay of factors, including the lingering effects of the COVID19 pandemic, post-crisis economic shifts and changing social influences. These dynamics have led to a shift in values, motivations and engagement levels among job seekers. Moreover, the alignment between academic courses and private sector needs often falls short.
Alexis says: “The job market itself is evolving, with parameters like work-life balance and the desire for meaningful, engaging work becoming increasingly important, challenging traditional recruitment processes. Retention, especially among the younger generation, is a growing concern, as they prioritise job satisfaction and quick career changes. While our recruitment efforts at Challenge Group continue to yield dedicated talent, the landscape has undeniably transformed, ushering in a new era of workforce dynamics and uncertainties.”
As well as labour issues, Alexis has the rise of AI (Artificial Intelligence) in his sights. He considers the question that with the rise of AI, will we see a completely automated airfreight supply chain? If not, what will save the humans in the supply chain?
He says: “The rise of AI and automation in the airfreight supply chain is indeed a transformative development, and it’s plausible that we may eventually witness a predominantly automated supply chain in the future. The technology already exists, and the efficiency gains it offers are significant.
“However, it’s crucial to recognise that a fully automated supply chain may not completely replace humans. While certain tasks may be automated, the human element remains invaluable in several aspects of the supply chain. Humans bring creativity, adaptability, and problem-solving abilities that machines cannot replicate entirely. Furthermore, the socio-economic implications of a workforce entirely displaced by AI are complex and require careful consideration.
“As technology evolves, it’s essential for society to strike a balance between automation and maintaining meaningful human involvement in the supply chain, ensuring not just efficiency but also the well-being of the workforce. This is a multifaceted challenge that necessitates thoughtful decision-making on both technological and societal fronts to navigate the potential disruptions posed by this new era of industrial evolution.”
Challenge Handling operates as a neutral service provider, serving not only its own clients but also third-party clients, freight forwarders and e-commerce operators. According to Alexis: “Our commitment to neutrality ensures that our services are accessible and beneficial to a wide range of customers. These foster a competitive and inclusive environment in the airfreight industry.
“Challenge Handling plays a pivotal role within the Group as it serves as a cornerstone of our end-to-end solution. It is an essential enabler that empowers us to exercise full control over the supply chain. By efficiently managing cargo handling in-house, we not only ensure the highest levels of service quality but also achieve significant cost-effectiveness. This strategic element of our operations allows us to maintain a competitive edge and deliver comprehensive, seamless solutions to our clients.
“Challenge Group has the exclusive management of the horse inn, which is recognised as one of the finest in the world. This unique facility underscores our commitment to specialised cargo handling and positions us as a leading player in equine logistics.
“Furthermore, we are dedicated to innovation and sustainability, as evidenced by our investment in the development of a prototype horse trailer. This initiative aims to serve the broader Liege community, offering efficient and secure horse transportation services.”
“However, it’s crucial to recognise that a fully automated supply chain may not completely replace humans”
The “Ground and Cargo Handling Services Market - Global Outlook & Forecast 2023-2028” report has been added to ResearchAndMarkets.com’s range of reports.
The global ground and cargo handling services market is expected to reach a value of $43.8 billion by 2028 from $31.5 billion in 2022, growing at a CAGR (Compound annual growth rate) of 5.65% from 2022 to 2028.
Airports are actively developing modernisation plans and investing in mega modernisation projects to improve their infrastructure and services. For instance, the Sapa Domestic Airport Development project involves the construction of an airport to handle three million passengers per annum on 371 ha (916 acres) of land in Lao Cai, Vietnam. The project started in 2022 and is expected to
be completed in 2030.
The construction of various airports takes into account ground and cargo handling, supporting the growth of the global ground and cargo handling services market. Furthermore, the transportation of temperature-sensitive goods such as drugs, chemicals, and medicines has also increased demand for specialist cargo handling services.
Booming passenger numbers
The aviation industry is witnessing a trend towards larger aeroplanes, longer air routes and lower ticket prices than ever. The airlines are including newer aircraft and investing heavily to enhance the customer experience and make air travel more comfortable. Rising global travel is expected to act as an industry push factor, supporting the demand for the
global
market.
Ground handling services dominate the global ground and cargo handling services market owing to the increasing number
of scheduled passengers. In 2021, the total number of expected passengers travelling by airlines worldwide reached an estimated 22.2 million. The handling of passengers and their baggage remains the largest revenue segment
for service providers.
Moreover, the growth in scheduled international passengers, the development of new airports, and an increase in airport retrofitting activities are expected to boost the ground handling segment. However, at the same time, rising airfreight is expected to raise the demand for cargo handling services.
The cargo handling market is expected to witness the highest growth rate of over 5% in the service type segment during the forecast period. Cargo handling services are usually outsourced by airlines which deal with freight transportation by air. While most airlines are primarily passenger airlines, they partner with several e-commerce companies to offer belly cargo space to carry express shipments, including perishable items and timesensitive and temperature-controlled products.
North America dominates the global ground and cargo handling services market due to its well-developed airports with state-ofthe-art infrastructure to accommodate many passengers. North American airports have seen a surge of investment in new cargo
handling and air logistics capacity. Rising freighter traffic and congestion at the main hubs provide a particular boost for secondtier and cargo-focused airports.
Further, many major hub airports are also expanding their facilities after the strong performance of cargo has highlighted the potential for logistics investments and the shortcomings of some of these airports’ cargo facilities and infrastructure. For instance, Realterm, the parent of air cargo facility developer Aeroterm, is preparing for more cargo projects.
The global ground and cargo handling services market is highly concentrated, with many local and international players. The competition among these players is intense, and the industry witnesses both monopoly and fair competition. Entry to the market is generally based on regulations set by airport managing authorities.
State or federal governments often place entry barriers for multinational ground and cargo-handling service-providing companies to safeguard local airline subsidiaries. Some vendors in the global ground and cargo handling services market are Swissport, dnata, Menzies Aviation and Worldwide Flight Services.
“The global ground and cargo handling services market is highly concentrated, with many local and international players”
How the humble raspberry and cut flowers played a key role in field-to-market trials
The Cool Chain Association (CCA) unveiled a groundbreaking educational video on best practices for handling perishables during the Airfreight Pharma event in September. This initiative, based on valuable insights gleaned from recent trials conducted by CCA member, the Perishable Products Export Control Board (PPECB), marks a significant step forward in the industry.
Soft fruits, including blueberries, blackberries, strawberries and raspberries, represent high-value agricultural commodities that demand meticulous handling. A paramount challenge in the cultivation of soft fruits lies in the management of calcium mobility. Insufficient calcium levels can trigger internal breakdown and softening, resulting in diminished marketable yield, compromised transportation and storage difficulties.
In the realm of fresh produce logistics, temperature control emerges as one of the most pivotal considerations. This principle extends to cut flowers and all types of fresh produce alike. The preservation of quality and the prevention of wastage hinge upon precise temperature management during transportation and storage. A failure to maintain the correct temperature regime can lead to untimely ripening, spoilage and the erosion of flavour and nutritional value.
Moreover, it is essential to recognise that diverse types of produce have distinct temperature requirements. While certain fresh fruits demand refrigerated conveyance via trucks and containers, others can withstand transportation at ambient temperatures. The complexity of ensuring appropriate temperatures becomes particularly pronounced during extended journeys, while stored in transitional phases or when confronted with adverse weather conditions. Adherence to these temperature imperatives constitutes a fundamental facet of successful fresh produce supply chain management.
The instructional video meticulously distils the knowledge garnered from PPECB’s two pivotal perishables trials, which scrutinised the challenges faced in shipping raspberries and cut flowers from South Africa to the UK and Europe. It imparts essential guidance on optimal handling techniques aimed at safeguarding product integrity and extending shelf-life.
With a keen focus on achieving these critical objectives, the video delves
into various aspects of the perishables supply chain. It spotlights best agricultural practices, fresh air ventilation requirements, and strategies to combat taint issues. Furthermore, it offers invaluable advice on ensuring the thermal protection of perishable goods, encompassing everything from carton design and packaging to labelling.
The comprehensive guidance does not stop there; it also encompasses the intricacies of aircraft loading and transport procedures, as well as the importance of cold storage and precooling processes. Specific temperature recommendations derived from extensive trials are included to aid industry professionals.
Vijan Chetty, CCA board director and general manager of PPECB at Airfreight Pharma, emphasised the practicality of the initiative, stating: “We’ve distilled the findings from our recent flower and raspberry trials into an accessible format that the entire industry can benefit from. By adopting these optimal practices, the industry can significantly reduce the pervasive waste within the perishables supply chain.”
Given the success of their perishables trials and the resulting best practice video, the CCA is committed to further research and experimentation. They have announced a collaboration with Lamprecht Pharma Logistics, a CCA member, to embark on a new trial focused on pharmaceutical shipments.
Felix Johannes, commercial representative operations at Lamprecht, explained: “Lamprecht Pharma Logistics will lead a comprehensive pharmaceuticals trial in conjunction with the CCA. This trial aims to meticulously trace critical aspects of the pharmaceutical supply chain, pinpointing pain points for further performance optimisation.”
This eagerly anticipated trial is scheduled to commence in Q4 2023.
The Cool Chain Association (CCA) operates as a non-profit organisation, uniting all facets of the temperature-sensitive supply chain to drive tangible and measurable improvements for both companies and society. Their mission revolves around minimising waste and enhancing the quality, efficiency and value of the temperaturesensitive supply chain through collaborative efforts, education and innovation among members and stakeholders. The CCA serves as a community for professionals in the temperature-sensitive supply chain, offering thought leadership, networking opportunities and potential solutions to complex industry challenges.
“We’ve distilled the findings from our recent flower and raspberry trials into an accessible format that the entire industry can benefit from”
Air cargo handling’s green initiatives have a part to play in reducing the environmental impact of air cargo operations and improving the sustainability of the airfreight industry. The air cargo industry has recognised the need to address its carbon footprint and adopt more eco-friendly practices to mitigate the effects of climate change.
In the air, it’s all about sustainable aviation fuels (SAFs) made from renewable sources, biofuels or synthetic fuels. However, on the ground, cargo handlers can point to transitioning from conventional ground support equipment (GSE) powered by fossil fuels to electric or hybrid alternatives. Electric GSE, such as cargo loaders, produce fewer emissions and lower noise levels. Air cargo handling facilities are implementing energy-efficient technologies such as LED lighting, smart HVAC systems, and energy management systems to reduce energy consumption and operating costs.
Some cargo handling facilities are installing solar panels or utilising other renewable energy sources to power their operations, reducing their reliance on grid electricity and decreasing carbon emissions.
Data analytics and optimisation can also be called on to streamline cargo operations, reducing unnecessary fuel consumption and emissions. These tools can help in route planning, load balancing and operational efficiency.
One example of how key players are taking on eco-measures is Middle East-based dnata. It continues its efforts to meet a pledge of reducing its carbon footprint and waste to landfill by 20% by 2024 as part of its two-year green operations strategy. The company’s recent key initiatives include continued significant investment in infrastructure, green ground support solutions and process improvement.
In June 2022, dnata announced that it would invest $100 million in green operations in two years to further enhance its global environmental efficiency globally.
Steve Allen, CEO of dnata Group, said: “We are proud to have made significant progress on improving our environmental performance since the announcement of our strategic objectives. I thank each member of our team for their hard work and contribution to our green initiatives that help us make a difference across our global operations.
“We will continue our investments and efforts alongside our partners to further reduce our environmental footprint.”
In pursuit of heightened global resource efficiency, dnata has directed substantial investments towards the expansion of renewable energy initiatives. This encompasses the installation of rooftop solar power systems across the range of its existing infrastructure. Notably, dnata has successfully integrated solar panels into operational sites situated in Singapore and Australia, specifically at its SnapFresh facility.
This strategic deployment generates an impressive annual yield of more than 4,300 MWh of renewable electricity, consequently effecting a reduction of approximately 1.85 million kilogrammes of carbon dioxide emissions. Another promising development is Phase 1 of a solar PV panel installation in Pakistan, anticipated to deliver an annual output of 244,000 kWh. It is worth mentioning that the company’s procurement of electricity within the UK and Ireland is exclusively derived from local renewable grids.
Parallel to these renewable energy strides, dnata is taking decisive actions towards water conservation. Investments encompass the innovation and implementation of systems to capture and repurpose condensate from air conditioning systems, as well as rainwater, across both existing and future facilities. These strategic measures serve to optimise water consumption while effectively containing associated expenditures.
dnata’s projected or planned 20,000 sq m cargo facility in Iraq, scheduled for 2024, showcases its environmental commitment. This structure will feature a pioneering rooftop rainwater harvesting system, designed to capture, treat, and store rainwater within subterranean reservoirs. The harvested rainwater will serve irrigation and potable purposes, thereby projecting a 50% reduction in water costs by 2025. In line with this innovation, the company’s Philippines endeavour mirrors this technology, albeit with a focus on collecting and recycling rainwater for drinking and cleansing purposes. Moreover, dnata’s Singapore facilities are imminently slated to embrace similar advancements.
In arid climatic conditions, such as those prevailing in the UAE, dnata has proactively installed a Reverse Osmosis Plant to reclaim condensate water from cooling systems in the Dubai-based cargo warehouses. This innovation has enabled the repurposing of 5,000 litres of water daily for cleaning and sanitation purposes.
Notably, dnata’s commitment to sustainability extends to
“We are proud to have made significant progress on improving our environmental performance since the announcement of our strategic objectives”
operational aspects beyond energy and water. It has launched a pioneering bottle-free drinking water system across the corporate headquarters, dnata Travel Centre, and Alpha catering facilities. This groundbreaking initiative is anticipated to drastically curtail plastic consumption while preserving over 95,000 litres of bottled water annually.
With unwavering dedication, dnata is revolutionising its ground handling fleet by powering it with electrification and embracing biofuels where appropriate. Its global fleet has already transitioned to more than 15% of its fleet being electric power. It extends its support to ensuring partner airports are equipped for future electrification.
Emphasising a pragmatic approach, dnata understands that a singular focus on electrification may not suffice. Its strategy meticulously considers diverse factors including climatic conditions and infrastructure availability. Consequently, investment is undertaken in a diversified range of equipment, including biodiesel, electric, hydrogen and hybrid solutions, optimising both environmental and operational efficiency.
The handler’s role in vital winter operations in Switzerland has prompted the inclusion of five hybrid de-icing trucks in the ground support equipment (GSE) fleet. This move has propelled the proportion of electric GSE in dnata’s Swiss operations to 35%. Likewise, their Amsterdam operations have transitioned the entirety of the legacy GSE fleet to 100% biofuel, setting a pioneering example in sustainable transformation.
As part of an unwavering commitment to sustainability, dnata embarked on the IATA Environmental Assessment (IEnvA) programme in December 2022. Aligned with globally recognised environmental and sustainability standards, this initiative reinforces dedication to enhancing environmental sustainability across core operations, encompassing cargo handling, catering, freight forwarding and ramp handling. With aspirations of full certification by the end of 2023, dnata’s commitment to this programme is resolute.
In the fiscal year 2022-23, dnata accomplished over 710,000 aircraft turns, which facilitated the movement of more than 2.7 million tonnes of cargo.
“ With aspirations of full certification by the end of 2023, dnata’s commitment to this programme is resolute”