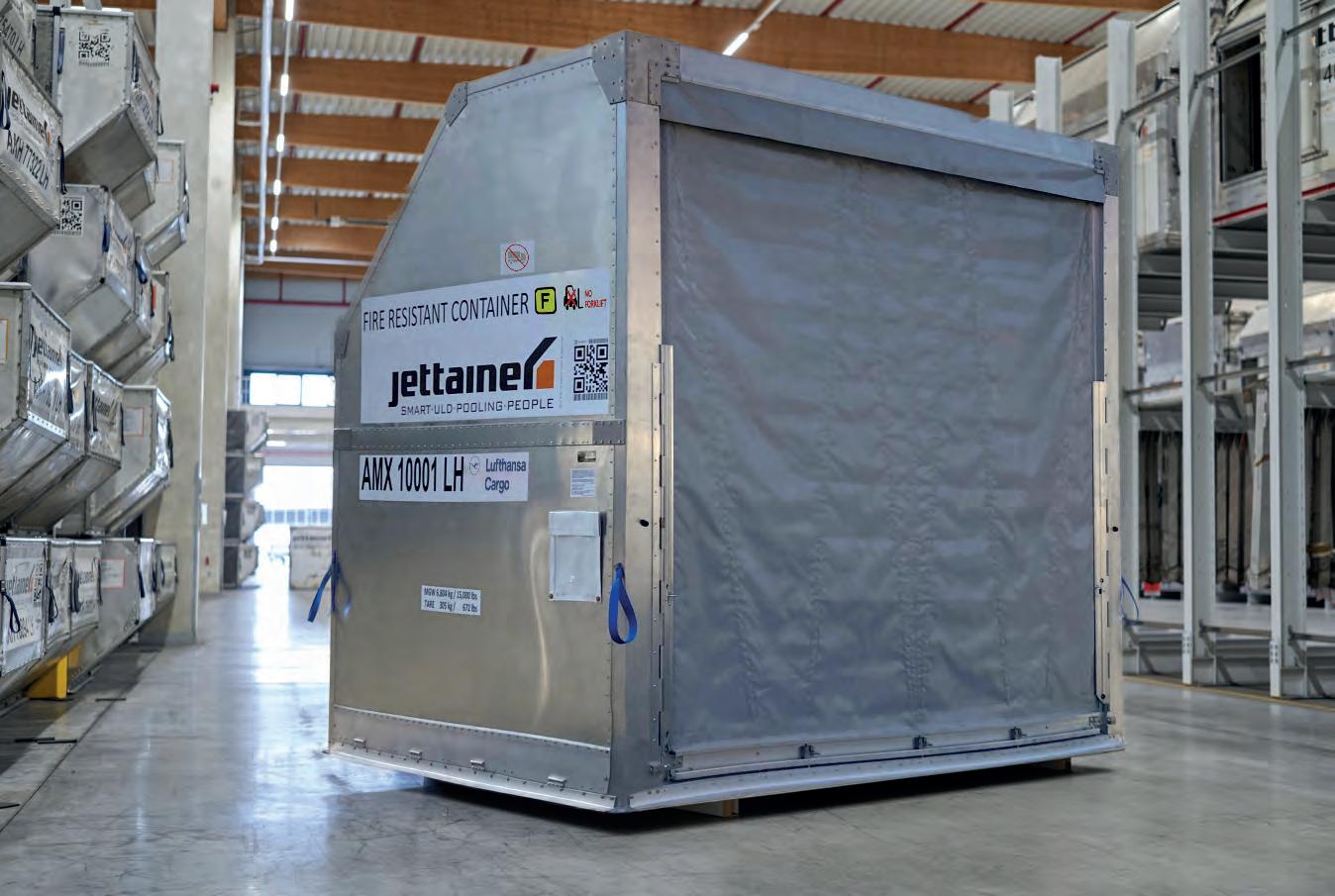
5 minute read
FIRST FULLY-CERTIFIED FIRERESISTANT CONTAINERS PUT INTO SERVICE
Satco, an American Unit Load Device (ULD) manufacturer, has introduced what it claims is the safest certified ULD on the market with its fire-resistant AMX model. Equipment lessor Jettainer, with over 100,000 ULDs in 500 locations worldwide that allows it to operate the world’s most efficient ULD fleet, has put these first fully-certified fire-resistant containers into service with Lufthansa Cargo, the first Jettainer customer to utilise these containers.
These fire-resistant containers (FRCs) meet the latest Technical Standard Orders (TSO) C90e specifications defined by the Federal Aviation Authority (FAA) and can contain a fire for up to six hours and provide crucial time for flight crews to safely land the aircraft in the event of a cargo fire.
Advertisement
Since the beginning of June, Jettainer has supplied Lufthansa Cargo with 50 of these ULDs. Marcus Bezold, head of global handling performance at Lufthansa Cargo, highlights their commitment to safety and praises Jettainer’s efforts in driving innovative ULD solutions. Thorough tests have confirmed the high effectiveness of Satco’s new FRC containers, and Lufthansa Cargo is pleased to have access to this solution through Jettainer.
Bezold says: “As a leading cargo airline safety is our top priority. That’s why we are constantly looking for solutions that reduce risks in freight transport. Our ULD management provider Jettainer makes great efforts to drive innovative ULD solutions. Thorough tests have confirmed that Satco’s new FRC containers are highly effective, and we are very pleased that we can now draw on this solution thanks to Jettainer.”
Frank Mühlenkamp, director global operations at Jettainer, emphasises the close collaboration with Satco, a renowned manufacturer with extensive technological expertise and a commitment to quality.
He says: “These new fire-resistant ULDs are setting new safety standards in the air cargo industry. By rolling out their use, we are once again underscoring our commitment to the highest quality and innovation. We always strive to offer our customers the most innovative solutions on the market, which make their supply chains more efficient and provide cargo in transit with the best possible protection.”
Air Cargo Safety Research Center
The Air Cargo Safety Research Center is a facility owned by Satco. The centre is the world’s first manufacturer-owned full-scale burn test facility dedicated to air cargo safety research.
Satco has been delivering ULD containers, pallets and textiles to the aviation industry for over 50 years. It has created the Air Cargo Safety Research Center to develop and test new designs for FireResistant ULDs (FRULDs). Satco recognises the importance of ensuring the safe transport of cargo, particularly hazardous materials such as lithium batteries. By conducting rigorous burn tests and collaborating with customers and industry experts, the centre aims to develop innovative FRULD designs that provide the best possible safety solutions for customers.
The facility’s full-scale burn tests allow Satco to simulate and evaluate the behaviour of ULDs under fire conditions. This testing process helps identify potential vulnerabilities and areas for improvement in ULD designs. By subjecting ULDs to intense heat and flames, the centre can assess their fire resistance capabilities and ensure they meet the highest safety standards.
The centre also serves as a collaborative hub, enabling Satco to work closely with customers, such as airlines and ULD management providers like Jettainer, to address safety concerns and develop tailored solutions. Leveraging insights gained from their airline customers and engineering team, Satco aims to deliver a higher level of safety through the deployment of Fire-Resistant ULDs.
Overall, the Air Cargo Safety Research Center demonstrates its commitment to advancing air cargo safety and innovation, claims Staco.
“By investing in cutting-edge research and development, Satco strives to provide the aviation industry with the most effective and secure ULD solutions, ultimately enhancing the safety of air cargo transportation,” says the California-based company.
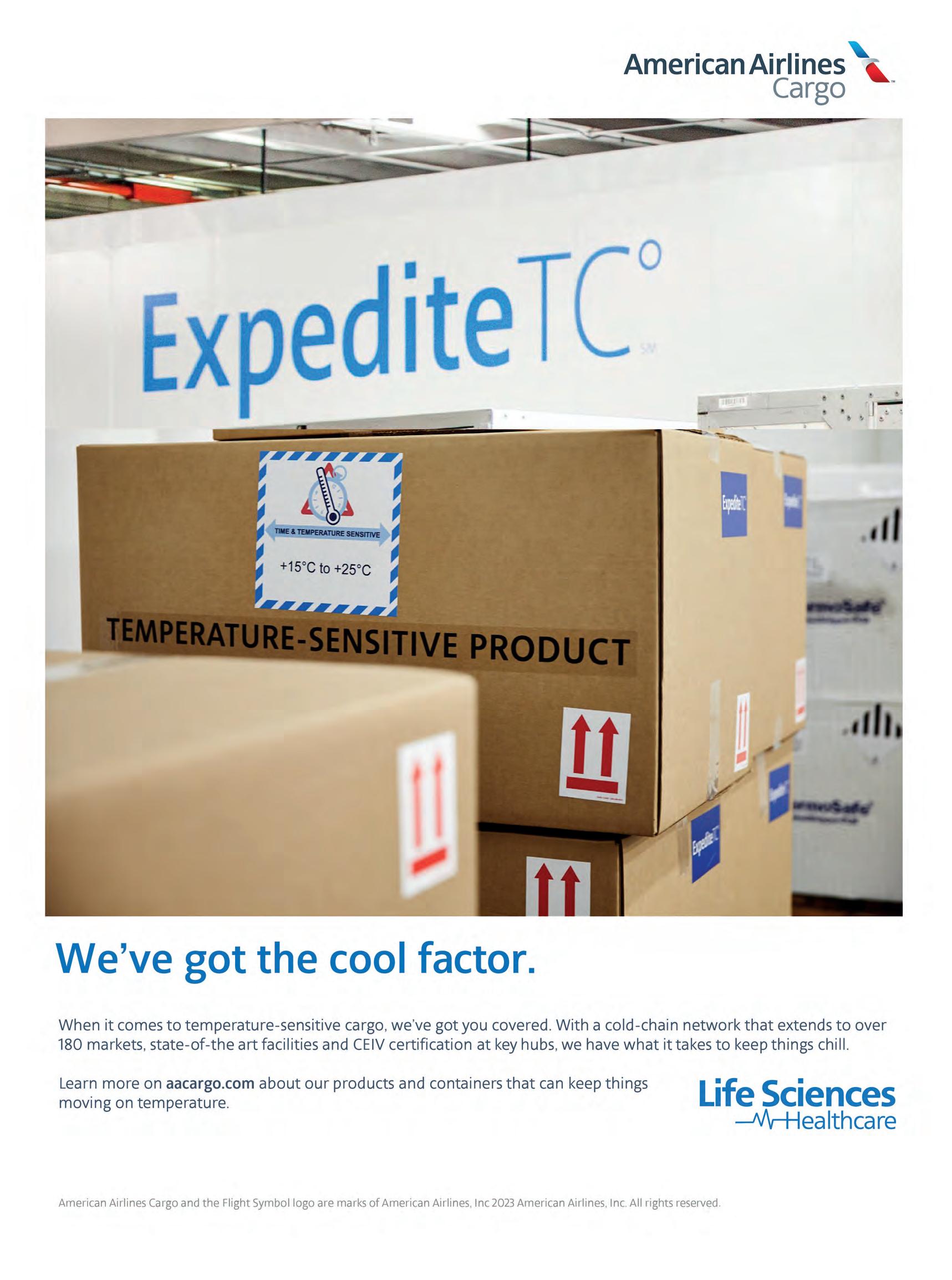
It all begins with a simple question - what sets ULD (Unit Load Device) lessor ACL Airshop apart from its competitors in the market? Given that the US-based operation is headed by a ‘Chief Encouragement Officer’ it comes as no surprise that its people rank very highly in its concerns.
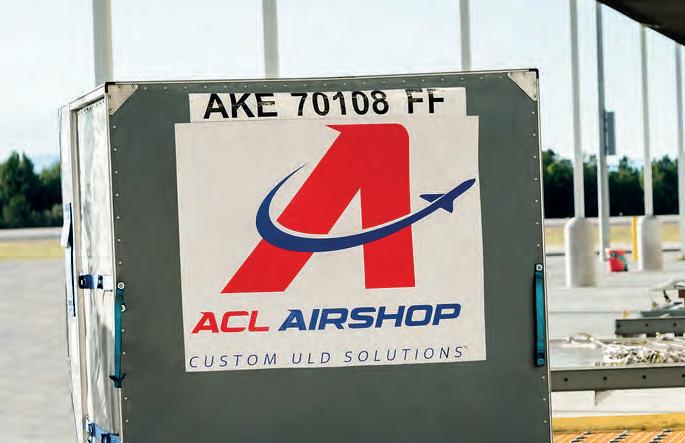
President and CEO ACL Airshop Holdings Inc Steve Townes speaks for a team of managers including Wes Tucker, executive VP and COOWestern Hemisphere, ACL Airshop; Jos Jacobsen, managing director global leasing and COO eastern hemisphere, ACL Airshop; Harold Elfring, director - technology and IT ACL Airshop.
The managers believe it is “not trite” to say it is ACL Airshop’s “unique high-performance culture. Yes, the secret weapon is our people and the working atmosphere across the whole company. Company culture trumps just about everything else - we see tangible evidence of that elsewhere in our competitive sector.”
Townes says: “The leadership and management climate in ACL Airshop is positive, nurturing, and encouraging. That tone has been imbued across the far-flung organization for 40 years so far, and we are continuously improving. Managers everywhere in ACL Airshop are reminded to focus on the ‘people factors’, take good care of colleagues and remain a strong and positive employer. Townes has said in numerous public settings: ‘People are the priceless soul of any successful enterprise, and we are proving that every day in ACL Airshop.’
“Our remarkable culture is the one thing that our competitors cannot easily duplicate.”
ACL Airshop primary focus
ACL Airshop is a technology-enabled global leader in air cargo ULD logistics solutions to over 200 airlines, air cargo carriers and other transportation clients. ACL Airshop owns, maintains and leases more than 70,000 ULDs, including airfreight pallets and containers, issued from 57 airport hub locations across North America, Europe, Asia Pacific, the Middle East and Latin America.
Its worldwide services network has expanded from 23 airport hub locations in 2016 to 57 at latest count, most recently in Istanbul with other locations in-work. ACL maintains the largest independent inventory of lease-ready ULD assets in the industry for short-term solutions and also has an array of longer-term ULD management contracts. Roughly half of its business is now in profitable multi-year contracts, while maintaining market dominance on short-term solutions. The company is deploying innovative logistics technologies such as “FindMyULD” which yield better fleet efficiencies and operational cost savings for customers. The company’s Manufacturing Centre and Repairs Division add strategic enhancements to customers as a one-stop shop for pallets, containers, straps, nets, and the logistics technologies to do more with less.
ACL Airshop’s five pillars
Airshop operates in five pillars of highly complementary business segments: ULD leasing, sales, repair, control and cargo products manufacturing. It was first-in-market with Bluetooth tracking and tracing. From a modest start 40 years ago with the air shipment of horses, it has evolved into a powerhouse enterprise with accelerated growth around the world.
Just a few years ago it was at 23 locations with around 24,000 ULDs. Now its 57th hub service capability is in Istanbul, with more in the pipeline for continuous expansion of its network. Its in-house ULD fleet has more than trebled to over 70,000 under ACL Airshop’s ownership and steadily expanding, yielding a total of over 100,000 that are under its management.
Real-time visibility of shipments
Air cargo technology enables real-time visibility of shipments through various advanced tracking and communication systems. By leveraging these technologies, air cargo stakeholders can track the location, condition, and status of shipments in real-time. This visibility improves operational efficiency, facilitates proactive decision-making, and enables better shipment management by providing accurate and up-to-date information about the shipment’s progress.
The company does not discuss partnering relations with airlines without their explicit approval but can say major names in airlines, air cargo, trucking and package express preferentially use ACL Airshop for its network size, inventory availability, useful technologies and “people factors.”
Townes says: “The service ethos of ACL Airshop has been refined and strengthened over four decades.” This is how ACL Airshop recently helped one of the fastest growing freighter operators in the world with issues they were having with ground handlers and freight forwarders at a gigantic hub. Experts swooped in and trained everybody on “FindMyULD” for free, acting essentially as “triage managers,” and within a few months that whole ecosystem of various critical parties all had the same sheet of music. A major global express delivery company has sourced the company’s uniquely-made cargo nets exclusively for nearly 20 years, though they could go anywhere for lower prices. Townes