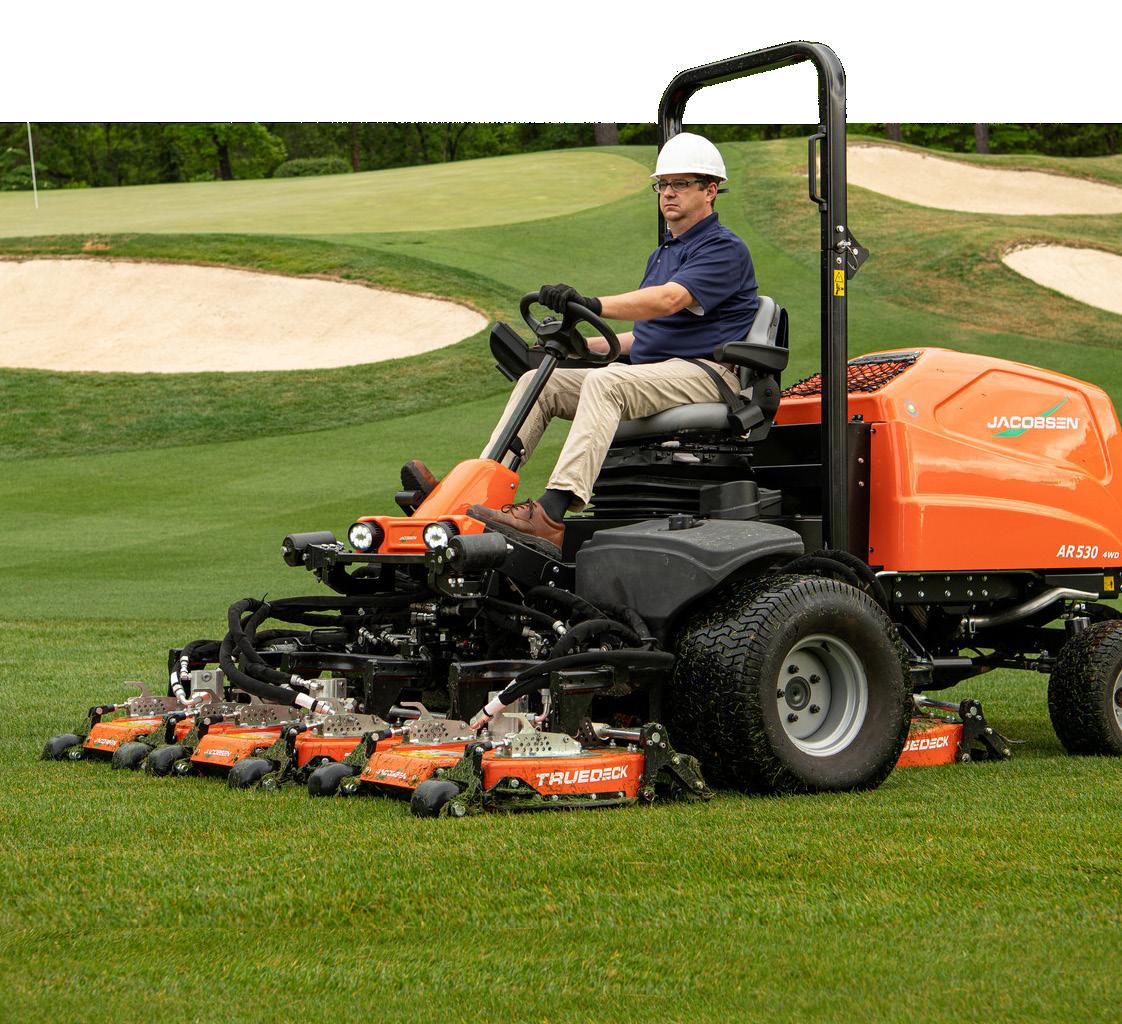
12 minute read
Technical
What next for landscape machinery?
During the 2020 Budget the Government announced it was considering removing the entitlement to use rebated fuel from most sectors – including landscape maintenance and mowing machines – from April 2022 onwards, to incentivise the development and adoption of greener alternatives. A consultation document at the time advised: For the Government to reach its objectives, it also needs to ensure that the tax system incentivises users of polluting fuels like diesel to improve the energy efficiency of their vehicles and machinery, invest in cleaner alternatives, or just use less fuel.
This statement represents a bitter pill to swallow for operators of dieselpowered equipment in the landscape industry, who are now required to run most machines on duty paid fuel whilst colleagues in the horticulture and agricultural sectors continue to benefit from the savings that use of rebated fuel provides.
For operators running ride-on mowers with diesel engines the only realistic option in terms of reducing environmental impact, adopting greener alternatives, and improving the energy efficiency of machinery - is currently to use less fuel.
Easier said than done for the landscape industry.
The industry has invested in greener technology where possible; most landscape contractors make use of battery technology in hand-held landscape equipment such as blowers, hedge trimmers and brush cutters as well as running a fleet of hybrid and fully electric cars and vans for staff.
Adoption of green technology for larger, ride-on equipment – the sort of equipment that uses an internal combustion engine – is a challenge for the industry; whilst a handful of manufacturers have released battery-powered pedestrian mowers, the industry has yet to see a batterypowered ride-on mower or tractor with the runtime to satisfy a busy landscape contractor.
While some manufacturers of construction equipment now offer a battery-powered option for small excavators and dump trucks, this technology is currently confined to equipment with relatively short duty-cycles. Ideal for digging graves in a cemetery, but not cutting hectares of long grass.
Research by the Association has revealed the landscape industry is caught in an awkward middle ground in terms of equipment development. Existing battery technology is not suited to the long duty cycle of ride-on mowers, while the relatively small size of the sector does not warrant the same level of technological investment the vehicle and large construction industry is benefitting from.
The Association has contacted manufacturers regarding release of new, green technology, but have not been provided with a clear indication of when affordable, green technology will come to market. The Association also recently met with a manufacturer of construction equipment, who confirmed they were developing hydrogen engines for larger construction equipment only, with no indication of timeframes.
In the absence of clear guidance from the Government or suppliers of equipment regarding introduction of greener alternatives, the Association contacted research institutions within the UK to investigate the likely timeframes associated with new, green technologies for the landscape industry.
Battery technology
Researchers believe the supply and use of battery technology such as that found in handheld landscape maintenance equipment will likely spread up to ride on machines over time. There are a couple of factors that back-up this theory: 1. There is currently huge demand at present for batteries as many automobile manufacturers develop new technology to fulfil the first wave of consumer demand for EV product. Battery factories take around three years to build and the supply chains longer, but many battery plants are being built all around the world with batteries that will, over time, be suitable for applications such as larger landscape equipment. Currently supply is limited, and prices are high for all, especially for those that do not have significant market leverage – such as the landscape industry. This situation will change over time as supply and demand settles. This period is likely to be at least 3-5 years from present day, when researchers expect more affordable supply of high-grade batteries to become available.
2. Battery chemistry and battery technology is improving at a significant rate. Researchers expect over time smaller machines are likely to adopt Lithium Iron
Phospate (LFP) batteries. These are lower cost than the technology currently going into mid/high end cars and offer greater cycling capability – ideal for landscape applications. As the technology develops it will provide better performance and lower cost to equipment manufacturers.
Hydrogen technology

Researchers believe hydrogen fuel cells and hydrogen combustion will be developed for heavy duty applications, but that this is unlikely to be commercially available until late 2020s/early 2030s. Researchers warn this technology may never be economically viable for smaller equipment due to high costs, but this may change in the future.
Industry moving forward
All avenues explored by the Association suggest alternatives to traditional internal combustion engines in landscape equipment are at least 5 years off, meaning operators are at the mercy of fuel prices for the foreseeable future.
In light of the burden placed on the landscape industry by the transition to duty pad fuel from April 2022, the Association met with government during May 2022 to highlight the plight of the sector once more. The Government were receptive to the Associations concerns and invited them to submit a suite of evidence in relation to this.
While the Government made no commitment in relation to future rebated fuel use by the landscape industry, armed with research carried out internally and data submitted by members, the Association will continue to look for a temporary solution that reflects the important role the industry plays in relation to maintenance of green spaces.
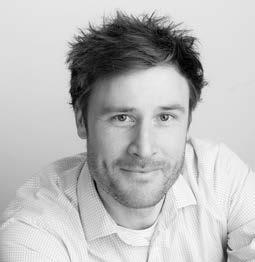
Owen Baker – Technical Officer (Policy & Research)
Working together to reduce industry accidents

The Association’s National Contractor’s Forum (NCF) is a specialist group set up to lobby on important issues and address key challenges within the land-based sector. In this issue of Landscape News we take a closer look at the huge strides that they have been taken to help make the industry safer.
What is the National Contractor’s Forum (NCF)?
The forum was established with the aim of furnishing members and their employees with knowledge and training, which would result in fewer injuries and accidents.
Its constituents are drawn from different sectors of the industry, creating a formalised group of influence. It provides the landscape management, maintenance and construction sectors with a structure through which they can communicate across and beyond the industry. Within this remit the forum aims to: • Develop training materials based on insight gained from the forum • Provide training courses to address specific areas of accidents and near misses • Work with manufacturers to develop safer products • Use benchmarks to compare landscape construction and maintenance with other industries • Share knowledge with the wider landscape and horticulture industries
Using data to drive positive change
Accident and near-miss data shared by members of the forum with the Association has enabled BALI to analyse and identify trends in accidents and near misses within the industry.
Thanks to the contributions of forum members, the data submitted has been of sufficient number and quality to allow detailed analysis. Over 12,000 near-miss and 1,000 injury records have revealed trends in accidents and near misses which have already been used by the forum to develop training initiatives. Of the accident data submitted, most are minor injuries, although more serious RIDDOR incidents are also logged.
Data collected by the forum during 2017 and 2018 revealed that, along with pedestrian mowers, hedge trimmers and brush cutters were responsible for the highest number of accidents and nearmisses. Consequently, together with Accredited Supplier STIHL, courses were developed to educate staff on the correct way of transporting, operating and maintaining hedge trimmers and brush cutters. This training resulted in a 52% increase in examination score amongst course attendees, which the BALINCF hope will lead to a reduction in accident numbers reported by members. This will be monitored.
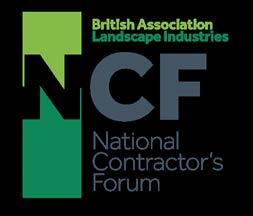
A slippery slope
The Association believes that there is considerable potential behind the analysis of accident and near-miss data. Initial analysis has revealed there are several common injury themes, which BALI would like to explore and raise awareness of.
Working together to reduce industry accidents
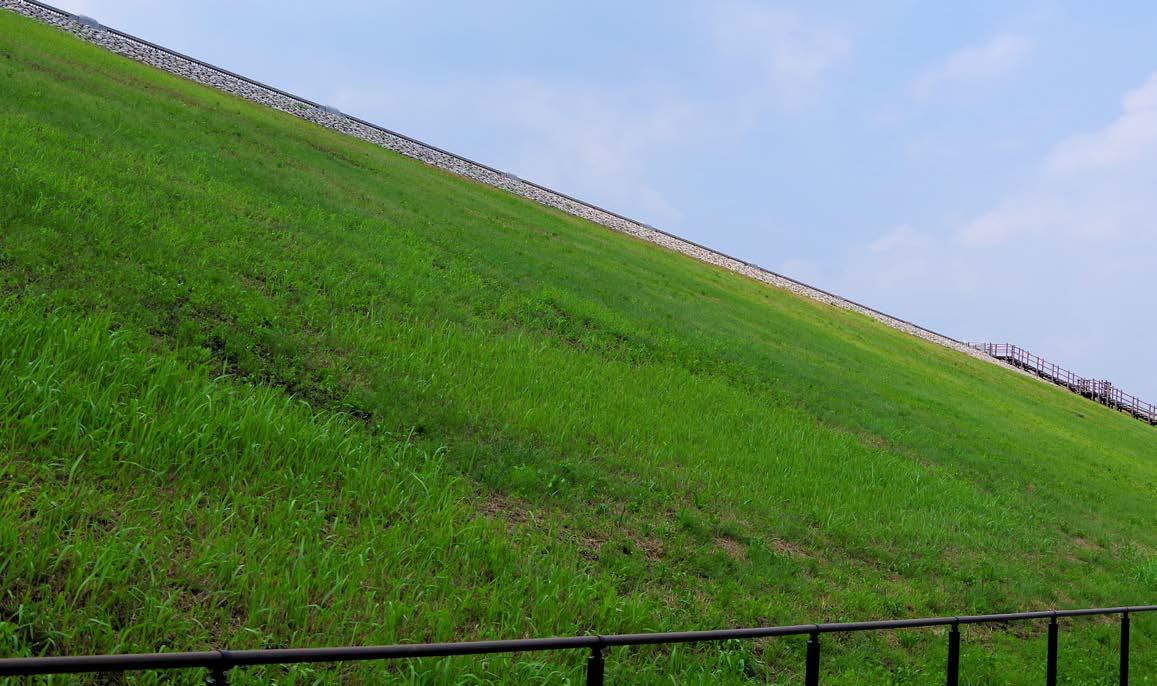
(cont. from page 32)
Recently members of the forum have turned their attention to the hazards of working on slopes.
The landscape industry is frequently challenged with maintenance activities that involve a gradient of some description. Maintenance of slopes cannot always be avoided or ‘designed out’ of operations; Association members maintain grass on a wide variety of sites, many of which require vegetation to be managed for the purpose of inspection, site security or amenity. Such sites include water reservoir embankments, underground defence installations as well as amenity slopes which form part of a park, housing estate or commercial development.
One thing that unites all slopes is risk. The variable nature of slopes means the risk they pose to operatives working on them varies accord to factors including: • Weather • Location in relation to other hazards (traffic, water course) • Terrain • Obstacles • Surface
The considerations facing those who either manage safety or undertake work themselves on slopes are numerous and require careful planning. The consequences of not managing the risk are serious; there have been numerous fatalities and serious injuries that have arisen whilst operatives have been undertaking maintenance activities on vegetated slopes.
The majority of serious or fatal accidents on slopes involve ride-on machinery. Incorrect operation has historically led to machinery overturning and injuring the operative or led to the operative coming into contact with moving parts.
Whilst the most serious accidents are reported to the HSE, it is likely many more less serious injuries or near-misses occur without record – with only luck protecting operatives if similar circumstances occur in the future.
Although information required to safely undertake works on slopes is straight forward, it can be elusive.
Guidance on the Health and Safety Executive website is not industry specific, nor does it provide sufficient instruction on correct procedure for assessing risks and devising a suitable method statement.
Provision of industry-specific guidance is something the Health and Safety Forum wish to develop over the coming year and join other industries who have worked with the HSE to jointly develop guidance which helps reduce industry accidents.
bali.org.uk/about/bali-ncf
Accident and near-miss data shared by members of the forum with the Association has enabled BALI to analyse and identify trends in accidents and near misses within the industry.
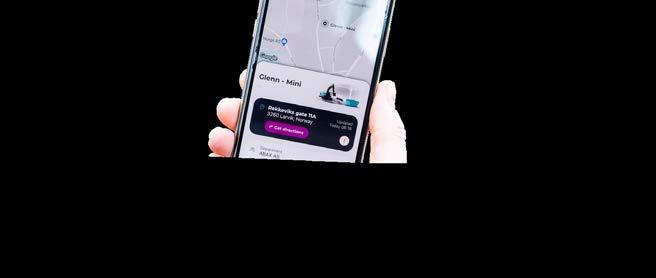
4 ways telematics can optimise your mixed fleet
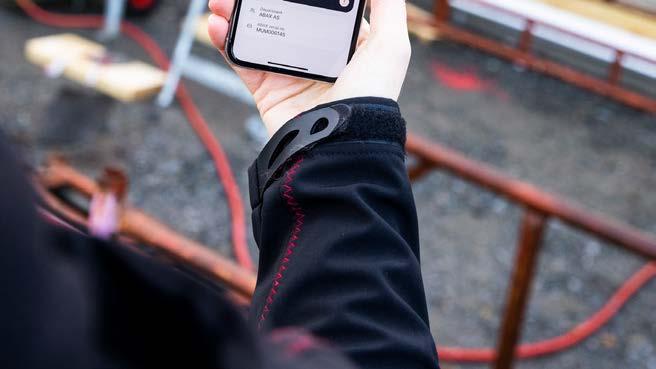
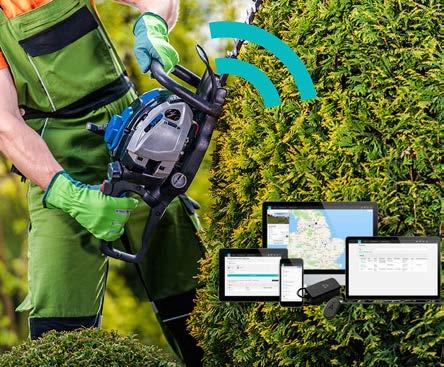
It can be challenging to stay ahead of the rapid advancement of technology, especially when you work in a sector like construction or plant hire. However cutting-edge telematic solutions like the one provided by Accredited Supplier ABAX will help you cut business costs while maximising profits – read on to see how.
1. Technology will do the work for you
Running a profitable construction company entails having the right equipment, materials and people together on the jobsite simultaneously, and the logistics to make that happen is time consuming.
A connected telematics solution gives you the insight needed for optimal planning by consolidating data from all fleet assets into one single interface, meaning you know the status of every single tool, equipment, vehicle and machine in real time.
Leverage your data so you can get: • Easy to run profitable projects • Cost savings – less fuel and no extra hardware • Maintenance control - less downtime for vehicles and machines • Asset tracking made easy to reduce loss and theft • Working hours verification and accurate timesheets or invoices • Overview of assets within a project • Machine data for a replacement strategy
2. Collecting data into one unified view
Wouldn’t it be nice to eliminate the stress of switching between platforms and using multiple logins?
By using a solution that delivers a unified view with one login, it is easier and faster to get an overview of all company assets in one map. Now you can get easy access to daily updates on driver performance, asset location, maintenance, fuel use and idling on all company vehicles and machinery.
Brand neutral platforms like the ABAX Smart Connect can be used as an add-on to the in-depth OEM data. Most operators and fleet managers will benefit by using both a brand neutral platform, for example, ABAX Smart Connect, which is ideal for a quick daily overview and user friendly reports, while machine administrators can still log into their OEM platform to gain deeper insight like error codes and diagnostics for repairs.
3. Asset tracking side by side with your fleet
There are other types of assets that aren’t technically part of a fleet, but are no less crucial to projects like excavator buckets, power tools, generators and pumps. If assets like that are left behind at a site or get misplaced, it will delay your project.
Fortunately, fleet managers can track these assets in the same platform as the main fleet. Depending on the size of the asset, there are multiple solutions available such as long term battery devices and Bluetooth tags that can fit your need.
4. Data will help you keep the engines running
Scheduled reports will allow you to shift from reactive fixes to proactive maintenance. The data pulled from your mixed fleet will give you a great insight to plan for upcoming maintenance and repairs, which creates a competitive advantage by keeping your largest investments fully operational.
Higher availability of equipment through optimised servicing, as well as a more efficient use of the machinery, helps your operation become more productive and profitable on every project.
ABAX telematics units are selfinstallable, provide HMRC compliant data and offer live-tracking solutions, all allowing you to access actionable location and usage data on all your assets – and via one easy-to-use interface. Mixed, large and small fleets can all be tracked in an efficient and cost-effective manner, whilst also provide vital reporting data on demand.
If you’re looking for your fleet to make financial and productivity savings, then ABAX could be the solution for you. Go to ABAX.com or call 01733 698888.
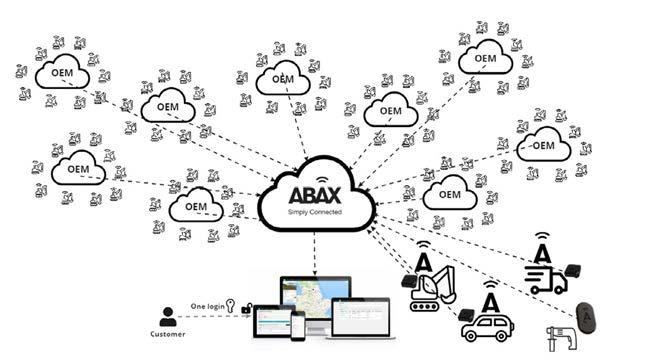