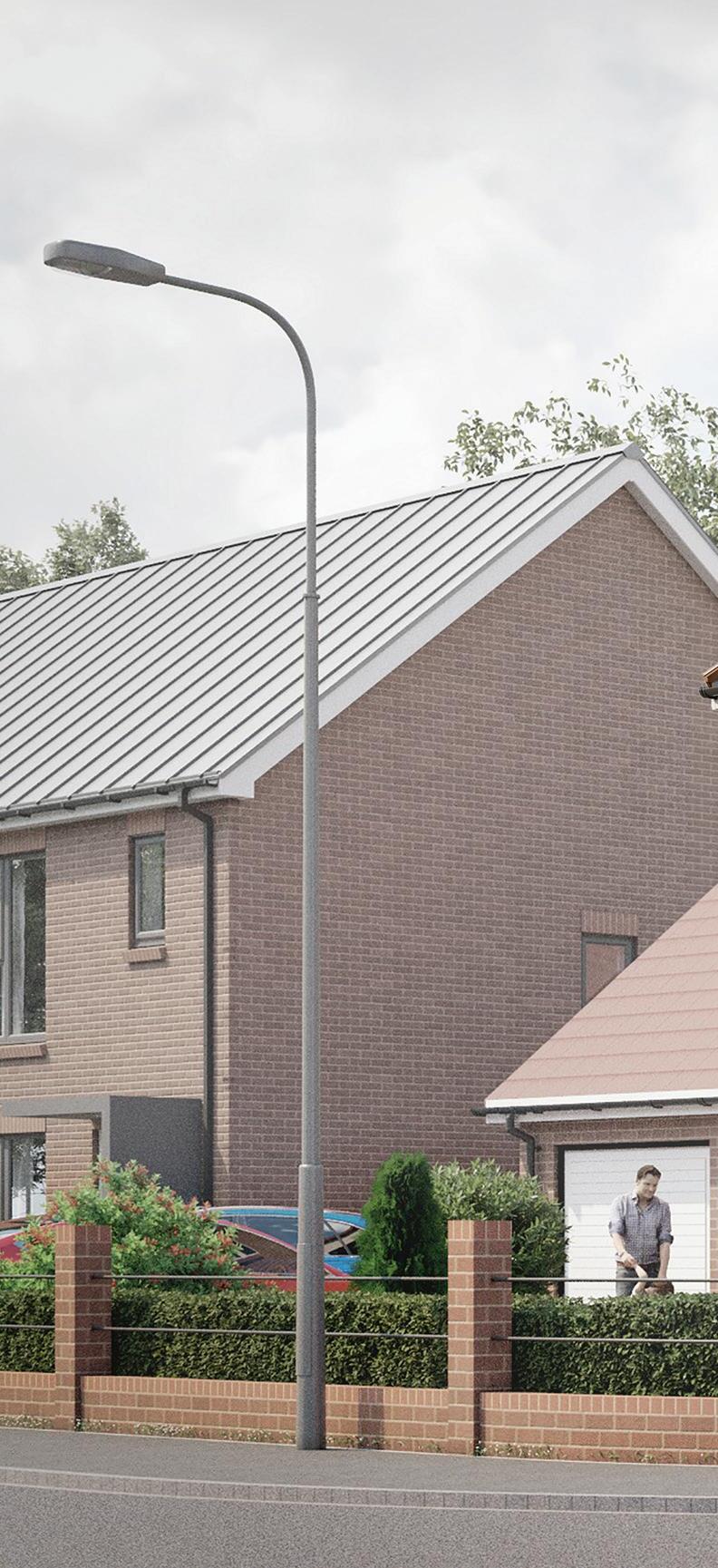
4 minute read
driving seat
This could be big. A major investment for Travis Perkins, WholeHouse is a first for the housebuilding sector, and it means that SMEs can now plan and design a bespoke digital model of a house before physically constructing it.
The model ensures detailed and accurate design, plans and material pricing from day one. Start to finish, the process can be completed in under an hour—saving weeks of work.
Based on BIM, WholeHouse has been developed by Travis Perkins over several years, in partnership with leading industry experts, including architects, engineers and planners, as well as customers and suppliers.
To contact WholeHouse directly, please email lee.jackson@travisperkins.co.uk
The portal is specifically designed for housebuilders building up to 250 units a year, and means they can bring plots and developments to life through 3D visualisation in designs that can be easily adapted, personalised and tailored depending on customer requirements.
When did the thinking for this start?
We’ve been working with partners on this for the last few years; there have been 40 manufacturers and 20-plus consultancies and designers involved in the wider design team, representing more than 500 years of industry knowledge.
In a sense, WholeHouse has been incubated over 15 years, and brings together the accumulated knowledge of the challenges facing SME housebuilders, manufacturers, subcontractors and customers. This is an industry where 2,500 players are collectively twice the size of the single largest player, but suffer from structural disadvantages. With WholeHouse, Travis Perkins is supporting them in being agile and flexible.
So, how does it actually work?
WholeHouse is based around a simpleto-use online portal that streamlines the design process, enabling builders to create costed construction drawings with accurate elevations, floor plans, specifications, cross sections and more at the click of a button—traditionally, many of these items would need to be manually costed from drawings and separate subcontractor quotes.
The platform, which works in real-time, collates and automatically processes all relevant information in one place and is fully compliant with the latest regulations and industry standards.
In under an hour, WholeHouse can supply housebuilders with an entire set of drawing sheets, up to 200 pages of construction details and a full bill of all the items needed to build a property, saving weeks on design development.
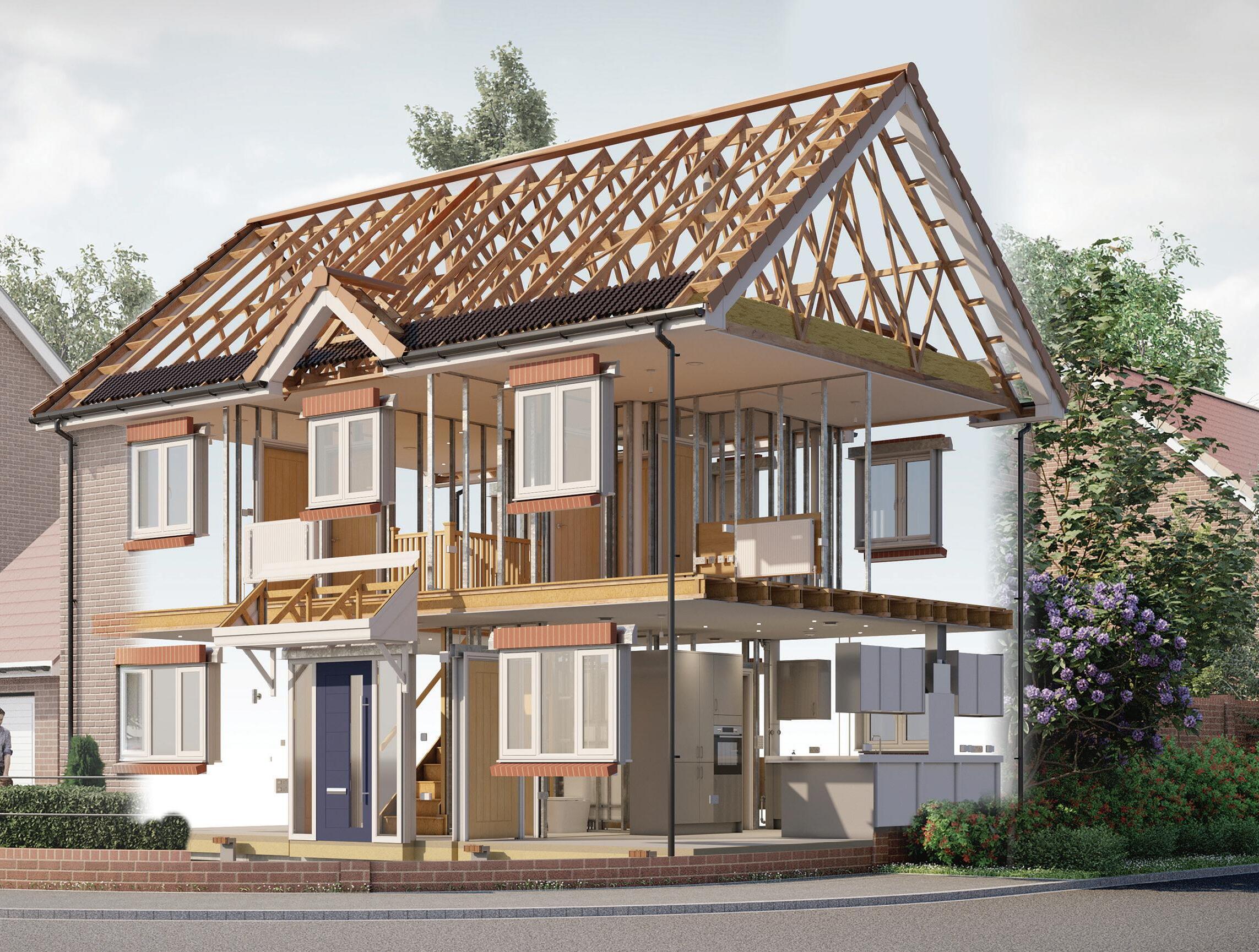
It also reduces risk greatly, which is what lenders want to hear—after all, they are the ones with money on the line.
It adds certainty, too?
It is common that a builder will start a house knowing only about 20% of the actual design is there; they’ll be working off a sheet of paper and the design has to come together ‘on the fly’. What actually gets built and when can often depend on whether the plumber gets in before the electrician or vice versa, and whether the right furniture or fittings are available on time. half a billion house types. That’s correct, half a billion. In a way, it is similar to a car configurator, with five chassis types providing the basis for a whole world of choice.
Too often when people talk about value-engineering it’s in a negative sense. This is quite the opposite. The model takes out cost by driving efficiencies, which can be reinvested where it adds value.
Such as where?
Is it important to note this is not a ‘standardisation’ process?
It’s absolutely true that this isn’t ‘standard’ in any way—SME housebuilders rightly pride themselves on not doing ‘standard’. Rather, the portal offers five basic footprints that can then be configured into
One of the potential benefits here is the ability to devote more time to the ‘hero’ plots within a development, those at the boundaries of developments, which need to respond to local nuances and character. With design time freed up, there can be more focus on these, they can be removed from the critical path; you can buy yourself time to get those designs truly mastered.
Future-proofing and flexibility is key. Design elements such as large windows in kitchen and dining room areas mean that should the home-owner want to extend in the future, that will be made easier, because creating that hole in the wall is often the largest cost. Similarly, extending into the roof space can be facilitated better.
A specific example of simplifying things is concerning door width; with one uniform size, it makes things considerably easier. Builders can always get hold of the supplies they need, without any danger of the programme being disrupted and housebuyers being delayed with moving in.
So, really, it’s about empowering the housebuilder and democratising BIM?
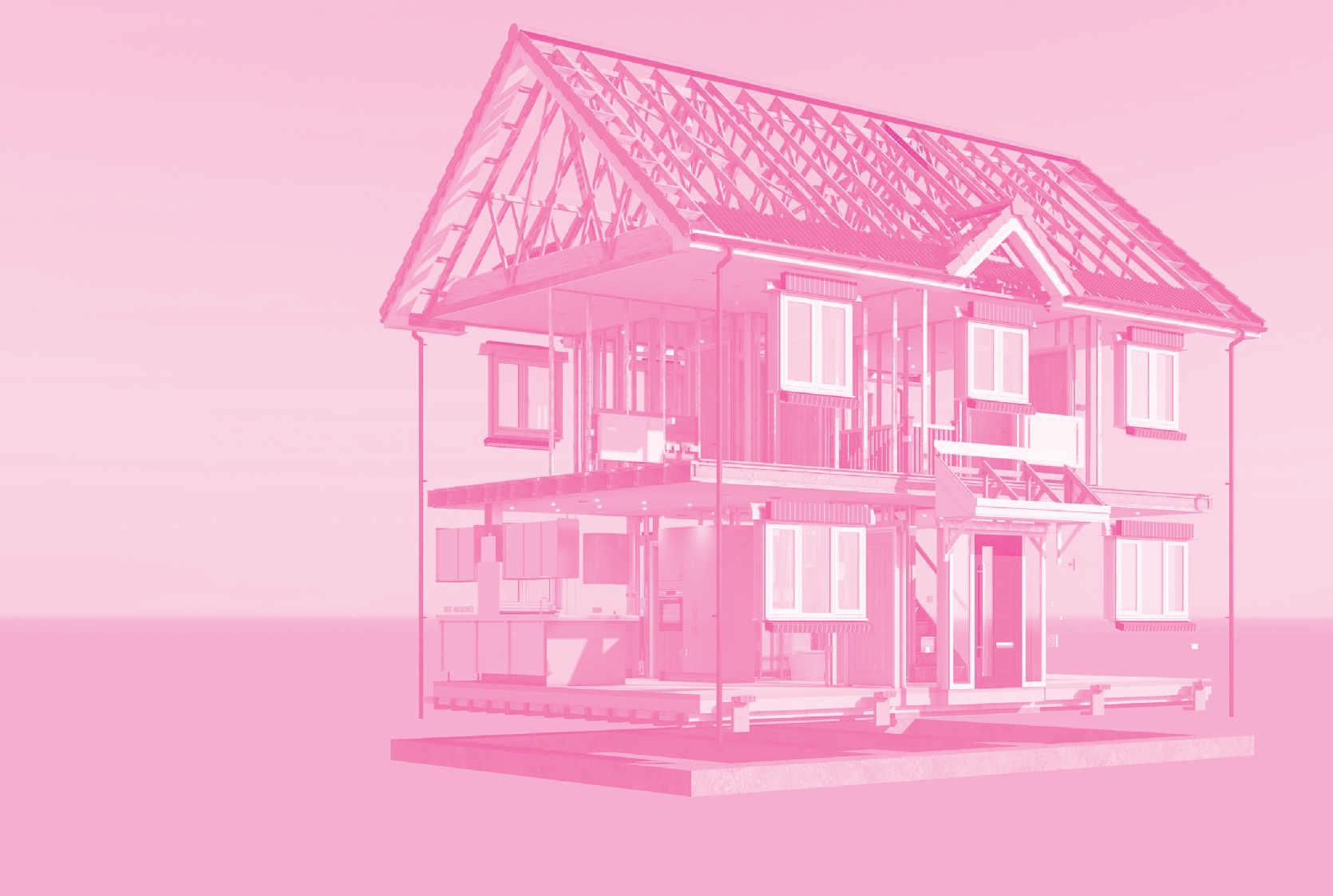
For housebuilders, as things stand, there’s a huge amount of risk in doing anything ‘outside the norm’. What this does is elevate the position of the SME builder in the process. It is a genuine
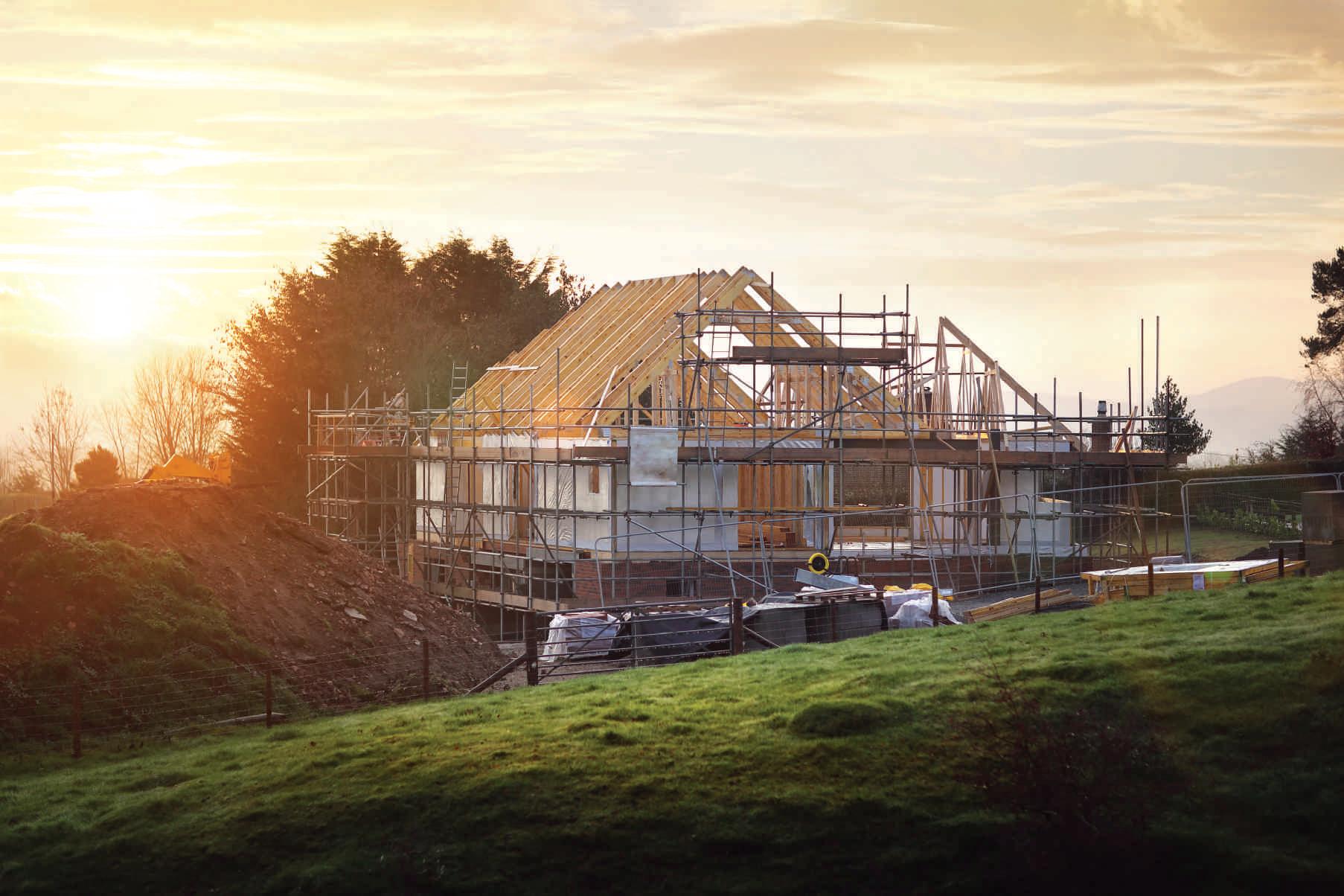
MMC (modern methods of construction) solution, but delivered in a traditional brick and block style, in a streamlined process that brings in principles from other industries.
In time, we intend to add in other build methods, but this moment is a line in the sand—a value-engineering proposition for building traditionally. Everything becomes an informed choice for the customer. It’s not about Travis Perkins saying, ‘This is the most efficient way to build’, rather, ‘This is what it will cost to do this, and what it will cost to do that.’
Ultimately, this brings digital construction technology to the regional housebuilder, because we believe digital design and BIM has a huge amount to offer to them. We’re not reinventing the wheel in how people work on site, but the future possibilities are mind-blowing: early adopters will be in a really strong place.
Being at the heart of construction, we take great pride in supporting our customers with new value-added services that help them to navigate an increasingly complex construction landscape with new legislation and decarbonisation targets.
WholeHouse will do just that, and help SME housebuilders, who are the lifeblood of regional property markets, to build better, more sustainable homes quickly and safely, whilst retaining control over the creative design elements and saving time and money.
How’s progress so far?
The WholeHouse launch went even better than expected; there’s really firm interest from people who knew a bit about what we were hoping to do, and real conversations are taking place now.
The first two homes built using the platform will be ready by September and are based in the Midlands. Extensive work has been carried out on pilot schemes across the country. The platform has recently won Best Business Product at the Housebuilder Product Awards.
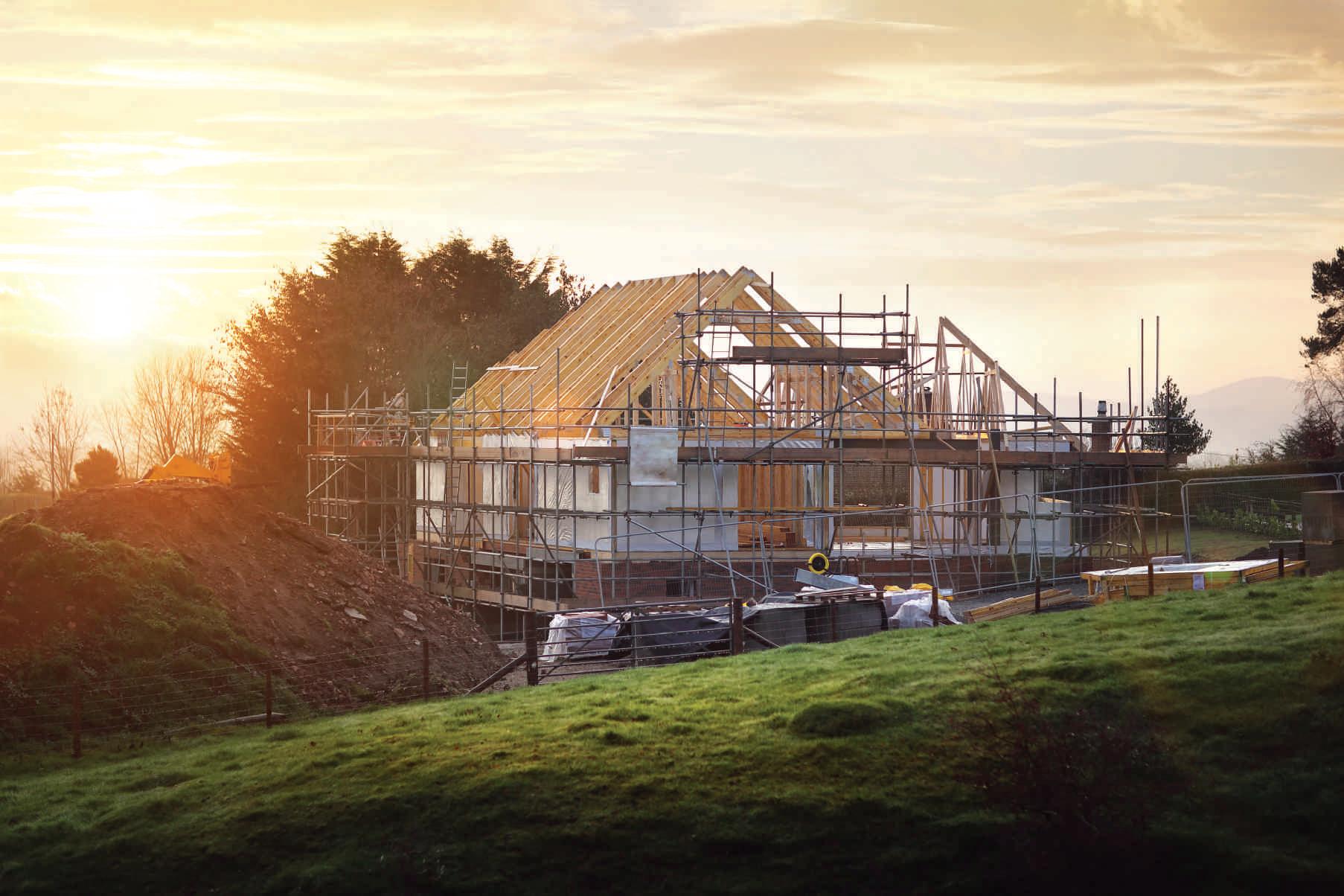