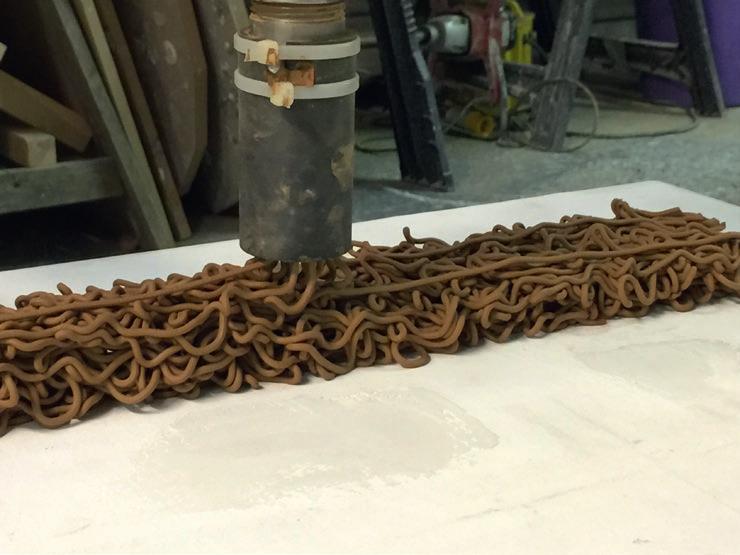
13 minute read
Methodology
1. Interdisciplinary engagement with architects, manufacturers, historians, craftspeople, ceramicists and artists
Grymsdyke Farm is a communal working space, where researchers and students are able to stay for long periods and use workshop facilities that are not restricted by discipline or process; for example, they can move easily between a Computer Numerical Control (CNC) machine and a potter’s wheel. Within this communal environment, learning and research methods were developed collaboratively and across disciplines in various projects carried out over five years. The hypothesis was that this approach would enrich clay practices, invite local input and broaden the relevance of the project to other researchers and makers.
We designed a three-day ceramics workshop at the farm in February 2015 for ten artists from Eastside Projects in Birmingham – an artist-run gallery and studio space – to work with architecture students, heritage builder Rebecca Reid, and local ceramicist Jessie Lee. The artists were provided with images and information on local archaeological finds and the history of clay use, sourced in discussion with former Buckinghamshire County Archaeologist Michael Farley. Collaboration was encouraged by asking participants to bring their own objects and images to work from and identify crossovers in their research interests using digital and traditional clay processes. The workshop began with the opportunity to learn specific techniques. Gradually, participants were encouraged to work together with technical support. One of the key findings of this workshop and feedback was the importance of allowing participants to use equipment incorrectly. For example, the potter’s wheel is not just a machine to make pots, it is a platform that rotates and as such can be used in different ways, i.e. to make carved sculptures. This ‘wrong’ way of using equipment is a vital part of creating new possibilities when working between different clay technologies. The Eastside Projects workshop was the catalyst for a number of ceramic projects, including Clay Spaghetti with Glithero (10-1).
10 Clay Spaghetti, 2017. Different shaped nozzles were attached to the robotic clay extruder to experiment with form.
11 Clay Spaghetti, 2017, after the first firing.
10
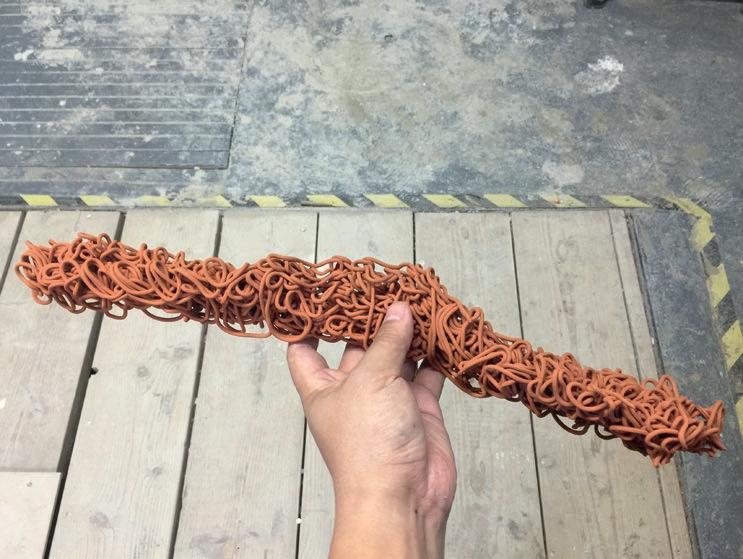
11
2. Research trips to visit specialist local workshops, archives and clay experts in ceramic production areas in the UK, Europe, Japan and China
Understanding local geology, history and culture is an important part of learning why particular manufacturing industry existed or is still in operation today. This research focused specifically on the area around Grymsdyke Farm in Buckinghamshire, where the majority of the fabrication was carried out, as well as other sites internationally including: · Manufacture nationale de Sèvres,
Paris: one of the most highly regarded porcelain fabricators in the
world (15, 22–3); · Sanbao International Ceramic Art
Institute, Jingdezhen: a Chinese cultural institution promoting the city’s history of ceramic art over more than two millennia (14, 20–1, 24–6); · Suzhou Imperial Kiln: making tiles since the Ming Dynasty (12, 27); · Ceràmica Cumella, Barcelona: a family-run factory making architectural ceramics for complex restoration and innovative projects since the 1980s (18–9); · Hasami, Japan: a town well-known for its ceramic manufacturing. Many contemporary designers have set up here precisely because of the town’s history (16–7).
12 One of the few remaining imperial kilns in Suzhou, China.
13 Glaze Library at the Manufacture nationale de Sèvres, Paris.
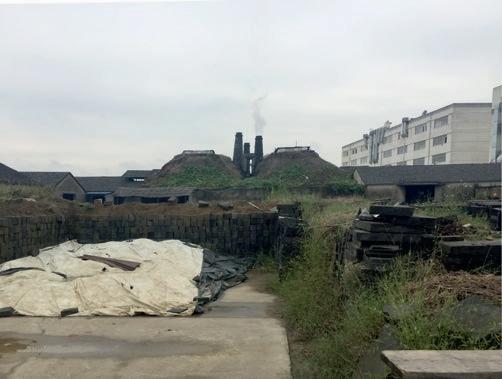


14 15

14 Small-scale ceramic production in Jingdezhen, China.
15 Modelling station at the Manufacture nationale de Sèvres, Paris. 16–7 Japanese mould makers in Hasami, Japan.


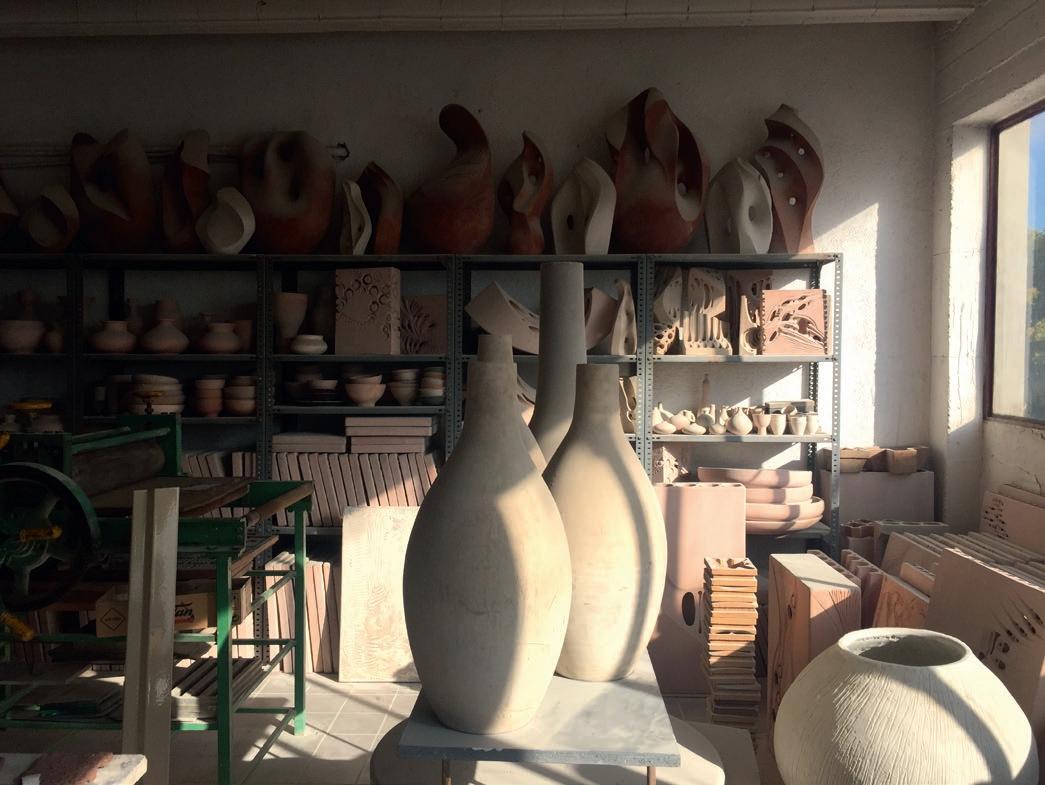
18 Display of ceramic pieces at Ceràmica Cumella, Barcelona.
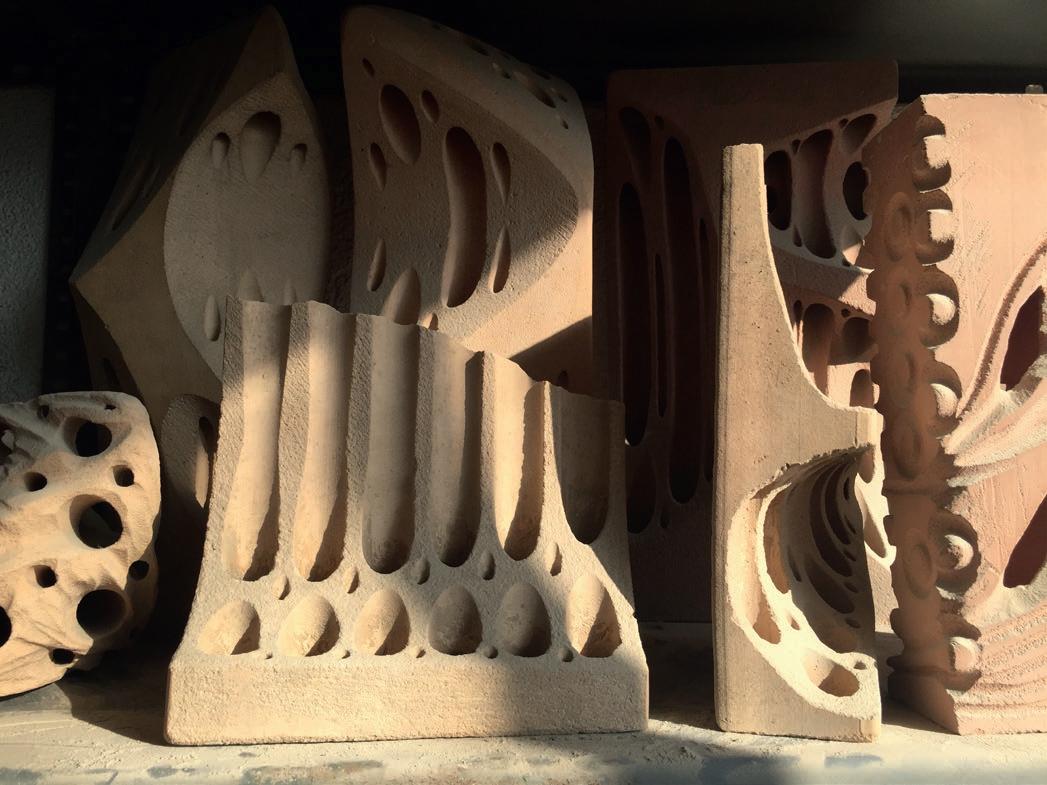
19 Prototypes by Antoni Cumella at Ceràmica Cumella, Barcelona.

20 Hand coiling of large ceramic pots in Jingdezhen, China.

21 Throwing of a large ceramic pot in Jingdezhen.

22 23
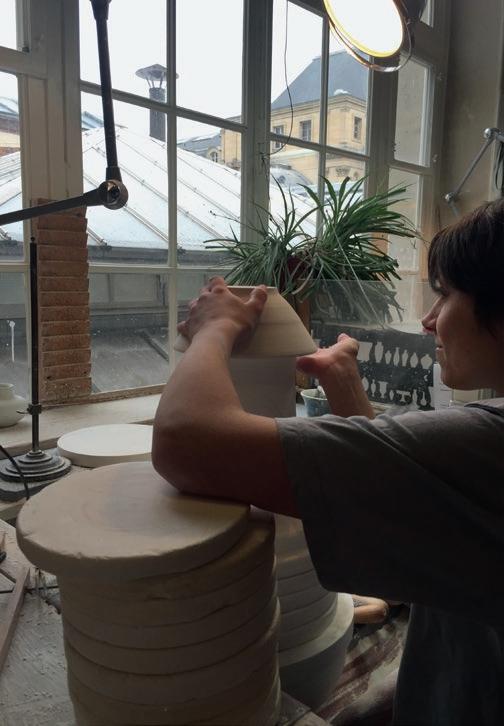
22 A handmade plaster piece mould at the Manufacture nationale de Sèvres, Paris.
23 A craftsman working on a porcelain bowl at the Manufacture nationale de Sèvres, Paris.

24 26


25 27
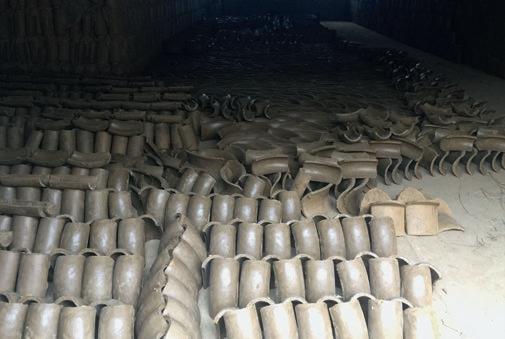
24 A section of a large ceramic pot being made in Jingdezhen, China.
25 Hand painting a ceramic pot in Jingdezhen. 26 Carving decorative ceramic surfaces by hand in Jingdezhen.
27 Ceramic roof tiles in Suzhou, China.
3. Working with the material directly through trial and error and empirical experimentation
Clay forms in all of the projects were made using the following: · Traditional processes, such as casting and throwing, using local clay; · Moulds made from original casts formed on the CNC machine; · Employment of a robotic clay extruder; · Combined use of CNC casts and formwork with the robotic clay extruder.
These forms included sample experiments in extrusion processes, cast domestic ware, 3D-printed tiles, screens constructed from interlocking cast units, experimental breezeblocks and two domes made from unique 3D-printed tiles. Each process and form had particular challenges and discoveries.
Limitations
Clay is a naturally occurring material which is widely distributed. Whilst the base chemical composition of clay bodies from different sources and suppliers is similar – a mixture of alumina, silica and water – they may have significantly different properties and therefore require trial-anderror experimentation when used in production. These properties include: naturally occurring solid particles such as flint, chalk and iron; additional solid particles of pre-fired clay (grog); fineness and evenness of the clay particles; inclusion of other minerals and oxides in trace quantities, such as feldspar and potassium; and the plasticity of the material, before and after processing. To ensure consistency and workability, clay is processed using a range of methods such as grinding, sieving, mixing, adding water, drying and weathering. The structural limitations of wet clay were explored by the artists from Eastside Projects who experimented with a robotic clay extruder, changing the direction and geometry of the output using different nozzle designs. These experiments included 3D printing a nozzle in the shape of a shard of Medieval pottery found near the farm, through which clay was extruded until the column collapsed. The extruder was also used to produce modular units. The Eastside Projects artists discovered that there is a height limit to which a build can go using a robotic clay extruder, due to the weight of wet clay and extrusion time. Inconsistencies in pressure meant that the extruder would stop and start, which affected the accuracy of the repeating layers and overall structure of the object created. Although this can be classified as a structural failure, the experiments successfully produced novel forms using robotic technologies.
Findings
A clay body suitable to be pumped and extruded, and sufficiently stable to produce a large component, is constrained by: · Specific gravity – targeted at around
SG 1.8 – was used as a proxy for viscosity, as it is largely a measure of the water content of the clay; · Solid particles in the clay body should be able to pass through a mesh size grade of between 100 and 180. Solid particles larger than this would damage the pump, requiring expensive repairs; · For improved stability during drying and firing, the clay body should include an element of finely ground solid particles,
e.g. by firing low-iron kaolin to a very high temperature, but the proportion of molochite should not exceed 20% by weight; · The clay body should withstand a firing temperature of not less than 1200°C (high-fired). After firing, low-fired clay bodies are less stable and durable than those that are high-fired; · Colour should be white to maximise options for glazing; · Shrinkage should be minimal, preferably no more than 15% overall; · The clay body should be workable, with minimal cracking during drying and warping during firing.
28 Breezeblocks, 2016. Expandable clay mixtures in draping configurations during the firing process.
29–30 Sample expandable clay mixtures after firing.




31 Soft Developables, 2019. Trial-and-error experimentation with clay composition.
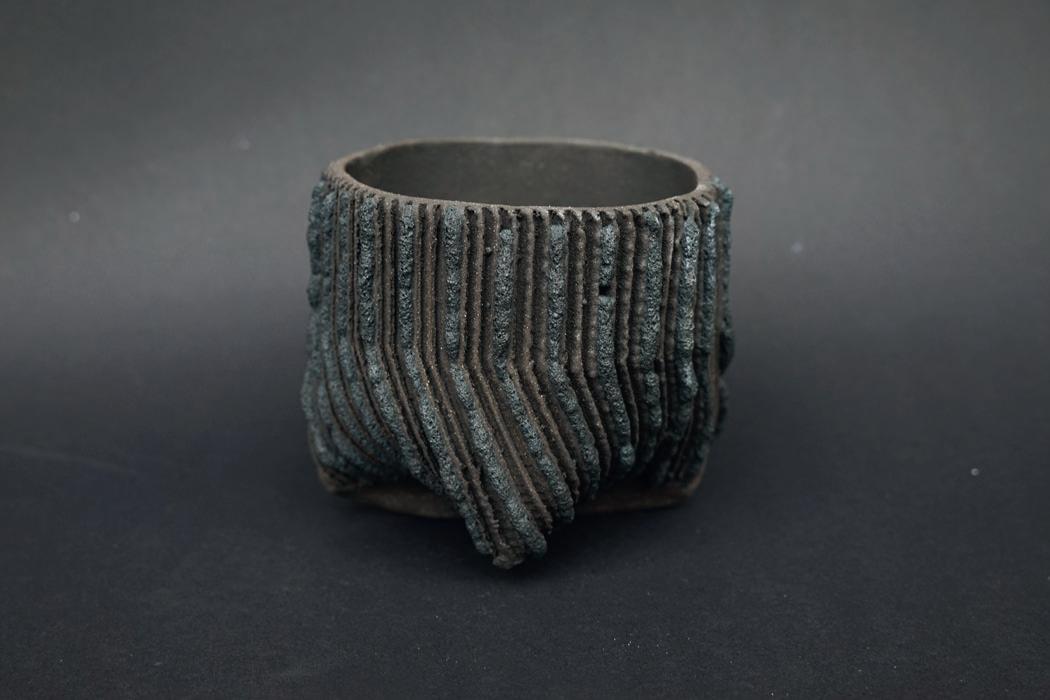
32 Soft Developables, 2019. Robotically engraved clay sheets interact with inlaid expandable clay beads.
4. Combining digital programming for clay extrusion with manual techniques for assembling and glazing
Ceramica, 2015
Ceramica considers the limitations of 3D printing with clay as a key design parameter (33). One such limitation is the weight of the clay. A programming solution was introduced to automate the subdivision of each build into archivable chunks, which were then air dried in a plastic tent to encourage even drying. When the sections were sufficiently stiff, they were manually joined together using slip from the same clay body (35). Even though the 3D-printed geometries were complex, it was still possible to make secure joints with the slip. It was, however, difficult to successfully seal all of the joining pieces, as the gap was in places too narrow to insert a tool or access by hand. As a compromise, a coating of decorative white slip was applied to the surface using a spray gun. This created a more even outer surface and helped to minimise cracks, allowing for smoother glaze application. Prior to glazing, this decorative finish was tested with the clay body to make sure that they would successfully combine. Two white slips for surface application were tested. One was a commercial slip from Potclays and the other was made up from raw materials using the following recipe: 20% Kaolin, 20% Ball Clay, 20% Feldspar, 20% Flint, 5% Zirconium, 10% Bentonite and 5% Borax. Both slips fitted the body of the clay. At the bisque stage (1000°C) both appeared white. The Potclays slip was eventually selected as the other looked slightly yellow.
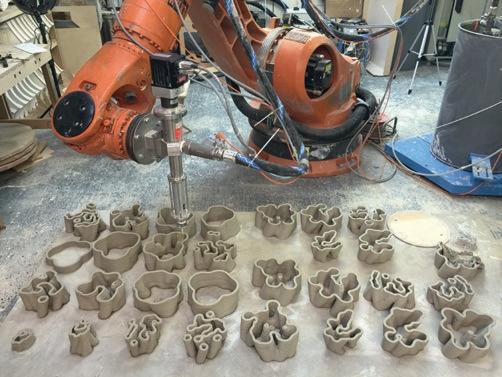
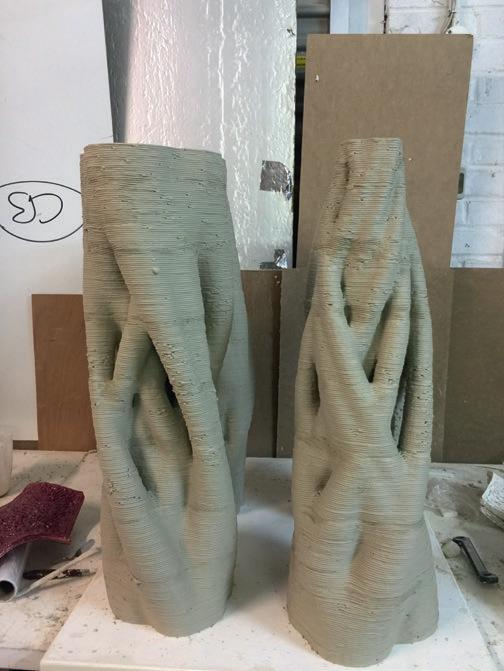
33 Ceramica, 2015. Chunks being printed.
34 Ceramica, 2015. After manual assembly of the 3D-printed chunks.
35 Ceramica, 2015. Touching up after manual assembly.
36 Breezeblocks, 2016. Individual components were used for overall diversity and porosity when combined.

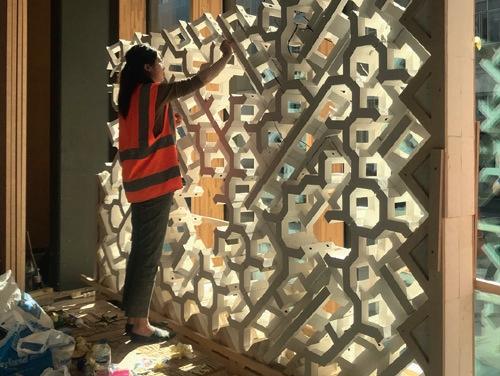
Breezeblocks, 2016
Breezeblocks consolidated various researched techniques, including two digital processes: robotic clay extrusion and CNC milling. Each tile was made by coiling clay through the nozzle of the robotic extruder onto a cast plaster formwork (37). Because the robot was printing onto a curved surface, the six-axis robotic arm traced the top whilst extruding clay. The technique of using plaster moulds was borrowed from slip casting as it allowed the tile to be released easily (38). The tiles were then assembled together and dried on a wooden scaffold designed on the CNC-milling machine (39–40). The form of the scaffold prevented the clay from cracking as it dried because it enabled it to shrink without restraint. The eight tiles were assembled into a block with slip and hand tools. By joining these pieces together – as they could not be 3D printed as a single object – height and overall geometry limitations were overcome. The relationship between the hand and the robot is not a limitation but is consistent with small-scale and local ceramic production.
37 Breezeblocks, 2016. 3D printing clay on a mould to make the individual parts.
38 Breezeblocks, 2016. The parts are then air dried on the mould for three to four days before being removed.
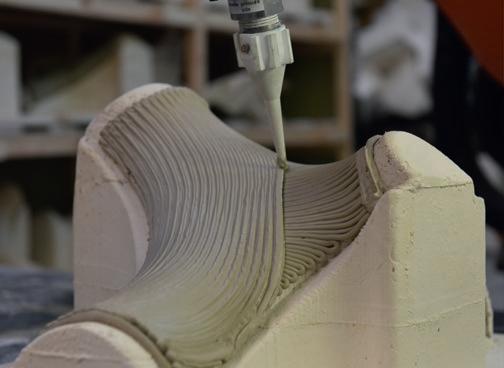
37 39
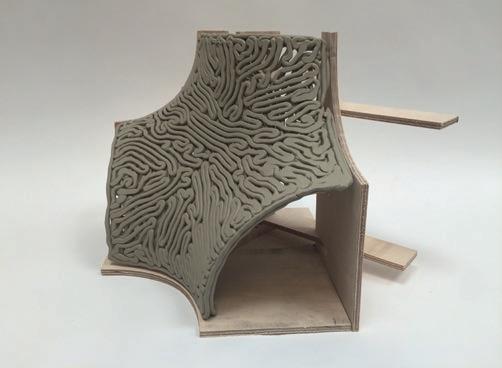
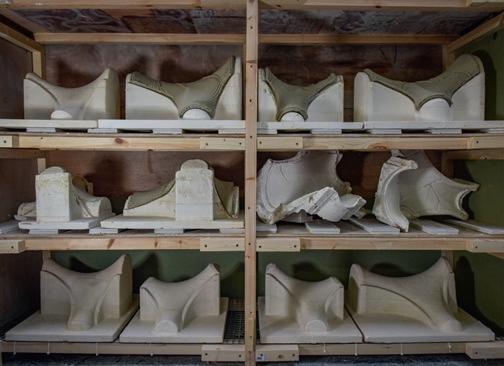
38 40

39 Breezeblocks, 2016. The 3D-printed parts are then dried on a CNCmilled scaffold.
40 Breezeblocks, 2016. The drying scaffolds were also used as jigs for manual assembly. 41 Breezeblocks, 2016. Finished components, painted and ready to be installed.
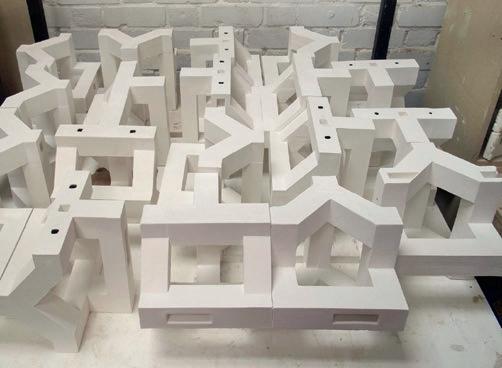
Clay Domes, 2016
The robotic clay extrusion process for Clay Domes allowed for experimentation with different forms, inspired by traditional techniques and building components, such as a nineteenth-century ceramic screen from southern China. Different shaped nozzles were attached to the robot to change the size of the clay coils. These affected both the appearance and stability of the object. Identical, unique or interlocking components were designed using 3D-modelling software to form larger intricate structures. A series of unique extruded clay tiles with saddleshaped surfaces curve in two directions. This shape is both strong and materially efficient. The tiles are joined together to create two large domes, each 170 cm in diameter (42–4).
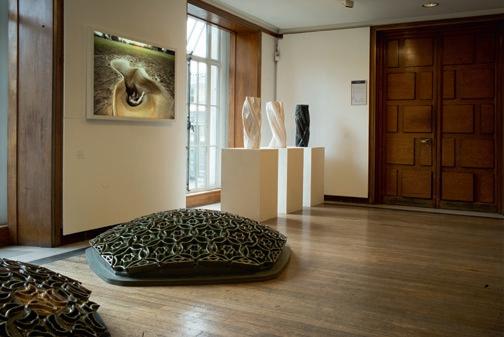
42 Clay Domes, 2016. Life of Clay, RIBA Practice Space.
43 Clay Domes, 2016, and Ceramica, 2015. Life of Clay, RIBA Practice Space.
44 Clay Domes, 2016, permanently installed at Grymsdyke Farm.
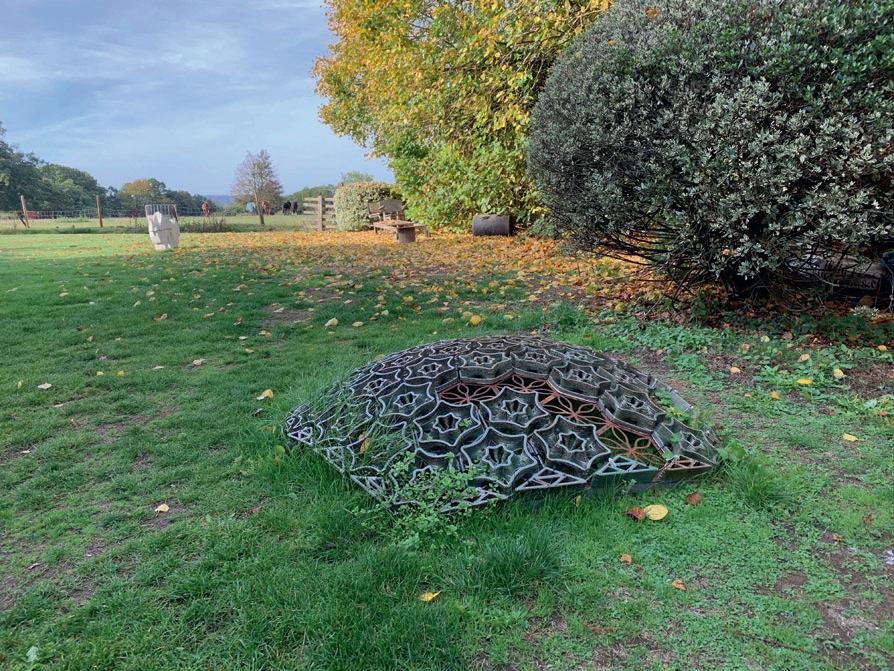
43

44

V&A Tiles and Pots, 2018
In 2018, the V&A commissioned Lee to create tiles for the floor area in its main shop. These had to be designed and made to be robust, slip resistant, geometrically consistent and, at the same time, all unique. Lee developed a way to 3D print each tile with a robotic arm. Without the need for moulds, there was no need for repetition. Over a period of two years, this project pushed boundaries in ceramic production with digital tools to make a large-scale architectural installation. A few months after installation, the tiles were realised to be too difficult to maintain and a decision was made to remove them.
The V&A, willing to promote design innovation, commissioned Lee to rectify the issue and fabricate a new set of 2,500 tiles. 3D printing was combined with traditional casting in the second batch. The tiles had their moulds removed whilst they were still wet and multiple casts were taken at a greater rate and with more overall consistency. The timing of this process was critical as the clay tiles began to shrink as soon as they were reprinted. The project demonstrated the value of combining manual and robotic practices of clay for a successful outcome (45–53).
45 Experimenting with glaze-pouring techniques for the V&A tiles, 2018.

46
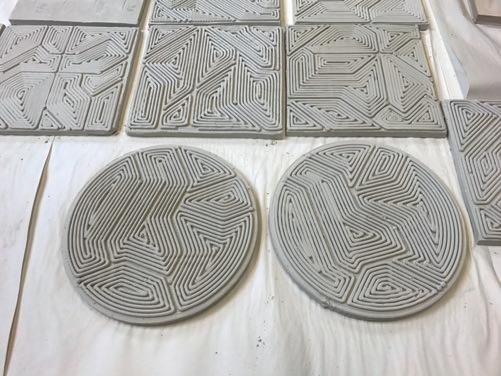
47
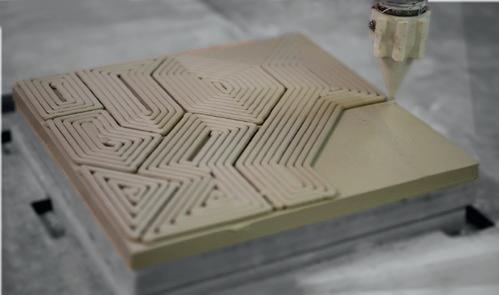

46 Glaze test on a V&A tile. 47 V&A tiles, 2018. Circular tiles were designed to cover redundant ventilation pockets.
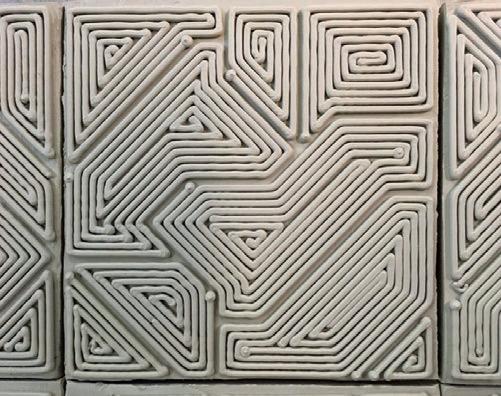
50

51
48 V&A tiles in production.
49 Tile design by Guastavino at the Avery Archive, Columbia University Libraries.
50 Extruded design on a V&A tile, 2018. 51 The V&A tiles are designed with 16 unique patterns that can be configured in multiple ways.