
13 minute read
Methodology
1. Research trips to digital or craft-based art and architecture fabricators, including metal forging, casting, stone carving and brick laying, in the UK, Europe and China
Different fabrication experiments and prototypes involving digital tools such as robotic arms and CNC milling were explored at Grymsdyke Farm in Buckinghamshire. Experienced brick layers like David Hussey, mould makers like Martin Hanson, carpenters and several material scientists visited the farm to instruct and oversee projects. Collaborations were formed with foundries and manufacturers in China to understand the scaling-up of processes. Exchanges of skill and research took place in design and fabrication institutions, including: · ETH Zurich. A leading institution in robotic fabrication and digital technology; · Factum Arte, Madrid, Milan and London.
The company has a research wing on advanced 3D scanning and art conservation; · Jianye Mould Maker, YuYao. The manufacturer uses both digital and traditional methods for plastic injection mould manufacturing; · Swan Foundry, Banbury. One of the UK’s few remaining sand-casting facilities · Tany Foundry, Hangzhou. Specialising in the fabrication of large-scale public art, this foundry works with digital technology and traditional fabrication techniques.
Attachment references a fabrication process studied at Tany Foundry in Hangzhou. The foundry specialises in forming metal sheets to a digital model. These digitally modelled designs can be hammered into their metallic equivalent under the skilful hands of artists in the workshop. Experienced craftspeople subdivide given geometries into segments to be formed, welded and polished. Each step of this process requires years of training and practice. This is the opposite of de-skilling due to the introduction of digital technology, as the fabricators decipher details of production. One can argue that this is an effective way to sustain manual skills through a collaboration between digital and hand modelling. A visit to see the craftspeople at work allowed for a deeper understanding of how digital designs can be approached by respecting both the limitations and boundaries of a craft.
8
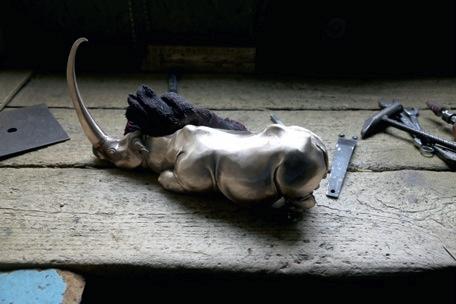
9
8–9 Polishing station for cast bronze objects at Tany Foundry, China.
10 View of a 3D-printed sculpture at the workshop of Factum Arte, Madrid.
11 A custom-made 3D scanner at Factum Arte.
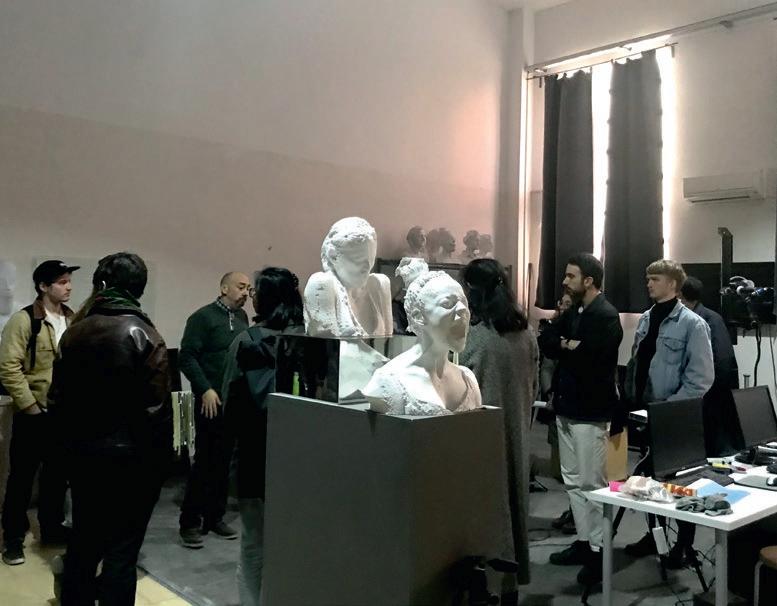
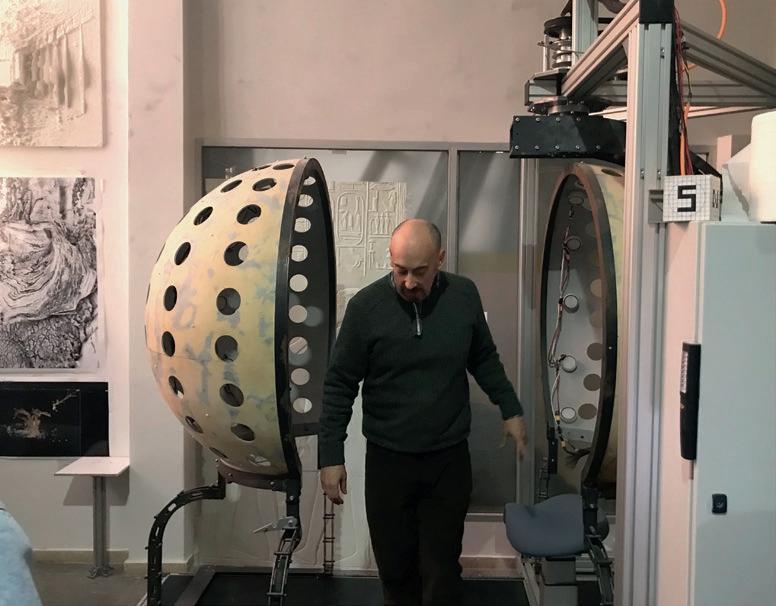

12

12 Martin Phillips, owner of Swan Foundry, Banbury, examining a CNC-milled timber mould for casting sand.
13 Sand moulds ready for casting in iron.
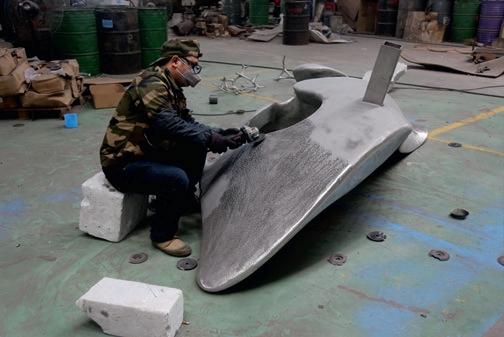
14 16


15
14 Polishing of welded stainless steel sculpture at Tany Foundry, Hangzhou.
15 Polished bronze sculpture ready for final application of finishing at Tany Foundry, Hangzhou. 16 Welding of stainless steel sculpture at Tany Foundry, Hangzhou.
2. Computation design, 1:1 prototyping, digital programming and use of augmented reality (AR) technology
Piercy & Company and Material Architecture Lab (MAL) at UCL set up a pilot research programme called Making and Practice. The idea is to pair an established architects’ practice with a material and fabrication-based research programme to design and realise a structure at 1:1 scale. As a collaborative platform, MAL’s interests in material are mediated through experimentation with current advances in computation design and digital fabrication, and also applicability testing utilising live projects in the construction industry. Two research assistants, Changjian Jia and Teng Wang, spent a month at Piercy & Company and another at Grymsdyke Farm learning bricklaying from chief bricklayer David Hussey. The programme was grounded in a process of making prototypes with rigorous and iterative refinements of design and digital and manual models.
SUP’s goal was to design a building system using modular components. Digital tools were used in combination with physical prototyping to design and test combinatory options. The system has unlimited possibilities for what can be made, from a toy to an architectural structure. While SUP is made up of modular components, it is also multiscalar, meaning different sized components can link together. Digital processes were used to design the system and some potential outcomes, but it could also be approached manually without specialist knowledge. It is simple enough for intuitive play as the assembly and disassembly require no tools, adhesive or mechanical connectors.
17 Front of ‘chair design one’, assembled using large-scale recycled-ABS SUP components.
18 (overleaf) ‘Stool design one’, assembled using middle-scale recycled-ABS SUP components.
19 (overleaf) ‘Stool design two’, assembled using small-scale recycled-ABS SUP components.

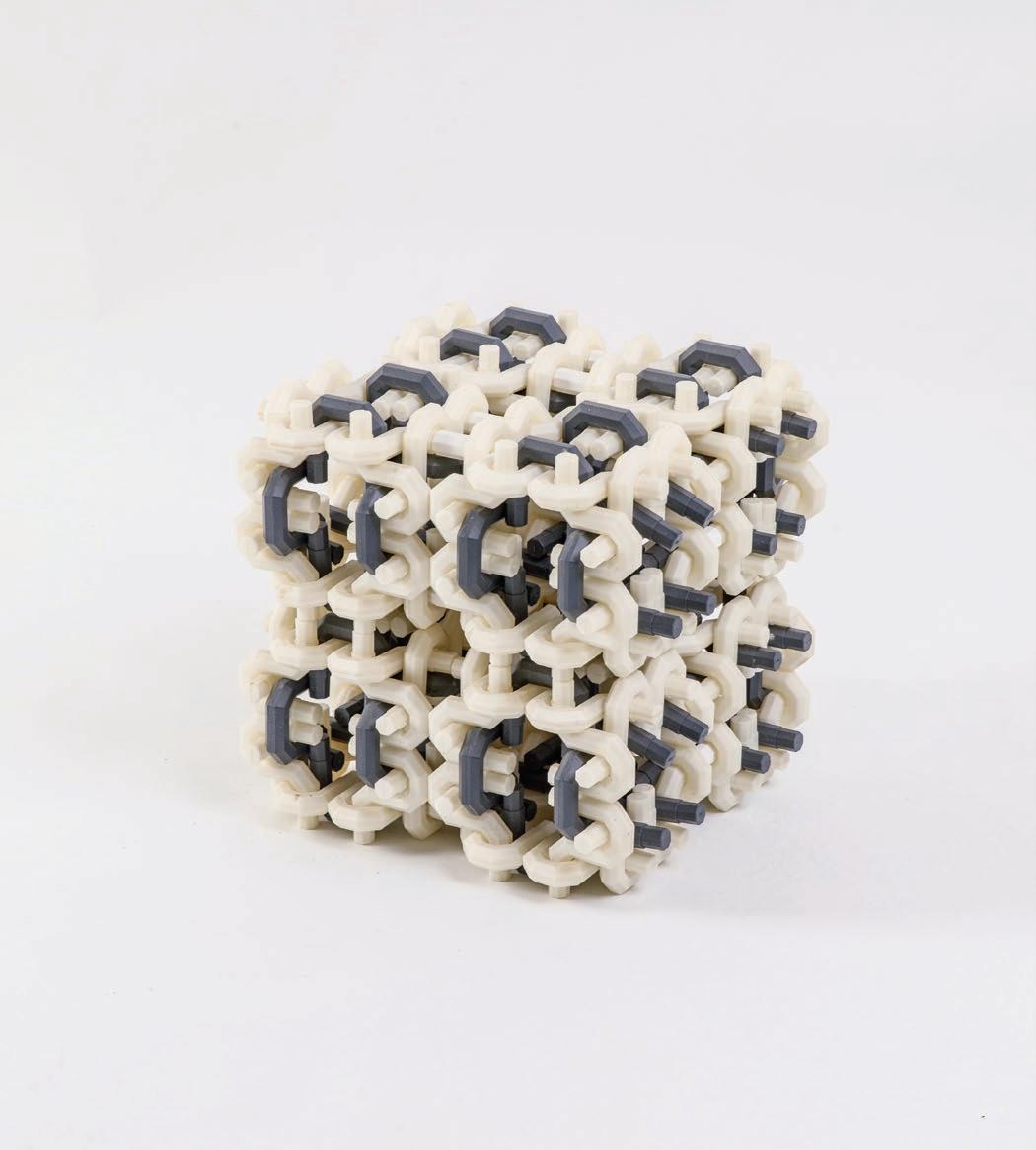
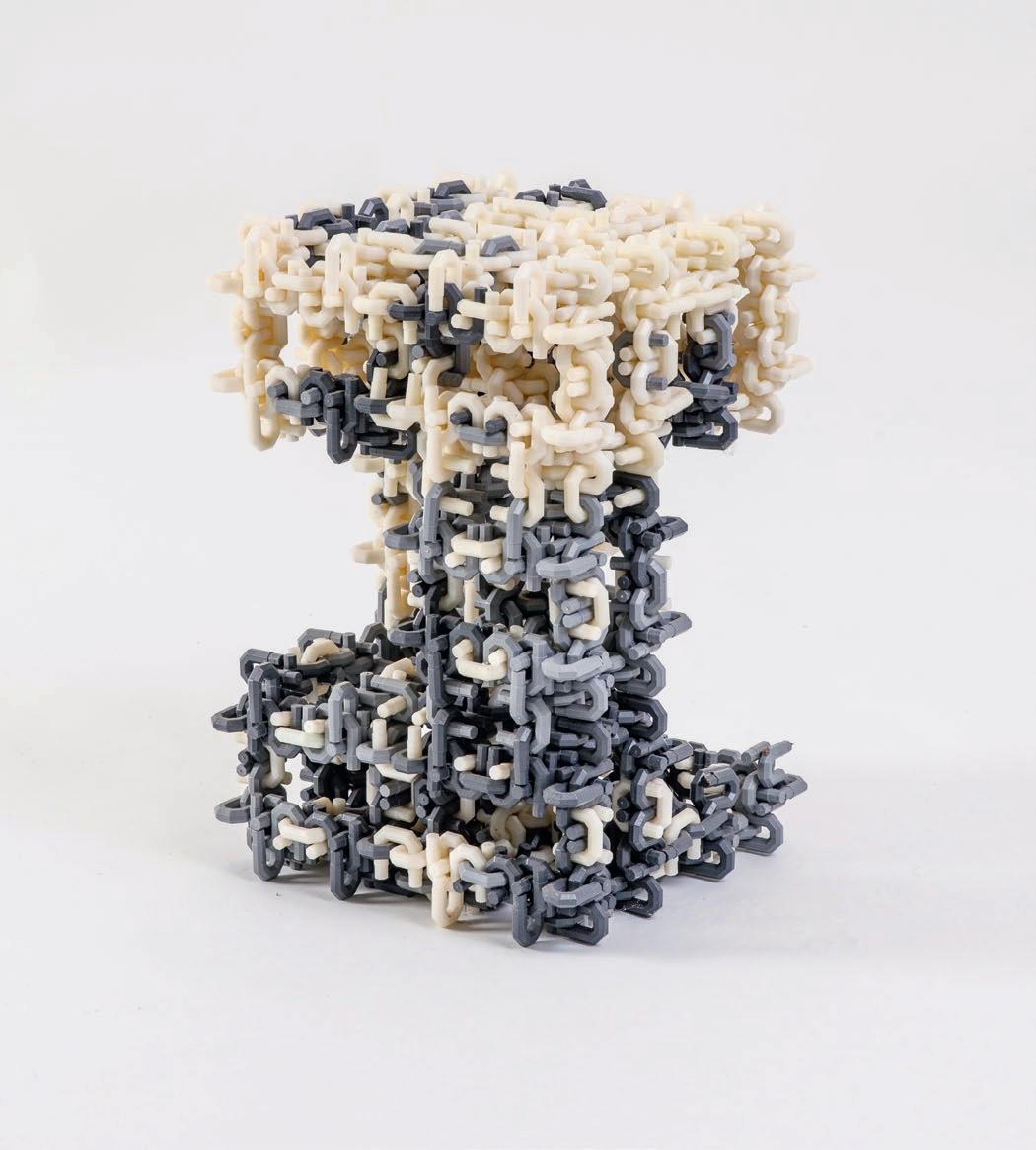
Most discrete architectural design systems are built using either nodal connections or flat faces stacked up in grids. SUP, however, explores a component system based primarily on interlocking joints, which allows for stable standardisation without losing expressive design potential. The components can be digitally generated to fill any volume. Conditional rules allow them to be used expressively to design large, complex, architectural spaces.
The research for Code-Bothy examined the relationship between manual and digital assembly using the standardised brick. An assembly method based on mixed-reality technology was employed for the construction. The Bothy was designed using parametric modelling tools. The result is a brick structure that is challenging, if not impossible, for a skilled bricklayer to set-out and build without some kind of digital aid. Bricklayers were equipped with wearable technology – the mixed reality smartglasses Microsoft HoloLens – that allowed them to combine traditional skills with digital placement capabilities to build the computation design. ‘Code’ thus comprises both written laws for the use of a Bothy and computer language for its design and fabrication.
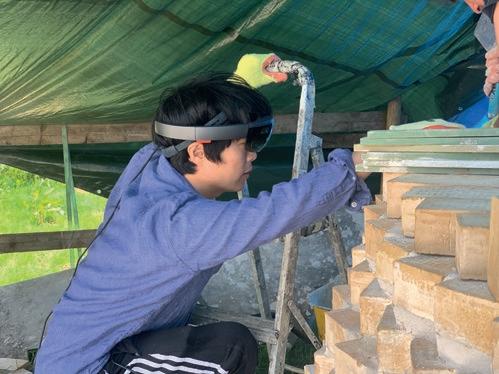

20 Hanjun Kim realigning the bricks after the pointing process with mortar for Code-Bothy, 2020.
21 Construction site for Code-Bothy, which needed to be covered on sunny days to allow for the person using the HoloLens to be able to see the digital model.
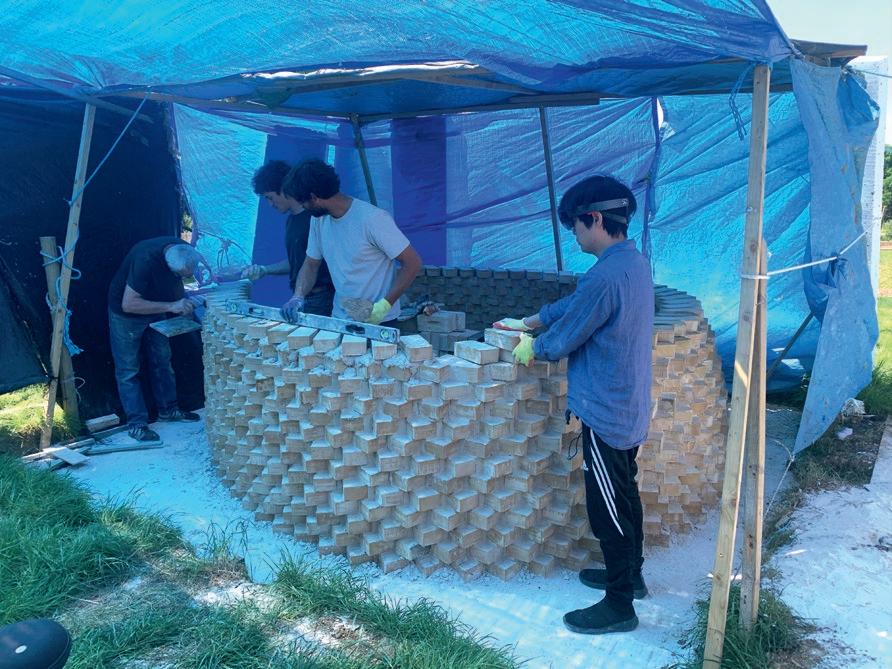
22
22 Hanjun Kim positioning the bricks before application of mortar, Code-Bothy, 2020.
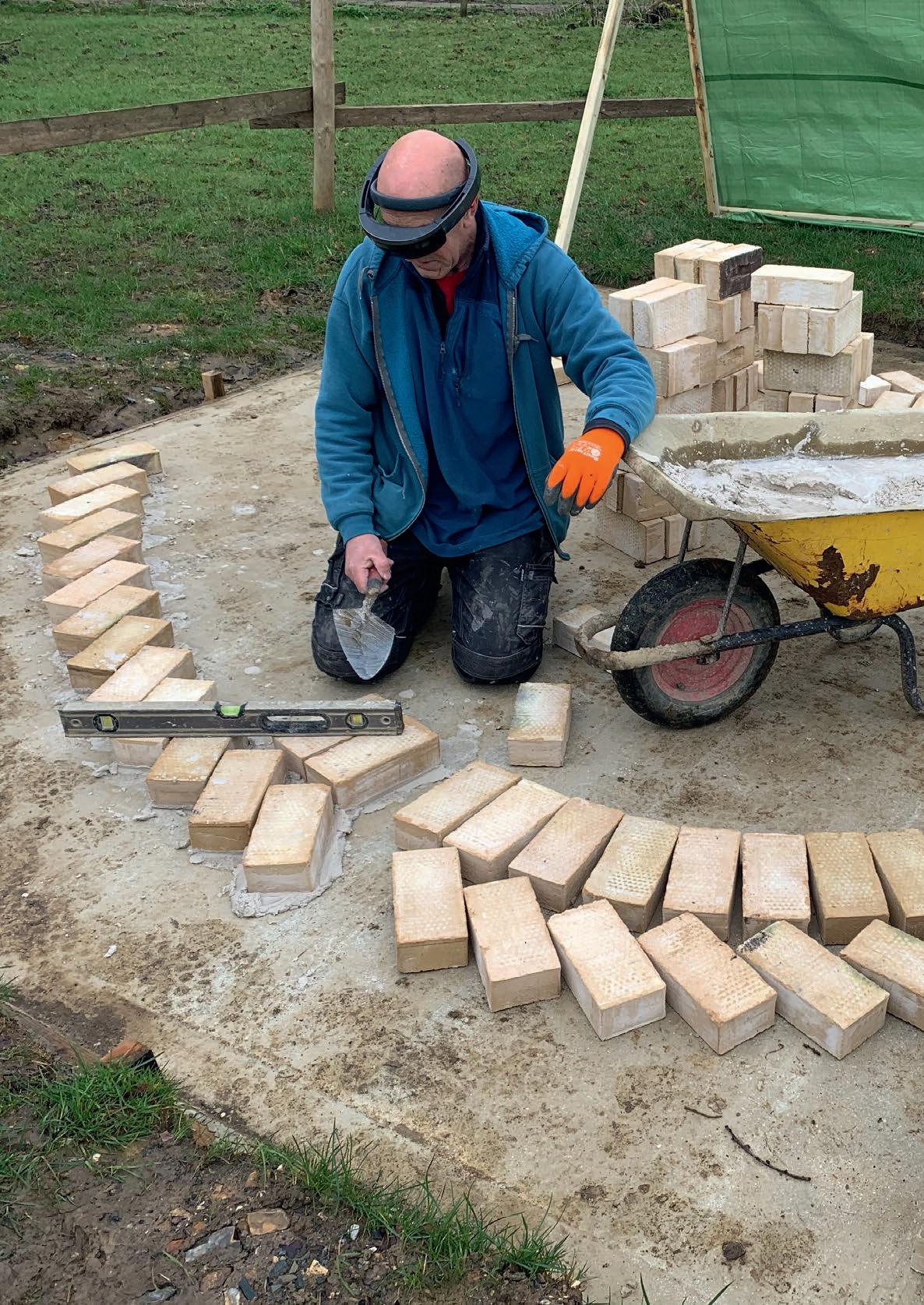
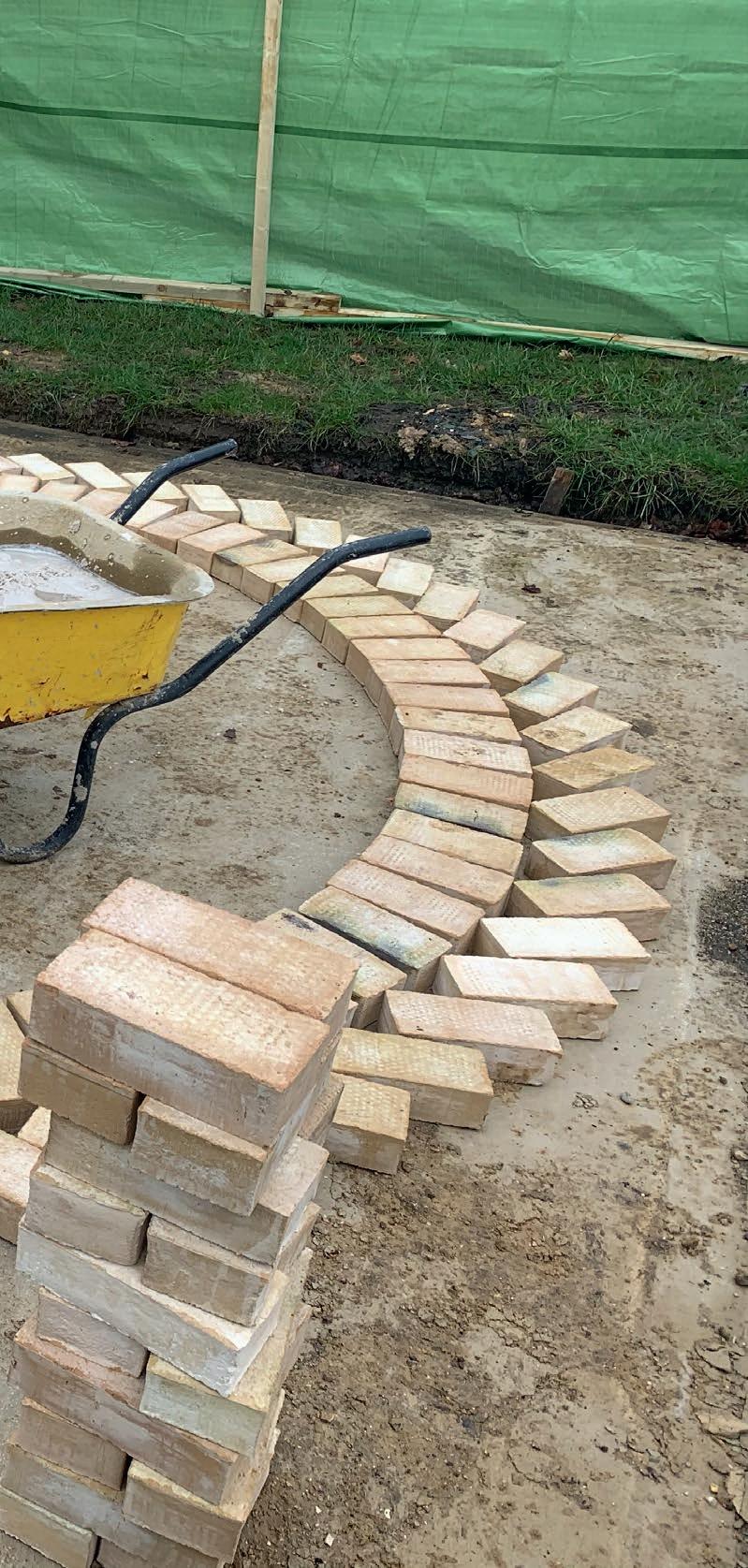
23 David Hussey using Microsoft HoloLens to position the first layer of bricks for the Bothy.
24 (overleaf) Exterior view of the Bothy and the incremental rotation of the brick arrangement. The design pattern is clear with the help of direct sunlight and the shadows cast by the protruding bricks.
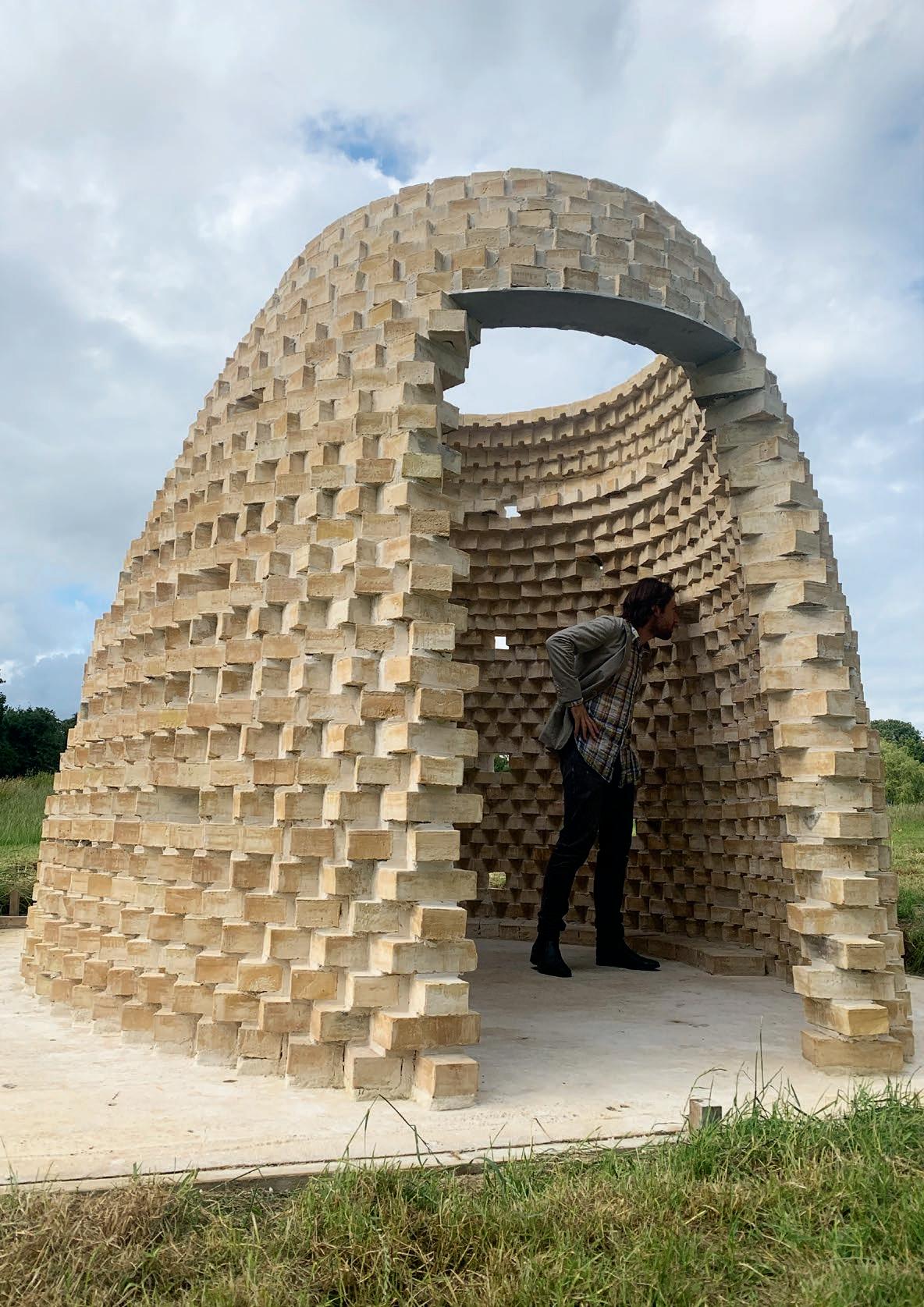
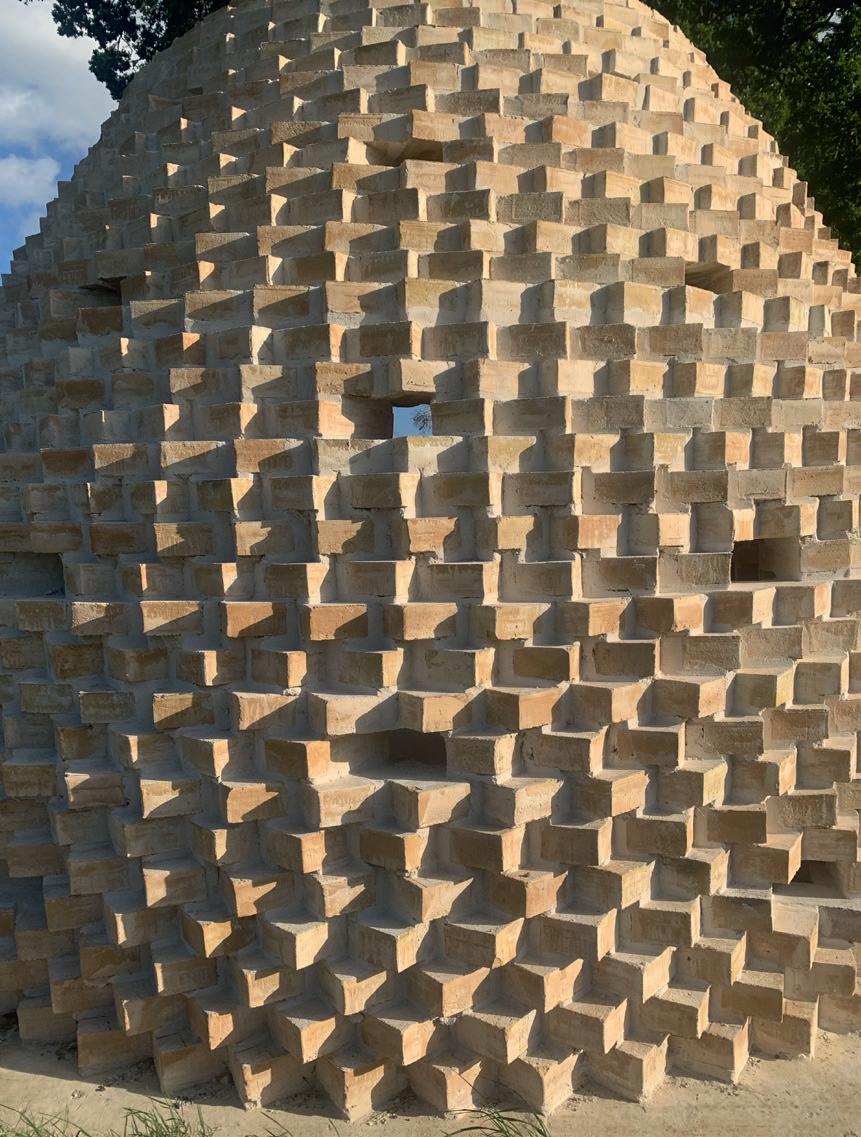
25
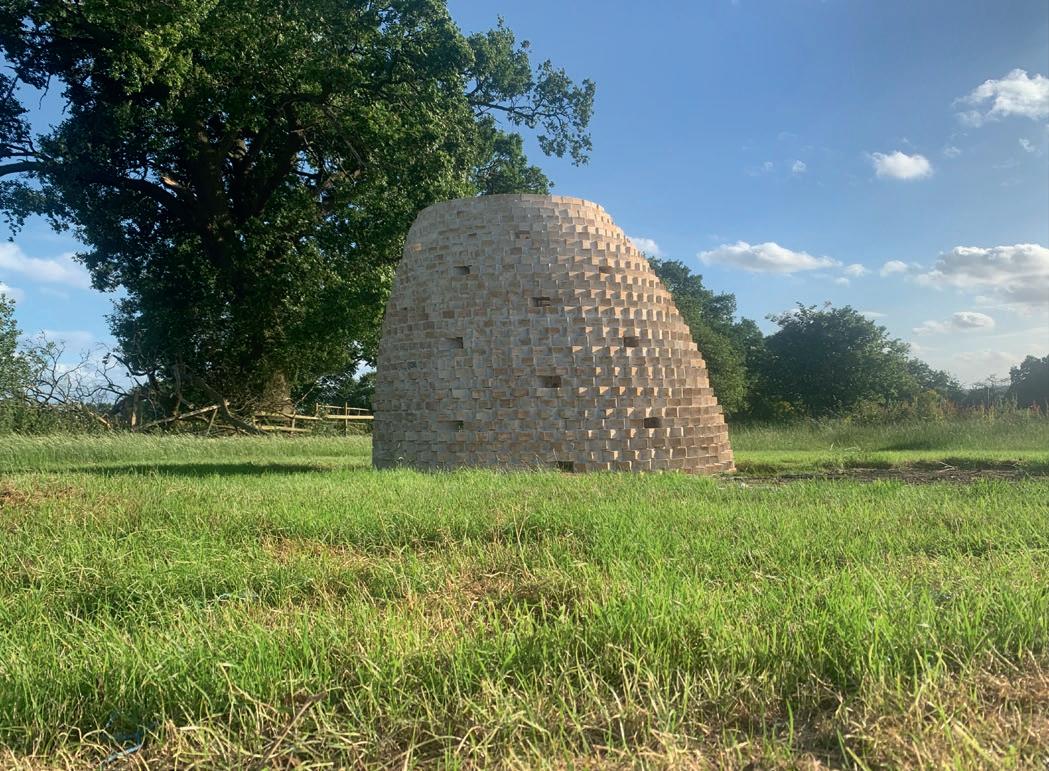
25 (previous) View inside Code-Bothy, 2020. The small openings are a design feature.
26 Code-Bothy in the paddock at Grymsdyke Farm, 2020.
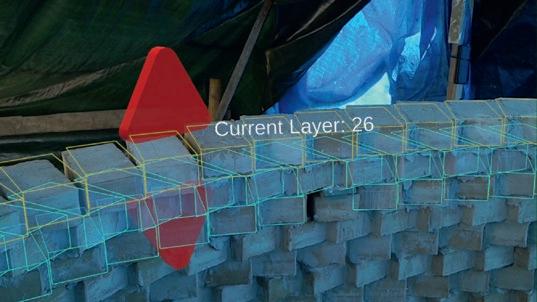
27
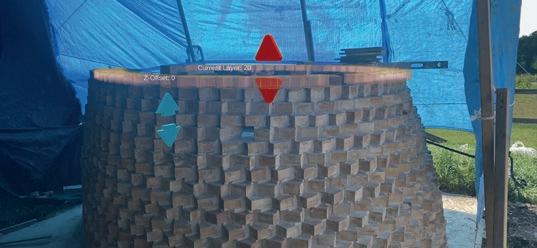
28
27–8 View through the HoloLens showing the digital model of CodeBothy superimposed on the physical structure.
29 Screen capture of the Fologram software showing the interaction between the bricks and the person in charge of positioning them.
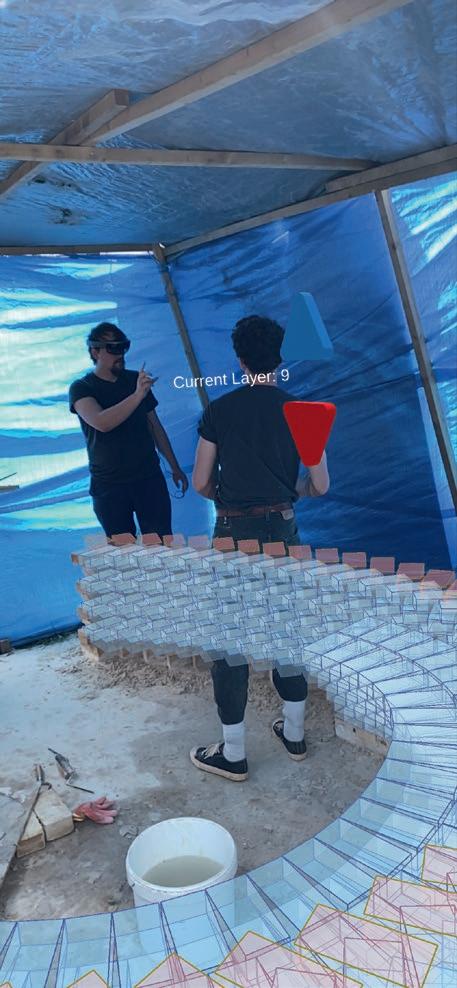
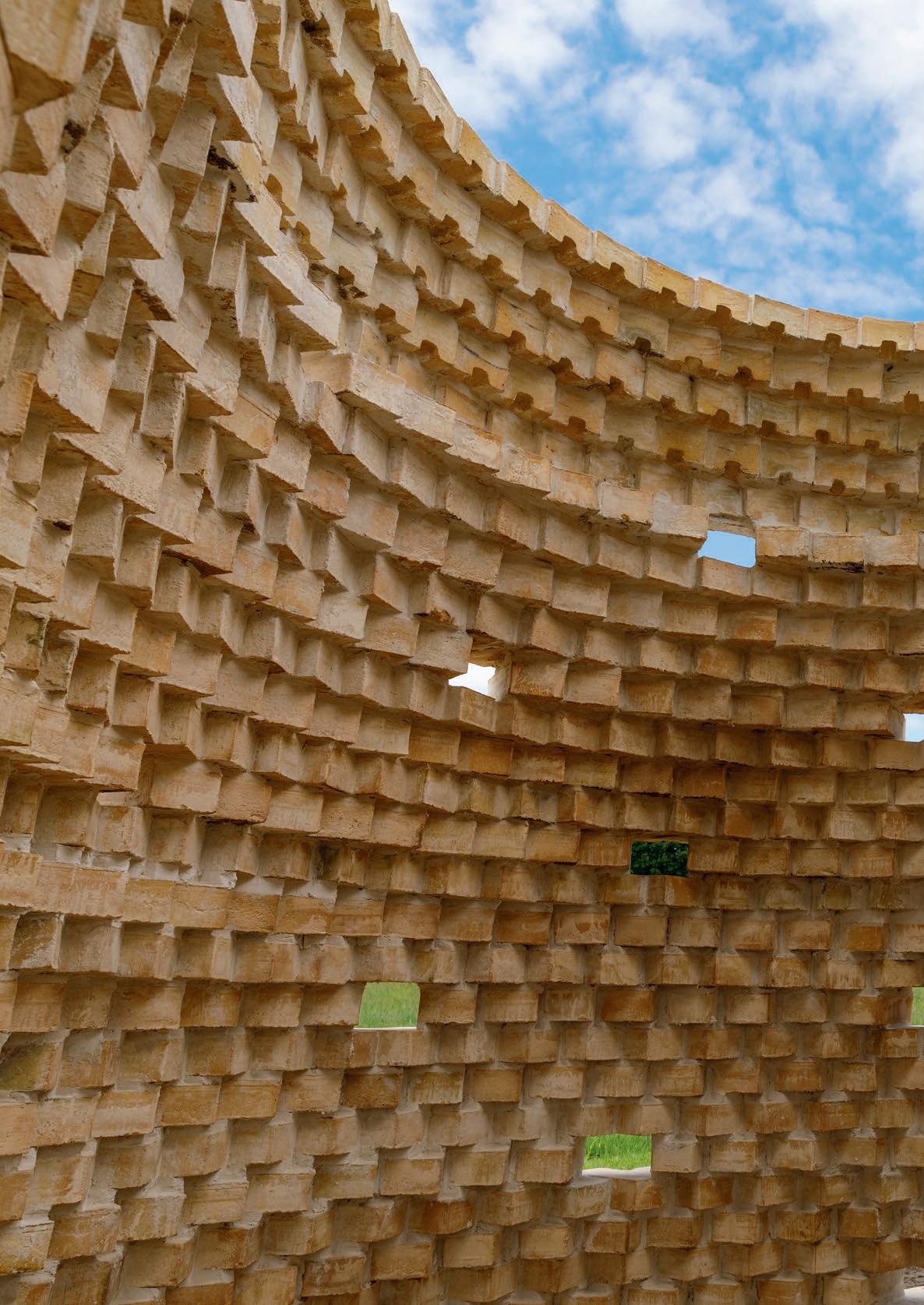
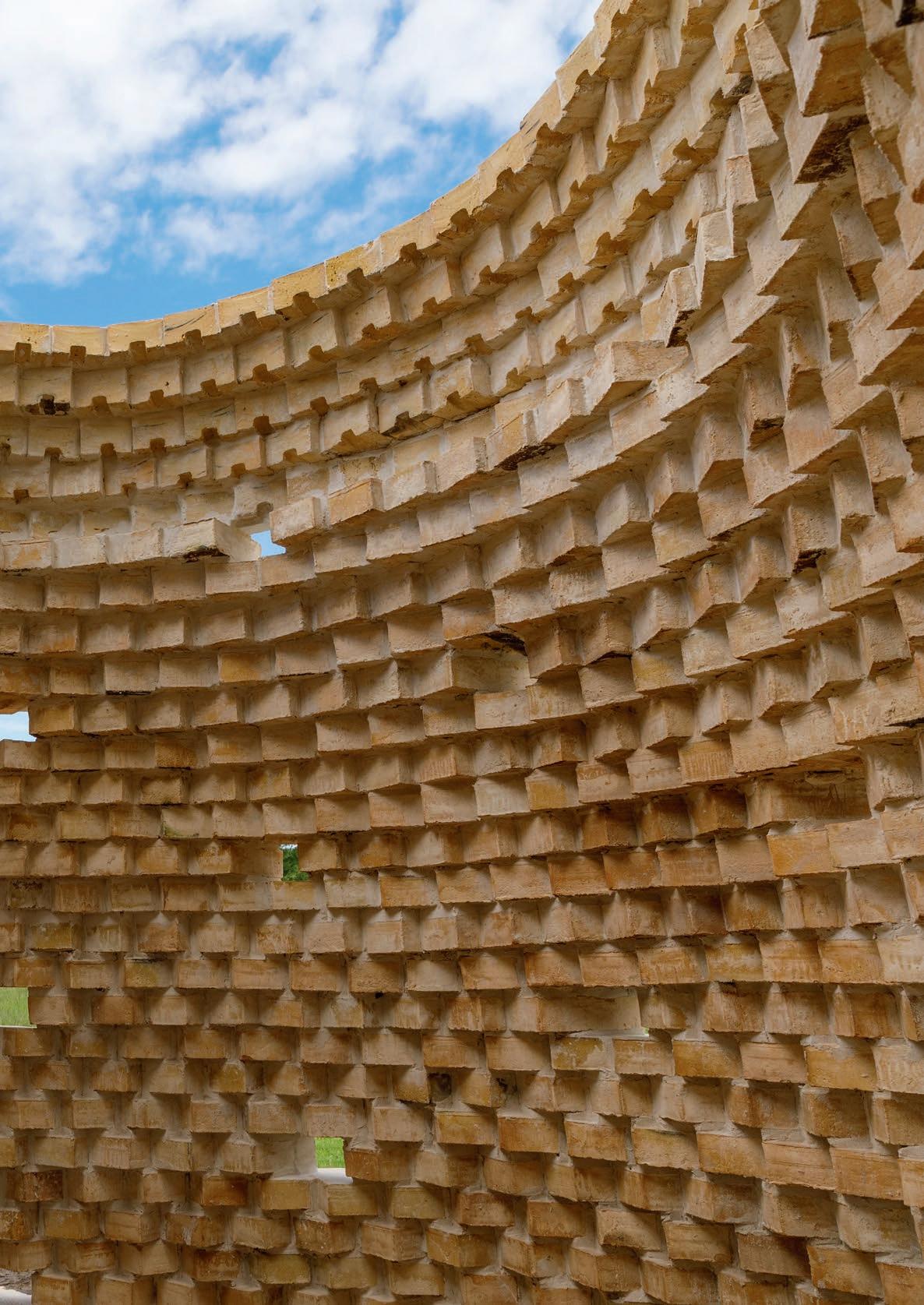
3. Working with materials directly through trial and error and empirical experimentation
The authors worked with a variety of materials, traditional and hybrid, and employed digital fabrication techniques and manual operations in testing them. The aim is that these materials can then be scaled-up or further developed for exhibitions or commissions. The experiments were conducted for Balustrade Garden and for furniture featured in exhibitions in London and Paris. The chosen materials are underused, recycled raw materials or industrial waste.
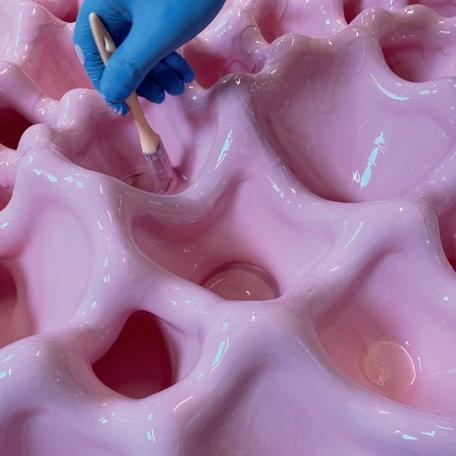
31
30 (previous) View of Code-Bothy’s oculus, 2020.
31 Silicon mould for a 3D-printed part of Balustrade Garden, 2019.
32 Testing the assembly of Balustrade Garden at Grymsdyke Farm, 2019.

Weaving Coir
This research looked at new uses for coir – coconut husk fibre – which is an abundant waste product. The aim was to investigate its potential as a surface material by combining fibres with a natural starch-based binder, which was then applied to a fabric’s surface by hand to give it a new visual language. The finished object is much stronger than its constituent parts, with a robust shell that hardens when it dries.
One of the larger tests was a prototype coir chair with a digitally produced substructure. The inside of the chair was made from polystyrene spheres, drilled with a robotic arm at precise points. The spheres were connected point-to-point by rods and the whole assembly was covered by fabric. In this project, both the design and the fabrication technique were digital. The structure was modelled beforehand using a script that mimics the flow of fibres around an object: a space-filling curve that can be described as a continuous mapping from a lower- to a higher-dimensional space. This was adjusted to see the overall texture and visual effect; fibres were then hand-applied layer by layer to resemble the digital creation. In this way, final objects are assembled based on digital information rather than being sculpted. The intention is that this methodology could be used where coir is produced, instead of shipping it from tropical countries to factories internationally.
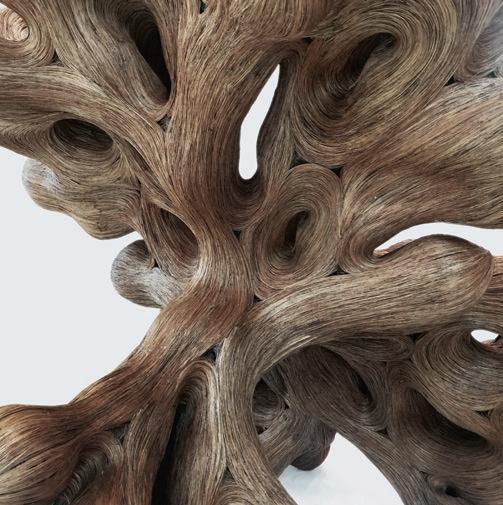
33-5 Woven coir structures modelled using a script.

34 35
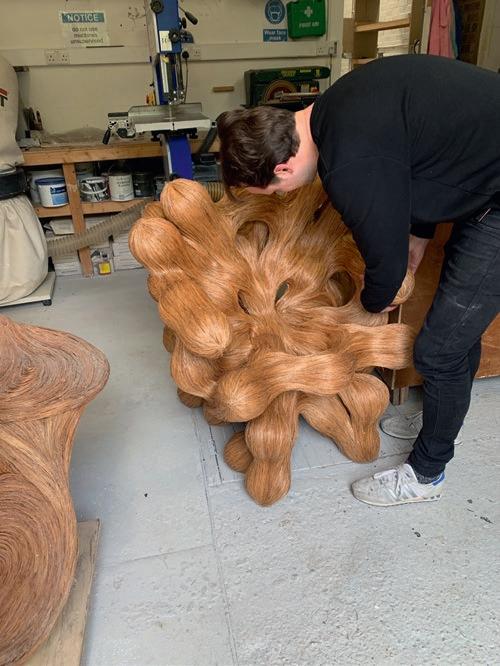
Sand Printing
This project engaged 3D printing with sand, not as a means to reproduce a digital model but to allow the printing process to create a language of its own. Initial tests were made by combining sand with a liquid binder. A dispenser filled with the binder was attached to a robotic arm, which was digitally controlled according to a script, and traced predetermined lines and patterns into a sand bed. The binder set in a few hours according to where it had touched the sand; where two lines crossed, a stronger bond was formed. To achieve more structural integrity, the lines of sand can be designed to cross over each other several times. The advantage of using the robotic arm is that the same object can be made again, allowing similar objects to be assembled; unlike casting, however, they cannot be made identical. Although the same script is followed each time, the way the binder interacts with the sand can’t be precisely controlled. This gives the objects an uneven, handmade quality, even though they are digitally produced. So far, the method has been used to make a prototype screen, a column and a chair.
In parallel, the density of a sand object was also explored. If printed very thin, sand has the potential to transmit light. A series of experiments was carried out using thin layers of sand mixed with a binder to produce a translucent sheet material. This was also done with digitally created moulds using scripts based on natural sand formations. The robotic arm carves flowing formations into moulds made of reusable polystyrene. The sand coating is manually applied to the base object, which is later removed, leaving just a thin translucent shell with textures and two contrasting sides. The inner side has a clear impression of the robotic arm’s movements and looks like a digitally produced object, while the outer has a rough texture that reflects the process of applying sand by hand. In this way, these products are literal embodiments of digital and manual methods.
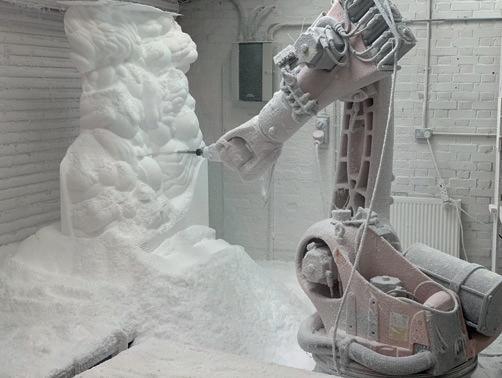
36 Six-axis robotic arm carving a mould for sand casting at Grymsdyke Farm.
37 3D-printed chair made with injections into sand using a sixaxis robotic arm.
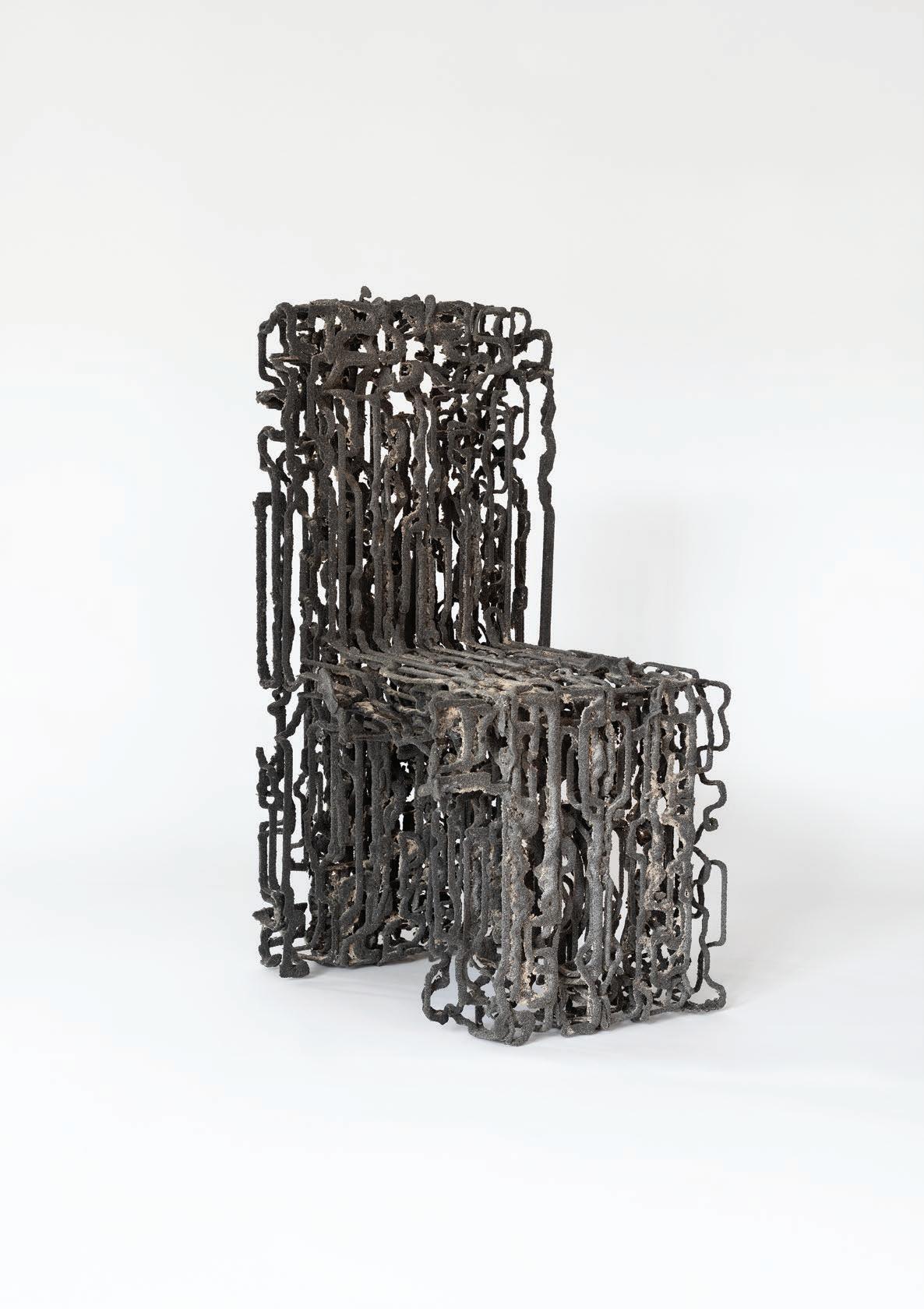
4. Interdisciplinary workshops and exhibitions with educational institutions, museums, architects, craftspeople and artists
The researchers collaborated with St John’s C of E Primary School in Princes Risborough and Bucks County Museum for an exhibition, SUP: Keys for Design and Play (postponed to 2021). A programme of workshops was designed for Year Five pupils to explore and identify SUP as a toy and an educational design tool, highlighting the value of play. These workshops were led by Grymsdyke Farm’s artist in residence, Rachel Jones. The participants were provided with a set of SUP components, which varied from session to session. The students were given prompts rather than instructions, which allowed them to use SUP however they liked. Collaboration was encouraged through a series of exercises in which the groups worked individually for the first half of the session, before connecting their creations with those by the other groups. There were several opportunities for the children to reflect on their creations and to draw and discuss what they had made and what they might like to make in future sessions.
Discussions and workshops were key to the curation of the exhibition at Bucks County Museum. The workshop structure was adapted from the V&A Young Curators Teaching Session, a framework for young children to learn about working in a museum, particularly as a curator. When designing the workshops, we looked to the methods and ideas of the play-based curriculum Anji Play: ‘teachers do not structure, guide or direct the activities or outcomes of the child’s experience during play. This means that you will not see Anji Play teachers actively lead a lesson or set out activities for the children’. This is to allow for ‘open-ended, self-determined True Play’ (Anji Play 2020).
We also looked at the work of play designer and professor of industrial design at Rhode Island School of Design, Cas Holman. Of particular interest was Rigamajig, a large-scale building kit inspired by industrial hardware for hands-on free play and learning. The design language of Rigamajig is paired back with minimal detail so that children can decide how they want to play. This thinking can be applied to the design language of SUP. The components are tonal but colourless, which allows for children to project their own ideas onto them.
Bucks and Thames Valley Local Enterprise Partnership (BTVLEP) are key partners in Buckinghamshire County Council’s Cultural Strategy for the county that ‘explores how creativity and culture can add to and enhance quality of life for the people that live and work here’ (Buckinghamshire Culture 2020). Through guidance and cooperation with Buckinghamshire County Council, the forthcoming exhibition at Bucks County Museum, SUP: Keys to Design and Making, aims to support the County Council’s cultural agenda.
38–9 Children at St John’s C of E Primary School playing with SUP components.
40 SUP table extension.
41 SUP roller coaster. 42 (overleaf) Le Mobilier d’architectes, 1960–2020, Cité de l’Architecture et du Patrimoine in Paris, 2019.
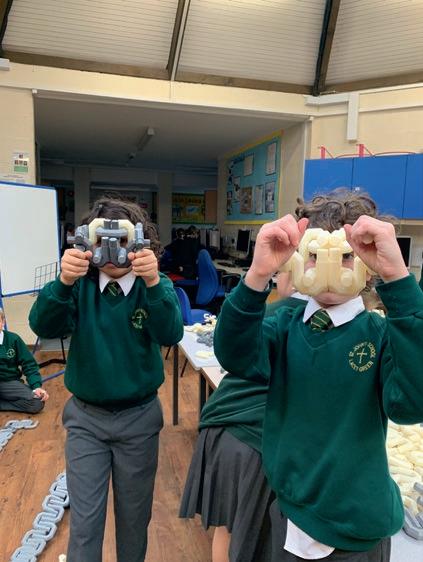
38 40
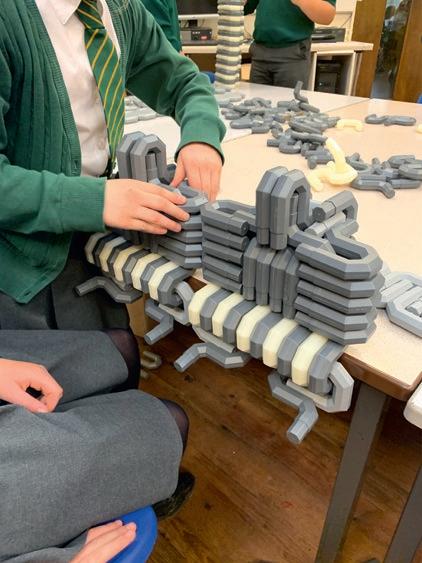

39 41

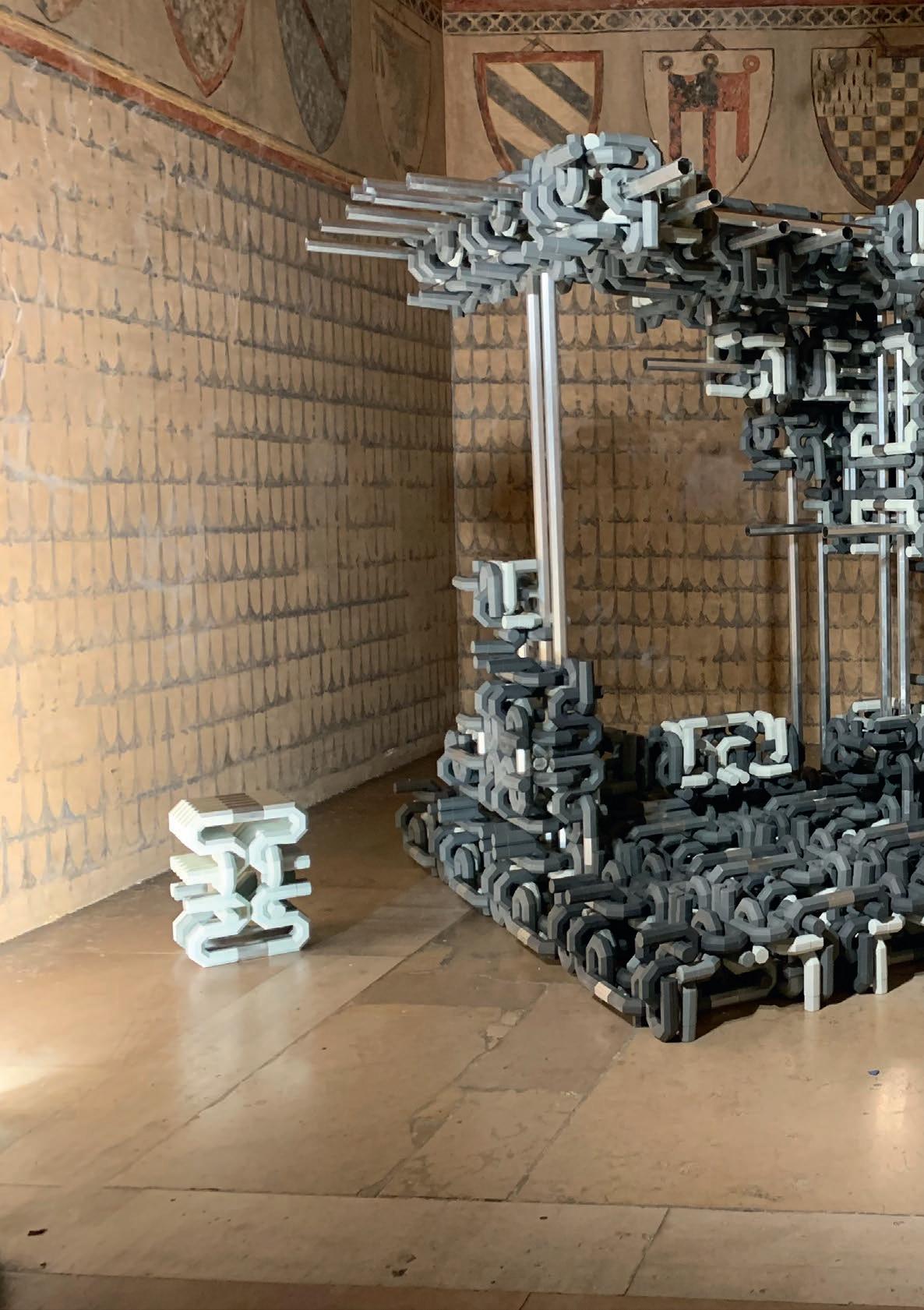
