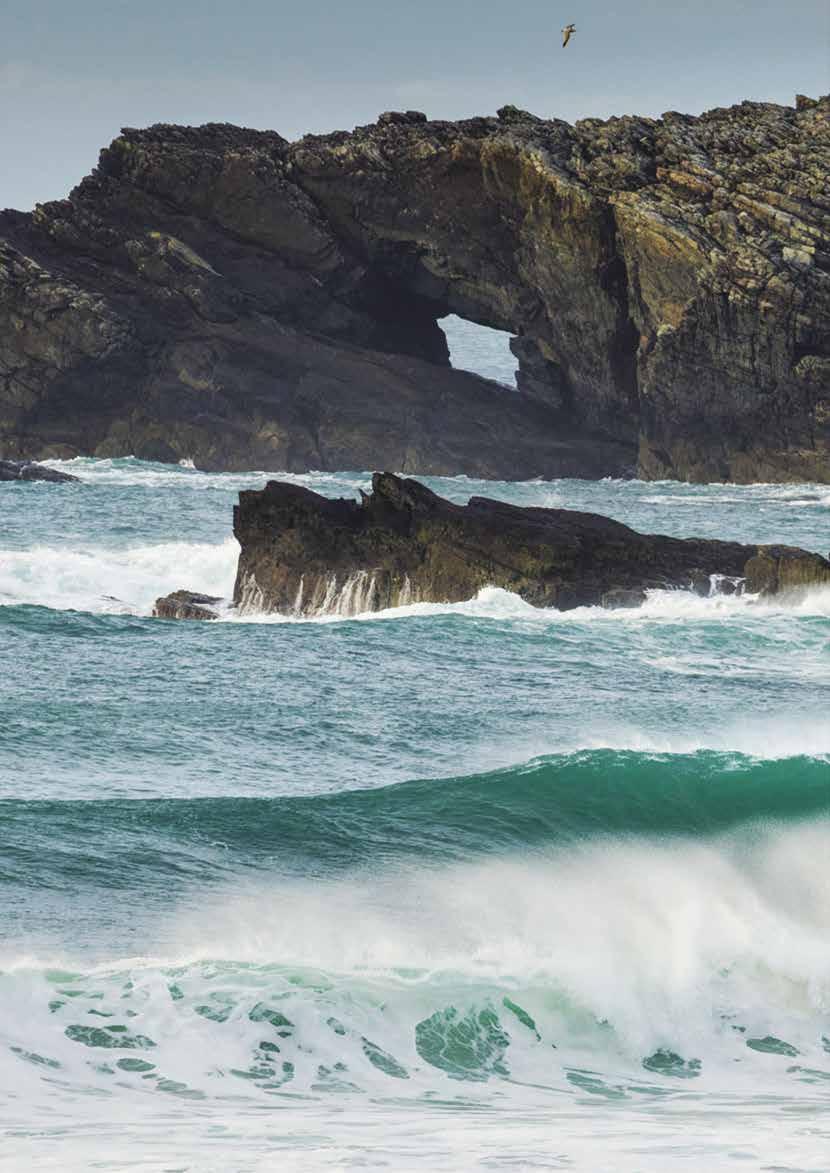
10 minute read
MAKERS AND INNOVATORS
from BASE # 07
The problem with neoprene: a closer look at environmentally friendly wetsuit innovation
Story | Chris Hunt
Advertisement

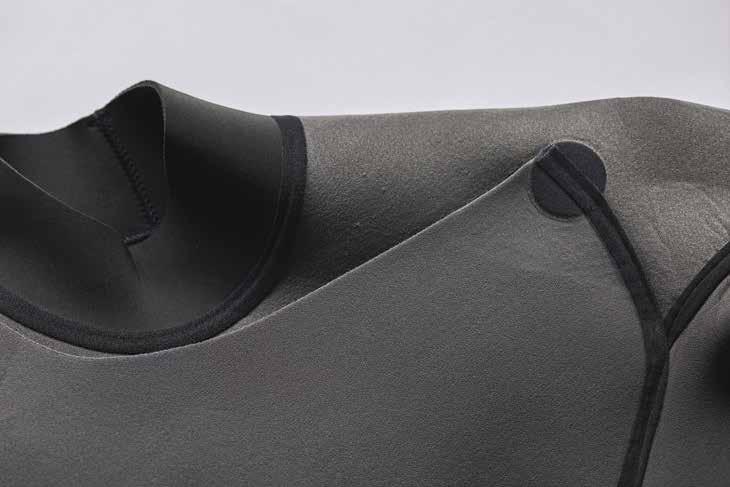
On the one hand, our community of ‘outdoors people’ are pretty well connected to the natural world. With endless hours spent exploring intricate regions of our environment, we’re often among the first to see the impacts of environmental destruction and global warming. Skiers and mountaineers are some of the closest witnesses to the ever rising snow-line; the relationship between land management and hikers and mountain bikers alike is an intimate one; while divers and surfers are acutely aware of ocean pollution and humanity’s losing battle with microplastics. On the other, sits a painfully real contradiction. We’re some of the most active travellers – ready at the drop of a hat to jump on a plane in order to chase specific weather windows around the globe and our addiction to kit is all too real. Cognitive dissonance at its finest. While the simple act of sliding across an open wave face is a movement intrinsically linked to the natural world; reliant on an understanding of tides, distant and local weather systems, ocean floor topography and marine wildlife, surfing still maintains a toxic dependence on damaging materials and unsustainable practices, ultimately polluting the same environments on which it relies. This is a brief history of the wetsuit and an exploration of where the industry finds itself today.
Riding waves is an ancient practice, with the first ridden swells being in sub-tropical island chains like Hawaii and French Polynesia, but the story of wetsuits designed for cold water surfing is relatively much more recent history.
In 1951, Hugh Bradner, a physicist from the University of California was experimenting with designs for the U.S. Navy. Deemed too similar to flight suits though, his first patent application was rejected while the Navy expressed their concern that in wearing his design, divers became more visible on sonar due to the gas within the suit itself.
The following year, with surfing in mind, Jack O’Neill started producing wetsuits out of his home in Santa Cruz. He formed the company O’Neill and began selling these suits in 1959 with the motto ‘It’s always summer on the inside’. Around the same time, Bob Meistrell started producing a similar design under the name Body Glove. Both O’Neill and Body Glove soon became iconic names within the sport and have endured right to the present day.
The main component in all of these historical wetsuit designs as well as today’s is of course neoprene: a foamed synthetic rubber compound, developed by DuPont in the 1930s. Neoprene is created through a chemical reaction using chloroprene and an oil derivative called butadiene as the binding compound in a process called polymerisation to create long chains of repeating molecules leaving polychloroprene chips. Those chips are then melted together and combined with other foaming agents and carbon pigments, before being baked and sliced into sheets.
Neoprene is of course not at all a unique material for wetsuits, it’s used in anything from car parts to drinks coolers. Making up the main body of the suit though, wetsuits are its most direct and obvious function – designed to absorb and trap a small amount of water warmed from the wearer’s own body temperature then used as insulation. Those first wetsuits of the 1950s were delicate and easily torn but they soon evolved to include a nylon lining, which
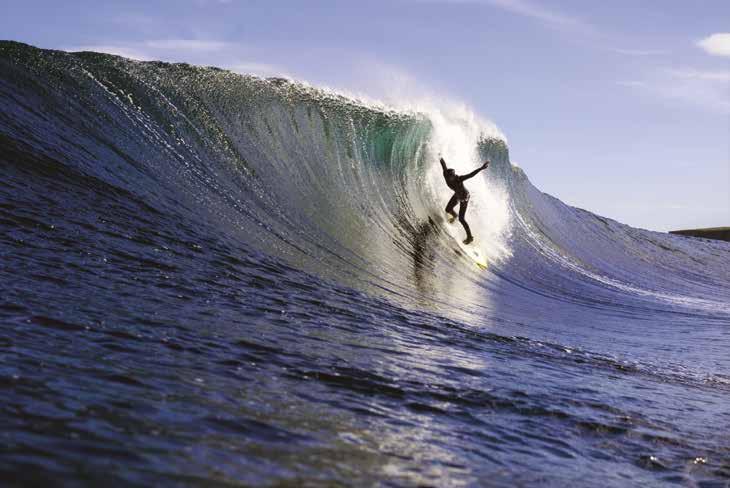
although strengthened the material, made them less flexible. By the 1970s, wetsuits were made of double-backed neoprene stitched together with new techniques developed for joining the seams, such as taping, glueing or binding. Eventually the process of blind-stitching was adopted in which the material is not completely punctured to further prevent leaking.
The decades that followed saw a boom in the popularity of surfing across the globe and across a greater range of water temperatures and so wetsuit brands experimented in the push towards increased comfort, flexibility and insulation. That included the introduction of different materials like Spandex, stronger glues and thermoplastics and in the ‘90s titanium became a feature of many higher-end wetsuits.
Today, riding waves is no longer dictated by season – at least not in the sense of temperature. Waves in the most northern reaches like the Aleutian archipelago of Alaska, Iceland or Arctic Norway and as far south as South Georgia and even Antarctica are all explored by travelling surfers.
Understanding our impact on the natural world is relatively recent in itself, and caught up in the quest for lighter, more durable, better performing kit, the application of those impacts to our outdoor kit is even more recent. In creating better performing wetsuits at a competitive price point, the environmental footprint of doing so has rarely been at the forefront of the agenda and neoprene has remained as almost the sole material. In a shift towards better environmental stewardship though, we’re seeing brands across the product spectrum reverting towards naturally occurring, responsibly sourced materials with a consideration for product afterlife.
For a while now, many mainstream surfing brands have opted for a limestone-based neoprene as an ‘environmentally friendlier option’. And while arguably the lesser of two evils, in reality this is still far from a lightly treading option. Limestone-based neoprene requires a huge amount of energy to process. First being quarried and shipped to its production facility, it’s then melted at temperatures of 3000ºC to be blended with other materials.
Gabe Davies is a former professional big wave surfer and several-times National Surfing Champion. He’s also from the North East of England which means he’s spent a huge amount of time wearing all kinds of wetsuits.
‘As a community we’re addicted to neoprene, with the history of the modern wetsuit built upon a reliance on the environmentally culpable petrochemical industry,’ he tells me. ‘This main ingredient in all the conventional wetsuits we surf and swim in is either derived from petrochemical or limestone sources. Both are non-renewable, fuel the climate crisis and do not have a circular end-of-life pathway.’
PREVIOUS PAGES: Cornish born Patch Wilson taking off deep under the curtain with a bit of ground to make up. AL MACKINNON FACING PAGE: The chest panel inner-lining from one of Patagonia’s natural rubber Yulex wetsuits. PATAGONIA THIS PAGE: Patch Wilson again weightless on a heavy North Atlantic slab. AL MACKINNON
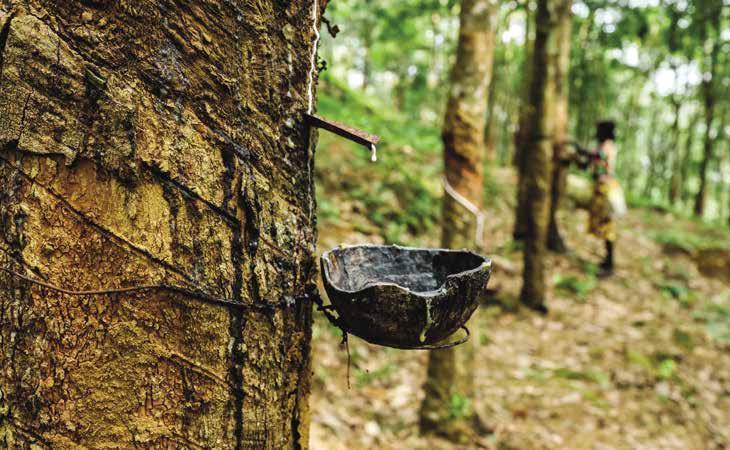
Depending on where in the world they live, keen surfers are likely to have several wetsuits to cover temperature fluctuation across the year, and each of those will go through a hell of a lot of stress each year, stamped on and dragged across gravel car parks in the fight to peel wet neoprene from skin in the icy depths of winter. But once deemed to be no longer functional the suits are not also easily recycled.
‘Once it’s started leaking due to wear and tear, pretty much every wetsuit made, is either dumped in landfill, or left to decay in folks’ garages,’ says Gabe.
And the idea of old product simply breaking down in an isolated location might seem like a pretty minor issue, all things considered, but the problems with neoprene run a little deeper than just the product itself.
‘Materials like Chloroprene have a dark shadow behind them,’ he says. ‘Communities surrounding the facilities that make Chloroprene, have been known to suffer very high risks of cancer. This is a very industrial process and we are only just learning about the shocking effect of the processes and its links way beyond their environmental footprint,’ he continues.
So, what’s the alternative when such a large portion of the world’s surfing population lives in some degree of cold water and it’s in the most northern and southern reaches in which the most exciting and untapped modern day surf exploration exists?
Natural rubber (as explored in issue 3) is available as a renewable source in the form of the Hevea plant and increasingly becoming a valuable resource in the world of manufacturing. Recognising that natural rubber in this format could be used to create a more sustainable alternative to traditional neoprene, the company Yulex began to explore the opportunity to replace the largest ingredients of a suit.
In 2014 Patagonia became the first brand to bring the material created by Yulex to market in the form of wetsuits. Since then it has revolutionised the brand’s entire wetsuit product line and in 2016 Patagonia’s entire range was manufactured using the naturally sourced neoprene alternative. As Oceans Manager for Patagonia, Gabe is a tangible part of this movement.
‘Natural rubbers are used in zero-failure products, such as surgical gloves, condoms and airplane tyres and in wetsuits, the performance properties match or beat limestone neoprene quite easily,’ says Gabe. ‘I think the surf-world is addicted to environmentally unsound ultra-flex suits. Patagonia doesn’t produce such suits as they’re made to hit a reduced price point which is then reflected in their limited lifespan, and poor durability. Yulex is a premium material which does increase the cost of the suit; however, the benefit is reflected both in performance and planetary impact. The process saves 80% CO2 per suit.’
As we as outdoor consumers better understand our responsibilities as environmental stewards, the industry moves slowly towards better environmentally concious decision making. But while Patagonia may have blazed the trail in the wetsuit space, it’s not something they’re looking to exclusively hold onto and a number of other companies including Finisterre in the UK and France’s Sen No Sen, have since followed suit.
THIS PAGE: Natural rubber being tapped from the FSC Certified Hevea tree in Sri Lanka. TIM DAVIS FACING PAGE: Dan Ross stood tall in the belly of the beast in the North Atlantic. AL MACKINNON
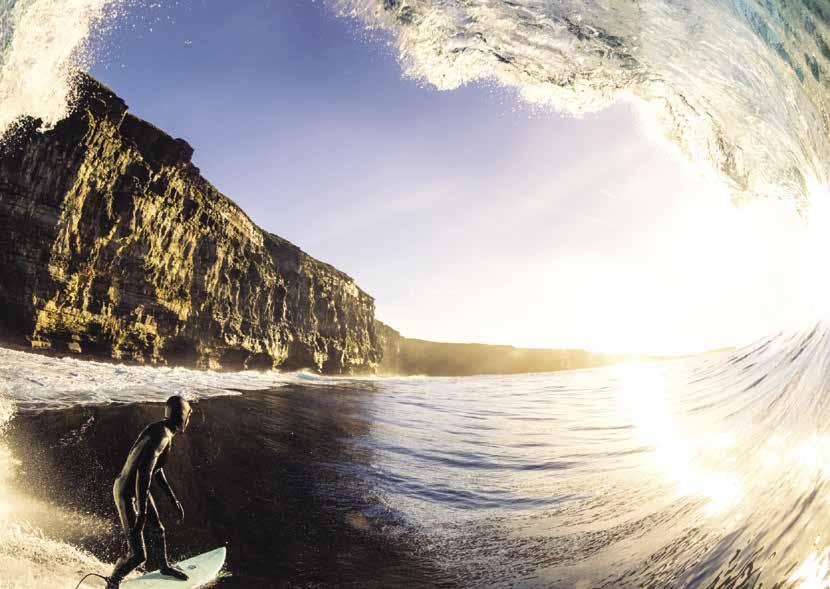
‘The journey has been over 10 years long from R&D to production,’ explains Gabe. ‘But as a company, Patagonia doesn’t seek to monopolise environmentally responsible innovation. We’ve been sharing our learnings around Yulex with other businesses and advocating that the industry kick its neoprene habit for years with limited success.’
But as is apparent across other industries, so-called environmentally friendly alternatives often just see the problem shift from one subject to another. Traditionally, Hevea plants are native to the Amazon rainforest where the issues around such cash crops are well documented.
‘It’s really important to recognise that sourcing natural rubber on the open trade market can result in clear-cutting of rainforest ecosystems, which again could be worse than the petrochemical process, and only 1% of natural rubber is certified by the Forest Stewardship Council,’ says Gabe. ‘Sri Lanka is where Yulex have their FSC Certified Hevea rubber trees which are tapped for their natural rubber.’
So what’s the impact of better sourced material on the final performance of these environmentally conscious wetsuits, something that brands occupying the space have worked tirelessly to build over the last decade? Does being environmentally conscious mean compromising performance and perhaps even comfort or durability?
‘If you want a super-flex suit with a limited lifespan, then don’t buy Yulex – that’s not why we use it. We design our suits to be repairable, long-lasting and multifunctional. We stand by our products and try and keep them in the water for as long as possible,’ says Gabe. ‘The first point of failure on a suit is usually the seams, rather than the rubber panels, or the recycled liners which coat the inside and outside of the suit so repair is our first course of action with our suits.’
Durability is undoubtedly an integral element in stiving towards sustainability and while there is still a huge shift towards lighter and smaller functional products across the outdoors space, we are seeing stronger multi-use items retake their seats at the table alongside them.
So with this in mind, has Patagonia perfected the recipe?
‘No, far from it, we’re certainly still learning. The blend of Yulex is the single largest ingredient, but the rest of the suit comprises carbon black [a material produced by the incomplete combustion of heavy petroleum products] which we use recycled tyres for, then there is a list of other chemicals, which are not clean, sustainable or eco-friendly,’ says Gabe. ‘We continue to strive to reduce or replace the harmful content in our suits, but Yulex alone is only part of the solution when it comes to the footprint of a wetsuit.’