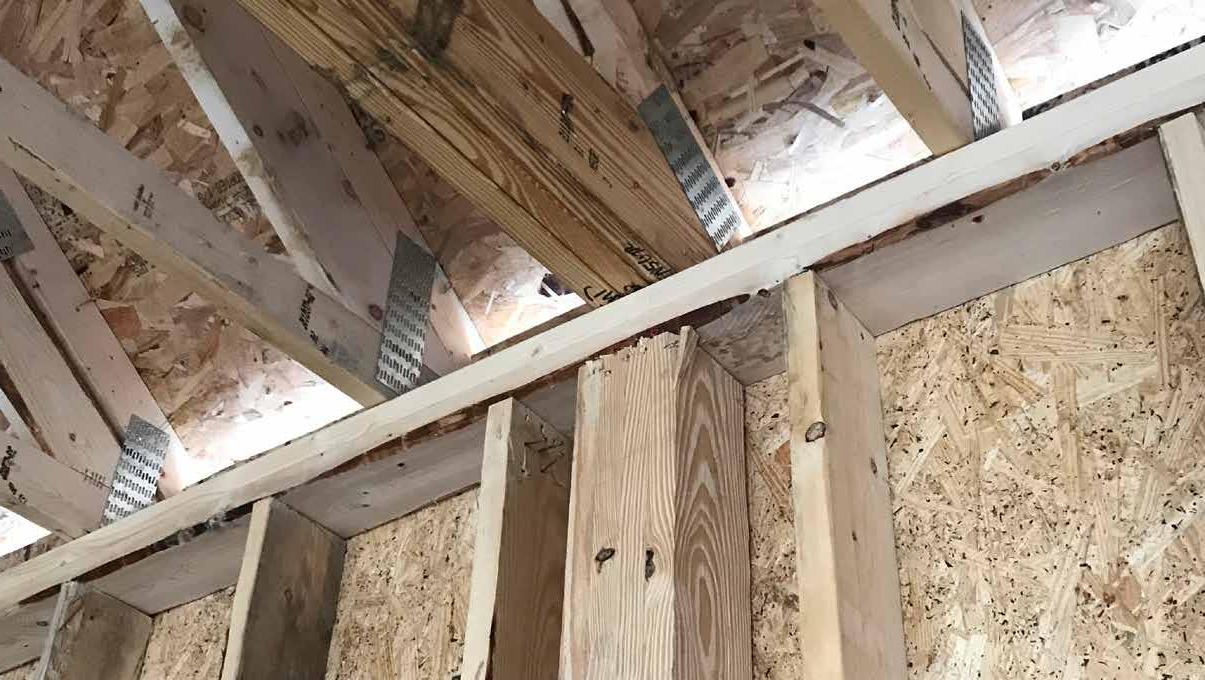
7 minute read
Q+A: Ask the Building Inspector
Ask the
Building Inspector
with Peter Kulczyk
Have questions you’d like to ask an expert?
We’ll feature a Q+A with various experts and topics each issue. Send your questions to
ASK@ HOUSINGFIRSTMN.ORG
Q. As a builder, we are often approached by product manufacturers who want us to use their latest and greatest products, such as new house wraps, foundation anchors, plastic decking, and other components that are intended for residential projects. Do we have any assurance that the local building inspector will approve the use of these products?
The answer depends on what information is provided to the building inspector for the plan review. The language in the code is prescriptive in nature as it addresses specific limitations and requirements related to life/safety, structural integrity, weatherresistance, and other considerations, but the code language is not intended to prevent the use of alternative materials, design, and methods of construction, provided that it is approved by the local building inspector (Minnesota Rule, MR1300.0110, Subpart 13). Your inquiry refers to house wraps (aka house sheathing paper), whereas the code refers to the use of one layer of No. 15 asphalt felt (Type I) or other approved water-resistive barrier (International Residential Code, Section R703.2). If a house wrap is proposed in a project, the permit applicant (typically the builder) should provide available project data that may include the manufacturer’s installation instructions, third-party test data, or a product evaluation report written by an approved agency (evaluation report numbers are generally stamped on the product). This process is very common with house wraps, foundation anchors, and many other components. In response to your inquiry regarding plastic (composite) decking, the code now requires compliance with ASTM D 7032 (International Residential Code, Section R507.2.2), and this information should be made available for the designer, builder, and building inspector as needed.
Q. Many new home designs contain roof girders and multiple-engineered wood beams intended to carry significant roof loads and floor loads. Who is responsible for
determining what is needed for the end support?
Generally speaking, the designer is responsible for this determination and ultimately the builder or permit holder. The building code addresses uniform loads for floors, walls, and roofs that are based on repetitive-member conventional framing techniques (three or more studs, joists, or rafters in the same plane) that includes the effects of wind, snow, soil, and earthquakes (International Residential Code, Section R301.1). Span tables in the code also address girder spans and header spans of multiple member solid-sawn lumber and required end support for four common species of wood. The tables in the code are based on the lumber species and grade of the wood (International Residential Code, Section R502.1). This is often referred to as both conventional framing and prescriptive design because of these known values. With that said, the code does not address span tables or bearing requirements for engineered beams (such as laminated veneer lumber, also referred to as LVL lumber; and other composite wood beams), and this also includes engineered floor trusses
(wood I-joists, open-web floor trusses, engineered joists) and engineered roof trusses. Engineered products are often designed and created using machinerated lumber, layers of wood and/or wood fibers (with random or oriented direction), gusset plates, combinations of engineered and solid-sawn lumber bonded together, and multiple other possibilities. This is often referred to as performance-based design or engineered design. The ability of these components to carry a load can vary from manufacturer to manufacturer.
When a new house plan includes an engineered wood floor system or roof system, it is the responsibility of the designer, and eventually the builder, to ensure that the house plan contains sufficient details to construct it in the field. For example, roof truss specifications and floor truss specifications should be on site during construction and available for the framing inspection. One of the biggest challenges for many designers and builders is in determining what type of support is required at the bearing locations (whether at the ends of the girder or at the mid-spans). Most truss specifications will indicate the actual design load, often referred to as the reaction load, at the bearing locations. The truss manufacturer will not typically indicate the actual type of end support needed, whether it is a built-up column of studs, engineered column, or steel post/column. This falls back to the designer who will need to take that reaction load along with other structural information and determine exactly what will be needed to carry that load, both in compression and laterally within the wall if applicable. This determination needs to be on the design drawings/house plans. It is not the responsibility of the framer to figure it out on site. This information will also be required by the building inspector during the plan review and possibly again at the framing inspection of the house. Putting a note on the plan that says “design by others” or “solid blocking under beam ends” will not fly for most building inspectors. When a bearing point of a girder takes place at an exterior or interior stud bearing wall the designer also needs to consider the height of the studs, how they are laterally braced (such as nailed to a wood structural panel or horizontal blocking), and the ability of the top plate to resist the crushing effect of the load (it might actually require a bearing plate for extreme loading situations).
Q. During the delivery of our framing materials for a new house, one of the roof trusses was damaged. We decided to scab a two-byfour to each side of the damaged truss and install it so we could get the roofing material installed before the snow comes down. What is the best procedure to handle this situation with a damaged roof truss?
Damage to an engineered roof or floor truss is unfortunate, but not uncommon. Sometimes they may be damaged during the delivery as they are slid off the truck on site or even while lifting the trusses into place. A roof truss is an engineered system with specifically placed framing members (usually machine-rated lumber) and gussets designed to typically clear-span greater distances than solid-sawn lumber joists and rafters. Trusses are generally designed by either computer programs or design professionals competent in that industry. Any alteration to an engineered truss will require the written approval of a registered design professional who will typically provide a truss correction sheet, and approval from the building inspector on site who will determine if the truss correction was made in accordance with the correction sheet provided (International Residential Code, Section R802.10.4).
A word of caution about truss corrections: The design professional may specify a particular grade of lumber for the correction, maybe even a wood structural panel gusset with a very particular glue and nail pattern, or maybe even some type of throughbolting for built-up damaged trusses. The correction on site needs to be as specified by the design professional with no substitution of materials (such as staples for nails or skipping the glue for more nails).
Q. We understand that the code requires a 36-inch guardrail for a deck when the walking surface of the deck exceeds 30 inches above the adjacent ground and that the openings in the guardrail need to be less than 4 inches. If the surface of a deck is less than 30 inches above the ground, can we build a guardrail of a lesser height and larger openings that would serve as a visual reminder to the homeowner where the edge of the deck is located? For example, if we constructed a guardrail that was 24 inches high with openings larger than 4 inches?
Yes. A guardrail 24 inches high with openings greater than 4 inches would be permitted if the adjacent grade (ground) was less than 30 inches.
The charging language in the code (International Residential Code, Section R312) only requires a “guard” when this deck example is “located more than 30 inches measured vertically to the floor or grade below.” In the code sections addressing “Height” and “Opening Limitation,” the code only applies to “Required Guards.” If you do not have a required guard then you have no height or opening limitations. In other words, the guardrail can be whatever height you choose and have whatever size of openings you choose.
DREAM BIG.
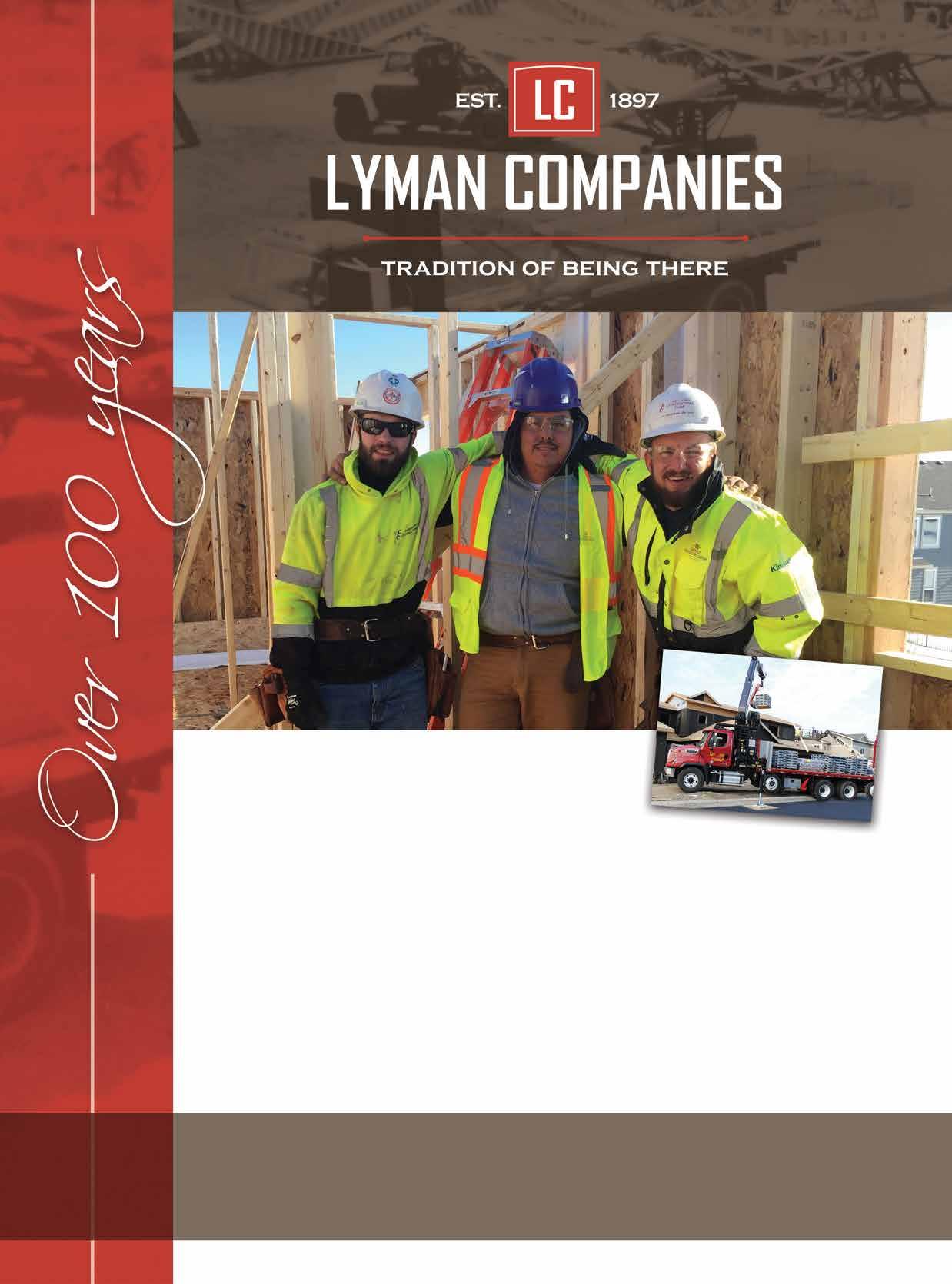
We all have dreams - dreams of making a difference in the world, challenging ourselves, achieving more and forging relationships on the job and in our lives. Here at Lyman Lumber, our goal is to be the best while being committed to helping our employees make their dreams come true. Lyman provides endless opportunities for growth. The company is built on excellence – in the services and supplies we provide to our customers, our working environment and the opportunities we provide to our employees. If you are a self-starter, with an entrepreneurial spirit, and are looking for a challenging career with endless opportunities for growth, consider joining the team at Lyman Lumber and our affiliated companies. The rewards go above and beyond great wages, benefits, and career paths. Build your dream – and make a difference in the world.