
10 minute read
Lessons learned
FOCUS
SAFETY
Lessons learned
By SAM BARNES
Seasoned South Louisiana EHS leaders share emerging best practices in safety.
Safety in the industrial space has been altered, perhaps permanently, by COVID-19. In the early days of the pandemic, safety leaders had to quickly pivot—often with little official guidance or information— to address a safety threat with unknown potential.
After more than a year of changing policy and evolving risks, along with significant investments in masks, sanitizing products and other measures, many of these policies have coalesced around a handful of central guiding principles. 10/12 Industry Report sat down with a few of south Louisiana’s seasoned safety leaders and asked them to reflect upon the challenges of the last year, and to discuss how they now approach safety on a daily basis.
DAVID MIHALIK Director of Environmental, Health, Safety, Medical and Security BASF, Geismar
GREG SATTERFIELD Senior Safety Engineer LyondellBasell, Westlake
SHAWN WARD Director of Corporate Health, Safety, Security, Environment and Sustainability Cornerstone Chemical, Waggaman The COVID-19 pandemic has been undeniably impactful to the safety environment in 2020-21. How has it impacted your daily schedule and the way you now approach safety in the field?
MIHALIK: BASF’s pandemic planning had been in place since the mid2000s with the arrival of H1N1 and the bird flu. We understood at some point a virus could emerge that would challenge the way we protect our team members and our workplace, and we were prepared to deal with it. What we did not anticipate or expect when we put the COVID protocols into place was just how long it would last.
SATTERFIELD: Dealing with the virus has resulted in our site and company creating additional safety measures for our teams to keep our site and employees safe. Over the last 18 months, we have spent a significant amount of time dedicated to the health and safety of our workforce. While it has always been a priority for our company, the COVID-19 pandemic has created a whole new layer to our health and safety protocols and brought additional challenges to managing the health and safety of our personnel.
WARD: Over the past few years, safety in the industrial workplace has continued to evolve with new challenges, new technologies and new processes to continue to drive our zero injury and incident goals. The most recent challenge, of course, has been the response to the COVID-19 pandemic. We have pandemic plans in place as part of our emergency management procedures; however, even the best plans must be adjusted to address unique situations, not the least of which is an evolving pandemic.
What have been some of the specific challenges posed by COVID-19? And solutions?
MIHALIK: BASF was prepared with a plan, but we recognized early on that the amount of safety supplies we had stockpiled would not sustain us for very long. This was due, in large part, to a supply chain that did not have enough inventory and struggled to supply the needs of even the health care industry. That meant we were forced to come up with alternative methods and materials to ensure safety protocols were being met at the sites until the supply chain and inventory could catch up to demand.
WARD: COVID-19 has taken workplace response planning to a whole new level to ensure the health and safety of everyone at our site. From enhanced monitoring and screening processes to appropriate PPE, to how we meet with one another to conduct business―all of these had to be reassessed and designed to ensure employee health and safety. Following Centers for Disease Control guidelines and other best practices to keep employees safe and healthy amidst a pandemic has been a real learning curve, but it has also inspired new ideas and approaches to pandemic response and exposure prevention, including enhancing work stream efficiencies and safely minimizing potential for exposure during the work day. Throughout the pandemic, we have continued to increase and refine our industrial hygiene practices and procedures onsite, and we have made sure to update those aspects of our regular workplace safety programs.

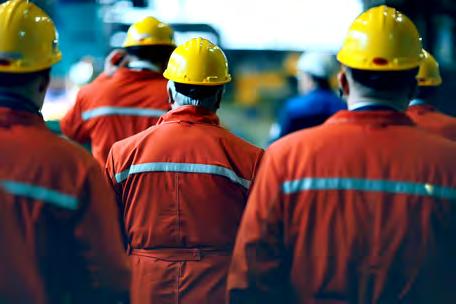
Apart from COVID-19, have there been other safety measures that have evolved or been refined in any way? And are there any new metrics that you use to measure and evaluate safety? Have the tactics or strategies for improving safety changed?
SATTERFIELD: Personally, I think it is important to be empathic when dealing with employees and contractors. For example, “What would I have done if I were in their shoes?” To treat employees and contractors fairly as one team promotes belonging, builds relationships and empowers those to be more engaged in the program and the processes resulting in success. Treat them how you would like to be treated. This takes time, effort and consistency by the entire management team. In my opinion, having strong relationships with your workforce is key to success in any type of work environment.
Each year, LyondellBasell holds the annual Global Safety Day, which is an opportunity for us to advance LyondellBasell’s GoalZERO culture. It means that we are committed to operating safely with zero injuries, zero incidents and zero accidents. This year’s theme was “Back to Basics,” which was an important emphasis, as many employees and contractors performed their job duties in other locations due to the pandemic, with less people and under different circumstances. During this time, it has become even more critical to stop, think what could go wrong, and adjust the plan, if necessary, to complete the job safely.
MIHALIK: The increase of diversity and inclusion in the workforce has changed many of the strategies and practices for improving safety. An emphasis on diversity not only increased the number of women and minorities in roles within industry, they were also encouraged to speak up about safety at work―both their own and that of their coworkers. By asking personnel to challenge the norm, or the way tasks have always been done, we have seen continuous safety improvement.
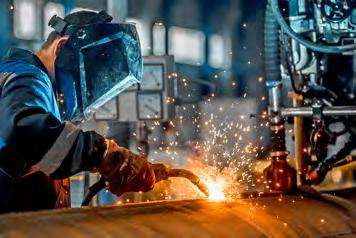
WARD: Our training is more robust now. Our processes―from potential exposure reporting to behavior safety practices―are now even more clear to make sure we identify, address and correct any issues quickly as they arise. New technologies and equipment have also improved worker safety over the past decade. A shift to more improved virtual monitoring systems and equipment, improved personnel and stationary monitoring equipment, and automation has improved the way we can utilize data to improve the overall safety, health and security at our site.
MIHALIK: From a pure safety perspective, we have seen a more focused emphasis in several areas during the last 10 years. One example is preventing dropped objects from overhead. Workers did not always concern themselves with controlling tools, parts and other objects near edges of structures while working overhead. Historically, the answer was to simply barricade the area below the work, and no harm would be done if something fell.
However, when working major turnaround projects with hundreds of contractors, this approach simply does not work. Now, BASF and others in the industry implement protective netting, require the use of safety tool tethers and train employees on prevention and reporting of dropped objects as significant incidents. This is just one of many areas where we have focused on a problem and developed solutions to improve workplace safety.
SATTERFIELD: There have been a lot of improvements around PPE, such as gloves and fall protection. Looking at and managing human factors has also been getting a lot of attention in our industry, especially around incident investigation. What are the biggest challenges to doing your job, and how do you overcome them?
WARD: Our challenges are also our biggest opportunities. They are the new generation of employees, and new advances in technology and equipment. This new wave of talent has inspired a renewed focus on how to ensure a good understanding of safe practices and how we communicate with and train employees on the job.
New technologies and equipment have also improved worker safety over the past decade. A shift to more improved virtual monitoring systems and equipment, improved personnel, and stationary monitoring equipment and automation has improved the way we can utilize data to improve the overall safety, health and security at our site. This also creates an opportunity for us to take a fresh look at how to improve already robust process safety programs by looking to new metrics and data. For example, instead of only focusing on traditional lagging indicators, such as the number of recordable injuries and first aid injuries, we can now also focus on more leading indicator metrics, such as the number of near misses, to help us implement preventative measures that can allow us to continually improve.
SATTERFIELD: Dealing with the virus and not being able to have face-to-face meetings with our employees and site contractors has created a big gap in how we communicate and train. We just continue to try to be creative with our communications. It has caused a tremendous impact on safety and how it is managed.
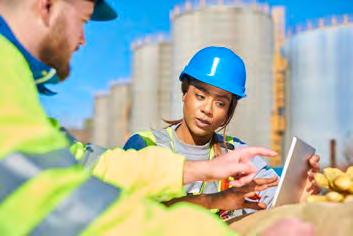
MIHALIK: The biggest challenge of this job is changing people’s mindsets and behaviors. BASF introduced behavioral-based safety about five years ago. With this program, employees have the opportunity to improve their personal safety and that of the workplace through observations and are trained to identify the barriers to a continuous improvement in safety performance. I would say supervisor support of this approach has been a challenge. The perceived pressure to produce can run counter to the basics of a behavioral-based program. The behavior-based premise that we must “go slow to go fast” is contrary to what many have historically been taught. Although we faced some obstacles in the beginning, we have seen tremendous payoffs with improved safety at our sites.
INDUSTRY INSIGHTS
SPONSORED BY:
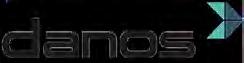

Reduce expenses and increase efficiency with i2ms
Q: What’s a surefire way to tank productivity and profitability? A: Relying on antiquated tracking systems to manage today’s Supply chain demands.
For companies looking to stay ahead of the curve with their inventory management capabilities, technologies such as automation, artificial intelligence (AI) and machine learning (ML) are a must. Working with a team of experts, Danos has created a fully customizable data platform that leverages cutting-edge technology to optimize even the most complex inventory management demands.
INTELLIGENT INTEGRATED MATERIALS SOLUTIONS
Danos’ Intelligent Integrated Materials Solutions (i²ms) imbeds automation and digitization into your supply chain management system. Marrying people, processes and technology, i²ms seamlessly manages the largest, most complex systems with greater efficiency.
For nearly 75 years, Danos has delivered innovative solutions to help solve their customers’ big challenges. i2ms is the latest example of that innovation at work.
IF YOU CAN MEASURE IT, YOU CAN IMPROVE IT.
Knowing exactly what items you have in your inventory means you can avoid over- or under-stocking, optimize available resources and cut back on unnecessary (previously hardto-track) costs. This is the key to increasing business efficiency and profits, particularly in materials management. i²ms impacts your bottom line with accurate, visible and real-time, up-to-date information.
Using the most forward-looking technologies like AI, ML and IoT (the Internet of Things), i²ms functions as an upgrade to your existing system. i²ms utilizes nine independent modules—each targeting a different aspect of materials management—to optimize operations. When applied together, these modules represent a comprehensive, end-to-end solution with “plug-and-play” components to meet individual customer needs.
Built for companies of all sizes, Danos’ i²ms carries low up-front costs and has options for transaction- or subscription-based pricing. The new service offers customers a unique opportunity to optimize and manage the full range of materials management operations. Visit www. danos.com/i2ms to find out how much you can save.
Customers can realize 10- to 30-percent cost savings using i²MS.