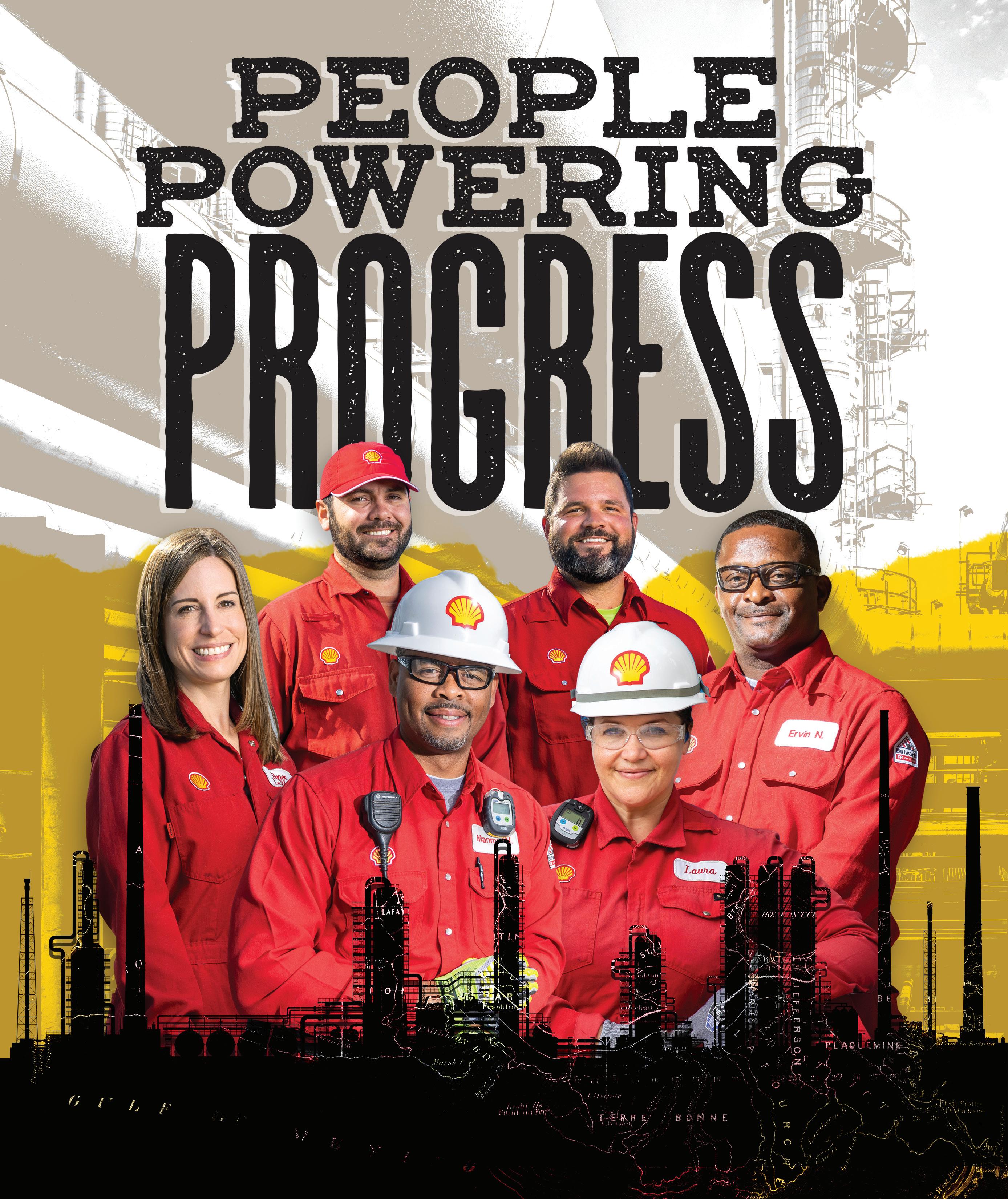
LOUISIANA IS A MAJOR PLAYER IN SHELL'S BOLD NEW FUTURE.
“
LOUISIANA IS A MAJOR PLAYER IN SHELL'S BOLD NEW FUTURE.
“
Louisiana
With over 100 years of history in Louisiana, Shell remains committed to powering progress by transforming our business.
OUR PROMISE is to deliver lower carbon fuels and products. As a key part of Shell’s energy transformation and path to netzero emissions by 2050, we are in the process of repurposing our Convent site into a hub for low-carbon fuels and products.
In addition, Shell will increase performance chemicals production at its Geismar chemical facility and produce more renewable fuels, lower-carbon ethylene and circular chemicals from recycled plastic waste at its Energy and Chemicals Park, Norco.
SHELL IS LEADING THE TRANSFORMATION INTO THE NEXT 100 YEARS.
The creative thinking of more than 3,000 Shell employees will power progress here in Louisiana.
The U.S. Gulf Coast has for decades been a key hub for Shell and the U.S. energy supply. Shell’s investment in transforming our assets is the latest example of bold plans to decarbonize our operations. We are committed to transitioning to a net-zero emissions energy company by 2050.” EMMA LEWIS | Shell Senior Vice President U.S. Gulf Coastis at the forefront of Shell’s energy transformation.RANDY Instrument Inspector Shell Geismar
Powering Progress” isn’t just some catchy new marketing slogan. It represents the literal transformation of Shell’s global business model and the pursuit of a more holistic approach to caring and providing for the people of Louisiana and the communities in which our plants reside.
It’s about honoring our past while also building a legacy for our children, grandchildren and future generations through the achievement of net zero emissions, empowering lives, respecting nature, and generating shareholder value.
Internally, that means producing the sustainable products that our customers want, such as low-carbon fuels, sustainable aviation fuels and circular chemicals. Externally, it means working in a decidedly different and engaging way with the communities around our sites and being respectful of the state’s ecosystem.
All of Shell’s Gulf Coast manufacturing sites will be involved in the company’s energy transition in the coming months and years—and in many ways that change has already begun. At Geismar, we’re now making sustainable products for our customers, and at Norco we’re using sustainable feedstocks in our steam cracker and cat cracker units. And upon completion of its “re-birth” in the coming years, the Convent plant will serve as an anchor for carbon capture, hydrogen, low-carbon fuels and circular chemicals, among other things.
The future is bright for the Louisiana industrial community, as it is a critically important state to Shell’s global strategy. As evidence, the Norco facility was recently designated as one of five Shell Energy and Chemicals Parks and Geismar as one of six dedicated chemical sites.
Above all else, though, Shell recognizes that people are integral to our future success. Therefore, one of our biggest goals will be to diversify and expand our reach so that there are more opportunities available to a more diverse mix of businesses and individuals in our communities. We’re also expanding our emphasis on growing local businesses so that they can more easily participate in Shell’s bold new future, and we’re also renewing our investments in education, the arts and a host of charities.
Shell recognizes that we all need to work together, collaboratively, to grow as a company and as a community. As an outcome of that, we hope to create a place that flourishes alongside us.
We hope you’ll discover in these pages our excitement about the future and commitment to our community. Together, we will be first-hand witnesses to the reinvention of the industrial sector. What an exciting journey ahead of us. Thank you.
Kallenberger General Manager Shell ConventShell pioneered energy exploration and production in the U.S. DeepWater Gulf of Mexico and continues to build on that legacy in Louisiana.
The world’s largest refining catalyst plant completed an expansion in 2020.
GEISMAR CHEMICAL PLANT
One of six dedicated performance chemical sites focused on net zero ambitions
NORCO MANUFACTURING COMPLEX
Home to Shell Oil Products and Shell Chemicals, now designated as one of five energy and chemicals parks
CONVENT FACILITY The shuttered refinery is being transformed into a hub for low-carbon fuels and products.
• Robert Training and Conference Center in Tangipahoa Parish, a world-class facility providing offshore training for oil and gas industry workers as well as military and law enforcement
• Corporate Center in New Orleans with an advanced technology center for monitoring and supporting offshore assets in real time
• Marine logistics activities from Port Fourchon
• Contracted Heliport Base and Distribution Center for supporting marine and aviation logistics in Houma
SHELL HAS BEEN a strong presence in Louisiana for a while—a long while. For more than 100 years, the company has had a significant economic and social impact on the region. That isn’t about to diminish in the coming decades.
Louisiana is already home to a wide range of Shell activities, from oil and gas exploration and production to pipeline supply and distribution, from refining and chemicals to LNG for transport. But they’re on the verge of a metamorphosis that will reinforce the company’s commitment to a sustainable future.
Nothing made that more apparent than the recent announcement of an unprecedented $27.5 million investment to create the Institute for Energy Innovation and the Our Lady of the Lake Interdisciplinary Science Building at LSU. And big changes already underway at its Convent plant will convert the facility into a producer of alternative fuels.
It all sends a very clear message: Shell, along with much of the state’s industrial community, plans to evolve, grow and thrive no matter what the future of energy might bring. As the new energy system emerges, the team behind it will continue working with stakeholders to keep energy flowing and transform facilities to deliver lower carbon fuels and products, such as circular plastics, biofuels and lower carbon specialty chemicals.
They do that with a strong commitment to the places they live. Case in point: Shell is continuing its three decades-long partnership with academic institutions and key thought leaders on ways to advance research and deploy nature-based solutions to protect coastal communities and critical infrastructure along the coastline.
Through its partnership with Nicholls State University, for example, Shell is helping to research, propagate, and plant native coastal vegetation, and improve wetland restoration efforts for a wide array of project partners.
But of course, Shell’s economic impact to the state of Louisiana is the big story. From a business perspective, the company’s impacts are far reaching.
THE SHELL CONVENT FACILITY, located midway between Baton Rouge and New Orleans, has been remarkably resilient since its founding in 1967. The Convent site is situated on a 4,400-acre tract of land straddling Ascension and St. James parishes and, until its closure in 2020, processed about 240,000 barrels per day of crude oil, producing conventional petroleum products and refinery grade sulfur.
It began operations as a Texaco refinery, but in 1998 a joint venture formed between Texaco, Saudi Refining and Shell Oil Co. operated the site under the Motiva name. Then in May 2017, Shell assumed full ownership.
But the story doesn’t end there. Not long after Shell made the difficult decision to shutter the refinery, they chose to resurrect the site as an alternative fuels complex. It’s all part of the company’s global strategy to invest in a core set of uniquely integrated manufacturing sites strategically positioned for the transition to a low-carbon future.
Shell views Convent as well-positioned to support its plans for growth while delivering value to shareholders. The site is currently managed by Kirk Kallenberger.
A groundbreaking transformation is already underway
THE SHELL CHEMICALS GEISMAR facility along the east bank of the Mississippi River, some 20 miles downriver from Baton Rouge, has a long and storied history. In January 1965, Shell purchased 700 acres for the Geismar site.
Today, the site has grown to 800 acres, of which only 400 acres are developed. From that location, the more than 600-employee facility manufactures detergent alcohols, ethylene glycol, alpha olefins and a diversified line of ethylene based industrial chemicals used in a range of modern applications.
Recently, Shell Geismar expanded its alpha olefins capacity during the historic Tiger AO4 project, adding some 425,000 tons of capacity to make it the largest producer of the material in the world. Alpha olefins are used to make highperformance synthetic lubricants, biodegradable detergents, drilling fluids and stronger, lighter polyethylene film.
The plant also produces a significant amount of ethylene glycols, which are used to make soft drink bottles and containers, as well as polyester fibers in clothing, upholstery, carpet, pillows, and surgical supplies. Some ethylene glycol is used in the production of antifreeze and heat transfer fluids.
Shell Geismar is a major economic engine for the Ascension Parish community. Plant personnel strive to improve the quality of life in the community, chiefly by playing an active role in the education system and charitable organizations. Employees also devote their hours to community service.
The site is currently managed by Dai Nguyen.
CONVENT GENERAL MANAGER Kirk Kallenberger has never intentionally quit a job, but the name on his paychecks has changed quite a bit. Shortly after the Kansas native earned his degree in mechanical engineering from Kansas State University, he landed his first job at Star Enterprise, then worked in the company’s Delaware office for 10 years before landing in Louisiana in 2000.
For 18 of the last 22 years, he has been working at the Convent facility. “It’s an interesting dynamic,” Kallenberger says. “I’ve never intentionally left a company; they’ve just changed owners. Star Enterprise became Motiva, and then Motiva became Shell.”
One could say that refining is in his blood. Kallenberger is a third-generation crude oil refiner: His father worked for Texaco and his grandfathers worked for Sinclair and Sunray-DX. His background and experience are in maintenance turnarounds and projects. In fact, prior to the Convent facility’s closure in late 2020, he was the facility’s maintenance turnaround and construction manager.
The closure was a pivotal moment for him. “They asked if I would be willing to stay, and since my heart has always been at
this site, I said yes,” he says. “At that point in time, I didn’t know what the future of the site was going to be. All I knew was that my purpose was to safely shut down and preserve the site.”
It later emerged as one of the best decisions of his life, as some months later Shell began seriously contemplating the facility as a location for its new alternative fuels plant. For Kallenberger, it’s the perfect feel-good story for the site and community. “Now we’re talking about transforming our business into something that will prepare us for the next 100 years and, to me, being a part of that is just incredible," he says. “To set up the energy business for the future of my kids and their kids is the opportunity of a lifetime.”
Kallenberger’s knowledge and expertise certainly qualifies him to help design, build and operate the plant, but he admits there’s still a bit of a learning curve. A lot of the technologies to be deployed are new to him, but he is not alone. “They’re new to most people, and some of them, quite frankly, are still in the developmental phase,” he says.
Along the way, he has partnered with Shell technical experts to learn about new technologies and processes. “I want to be able to explain to the people that work for
me what the future looks like and what a future operating facility at Convent might look like.”
These days, there are some 230 contractors buzzing about the Convent site, working on preservation activities such as demolition, tank cleaning and moving hydrocarbons out of the plant. At the same time, others are supporting the development of new projects.
All the initiatives associated with the energy transformation are in the early phases of design, with the first project expected to come online in 2025, and the last in 2029. In the meantime, he has begun conversations with several contract partners as well as local educational systems to see what Shell can do to ensure there will be an adequate workforce available when it’s needed.
Having a front row seat to the rebirth of Convent has been a humbling experience for Kallenberger. “This is the 55th anniversary of the site, and if you’d asked me a year ago, I wouldn’t have thought we’d be able to celebrate it,” he adds. “I think that’s going to be a very big milestone for Convent and Geismar. These two sites are really trying to chart a course for the next 55 years, and that’s pretty special to me.”
THOUGH SHELL GEISMAR’S general manager Dai Nguyen is a Louisiana native, he took a very roundabout way to return home. After graduating from Tulane University with a degree in chemical engineering, he landed his first job at Shell’s Deer Park, Texas, plant. From there, his job took him overseas to such exotic locales as Amsterdam, Kazakhstan and Singapore as he worked his way up in the organization.
His 32-year professional career at Shell reached its pinnacle when he was appointed manager of the Geismar plant.
But growing up in New Orleans, his life was originally going in a different direction. “My parents wanted me to be a doctor,” Nguyen says. “I was pre-med, but after my first year or so I started to think it would take way too long to be a doctor. I said, ‘That’s OK. I think I’ll be a chemical engineer.’”
Throughout his life, Nguyen has made a point to work outside his comfort zone. He has not only dabbled in engineering, but also in human resources and HSE in both the upstream and downstream parts of the business, and in increasingly larger roles.
That’s been the pattern most of his life: He strives to do things he has never done.
In the process, he has adopted a learner’s mindset. “I’m always seeking challenges both from a business and personal side,” he says. “Nearly all of my assignments have given me very specific business challenges where I had to go and transform a business—take it to a different level.”
His experience abroad was particularly impactful and went a long way toward shaping his current management style. “Overseas, I would frequently go into a space that was completely different than an established facility,” he adds. “I was going into countries where the entire workforce was different. I had to learn about that workforce and their capabilities. Typically, the organization wasn’t as mature, and the skill levels weren’t what I was used to.”
In Singapore, he managed a safety program for a large multinational workforce. “I was challenged with finding ways to make those safety measures simple and effective for folks who didn’t necessarily know English,” he says. “I had to be sure of the message, simplify it as much as possible, and make it clear and concise.”
It was a valuable experience, as Nguyen learned to be more precise in
his communications. There’s little doubt that has helped him in his current role. As manager, he feels it’s important to connect with and understand the people in his plant. “If I am transparent and communicate honestly what I know and don’t know, typically people are willing to listen.”
When asked to lead the Geismar plant, he felt it was the next logical step. He also knew that the southeast Louisiana plants would soon become the epicenter of Shell’s strategic plans for the future. “We’re celebrating 55 years, and we want to be around for another 55-plus,” he adds. “The way to do that is to lead from the front. We are a leading business, so let’s make sure that we extend that and continue to grow and perform.”
Nguyen is equally committed to growth in his community. Apart from Shell, he is on the board of directors for the Capital Area United Way, the Baton Rouge Area Chamber, Louisiana Chemical Association and The Arts Council of Greater Baton Rouge. He also promotes investing in childhood education. “Drawing on my own experience, being an immigrant to the U.S., I’ve seen education as a proven way to improve yourself, your community and your family.”
From the age of 6, George Stoulig can remember seeing his dad come home from work each day, dressed in his iconic Shell uniform. As he got older, he came to understand the financial security those moments symbolized for the family. Chris and Jordy Templet grew up in a circle of dads and uncles all working at Shell. And 16-year Shell veteran Terrance Coleman Sr. is experiencing indescribable pride right now that his 24-year-old son is following in his footsteps with the company.
Over the years, thousands of Louisianans have found their calling— and their comfortable livelihoods—in industrial service at Shell. But there’s a unique phenomenon here that spans generations: Inspired by a grandparent, father, brother or cousin, relatives follow in those footsteps, seeking the same opportunities. It’s not uncommon to see daughters, sons, cousins, aunts or uncles working with or near—and in some instances, even training—one another.
It’s a culture that is welcomed and fostered by Shell, through family picnics, jambalaya cookoffs, a longtime focus on work/life balance— particularly for those who are related to one another—and more.
“It’s like a hometown,” Terrance Coleman Sr. says, “and everyone thinks highly of the company.”
BEING just six years old and watching his dad come home from work each day, donning his Shell uniform. His father worked at the Convent plant as an operator, and eventually retired as the site’s Leak Detection and Repair Coordinator in 2013.
“I saw him work throughout my entire life and noticed what kind of financial security that his job provided for my family,” Stoulig says.
The son also remembers Shell-sponsored family days and plant picnics. From the beginning, the Shell family was like his family. “I knew the other plant workers’ children, whose father worked with my father,” he says. “So even when I got hired on, a lot of the guys I started working with were older gentlemen that I had known as a kid.”
When he began working for Shell 23 years ago, it was more like a reunion than a new job. It felt like coming home. “For about 14 years, my dad and I both worked at Convent,” Stoulig says. “Most of the time, we worked in different areas and had different jobs, but sometimes we’d work a turnaround together.”
There was no doubt that they were related. They share the same name, for one thing. “I’m 6 foot 7 inches tall and he is 6 foot 5 inches,” George says. He was always ‘Big George’—until I got there. It led to some funny nicknames for the both of us.”
Stoulig began working for the Convent plant as an operator in the tank farm area. Eventually, he was elevated to production team leader, then advanced to interim production supervisor, and ultimately to an operations turnaround supervisor in his last years at Convent. He now works as a project specialist at Geismar.
He initially took a different path, pursuing a career in criminal justice. He even worked in law enforcement for a couple of years. “I liked it, but it wasn’t providing the benefits that I saw in the plant job,” he adds. “Convent was hiring, and in talking with my dad I decided to go ahead and apply. Even federal law enforcement probably wouldn’t provide the salary or benefits of a company like Shell.”
There have been no regrets, and while
the closure of the Convent plant was initially a “kick in the gut,” he is “excited and proud” to see it being transformed into a new purpose.
He easily transitioned to the Geismar plant, albeit in a different role. He trained at the Geismar training facility, and even worked hand in hand with the person he would eventually replace. He now serves as a liaison between the capital projects group, construction group and operations team during capital projects.
Stoulig will be eligible to retire in just five to seven years. That’s one of the big benefits of working for an industrial company, he says—workers can actually turn it into a
lifelong career. “I like where I’m at; I like the people and the job,” he says. “I’m just happy to be able to stay with Shell.”
Who knows? Upon retirement he might return to law enforcement. In 2020, he re-enrolled at Southeastern Louisiana University and over three semesters knocked out the last six classes he needed to earn a bachelor’s degree with a concentration in behavioral sciences and minor in criminal justice.
But in the end, what matters most to Stoulig is family, and following in his father’s shoes. “My father is proud of me, and that I’m advancing in my career at Shell.”
IT WASN’T PLANNED this way, but St. Amant cousins Chris and Jordy Templet began their Shell careers at the same time back in 2011. A Shell job was already a family thing— Chris’ dad and uncle and Jordy’s dad and uncles were already working at the plant.
And while all their relatives have long since retired, these two continue to thrive and advance in their careers at Geismar.
For Chris Templet, joining the Shell team was a lot like coming home. Chris is currently a support technician in the Geismar plant’s HFE K-Unit, where he assists with troubleshooting, permitting and turnaround oversight. It also happens to be where his dad worked until his retirement in 2010. In fact, his father was asked to help with his initial training.
Even before then, Chris was following in his dad’s footsteps. Prior to 2011, he worked for a variety of contract companies and for a pipefitters’ union in New Orleans. “My dad was also a pipefitter and welder when he was younger,” he adds.
Jordy Templet’s current role is as the E-Permit to Work focal point, where he and a group of technicians assist in the rollout of Shell Geismar’s new electronic permitting process. For a time, he even worked alongside his cousin, before Chris was transferred to another unit.
In his early years, Jordy’s path was going in a different direction. After graduating with an industrial technology degree from the University of Louisiana at Lafayette, he taught school for three years. He even dabbled in professional baseball, playing for the Toronto Blue Jays organization.
His family connection was without a doubt a reason for his decision to come work for Shell. Back in the day, Jordy says, he had a lot of friends and family members who worked at the plant. “When we got hired on, there was still that same vibe,” Jordy says. “That was a big draw for me—the culture and the atmosphere of knowing a lot of family and friends that worked out here.”
The promise of a stable career was another benefit. “My dad worked in the Geismar lab,” Jordy says, “so I knew a lot about the place, the benefits of working here.”
Over the years, Chris and Jordy have witnessed a lot of change and growth at the Geismar plant, most of it prompted by new technology. “There have been a lot of changes in policies, processes and tools … such as E-Permit. Chris and I have been a big part of that,” Jordy says.
There’s plenty to like about working for Shell, with the security the company provides near the top of the list. There’s also a unique family culture fostered by Shell, reinforced by the knowledge that their fathers and uncles made a career out of it.
They both remember a lot of family functions at the plant. “They’re still doing things like that at the Shell Recreation Club Park down the road,” Chris says. “They’re always being proactive in encouraging a sense of family. There’s a jambalaya
cookoff, and they’re also bringing back ‘module dinners,’ when each module crew goes offsite for a meal together.”
There are other benefits the cousins note. Shell proactively supports training and provides opportunities for advancement. Chris, in fact, recently finished training to be an industrial emergency response specialist, and Shell paid for the experience and gave him time off to go to the Texas A&M training facility. “There are opportunities everywhere,” he says. “You just have to show interest and ask for it.”
Both are excited about their future at Shell. “For me, Shell’s commitment to the Convent plant is exciting,” Chris adds. “That tells me that we’re not going anywhere, and that I can provide for my family in the long term.”
TERRANCE COLEMANTERRANCE COLEMAN SR. IS PROUD of his 16 years at Shell Geismar. He has risen in the ranks from process technician to production team leader in the logistics unit. But there’s no mistaking he is prouder of the fact that his 24-year-old son is following in his footsteps.
Terrance Coleman Jr. joined the company as a process technician in 2021 after earning a four-year industrial technology degree from Southeastern Louisiana University.
It’s easy to see why Terrance Jr. decided that working for Shell was the best route for achieving his goals. He’d listened to his father talk about the company for years, and even toured the plant as a child. “I think he recognized the kind of life that was made possible by me working for Shell and how it enabled me to put him through school,” Terrance Sr. says. “He also saw how Shell was the type of company that cared for its employees.”
Terrance Sr. took a more roundabout path to Shell. A Mt. Herman native, he enrolled at Southern University after graduating high school in 1990 to pursue a degree in electrical engineering. After two years, however, he chose to enter the workforce and landed a job delivering laboratory chemicals to surrounding industrial plants.
“I was going in and out of the plants every day and I got close to a lot of the people there,” he says. “They suggested I get involved in industry to make a better living.”
Heeding their advice, he enrolled in Baton Rouge Community College and ultimately earned an associate degree in process technology.
After a brief stint working for Entergy, he joined Shell in 2006 as a process technician. In his current role, he is responsible for creating and executing daily shift plans, as well as managing personnel in the logistics unit.
While he doesn’t work directly with his son—Terrance Jr. works in the electrical department—they’re scheduled to work on the same days. “We have the same off days,” Terrance Sr. says. “Shell is good about that—if you have family members
working at the plant, they try to create a good work/life balance.”
Shell also actively encourages advancement within the company. “You can even go back to school. They promote going to school and furthering your education in order to be promoted within the plant.”
In fact, that’s the path that his son just recently decided to take. This past summer, Terrance Jr. enrolled in online classes at the University of Alabama in pursuit of a degree in engineering. He expects to graduate
in two years. “From there, anything is possible,” his father says. “He definitely wants to advance in the company.”
As for Terrance Sr., he loves his job and the people he works with too much to ever look for work elsewhere. “It’s just a great culture here,” he says. “It’s like a hometown, and everyone thinks highly of the company. “It’s not a dog-eat-dog environment,” he adds. “Everybody lends a helping hand. It’s everybody working together to put out a great product. We’re all working toward a common goal.”
It feels almost as if Shell is reinventing the energy and chemical industries. It’s at the starting gate of another industrial revolution. One that’s focused on providing energy to power the world through sustainable and circular products for decades and generations to come.
When Shell announced in 2019 that it would begin a major restructuring of its refining and chemicals activities, it got the world’s attention. Not long after, it unveiled a newly integrated chemicals and products business, a single organization molded out of Shell’s previously separate chemicals and manufacturing divisions.
It was a truly transformative move. Headed by Shell Executive Vice President Robin Mooldijk, the revamped chemicals and products business, which began operating August 2021, is playing a pivotal role in helping Shell and its customers realize a decarbonized future. It all supports Shell’s “Powering Progress” strategy, which aims to make the company a net-zero emissions energy business by 2050.
Mooldijk is overseeing the dramatic overhaul of Shell’s refining strategy through the consolidation of the company’s refining footprint into five energy and chemicals parks by 2030. In that regard, Shell will also operate six chemicals-only production sites by the end of the decade, all at existing locations. The new chemicals and products business effectively brings
together all of Shell’s activities into one accountable entity.
It’s an exciting time to be in the business. Within these energy and chemicals parks, Shell is creating platforms for bioproducts, circularity and carbon capture and storage. They’re merging them and bringing them together with refineries and creating a system that is genuinely and uniquely positioned.
By taking this proactive step forward, Shell has created an indisputable competitive advantage that builds upon the success of its base and intermediate chemicals business, with an enhanced focus on performance chemicals. Since Shell aims to reduce the production of traditional fuels, more of its crude consumption will end up in chemical feedstocks. That reduces its commodity business, as they become less dependent on selling gasoline, diesel, ethylene and propylene, and extend the value chains.
Shell’s dedicated chemicals sites will, in turn, act as drivers for enhancing the supply of circular and sustainable feedstocks from the company’s integrated parks. It is also becoming increasingly clear
that large chemical facilities such as these will become the anchor sites for Carbon, Capture and Storage (CCS) projects and/or green power options. Shell feels confident that chemicals will always be part of the solution, no matter the pace of the world’s energy transformation or its approach to sustainability. Whether it’s solar panels, windmills or polycarbonate in the lenses of iPhones, Shell has positioned itself for continued growth.
Louisiana will play a decidedly pivotal and central role in this new future. Shell’s Norco facility has been designated as one of the five energy and chemicals parks and Geismar one of six dedicated chemicals sites.
What’s more, the previously shuttered Convent site is being reborn as an alternative fuels facility. Kirk Kallenberger, general manager at Convent, has a front row seat to the transformative side of Powering Progress, and is excited that all four manufacturing sites on the Gulf Coast will be involved in Shell’s energy transition.
Louisiana and the communities of
St. James and Ascension parishes will undoubtedly play a significant role in Shell’s future. “After the closure of the Convent plant, the economic impact in St. James Parish was immeasurable,” Kallenberger says. “We were their largest employer and their largest taxpayer. The parish had to make some significant and difficult decisions about what they were going to do going forward.”
So when word came down that the site would be “reborn,” it felt like the dawn of a new day. “The closure of the site was very difficult for me, personally, and it impacted me probably more than they realize,” he says. “To be creating a future for this site, which has been here for 55 years, is special. The people here are beginning to realize that the rebirth of Convent is something that will have an impact for generations to come.
“Shell’s energy transformation plans will set us up for the future over the next 100 years or so. The people of Louisiana should get excited about this future because it’s coming and it’s coming much quicker than they might think.”
While the stated goals of Powering Progress are “achieving net zero ambitions, powering lives, respecting nature and generating shareholder value,” for Kallenberger it boils down to a more holistic approach to caring and providing for the people of Louisiana and the communities in which the plants reside.
“I’ve been in this industry for a long time, and I’ve never been at a point in my career where I’ve actually transformed how I do business,” he adds. “To be a part of that is inspirational and exciting for me.”
Dai Nguyen, general manager at Shell Geismar, says Powering Progress represents more than the transformation of Shell’s business model. “It’s about
respecting nature and the community in which we serve,” Nguyen says. “Most importantly, it’s about building a legacy. It’s not simply about the commercial side of things. What are we leaving behind? And what are we doing for our communities?”
In the process, Shell seeks to take better care of its workforce and engage the local community by providing more opportunities. There’s also an increased emphasis on growing local businesses so that they can more easily participate in Shell’s bold new future. “We’re wanting to grow those businesses so that they’re ready to participate,” he adds. “One of our biggest goals here is to diversify and expand our reach so that there are more opportunities and more available companies and businesses that can take part in our activities.”
The company is working with
organizations such as the Baton Rouge Area Chamber to coordinate workshops that will help businesses find work at Shell. “Next year, we’re going to target minority businesses and help them grow their leadership and businesses so that they can participate and win some of our contracts.
“We have an opportunity to take this fantastic business to even greater heights, and some of the initiatives we’re taking are truly game changing.”
Nguyen says the people component is integral to Shell’s future success. “It only works if we care for our people,” he adds. “As long as our folks see that, I think they’ll be able to join in and work toward the creation of a stronger business. We’ll all be able to work together to make this a greater place to work and a greater place for the overall community. That’s exciting stuff. I think everyone can get behind that.”
“It only works if we care for our people. We’ll be able to all work together to make this a greater place to work and a greater place for the overall community. That’s exciting stuff. I think everyone can get behind that.”—DAI NGUYEN, General Manager, Shell Geismar
EMMA
LEWIS’ CAREER TOOKHER on a worldwide journey before she became Shell’s Gulf Coast senior vice president for chemicals and products, but it was tragedy that shaped her as a leader.
A British-born, first-generation university graduate, she developed an ardent interest in chemical engineering at an early age. She got her start working at an independent oil company for some 15 years, gaining global experience in such settings as Brussels, Shanghai, Singapore and Mumbai. She joined Shell in 2012, helping to guide its entry into the polyethylene business and rising into her current role.
It was an unfortunate tragedy, however, that most profoundly influenced Emma’s views on leadership. While on the job as a production unit manager early in her career, she was informed that a tragic accident had taken the life of her fiancé.
She was sitting in her office in the control room at the time, surrounded by operators and the maintenance team as her life came crashing down around her. In the following months, her co-workers voluntarily helped in her recovery by performing some of her duties and otherwise “covering” for her as she struggled to deal with her new reality.
That, more than anything else, gave Emma a deeper appreciation for the men and women who were on the frontline that provided support. She not only understood the importance of their day-to-day roles, but in this difficult time she was able to see first-hand their level of care and compassion.
“I have a special place in my heart for our hourly staff, the maintenance craft, operators and contractors who I’ve worked alongside through my entire career,” she says. In the coming months, Emma will be a guiding force as Shell initiates many of its “Powering Progress” initiatives. We sat down with her to discuss how she views the future of Shell in Louisiana and the Gulf Coast.
What does the slogan “Powering Progress” mean to you?
It means several different things, both internally and externally. Internally, it means producing the products that the company and our customers want. Those are low-carbon fuels, sustainable aviation fuels, low-carbon and circular chemicals. It also means being the anchor customer for things such as carbon capture and hydrogen.
Externally, it means working in a different way with the communities around our sites and respecting the ecosystem around our sites. We’re going to work to make sure that we improve them and make them better. It means improving the lives of our employees and improving the lives of communities. It really means how do we move all those things forward, and move them forward together?
Do you feel that Shell is positioned to respond to future changes in the industry, no matter what they might be?
This isn’t a revolution where we’re going to wake up Monday morning and everything will be different. We will continue to make fossil fuel products as we transition. What’s exciting, though, is that having these sustainable and low-carbon products will help us get more out of the products that we already make today.
There are also some cultural and behavioral changes. For one thing, we’re shifting from being cost driven to being value driven. That means less obsession around the number of dollars that we spend and more thoughtfulness about the return we get on those dollars. That’s a big shift for this organization.
It’s about never being satisfied with the status quo and always striving to do more and do better, as well as coming up with new ideas and being brave. That’s a big cultural shift for us and that isn’t going to happen overnight.
Of course, a lot of those changes aren’t
going to happen without our frontline staff. They are an important part of the heart of our organization. I think we’ve become a little disconnected with them during COVID, so we need to reengage with them and get them involved in this journey.
What differentiates Shell from others in industry in terms of its view of the future?
I believe we have both the skill and the will to want to lead in the energy transition. I think several of our competitors have the skill, but the focus is not on being the first mover in that space. And then there are those who have the will but not the technology to support that. I think we have the technologies, the integration across our businesses and our sites. We also have the desire to make a difference and lead in this space, and I think there’s so much opportunity that comes from that.
How does Louisiana fit into that narrative?
Louisiana is a critical part of our operations—not just in the U.S. but globally. I think we have a very proud history here in the way that we’ve worked with our communities and the state of Louisiana.
Internally, we call our current transition “Cathedral.” It represents a suite of projects that will transform all of our assets and our businesses across the Gulf Coast. At sites such as Norco, we’re already working on putting sustainable feedstocks into our steam cracker and cat cracker and making products that are sustainable for our Geismar plant customers.
And for our Convent facility, it means anchoring carbon capture, anchoring hydrogen low-carbon fuels, and potentially circular chemicals. It’s really a transformation of everything we have in Louisiana. It’s incredibly exciting.
Louisiana is a critical part of our operations—not just in the U.S. but globally. I think we have a very proud history here in the way that we’ve worked with our
SENIOR vice president for chemicals & products, U.S. Gulfcommunities and the state of Louisiana.
So much of the investment, particularly for chemicals and products, will go into this state. I think its importance will only grow, and I’m excited about the future for these assets and for the employees.
What role will the Convent facility and its impending transformation play?
Convent is an important part of our
powering progress journey on the Gulf Coast. In that regard, it’s going to integrate with several other Shell businesses, whether that’s through low-carbon fuels, carbon capture or hydrogen. That’s the place where a lot of that will come together for us in Louisiana.
Whether it’s our retail business, our mobility business, our chemicals and products business, Convent is the place
where it all comes together. I’m so excited to see this site come back to life. It’s just a phenomenal opportunity. It’s also a huge responsibility for all of us to make sure that we deliver on this, because it’s going to take some hard work to get it there.
How important are diversity and inclusion to Shell’s future?
Diversity and inclusion are really important to me, personally, and will always be something I’m passionate about. Not only because it’s the right thing to do, but because it’s just better for business. When you have a diverse group of people on a team, it unleashes the cumulative power of their creativity and ideas. That requires a diversity of backgrounds, diversity of experiences, diversity of gender, race and all of those things.
We wouldn’t be where we are today if not for our workforce. I talk a lot with my leadership team about how we can do better. All of our employees need to feel included and valued. That’s the inclusion part. I would encourage our employees to engage in that space and challenge leadership, because if we want to win in the energy transformation, that is an important part of winning.
Where do you see Shell in 20 or 30 years?
Shell has a bright future, but a slightly different future. Chemicals are such an integral part of modern life and they will continue to be important, so whether you think of EV cars, solar panels or wind turbines, all of those require the chemicals that we make here on the Gulf Coast.
Our customers are asking for lower carbon products and more circular products, and that means we’ll see more diversity in the feed stocks that we bring into our assets. The future is still bright; it’s just a bit different.
—Emma Lewis“Louisiana is a critical part of our operations—not just in the U.S. but globally. I think we have a very proud history here in the way that we’ve worked with our communities and the state of Louisiana.”
SHELL EMBRACES LOUISIANA’S UNIQUENESS and seeks to make a real difference in the communities and environments in which it resides.
They call it their “Creative Energy: The Rhythm of Louisiana” initiative, but it’s not just lip service. Shell and its employees are actively engaged in supporting the local arts community, preserving its culture and in helping the disadvantaged. In the process, they’re giving their money, time and knowledge to create a better world.
It boils down to a culture of respect—respect for the ecosystem, for the community and for the lives of those around them. Shell recognizes that no accomplishment matters if they fail to care for their people.
AT CAMP CATAHOULA, campers depart with all of the usual lifelong memories that summer camps provide.
But this one-week retreat has an extraspecial purpose: Providing moments of normalcy to pediatric burn survivors and an opportunity to move past their fears.
Run by the Baton Rouge General Foundation, it is staffed by volunteers from Baton Rouge General and other community organizations. Shell is the camp’s presenting sponsor.
Each year, campers at Camp Catahoula
enjoy an action-packed experience, from inflatable obstacle courses and Relay Olympics to fishing and a fair complete with games and a DJ. They also have a chance to ride and groom ponies and make arts and crafts. “Therapy is a big component of this,” says Erik Showalter, president of the Baton Rouge General Foundation. “They can join in small groups for sharing their stories, and we spend time with these kids in the kitchen. Getting them to do that can take days to a week, but they accomplish that.”
Camp Catahoula is one week out of the
year, but its founder, Dr. Tracee Short, wants to expand its scope to include burn survivors from other hospitals.
Shell, which began helping the hospital during its campaign to build a regional burn center, also maintains an Amazon “wish list,” whereby its employees can donate items such as goggles, water shoes and towels. Its team also contributes time, sponsoring petting zoos and other types of activities. With the help of corporate leaders, “almost anything is possible,” Showalter says. “We have the ability to do more.”
Shell is an engaged community partner, providing money, time and knowledge to make Louisiana a better place.
TODD STERLING, BOARD PRESIDENT OF the River Road African American Museum, says the Donaldsonville facility has a long history of tackling challenges.
Founder Kathe Hambrick opened the museum at Tezcuco Plantation in 1994 to educate the community and interpret the lives of African Americans in rural South Louisiana, only to have it destroyed by fire in 2002.
The museum then moved to Donaldsonville in 2003, where it continues to advance its mission today.
Sterling says there’s little doubt that corporate sponsors and volunteers have been vital to the museum’s success. He came on board about four years ago when Hambrick left to work for the West Baton Rouge Museum. It was a natural fit for him—he studied history in college, with an emphasis on African American history.
Hambrick has long recognized the importance of industrial philanthropy. In 2018, she worked with Shell to protect and commemorate two
slave cemeteries on its land near Convent in St. James Parish between Baton Rouge and New Orleans.
The work was the culmination of years of efforts to honor those buried at the Monroe and Bruslie sugar plantations. “We helped them (the sugar cane owners) to see the humanity and decency of taking those areas out of production,” Sterling says.
Shell marked, blocked off and spruced up the tracts of land and held dedication ceremonies in March 2018, about five years after archaeologists confirmed the presence of the burial grounds. The company also worked with Sterling’s museum to arrange commemorative events and accommodate visitors.
There have been other contributions. Sterling says Shell’s minority employee group, the Shell Black Network Group (SBNG), has also assisted the museum through various service projects.
“And in 2020, Shell donated $300,000 to help us renovate our Rosenwald School at the
RENEE CHATELAIN, PRESIDENT & CEO of the Arts Council of Greater Baton Rouge, says it’s sometimes difficult for the industrial sector to see the value in anything other than the STEM disciplines.
Fortunately, she adds, there are some who recognize that a commitment to the arts builds a foundation for community vibrancy and growth.
In the late 1990s, a feasibility study revealed a lack of afford able and accessible space for artists in the Baton Rouge area. Changing that dynamic has be come Chatelain’s mission, with corporate financial support an integral component for meeting that goal. For years, the indus trial community has provided
financial contributions, served on the Arts Council board and assisted with capital campaigns.
“Shell has a unique under standing of the vitalness of the
museum site,” he adds.
In the early 20th Century, the Rosenwald School project built more than 5,000 schools, shops, and teacher homes in the U.S., primarily for the education of African American children in the South.
Today, the River Road African American Museum holds more history than one can
imagine. Settled in the middle of what many call Louisiana’s “plantation country,” it serves a central purpose: to educate visitors about the history and culture of African Americans in the rural communities of South Louisiana through the collection, preservation, and interpretation of art, artifacts and historic buildings.
arts in any community, and in the success of that community,” Chatelain says. “The support of that leads to a quality of life and talent recruitment that serves everyone.”
Case in point: The Arts Council recently renovat ed and repur posed a blighted building to create an art center and workspace for the region—the 12,000-plussquare-foot Cary Saurage Community Arts Center —with the help of corporate and community
donations. The building serves as creative space for artists and arts organizations to meet, work, and create.
“Shell was supportive from the get-go because they knew what it could mean for this communi ty,” she adds. “We want to create a vibrant community where people want to stay, and cor porate support is making that happen. They saw that this as an investment that would yield a great return.”
The company even com missioned a Louisiana artist to create a sustainable piece of art for permanent exhibition at the center. “It goes far beyond money … when you’re helping in a way that will foster a vibrant arts scene in the future.”
Shell isn’t merely accepting the reality of an evolving industrial landscape. It is proactively fueling the transformation through research and unique academic partnerships.
The recent creation of the LSU Institute for Energy Innovation made that perfectly clear. Financed primarily through a $25 million donation, the institute was created to assemble energy leaders and academics in the pursuit of a shared vision for the future of energy.
Its five-year vision is rooted in five work streams: talent, research and development, policy and economics, social and environmental justice, and technology transfer and commercialization. In particular, LSU and Shell plan to serve as a national model for energy-related collaboration involving both science and engineering, seizing the urgent
opportunity for scholarship and solution delivery within the areas of hydrogen and carbon capture, utilization and storage, the coast and low-carbon fuels.
Shell donated another $2.5 million to support construction of the LSU Our Lady of the Lake Interdisciplinary Science Building, a 148,000-square-foot, four-story epicenter for academics, research and industry collaboration. Once constructed, the facility will meet the need for educational and lab space in biological sciences, chemistry, geology and geophysics, mathematics and physics and astronomy.
Some $6.4 million of the gift will be directed toward diversity, equity and inclusion initiatives centered on faculty and student support and workforce development within the energy industry. “We are uniquely positioned to be at the forefront of energy transformation in
America,” says LSU President William F. Tate IV. “Our success will depend upon, in part, the level to which leaders in energyrelated thought, talent, and industrial impact seize this opportunity with us.”
Sam Bentley, LSU’s former vice president of research & economic development, says the partnership epitomizes the importance of industry and academia working together. “The state of Louisiana’s recent $5 million commitment to improve energy-related research at LSU further extends the impact the institute can have, importantly by enabling LSU to become a national leader in CCUS and hydrogen technologies,” Bentley says.
For Lee Stockwell, Shell’s LSU “campus executive,” the Shell-LSU bond is personal. Stockwell grew up in Baton Rouge and graduated from LSU in 2001 with a degree in petroleum engineering.
Shell’s innovative academic partnerships are a model for energy-related collaboration, targeting talent, research, social and environmental justice and more.
“Rhoman Hardy, my predecessor, recognized the role that Louisiana and LSU would play as we begin to advance our energy transition plans,” says Stockwell, who also manages the company’s CCUS effort from his Houston office. “We asked ourselves, how do we support the energy transition and leverage the diversity of the university? That’s when this opportunity began to materialize.”
It just made sense to partner with the state’s flagship school as Shell began to invest in transitioning its products and installing decarbonization capabilities along the Gulf Coast. It made good financial sense, too. For every $5 Shell spends, globally, about $1 of that goes to Louisiana. And for every $3 earned by the company, about $1 is earned from products made along the Gulf Coast. “We wanted to take steps to ensure that we maximized that value,” he adds.
It also meshes nicely with Shell’s other initiatives around diversity and coastal restoration, as well as the impending conversion of its Convent facility into a renewable energy production facility.
“It all carries the common theme of energy transition,” Stockwell adds. “We’re talking about building the future of Shell. We’re transitioning fuels to low-carbon fuels, creating low-carbon chemicals and plastics, creating CCUS and more. All of these things epitomize the business we want to be in the future.”
Shell’s commitment to education and the institutions of Louisiana specifically has come into sharp focus over the last couple of years. Not only has the industrial owner increased its investments—in 2021, it contributed some $2.25 million in Louisiana and $19.5 million nationwide—it has provided comparable donations of time and expertise.
It’s all necessary to meet the expected future demand for local workers. To stay ahead of the need, they’re strengthening their bond with area community colleges and technical schools.
Lillie Murphy, president of the River Parishes Community College Foundation, says the inseparable partnership between Shell and RPCC goes beyond money. In fact, when Shell closed its Convent refinery, one of its first calls was to the Gonzales campus. They knew that their people would need retraining. “It’s not just about the foundation, it’s about the entire partnership,” Murphy says. “It’s an integration of the two of us. We need each other.”
Perhaps nothing epitomizes that better than Shell’s investment in the recently
commissioned Process Equipment Trainer Plant at RPCC’s Gonzales campus. Some $100,000 of the $300,000 in funds donated by Shell to the college since 2000 went toward the design, construction and operation of the PET facility.
Ultimately, it will give RPCC the ability to train students as wind and/ or solar technicians, in addition to other opportunities in renewables. New equipment for solar technician training will support new solar farms in the area, and the offshore wind farm initiative in the Gulf of Mexico. Electrolysis training will also be included in the portfolio, in support of efforts by CF Industries and others to produce green ammonia.
Quintin Taylor, interim chancellor at RPCC, says the project has been years in the making. “By working with industry, we’re ensuring that we move at the pace of business and that we’re aligned in lockstep with them as they re-imagine what they’re operations will be.”
But Murphy says Shell’s investments in money and time go much farther. Donations have been used for numerous other types of training and scholarships, and they also sponsor Career Link, giving high school students “hands on” exposure to careers in the industrial field through one-on-on discussions with industry partners. They also provide support for tutoring.
“Every year, Shell Workforce provides funding for free tutoring for our students majoring in Process Technology or Instrumentation,” Murphy says.
Shell also provided support for RPCC’s chemistry laboratory at its Gonzales campus and have been supportive of the “Energize Your Destiny” campaign aimed at promoting careers in industry to women.
Taylor says the Shell is an indispensable part of RPCC’s economic and educational framework. “It’s important that partners such as Shell are at the table with us to
say this is what we need at Shell in our employees,” he says. “Therefore, we’re going to invest money, time and human capital to set up those programs.”
Looking ahead, Shell remains firmly committed to educating the local community and seeking to build a more diverse workforce. And they’re simultaneously raising the bar: Students entering their summer internship program must have a 3.25 GPA.
The program is growing, nevertheless. There were some seven interns working at Shell Geismar earlier this year, and a record 20 at the company’s Norco plant.
Of course, Shell’s investment in education doesn’t end after a worker is hired. On-board training plays an equally important role in preparing workers to perform their duties within the plant. In his role as learning manager at Geismar and Convent, Steven Mooney oversees eight learning advisors who train and onboard all the plant’s technicians.
“We take new hires through the whole process to get them trained, otherwise they can’t work the unit,” Mooney says. “It’s pretty intense. It could take as long as nine months to demonstrate that you have full competency, depending upon your role.” Shell also provides training in leadership development and other subjects.
To facilitate the process, Shell is making big investments in technology, including new simulators and augmented and virtual reality training. Most of the training takes place in Shell’s full-time learning center just outside of the Geismar plant gates.
Above all else, they want new hires to understand their unit inside and out. If anyone scores low, they’re given more shifts and training until they reach 100%.
Says Mooney: “That’s why we invest as much as we do in training. We want to get it right.”
Cooperation
USA TOOK A CATALYTIC STEP FORWARD TO POWER PROGRESS in the production of more and cleaner energy with an unprecedented $27.5M dollar gift to LSU. The gift is the university’s largest in history from a for-profit corporate partner and largest philanthropic investment in energy-related initiatives.
AS THE FOUNDING PARTNER of the new LSU Institute for Energy Innovation, Shell demonstrates its commitment to Louisiana’s future. Together, Shell and LSU will serve as a national model for energy-related collaboration at the intersection of science and engineering within the energy transformation.
among industries and academia represents the pathway to answer the challenges of the future.”