
9 minute read
Excavation contractors can reduce risk with in-house ground penetrating radar operation
By Ray Cummins
Excavation crews in the field face a variety of complex challenges before they dig. These are magnified when considering other major factors like project timelines, budget constraints, and the quality of existing utility maps and other subsurface data for specific jobsites. They also have to work in a diverse range of landscapes and soil conditions.
Preventing damage to underground utilities and locating other underground obstacles should remain a consistent goal for excavation contractors. The best way to accomplish this is by collecting data on the subsurface field conditions of each jobsite before breaking ground.
To best mitigate damage risks and collect necessary data simultaneously, many excavation contractors are deploying advanced ground penetrating radar (GPR) systems. When implementing the technology in-house, GPR creates an instant, data-driven deliverable that can be put to immediate use in the field.
Here are just some of the ways that excavation contractors can benefit from deploying GPR on their next project.
The second opinion after the one-call
A one-call must be placed at least five business days prior to digging; information on regulations and the one-call service for each province can be found at digsafecanada.ca. (Excavation contractors in the U.S. should visit call811.com/Before-You-Dig for information on state regulations and 811 call services.) The one-call is a necessary and valuable initial survey of the dig site. However, once the locators have finished their assignments, the colour-coded flags and paint marks only tell part of the story. Here are some important factors to keep in mind:
First, one-call locators are only obligated to locate public utilities within the boundaries of the dig site. They are not responsible for private facilities or non-utility objects beneath the surface.
This offers a partial view of the conditions below but does not guarantee absolute risk mitigation.
Second, the one-call service providers suit their equipment arsenal to find the specific utilities they are assigned to locate. Common tools like electromagnetic locators, for example, are designed to identify metallic and conductive objects. Instead of providing a complete view of the subsurface field conditions, these tools are intended to find key touchpoints.
Advanced GPR systems are designed to image the entire subsurface with greater depth and clarity than traditional counterparts. Using the system controller, the operator can view prevailing field conditions in real-time, confirm one-call findings, and expand upon them by also surveying for private facilities, boulders, tanks, changes in soil structure, and other targets of interest that may otherwise go unnoticed.
GPR data not only confirms and expands upon one-call findings, but it also provides the contractors with the confidence to start a project with peace of mind and the ability to modify project strategies should any obstacles arise. The crew in the field can also begin working with greater efficiency and assurance knowing measures have been taken to mitigate common damage risks prior to breaking ground.
Overcoming unforgiving soil
North America’s diverse landscape creates a variety of environmental and operational challenges for locators. Someone working in the plains will have a different set of parameters from someone locating at a seaside beach resort. For contractors that operate across multiple locations and situations, soil conditions can change on a day-to-day basis depending on the jobsite.
The composition of the soil and surface terrain conditions can impede some locating equipment from creating usable data. Rough terrain and lossy soil will negatively affect signal penetration, especially for higher-frequency signals.
Conversely, dry, sandy soil will allow signals to travel at greater depths with far less resistance and signal loss. Someone using an EM locator over wet clay will find the signal dissipating quickly, if it even registers at all.
When selecting a GPR system for in-house field use, it’s important to consider a system that has both the hardware and antenna capabilities to traverse multiple terrains without breaking down or losing signal. Look for a unit with a tough construction and airless tires, so that the system can endure long stretches of use.
If you are operating in lossy soil, consider using a triple-frequency system as well. These systems will collect data across low-, middle- and high-centre frequency ranges simultaneously. This not only compensates for unforgiving soil, but it allows the operator to cross-compare multiple datasets for an even clearer understanding of prevailing subsurface conditions.
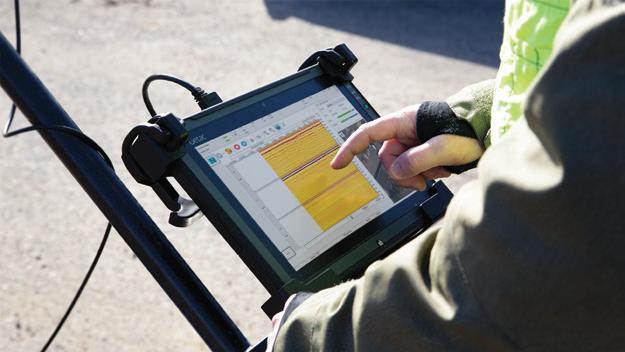
Creating a deliverable for the future
GPR’s greatest advantage to crews in the field is its ability to generate instant deliverables that can be immediately implemented. A high-end GPR system should also enable the user to store, share, and post-process the data directly from the controller console.
These deliverables create a common point of reference for future installation and maintenance projects at the same site. Though GPR already proves a time-effective damage prevention solution, that time is reduced even further with existing data in hand. This enables the crew in the field to begin followup assignments with much shorter preparation requirements.
When considering a GPR system, be sure to look for post-processing features like 3D imaging, GPS integration, and mapping software that can enable the user to create dynamic visual models of the raw data. This will translate key information into easily understandable models that decision-makers can use for future reference or to strategize in the present.
REMOTE CONTROL, ZONING PART OF EFFORTS TO INCREASE CRANE SAFETY
by Lee Toop, Editor
As technology advances steadily in the construction industry, it is bringing new opportunities for improving safety to a range of equipment found on jobsites. That includes cranes, which are steadily moving ahead with improvements that make work safer and easier for operators and the crew working around them.
Remote control, zoning systems and camera systems to improve visibility are several approaches being used to add safety for operators of tower cranes especially, explained Ryan Burton, managing director with Abbotsford, B.C.-based Bigfoot Crane Company and chair of BC Crane Safety. Each of these systems helps improve the safety of these large cranes, a challenge at the best of times.
Ground-level operation with remotes
Bigfoot rents a variety of tower cranes into the busy Lower Mainland construction market, and on most jobs the company renting the machine provides their own operator. In many cases, those operators are working the crane from the ground with remote controls.
“Remote controls have been around for quite a while – you don’t have to be in the operator’s cab, but instead can be right on the ground or on the floor you’re setting the loads on,” Burton described. “You don't need a signal person, and you can land the loads just right.”
Radio remote controls have become more advanced over time, Burton noted, and today’s remotes have a full display available for tracking key crane data. “You can see exactly the capacity of the crane at the exact radius. They have temperature readouts to see if it’s too cold to run the crane. They have wind readouts on them so you always know what your wind readings are – basically, it's everything you need to run
3D Paving Technology with Easi-Pour Compact 880
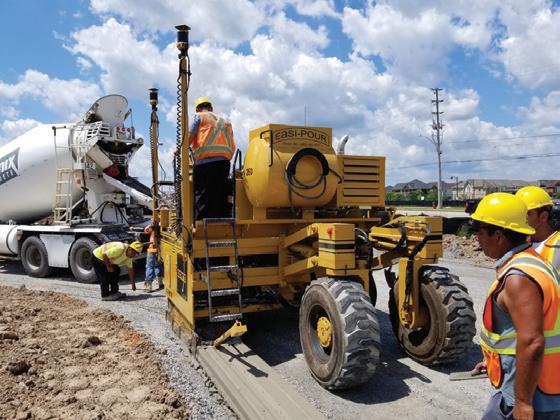
Invest in the most proven concept in slip-form paving equipment from Easi-Pour. 3D paving technology makes you more efficient and profitable. Ergonomically designed with unparalleled dependability for your concrete paving applications. Ease of operation coupled with the best operator visibility in the industry makes your jobsite safer and more productive.
Curb & Gutter | Sidewalk | Barrier | Drainage Ditch | Special Applications
www.easipour.com | 605-352-1412 | OVB Holdings, LLC

With more cranes on today’s jobsites, technology advances are playing a part in protecting workers and equipment.
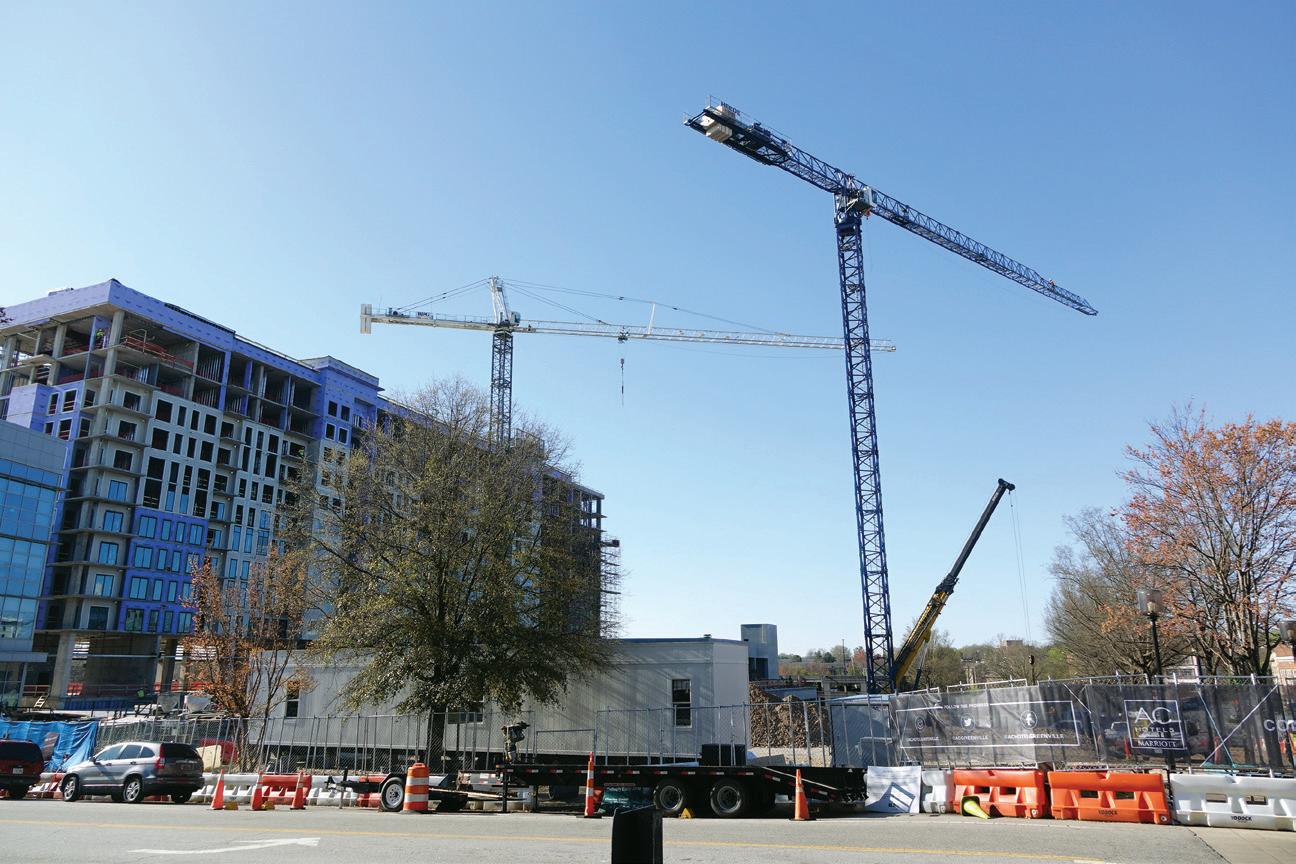
the crane right at your fingertips anywhere on the jobsite.”
Ground operation of a tower crane improves safety in a number of ways, Burton described. “When you’re in a tower crane cab, you rely on the rigger who’s on a radio – you’re trying to decipher what that rigger is saying all the time, but there's lots of noise, pounding, banging and jackhammering all coming through the speaker,” he said. “It’s really difficult to hear what they’re saying. When the operator’s on the ground, he can see exactly what he’s picking up and what he’s dropping down.”
Electronics protect multiple cranes
Another growing area of technology involves tracking the way in which cranes can operate on increasingly busy jobsites. Electronic zoning systems are used to essentially geofence cranes and keep them from moving into areas that could be dangerous.
“These systems are installed on the tower cranes, and these limit the crane from going into dangerous areas. So, if you have power lines on the jobsite, you can work the crane anywhere, but if you go into the area where the power lines are it will limit the swing, the trolley and the hoist so you can not come into contact with those wires,” Burton said. “Those have come on really strong in the last two years.”
Bigfoot has seen a dramatic reduction in the number of high-voltage power line contacts using these systems, which also tie into anti-collision systems that protect against conflict between multiple cranes, Burton described.
“This allows the cranes to actually talk to one another – each crane knows where the other one is at any given time, and it knows if there’s a possible collision. It will slow the crane down or stop the operator from going into a dangerous area,” he said.
Burton said that of the roughly 100 jobs Bigfoot’s cranes do in a year, it used to experience four or five collisions between machines. That doesn’t sound like much, but when it involves two crane jibs or load lines being caught up with one another it can be very hazardous.
“You have stuff falling from the sky at that point. You don’t want that,” Burton said.
Connectivity and cameras add to safety
Growing connectivity on jobsites has led to another innovation that Bigfoot has adopted, allowing everyone on a jobsite to check wind speeds for safe operations. Anemometers are attached to the cranes magnetically wherever they’re needed, and connect by Bluetooth to mobile devices.
“Everyone, the safety officer, the site superintendent and everyone else know if people are working in dangerous situations as far as wind speeds. A lot of times there’s a lot of equipment working on a site, and it’s all got to be managed in certain wind speeds,” Burton described.
Cameras are being installed more frequently on tower cranes to allow for greater visibility when operators are in the cab.
“There are cameras that go on the crane hook blocks – these really help the operators in the cab,” Burton said. “People that are working in the blind have been helped a lot by those.
These and other advances in technology around crane operation are an ideal way to improve working conditions on busy jobsites, Burton affirmed. “It helps us out a lot. The safer that we can make operators and people on these sites with technology, the better, and the better the condition our equipment comes home in.” HEG