
7 minute read
Grade control integration adds precision tools for excavators
GRADE CONTROL INTEGRATION ADDS TOOLS FOR EXCAVATOR OPERATORS Hitachi’s Solution Linkage Integrated Grade Control system uses Topcon technology
By Lee Toop, Editor T he growth of grade control options has brought more efficiency and ease to excavation in recent years. Its evolution has steadily increased the amount of automation that operators can benefit from, and the trend has continued to improve the precision of excavators with each new addition.
That precision is at the heart of a new offering from Hitachi that will integrate grade control into its Dash-6 excavators, allowing operators to set the grade they need and keep their machine there. Solution Linkage Integrated Grade Control, with Topcon technology, is aimed at improving efficiency and lowering daily operating costs for owners.
Response to needs of changing workforce
Introduced at CONEXPO 2020 on a ZX350LC-6 excavator, the new system is a response to the needs of a changing workforce while leveraging constantly developing technology. Jonny Spendlove, Hitachi product marketing manager, excavators, explained that the demand has expanded as new operators take over where those with experience step away from their machines into retirement.
“Operators are getting older and closer to retirement, and you have new folks coming in, younger people getting into the operation role. As the workforce changes, closing productivity gaps is really a function of technology,” explained Spendlove during a walkthrough of the system at CONEXPO.
Hitachi has offered systems with indicators as a reference system, which provides visual cues to the operator related to the position relative to grade. While that system continues to be popular and provides a more efficient grade control option, the new offering takes that to a new level.
Components integrated onto the excavator right from the factory provide precise control of the bucket and boom of the machine while the operator controls the stick. The system then manages the location of the bucket tip as the grade nears, making for a more precise last few passes to reach the desired dig depth.
The system continues to rely on the operator for control, Spendlove noted.
“We really want to focus on enhancing the way the operator digs. Our pilot control system allows the operator to enjoy the same controllability, the same functionality that they’ve always enjoyed on their Hitachi excavators,” he said. “Then, as they get down to that final pass, the grade control is really going to lock into place and it will keep the bucket tip at grade. . . that’s always been the challenging part for the operator – making sure you’re at that grade, not below.”
Hitting grade on the first try cuts down on additional time and cost for backfill, he added. “The additional
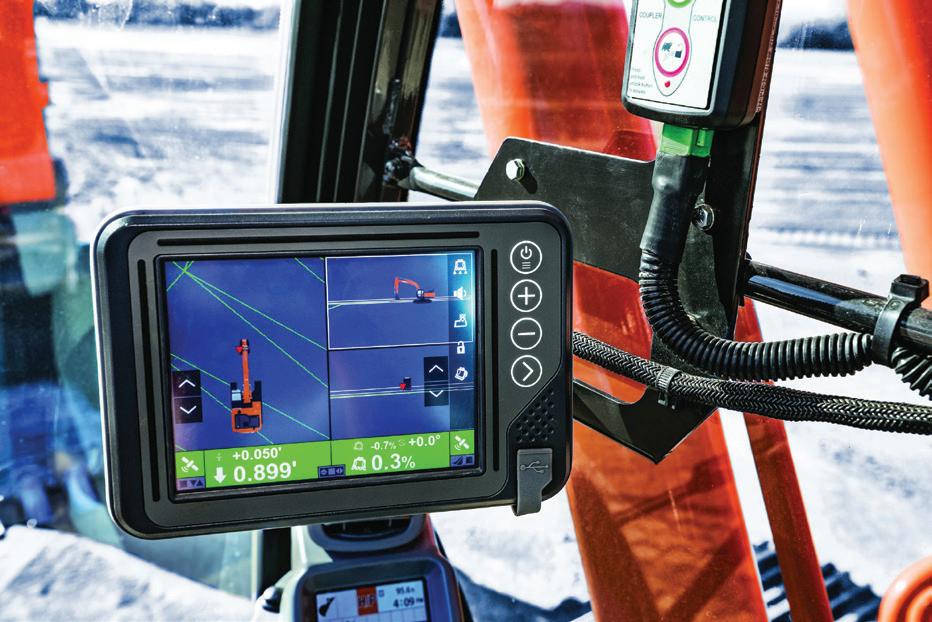
aggregate you are going to put in there is just going to add up, and that's going to take away from your profit.”
Large, easy-to-read monitor
In the cab of the ZX350LC-6 on display at CONEXPO, the Solution Linkage Integrated Grade Control includes a large, easy to read monitor that is well placed to give the operator all the information needed to hit their grade with ease. The system is scalable, as well, offering owners 2D and 3D options.
“If you have a contractor who really isn’t in the grade technology game yet he can start with a 2D guidance system and a rotating laser; you have a laser catcher on the arm and you can get the grade checker out of the hole,” he said. “Then as he gets more comfortable with grade technology you can upgrade to 3D guidance. . . we think there’s a lot of interest in the ability to upgrade, to dip a toe in and get more into grade technology more as they go along.”
Other offerings from the new system include such things as virtual fencing, in which a perimeter can be set that keeps the machine inside a specific frame – that means the machine can work under obstacles like power lines without the worry of making contact, as well as setting a floor the machine can not dig beneath. There is also a payload weighing system that allows the operator to keep track of how much material is being moved. Wireless data transfer and remote display access are also available. HEG
A FLEET MANAGER’S GUIDE TO LOWERING EXCAVATOR OWNERSHIP AND OPERATING COSTS
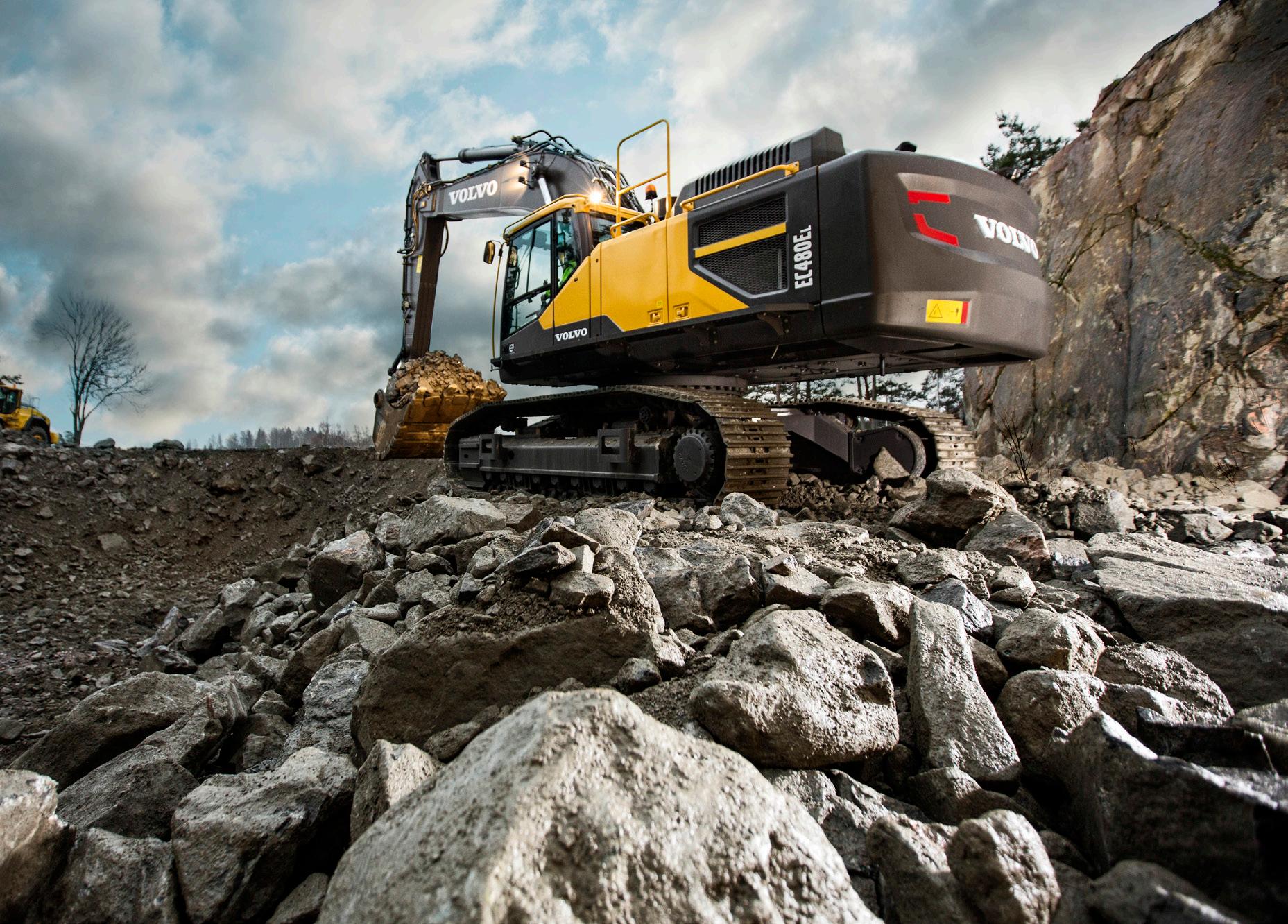
Evaluate key features, learn best practices and better utilize machine-specific data
YOUR GOAL:
Control the operating costs of the excavators in your current fleet.
We know there are daily challenges that get in the way. Unexpected downtime, excessive fuel use and unintentional operator misuse — to name a few — all contribute to higher operating costs.
Your choice of machine, and the service and technology provided by the OEM, can make a big difference in your operating costs — and ultimately, your total cost of ownership (TCO). Here are some things to consider:
START BY EVALUATING MACHINE FEATURES AND THEIR IMPACT ON TCO
When it comes to purchasing excavators, evaluate the features that provide you with the best value over the life of the machine. A few examples:
Fuel-saving features such as integrated work modes and auto idling.
For most owners, fuel consumption is the first cost of operating an excavator. Built with nine different settings within four work modes, Volvo excavators allow operators to dial in the exact amount of power and control for the task at hand, while burning as little fuel as possible. The auto idle feature automatically switches the engine to the high idle setting after five seconds of inactivity, lowering the engine’s RPM and saving fuel.
Productivity features like Dig Assist. In-cab machine control systems show operators — in real time — how to level sites, dig trenches and grade slopes, or even create complex, multidimensional site profiles. They make operators much more accurate — ensuring they get the job done right the first time, every time.
Guarantees for less worry. Choose a machine with that comes standard with a lifetime warranty on the boom, arm and frame, as well as a fuel efficiency guarantee — as Volvo crawler excavators do.
USE MACHINE MONITORING TO CORRECT PROFIT-DRAINING OPERATOR BEHAVIOR
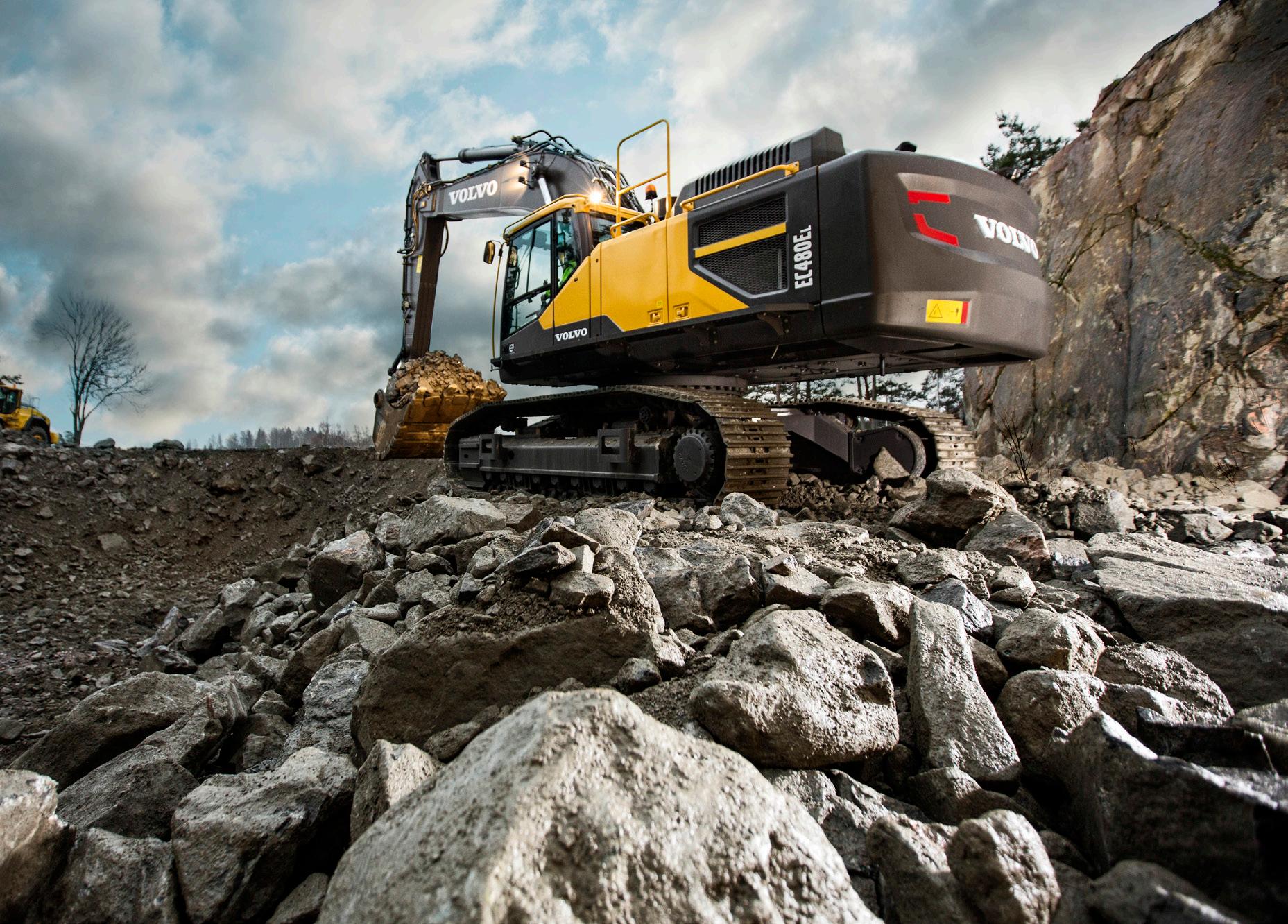
Evaluating machine features is only the start. To truly get the lowest TCO, you need to monitor how the machines are being used. Volvo ActiveCare Direct makes this incredibly easy. Monthly reports include information that empower you to train your operators in ways that can lower your TCO significantly. Examples include:
Limit excessive travel to reduce half your
maintenance costs. Excessive excavator travel time is the number one cause of undercarriage wear. It puts a lot of stress on the tracks, sprockets and idlers, and these repairs can represent more than half of your machine maintenance costs. ActiveCare Direct monthly reports show excavator travel time by machine and across the whole fleet — making it easy to spot opportunities for operator training or site reconfiguration.
Reduce idle times to boost resale value by $20,000
and reduce service costs by $9,000. It’s important to first evaluate similar machines to determine if there’s a large variance in idle percentages. For example, if you had data to help an operator get the same amount of work done while reducing his idle time from 50% to 33%, the difference in lifetime hours could add $20,000 in resale value at the end of five years — not to mention the lower-hour machine would require five less service intervals over that time, estimated at a $9,000 difference. By tracking idle times with Volvo ActiveCare Direct, you can set realistic goals for improvement.
Train operators to use the right work modes
and save $10,000 per year. Too often, operators have a tendency to jump directly into the highest mode, regardless of the task. With a Volvo excavator, balancing engine RPM with hydraulic flow is simple. Everything is integrated into a single dial to change both the pump flow and engine speed — a feature unique to Volvo excavators. With programs like ActiveCare Direct, you can track any operators who run in too high of a work mode and help them change that behavior. By simply switching to a lower work mode, you could be saving upwards of $10,000 per year, per excavator.
AVOID UNNECESSARY DOWNTIME
So many telematics programs still send a large number of confusing fault codes — but those are becoming a thing of the past. ActiveCare Direct makes them simple and useful. With easy-tounderstand case alerts, you get the fault codes that went off, their probable causes, the specific action you should take, and the possible consequences if you don’t. It’s that simple.
Learn more about how ActiveCare Direct simplifies fleet management by contacting your local dealer or visiting VolvoCE.com/ActiveCareDirect.
TAKE ADVANTAGE OF SPECIAL FINANCING NOW THROUGH AUGUST

Ownership costs are another part of the TCO equation, and we’re committed to helping lower those, too. Right now, we’re offering incredibly low rates starting at 0% for 24 months on 2018 and newer excavator purchases through August 31. These offers are packed with flexible options like: