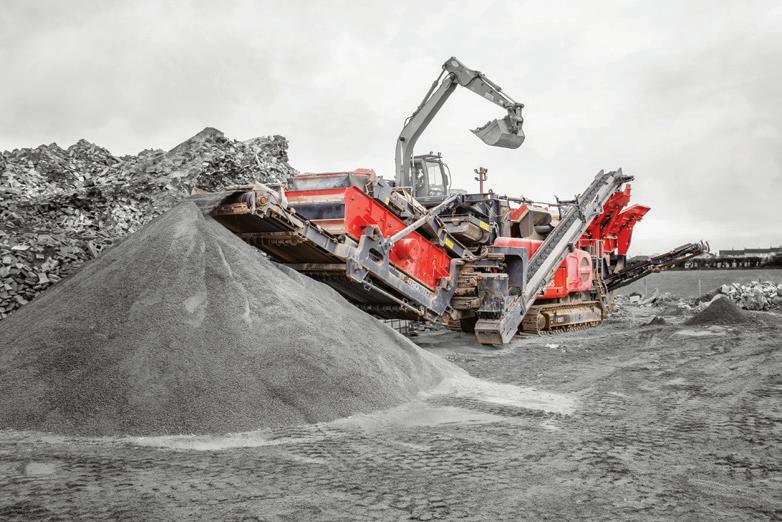
7 minute read
FOCUS ON CRUSHING PLANTS
TEREX FINLAY NEW IMPACT CRUSHER Terex Finlay displayed three machines at CONEXPO-CON/AGG 2020: the I-120RS impact crusher, the 883+ (triple shaft) heavy-duty screener and the TF-75L low-level feeder.
The new-generation I-120RS impactor (right) includes a redefined style and advanced technological design, providing improved material flow and production capabilities in demolition, recycling, quarrying and mining applications, for large-scale producers and contract crushers. Units are easy to operate and maintain, and use a Terex CR038 impact chamber with direct drive and an advanced electronic control system, providing high material reduction ratios and consistent product shape.
ANACONDA ANACONDA ENTERS TRACKED CRUSHING PLANT MARKET Anaconda has diversified its product range, from a focus on screen plants and conveyors, with the introduction of a new crushing division. Anaconda’s new tracked J12 jaw crusher and I12 impact crusher (above) were a focus for the company at CONEXPO-CON/AGG 2020. According to Anaconda’s Senior R&D Engineer, “Core to the concept of the J12 and I12 tracked crusher range is that the same running chassis is able to be integrated with either an interchangeable, hydraulically driven jaw or impact crusher chamber.”
Both machines use a generic Cummins-powered tracked chassis and come standard with a 14-foot (4.3-m) variable speed vibrating grizzly feeder, hydraulic hopper wing extensions, an overband magnet, side discharge dirt belt, and McLanahan Universal crusher chambers as standard.

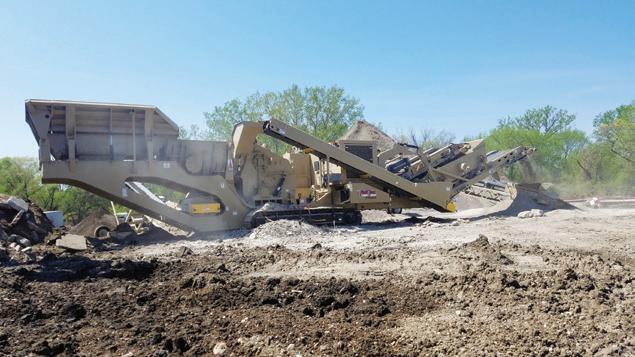
KPI HYBRID IMPACTOR PLANT WITH PRESCREEN Kolberg-Pioneer (KPI) announced the launch of its hybridpowered FT4250CC mobile impactor plant with pre-screen at CONEXPO-CON/AGG 2020. The unit’s new two-deck pre-screen minimizes the amount of undersized material that passes through the chamber, reducing wear costs and increasing the amount of final product by up to 30 percent, according to KPI.
The FT4250CC hybrid power option allows producers to operate using diesel or electric power, providing reduced noise levels, no engine emissions and the ability to run indoors with decreased operational and maintenance expenses. The trackmounted FT4250CC is remote-control operated, features a heavy-duty steel frame, uses a robust horizontal shaft impactor, and with a 36-inch feed opening, is well-suited for both aggregates and recycling.

RUBBLE MASTER RM CELEBRATES 20 YEARS IN NORTH AMERICA RUBBLE MASTER, which celebrates 20 years in North America this year, exhibited their RM 70GO! 2.0 crusher in combination with the company’s line of screens and other compact crushers. According to RM, starting this year, a combination that has been available for its larger compact systems for some time, a proven, integrated mesh screen with refeeding belt, is now offered with the RM 70GO! 2.0, along with a range of updated features.
Keestrack displayed their Red Dot award-winning R3e electricdiesel hybrid impact crusher at CONEXPO. These machines were designed to meet all criteria of C&D recyclers, contractors and aggregates processors, considering current stringent requirements with respect to mobility, productivity, weight and transport dimensions, dust and noise suppression, and other health and safety considerations. Units use a rotary impact crusher with a capacity up to 250 tons per hour and provide low emission levels, low costs per ton and high end-product quality. With options such as a screen and magnetic separator, the R3e is under 30 tonnes in weight, and with its hydraulic folding system, can be folded to one-piece transport mode within five minutes.
As a hybrid-electric machine, the R3e’s diesel engine can be switched off and it can be run from a noise-suppressed generator set or the main electrical power grid. Zero emission levels are achieved due to the hybrid system when running on main grid electrical power, with both the crusher and the anti-dust suppression system capable of running while the diesel engine is switched off. Plus, due to the unit’s plug-out KEESTRACK AWARD-WINNING HYBRIDELECTRIC IMPACTOR ON DISPLAY AT CONEXPO-CON/AGG
connection, additional electric equipment, including stackers, can be powered via the R3e. Other key features of these impact crushers include: high-tensile steel in the frame and feed hopper; standard dust suppression as well as a unique optional separate automated dust suppression system; anti-vibration system; telematics for system diagnostics and control; the largest crushing chamber in its weight class; and a range of available options.

COMING UP IN THE MAY/JUNE ISSUE OUR CONEXPO 2020 REVIEW CONTINUES FOCUS ON: SCREEN PLANTS FOR C&D AND ORGANICS; RECYCLING APPLICATIONS AND FIND ALL OUR NEWS ONLINE
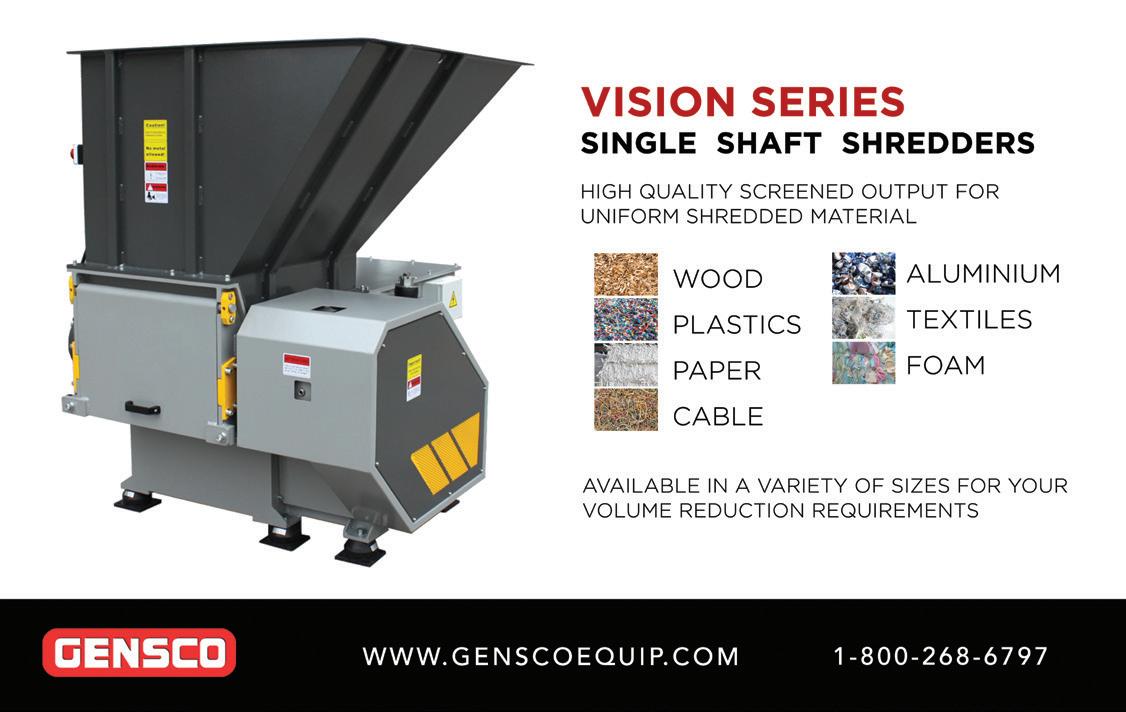
The MOBICAT MC 120 Zi PRO jaw crusher plant debuted at CONEXPO-CON/AGG 2020, as one of four innovations from Kleemann on display at the Wirtgen Group / John Deere booth.
With an output of up to 717 U.S. tons per hour, the MOBICAT MC 120 Zi PRO is impressive in natural rock applications as well as C&D recycling. This powerful jaw crusher has a feed opening of 48 x 32 inches and is equipped with an extra-long articulated crusher jaw. To ensure the best possible material flow, the continuous feed system (CFS) adapts the conveying speed to the fill level of the crusher. On most jaw crushing systems, the operator has the timeconsuming task of clearing the crushing chamber in the event of material blockages. Not so with the optional crusher unblocking system. Should material bridging occur in the jaw crusher, the crusher can be reversed with the aid of the electric crusher drive and in this way the blockage can be cleared in no time. The machines of the PRO line can be operated with the simple SPECTIVE control system via a 12-inch touch panel. All components and functions can be controlled conveniently from the ground.
Also on display this year for Kleemann was the new MOBISCREEN MS 952i EVO classifying screen, as well as the MOBIREX MR 130 Zi EVO2 impact crusher. This 496 U.S. tons per hour impactor is designed for easy transport and setup, includes SPECTIVE control, and features a direct diesel drive concept for high output and low fuel consumption. KLEEMAN MOBICAT PRO JAW CRUSHER
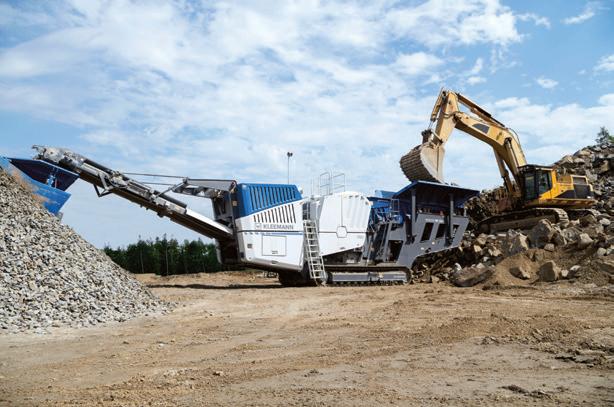
NEW NW RAPID RANGE TAILORED FOR NORTH AMERICA Metso has extended its NW Rapid series of transportable wheel-mounted crushing plants with a range developed specially to accommodate road transportation regulations in North America. The first models of the range are the NW120 Rapid portable jaw crushing unit and NW1213 Rapid portable impact crushing unit, which have been re-designed to permit their transportation in most regions of the North American market. The first NW1213 Rapid impact crusher will be in operation in the USA in 2020. METSO

“Traditionally, it has been very common in North America to put crushers on wheels. We developed the North America specific models to meet our customers’ requirements: Road regulations are getting tighter and they are looking for more complete solutions from one supplier,” said Julius Mäkelä, Director of Portable and Modular Solutions at Metso. The NW Rapid can be moved from one site to another using standard prime movers. According to Metso, besides portability, other advantages of the NW Rapid models include quick setup and a production capacity of up to 500 metric tons per hour. NW Rapid has been designed so that the units can be set up in about an hour. The solution consists of modules that can be used to create a variety of combinations also in fixed installations as needed.
McCloskey showed off its redesigned impact crusher line in a new heavy-duty format. The updated McCloskey I44RV3 combines the productivity of a 45-inch impactor with the versatility of a full screening and recirculating system, allowing operators to produce a crushed and screened final product with one machine. The combination of the impactor and a High Energy Screenbox and a recirculating conveyor deliver maximum productivity and unmatched portability, according to McCloskey. New features include an open chassis for ease of access, a larger double-deck prescreen for more efficient fines removal, a swing-out radial return conveyor that can complete 90 degrees while the machine is running, and a direct-drive crusher boosting power and lowering fuel costs REDESIGNED IMPACT CRUSHER MCLOSKEY
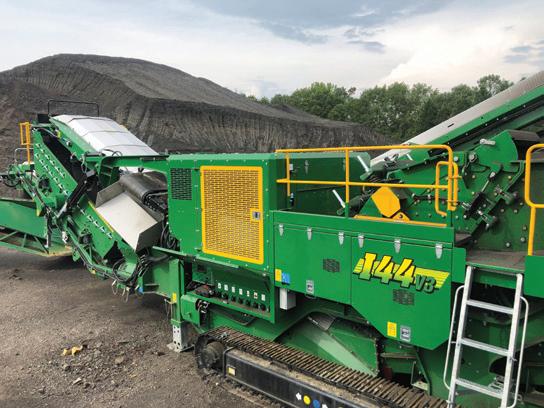
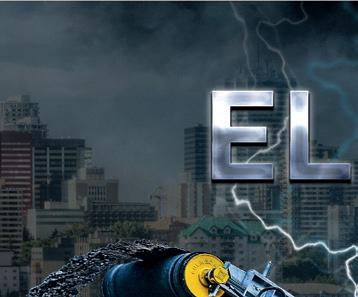


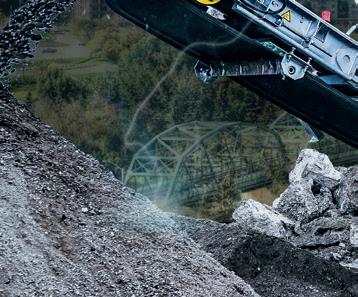
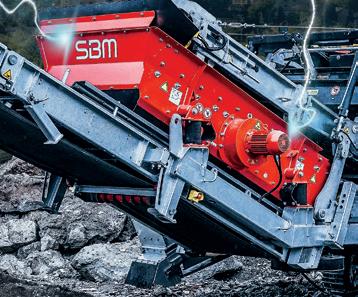


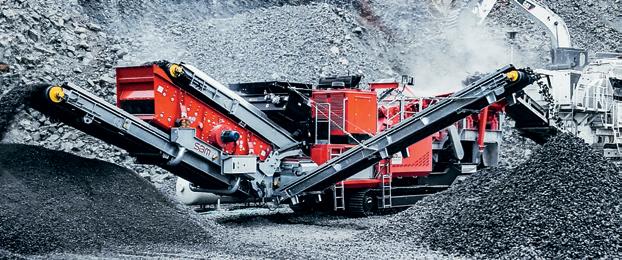
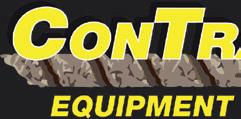
Toll-Free: 888.900.6869 (24/7) PHONE: 780.960.9475 FAX: 780.960.3407 E-MAIL: michaelk@contraceq.ca 220 Diamond Ave. Spruce Grove, AB T7X 4C7 www.contraceq.ca

MOBILE CRUSHING & SCREENING EQUIPMENT 50,000 LBS TO 150,000 LBS
NORTH AMERICAN PARTS & SERVICE HUB DIESEL-ELECTRIC OR 100 % ELECTRIC

SBM MINERAL PROCESSING NORTH AMERICA 650 RT. 112, St. Cesaire, Qc Jol 1t0, Canada P: 800-331-0043 – E-MAIL: americas@sbm-mp.at