
16 minute read
ISRI SHOW PREVIEW
ISRI 2020 T he Institute of Scrap Recycling Industries (ISRI) annual Convention & Exposition is the world’s largest annual scrap recycling industry event. The event focuses primarily on the recycling of ferrous and nonferrous metals, plastics, paper and fibre, tires and e-waste.
DOOSAN MATERIAL HANDLERS AND WHEEL LOADERS Doosan Infracore North America, LLC, will display its DX210WMH-5 material handler, along with a DL280- 5 wheel loader, at the 2020 Institute of Scrap Recycling Industries Convention and Exposition.
According to Doosan, the new DX210WHM-5 material handler is designed to provide scrap and recycling professionals with improved fuel efficiency, versatility and productivity. DX210WMH-5 material handlers excel in a variety of scrap-handling applications, at scrapyards, recycling facilities, solid waste centres and transfer stations.
The DX210WMH-5 includes four selectable power modes that allow customization for different jobsite requirements and features a lifting work mode which provides increased pump torque, low engine rpm and an automatic power boost to improve operator precision when lifting and placing materials.
Our show preview highlights some of the latest equipment and technology that companies will be exhibiting at this year’s event.
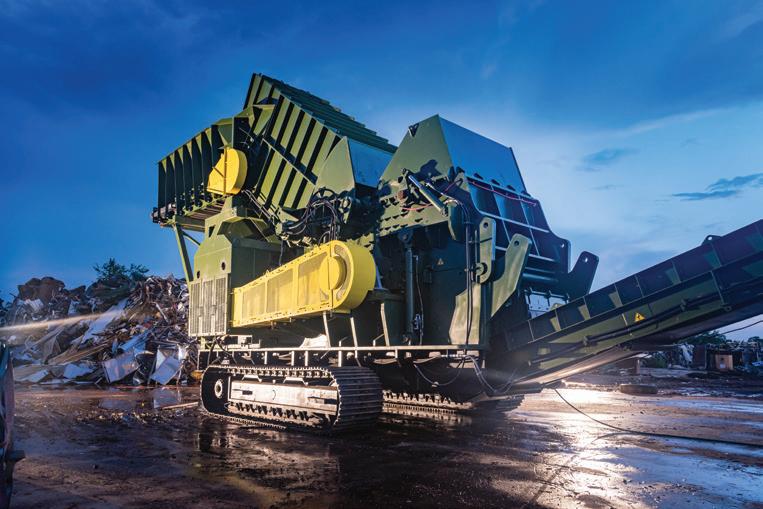
At press time Recycling Product News
was advised that ISRI 2020, originally
BRAVO 6280 SHREDDER FROM 3TEK GLOBAL 3TEK Global has introduced the compact mobile Bravo 6280 scrap shredder. Part of 3TEK’s lineup of mobile and stationary hammer mills and downstream sorting systems, this latest model was designed in partnership with Blanchard Machinery, Granutech-Saturn Systems and Riverside Engineering from the ground up as a true mobile hammer mill that can process up to 3,000 tons per month. The new machine will be a focus for the company at ISRI 2020.
“The Bravo 6280 was designed to serve the scrap marketplace,” said Bill Padula, VP of sales and marketing for 3TEK Global. “This is a true mill that delivers very clean, dense, furnace-ready scrap at a price point for both purchase and production that makes sense for small and large operators alike.”
According to 3TEK, the Bravo 6280 is an ideal option for smaller scrap operations or those that want to make the move beyond being just a collection site, or which may be seeking to expand existing scrap milling operations. And with O&O costs less than $28/ ton, the new Bravo 6280 will raise both the user’s capability and profits.
Driven by an 1,125-hp CAT32 diesel engine, the Bravo 6280 can comfortably produce 15–20 output tons per hour in ferrous output capacity (13.7 m tons/hour) with 240-pound hammers on a 315,000-pound single chassis that is 80 inches wide and equipped with a 19-foot feed chute. Its operating cost is less than $25 USD per ton, providing a combination of capacity and efficiency that provides top margin and return on investment. scheduled for the end of April in Las Vegas, will be postponed. Further information will be provided when available.
GENSCO DYNASET HMG HYDRAULIC-DRIVEN MAGNET POWER AND CONTROL Toronto-based recycling equipment specialist Gensco will highlight its DYNASET HMG and HMG PRO hydraulic-driven magnet power and control system (models from 3kW to 30kW) for use with hydraulic excavators along with a range of equipment for recycling applications. HMG systems are sold as a complete package, including the generating and electronic control system, custom priority or load sense oil flow valve system and wire harness kit, with on/off switch, push button activation and magnet indication sensor. According to Gensco, the new HMG PRO option offers the most sophisticated solid-state control system on the market.
These reliable, weatherproof generators can be supplied with everything needed to install on any make and model of hydraulic carrier. There is no need to add an expensive dedicated pump and auxiliary drive, and Gensco can customize any installation with custom valve packages, allowing operators to use multiple hydraulic functions with the magnet generator on. All genera tors are also supplied with 110V AC sockets, suitable to charge phones and operate computers, lights and small work tools like a

TRIPLE COVERAGE DUST CONTROL FROM BUFFALO TURBINE Buffalo Turbine recently introduced the Trident dust control solution. This system uses three separate turbines all powered by the same Kohler 74-hp diesel engine, capable of three times the coverage area compared to single turbine dust controllers. Different from other dust control units on the market, this unit is self-contained, meaning no generator is required, lower maintenance costs and less space required for setup.
According to Buffalo Turbine, each of the three turbines on the new Trident model uses their Gyra tory Atomizing Nozzle technology, which does not clog like conventional nozzle tips. The Trident is avail able with one, two or three oscillation kits to match desired coverage in a wide range of applications from scrap metal and C&D recycling to composting and solid waste. drill or grinder.
At ISRI 2020, Gensco will also be focused on its complete selection of round and rectangular 24V and 230V DC CANMAG Scrap Handling and Steel Mill Magnets, hydraulic H-MAG Magnets for scrapyards and demolition sites, and Heavy Severe Duty magnets for mill use, slab turning, billet/bloom and hot structural handling.

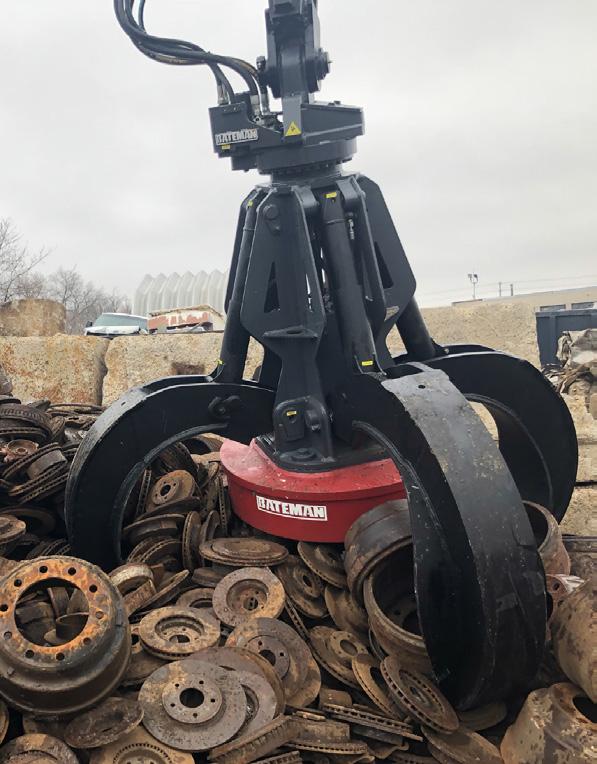
MAGNET GRAPPLE


BUNTING STAINLESS STEEL SEPARATION CONVEYORS This year at ISRI 2020, Bunting will be showcasing a strong lineup of products, including the patented SSSC (Stainless Steel Separation Conveyor). This piece of equipment utilizes its patented magnetic circuit design of high-intensity neodymium magnets to maximize the recovery and removal of stainless steel in applications such as wire chopping streams, auto shredding and general recycling. The intense power of the SSSC enables recovery of up to 94 percent of large fraction stainless steel, and up to 98 percent of small- and mid-fraction 300 series stainless steel from ASR zurik lines. By achieving the maximum removal of ferrous dust and stainless steel from wire fraction, Bunting says its SSSC provides users with the purest zurik and the greatest scrap metal recovery profitability.
According to Bunting, no other product available on the modern recycling market allows for the high stainless steel recovery levels that the SSSC delivers. Every feature on the SSSC has been designed to maximize separation efficiency while streamlining operations.
The SSSC is equipped with 8- and 12-inch-diameter patented high intensity neo magnetic circuit head pulleys that are capable of holding all sizes of 300 series stainless steel, as well as VFD controllers operating between 30 and 120 fpm to deliver effective separation. General capacities run about 1,000 pounds/hr/ft width on small fraction, 1,500 pounds/ hr/ft on mid-fraction, and 2,000 pounds/hr/ft on large fraction. Custom design options are available.
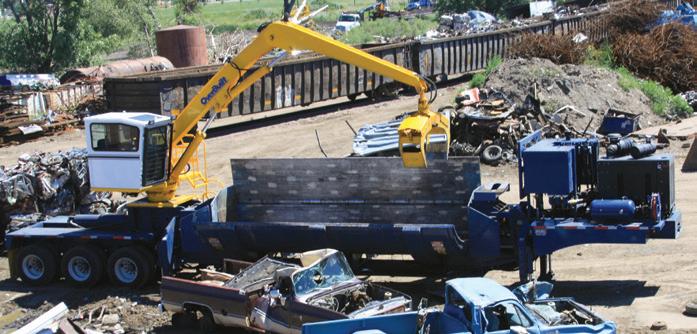
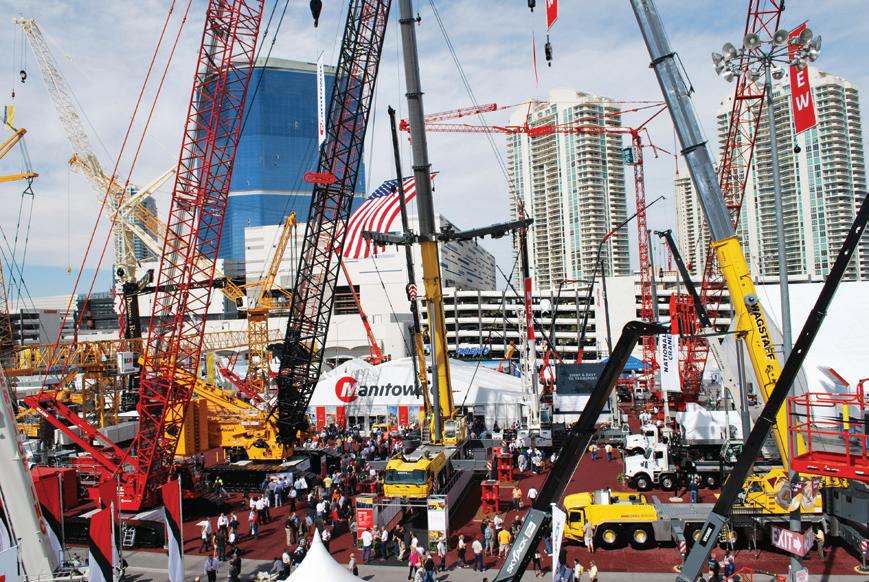
— Joe Pickard, ISRI chief economist and director of Commodities

OVERBUILT CAR CRUSHERS AND BALER LOGGERS OverBuilt’s latest models of recycling equipment include the Model 10 Car Crusher and the Model 20 Baler Logger (shown right). Both of these models will be a focus for the company on the show floor at ISRI 2020.
OverBuilt’s Model 20 Baler Logger is designed with crane reach at 26.5 feet and a 5,000-pound lifting capability at 25 feet, providing smooth operator loading and unload ing of material. The unit’s standard clam grapple is ideal for cars as well as loose scrap, and an orange peel grapple is available. According to OverBuilt, with baling at 4,600 psi and logging at 3,200 psi, these machines provide the highest pressures in the industry. Plus, all functions can be changed with the touch of a button in the unit’s heated, airconditioned and roomy cab.
OverBuilt Model 10 Car Crushers feature a large opening, at 10 feet, long crushing bed, at 20 feet 3 inches, along with a patented high-speed oil bypass system that cuts cycle time in half. The unit also features a 400-gallon fuel cell and fluid recovery system and state of the art remote control. Additional 22- and 24-foot models are available.

LBX Company has introduced Link-Belt LSG Series Scrap Grapples and LCG Series Contractor Handling Grapples, designed for scrap handling, C&D sorting and bulk material handling.
The new LSG Scrap Grapple is a low-maintenance, high-capacity orange peel model designed for highvolume scrapyard processing. Available in four models, LSG key features include: reverse-mounted cylinders that protect rods from damage; multiple tine and spade styles for all types of scrap material; fully boxed construction for strength and durability; an overall footprint that easily fits inside trailers; and a heavy-duty guarding system that completely protects cylinders and internal components yet is easily removed for maintenance. These scrap grapples use identical hardened steel bearings with dust seals at all pivot points that protect against external debris, and largebore hydraulic cylinders for maximum clamping force. Units also provide high-torque, continuous 360-degree rotation and feature abrasion-resistant steel tips that are easily replaced with a simple perimeter weld. LINK-BELT SCRAP GRAPPLES

LABOUNTY’S LATEST MOBILE SHEARS EMPLOY TELEMATICS LaBounty’s expanded line of mobile scrap shears, the MSD Legend Series, are available in four new models: the MSD4000R, MSD4500R, MSD2000 and MSD1500R. These new Legend Series shears include InSite telematics, which provides real-time data to optimize shear performance and productivity. An industry first, according to Labounty, InSite is an advanced telematics platform that provides actionable information about the shears’ condition and activity, such as job tracking, jobsite mapping and remote diagnostics. With the InSite app, available for iOS and Android, Legend Series shear users have access to valuable information that helps optimize performance. Additional MSD Legend mobile shear features include: full 360-degree rotation; enhanced, durable lower jaw; long-lasting index blades with four-way indexable cutting; full-protection for the indexable piercing tip; and wear bar protectors for maintaining heavy wear surfaces.
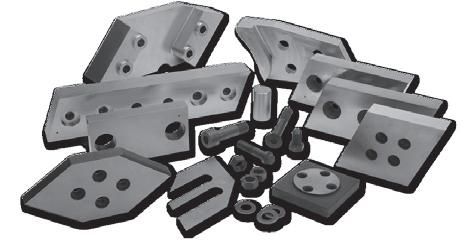
SCRAP RECYCLING PRODUCTS
MOBILE AND STATIONARY SHEAR BLADES
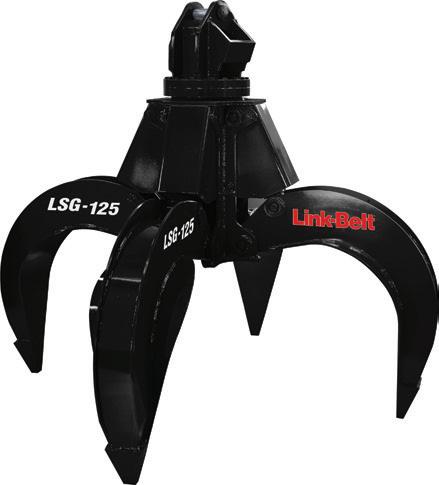
• Piercing Tips • Hardware
• Custom Blades • Shear Blades • Shim Kits • Wear Plates
SWANA 2019 SOLID WASTE FATALITY DATA SHOWS INDUSTRY LOSS OF 53
At least 53 solid waste industry workers died on the job in 2019 in the United States and Canada, according to the Solid Waste Association of North America (SWANA). The most common cause of death was being struck by one’s own waste vehicle, followed by single-vehicle accidents involving only a waste vehicle. Over 40 percent of worker fatalities were a result of one of these two causes.
Solid waste and recycling collection continues to have the highest occurrence of fatalities, representing about 68 percent of worker deaths. Fatalities at landfills increased slightly from 8 in 2018 to 11 in 2019, and fatalities at MRFs increased from three to four.
“The number of solid waste-related fatalities continued at unusually high levels in 2019,” commented David Biderman, SWANA’s Executive Director and CEO. “Although there was a small decline from 2018, and that slight improvement has continued into 2020, we
120
100
80
60 40 20 0
59
53
WORKER
2018
U.S. and Canada solid waste fatalities.
remain concerned about the solid waste industry’s overall safety performance. We urge all employers and employees to take advantage of the growing number and variety of SWANA safety resources,” he added.
SWANA collects data on solidwaste-related fatalities from a wide
A FIRE PREVENTION & MANAGEMENT PLAN FOR RECYCLING FACILITIES As an aid to helping scrap recycling facilities develop strategies for reducing the risks of fire, the Institute of Scrap Recycling Industries (ISRI) has released a new electronic publication, Creating a Fire Prevention and Management Plan. The book was developed by fire science, insurance and scrap recycling industry professionals. It is meant to be used as a guidance document to help business owners, operators and EHS professionals better understand and mitigate potential risks before they become bigger problems. “The Creating a Fire Prevention and Management Plan is a terrific resource for any scrap processing operation seeking guidance on preparing a plan,” said Scott Wiggins, vice president of environment, health and safety for ISRI. “This guidance document provides information on how to prepare a fire prevention plan, fight incipient stage fires, and to be prepared in the event of a crisis management scenario. Even if your facility has an existing plan, this is a valuable tool to help you review your operations and make any necessary improvements.” Creating a Fire Prevention and Management Plan serves as a living document, and ISRI plans to review and update it at least once every year. While the document does provide a detailed, and scalable overview of developing a plan, each site is different. Plans should be prepared according to the type and size of the facility and, depending on the size, not all suggestions may be appropriate. The document is available for free to those in the recycling industry.
101
80
2019
MEMBER OF PUBLIC
SOLID WASTE ASSOCIATION OF NORTH AMERICA
number of industry and media sources in order to produce an annual picture of the state of safety. In addition to the workers killed on the job in 2019, at least 80 members of the public were killed in an incident involving the industry. Almost all of these were the result of a collision with a solid waste collection vehicle. Two-thirds of the victims were a driver or passenger at the time, and about 16 percent were pedestrians. Incidents involving motorcyclists represented 9 percent and bicyclists 7.5 percent of fatalities in 2019.
Forty-four of all fatalities recorded by SWANA in 2019 occurred in the United States and nine were in Canada. This represents an increase from 2018 when four fatalities were recorded in Canada and 2017 when there were six. January was the deadliest month in 2019, with 22 total fatalities.
“Employers must look inward for causes and corrective actions,” recommended Suzanne Sturgeon, SWANA Safety Committee Chair and Health & Safety Program Manager for SCS Field Services. “Changing the culture of workers is essential to this effort. Training frequently in small and digestible doses is paramount to make this shift,” Sturgeon added.
Winds of Change in Halifax, Nova Scotia!

Join us in Halifax!
CARI’s 79 th Annual Convention - “Winds of Change” June 11 - 13, 2020
Contact: Donna Turner Phone: 613-728-6946 ext 2 Email: donna@cari-acir.org

“ “ I n 2020 Plessisville, Quebec-based Machinex is celebrating its 50th anniversary in manufacturing.
“Half a century in business is a great source of pride, but also a major accomplishment when we think of all we had to navigate through to be here,” commented Pierre Paré, CEO of Machinex Group. “Only 10 years ago, we were barely 200 employees and today we are nearly 500.” A HISTORY IN RECYCLING
Founded in 1970 in Plessisville, the company initially offered machining services, parts and equipment manufacturing for industrial and agricultural clientele. In 1980, Machinex began to offer engineering services, project studies, equipment manufacturing and installation, still within the industrial and agricultural sectors.
In 1985 Machinex officially entered the recycling industry by delivering a sorting facility in Victoriaville, Quebec. Another important turning point MACHINEX CELEBRATES 50 YEARS IN 2020 for Machinex came in 1989 when the company decided to devote its activities entirely to the recycling industry. Machinex was subsequently awarded the contract for design and construction of the first material recovery facility (MRF) for curbside recycling in Canada, for Laidlaw in Ontario.
After experiencing significant growth in Canada and in order to better serve customers in Ontario, Machinex opened a sales and service office in Toronto in 1995. This division was registered Machinex Recycling Services Inc., and now includes a satellite office near Vancouver.
In the early 1990s, Machinex won its first contracts in the United States which led to the creation in 1996 of the Machinex Technologies Inc. division, with the opening of an office in Chicago. The sales office in the United States is now relocated to High Point, North Carolina.
The European division of Machinex, currently called MRS Europe Ltd., was METHODS HAVE EVOLVED IN THE FIELD OF RECYCLING, MARKETS CONTINUE TO FLUCTUATE AND WE HAVE TO ADAPT IN ORDER TO REMAIN COMPETITIVE. PIERRE PARÉ, CEO OF MACHINEX GROUP
Right: Machinex Group CEO Pierre Paré, at the Plessisville main factory in 2020. Right middle: In 2019, RPN was invited to visit Machinex’ SamurAI robotic sorters at the Sani-Eco MRF in Granby, Quebec. Right bottom: Machinex’ planned Technology Hub. Left: Machinex’ original factory in Plessisville, Quebec, when the company specialized in machining, parts and equipment for industrial and agricultural customers.
created in 2009 after Machinex was awarded a first major contract in England. A service office near Manchester was opened in 2012 to better serve Eu- ropean clientele.
These various companies are now gathered under Machinex Group, owned by Pierre Paré, the single shareholder since 2016. Paré joined the company in 1983 as a sales engineer and became a co-shareholder in 1989.
According to Machinex, over the years they have always adapted to market changes, and focused on the development of equipment and systems that al- low customers to improve the performance of their recycling operations through advanced automated sorting and techniques.
Today the company continues to pursue its primary vocation to deliver high-performance turnkey material recovery facilities. Machinex-built equipment and systems for recycling is wide rang- ing, including disc screens, trommels, balers, glass cleaning equipment, ballistic separators, optical and robotic sorting technology, as well as special- ized equipment such as plastic perforators and eddy current separators.
To fuel its vision for the future and the develop- ment of its latest technologies, the company is currently completing the construction of a new Technology Hub which will welcome its research and development department along with the manufacturing line of high-tech equipment such as optical sorters and sorting robots.
“Methods have evolved in the field of recy- cling, markets continue to fluctuate, and we have to adapt in order to remain competitive,” said Paré. “Machinex has greatly contributed to the development of the recycling industry and sorting technologies over time.
“We can affirm that we are an international reference in the environment and waste management industry for our expertise in high-performance sorting solutions. This happened due to the hard work of a great team.” RPN


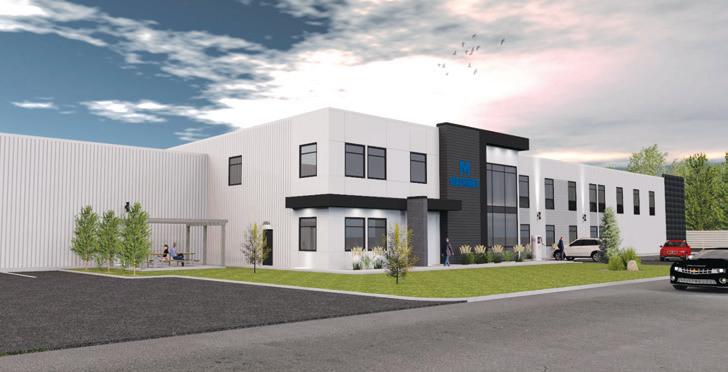