
16 minute read
DOUBLING DOWN ON SCRAP
THE MRYGLOD FAMILY SCRAP BUSINESS IN SASKATCHEWAN ADDS THIRD SCRAP HANDLER IN FOUR YEARS TO KEEP UP WITH GROWTH
BY JOSH HAFNER
When Mryglod Steel & Metals, based in Weyburn, Saskatchewan, bought its first Doosan material handler in 2016, the family-owned business had a 10-acre yard backed up with steel, aluminum and copper. They needed to sort slews of scrap metal as efficiently as possible, and its new DX300MH-5 proved up to the task. Four years later, the business has grown significantly, and its Doosan fleet has grown with it.
Their initial purchase, a DX300MH-5 material handler from Bobcat of Regina, performed so well that the family picked up a second Doosan material handler, a DX225MH-5, in 2017. That’s also when the Mryglods expanded to a second location, a 3-acre yard in Regina. Earlier this year, the business swapped out their four-year-old DX300MH-5, their first Doosan material handler, after 9,000 hours of smooth service, for a new DX300MH-5 model.
“If it didn’t perform like we expected it to, I wouldn’t have traded it in on a brand-new one,” said Mryglod Vice President and CEO Travis Mryglod, who now owns the business with his three brothers and their mother, Sandra.
DOUBLED EFFICIENCY
The Mryglod family has collected scrap metal since the 1940s when Travis’ great grandfather, Alex Mryglod, recycled scrap for military equipment in World War II. Today, Mryglod Steel and Metals Inc. buys metal from a range of sources, including auto yards, railroads and industrial firms. That metal gets sorted by their Doosan material handlers before being cut and shredded. It’s then torched and baled for melting into new steel and products. Finally, using their material handlers again, recovered scrap is reloaded onto trucks for transportation to the steel mill.
The DX300MH-5 and DX225MH-5 play vital roles at both ends of the process, Travis says. The machines unload the aluminum, steel, lead and copper, old vehicles, appliances and other outdated machinery. Then excavators outfitted with shears aid with the
processing, cutting scrap metal down to mill-ready specifications. Once ready, the material handlers then pile up the material and load it into 8-foot walled trailers or end dumps for shipping.
According to Travis, their purposebuilt material handlers have given a much-needed boost to Mryglod Steel & Metals, which previously sorted using older excavators with grapple or magnet attachments. “It’s, at least, doubled our efficiency, as far as loading goes,” he says. “With the converted excavator, we were taking upwards of an hour, hour and a half, to load a truck. Now it’s not even 25 minutes.”
Doosan says that improved speed stems partly from the machines’ improved reach: the DX300MH-5 has an extra 15 feet of reach compared to machines that Mryglod used prior, and also benefits from a straight boom, a droop-nose stick and a sandwiched counterweight. see anything. So you’re just kind of grabbing at stuff and hoping for the best.”
One other notable detail his team really appreciates is the Bateman generators that came with both handlers to operate the magnets. Customers can add a Bateman generator to their Doosan material handler as an option when they order a machine. “Hydraulic gensets can be finicky,” Travis says, “but the Bateman system has proved very good.”
“We put 9,000 hours on that 300, and the generator – not one problem.” He adds that this is the same for their Doosan material handlers, with which, after years of very tough, continuous work, they have “never really had any issues.”
Josh Hafner is a technical writer based in Des Moines, Iowa.


high-speed Car Crushers & baler loggers
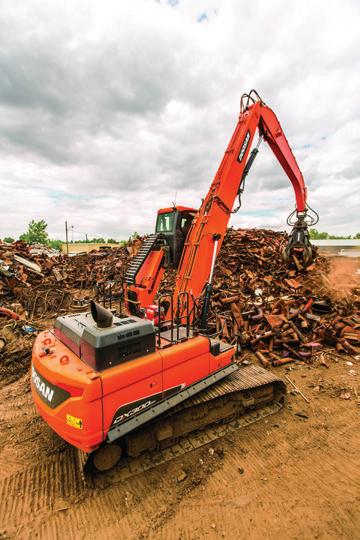
customized options available!
ADDED SAFETY FOR SCRAP
Doosan’s material handlers aren’t just very productive. They’re safe too.
With an optional hydraulically raised cab of 6.5 feet, the DX300MH-5 lets operators see clearly around them and into the loading trucks – a boon for any scrapyard with tight quarters.
“You don’t need a spotter trying to tell you what holes to fill in the trailer because you can see right into the bottom,” Travis says. “And same goes for unloading, where with the converted excavator, you can’t get up high enough. You can’t
OverBuilt Car Crushers boast the highest opening and fastest cycle times in the industry. The crane on our Baler Logger has a 26.5-foot reach with a 5000 pound lift at 25 feet.


OVB HOLDINGS, LLC

overbuilt.com | sales@overbuilt.com | 800-548-6469 | 605-352-6469
EQUIPMENT FOCUS: MATERIAL HANDLERS FOR SCRAP Sometimes referred to as a “mobile crane,” and sometimes as a “scrap handler,” this category of heavy equipment has the speed, agility, quick cycle times, operator safety and comfort features to make a real difference for recyclers at the scrapyard or at the MRF. Compared to using a hydraulic excavator, which costs less up front, but which uses considerably more fuel to do a job it was not meant for (the moving, sorting, loading and unloading of scrap materials), these fuel-efficient, highly productive, purpose-built machines come with a very quick ROI for recyclers.
Following are the latest models available from the leading manufacturers in the industry.

<< Caterpillar introduced the MH3040 material handler in 2020. Specifically designed for scrap and millyard applications, the MH3040s are the largest in Cat’s lineup, and feature boom, sticks and other high-stress areas with thick, multi-plate fabrications, castings and forgings to withstand wear and deliver years of durable operation, as well as specially designed mountings on the upper frame to support a new heavy-duty cab.
The MH3040 uses a Cat C7.1 152-kw (202-hp) engine, has a maximum operating weight, of 38,529 kg (84,940 pounds), and maximum reach of 15,490 mm (50 feet 10 inches).
E-Crane’s commitment to quality during design and fabrication including installation and service has been outstanding. Clyde Billips, MetalX


<< Hyundai Construction Equipment Americas introduced the HW250MH wheeled material handler in early 2020. Hyundai says its new wheeled material handler is evolved from its wheeled excavator line and is designed to meet a wide range of onroad and off-road applications, including scrap metal and other recycling applications. Units feature high agility, load-and-carry capacity and versatility for high productivity and efficiency.
<< LBX introduced two models for the U.S. and Canada in 2019 including the 250 X4 Scrap Loader/handler. This machine uses an electronically controlled 177-hp Isuzu engine that meets Tier 4 Final requirements without the need for a diesel particulate filter. Other features include a straight boom and droop-nose arm, and a new hydraulics package delivers up to 7 percent faster cycle times than its predecessor.
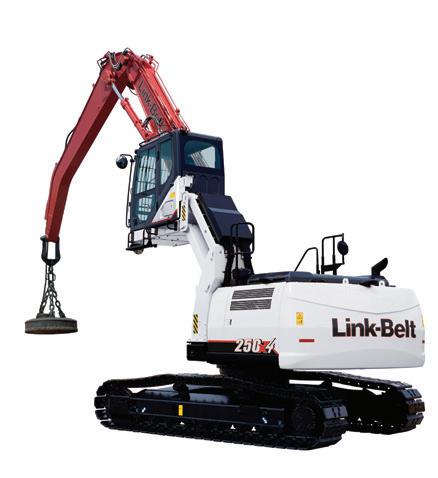
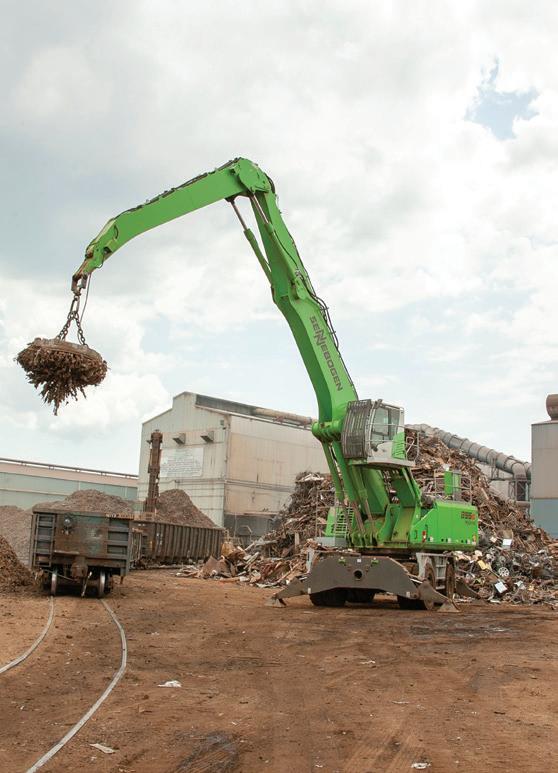
<< SENNEBOGEN’s recently introduced E-series 855 M Hybrid dedicated material handler at 71,000 kg (157,000 pounds) is the smallest in the SENNEBOGEN lineup to offer SENNEBOGEN’s Green Hybrid energy recovery system, which uses a large energy recovery cylinder mounted between the two hoist cylinders on the lifting boom. On every downstroke of the boom, this oversized hydraulic cylinder captures the energy produced by the lowering action and stores it in compressed nitrogen cylinders located in the rear of the machine. The stored energy is then used during the next upstroke to supplement the hydraulic power that lifts the load.
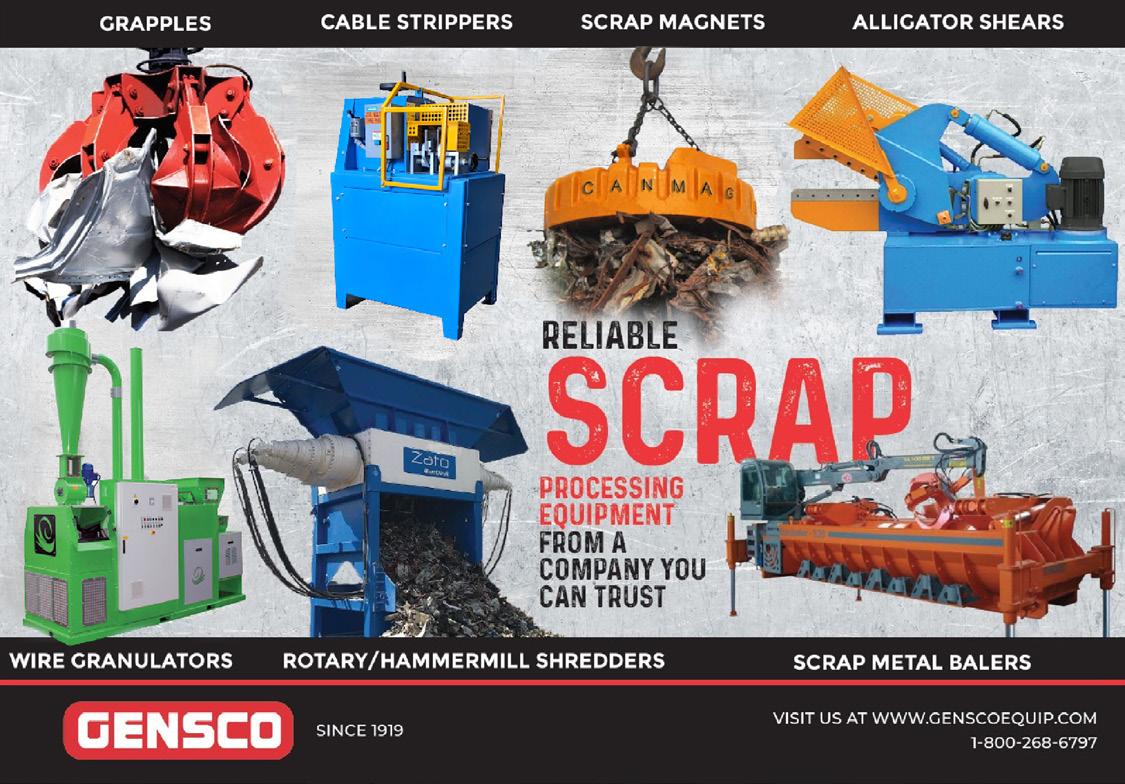
<< Liebherr introduced two new models specifically designed for scrap handling in 2020: the LH 30 M and LH 60 M, both part of the Industry Litronic series. The LH 60 M Industry Litronic is designed for heavy-duty scrap handling with an operating weight between 121,300 and 134,500 pounds (55 – 61 t) and an engine output of 190 kW / 255 hp. The LH 60 M includes hydraulic cab elevation, which can be variably adjusted for different loading situations, giving the driver an optimal view of their working area at all times, and cameras allow optimal monitoring of the rear and side of the machine.
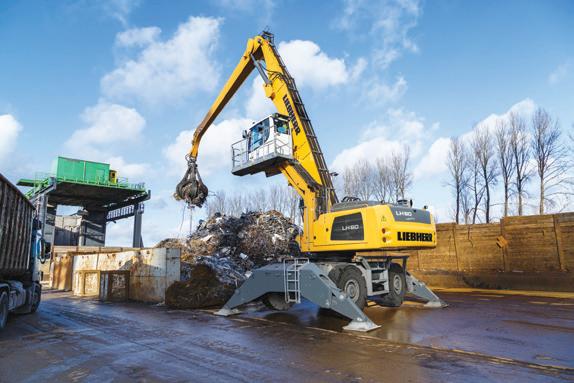

<< Terex Fuchs’ latest material handler introduced at the end of 2019 is the MHL375 F, which the company says bridges the gap in the 132,000 – 154,000 pounds category. According to Fuchs, the machine was designed from scratch and the main target groups are scrapyards which load shredders or shears, steel mills and river terminals. One stand-out feature is the huge undercarriage, which provides room for different tire combinations.
Car-Go-Net® “The preferred disposable”
•Fused joints won’t unravel • Easy to apply in a single pass • In stock for immediate shipment


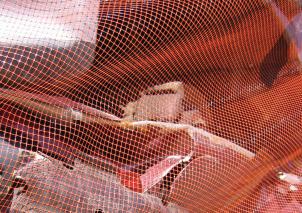

<< Doosan introduced the DX250WMH-5 wheel material handler in early 2020. This 25-metric-ton material handler is built to provide increased lifting performance. The DX250WMH-5 replaces the Doosan DX210WMH-5. The new DX250WMH-5 material handler is designed for scrap, solid waste and recycling applications.
New to the DX250WMH-5 material handler are two arm cylinders straddling the machine’s boom and arm. This update improves the machine’s performance and control of the material during the lift and placement cycle. A droop-nose arm continues to be standard, but Doosan also now offers an optional straight arm.
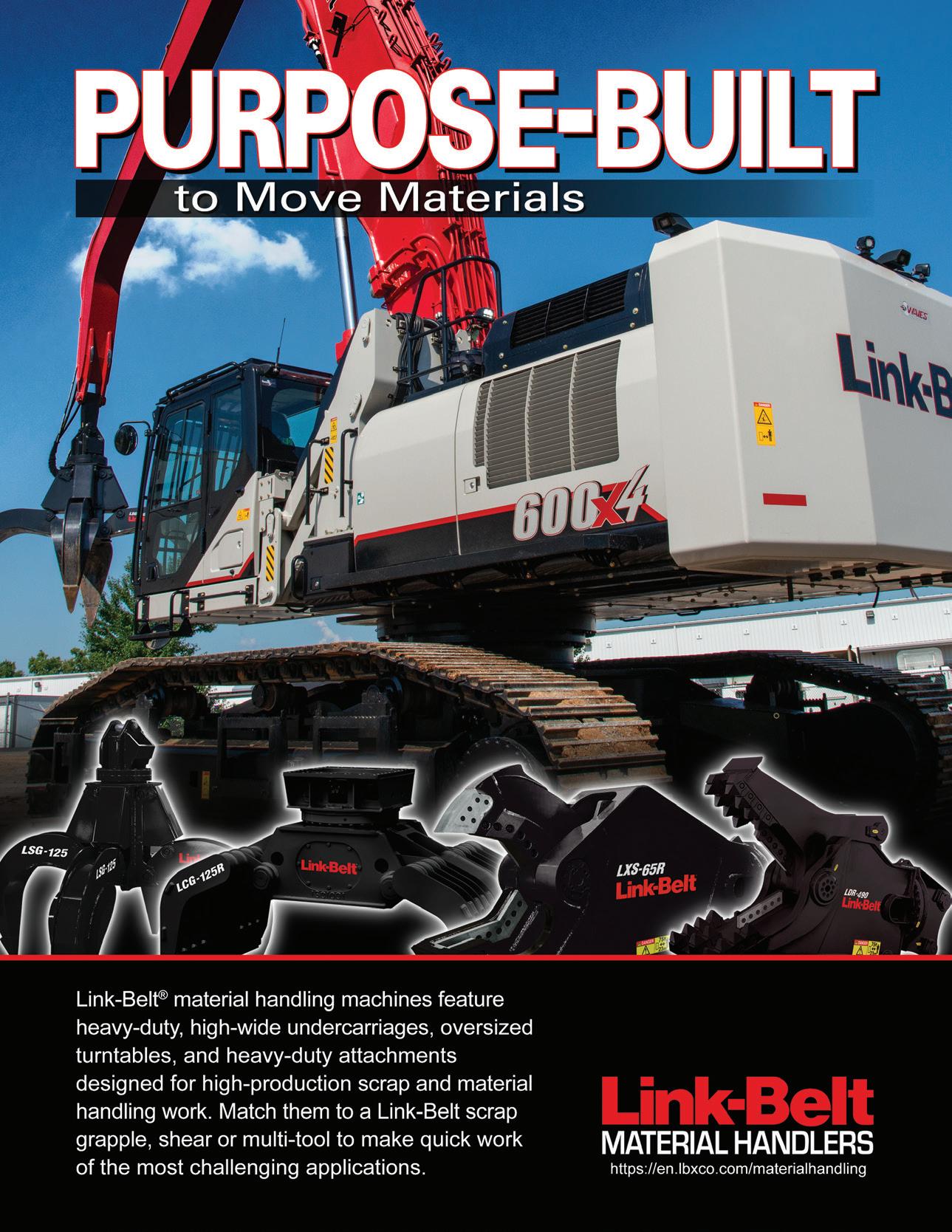
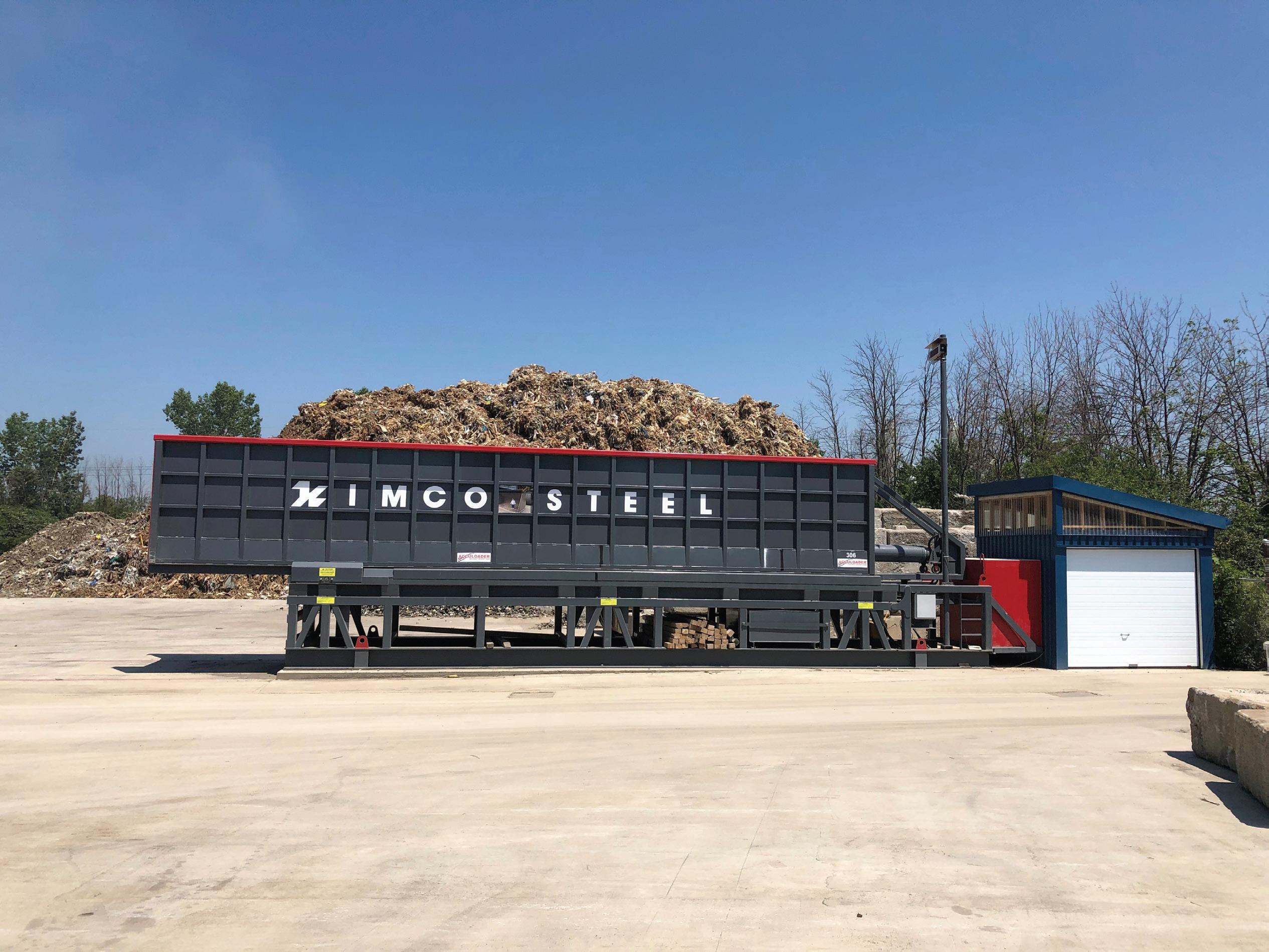
CONTAINERIZED OPPORTUNITY
WITH AN ACCULOADER AUTOMATIC LOADING SYSTEM, EVEN SMALLER YARDS CAN TAKE ADVANTAGE OF SURGING OVERSEAS DEMAND FOR CONTAINERIZED SCRAP METAL
Traditionally, recyclers across Canada have sent a huge percentage of their recovered scrap metal to Hamilton, Ontario, or Pennsylvania in the U.S., via open-top rail cars and truck trailers. The scrap is then melted down and turned into new steel. This is still the case for much of our scrap steel, but recently the growing trend toward containerization has introduced new opportunities for efficient, costeffective shipping of both non-ferrous and ferrous materials to overseas markets.
According to Greg Bushong, founder of Acculoader, any size scrapyard can order five, ten or one hundred 40-foot containers and use Acculoader’s high-speed container loading system to fill them 25 tons at a time, in under 15 minutes each, and sell to high-demand steel mills overseas.
“Containerization is a relatively new trend in the industry,” he says. “The Acculoader container loading system can help recyclers take advantage of it,” adding that this not only applies to larger scrap recycling companies, but smaller yards and family-
run businesses. “With the Acculoader, any scrapyard can now sell direct to mills overseas, basically cutting out the middleman, and they can compete in the same market that the big scrap producers are competing in.”
Overseas demand for containerized scrap is currently particularly high; in Canada, especially on the east coast, this is not going unnoticed. At Acculoader, compared to 2018–2019, Bushong says they have seen about a 200 percent increase in installations over the past year on the east coast of Canada, from Nova Scotia down to the Maine border.
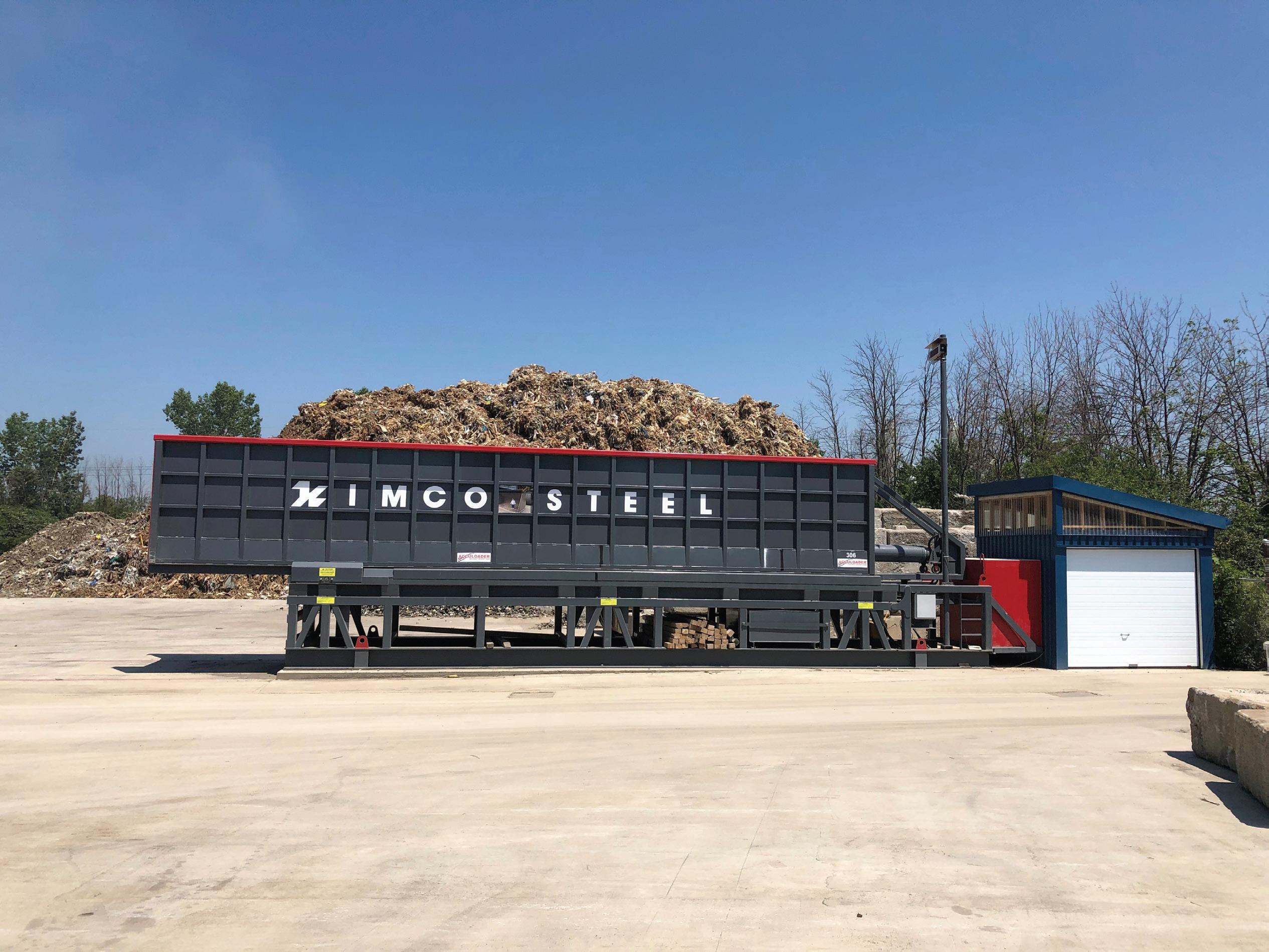
THE ACCULOADER PROCESS
The yard space required for an Acculoader on the ground is about 100 feet by 10 feet wide which allows for a 45-foot loading box and space for a 52-foot tractor trailer combination to back up to it. Users simply place the Acculoader opentop box near the scrap pile where it can be loaded with a material handler. It runs on either diesel or electric power and uses a highly accurate, integrated scale, displaying loaded weight in real time so recyclers can maximize capacities very efficiently. Once full, the Acculoader is inserted into the shipping container.
“We push a couple of buttons and we transfer the load into the container, without damaging the container and without having any personnel near the loading process,” explains Bushong. Once the Acculoader slides inside the container, a hydraulic packer pushes the load in while withdrawing the packer blade. This all happens in as little as 10 minutes. The Acculoader’s reinforced heavy-duty sidewalls absorb all of the impact and wear from loading abrasive materials, protecting the inside of containers, and the full, accurately weighed container load of scrap is ready for transport.
THE CASE FOR KIMCO STEEL
Scrapyards on the east coast of Canada aren’t the only ones currently taking advantage of surging overseas markets for containerized scrap. Kimco Steel Sales Ltd., operating out of Kingston, Ontario, installed their first Acculoader in late March 2020.
According to Kimco founder and owner Gregg Rosen, “Our new Acculoader doesn’t stop. We’ve shipped 400 containers of scrap metal already this year,” he says. “If I didn’t have an Acculoader, I would have had to sell all of my scrap domestically and simply wouldn’t be able to take advantage of the great overseas export market.”
Rosen bought the Acculoader with intent to increase his efficiency exporting non-ferrous materials such as Zorba and Zurik, which he has been doing for many years. The way they did it previously, with skid-steer loaders, was time-consuming, difficult and costly. Plus, they weren’t able to load containers to maximum capacities. Since adding the Acculoader, Rosen finds that he is using it more for ferrous export to meet current market demand from countries including Turkey, India, Bangladesh and UAE.
“I really bought it for non-ferrous and didn’t think that I would ever be using it for ferrous,” he explains. “But the ferrous market for export opened up, better than the domestic market, and I was able to take advantage of it. If I didn’t have an Acculoader, I wouldn’t have been able to do that. I would not have looked at ferrous material for export at all, only non-ferrous.”
Rosen continues, “Greg Bushong handled it from beginning to end in the most professional way I’ve ever seen anybody do it. He spent basically a week here in Kingston, installing our loader and training our men on how to operate the machine. He was a gentleman, extremely professional and did everything he said he would do and more. I give

Greg a lot of credit for what he’s come up with, on the Acculoader design, and in the way he handles his customers.
“We have a diesel-powered generator on ours, so it’s not powered by electricity, and it hasn’t stopped since we got it. I think we have a very nice installation of the Acculoader machine.”
Rosen notes that prior to their new installation, Kimco did have a tilter to load containers – but he never really liked it. “It was not for us. It takes longer. It’s more cumbersome and it’s a lot more dangerous,” he says. “There’s more opportunity for problems. The Acculoader is very simple, and it is an absolutely unbelievable safety improvement because only one guy is involved, and he’s basically hands-off. It’s all remote control: the operator that operates the excavator can operate everything.”
“When I bought the machine, I was happy to do what I was doing before, about 20 containers per month of exported, mostly non-ferrous materials. I would have been happy to have bought the machine and only do 20 containers a month, or about 240 containers a year.
“What used to take us two and a half hours now takes 20 minutes,” he says. “I’ve only had it in operation since April, and from then through September I’ve already done over 400 containers.”
QUICK ROI FOR THE SCRAPYARD
According to Bushong, “Costs have really changed over the years. It’s hard to give exact ROI numbers because it really is a moving target. But what I can say is for yards that are doing 1,000 tons per month or more, the return on the Acculoader is very quick.”
He says they generally calculate ROI for customers based on several factors, including savings from reduced labour costs, loading times and safety incidences, as well as lower maintenance costs and general wear and tear on loaders and containers. Plus, with accurate real-time weighing, loads are maximized every time, which saves a lot of time and money in transport. “Even if you’re a small yard and you’re doing 500 tons, your ROI is going to be about three years,” he says. “That’s great on a big piece of equipment.
“I can’t tell you how many times I get a call back, six months into their ownership, and they tell me ‘I should have done this five years ago.’”
With respect to life expectancy of an Acculoader, Bushong says they haven’t seen one hit its end of life yet. “Ten years into the business, I’ve replaced only three upper boxes. And each of those three customers had put through more than 25,000 to 35,000 containers before we replaced the tops. All we had to do is replace basically the upper half. That’s about 25 percent of the original cost – and that’s it. For life expectancy, I predict 20 years plus.”
He adds, “When the market’s down, it’s the perfect time to buy an Acculoader, because if all things are equal, and you’re getting less money for your product, but you still have the same costs, then it holds true that if you can lower your costs, you make money in a down market.
“It’s really hard for a yard to outproduce the Acculoader,” he concludes. “The current world record is 62 loaded containers in one 10-hour day, with one man.
“In Southern California, I have yards that regularly do 30 containers every day. These are yards that started off doing five containers a week, and they’re able to take their business to 30 a day based on using the Acculoader.
“If you’re loading scrap steel, you should own one of these machines. Period.”

X-Body Equipment, Inc. 6100 Horseshoe Bar Rd., Loomis, CA 95650 Contact: Greg Bushong • 877-464-0056 info@acculoader.net • www.acculoader.net
The Acculoader charge box or loaded hopper is driven into the container via hydraulic cylinder. Once inside the container, a second telescopic cylinder is activated and pushes the material out of the charge box into the container. The charge box is then reversed and exits the container as the telescopic cylinder continues to push forward, emptying all contents into the container.

THE ACCULOADER HIGH SPEED CONTAINER LOADER
• 14.63 m (48 feet) total length • 28,000 kg (62,000 pounds) total weight • 2 minute 30 second full cycle time • 40-hp electric motor or Tier 4 Final diesel engine • Integrated real-time scale with display • AR 400 material on wearable surfaces • Patent No. US 8.662.813