
8 minute read
News Room
STAY CURRENT
www.recyclingproductnews.com
CONNECT WITH US @RecyclingPN
JOHN DEERE AND FORD CREATE CONCEPT GATOR MADE OF RECYCLED MATERIALS
Ford and John Deere have collaborated to produce a new sustainable concept Gator, a machine prototype built in collaboration with Ford Motor Company’s sustainable materials team to examine ways of taking waste streams and turning them into viable machine components. The concept
Gator features sustainable elements such as a hood made of plastic bottles pulled from the Mississippi River and a storage bin made of coconut filler.
“When the idea of the sustainable concept Gator project came about, the goal was to explore a variety of materials to be used for possible adoption across product lines to support our goals around increasing use of sustainable materials,” says
Andy Greenlee, senior staff engineer for sustainable solutions at John Deere.
Greenlee was one of six Deere employees on the team tasked with developing the sustainable concept Gator. While the project presented many challenges, the team worked closely with both Deere and Ford’s network of suppliers to build a prototype created with renewable, recycled, and recyclable materials such as soybeans, flax fibre, sugar cane, hemp fibre, bottles, and fishing nets.
“It was difficult because we had to work within our current framework of production tooling, we weren’t going to invest in new tooling for a product that won’t go to market, but we did everything we could to find sustainable materials that were suitable replacements,” says Keith Shanter, senior materials engineer at John Deere.
“The sustainable concept Gator has provided us with key learnings,” Jill Sanchez, director of sustainability at John Deere says. “It shows how innovative thinking and innovative partnerships provide invaluable insight into how we can apply sustainable material use in the future.”
Though many components used in the sustainable concept
Gator are not a short-term production solution, the materials pave the way for sustainable solutions, including one that is in production now.
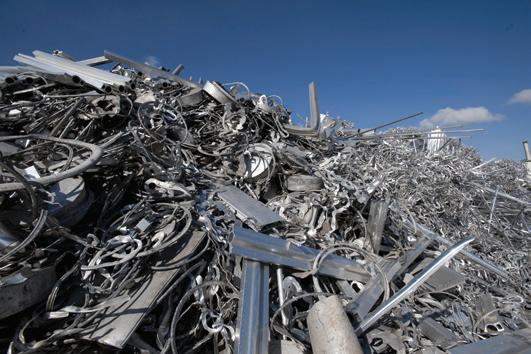
STEEL DYNAMICS TO BUILD AND OPERATE 650,000-TONNE RECYCLED ALUMINUM FLATROLLED MILL MACHINEX PARTNERS WITH RUMPKE TO BUILD DEDICATED RESIDENTIAL SINGLE-STREAM SYSTEM
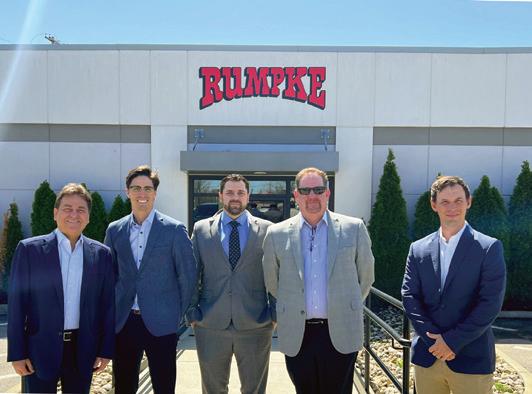
Steel Dynamics will construct and operate a 650,000-tonne low-carbon, recycled aluminum flat rolled mill with two supporting satellite recycled aluminum slab centres. The investment is estimated to be $2.2 billion for the three facilities, and commercial production is planned to begin in the first quarter of 2025.
The planned $1.9 billion aluminum flat-rolled mill will be located in the Southeastern United States, with an annual production capacity of 650,000 tonnes of finished products, serving the sustainable beverage packaging, automotive, and common alloy industrial sectors. The product offering will be supported by various value-added finishing lines, including continuous annealing solutions, heat treating lines, continuous coating, and various slitting and packaging operations.
The company’s focus on decarbonization will also be applied to this aluminum operation, including plans to use a significant amount of pre- and post-consumer aluminum scrap in its production process, supported by the company’s metals recycling platform. The company will own over 94 percent of the rolling mill facility through a joint venture arrangement with Unity Aluminum.
At full capacity, the aluminum rolling mill will require approximately 900,000 tonnes of annual aluminum slab supply. The rolling mill is expected to have the capacity to supply approximately 50 percent of its recycled aluminum slab requirements on site, with the remaining amount to be provided by the construction and operation of two additional satellite recycled aluminum slab centres, one to be located in the Southwestern United States and the other in Northcentral Mexico. The satellite slab centres will benefit from abundant regional aluminum scrap supply and cost-effective operations. The two facilities are expected to cost approximately $350 million in aggregate, with the Mexico facility expected to begin operations in 2024 and the U.S. facility by the end of 2025. The company will own 100 percent of the satellite facilities. Machinex has launched a new project with long-time partner Rumpke Waste & Recycling that includes the delivery of a brand new 56-tph residential single- stream system in Columbus, Ohio. The new material recovery facility will be one of the largest dedicated residential single-stream systems in the country.
Rumpke’s facility will not only feature advanced technology, but will also host a research centre for college students as well as an educational area to raise awareness and consciousness about the environment.
The system, entirely designed and equipped by Machinex, will efficiently sort all recyclable materials, including papers, cardboard, HDPE, PET, PP, and mixed plastics coming from local residential and commercial curbside collection. Achieving effective sorting of all these materials while maximizing purity rates, interconnectivity, and high-tech equipment were the driving requirements for the design of the system for Rumpke.
This 160,000-tons-per-year MRF will include several types of sorting equipment, with a focus on high automation to maximize recovery. The system will be equipped with 18 MACH Hyspec optical sorters for fibres, non fibres, and plastics sorting, along with three SamurAI sorting robots on the container lines for quality control. The automation will drastically increase material recovery and purity without extra workers.
According to Chris Hawn, Machinex Technologies’ CEO,
“Working with Rumpke and their team has always been a pleasure. Going into large projects such as this, it is important that any buyer complete due diligence to understand market changes and the equipment necessary to tackle past, present, and future challenges. We were fortunate enough to remain Rumpke’s selected vendor and with the level of automation provided, they are prepared to handle what the future might bring.”
“Rumpke’s commitment to recycling dates back nearly 90 years . . . by working with Machinex to develop the Rumpke
Recycling & Resource Center in Columbus, Ohio, we remain confident that we can continue delivering the best recycling solutions to our customers for years to come,” said Jeffrey Snyder, director of recycling at Rumpke Waste & Recycling.
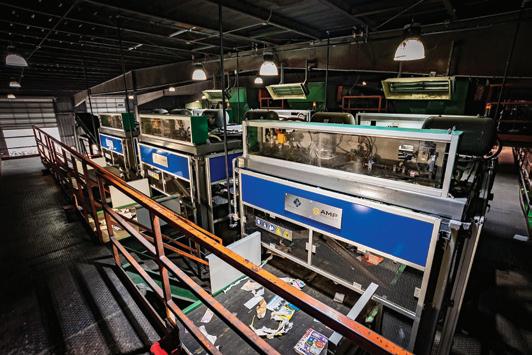
packaging types reclaimed for raw material processing. For example, AMP recovers a portfolio of #1 to #7 plastics in a variety of different form factors, colours, and opacities with high precision and purity.
PET and HDPE together account for a majority of recycled plastic demand, with growing interest in polypropylene – a highly recyclable polymer with demand in food-safe applications and flexibility to accommodate packaging in a variety of shapes and sizes. The ability to precisely separate different plastics and other recyclables with AI-driven sorting is helping recyclers meet the need for sufficient quantities of high-quality recycled content from brands and packaging producers.
AMP ROBOTICS AND WASTE CONNECTIONS EXPAND RECYCLING TECHNOLOGY PARTNERSHIP
AMP Robotics has expanded its partnership with Waste Connections. Since late 2020, Waste Connections has booked or deployed 50 of AMP’s high-speed robotics systems on plastic, fibre, and residue lines.
AMP’s technology identifies and recovers plastics, cardboard, paper, cans, cartons, and many other containers and
FULLY RECYCLABLE PEF FIBRE BEER BOTTLE TO BEGIN PILOT TRIAL
In the company’s largest pilot to date, Carlsberg Group has initiated the trial of its new fibre bottle. The bottle is a biobased, fully recyclable beer bottle and will contain beer brewed with organic and regenerative barley.
The bottle is 100 percent bio-based apart from the cap, which is currently needed to ensure the quality of the product, and together the bottle and cap are fully recyclable. Going forward, the company is exploring alternative fibre-based bottle
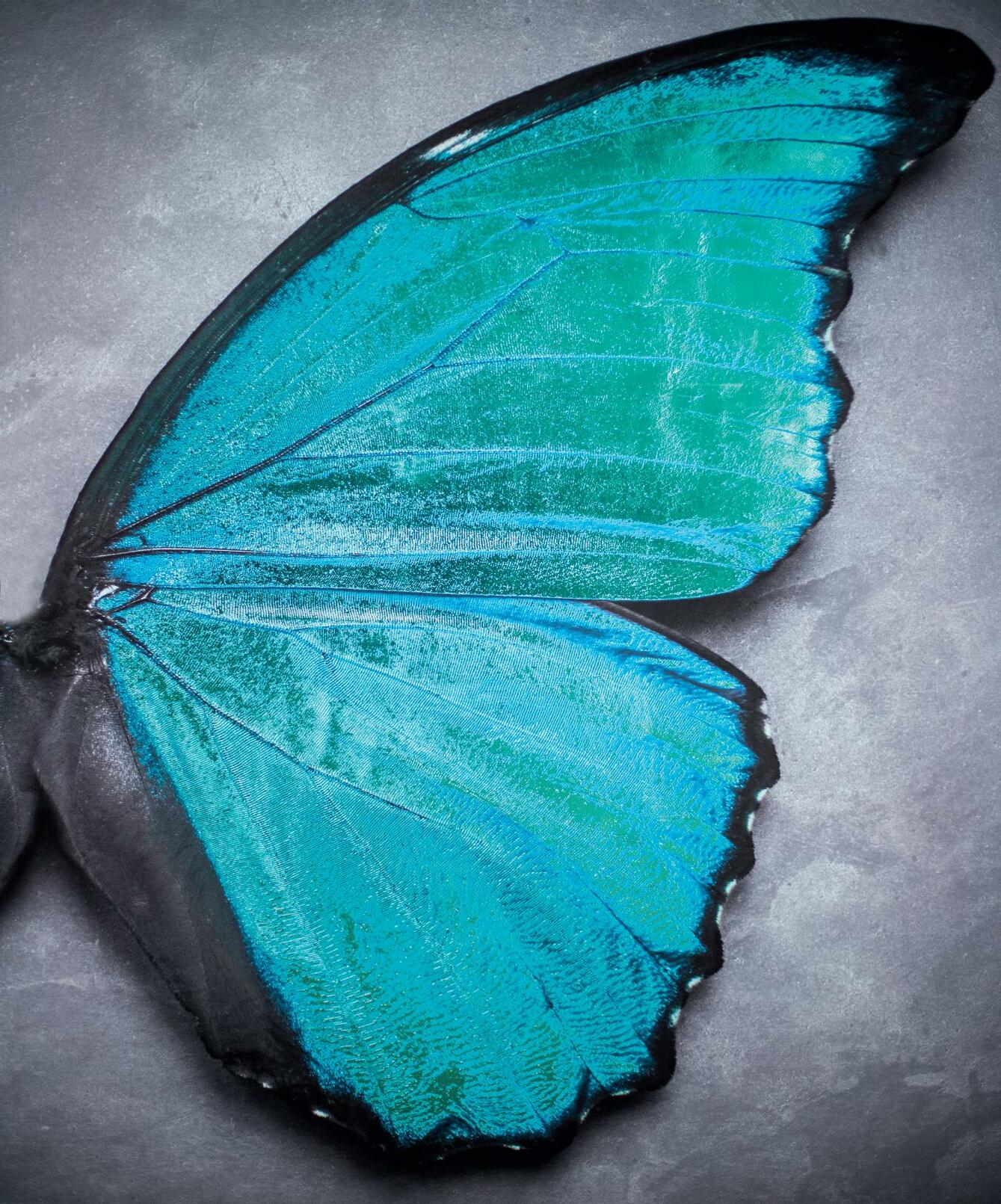
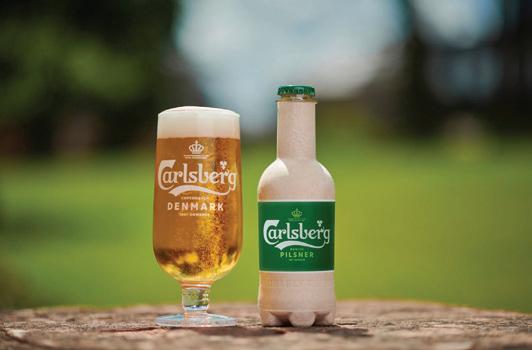
caps, with a generic solution expected in 2023.
According to Carlsberg, the fibre beer bottle already performs better than the single-use glass bottle in the product’s life cycle assessment. Carlsberg aims for the fibre beer bottle to achieve up to 80 percent less emissions than current single-use glass bottles.
With that goal, for every single-use glass bottle created, five fibre beer bottles could be created using the same carbon footprint. Ultimately, Carlsberg aims for the fibre bottle to achieve the same low carbon footprint as a refillable glass bottle, which is currently one of the best-performing primary types of packaging when collected and reused in efficient systems.
DS SMITH REMOVES 313 MILLION PIECES OF PLASTICS FROM PACKAGING IN TWO YEARS
DS Smith consumers have asked for packaging to replace single-use, unrecyclable plastic items. DS Smith responded and designed out over 313 million pieces of problem plastics in the last two years alone as part of its plastic replacement program. DS Smith’s designers have worked with clients on their packaging and displays to replace or remove more than three million units of plastic per week, or 13,000 an hour, as consumers demonstrate a demand for fibre-based packaging as an alternative to hard-to-recycle, single-use plastics. DS Smith’s designers have created thousands of designs to eliminate even the smallest amounts of plastic in its packaging, such as replacing plastic sealing tape with self-locking cardboard flaps and swapping plastic labels by printing directly onto cardboard. Over the next year, DS Smith will continue to drive the adoption of fibre-based alternatives in response to consumer demand for plastic alternatives.
MORE NEWS
www.recyclingproductnews.com
WASTE PROCESSING
MADE EASY
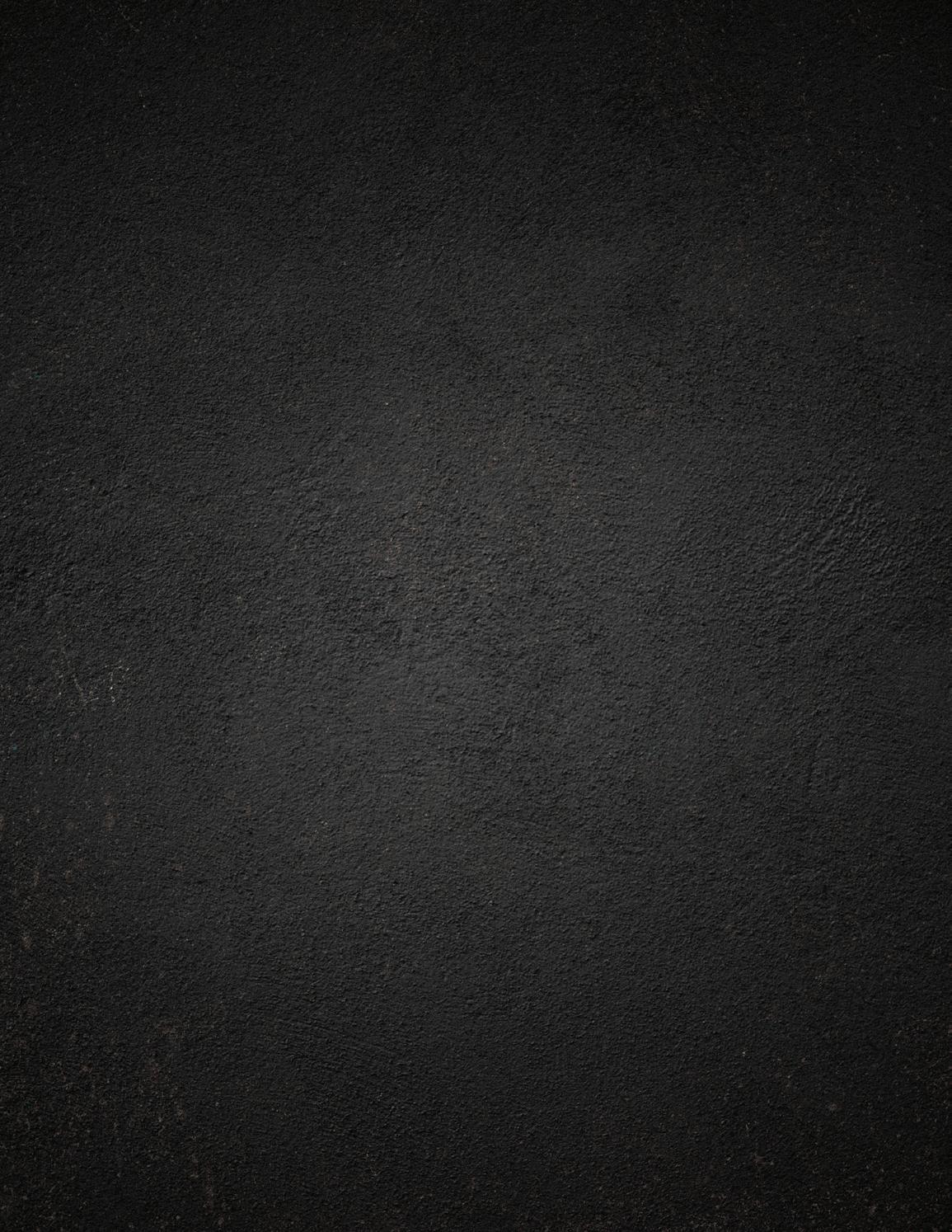
ELV Select Equipment is the authorized North American Distributor for Ecohog Waste Processing Equipment. There is a machine for a variety of waste applications, including: C&D, Compost, Scrap Metal and Biomass.
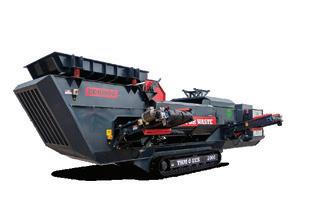
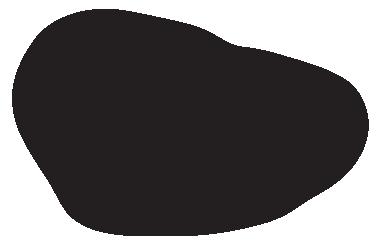
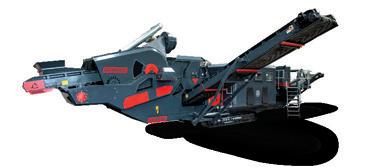
ECOHOG HOGMAG

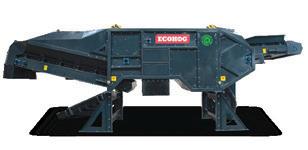
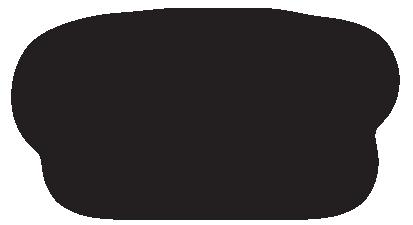
TRACKED EDDY CURRENT SEPARATOR
ECOHOG WINDSHIFTER
STATIC AIR SEPARATOR
ECOHOG RECON-Q
MOBILE SCRAP RECOVERY DOWNSTREAM
NORTH AMERICAN MASTER DISTRIBUTOR
elvselect.com | +1-866-733-2358 | sales@elvselect.com