
17 minute read
A ROBOTIC FUTURE FOR RECYCLING
Machinex’ Matthew Smith with a newly installed SamurAI sorting robot, charged with processing waste and recyclables 28 Recycling Product News September 2020 at the Hong Kong airport.
MACHINEX SALES ENGINEER MATTHEW SMITH PROVIDES INSIGHT ON THE LATEST ARTIFICIALLY INTELLIGENT ROBOTIC SORTERS AND HOW TO OPTIMIZE THEIR EFFICIENCY AT THE MRF
BY KEITH BARKER, EDITOR
Artificially intelligent, highspeed robotic sorters are now commonly considered to be the future of largescale recycling. They are one of many technology-based options that can help recyclers adapt to both changing practices in our industry, and changing commodities markets worldwide. Currently, there are only a handful of manufacturers of robotic sorting systems for recycling applications, with available machines offering as much as 70 picks per minute (on a recovered fibre or plastics line in a MRF or other recycling facility). Robotic sorters use the latest optical vision technology, learn as they go with artificial intelligence, and can recognize and sort (either positively or for quality control) a wide range of plastics, cartons and paper, including film, and in some cases hard-to-detect black plastics.
The cost-efficiency and safety benefits of automated pickers as an addition to, or replacement for, human pickers is catching on. Every month, more and more recycling facilities and MRFs around the world are adopting these high-tech systems into their plants, all with the goal of maintaining and increasing profitability in especially challenging times.

CANADIAN-BUILT ROBOTS
Born from roots in the agriculture industry Machinex, the Plessisville, Quebec-based MRF and turnkey recycling systems provider, is 50 years old in 2020. Machinex is the only large-scale manufacturer of optical and robotic sorting technology for recycling in Canada and currently offers two robotic sorter models. The SamurAI 800 series is tailored toward a wider belt and the smaller SamurAI 650 model is ideal for anywhere with tighter space constraints for installation or operation.
According to Machinex Technology Sales Engineer Matthew Smith, the 800 model is primarily targeted at the North American market, while the compact 650 model (which fits pre-assembled in a single container for shipping) is more geared for the European market.
“Normally, in Europe, the sorting line is in an enclosure, with conveyors that are about one metre wide, so based on the enclosure restrictions you need a smaller robot,” explains Smith. He adds that wherever it is located, the Machinex’ SamurAI robotic sorter is particularly ideal for paper, plastics and aluminum recyclers looking to purify their streams and reduce output contamination.
THE ROBOTIC SORTER AT WORK
The SamurAI robotic sorter is taught to recognize various materials via its camera and its AI (artificial intelligence.) Smith explains that different materials are labelled according to their size, shape and composition, and then loaded into the AI of the robot. Based on this information the robot recognizes various materials.
Key features of the SamuraAI include its unique multi cyclone vacuum system and its ability to positively pick and remove plastic film from a line. Other robotic sorters on the market currently use compressed air to induce their vacuum.
“The way our system uses a blower to induce a vacuum works similar to a multi-cyclone,” explains Smith. “Many would know this concept from Dyson vacuum cleaners. It’s a similar principle to that. Our system sucks the objects through the tubing into the multi cyclone, which causes the heavy material to go to the sides and then drop down. The clean air exits, and thus efficiently removes film from the line.”
THE RECIPE FOR SUCCESS
In today’s MRF, materials can be sorted for quality control (picking out what should not be in a stream) or positively sorted (picking out the desired material for capture).
“We can pick all different types of plastics, cartons, film or aluminum,” explains Smith. We can do a positive sort or we can do quality control.
“We’ve got some robots doing the QC sorting on different plastics. They’re removing unwanted materials and purifying the plastics stream. We’ve also got one that’s processing aluminum cans, doing QC on an aluminum line. It’s picking anything that is not an aluminum can and removing it to get a purer stream; this is quality control.”
He continues by describing positive sorting. “If you’ve got a stream with many different types of material, and you’re going for natural HDPE, you can target and pick out this material first, resulting in a very pure stream of that material. We can also positively sort a second material. So, if the robot is programmed for natural HDPE, but
Machinex’ SamurAI robotic sorter at the Pratt Recycling MRF, Atlanta, installed spring 2020.

doesn’t see any, a second priority can be set, such as coloured HDPE, and it will automatically pick the second material on its list and place it in the desired chute.”
Currently, positive sorting of plastics in North America focuses largely on HDPE or PET. The SamurAI will also sort PP (polypropylene tubs and lids), but Smith says this choice would depend on the market. Recyclers currently are getting a better price on HDPE than they do for PP.
“We create different recipes according to customers’ needs. The type of material a robot is programmed to pick at a given facility is best determined based on the market prices of certain materials.
“Natural HDPE is currently the highest priced recovered plastic, so if a facility is picking both HDPE and PET, they may not want to set the robot at a recipe to pick 50:50.
“If the market dictates, and there is enough material, it might be better to pick 70:30 (natural HDPE:PET). The SamurAI would then be programmed to pick 70 percent of the natural HDPE from the line and only 30 percent of the PET. This way, recyclers will get a better return than if they were to pick at a rate of 50:50.”
ALLEVIATING LABOUR CHALLENGES
Currently at most MRFs, there’s a policy in effect for keeping a 2-metre distance between colleagues.
“It’s about making sure that you can actually get the staff in to do the job and have enough space to do it.” Smith says that normally a robot can do 70 picks per minute, while an average person does 35 to 40 picks a minute. “With
one robot, you’ve almost doubled your manpower.” It also helps avoid the risk of having employees in close quarters, inside a dusty, very-hard-to-sanitize environment.
Smith agrees that the industry has been moving toward increased automation for decades now, and that in the future it’s going to become almost completely automated.
“A recycler can get $75 per ton for a certain quality or purity, or spend a little bit more money to automate and produce very pure output. Then the return can go up to $120 per ton. That is a huge impact.”
He also agrees that levels of purity demanded by the market for MRF output are challenging for current systems to achieve.
“You need a high level of quality control. To do that with a person who has a limited pick rate, you then have to employ two people to do the job. With a robot, maybe you only need one. And they’re just going to get faster and more efficient. The current status is that our robots are doing 70 picks per minute. In a year, we might be up to 80 or 85 picks per minute. This could be done with the same equipment bought today. It’s just a case of software upgrades and programming in better recognition.
According to Smith, with 80 to 85 picks per minute, you’re definitely replacing two people. “The robot doesn’t need a break and maybe it works two shifts. Social distancing in the workplace could be around for some period of time. In this scenario, one robot can potentially free up two people to work in other areas of the MRF where manpower is now needed.”
KEEPING UP WITH AN EVOLVING STREAM
A unique feature of SamurAI robots is that they are connected to the MACH Cloud, through which Machinex updates the system on an ongoing basis. MACH Cloud is offered free for the first year, and then it’s cost is based on a subscription.
“With this system, any new developments made in regards to improvements in the software (adding better recognition capability for example, or programming in new types of materials to be recognized, or different flight paths that the robot takes toward the bin) can be updated simultaneously, for all new users and subscribers, wherever they are located.
“For new packaging materials entering the market, the robot won’t recognize it until it is programmed in,” continues Smith. “You could have a recycler in Quebec who notices something new. We teach their robot about the new item, generate all the data, and then through MACH Cloud, everyone that is signed up receives the new data. As part of the MACH cloud, all our customers benefit off each other.”
TIRES IN 00:00:35

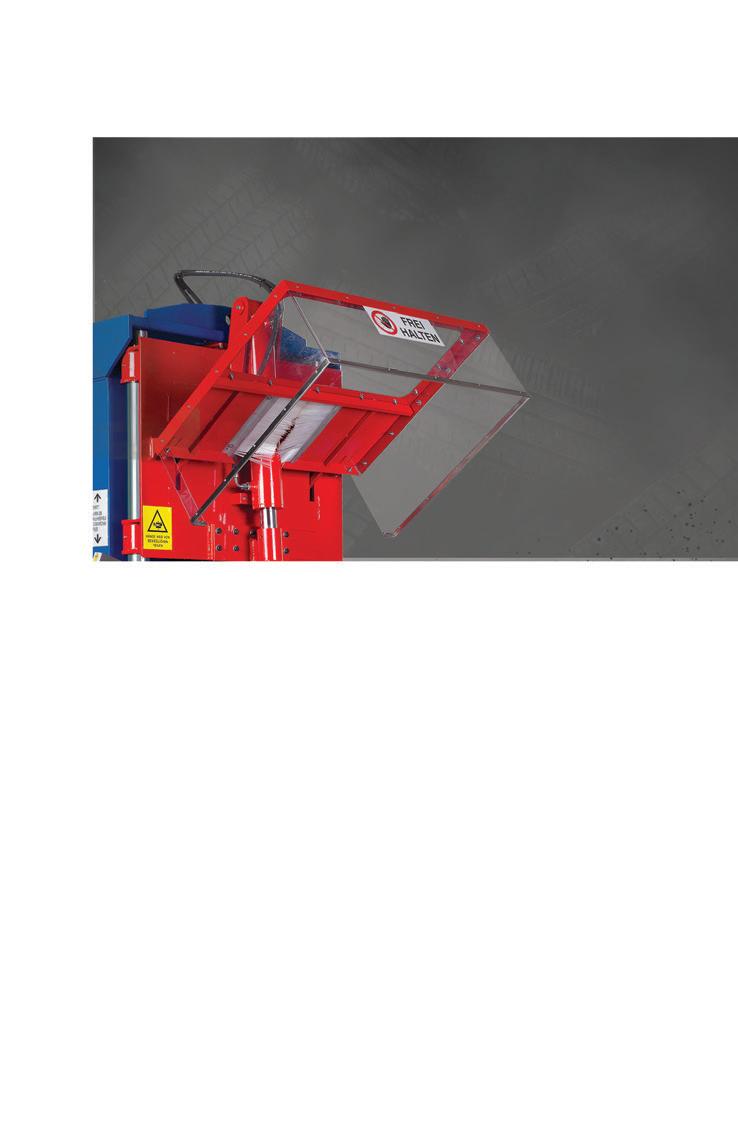

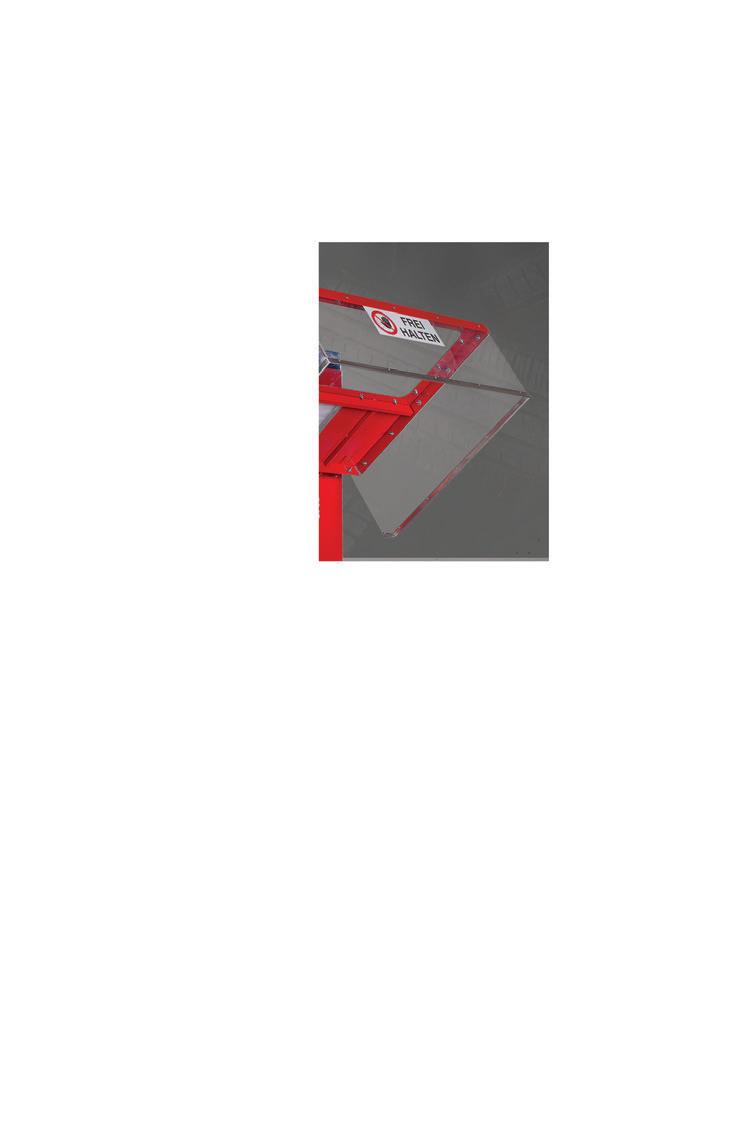

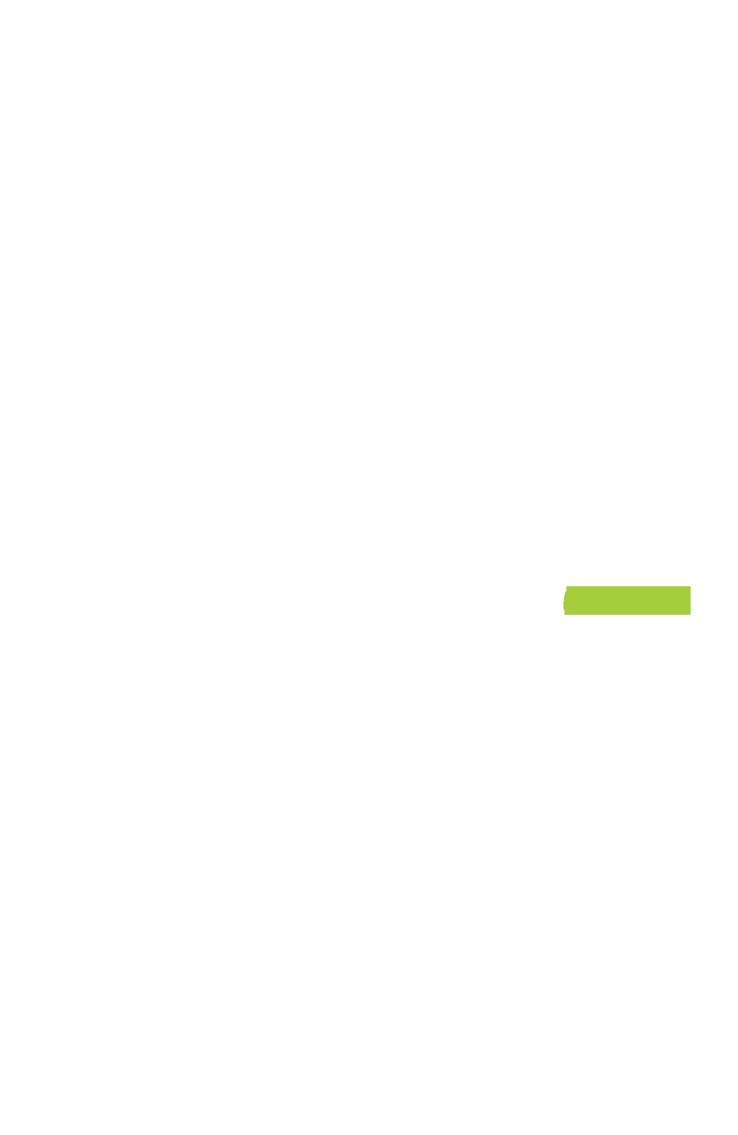
FINANCING THE ROBOT
For most MRFs and other recycling facilities, an automated robotic sorting unit is an add-on piece of equipment. “It’s not like you’re building a complete new MRF from scratch, which costs millions, but it is a big investment,” says Smith. “For those with an existing MRF, generally they are adding a robot to their system. The opportunity to find the capex [capital expenditure] in the current market can be really tough. There’s also the fact that the value of the end material being sold is down compared to what it used to be. So, for MRF owners to go out and get that capital investment to invest in a robot can often be difficult.”
Machinex now offers leasing options for their robots to help make the technology viable for more recyclers. “To add a robotic sorter to a MRF using a leasing program and spread the cost out to three, four or five years, can be really beneficial,” he says. “The expenditure per month is based on a fixed rate, so there’s no big surprises.”
Smith agrees that leasing is an interesting, newer strategy which may well extend to other types of equipment in the near future and become a more regular way of doing business in the recycling industry. “Many big companies can just go ahead and buy what they need. But other ones, maybe a smaller MRF, or small privately owned facility, it’s a really good option to go for a leasing program.
“It’s also a case-by-case situation,” he continues. “One MRF might want to lease just the robot, but immediately pay off the costs for installation and any upgrade to their structure. When it comes to that, we’re flexible. It all depends on what the customer requires.”
When asked if Machinex is working on any new recycling equipment that will incorporate AI, Smith says Machinex now offers a vision system that was first installed this past spring in a U.S. facility operating their equipment. This unique device is powered by AI and uses a combination of a hyperspectral infrared camera and a high-definition RGB camera to identify and label items on the belt into material categoMachinex’ SamurAI artificially intelligent sorting robot uses a vacuum system induced by a blower to capture and purify fibre, plastics, aluminum and film.
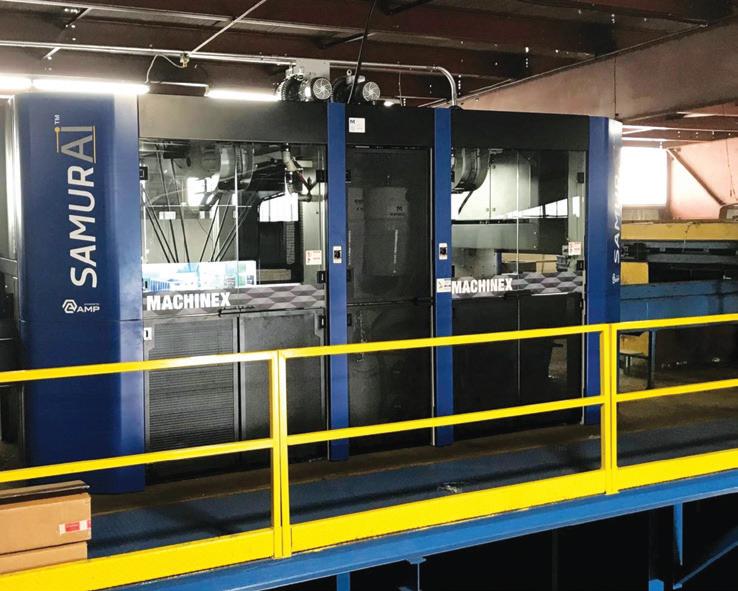
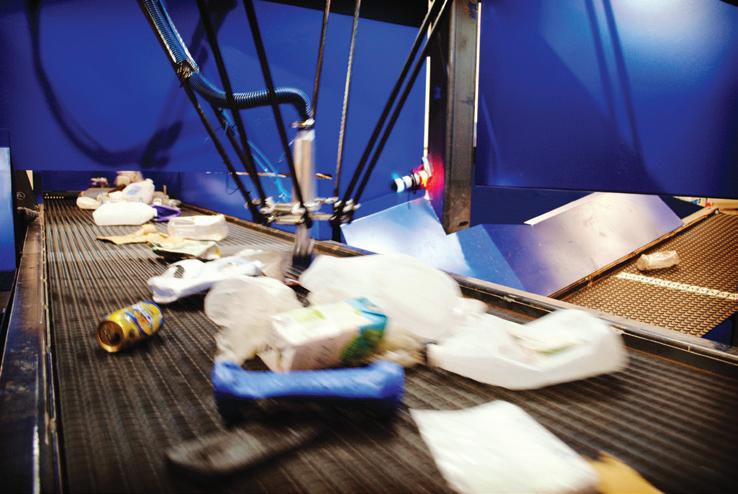
ries. The unit will ultimately generate real-time information in regards to the stream composition.
Smith concludes by emphasizing, “We’re not just a robot manufacturer here at Machinex. We understand the whole process of recycling. We see the robot as a unique piece of equipment, but we can also see the start and the end of the entire recycling process. We make sure a robot, as a piece of specialized equipment, is integrated in with the rest of the equipment in a MRF or other recycling facility. If needed, we’re also going to tune a facility’s optics or ballistics.
“We can change a lot to best suit the robot, so we get the very best out of the MRF.” RPN
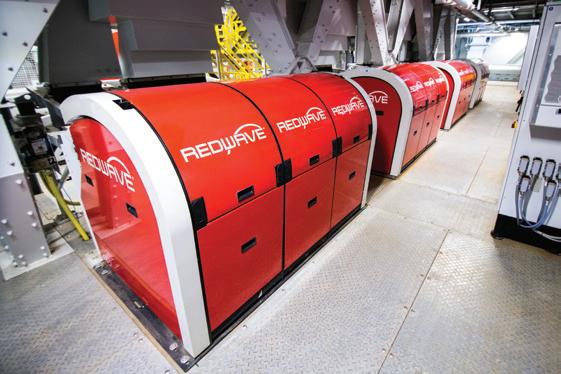
New REDWAVE sensor improves detection of dark scrap glass by more than 50 percent
According to REDWAVE, until now the glass sorting process in recycling facilities has caused a significant loss of good cullet, especially into the CSP reject stream (ceramics, stone and porcelain) with glass content of up to 90 percent. The company points to the reason for significant loss in glass as being the result of outdated sorting techniques and low transmission value, whereby dark and thick glass pieces cannot be distinguished from CSP and are ejected along with the CSP by optical sorters. This results in lower output rates and increased disposal costs for the CSP reject stream due to the higher volume.
To meet the need for improved glass sorting in recycling facilities, REDWAVE has, through continuous research and development of its glass sorting sensors and software, introduced the new REDWAVE CX. The Austria-based manufacturer says this sensor-based (optical) sorting machine for the glass recycling industry is the next generation of intelligent glass sorting and uses enhanced recognition technology for dark glass. With their new technology, the company says detection of dark glass can be improved by more than 50 percent, with no losses when it comes to semi-coloured glass or thin porcelain. REDWAVE’s new sensor and software can easily be upgraded, thus eliminating costs on facility extensions and avoiding the need to purchase additional sorting machines.
COM P A C T P O WER
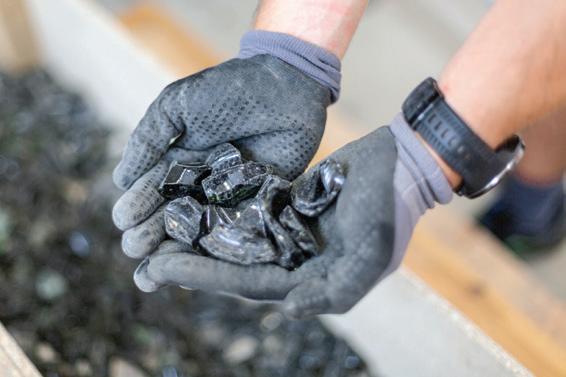
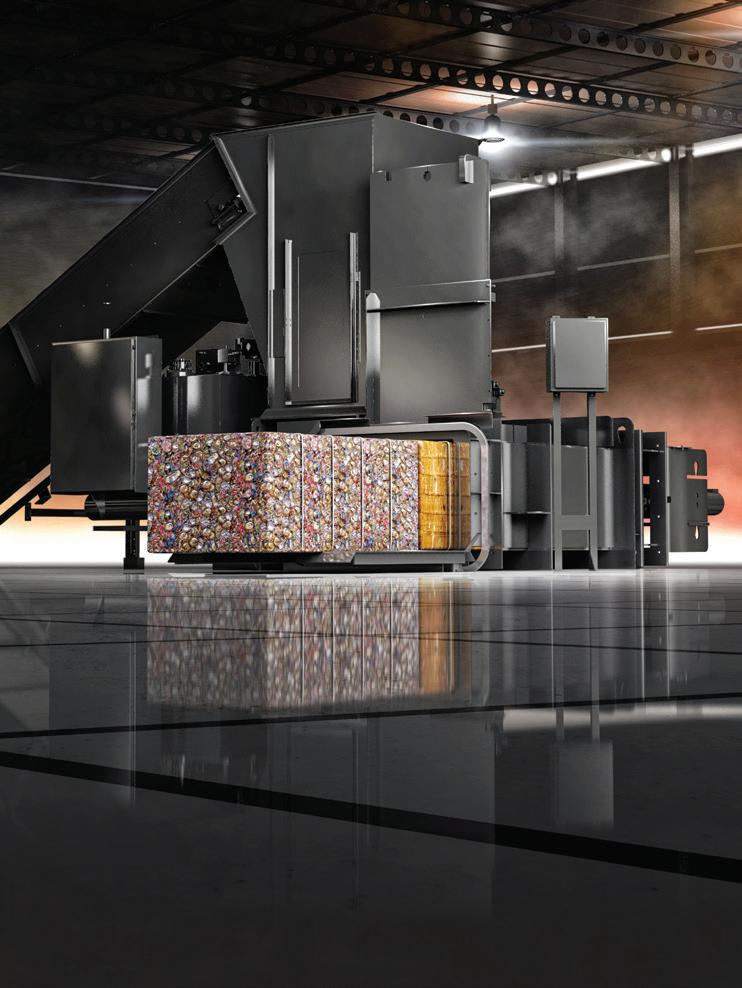

TWO-RAM ON A HORIZONTAL BUDGET VERTICAL BALE DOOR AVAILABLE IDEAL FOR MULTI-MATERIAL FACILITIES
AMERICAN BALER TAKES PERFORMANCE TO NEW HEIGHTS!
I N T E G R I TY
I
Q U A L I TY
I
R E L I A B I L I TY
I
VA L U E
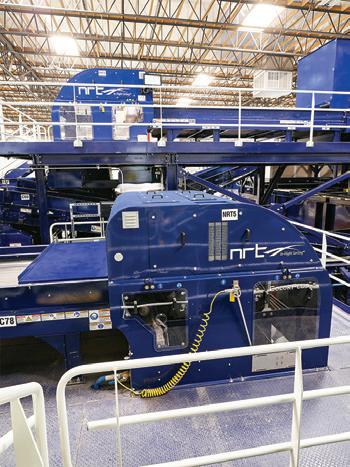
NRT COLORPLUS INTEGRATES AI INTO ESTABLISHED SORTING TECHNOLOGY The newly released ColorPlus with Max-AI we continue to integrate Max into more from National Recovery Technologies of our equipment and intelligent system (NRT) integrates artificial intelligence (AI) controls. NRT optical sorters are the into the company’s successful ColorPlus best in the world at identifying material sorter, which employs a high-resolution at very high confidence levels by colour RGB colour line-scan sensor to identify or material composition, but sometimes and sort recyclables by colour. Max-AI the most effective sort requires the type technology, launched by NRT parent of characterization that a person can company Bulk Handling Systems (BHS) make – that’s where Max comes in. in 2017, employs a camera and deepCardboard isn’t always brown and a clear learning-based AI to identify recyclables PET container isn’t always desired in the similar to the way a person does, and end product. The ColorPlus with Max-AI is is already at work in more than 100 going to solve a lot of sorting challenges installations worldwide. BHS says for our customers and we are thrilled to while most of these installations use introduce it to them,” Miller concluded. the technology in collaboration with The first ColorPlus with Max-AI is robotic sorters, the Max-AI VIS (Visual installed in a European paper recycling combination of proven colour detection Identification System) can also be facility to purify the fibre stream by and the added layer of AI ensures the installed as stand-alone equipment. removing non-paper fibre. In this case, ultimate removal of non-spec fibre. “From the beginning we realized Max Max-AI technology identifies material by Additionally, the technology has the was a game changer, not just for robotic type (such as pizza box, cereal box, OCC, flexibility to change what material types sorters, but really for the industry on a craft board, book, etc.), and the ColorPlus are targeted, allowing the customer to system-wide level,” said BHS CEO Steve technology is tuned to aggressively adjust along with market and material Miller. “This is another step forward as detect brown fibre. According to NRT, the fluctuations.
AUTOSORT CYBOT COMBINES FOUR TECHNOLOGIES
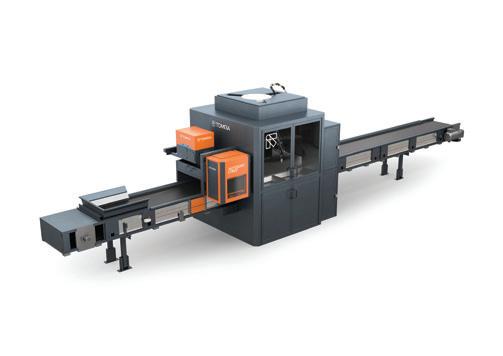
TOMRA’s newly introduced AUTOSORT CYBOT combines four technologies: Near Infrared (NIR) and Visible Light (VIS) spectroscopy, DEEP LAISER, and induction for ferrous and non-ferrous metals recovery.
According to TOMRA, it is the first robot on the market that combines those four technologies at once. AUTOSORT CYBOT’s robotic arm is capable of simultaneously sorting material into four different streams or fractions depending on the infeed material size, colour and criteria of the target fractions.
According to Valerio Sama, VP and head of product management for TOMRA Sorting Recycling, “The addition of a robot arm to our AUTOSORT system opens up a wealth of new opportunities for highly automated applications within the sorting process and will deliver an even higher level of quality control of recyclables such as HDPE, PET and PP.”
LATEST SESOTEC OPTICAL SORTING SYSTEM PROVIDES HIGH-LEVEL ACCURACY

The VARISORT+ optical sorting system for plastic bottles and trays separates plastic types, colours and shapes, as well as metals and foreign objects. According to Sesotec, this technology provides high-level accuracy and reliability, even when working at a material throughput of up to 8 tph.
This new VARISORT+ has been optimized for reliable system availability, quick cleaning and easy maintenance. A rejection accuracy of up to 99 percent ensures that sorting fractions achieve the highest degrees of purity.
Another advantage of the VARISORT+ system is its flexibility, allowing for the combination of up to three sensors (N = near infrared, C = colour/form, M = metal). The optical sorting system can also be equipped with innovative new FLASH technology for optimal colour recognition, which can even detect bottles made with additives. Retroactive sensor upgrades are available at any time and the optional tri-shaft construction enables simultaneous sorting into three material fractions.
BOLLEGRAAF’S ROBB-AQC ROBOTIC SORTER FIRST TO COMBINE NIR AND AI-POWERED LEARNING Introduced at the beginning of 2020, with very minimal retrofit costs and the Bollegraaf AI-powered RoBB-AQC is minimal downtime. Material selection the first sorting robot to combine the only requires the touch of a button, and accuracy of NIR (near-infrared) detection ranges from PET, HDPE, LDPE, PS and PP with the adaptability of AI-powered to Tetra Pak, OCC or paper/cardboard of learning, according to Van Dyk Reycling various shapes and sizes. Solutions, North American distributor and product support for Bollegraaf equipment. The fully automatic AI-powered RoBBAQC is ideal for use as a final quality control step on a container line, and one OUR RoBB unit will recover up to 70 picks per minute, considered to be equivalent to rates from two average human sorters. STRENGTH IS IN OUR
The new RoBB-AQC system is designed STRUCTURE with flexibility in mind, as it can be placed on top of existing sort lines
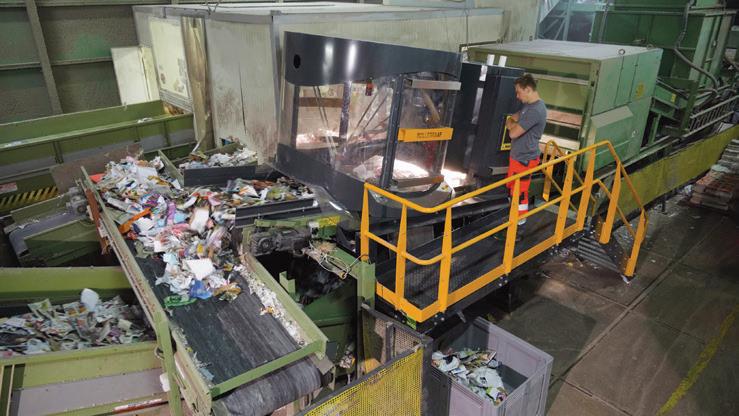
ABB IS USING ROBOTS TO RECYCLE ROBOTS, MAKING MANUFACTURING MORE SUSTAINABLE
ABB aims to create more environmentally friendly manufacturing facilities across the world by enabling existing robot users to sell inactive or legacy robots to ABB with a buyback service, rather than scrapping them or leaving them unused.
Over the last 25 years, thousands of robots have been refurbished and upgraded by ABB’s remanufactured robot teams to give them a second life. As well as previously owned robots, peripheral equipment such as controllers and manipulators are refurbished to like-new conditions at one of ABB’s Global Remanufacture & Workshop Repair Centers.
Before being labelled as an ABBcertified remanufactured robot, every second-hand unit undergoes rigorous checks, including a detailed inspection and a minimum 16-hour functioning test. Each remanufactured robot comes with a two-year warranty and comes with the same level of support from local service teams as they would with the purchase of a new ABB robot.
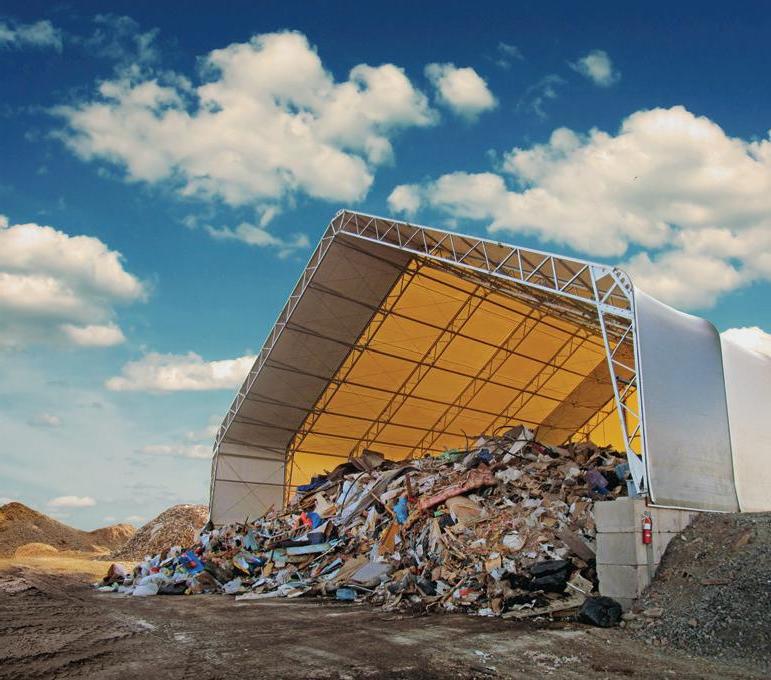
The Bidding is Done.
Calhoun’s new Sourcewell Co-Op Contract puts your new fabric structure on the ground faster. This means the bid process has already been satisfied so you can receive price quotes with ceiling-based pricing, and continue to rely on Calhoun’s local dealer network for installation and support.
Let’s get started.
calhounsuperstructure.com/sourcewell 1-844-873-3338