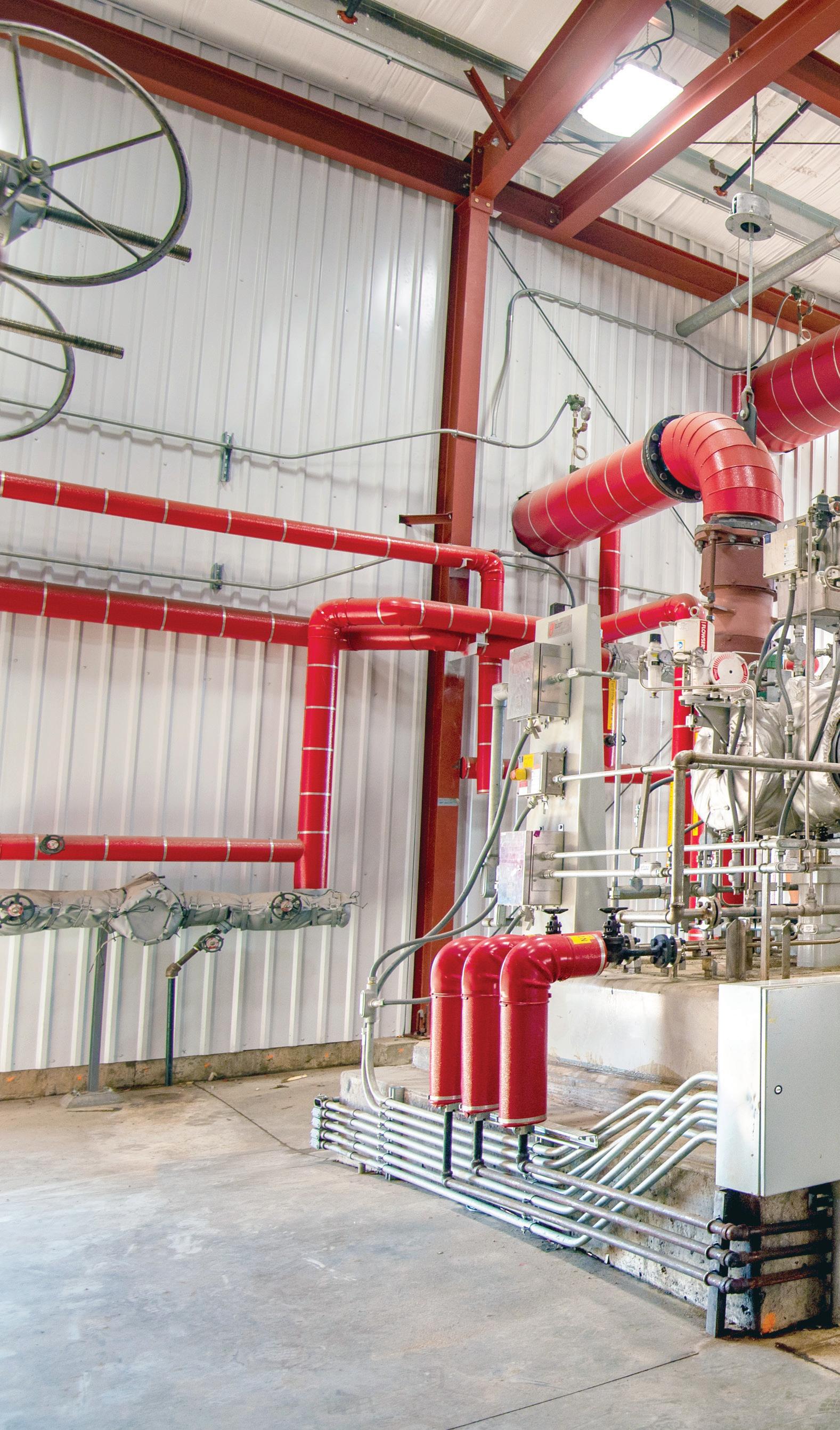
9 minute read
ENERGY
Revisiting CHP
Carbon reduction incentives are improving the cogeneration payback equation for ethanol plants, but only a fraction of producers are doing it. By Susanne Retka Schill
Today, the quest for carbon intensity reduction has plants revisiting combined heat and power (CHP) systems. Siouxland Ethanol in Jackson, Nebraska, recently began generating its own electricity with a
CHP system. Much of the payback will come in a lowered carbon intensity score in the California market. When The Andersons doubled capacity at its Albion, Michigan, facility a few years ago, it installed CHP partly to ensure it could maintain the greenhouse gas reduction target required in the U.S. EPA’s efficient producer program.
CHP has been an option for ethanol producers since the early days. But while all plants could utilize the energy efficient systems, cogeneration has been installed in only a fraction. A U.S. DOE database shows 37 ethanol producers with CHP— combustion turbines, boiler/steam tur-
POWER PLAY: Poet, the largest U.S. ethanol producer, has installed natural gas-fired turbines like this one at several of its facilities. Along with steam let-down turbines, the cogeneration systems are generating a combined 100 MW-plus of electricity throughout Poet's fleet.
PHOTO: POET
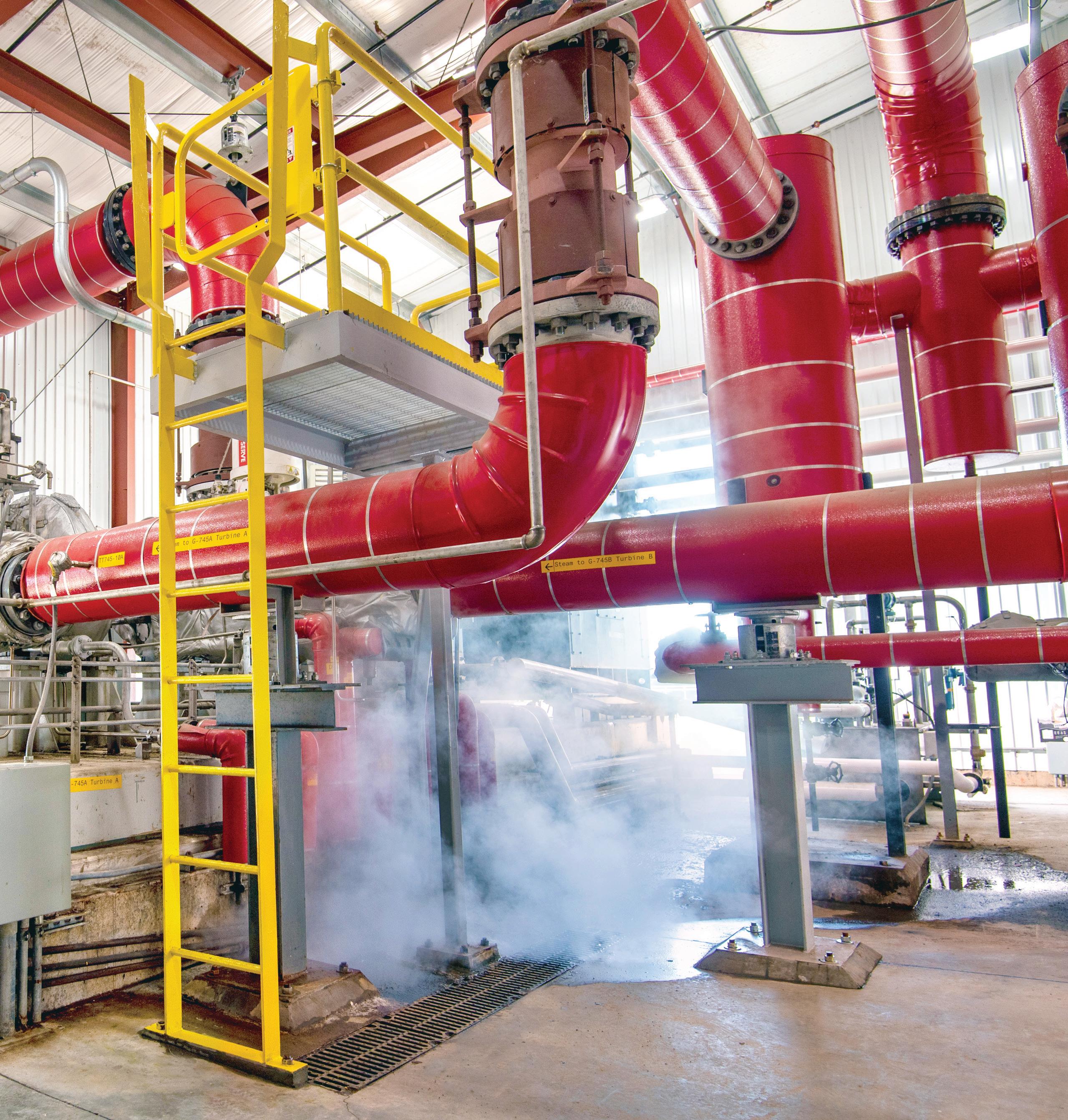
bines and back pressure steam turbines. With a combined capacity of 184.6 megawatts (MW).
Adkins Energy is one of a handful of plants that installed CHP when first built in 2002. Plant Manager Jason Townsend says electrical rates in the region at the time made generating the plant’s own electricity an economic decision. The rationale for CHP has changed over the years. “For a time, we were watching the electric market and turning the turbine off and on based on electrical pricing,” he says. “For the past several years, we’ve been running it 100% of the time. Part of that is electrical reliability. We would have had quite a few power outages if we had relied upon the grid.” Adding the steam from the natural gas turbine to the supply coming from the boilers also enabled running the plant at full capacity.
As the facility expanded to 60 MMgy and added another dryer, the increased electrical load led Adkins to install a second turbine that generates power from the high pressure steam coming off the evaporators that needs to be reduced for use elsewhere in the process. Rather than wasting the energy as the steam passes over a pressure reducing valve, it now generates electricity in a let-down or back-pressure steam turbine. “We’re able to generate a little over a megawatt of electricity now for very low cost,” Townsend says.
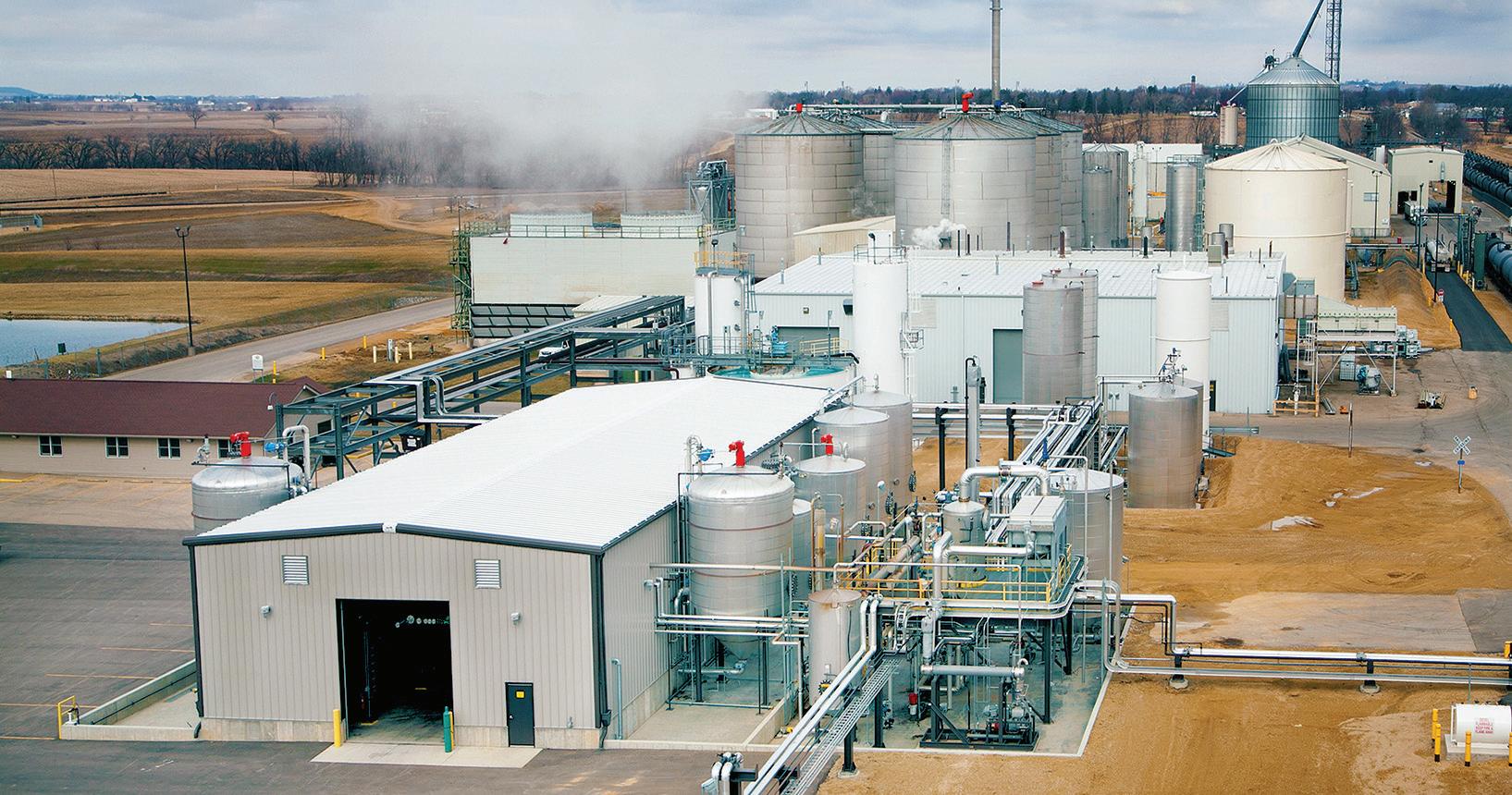
CHP PIONEER: Adkins Energy LLC, in Lena, Illinois, installed CHP when the plant was built in 2002. When the facility later expanded, Adkins installed a second turbine that generates power from high pressure steam coming off the plant’s evaporators.
PHOTO: ADKINS ENERGY
Evolving Strategies
Whether investing in a let-down steam turbine would pay was a straightforward equation when he started at ICM in 2007, says Jeff Scharping, ICM director of sales. Only if electrical rates were over 7 cents a kilowatt hour would the capital investment for a steam turbine make sense. Today, the value of the potential carbon intensity reduction is changing the equation.
But even in the earlier years, there were


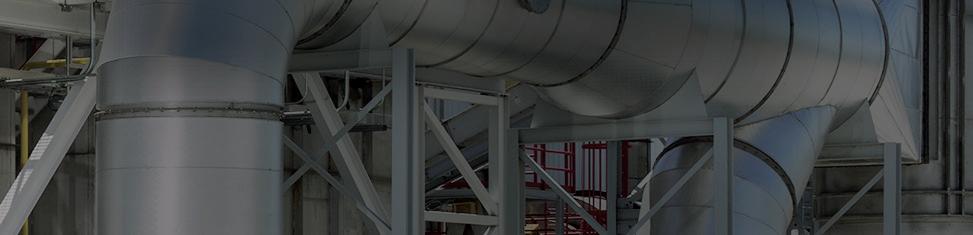
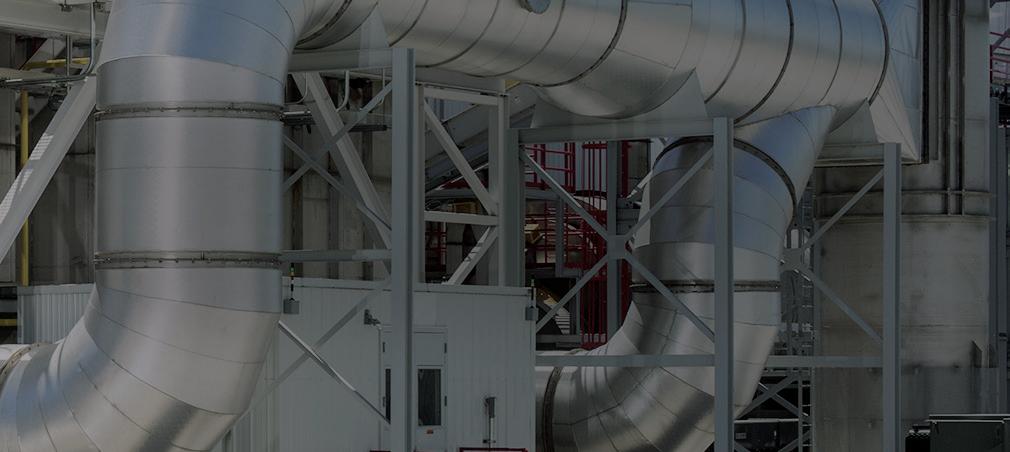
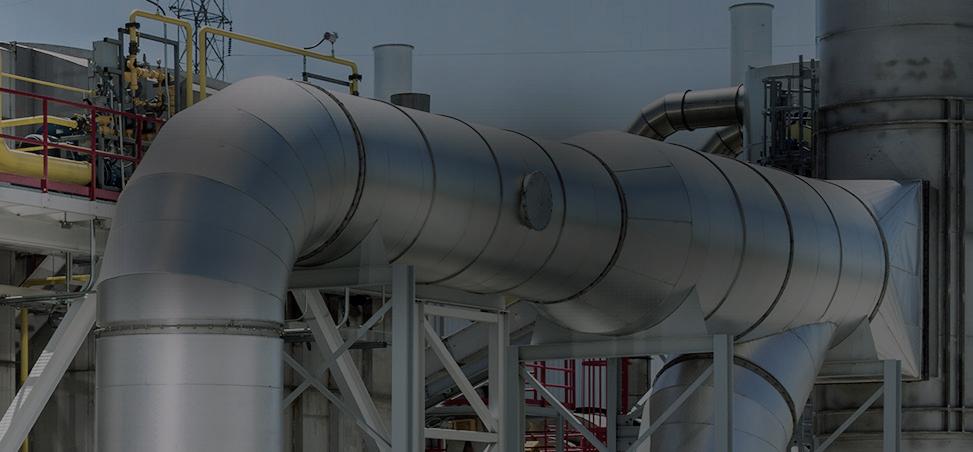


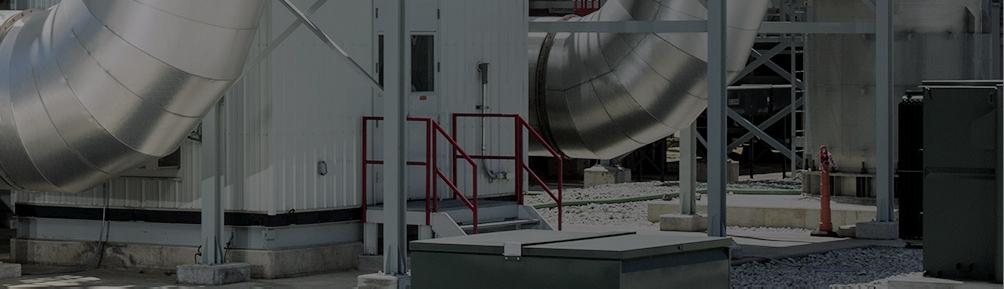

GRIDLOCKED: CHP-derived electricity from ethanol plants could be used to support peak power loads when needed. But selling power to the grid is challenging because other sources of electricity are currently cheaper.
PHOTO: STOCK
situations where plants were encouraged to install CHP, he says. “As an example, in Nebraska the ethanol plants are the largest electrical load in the state,” Scharping says. “Nebraska Public Power had to determine if they had the base load to generate that much electricity. They gave tax incentives to ethanol plants to put in combined heat and power to take load off their grid.”
Scharping expects a new carbon reduction strategy—carbon capture and storage (CCS)—similarly will lead to more CHP installations in power districts with load limitations and to add to the carbon reduction. Project developers have signed up more than 30 plants to consider capturing fermentation gases to be pipelined for injection underground (see page 14). “It takes about 6-8 MW to compress the CO2 to put it in the pipeline,” Scharping says, which would roughly double the electrical load at a typical ethanol plant.
CHP systems are designed around a specific situation, explains Marc Awtry, ICM technical support manager. “One plant might generate half their power, using the same steam they’d use anyway. Another might use more natural gas and offset 80 percent of their electrical. We’ve also seen some plants that physically can’t get more electricity off the grid because their local utility can’t make the substation larger. We talked to one plant that was told it would take three years and $3 million to get more electricity.”
If plants sized their turbines to provide all their steam load after first generating electricity, they would all produce excess power. In that case, CHP could be a source of distributed power supply shaving peak power loads on the grid. But very few plants do sell power to the grid because it doesn’t pay.
“Utilities don’t offer better rates for electricity being sold to the grid [from CHP producers] because they can buy it cheaper

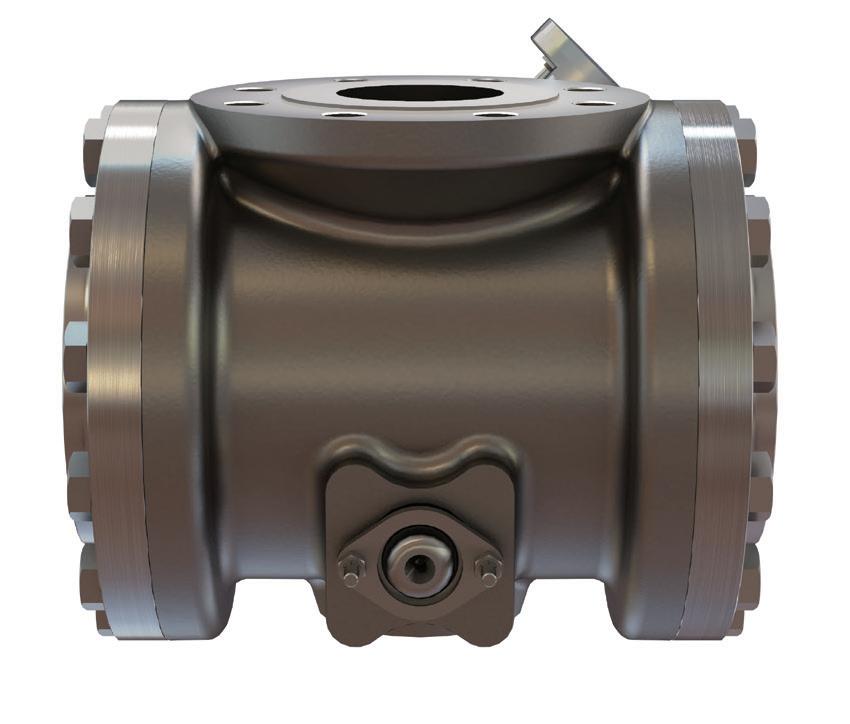
elsewhere,” explains Cliff Haefke, director of the Energy Resources Center at the University of Illinois-Chicago. The center assists CHP developers in partnership with the DOE. “You still have very lowcost nuclear generation and low-cost coal, although that’s going up, and renewables are becoming more competitive,” he says, “but [utilities] can shop at wholesale at a much lower rate than what it costs an ethanol plant to generate electricity.” Ethanol plants today in the 5-15 MW range don’t achieve the economies of scale that make selling power feasible, he explains, although bigger facilities generating 20-100 MW do attract interest from investor utilities.
Incentives are available in some states that qualify natural gas-fired turbines as energy efficiency technologies. “CHP is being looked at as a bridge technology today operating on natural gas,” Haefke says, explaining that it could transition to operat-
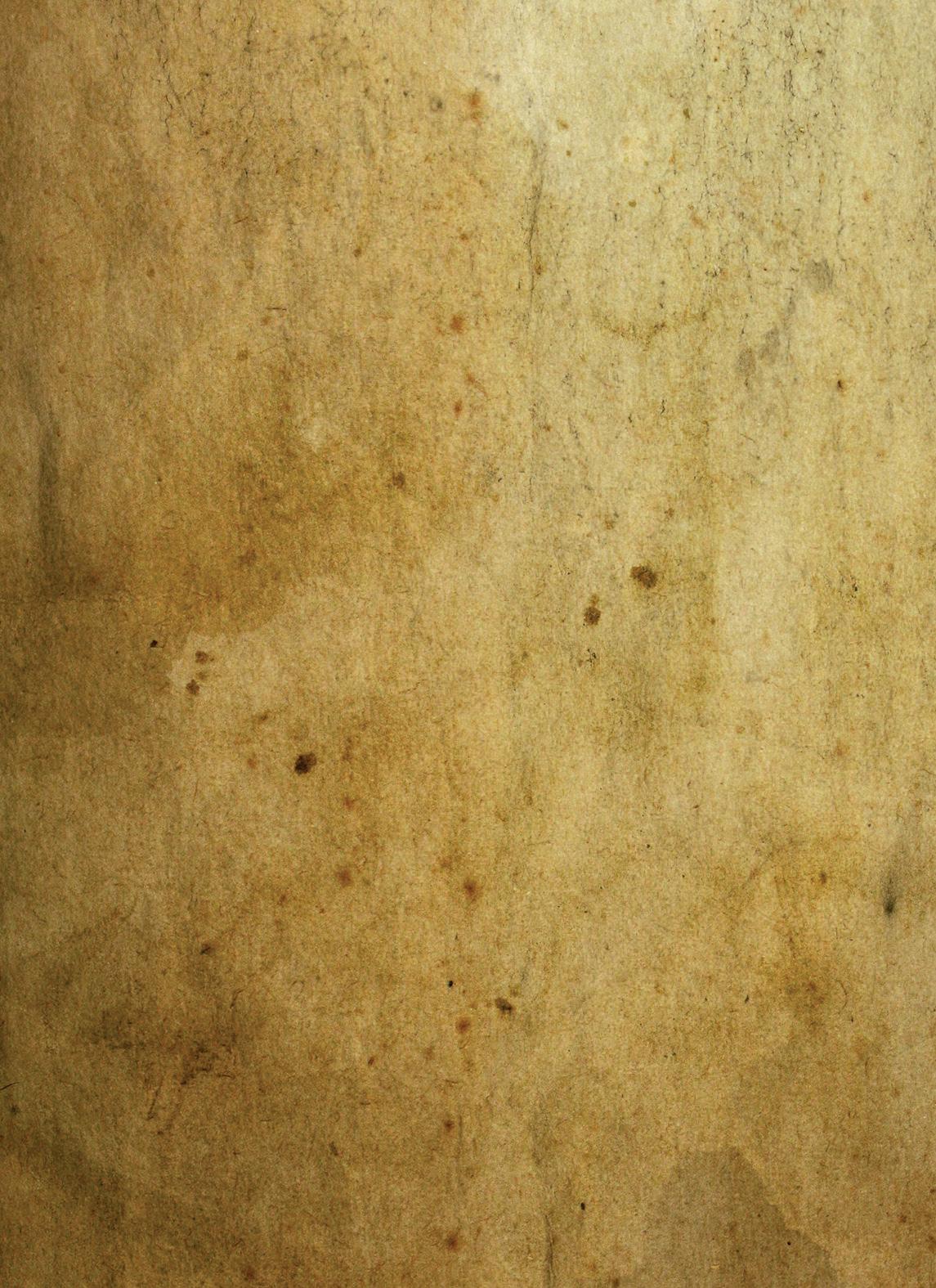
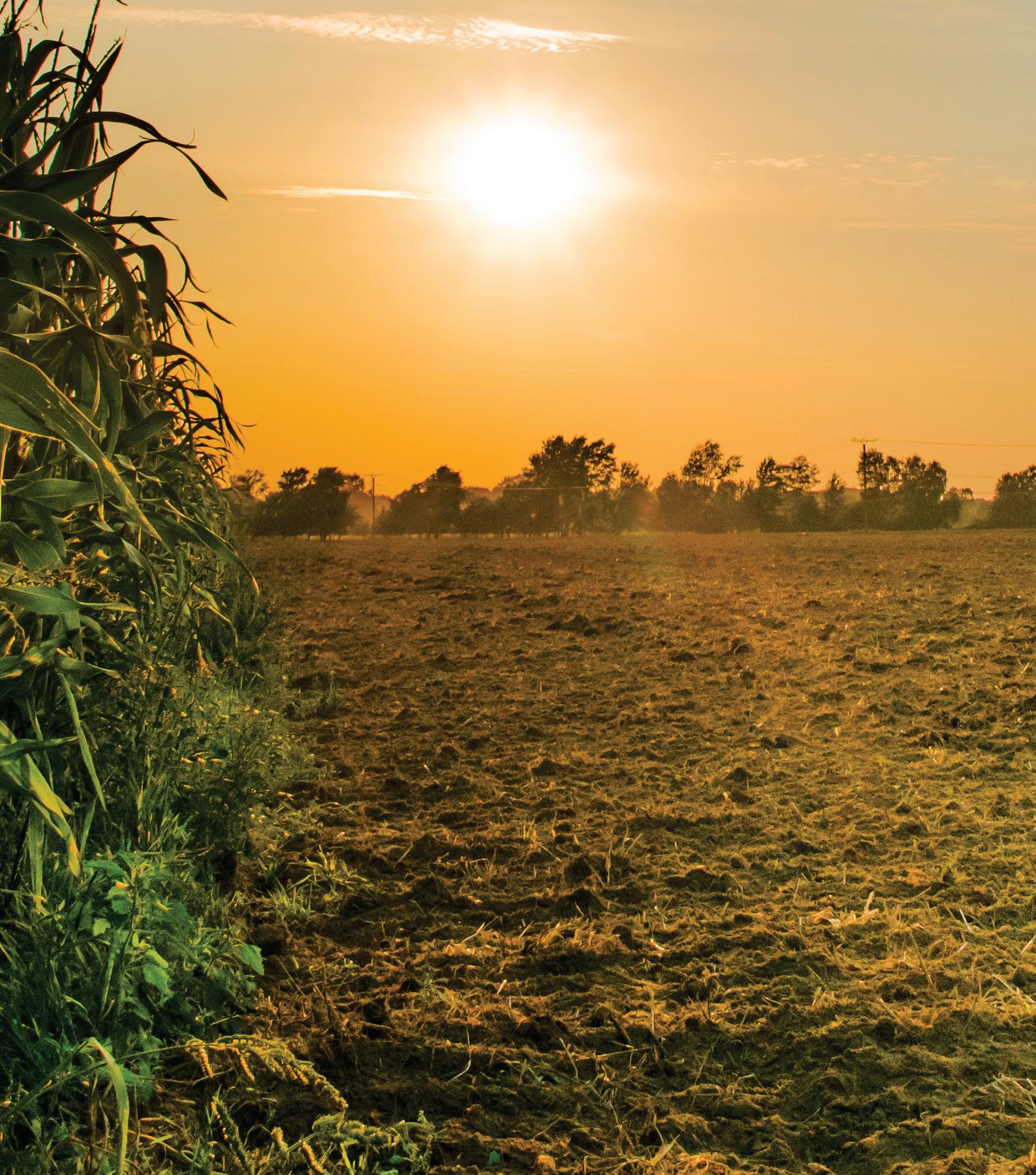
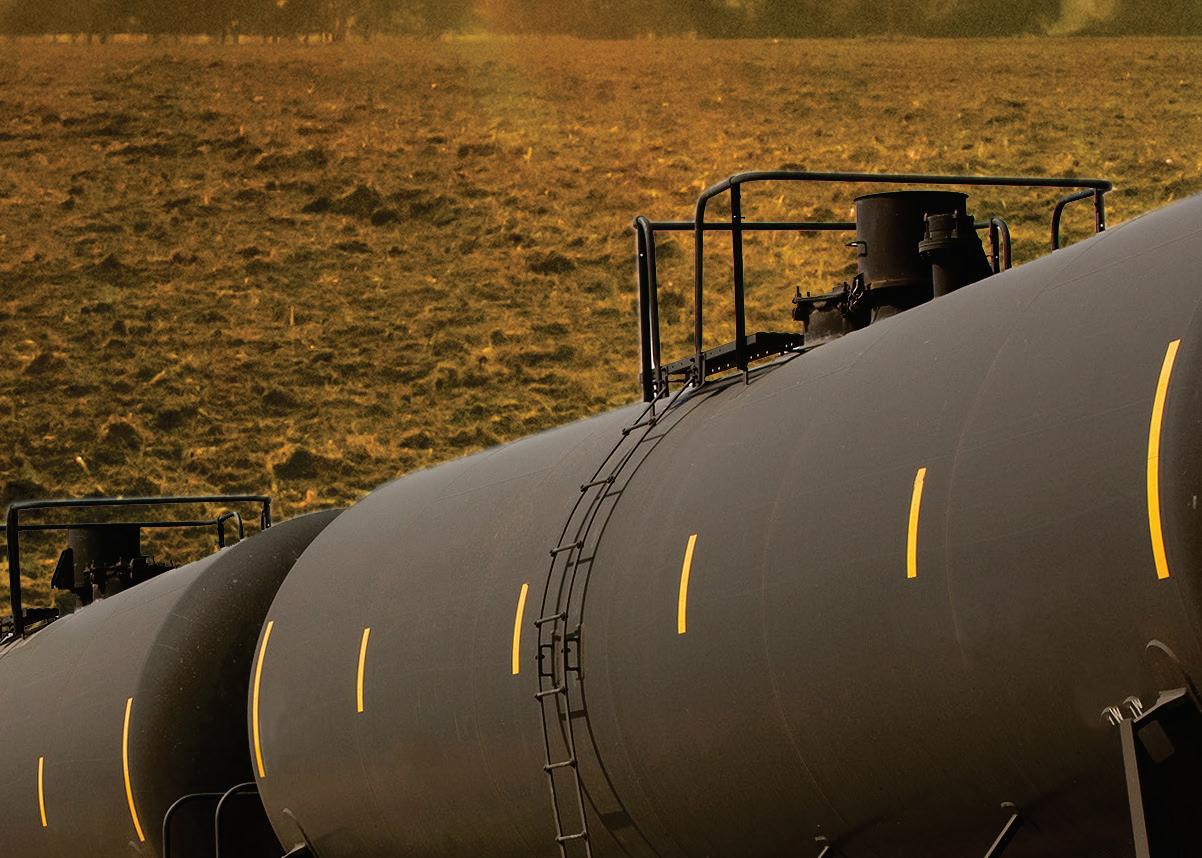

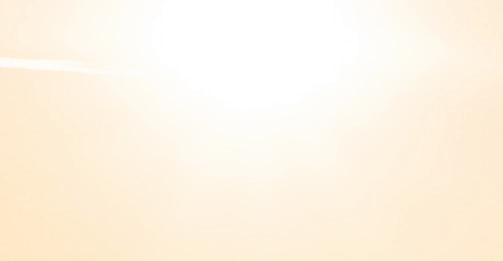
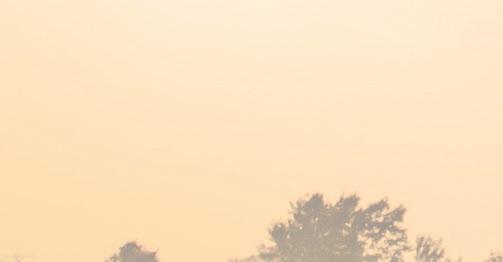

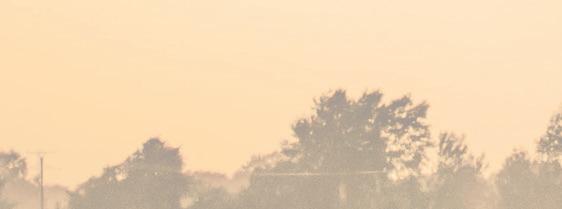
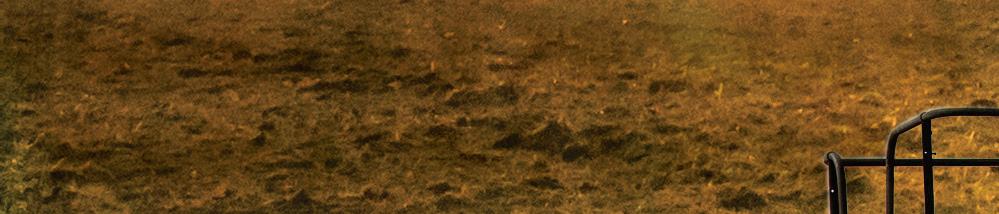
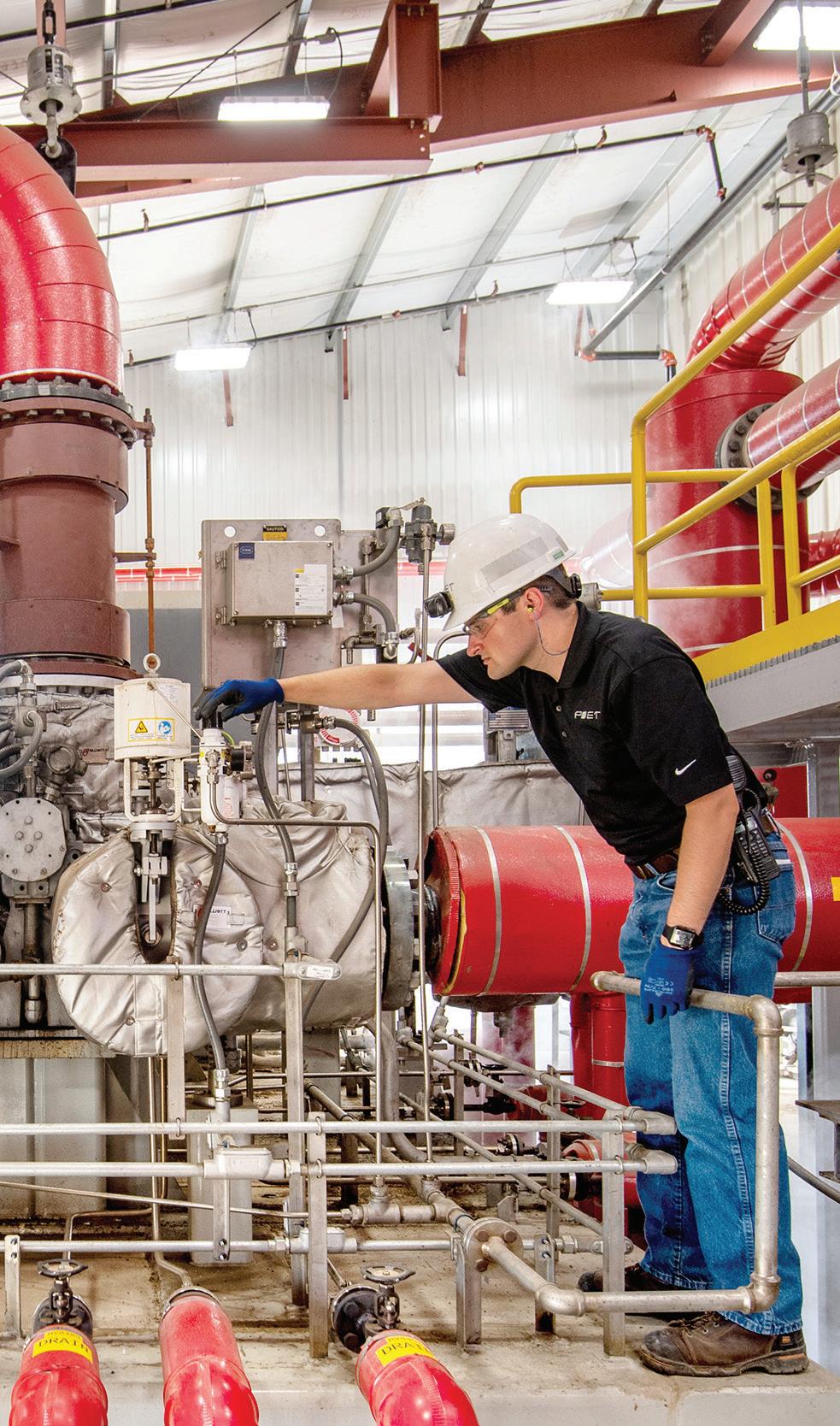
DIALED IN: Ryan Wood, an engineer with Poet Design and Construction, checks a steam turbine that generates electricity as high-pressure steam is being reduced for use in other parts of the process.
PHOTO: POET
ing on renewable natural gas or hydrogen in the future. But even operating on fossil natural gas, CHP is reducing emissions compared to marginal generation assets, he says, which are the lowest cost power plants responding to a change in power demand. Natural gas CHP plays very well, Haefke says, against peaking units operating on gas or coal that might be 30 to 35% efficient. Stand-alone thermal energy that is typically used in ethanol plants is around 80% efficient, he says. “We see CHP systems that are 70-85% efficient, even 90% or higher, depending on the technology and how well they use thermal energy.”
Looking for Opportunities
The enhanced efficiency translates into carbon intensities (CI) for the CHP electricity that score 50-80% lower than that from the grid, depending on the makeup of the grid power supply at a particular location and the type of CHP, says Rod Pierson, senior vice president and general manager of Poet Design and Construction. The importance of CI reduction continues to grow, he says, “and it goes beyond economics. The electricity off the grid has a lot of coal. Electrical consumption is going up, and not down. And CHP is a very efficient way to make electricity.”
Poet has installed 16 systems, both natural gas fired turbines and let down steam turbines, generating over 100 MW of electricity. “We have a few additional potential projects identified,” he says. “We’re always looking for those opportunities to reduce CI and improve our production process to be more environmentally friendly.”
As Poet looks for ways to partner with utilities, Pierson says the investor utilities have tended to be more interested than rural electric cooperatives. “We continue to have discussions to find opportunities. We want something that’s not going to hurt their local customer,” he says. One of the arguments in favor of ethanol CHP is that it could help a utility by reducing peak load demand, which is the most costly power to purchase.
While the current shift in national attention towards carbon reduction is likely to affect how utilities view CHP, the quest for CI reduction is also changing attitudes among ethanol boards and management toward capital projects. “Low carbon technologies have been installed that don’t have quick payback, but do have a sustainability component,” Scharping says. “The customers know sustainability is the right move to make. Turbines and CHP are going to fit into that thinking.”
“To be sustainable, ethanol needs to be low CI, zero carbon,” Scharping says. Currently electric vehicles benefit in the public eye by being considered zero emissions, zero carbon, he says. “It’s really important as an industry to brand ourselves as zero carbon, because we have to put a flag down to say you don’t have to go to electrification to get zero carbon. We can do it with ethanol.”
Reaching zero carbon will require far more than the plant process becoming less carbon intensive, he acknowledges, and will involve carbon capture and sequestration and lowering corn’s CI at the farm. “We have to combine it all if we want to get to zero. But we can get there, and combined heat and power is part of it.”
Author: Susanne Retka Schill Questions: editor@bbiinternational.com