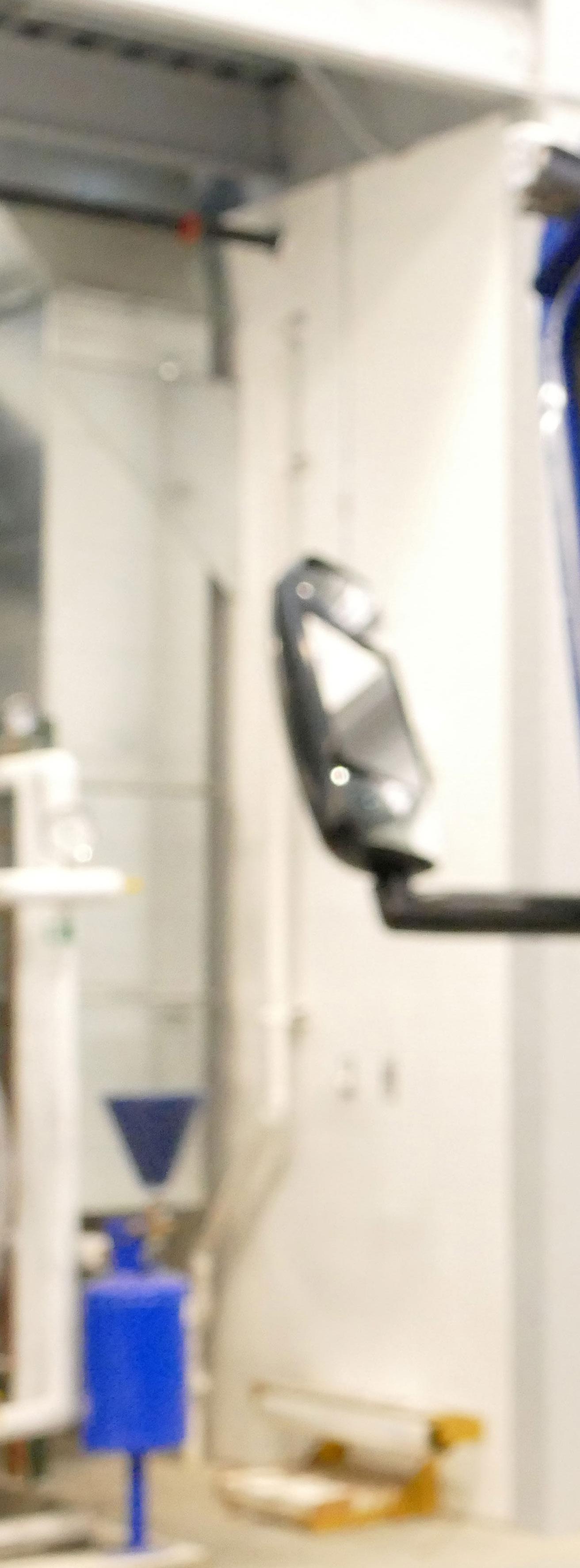
5 minute read
A Boost for B100
BY SUSANNE RETKA SCHILL
A year ago, Steve Howell was focused primarily on advancing B20. Today, B100 is high on his list, thanks to a favorable 1.3 million-mile fleet trial using new biodiesel technology alongside a proliferation of corporate carbon reduction pledges. “What we’re seeing now is that customers want to have maximum carbon reductions, and B20 simply is not enough,” says Howell, founding partner of M4 Consulting, senior technical advisor to Clean Fuels Alliance America and chair of the ASTM biodiesel task force. “Forward thinking, carbon-conscious customers with fleets—the Amazons, Walmarts and Pepsis—have corporate goals to reduce carbon over time, with some going all the way to net zero. There are a lot of public policy goals targeting 40% carbon reduction in 2030 and 80% carbon reduction in 2050.”
If fleets began using B100, they could attain that 80% reduction tomorrow, Howell says. With biodiesel considered a biogenic fuel, B100 under the U.S. EPA’s Scope 1 greenhouse gas (GHG) protocols provides a 100% carbon reduction. Under other GHG accounting systems such as Argonne National Laboratory’s GREET life-cycle model, B100 generally provides a 65-85% reduction.
While carbon reduction goals are driving interest, a new technology is solving biodiesel’s biggest problem—cold flow. The fleet trial not only demonstrated the technology works well in all weather conditions, but also dispels other concerns about biodiesel operation in modern diesel engines. The 16-month biodiesel field trial covered nearly 1.3 million miles of on-road operation with 10 Class 8 Mack trucks in Archer Daniels Midland’s trucking fleet. Five were upgraded with Optimus Technologies, Vector System and fueled with B100 to be compared against a control group of five unmodified trucks operating on B11. All 10 trucks operated on similar routes, consuming similar amounts of fuel and were equipped with New Technology Diesel Engines (NTDEs) that employ diesel oxidation catalyst (DOC), diesel particulate filter (DPF) and selective catalytic reduction (SCR) after-treatment technologies.
Optimus’ Vector System upgrades diesel to operate on B100 while never inhibiting the engine’s operation on traditional diesel, explains Optimus CEO Colin Huwyler. The system involves a series of heat exchangers, pumps, filters and sensors that are the core mechanical components controlled electronically and interacting with the engine’s fuel system controller and after-treatment electronics. “Everything is happening autono- mously,” Huwyler says, “so the drivers don’t have any interaction. Our software monitors fuel and engine parameters and as soon as the operating conditions are met, it will switch from diesel, which the engine starts up on, over to biodiesel.”
In over-the-road, Class 8 trucks, the larger fuel tank is filled with B100, while the smaller tank holds the regular diesel used for startup and shutdown. For vocational applications like snow plows and garbage trucks, the Optimus retrofit generally involves replacing the fuel tank with a dual-chamber tank. A 70-gallon fuel tank on a garbage truck, for example, will be replaced with a 100-gallon tank that holds 70 gallons of biodiesel and 30 gallons of regular diesel. Regular diesel is used to start and shut down the engine, Huwyler explains, with most trucks running on B100 between 90 and 95% of the time.
The Optimus system solves the issue with biodiesel’s higher cloud point that causes higher biodiesel blends to gel at much higher temperatures than traditional diesel.

“We circulate the waste heat that comes off the engine through the heat exchanger where we circulate the biodiesel through,” Huwyler says. “Regardless of ambient temperature, the engine can operate on 100% biodiesel.” Customers have operated the technology down to negative 20 or negative 30 degrees Fahrenheit, he adds.
The 16-month ADM fleet trial demonstrated successful cold weather operations and collected multiple points of performance data. “We saw a pretty dramatic benefit utilizing 100% biodiesel with our technology in engines with diesel particulate filters,”
Huwyler says. DPF filters essentially collect the soot from combustion, and since biodiesel generates roughly 50% less soot than traditional diesel, that correlated to about 50% improvement in the regeneration cycle of the filters in the ADM trucks running on B100, extending the 110-hour interval to 220 hours. “Any time you can extend those intervals, there is a direct cost savings to the operational aspect of running a fleet,” he says. In addition to the DPF regen benefit, the 1.3 million-mile-trial found no issues with crankcase oil dilution and a slight improvement in fuel economy running on B100.
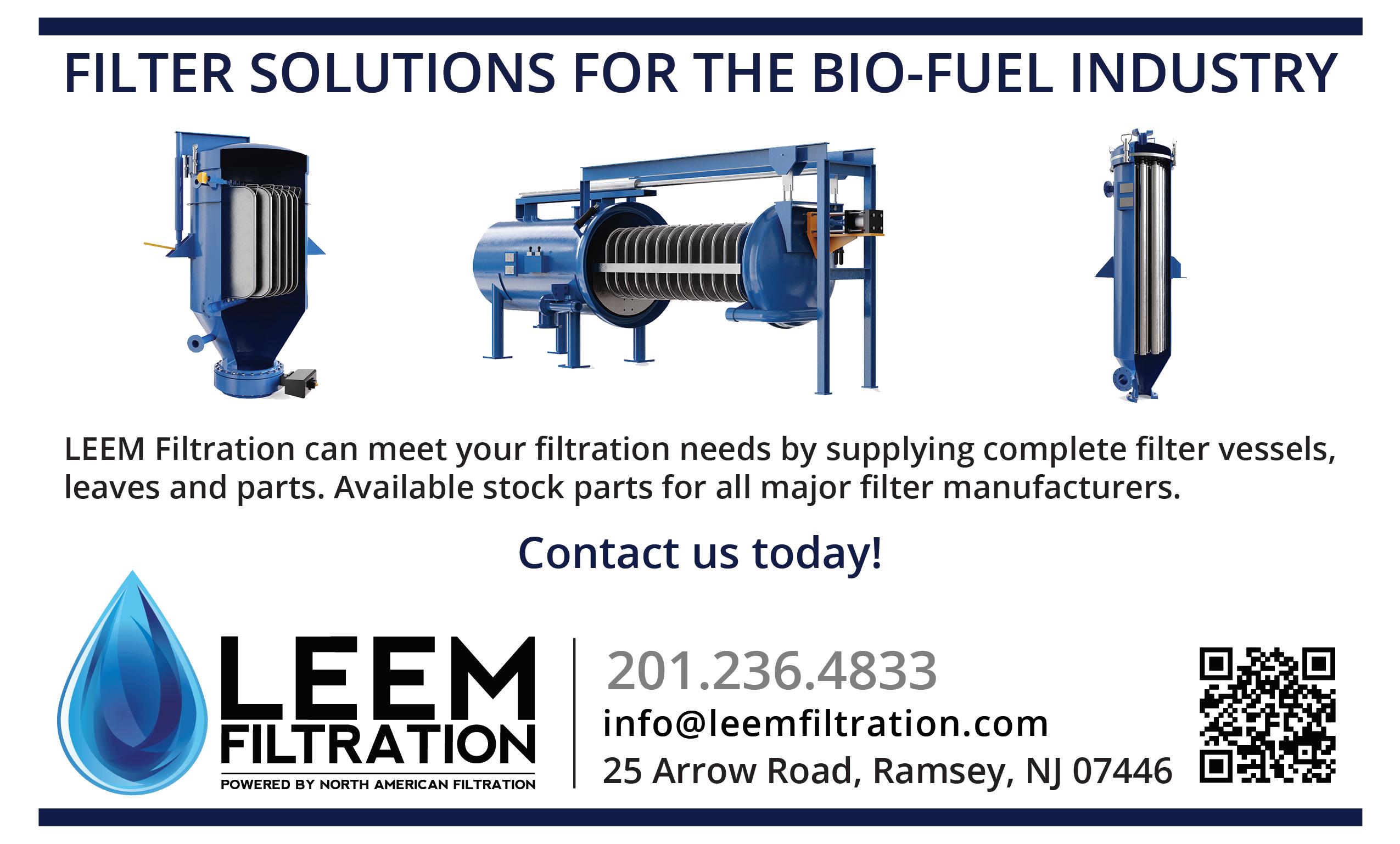
The ADM fleet trail results counter conventional wisdom that biodiesel’s lower Btu content than petroleum diesel will result in a fuel economy hit, Howell says. The results also address other concerns original engine manufacturers (OEMs) have with higher blends—the biggest being the potential for metals in biodiesel to impact the exhaust aftertreatment used in modern engines. The fleet trial data shows that isn’t a problem, Howell says, “And there’s rationale for that because biodiesel is really high quality today. The National Renewable Energy Laboratory’s fuel quality study show it’s near zero metals in biodiesel from the get-go.”
The positive B100 findings will improve biodiesel’s competitiveness with renewable diesel, Howell continues. “A lot of the reason companies were looking at renewable diesel was because the OEMs were concerned about the metals in biodiesel, and they didn’t think you could use more than B20. Renewable diesel is distilled, which removes metals, so most OEMs support use of 100% renewable diesel. Now we’re finding out you can use 100% biodiesel too, because our quality has improved so much.”
Biodiesel vs Renewable Diesel
Biodiesel is going to be competitive with renewable diesel, even as RD capacity is scaling rapidly, because it’s less expensive and available, Huwyler says. “Renewable diesel is only really available in California, and a little bit in Oregon and Washington. Because of the substantial price premium for RD compared to regular diesel, it needs the lowcarbon subsidy in those West Coast markets to be somewhat competitive.” The reality, he says, is that most of the freight moves in the other 47 states where renewable diesel is unavailable and, if it were, would be more expensive.
“The primary users of our technology are large fleets using significant volumes of diesel fuel annually,” Huwyler continues. “If a Class 8 truck is using 10,000 to 20,000 gallons on a yearly basis, paying a premium for renewable diesel on every single gallon for the life of the truck, which might be 10 years, is a substantial increase in cost. With our technology, there is a CAPEX investment—an upfront cost—but then, that ongoing cost is closer to or the same as regular diesel. So, it’s a much total lower cost to deploy a sustainable solution.”
“With the tax incentive and RIN program, B100 is similar in price to diesel,” Howell points out, while renewable diesel can run $1 to $2 more. “With relatively low capital cost you can retrofit, put in an Op- timus system and get carbon reduction and meet your goals, with no detrimental effect on the vehicle because the cold flow problems are solved. When an electric bus costs three, four, five times as much as a regular diesel bus, a $30,000 retrofit on a $300,000 vehicle is not very much of a cost.”
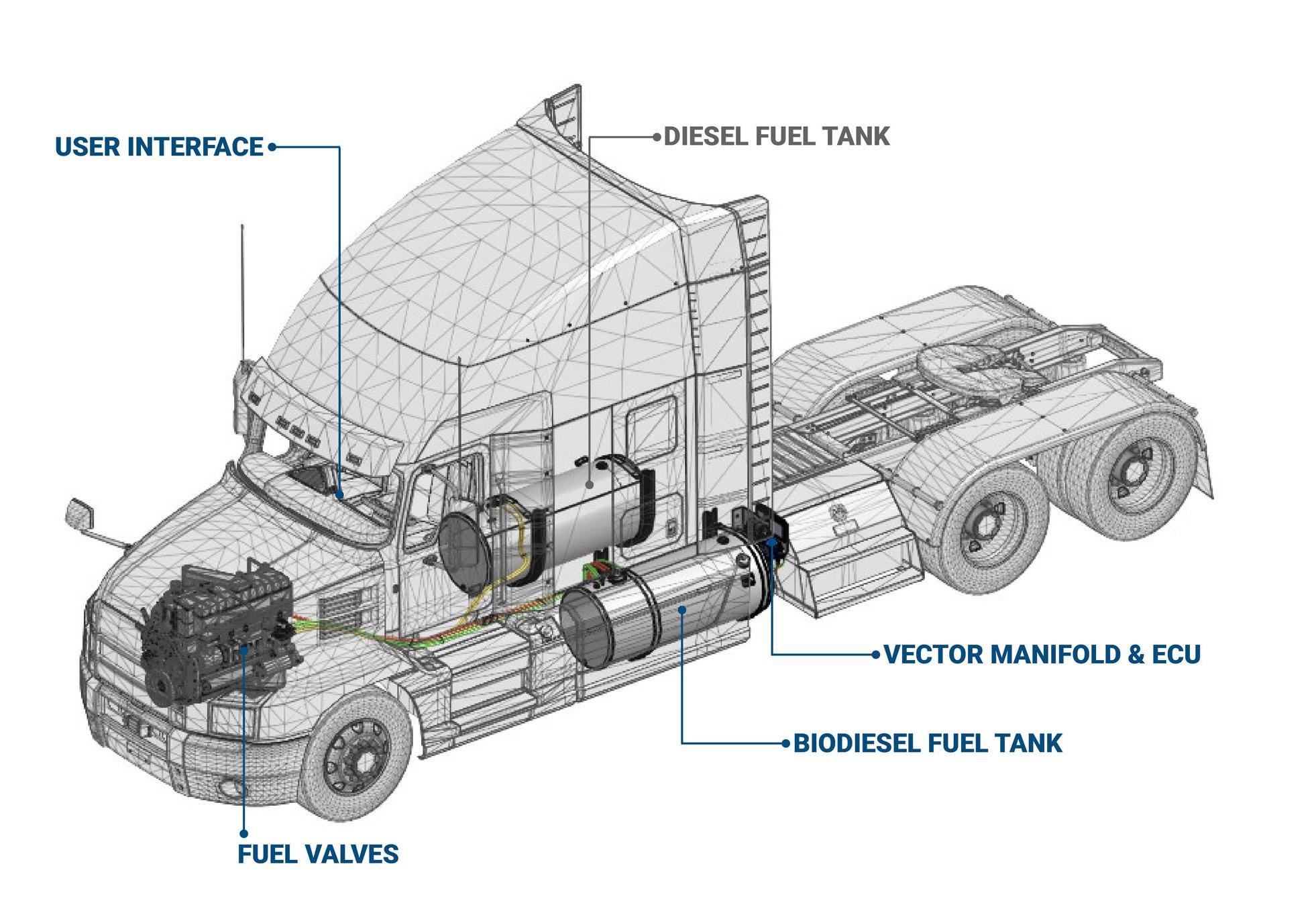
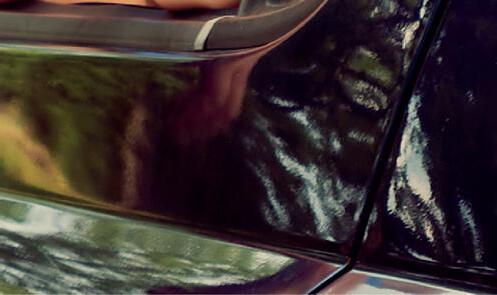
Biodiesel has other competitive advantages with RD, Huwyler suggests. While they use the same feedstocks, biodiesel gets almost one gallon of fuel out of a gallon of vegetable oil, whereas the renewable diesel process loses a portion. At the same time, RD energy consumption is slightly higher and its CAPEX is substantially higher than biodiesel. “I think in the future, biodiesel will always have a lower carbon intensity than renewable diesel,” Huwyler says. “And it’s much better suited to regional diversity and to be more distributed throughout the U.S. because you can have smaller, 250 MMgy plants, as opposed to a 1 million-barrel-a-day facility.”
One selling point for renewable diesel is that it is an identical molecule to petroleum diesel, making it a drop-in replacement for regular diesel. This raises the question whether renewable diesel’s toxicity will be identical as well. One of biodiesel’s advantages over petroleum diesel is its nontoxicity and biodegradability. “It’s much safer for operators and technicians to be around,” Huwyler says.
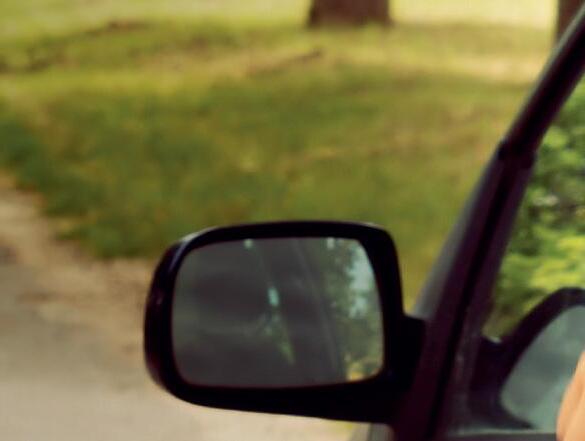
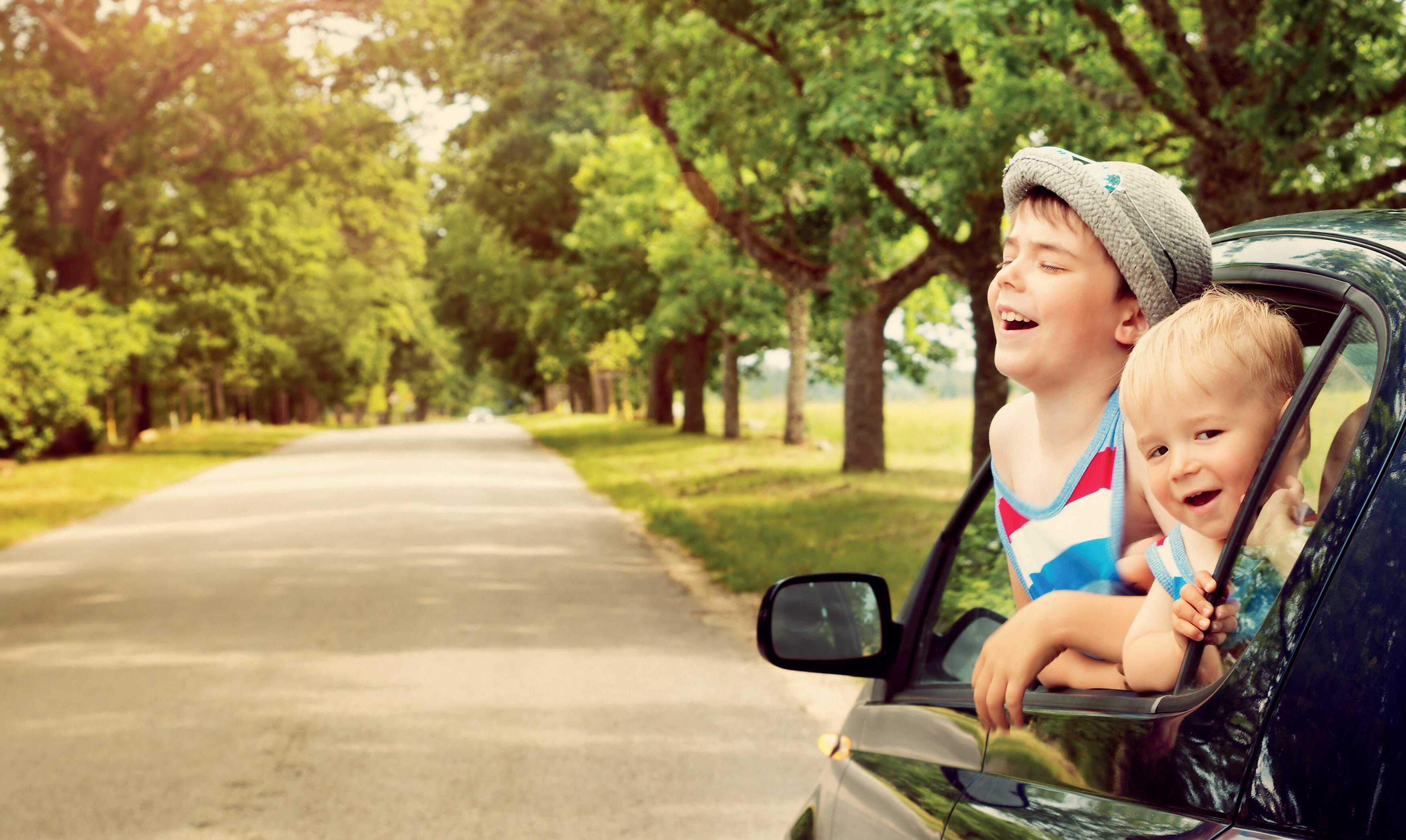
And, while there may be a claim for RD’s compatibility with existing infrastructure, biodiesel has been around long enough and used widely enough to have infrastructure in place. “Because of how biodiesel is used today, it gets blended with traditional diesel,” Huwyler says. “So, travel centers
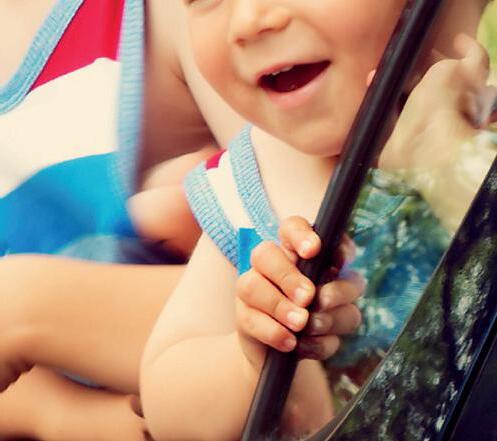