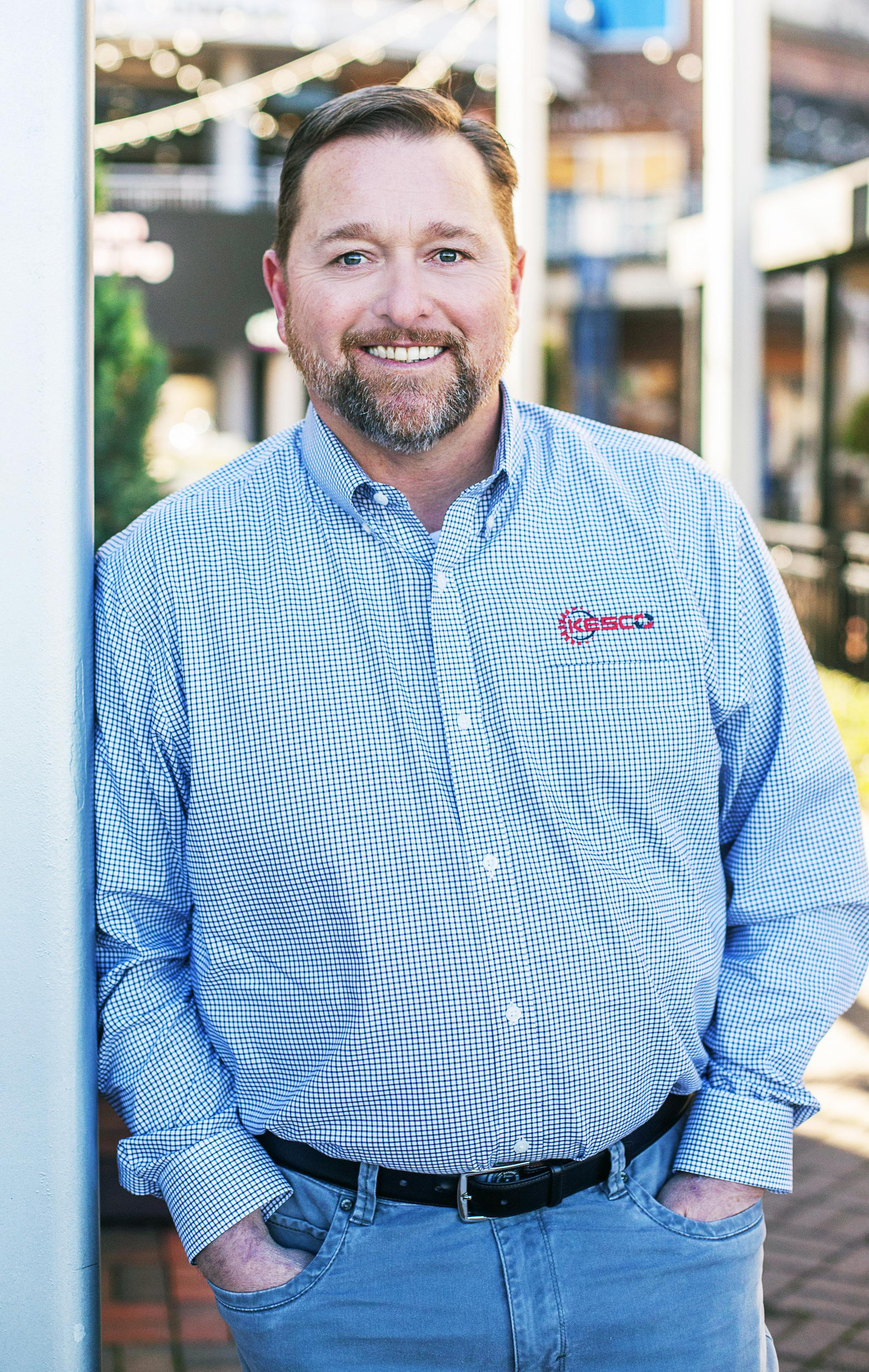
6 minute read
KESCO INC
Five Questions with KESCO
Biomass Magazine chats with KESCO founder and president Jason Kessler.
BMM: Tell us about KESCO—when and why it was founded, and the company mission.
J.K.: KESCO was founded in 2001. We are a solution-focused, American company that provides the expertise necessary to design, build and commission bulk material processing systems. Our tailored solutions are designed to satisfy your specific project requirements. We partner with leaders in their respective fields to provide an efficient project experience. Our work is spread across more than 30 wood pelleting plants throughout North America, with seven of these projects being complete plant supply.
As for KESCO’s history, in the 1990s, I worked for Bliss Industries, a leading manufacturer of hammer mills, pellet mills and pellet coolers. My primary focus was to develop emerging markets in the wood sector. We found that most opportunities required a complete system rather than individual pieces of equipment, which required that I find quality equipment manufacturers that shared our business philosophy. Customer-first problem solving was a philosophy taught to me by my father, Mark Kessler, who was working with Laidig Systems at the time. I was introduced to Drew Kice with Kice Industries and Justin Koenig with Rapat Corporation, and these three companies shared our philosophy. Along with Bliss, they made up 90% of the systems we were designing. There were tough times economically in 1999 and 2000. I believed in the team we assembled, the systems we designed, and that the renewable energy market was getting ready to take off. I had experience supplying several complete systems with Bliss Industries and found myself with first-hand experience in the wood pelleting industry that very few people in North America had at the time.
I created KESCO for three primary reasons. The first is entrepreneurial spirit. I always wanted to have my own business and enjoy the pressure of having the buck stop with me. Second was application knowledge—I could count on one hand the
number of people that had the same level of experience in the wood pelleting sector. Clients were tired of paying engineering firms for their time, boiler plate documents, and regurgitated “facts.” They needed help from someone with real-life experience. Finally, I wanted to help others. This had proven to be a rule to live by personally, why shouldn’t it be our mission in business? There were plenty of smooth-talkers out there. The clients I met with needed genuine help. They were understaffed, had good ideas and needed processing expertise. These were the primary reasons for starting KESCO and continue to be the keystones in our operation today.
BMM: You’re speaking at the upcoming International Biomass Conference & Expo in Jacksonville, Florida, March 14-16. What are some touch points that attendees can expect?
J.K.: The title of my presentation is “Islands are for Vacations, not Pellet Plant Design.” The wood pelleting industry has historically developed projects using an “island” philosophy: the dryer island, the dry hammermilling island, the pelleting island, the wood yard, etcetera. No one can really answer why it is done this way; it just seems to be how it was done on some of the early projects. I believe this approach is just a way for clients and/or engineering firms to break up responsibility for a bid package. They can dedicate a team to “this island” and another team for “that island.” This has often resulted in choppy operations that are designed around a series of small successes, in an industry that is judged on one thing: finished pellets out the door. The focus of my presentation is on the effects, both positive and negative, that one area of process, or island, may have on another area of process. We will use examples from operating wood pellet plants to show what happened, how it affected the overall process, and what needed to be done to improve the overall operation.
BMM: This seems to fall in line with KESCO’s business model of designing “cohesive” wood pellet manufacturing systems.
J.K.: Exactly. The island approach to designing plants does not take overall process objectives into consideration. A cohesive design means a design that is looking at the operational costs of the entire operation, not just a specific island. One example, which I intend on discussing in detail during my presentation, is the impact of moisture content and temperature on the grinding process. Warmer material can improve pelleting efficiency while decreasing hammermilling efficiency. Some pellet mills require higher moisture material than others. Higher moisture material may increase efficiency for certain pellet mills while significantly decreasing hammermilling efficiency. A cohesive plant design will take all these factors in consideration to determine the most efficient means of achieving their production objectives.
BMM: A common problem that some new wood pellet plants experience is bottle necks in process flow. What seems to be at the root of this problem? Can you tell us about KESCO’s experience when it comes to helping customers solve these issues?
J.K.: There are two primary reasons for bottle necks in process flow. One is the material itself—we are dealing with wood fiber. A large portion of a wood pelleting system uses volumetrically sized equipment. Mechanical material handling equipment, surge bins, silos, air handling equipment, airlock valves and feed screws are some of the specific components that are sized volumetrically. Specific processes within the wood pelleting process can decrease product bulk density and flowability. One example is microchips versus pre-shredded chips. Both products share similar particle sizes, bulk densities and moisture content, but shredded material has very different material handling characteristics than microchips. The pre-shredded material can nest together, leading to backups in discharges and chutes. Most new plants do not have material that can be tested prior to designing the system, so assumptions must be made. This leads to the second reason for bottlenecks. It’s easy for producers to ask why manufacturers aren’t more conservative in their sizing of equipment—the short answer is price. Most pellet plant purchasing decisions are being made on price. KESCO tries to explain the difference between price and cost to our clients. The greatest cost to a pellet plant is not producing pellets at the design rate, quality or within a timeframe that meets their contractual commitments. Establishing a design safety factor with the client is one of the most effective ways to eliminate potential bottlenecks while managing expectations of the system price.
BMM: Are you seeing any trends right now in the wood pellet industry?
J.K.: Green chip shredding is being incorporated into most new wood pellet plants. This process further reduces the chips prior to drying, and allows the wood yard to produce a larger, looser tolerance chip. Pre-shredding will break open the chip, allowing the dryer to operate more efficiently. Pre-shredding chips can produce enough fiber that meets particle size specification to justify screening the product prior to dry hammermilling. This decreases the amount of material that needs to run through the dry hammermilling process. Green chip shredding and dry hammermilling must be evaluated together to minimize connected horsepower. Recycling a percentage of dry hammermill air is also gaining traction in wood pellet plant design. A properly designed air recycle system will decrease the amount of air exhausting to emission control equipment, while having minimal impact on the dry hammermilling efficiency. Minimizing the amount of air needing to be permitted is a common goal of all wood pellet producers.