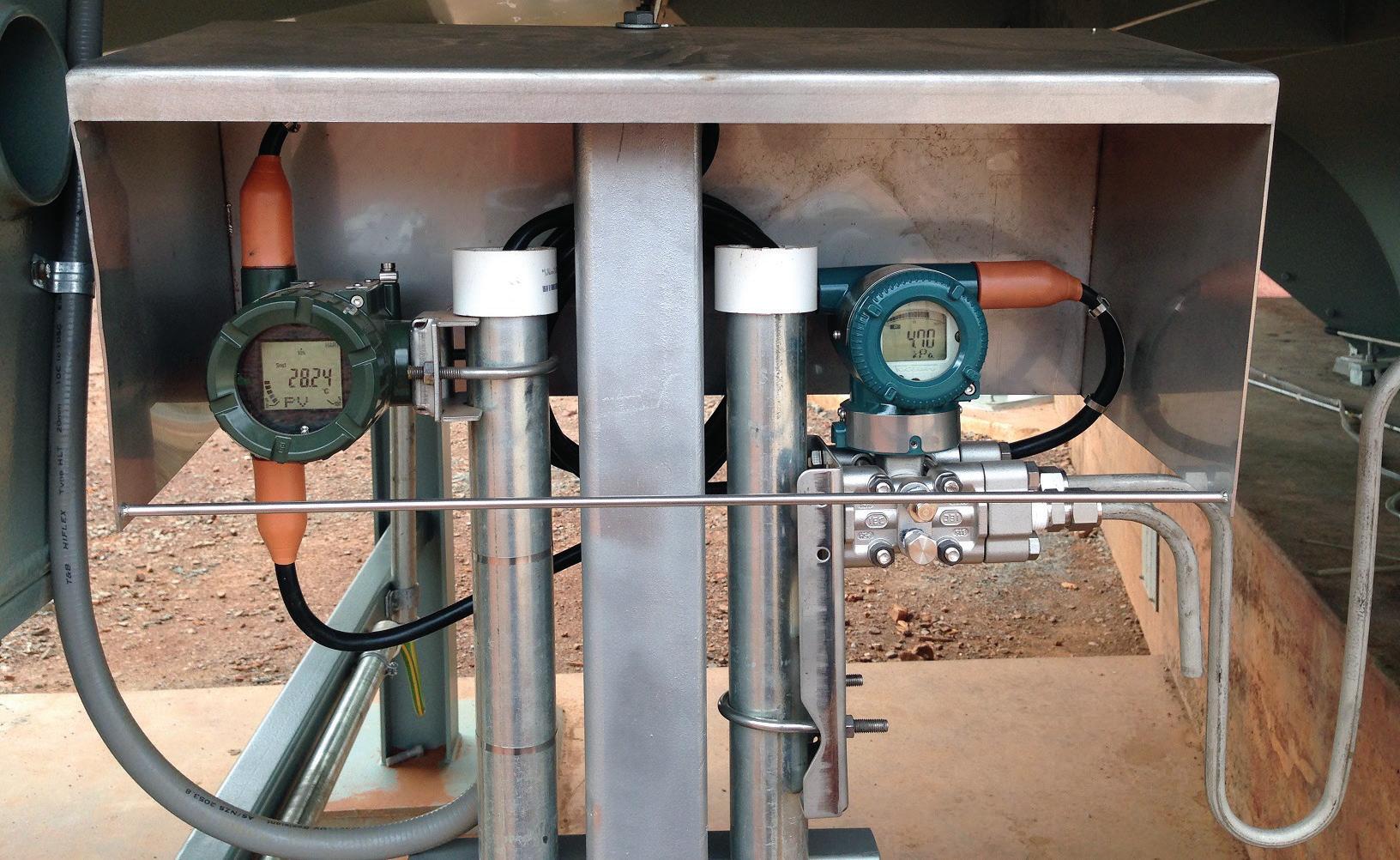
5 minute read
ASSET MANAGEMENT
Leveraging smart technology can reduce maintenance and power consumption costs, as well as compound cost savings over time with continuous monitoring and optimization. BY MARGARET WOOD
Specifying blowers for biomass energy applications requires finding the best value between the initial capital expense and ongoing operating costs. Biomass applications are inherently tough on fans, with extreme temperatures up to 1,800 degrees Fahrenheit (980 degrees Celsius), high vibration and heavy dust loads that can quickly wear down components. Meanwhile, fan reliability is paramount, as the equipment supports many critical functions.
The harshness of the environment— coupled with stringent energy and environmental standards—can make it challenging to specify industrial fans and blowers that both withstand the demands of biomass applications and avoid exorbitant costs.
It is a delicate balance: attempting to cut costs upfront can come back to bite in the form of excessive power consumption due to inefficient fan operation, financial risk due to safety hazards, and high ongoing maintenance and repair costs. In many cases, specifications for biomass applications come with outdated requirements or no allowance for inexpensive options and newer technology.
Finding the Balance
Fortunately, economical options do exist, and the challenges brought on by outdated methods are no longer inevitable. Instead, smart technologies like the Internet of Things (IoT) are transforming the industry and making possible what was once unimaginable. Now, there are many avenues to achieve high standards of equipment re-
The integration of remote monitoring systems is becoming more common. Pictured above is a shaft collar pressure and air temperature gauge.
PHOTO: NEW YORK BLOWER COMPANY
liability, safety and efficiency while reducing the costs of equipment installation, operation and maintenance. The key? Leveraging IoT technology to reduce maintenance and power consumption costs, and compound cost savings over time with continuous monitoring and optimization. The following are steps to achieve these goals.
Reduce Maintenance, Repair and Replacement Costs
Biomass power generation creates a hot and polluted environment for air-blowing equipment. For this reason, the first step to saving costs is specifying industrial fans suited to the environment to avoid the need for frequent repair or replacement. For example, induced draft (ID) fans for boiler applications should be constructed with wear-resistant materials like heavy-duty carbon steel. In addition, surfaces that are particularly susceptible to wear should be covered with liners or overlay material as an additional layer of protection. Fans used in boiler applications must also be able to withstand the high heats, including both normal operating temperatures and short bursts of very high heat—as high as 1,800 degrees—to ensure major fan components can survive in case of a boiler malfunction.
Along with extreme temperatures, the presence of dust and debris must also be considered when specifying fans for cost savings. When dust particulates accumulate on the fan, this buildup can reduce performance, efficiency and reliability. Furthermore, dust buildup on fan blades is rarely uniform and can lead to rotor imbalances, increases in vibration, and early bearing wear and failure. A reputable fan manufacturer can help you select the appropriate blade geometry to limit particulate buildup and protect the fan from costly damage.
A rugged build and ideal geometry is no longer enough for fans supporting critical power generation processes. Robust design
must now be paired with IoT and predictive maintenance to ensure long-term reliability, reduce maintenance expenses, and avoid costly downtime. For example, mechanical IoT sensors can be installed at the motor shaft to measure changes in vibration and temperature in real-time, comparing them to an established baseline to provide early indication of potential mechanical problems. Particle sensors can also be used to monitor the volume of dirt and dust in the airstream. This real-time condition monitoring makes it possible to quickly identify acute problems that require immediate action, as well as monitor subtle performance changes that predict future failures so they can be prevented.
Reduce Operating Costs
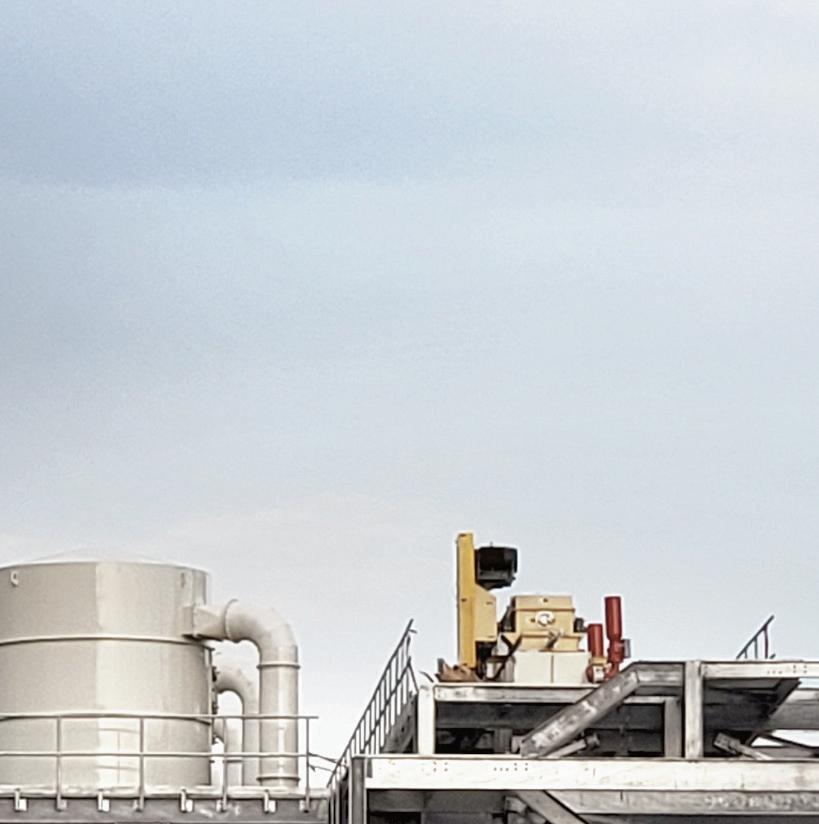

Power consumption is one of the largest expenses associated with the operation of air-blowing equipment, so energy efficiency is critical. Just like specifying fans for harsh environments, fan construction and geometry play an important role in determining the fan’s efficiency. For example, centrifugal fans provide the highest efficiency and consume the least amount of power when they are constructed with airfoil blades (blades shaped like an airplane wing). However, with the emergence of IoT tech, geometry is far from the only way to maximize efficiency. With economical, battery-operated IoT sensors, users can measure airflow, pressure and other fan efficiency metrics in real time—and adjust as necessary. In addition, users can be notified immediately when a fan is running inefficiently and using more power than normal or necessary, so the problem can be resolved before costs add up. Because power is such a major expense, optimizing fan power consumption can significantly save costs and improve margins over time.
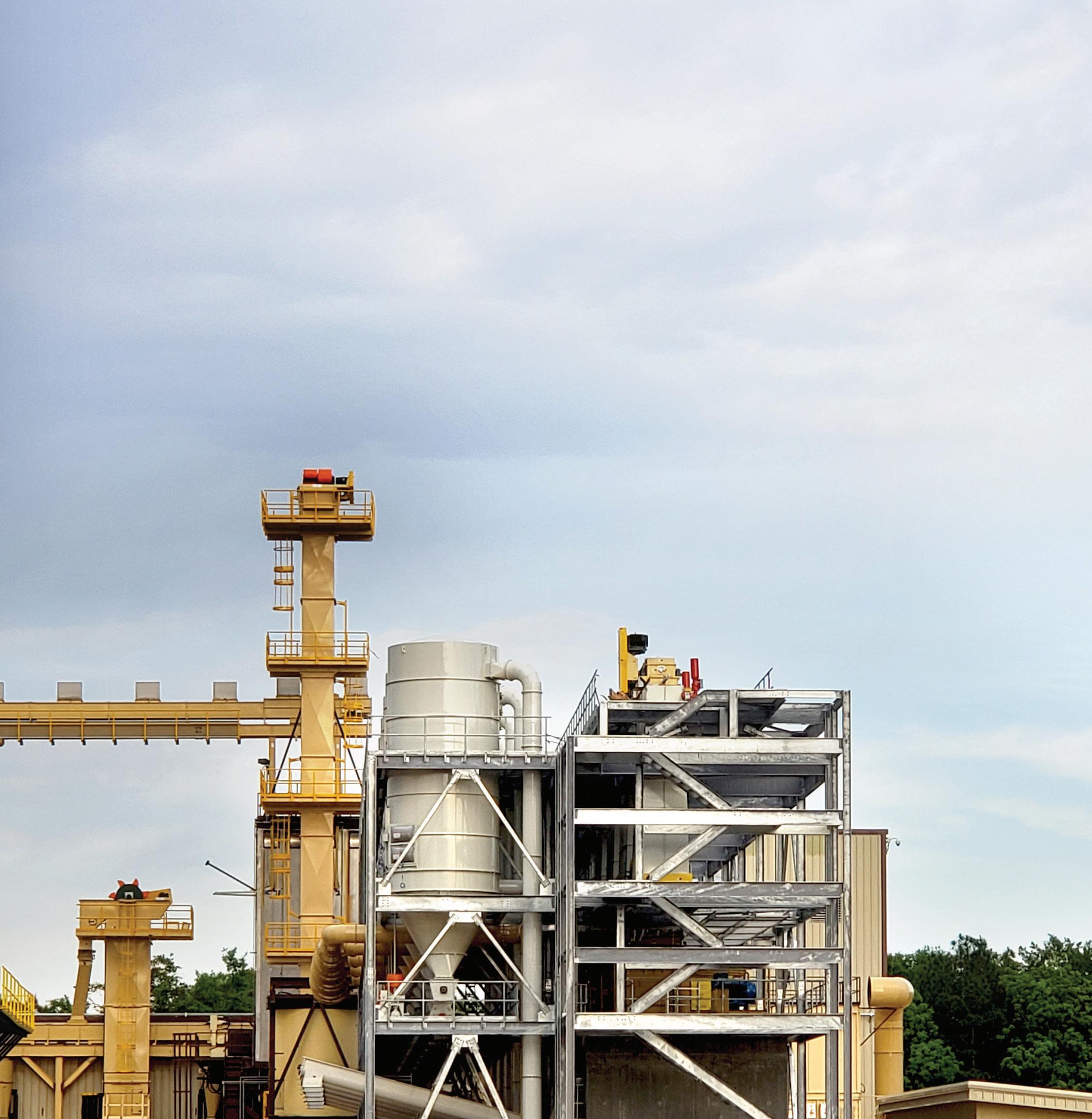
Compound Cost Savings Over Time
The real-time visibility provided by IoT sensors cannot be underestimated, but the true value is realized when these technologies are employed continuously over time. Not only does remote monitoring give equipment managers insight into fan performance and equipment health in real time, but it also allows users to track trends over time to continuously improve efficiency. For example, historical data from condition monitoring sensors can be used to measure and improve overall equipment effectiveness, which is a percentage value that represents the equipment’s total availability, performance and production quality.
Furthermore, IoT sensors can be connected to artificial intelligence, enabling proactive readings of machine health automatically. With machine learning, IoT sensors can even become self-improving through fine-tuning optimization, accelerated reaction times, and increasing accuracy and safety. Ultimately, pairing rugged fan equipment with the latest smart technology enables your equipment to run at peak performance level, and even get better over time.
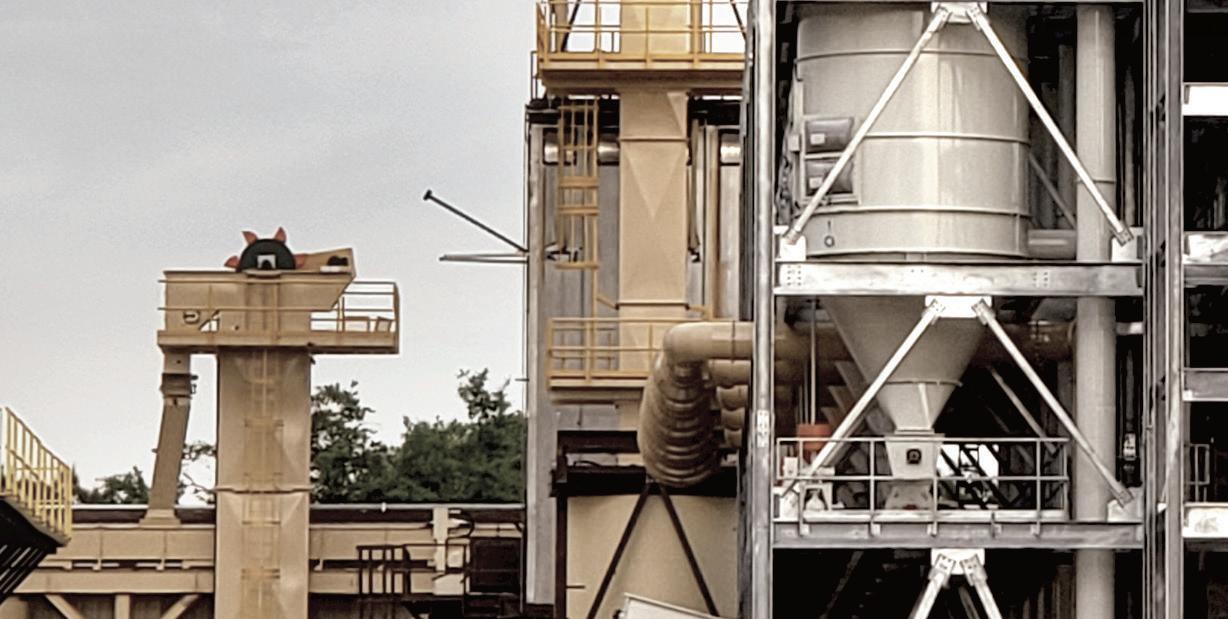
Air-Blowing Equipment Without Compromise
The old rules of industrial fan specification are out. Now, there are many modern strategies and technologies available to optimize efficiency and save on both capital and operating expenses. First and foremost, selecting reliable, high-efficiency equipment that can withstand the demands of biomass applications is key. This, paired with IoT tech that can remotely monitor real-time conditions, proactively identify signs of wear, and prevent premature failure will keep your equipment running smoothly, ensure efficiency and maximize uptime. Finally, partnering with a knowledgeable and experienced industrial fan manufacturer that is ahead of the curve with next-generation capabilities can help you customize the right solution for your application
Author: Margaret Wood New York Blower Company mwood@nyb.com www.nyb.com