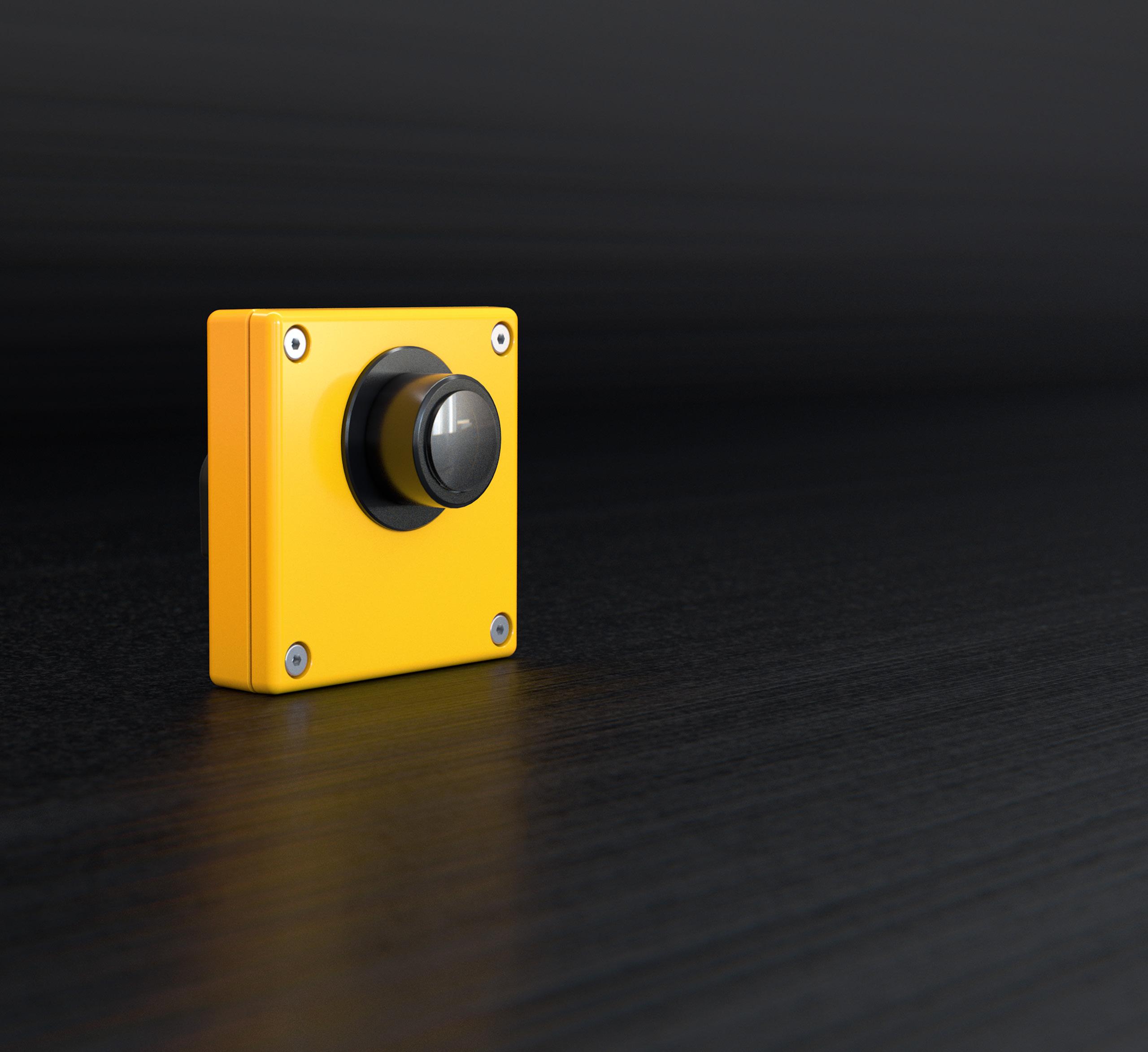
9 minute read
FIRE & EXPLOSION
ARMING THE INDUSTRY
Experts from FLAMEX, Fagus GreCon and CV Technology share some new and improved technologies for fire and explosion prevention and mitigation.
BY KATIE SCHROEDER
Fire and explosion protection are key in any industry with dust, and the biomass industry is no exception. The wide variety of fire prevention and mitigation tools available to producers are constantly evolving. Eric Peterson, CEO of Fagus GreCon Inc. in the U.S. and Canada, explains that there are three components needed to start a fire. First, there must be oxygen present; second, there must be a fuel source— generally this tends to be the product needing protection—and finally, an ignition source. “What our equipment is designed to do is detect that ignition source and extinguish it,” Peterson says.
Fagus GreCon
Fagus GreCon has two recently developed technologies that are utilizing advanced intelligence to improve accuracy. The first of these technologies is the DLD 1/9 Spark Detector, which was released last year. Peterson explains that while past spark detectors operated solely in fully lit or completely dark environments, this new spark detector has the ability to adjust to ambient light. While old detectors set up in air ducts might go off due to a hole in the duct letting in light, this detector is able to recognize a new environment and avoid potential false alarms. “Not only do we want to detect, [but also] we don’t want to detect things that may not actually be sparks,” Peterson says.
GreCon’s additional new technology, the Intelligent Extinguishment Module, is set to release in Q4 2022. Peterson explains that the module is integrated into the extinguishment system and communicates with the command console, letting it know when the extinguishment system needs maintenance. The module can also be installed with a heating device in colder climates to allow for a “built-in temperature, cross-monitoring system” to help the extinguishment system avoid freezing in the winter. “This will tell them that they have some wear on their nozzles or valves that’ll need to be replaced, so it’ll communicate that to the console, providing operators with notices like ‘Hey, you’re not getting the right water pressure,’ or ‘Your nozzle needs to be replaced, it’s a little worn and not spraying appropriately,’” Peterson says.
Both of these technologies require access to electricity, and the extinguishment system requires water access for installation. The number of spark detectors needed per application varies depending on each customer’s needs.
Peterson outlines several of the statistics related to industrial fires and what causes them. There are over 30,000 industrial and manufacturing fires every year in the U.S. and Canada, he explains, and many of those are started due to dust. The ignition source varies depending on the industry, which is why flame detectors or high temperature detectors are key to catching the situation before anything starts on fire. Problem spots in plants often include the dust collector, grinders, dryers and silos.
FLAMEX
New technology from special hazard fire protection company, FLAMEX Inc. gives clients the ability to protect areas where a sprinkler system may not be an option. The company’s MX One Fire Protection Turbine has the ability to spray 1,000 gallons of water per minute
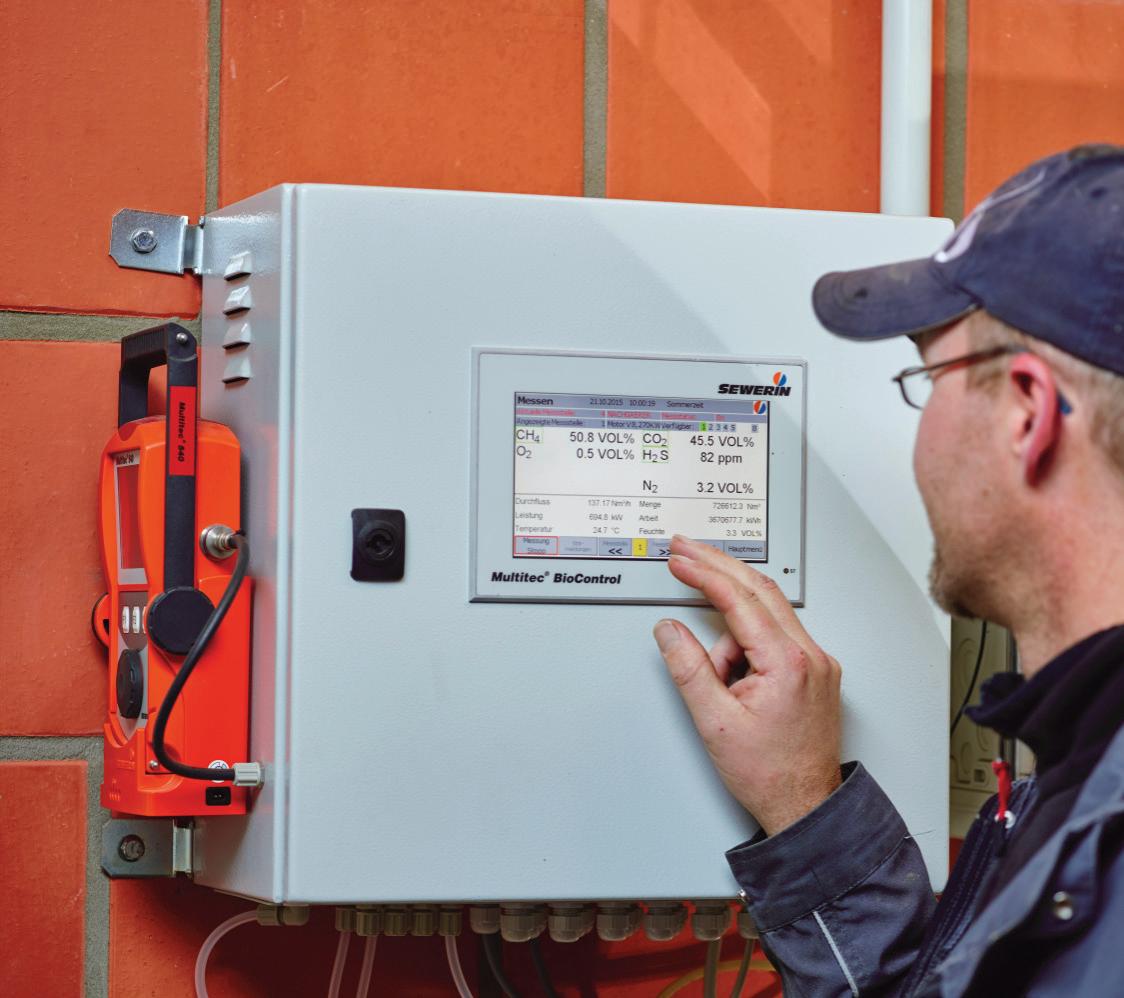
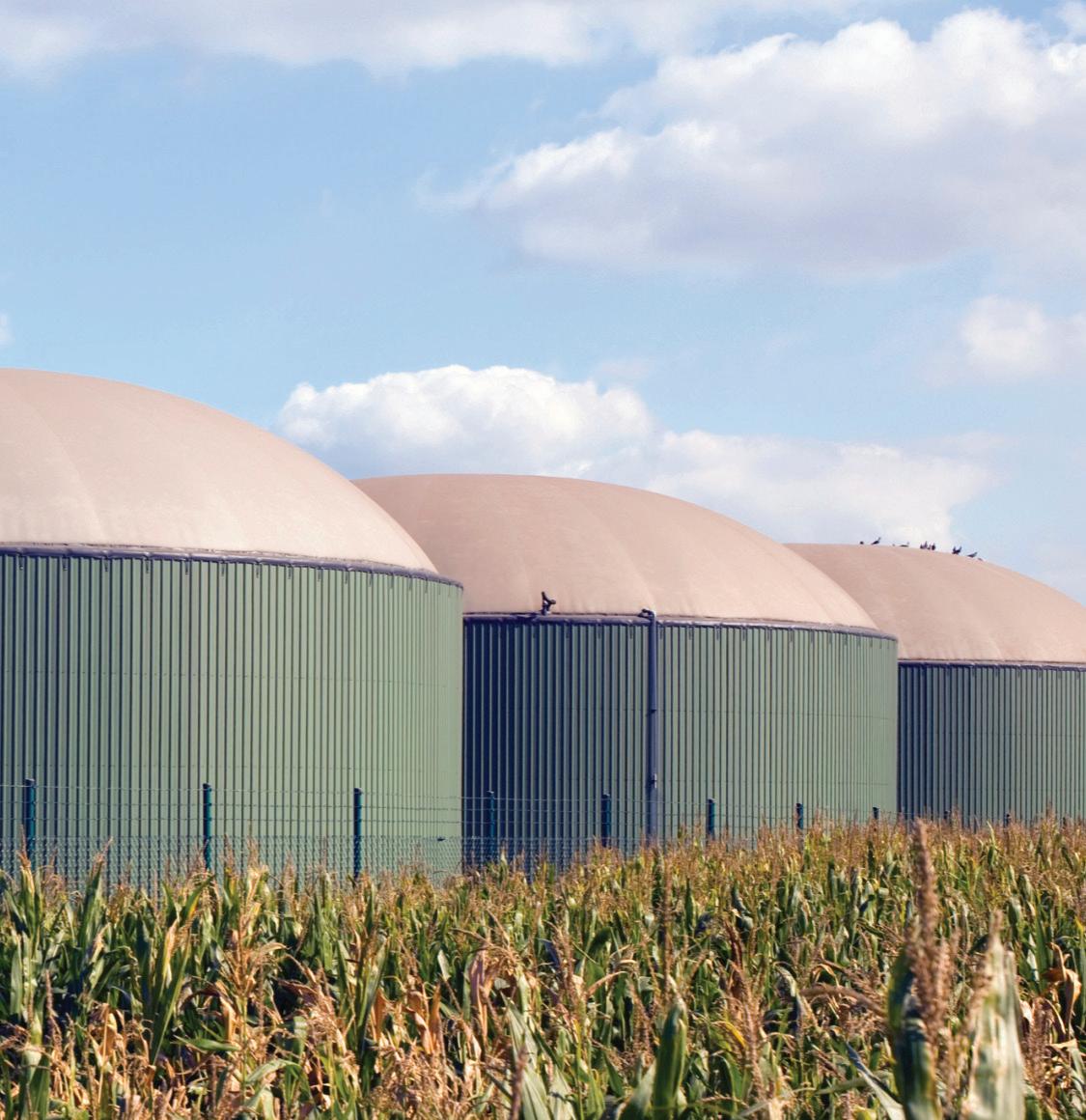
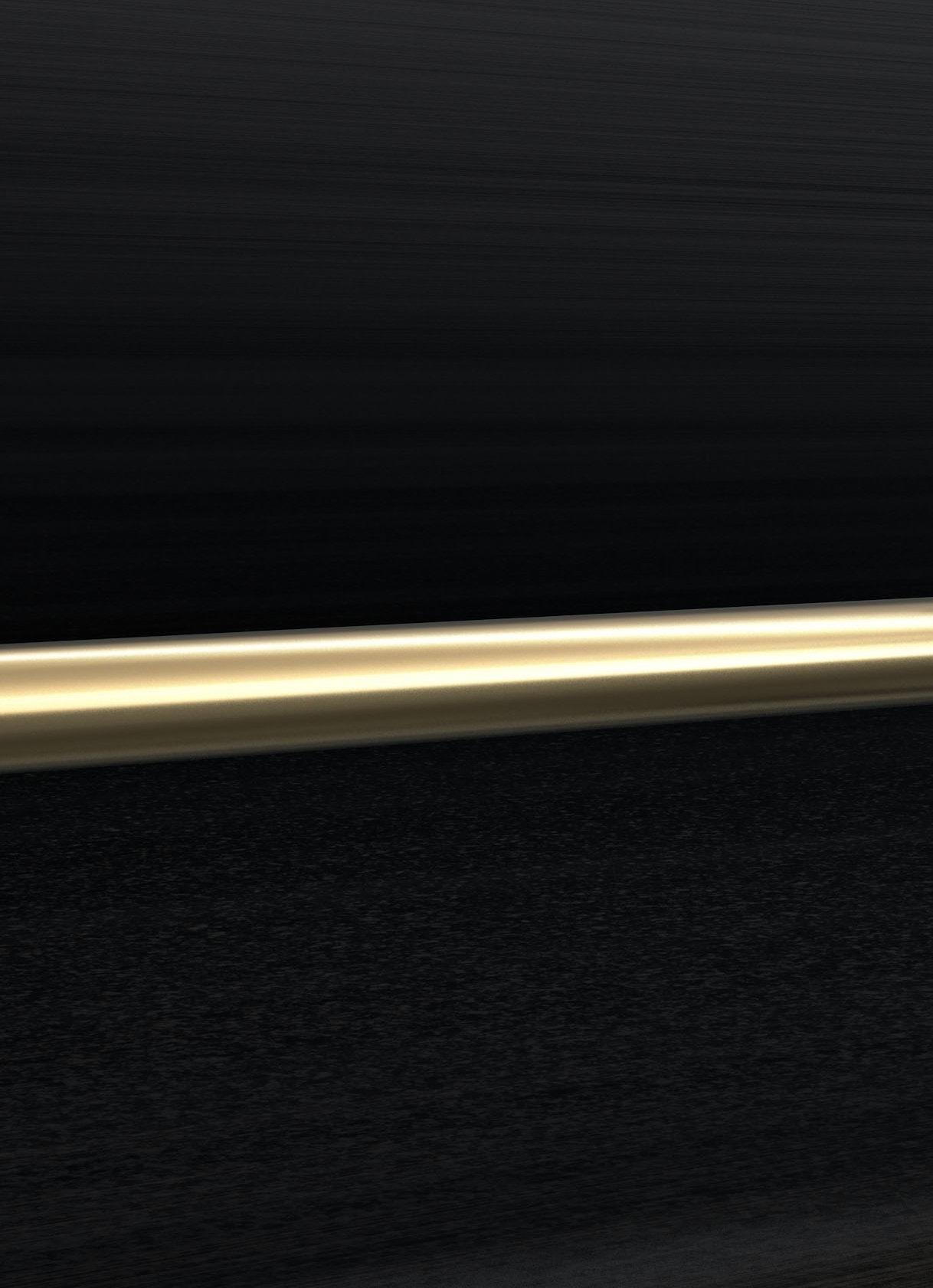
Fagus GreCon is set to release its Intelligent Extinguishment Module later this year.
PHOTO: FAGUS GRECON
at an 80-meter distance. The turbine can also cover the area in a fine spray at 500 gallons per minute. Ed Pridgen, FLAMEX vice president, explains that this technology can either be stationary, placed on a stand in an area the client would like to protect, or mounted on a trailer or fire truck, ready to be driven to the scene. The MX One also has the capacity to be linked to a flame detector and automated.
“We can automatically operate, so if a detector were to pick up a fire, we send a signal to the control panel, open up the deluge valve that would deliver the water to the base of it, and at that point, a signal would also be sent to the control panel of the MX One, telling it what position the MX One needs to be in and what type of spray scenario it needs to have,” Pridgen says.
The price for a stand-alone MX One turbine with remote control ranges from $140,000 to $160,000. If a client wants to automate the unit utilizing flame detectors and a control panel, it will add $40,000 to $50,000. The turbine is effective anywhere from an industrial setting or outdoor lumber yard to a rail yard or airport, and, if needed, can lay down a layer of foam instead of spraying water, Pridgen explains. The turbine has a 360-degree protection area, with an
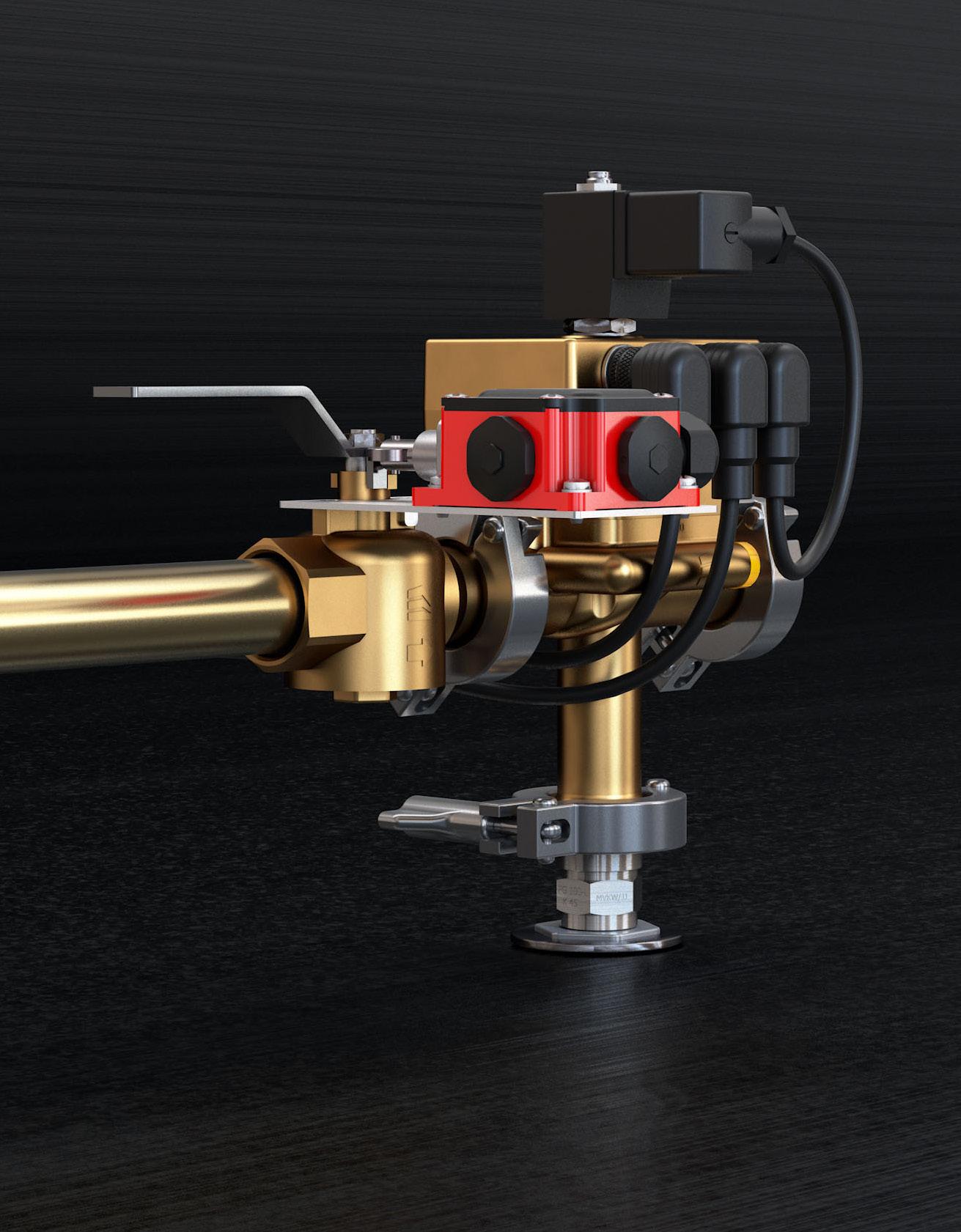
upward tilt of 43 degrees and a downward tilt of 19 degrees. The number of turbines needed by a client depends on the asset they are trying to protect.
“For example, let’s say you have a large building the size of a football field and you position the MX One at a common point, covering the building with flame detectors,” Pridgen says. “And say in section one, [the] flame detector goes into alarm. The MX One will actually align itself to protect that particular coordinate of the building, and if the fire spreads, then the actual single MX One can oscillate between the two points and protect the entire building.”
Pridgen describes the installation requirements for the technology. “It’s requires a six-inch line, a water supply line to the connection point of the MX One if this is a stationary unit,” he says. “If it’s a mobile unit, then the minimum requirements are either three two-and-a-half-inch fire hoses connected to a fire hydrant, or a single four-inch fire hose connected to a fire hydrant. So, that’s the water supply side. The electrical supply side is 480 volts, three-phase at 60 amps.”

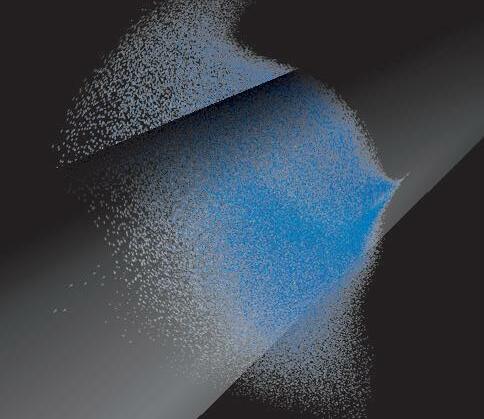
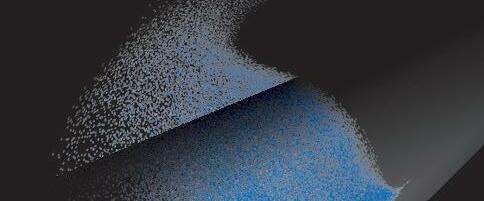
CV Technology
CV Technology is a manufacturer of explosion protection equipment including explosion vents, isolation, suppression and prevention systems. Its recently patented Interceptor QV, a clean air isolation device, gives operators an opportunity to protect low-dust air flow areas from explosions.
“A prime example is the clean air exhaust from the dust collector, so it’s pretty common in facilities that they want to return the air back to buildings or occupied areas for energy savings,” says Jason Krbec, sales and engineering manager at CV Technology. He calls it a “set it and forget it” device that keeps any dust collector explosions from propagating down the airline into the area to which the clean air is returning.
The QV Interceptor is unique in that it is the first device on the market to utilize flameless technology to isolate an explosion passively, according to Krbec. He explains that the technology uses a flame arresting medium—in this case, a stainless-steel mesh cartridge— that allows air to pass through without obstruction, but absorbs the energy and

The Flamex MX One Fire Protection Turbine system has a 360-degree operating range and enables the highly precise, targeted use of water mist from up to 80 meters distance.
PHOTO: FLAMEX
contains the heat from any flames. The device is set up inside the pipeline, and unlike many other explosion isolation devices, it does not have a minimum distance requirement since its presence is static in the pipeline.
Once bolted inline, the QV Interceptor works on demand, with no external electrical requirements. The device also has some optional features and benefits, such as a sensor that can send the control panel a notification when it has been ex-
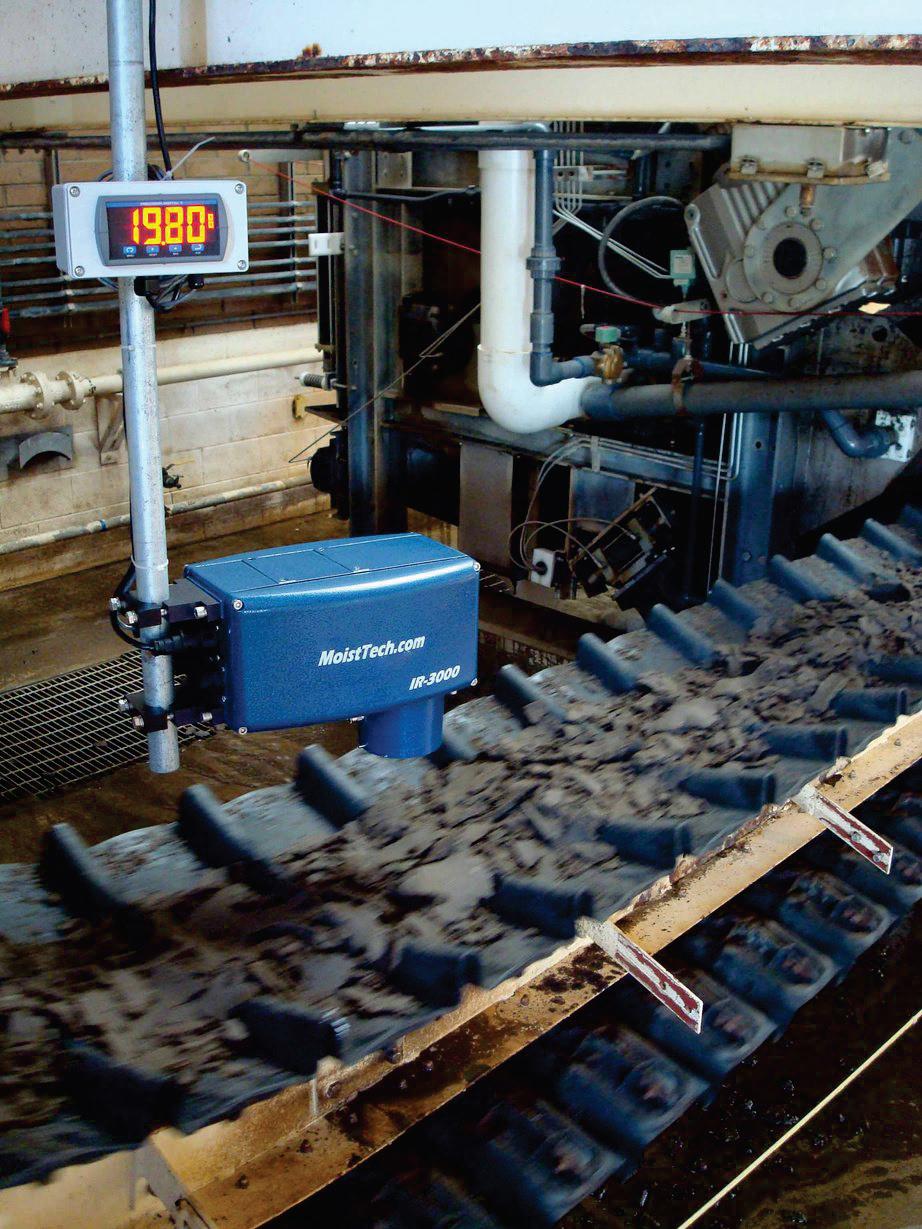
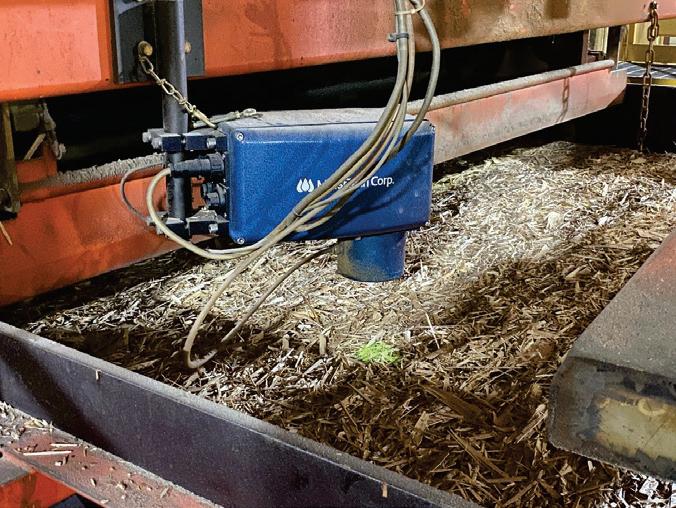
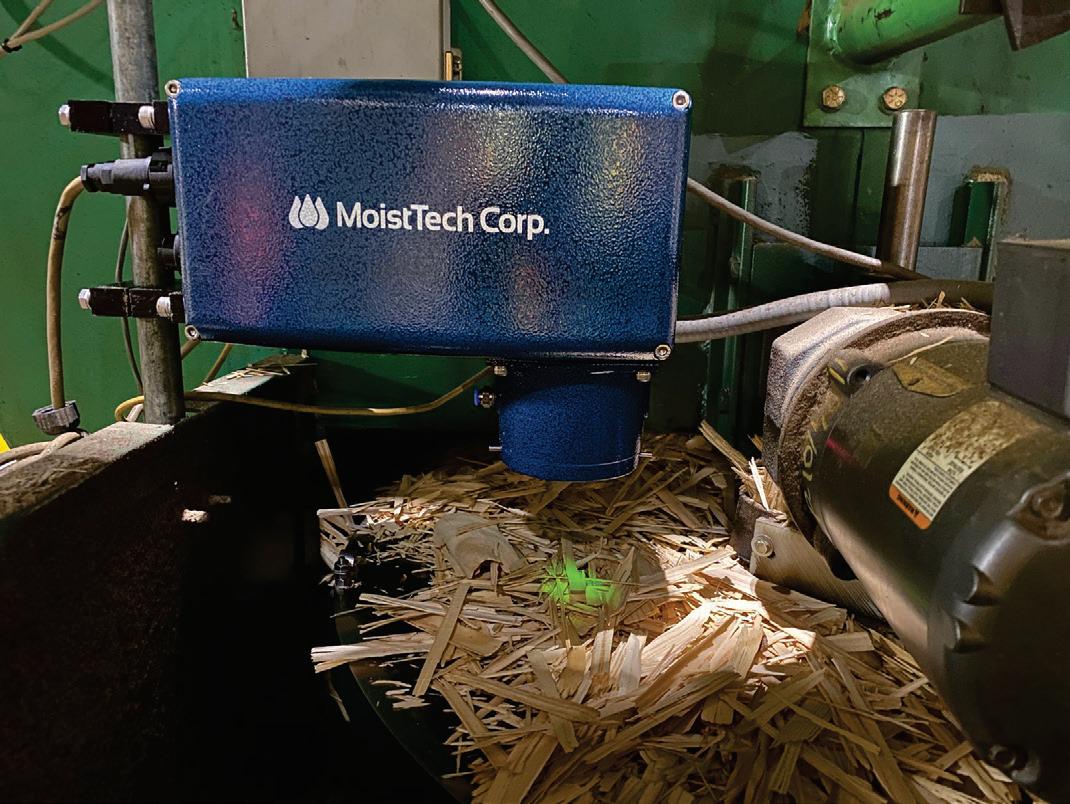
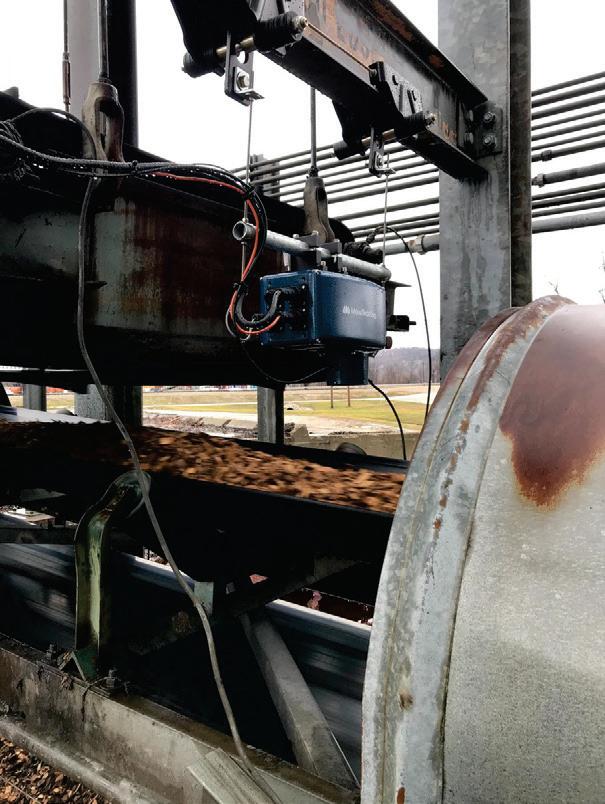


The core feature of CV Technology’s Interceptor-QV is the stainless-steel mesh cartridge, which is based on the flameless Quench Tubes the company has been applying for over 25 years.
PHOTO: CV TECHNOLOGY
posed to a flame, and a dust monitor to notify operators when the stainless-steel mesh needs to be cleaned, a task that can be accomplished in-house.
There are two primary benefits of installing an Interceptor QV in a biomass facility, Krbec explains. One is reduced down time due to the fact that the technology requires little maintenance, and the other is that the technology is 30 to 40% less expensive than traditional explosion isolation technologies.
“I’ll just say combustible dust is a growing issue, especially in biomass where they’re handling wood materials or biochar,” Krbec adds. “As materials get finer and finer in powders, they become easier to ignite and have increased combustibility characteristics. Explosion protection is dual-purpose: on the one side it protects your employees, on the other side it protects your process. So, there are two reasons as to why it becomes really critical.”
Author: Katie Schroeder kschroeder@bbiinternational.com www.biomassmagazine.com
Precision On-Line NIR Moisture Measurements
For Real-Time Quality and Process Controlss Control PrediktIR II Moisture Gauge
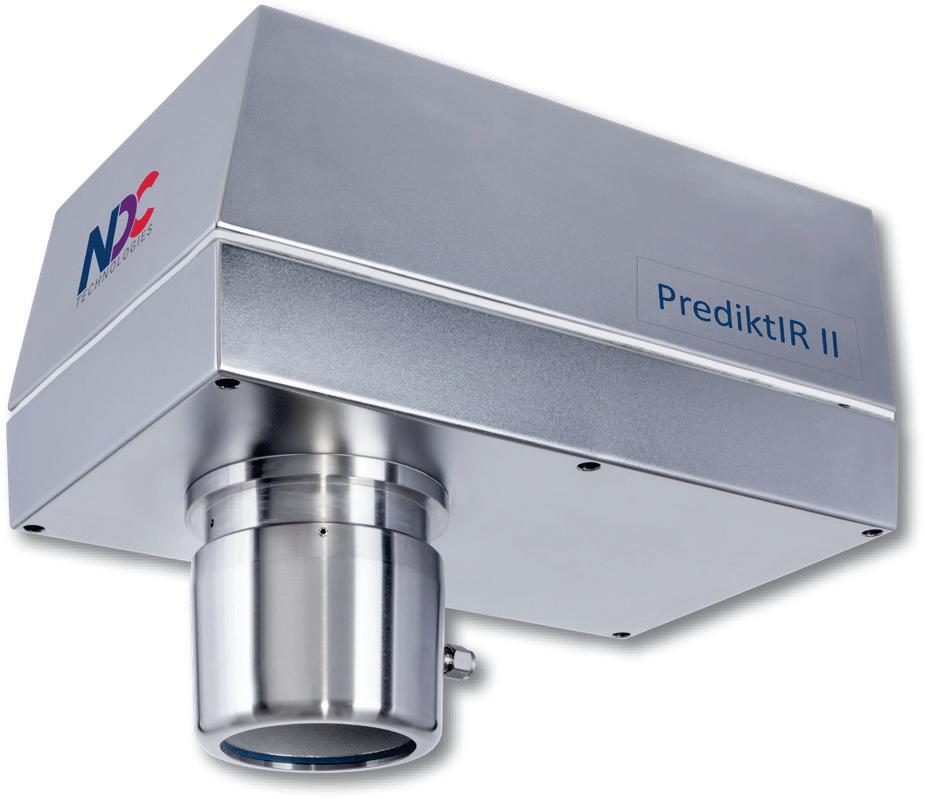
Woodchips Pellets Sawdust And other Biofuels & Biomass
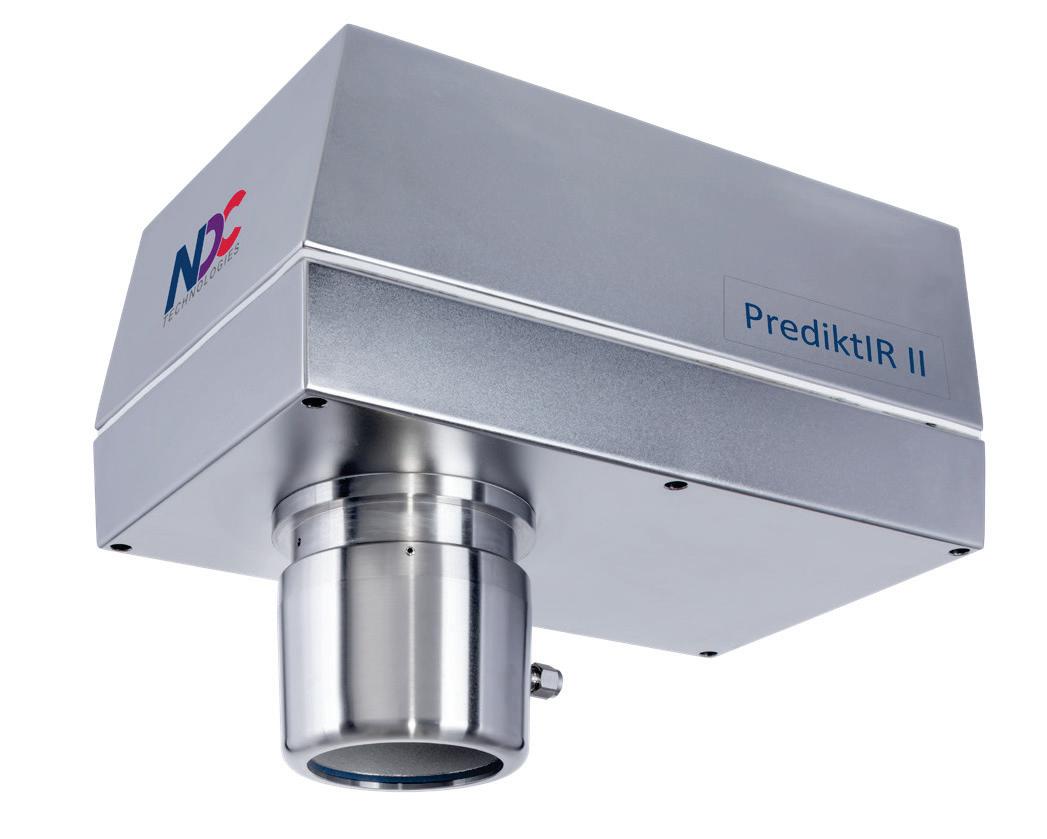
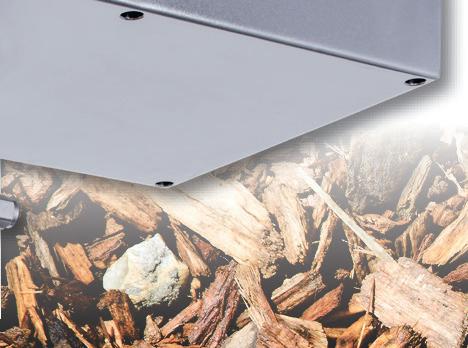
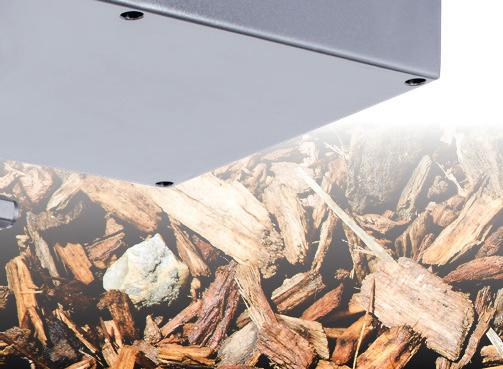
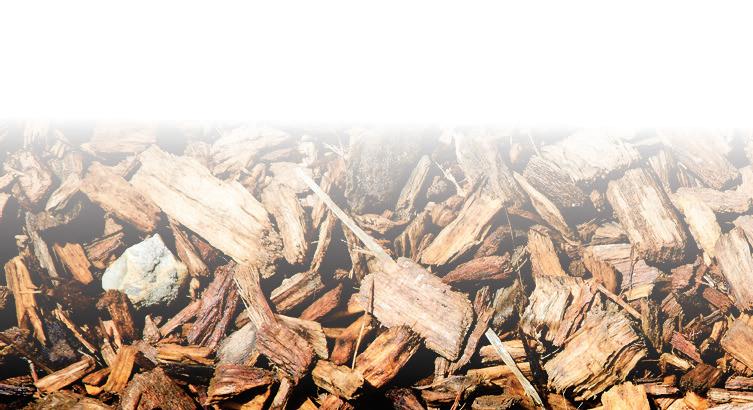

Learn More About Our Solutions.
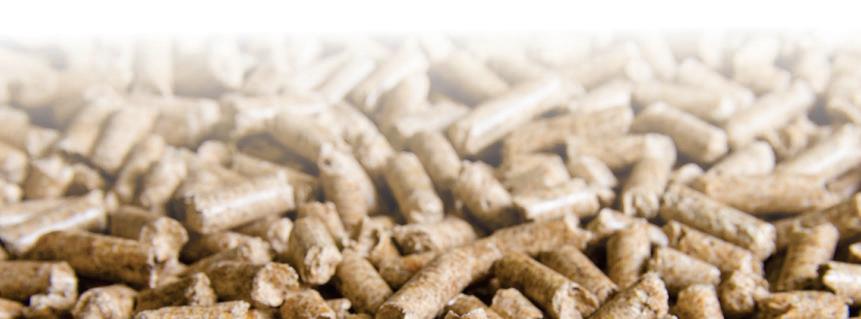
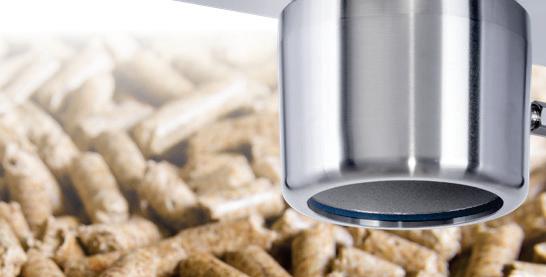
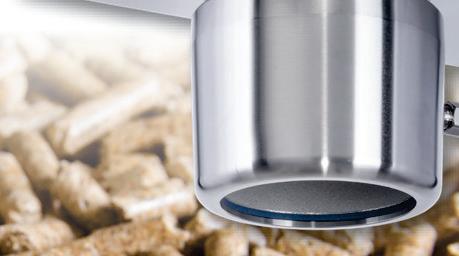
Enhance Product Quality Improve Production Efficiency Reduce Fossil Fuel Consumption Automate Drying Processes