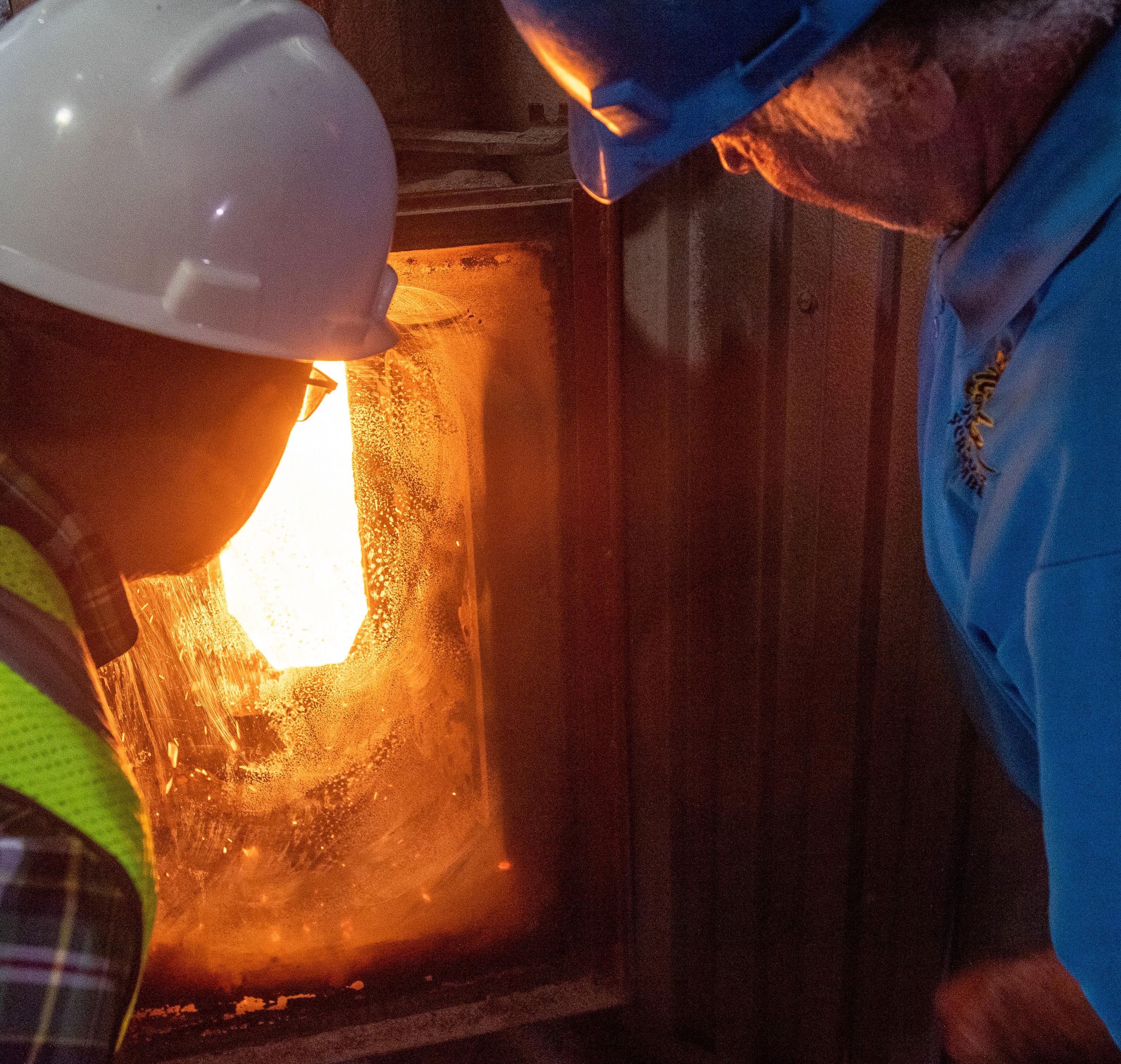
9 minute read
WOOD WASTE
MINNESOTA BIOMASS
REVIVAL
Urban centers are expecting the current onslaught of EAB-killed wood to continue, but lost infrastructure will need rebuilding for woody biomass markets to rebound.
BY SUSANNE RETKA SCHILL
Minnesotans are looking for a biomass revival—a combination of the growing movement toward decarbonization, expectations of continued high natural gas prices, and the need to better manage the state’s forest resources. But first, they need to overcome hurdles left by shifting policy impacts and earlier boom and busts. “Back in mid- to late 2000s, there was a surge of interest in trying to use woody biomass for bioenergy, biofuels and byproducts,” explains Eric Schenck, executive director of the Minnesota Forest Resources Council. A 2007 state renewable energy standard set a goal of 25% renewables by 2025, which supported early biomass projects. “At one time, three or four facilities were doing cogeneration using biomass for thermal and electrical energy. There developed, in response, a forest products industry, with loggers and people harvesting biomass, who bought equipment and got geared up to harvest and haul it. Then the market started to go away, and we had a bunch of people with equipment that had no use for it. A lot got sold out of state.”
The loss of the biomass market was partly due to economics favoring natural gas and partly policy driven, with federal policies restricting eligible woody biomass and tax credits favoring wind and solar. In Minnesota, wind and solar began to fill the renewable energy standard goals. In addition, the state’s largest utility had been required to purchase biomass power as a condition for its nuclear power permit. When that was repealed
Hibbing Public Utilities power plant operators take a look into the fire chamber, where 3,000 tons of wood chips are turned into electrical power each day.
PHOTO: MARK SAUER, MESABI TRIBUNE
in 2018, only one cogeneration facility kept firing wood: St. Paul Cogeneration in the state’s capitol.
Urban Wood Resource
The St. Paul utility’s use of woody biomass is based more upon providing an outlet for urban waste wood than meeting the state’s renewable power standard, so it survived the policy shifts.
The facility, launched in the mid-1980s, began cofiring wood chips with coal in 1997 to provide heating and cooling to St. Paul’s downtown area through District Energy St. Paul. Cogeneration was added in 2003. The system generates 33 MW of electricity and provides heating and cooling for 33 million square feet of building space, which includes the state capitol grounds, downtown offices and businesses, hotels and residential properties.
Today, woody biomass comprises about 50% of the boiler fuel, followed closely by natural gas. Fuel oil serves as a backup and a large solar thermal array supplies about 1% of the annual energy load. Coal is no longer used. The goal is to decarbonize entirely by 2050, says Ken Smith, CEO of Ever-Green Energy, the District Energy St. Paul subsidiary that manages St. Paul’s system along with nine others in five states.
Over the decades, they’ve learned to manage supply, Smith says. When the system first began cofiring with wood chips, inadequate infrastructure meant another subsidiary was created to manage and process urban waste wood from the Twin Cities Metro area. There’s an

ebb and flow to urban wood waste, he adds. In the spring, volumes drop as more gets used for mulching. In the fall, deer hunting season slows down deliveries. Neighboring cities as far as 70 miles away have contributed their wood waste and, when needed, forest residuals were trucked in from central or northern Minnesota.
Today, there are no concerns about wood supplies—the wood yard closes for deliveries at times, because it’s full. Ash trees killed by the emerald ash borer (EAB) are adding major volumes to the regular tree trimming, storm damage and construction waste. EAB supplies are expected to last for more than a decade, Smith says. Minnesota has more ash trees than any other state, comprising around 15% of the Twin Cities’ canopy, he explains, and some communities in the state have 60% ash. “We’re one of the very few outlets for that material. If we didn’t continue, there is no Plan B. There is no alternative.”
Nonetheless, Ever-Green faced its own challenge with its utility partner, regulators and policymakers when renegotiating its power purchase agreement. “We’ve been in conversation for seven years,” Smith says. “It took a while for folks to get their minds wrapped around the important role this facility has in managing tree waste.” While natural gas was a lower-cost fuel favored by some, “Where are you going to go with 250,000 tons of tree waste every year?” Smith asks.
Across the state, natural mortality of trees from storms, changing climate, disease and invasive insects covers as much or more ground every year than what gets harvested, Schenck says. On top of that, there is an accumulation of wood residuals from the state’s forest products



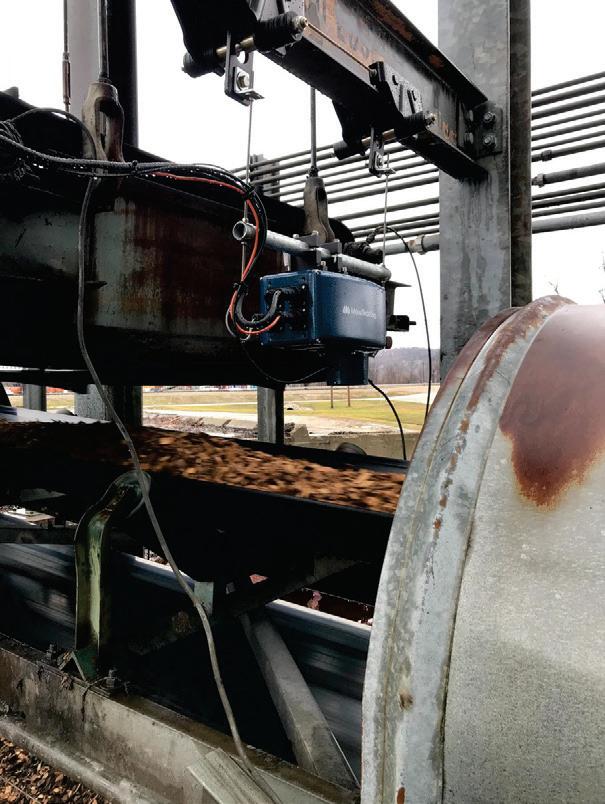

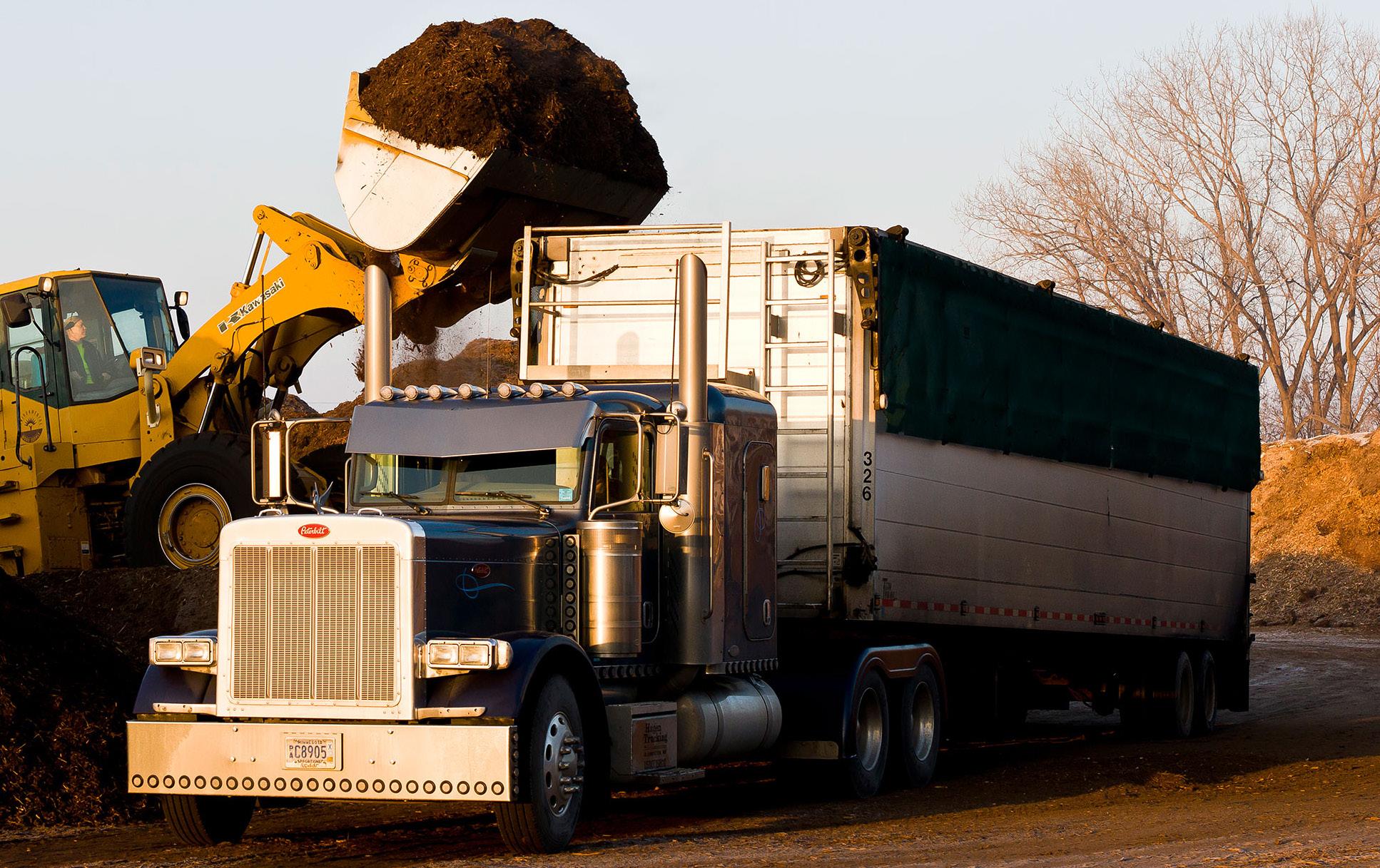
(Left) A truck unloads nearly 30 tons of wood chips into the Hibbing Public Utilities biomass power facility. The plant burns 3,000 tons of wood per day.
PHOTO: MARK SAUER, MESABI TRIBUNE
(Right) Roughly 260,000 tons of wood chips are supplied to St. Paul Cogeneration annually. The use of biomass keeps $12 million in the local economy each year.
PHOTO: EVER-GREEN ENERGY
industries but few outlets, meaning a lot of slash is not being managed optimally for regrowth. Back-of-the-envelope estimates suggest there’s about 5 million tons of dead wood and slash left in the forest every year, he says.
The Minnesota Forest Resources Council, which Schenck directs, is supporting revived efforts to better utilize those forest resources. A January resolution supports statewide fuel or energy standards for low-carbon renewable biofuels from woody biomass or other feedstocks and commits to developing strategies and recommending policies to attract new markets. “The governor had a big administrative push this past year to develop climate friendly policies that cut across all sectors—agriculture, forest, energy, transportation,” Schenck explains. “Part of this is looking at biomass again as a low-carbon fuel alternative, along with other uses.”
From Smith’s perspective, interest in woody biomass indeed is growing, thanks to higher natural gas prices, “but is it among the top solutions? We’re not there yet,” he says. Woody biomass is not likely to become the majority fuel source, he continues, adding that the St. Paul utility would never rely on just one fuel source, “but it can be an important role if it’s done sustainably, and if you’re dealing with waste streams.”
Biomass is playing an important role in many places around the world, he adds. “It tends to be a small percentage of the overall energy mix, but it plays an important role because it’s more of a base load.”
Smith suggests we’re in an energy system transformation, and not just a transition. The built environment—buildings and industry—will be the hardest to decarbonize, he says. “Between buildings and industry in Minnesota, they make
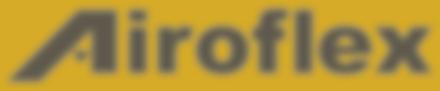
YOUR SOLUTION FOR BULK MATERIAL HANDLING
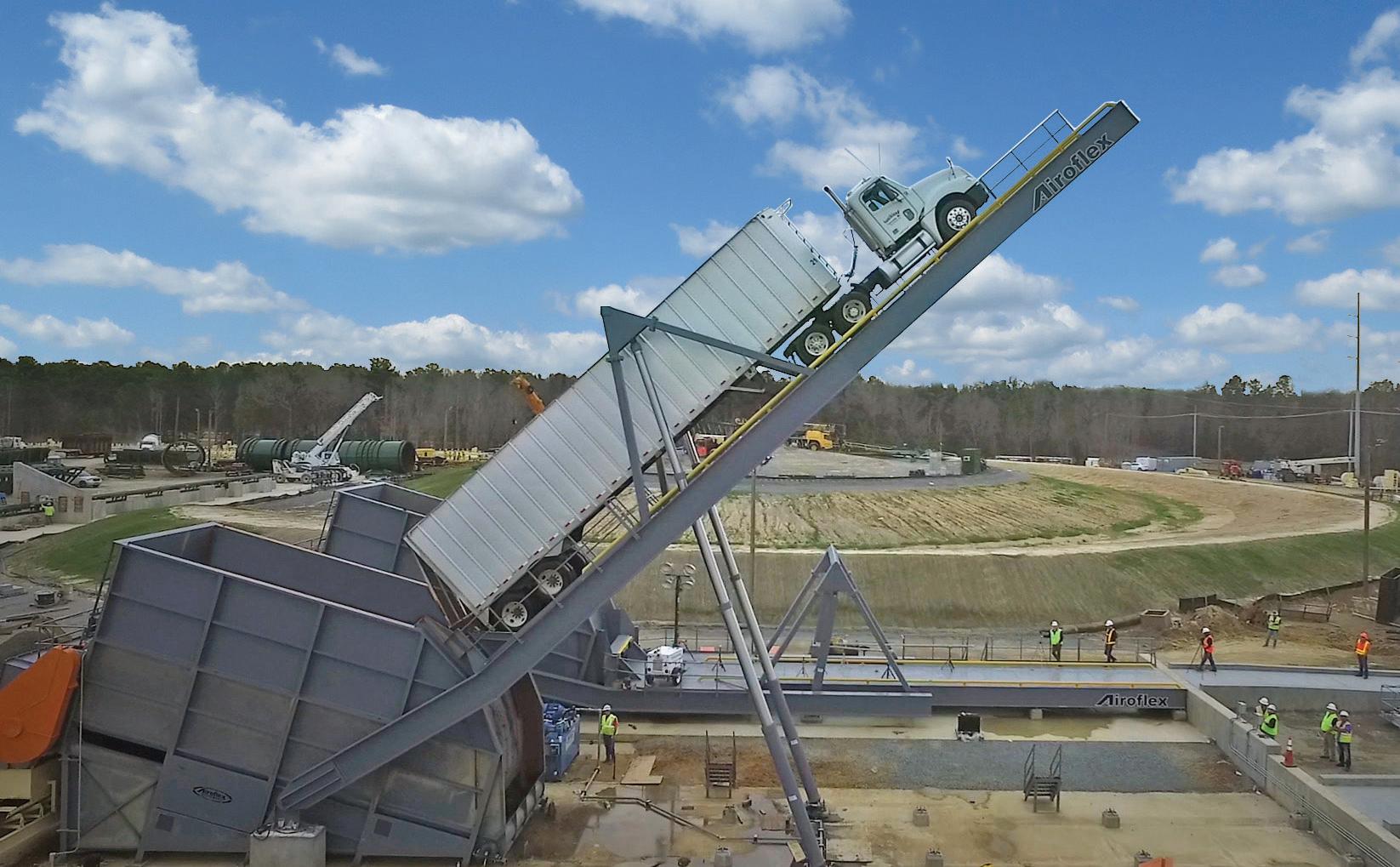
Pellets Woodchips Biomass
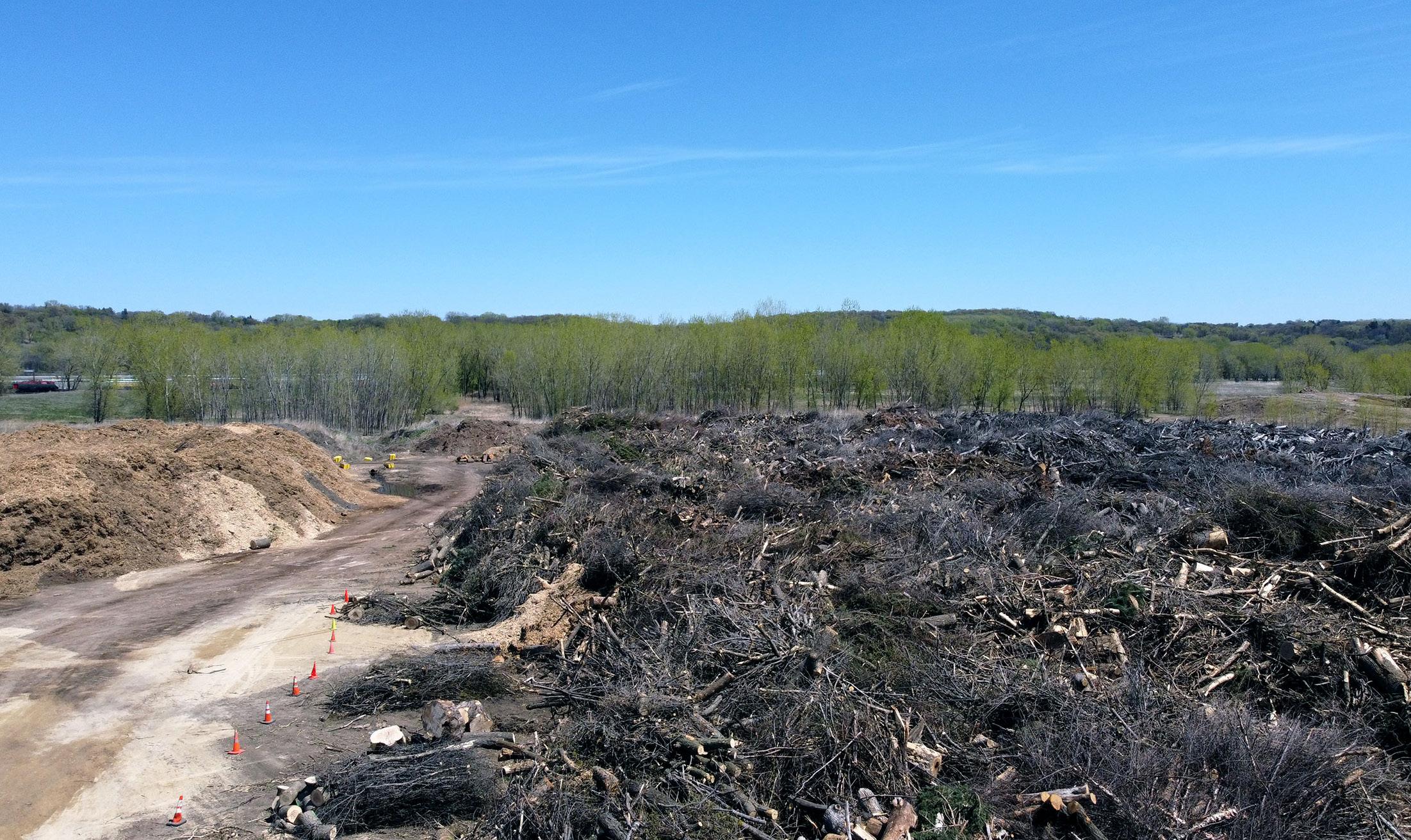
Across Minnesota, natural mortality of trees from storms, changing climate, disease and invasive insects covers as much or more ground every year than what gets harvested.
PHOTO: EVER-GREEN ENERGY
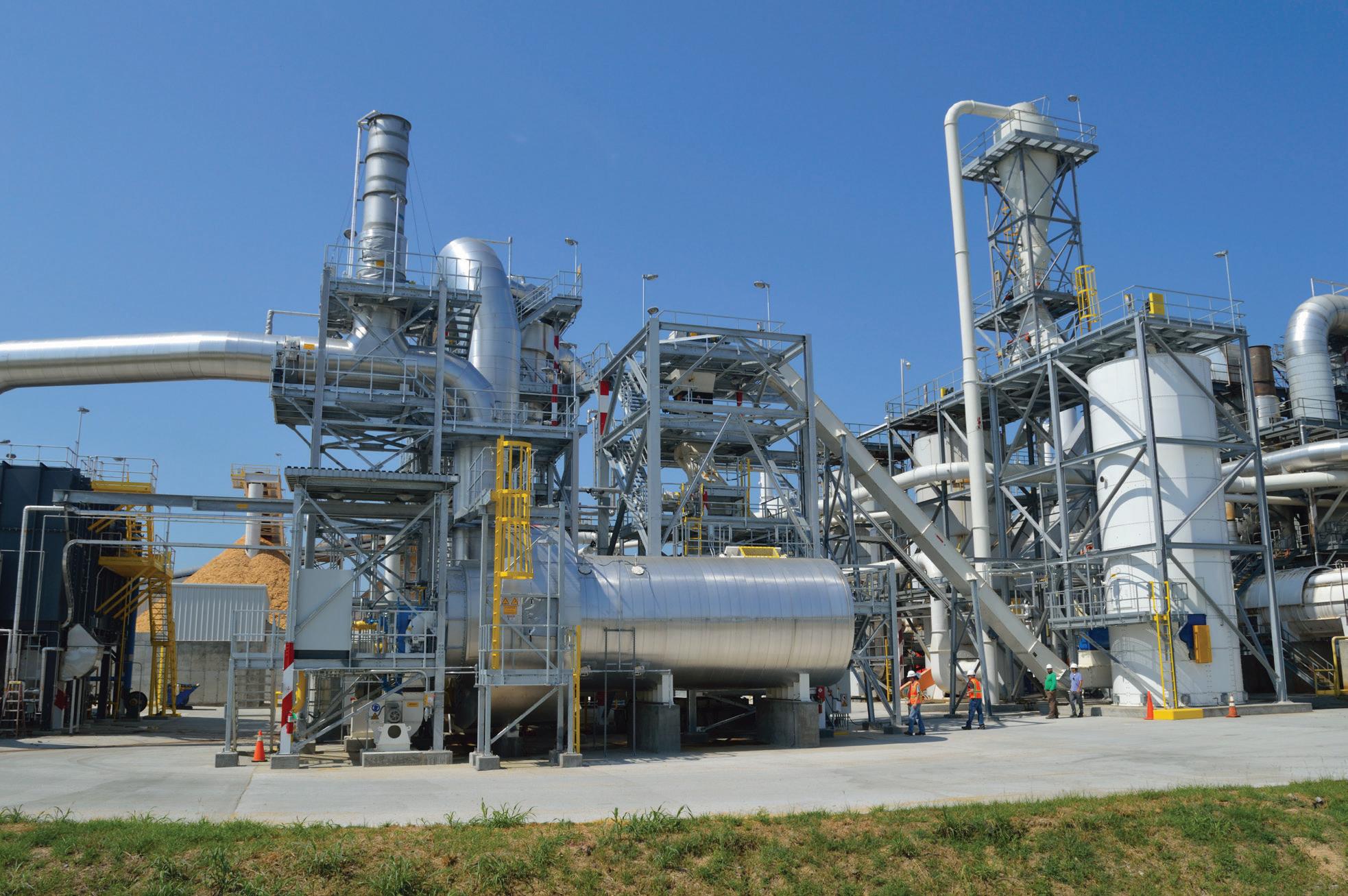
up 70% of where our energy goes. It won’t be a transformation that occurs necessarily building by building. It’s going to have to be done community by community.” Ever-Green has worked with a number of campuses—colleges, hospitals, communities—that are planning for the future of their district heating. Each defined area, he suggests, will be looking at available resources. Wind and solar may not be available to all, and woody biomass will make sense in some areas, he says.
Forest Fuel
Surrounded by northern Minnesota forests, Hibbing, Minnesota, is one of those places that illustrates the opportunities and challenges for woody biomass in the state. This year, Hibbing Public Utility upgraded and fired up the wood boiler it installed in the mid-
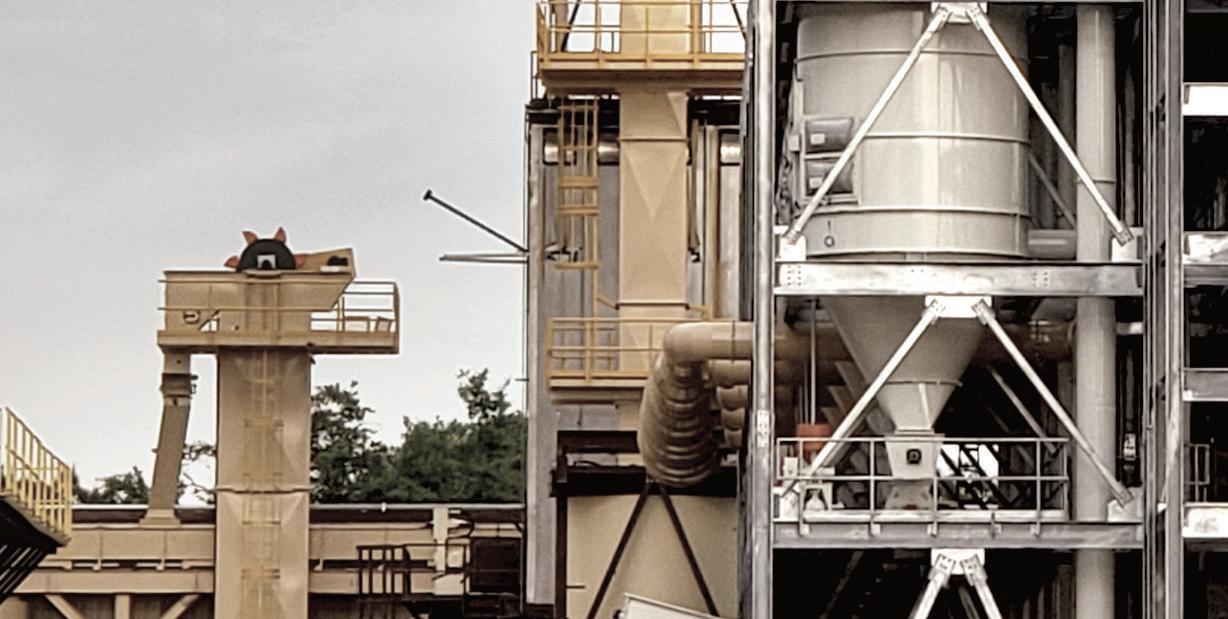
2000s and mothballed in 2018. The city has phased out coal and plans to increase the use of woody biomass. “A year ago, we were crazy for going back to biomass,” says Luke Peterson, general manager of Hibbing Public Utilities. “Now everybody’s going back to biomass.” The goal, he says, is not about using the lowest-cost fuel—particularly considering wood prices have gone up alongside natural gas—but making Hibbing a more sustainable community. One that is more resilient, relies on locally sourced resources and supports local jobs.
The Hibbing cogeneration plant generates about 33 MW, with about 10 MW exceeding local needs that can be sold to the grid, Peterson says. The district steam heating system makes a mile loop around the city, serving about 1,000 customers—including the hospital, several large civic buildings and residents.
Economics and the work involved in sourcing and managing the burning of wood chips were the main reasons the wood boiler was mothballed, Peterson says. Returning to woody biomass not only preserves 20 jobs at HPU, but is supporting at least 20 jobs in the community. “It requires this whole ecosystem of people and processes,” he says. “It can be a lot of work, but it’s worth it to explore and develop those value chains.” The utility was fortunate, because two local loggers kept their chippers when the market disappeared, he adds. With a goal of burning 200,000 tons of wood chips annually, the utility is finalizing an agreement to take residuals from a pallet manufacturer 60 miles away to add to local supplies.
The long-term goal is to eliminate fossil fuels entirely and use the city utility as a catalyst for economic transition. Possibilities include hydrogen and methanol, and attracting complementary industries such as cross-laminated timber. Another idea is to explore waste heat utilization, Peterson says, citing Iceland’s use of waste heat to melt snow on sidewalks and on the soccer field.
Peterson advocates for a restorative development approach that looks at total costs, not just financial ones, and takes a long-term view of sustainability. “What is it about wood that creates value,” he says. He’d like to see each log get managed for its best value, with the waste chips being used for cogeneration. Better forest management reduces debris that contributes to forest fires. New equipment requires new skills that build workforce capabilities. “There are all these offshoots, not just the tech, but the whole process and humans involved in taking care of the forest,” Peterson adds. “Like the loggers—you wouldn’t believe how many multigenerational vendors I have supplying wood to the power plant. What’s that family story worth? That means something, because that’s people, building a network for the future that has a strong family tie to the land, and also a hard work ethic.”

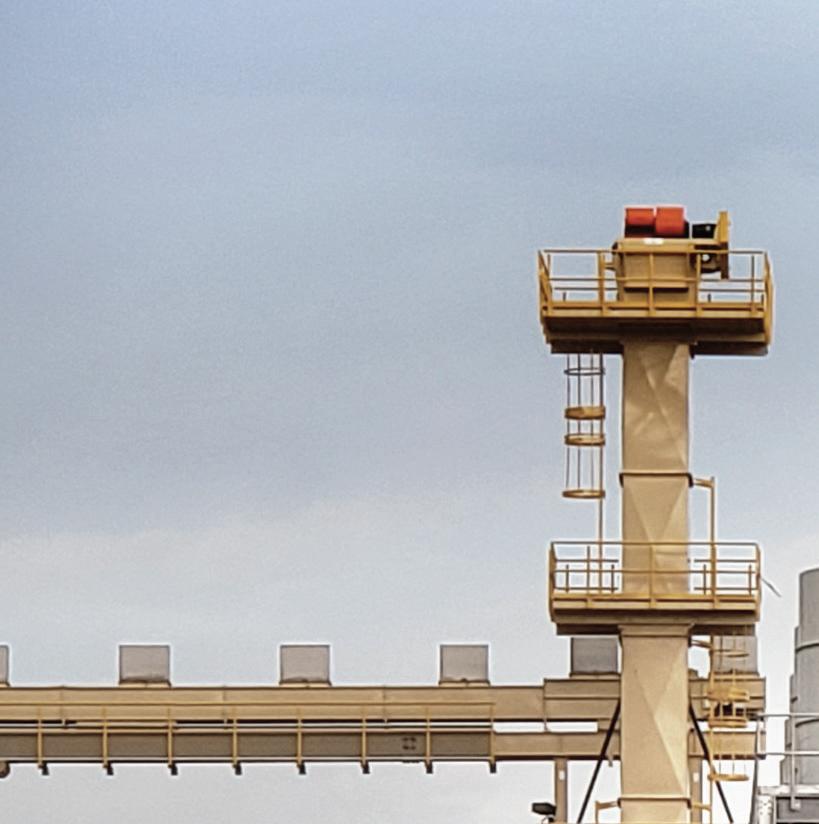
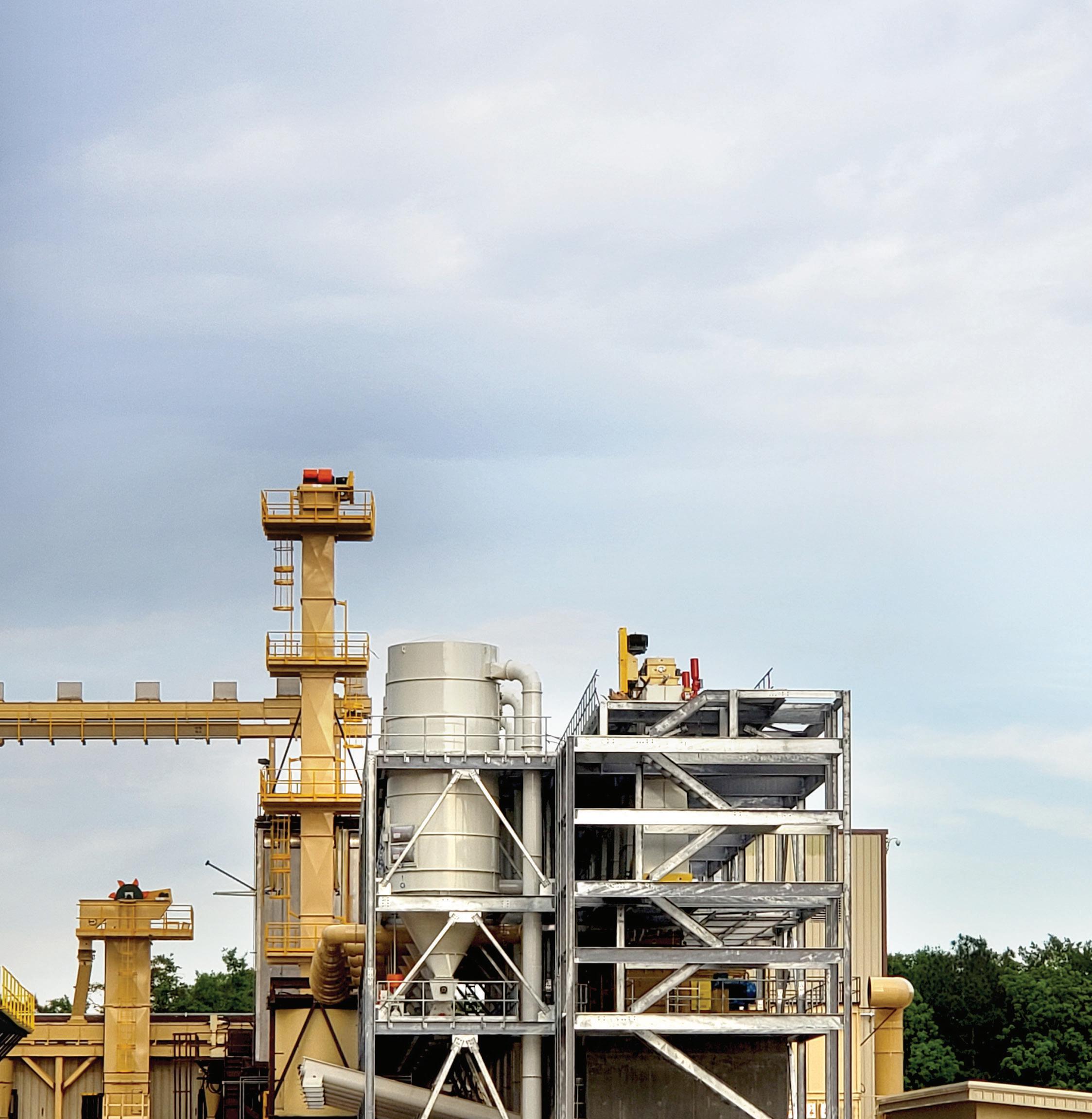
Contact: Anna Simet asimet@bbiinternational.com