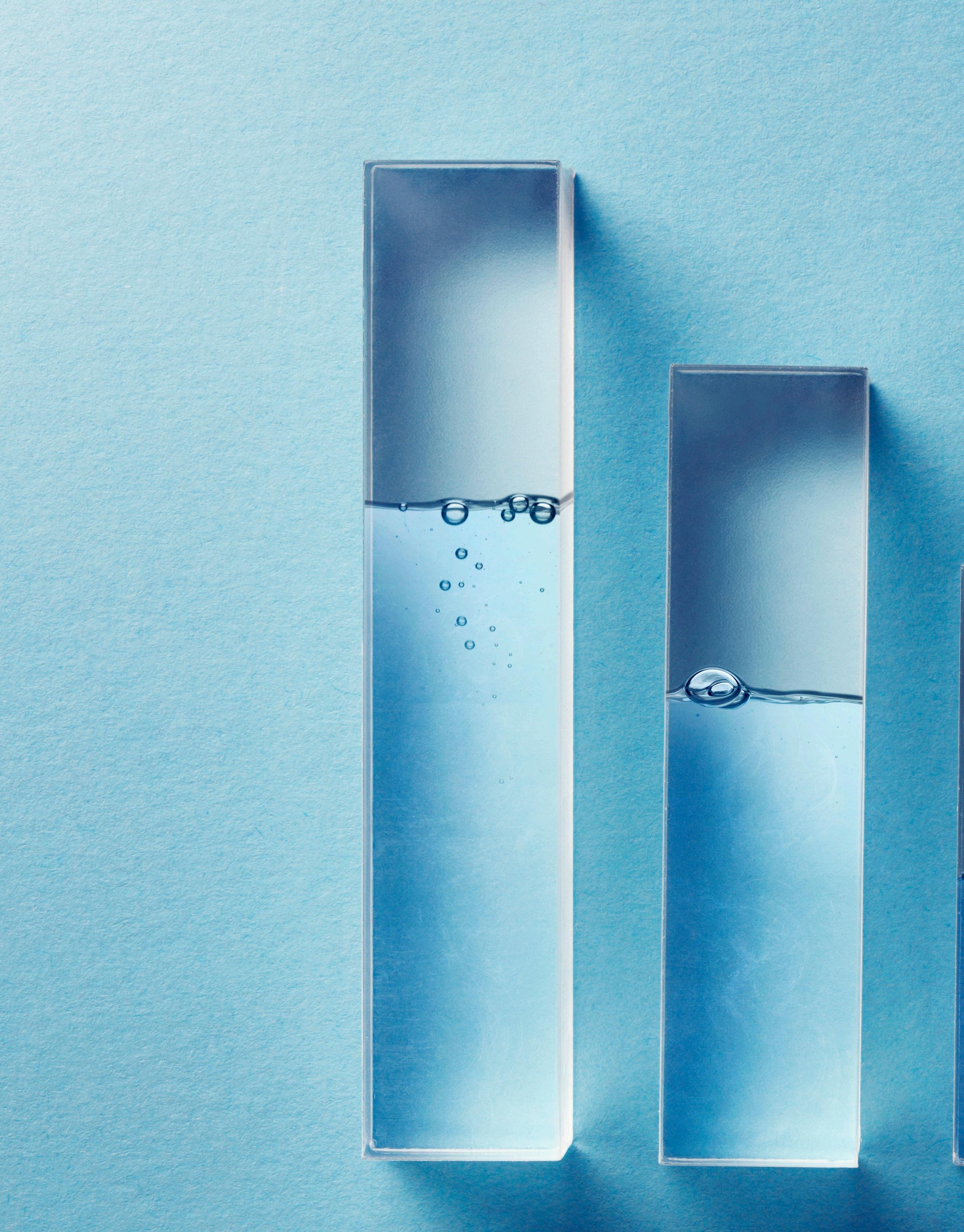
9 minute read
WATER
STRATEGIES TO STEP DOWN
WATER USE
At the facility level, water experts and engineers deal with issues big and small—from advanced cooling water analyses to sealing solutions and RO membranes—to reduce the use of H2O at ethanol plants. By Luke Geiver
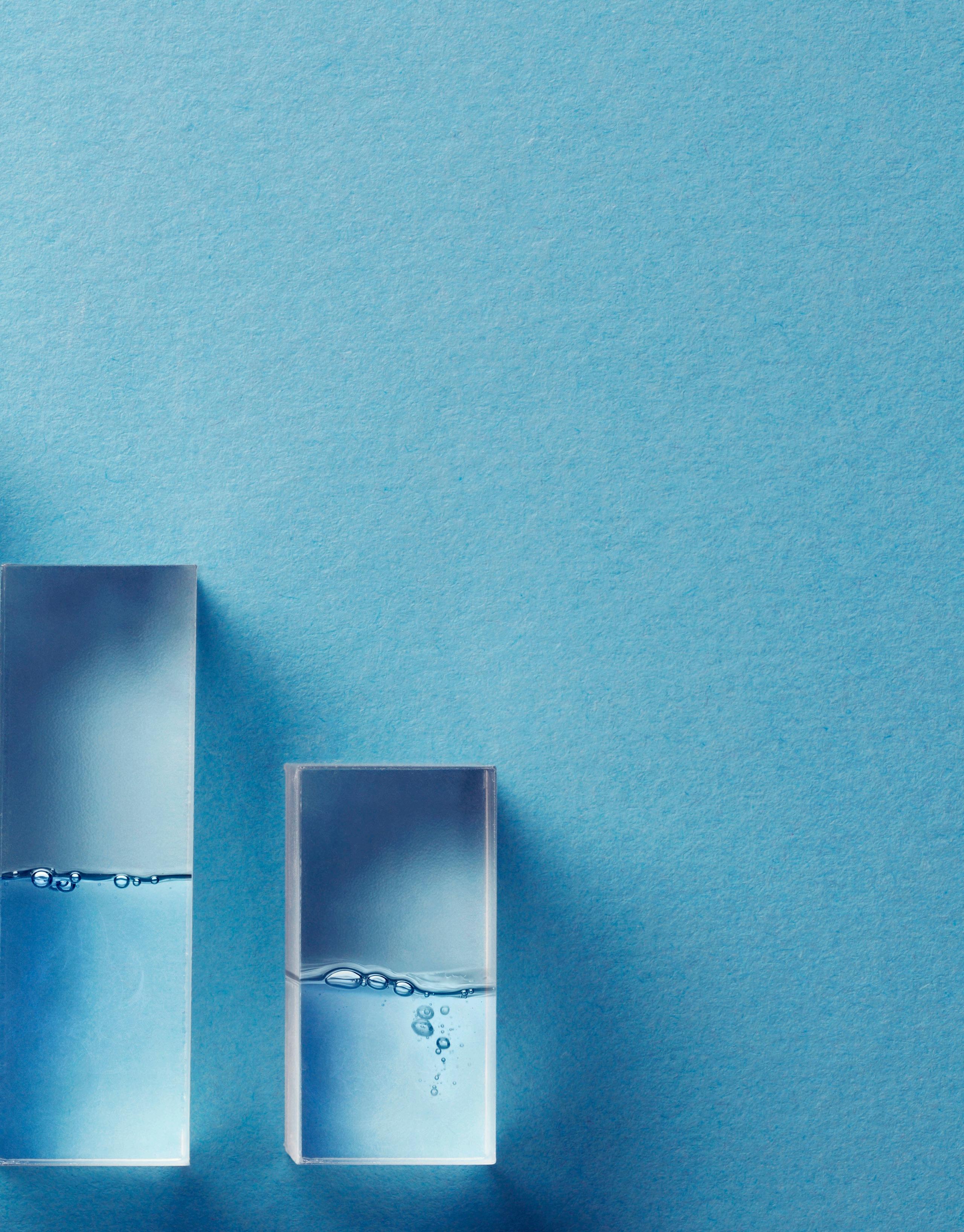
Deploying efficient and cost-effective water management solutions at ethanol plants is a topic that might not seem as important as carbon intensity score talk, and understand-
ably so. But at this past summer’s International Fuel Ethanol Workshop and Expo, the world’s largest gathering of ethanol producers, a panel on water was popular. Three panelists provided invaluable insight, helping plant engineers and others understand water-related issues—big and small—that ethanol plants and their service providers deal with.
Water Use: The Next CI Score
For the big-picture view, Quinn Hanson-Pollock, industry technical consultant from Nalco Water, provided a deep-dive into optimizing the utility water balance at an ethanol plant. Thinking about the world’s water challenges as a whole helps to explain water usage issues at the plant level.
By 2030, if nothing changes, global water demand will outpace supply by 56 percent, he noted in his presentation. More than 40 percent of the global population is affected by water stress. Nearly threefourths of all companies have water use reduction goals, but 85 percent lack the tools to achieve them. That is where Hanson-Pollock and his team can help.
His team works under the following understanding. Cooling tower water needs make up well over half (60 percent) of an ethanol plant’s utility water use. Next is reverse osmosis feed water for steam (19 percent), followed by scrubber water (17 percent) and then backwash/miscellaneous (4 percent).
Water consumption is also affected by the limitations of the production process itself. A cooling tower must reject heat via evaporation. From Nalco Water’s Cooling Tower Engineering Evaluations, a typical ethanol plant cooling tower rejects 13,500 Btu/gal of ethanol produced. A 100 MMgy plant has a cooling water evaporation rate of 314 gallons per minute (gpm), which results in 1.62 gallons of water use per gallon of ethanol. Scrubber water accounts for roughly 0.62 gallons of water per gallon of ethanol. Direct injection steam and deaerator venting accounts for 0.42 gallons of water per gallon of ethanol. Backwash and miscellaneous accounts for 0.13 gallons of water per gallon of ethanol.
To optimize all of those numbers, Hanson-Pollock says an ethanol plant’s water treatment provider should help formulate the facility’s strategy to maximize reverse osmosis recovery (increasing recovery from 65 percent to 80 percent reduces the water intensity of a plant by 0.13); maximize cooling tower cycles (increasing cycle times from 4 to 5 reduces water intensity by 0.14); optimize softener run-lengths or formulate a plan to recover clean water from the regen cycle; and evaluate creative solutions.
Managing the percentages related to water usage starts with recognizing the current state of the industry. While most plants are focused on carbon intensity (CI) scores, the time will come when they need to look at water intensity grading or something akin to it, Hanson-Pollock says. Right now, ethanol plants are modern facilities that have their water makeup streams metered. The next step is to totalize and trend that data to identify areas to optimize. In the future state of ethanol, he says, water will have continuous monitoring of water distribution, utilization and cooling tower performance.
In fact, Naclo has already started performing cooling tower analysis work. The main issues they’ve found, so far, are related to fermentation temperature, especially during hot and humid conditions. There are also typical issues with recirculation flow rate, water distribution among heat exchangers, water distribution at the tower, nozzle performance, air flow through tower, biofouling and scale or iron deposition. “Improving visibility on cooling water flow will allow for plants to maximize performance and production,” Hanson-Pollock says.

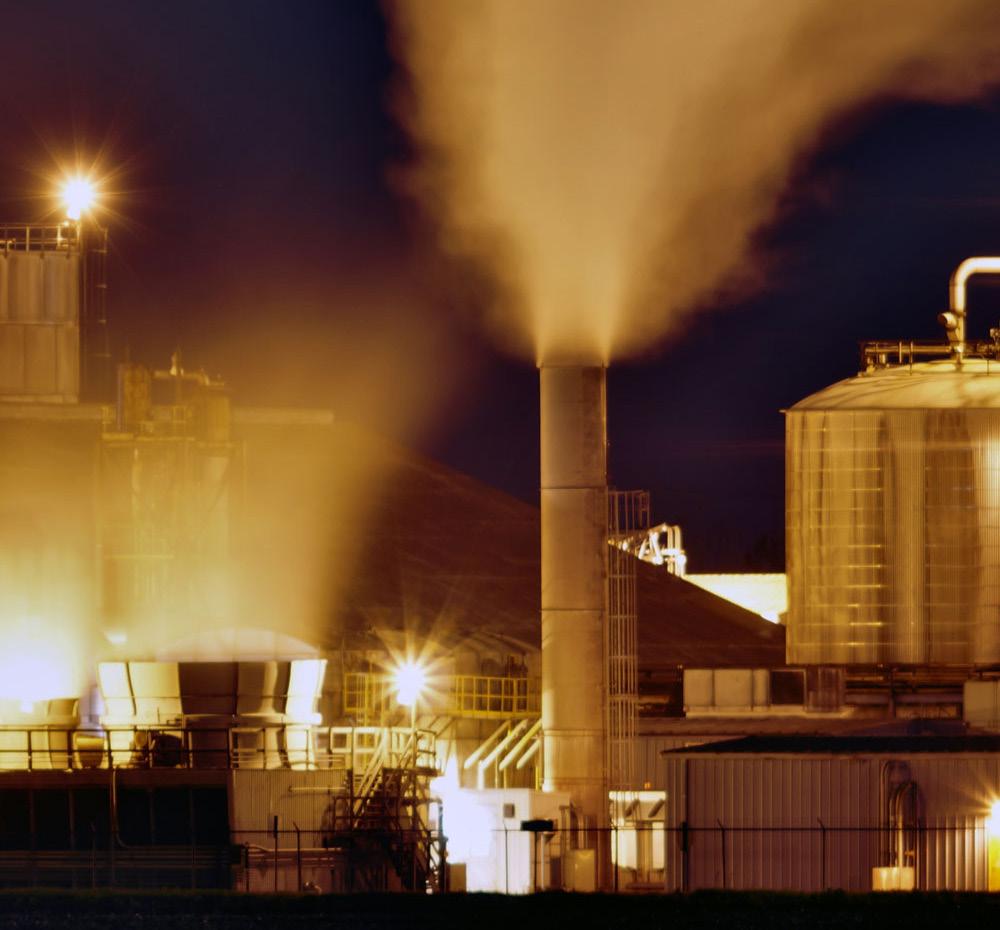
SPOTLIGHTING WATER USE: Cooling towers require the greatest need for water volume at most modern ethanol plants. New research is looking at ways to change that.
PHOTO: SOUTH BEND ETHANOL
Every Element In the Water Stream Matters
Terry Roberts, Midwest regional manager for SEPCO, an industrial fluids sealing solution provider that serves multiple sectors, says a seal is like a book. His presentation dialed down to a water related issue on a much smaller physical footprint area than that of Hanson-Pollock’s.
“A seal will tell you its story if you let it,” he said, explaining the information available after a failed seal is analyzed, especially in the case of ethanol evaporation operations. The mechanical seal itself is very simple. However, Roberts explains, there are hundreds of variables that can contribute to a failure. Examination of a failed seal can offer insight into failure prevention in the future, he says.
During his presentation, “Water Conservation In Ethanol Evaporation Operations: A Systems Approach to Sealing Im-
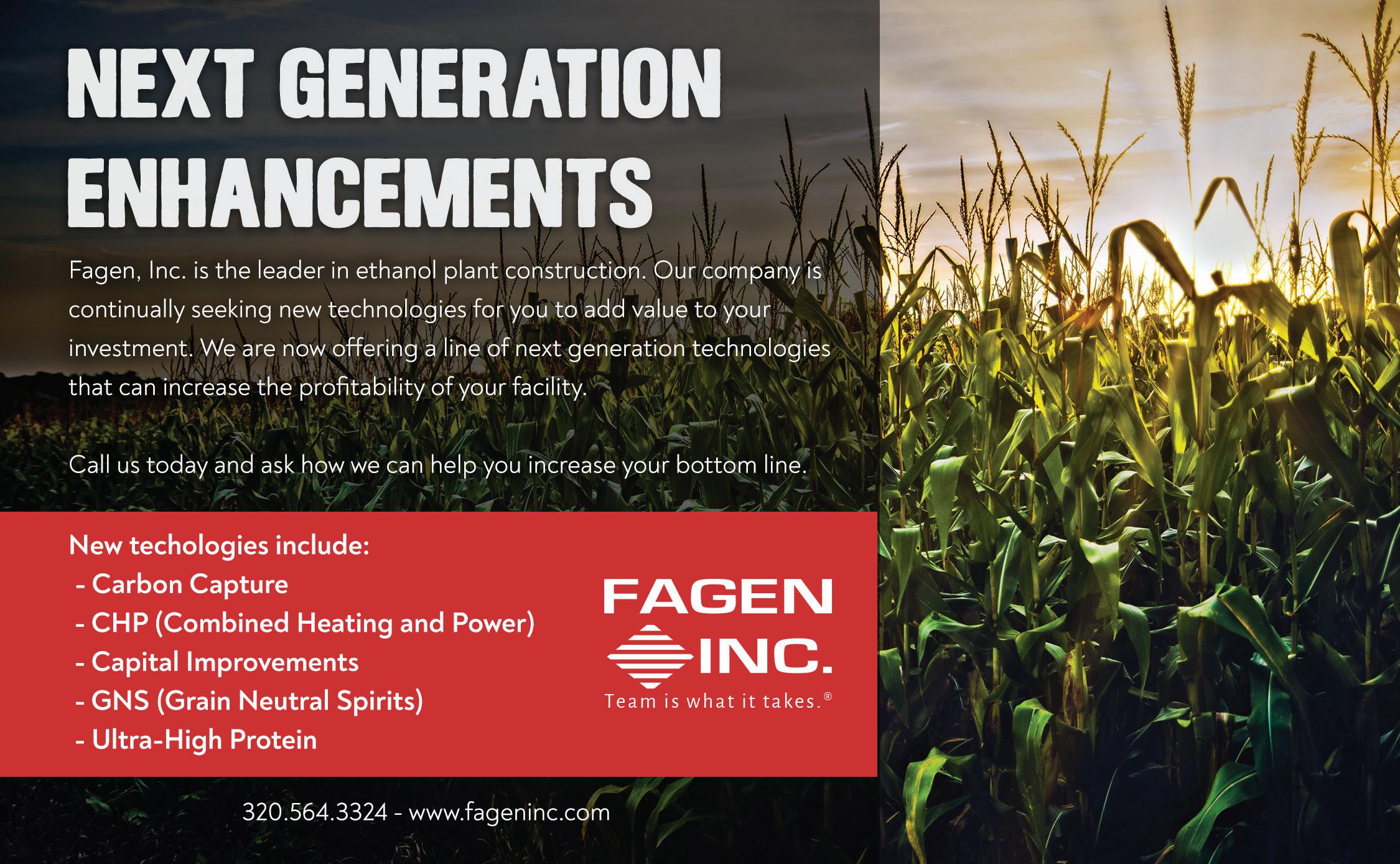
proves Asset Uptime in Difficult-to-Seal Processes,” Roberts offered a real case study to highlight SEPCO’s expertise. And, how effective its failure analysis team is at reading a seal like a book.
Roberts’ case study story starts with the evaporation stage at an ethanol plant. Specifically, after distillation where the remaining stillage goes through the process of removing the liquid, leaving the solids (i.e., the DDGS).
“One plant engineer had struggles with pump and seal failures,” he says. “The slurry flowing through the evaporator pumps was problematic for many reasons. In addition to the fluid complications, the engineer had problems with premature seal failure, detecting inboard seal leaks, setting up the environmental controls correctly and proper training of the maintenance team.”
The premature seal failures could have been from improper installation, pump misalignment or mismanagement of the seal chamber environment, according to Roberts. But the only way to know was to perform the failure analysis. Most analyses show that despite what many might believe, mechanical seals are not always the cause of larger failures. Instead, most failures are caused by systemic problems or poor seal selection. And, by design, the seal is the weak link in the system.
Seal analysis can reveal the following: if the right seal was selected for the application; if operating conditions are optimized; if the team set up the flush system properly; and if the barrier fluid is performing effectively.
For the ethanol plant issue in this particular case study, Roberts’ failure analysis team found three issues. First, the wrong mechanical seal design was used. Second, the environmental controls installed were not effective. And third, a more robust barrier fluid was needed.
For the new, appropriate seal, Roberts’ team selected a dual cartridge mounted seal. The new seal helped to provide a more robust and balanced design that allowed for
TYPICAL UTILITY WATER USAGE IN AN ETHANOL PLANT
• Water Intensity Ratio - gallons of water used per gallon of ethanol produced • Typical range is 3.5 - 4.0 gal H2O / gal EtOH • Example 100 MMgy plant at “Standard” Operating Conditions • 1,011,000 gallons of fresh water per day • Water intensity of 3.62 gal H2O / gal EtOH
FRESH WATER CONSUMPTION
Cooling Tower Makeup (gpm) RO Feedwater for Steam (gpm) Scrubber Water (gpm) MMF Backwash/Misc. (gpm)
17% 4%
19% 60%
SOURCE: PLANT PERFORMANCE AUDITS COMPLETED BY NALCO WATER
higher barrier fluid and process pressures. The new seal also provided an integral pumping ring in the seal that helped to move the barrier fluid from the seal gland to the convection tank for cooling. The tangential flush connections also provided more effective cooling in the seal gland.
The team also upgraded the barrier fluid. A synthetic oil specifically formulated for these applications was used. The main benefits of the new barrier fluid include its resistance to thermal and oxidative degradation, along with its ability to provide excellent heat transfer resulting in longer seal life.
Finally, the team installed a convection tank, commonly referred to as a seal pot. The convection tank provided a closed loop system that let the barrier fluid move heat from the seal gland to the tank for cooling and then back to the mechanical seal to provide the necessary lubrication to the seal forces.
The failure analysis and resulting work showed that reviewing the seal itself really did yield a good ending with the plant, upping its mean time between repairs (MTBR) to 37 months after previously needing to do maintenance work every four months. “Don’t underestimate how much each mechanic (on the SEPCO team) understands about seals,” said the ethanol plant engineer cited in the case study.
Know the Details to Deal with Issues
Brad Thompson, a water expert from Veolia (he presented under Suez which recently merged with Veolia), spoke extensively about the importance of selecting the right reverse osmosis (RO) membrane, a common and extremely important element of every plant’s water treatment and usage plan. RO membranes are typically used for purification across the process and, as Thompson
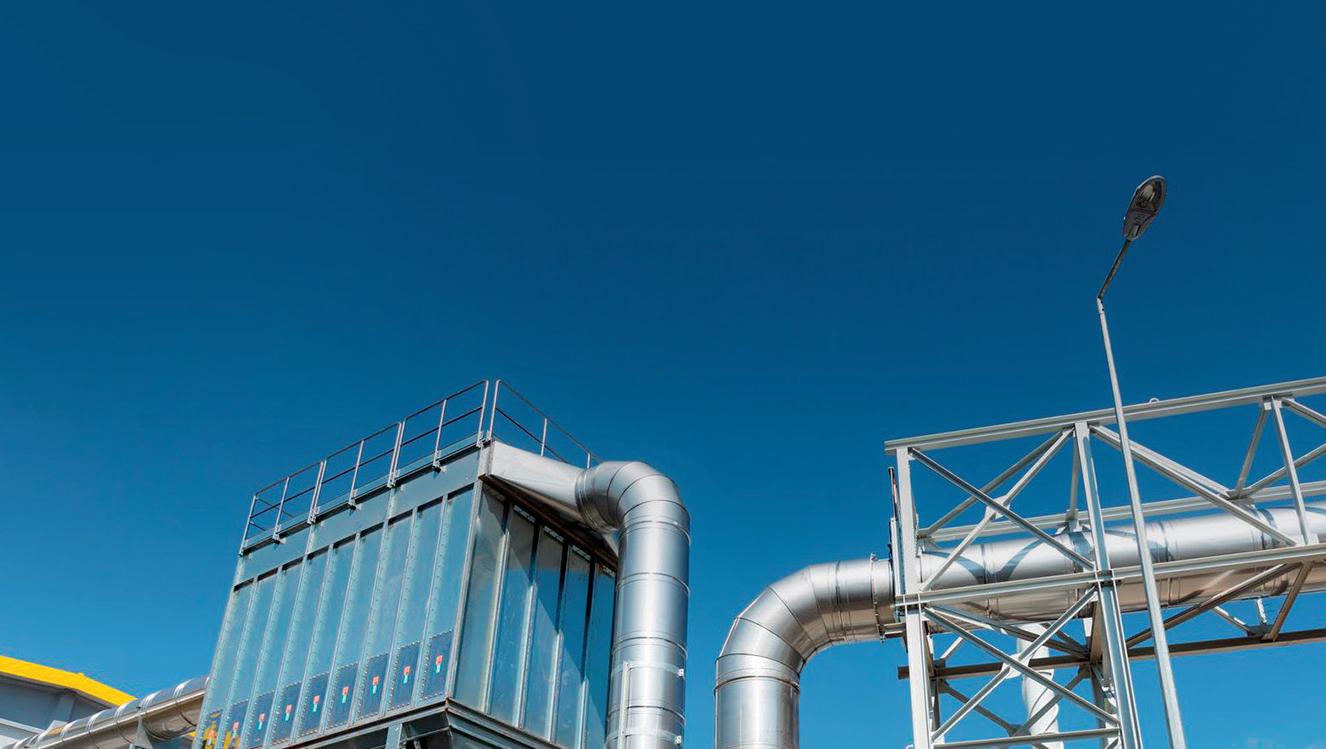
shows, most membranes only last three to five years. But, Thompson says, “membrane life can be extended by changing your approach.”
It’s important to understand why membranes fail first. The common causes include microbiological growth, degradation, scale formation, pretreatment fouling and structural fouling related to the previous reasons. The most predominant cause of failure is microbiological fouling (roughly 75 percent of all failures). Nearly half of all autopsies performed to look at RO membrane issues show the existing damage to be significant (42 percent).
To fix microbiological fouling issues, Thompson says removal includes aggressive clean-in-place practices. The process requires increased cleaner at higher pH, increased time, increased temperature and increased frequency. The ideal pH to remove microbiological fouling is 12.0.
There are two options to extend membrane life: non-chemical solutions or chemicals. For the non-chemical approach, the proper membrane needs to be selected from the start and then flushes need to be performed. Engineers need to know the membrane spec sheet. For example, a membrane at 99.0 percent rejection rate will let 1 percent salt passage, while a membrane at 98.5 percent rejection rate will let 1.5 percent salt passage. Thompson says the difference can be important. Fouling-resistant membranes should also be used. The No. 1 membrane he recommends is the fouling resistance option in 34-mil.
Chemical solutions involve stage-bystage CIP, knowing when to clean, and the use of enzymatic cleaners. For staged CIP steps, it starts with a 160 gallon per minute CIP followed by a 80 gpm CIP. To prevent degradation, an engineer needs to improve dechlorination by getting the strokes per minute of the system right. Overfeeding the system will create microbiological growth. Underfeeding the vessels will cause membrane degradation.
For membranes fouled with biofilm, there are new enzymatic cleaners that are comparable to conventional cleaners but won’t clean non-biofilm elements, Thompson says.
Overall, extending the life of a membrane includes on-time CIP, knowing the membrane specs, and stage-by-stage cleaning. Thompson’s presentation, like the others, highlighted the importance of understanding the modern-day solutions for everyday water issues at the plant level.
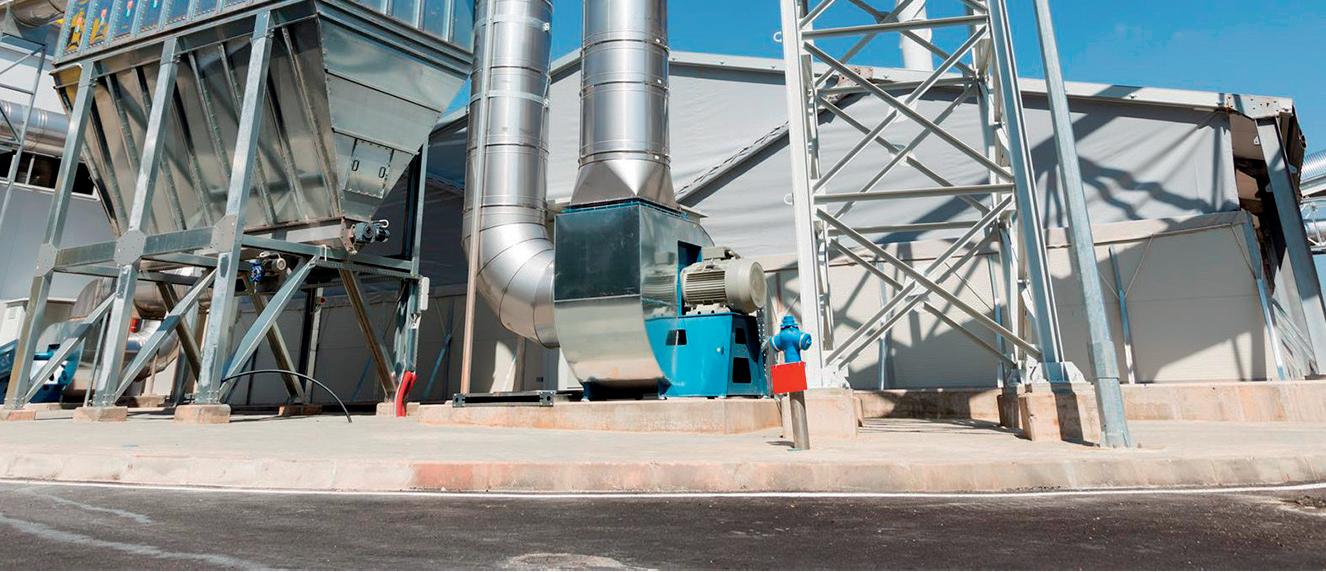
Author: Luke Geiver Contact: editor@bbiinternational.com
WE’VE GOT YOU COVERED.
With choices from spongeblasting, hydroblasting, industrial vacuuming and more, Premium Plant Services has the right mix of maintenance options for your facility.
• Confined space rescue • Dry ice blasting • Hydroblasting • Hydro reclamation • Industrial vacuuming • Restoration • Sandblasting • Slurry blasting • Spongeblasting • Surface chemical cleaning • Tube bundle and heat exchanger cleaning
(888) 54 9-18 69 .
Hibbing, MN • Dubuque, IA • Tracy, MN Stevens Point, WI