
12 minute read
DATA
When data became vogue in ethanol production half a decade ago, producers quickly embraced newly available tools for capturing, viewing and analyzing their lab and control system in-
tel. Process data, it appeared, might soon be the basis of all plant decisions. Every change would be guided by statistical analysis. Every trial would be immersed in data. Capital projects would be defined by it.
That future arrived only in part, says Joseph Reese, technical services manager at IFF. “When we look at data use in ethanol production today, we’re not seeing an all-in, one-size-fits-all approach,” he says. “There’s no single data technology helping every plant make all their decisions. Each facility is on a different point in their journey into datadriven optimization. They’re in different places on the continuum.”
Reese says almost every U.S. ethanol plant is currently using data to make process decisions—and looking to do more. But he also sees considerable gaps between producers with the most advanced analytical resources—like custom-engineered data platforms that integrate and conveniently dashboard process information from the lab and control system, or DCS—compared to those with only basic data regimens, using little more than spreadsheets to monitor core process parameters. “It’s still a wide spectrum in terms of what some producers are doing with data compared to others, but I think they’re all asking, ‘What more can we do?’”
Anne Chronic, director of market analytics for Phibro Ethanol, says there has been an incredible amount of real-time process input that’s become discoverable and incorporated into data reporting at ethanol plants in the past five years, and a total transformation of process monitoring and analytics during her 15-year career in ethanol.
“When I started in this industry in 2006, many were entering data manually and there was very little data automation,” she says, explaining that virtually every area of an
DIRECTED BY DATA
With support from fermentation product suppliers, ethanol producers are integrating process analytics into their decision making like never before. By Tom Bryan
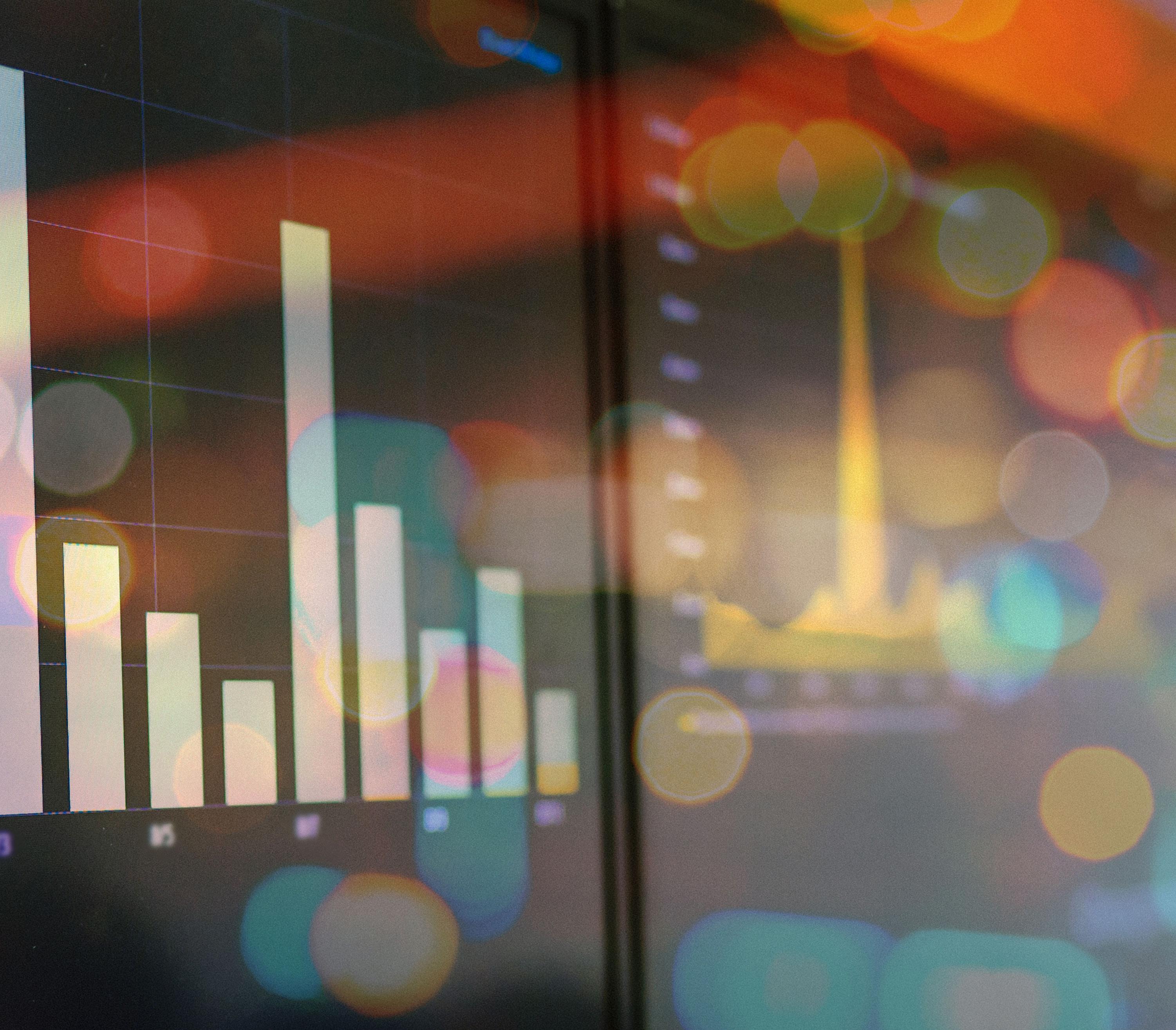
Chronic
Anne Chronic
ethanol plant is now capable of producing potentially useful data. “Right now, I think field instrument mapping represents the largest opportunity for near-term growth in the data space. Because the functionality is already there. It’s not so much about creating the infrastructure to collect data anymore, but querying the right data points for new and improved forms of analysis. That’s what we’re moving towards.”
Alex Sexton, technical service manager for Lallemand Biofuels & Distilled Spirits, agrees that a new reliance on data has caused a shift change in thinking about ethanol production. He credits early data capture platforms that made data more accessible for the industry with high-impact dashboards and robust reporting features. “It’s been extremely useful to have all that data, from any time range, in one convenient place,” he says. “Those tools not only help producers, but they also help us serve our customers better. There’s always room for improvement in terms of getting the data producers want and need—and doing it better—but there is no question that this industry is increasingly using data in more meaningful and powerful ways.”
Lallemand also has its own tools. Sexton says the company's Mobile Application Process System, or MAPS, which is housed in a 53-foot semi-trailer and used to test yeast strains under real-world conditions on site at
Alex Sexton
ethanol plants, complements Lallemand's data-driven approach to innovation. “It's quickly become a very useful R&D tool to help make the introduction of products both easier and faster through data-driven experimental approaches with real plant mash,” he says.
Reese agrees, explaining that some of the producers he works with are looking for ways to better house and engineer their data, if only to get it all into one convenient spot. “And the more advanced plants are now looking for ways to move beyond entry-level data technologies,” he says. “They’re ready to take their data approach to a higher level. Ethanol producers no longer need to be convinced that data-driven decision making is smart. They know it leads to better yield, better efficiencies, and greater profitability. The fact is, ethanol plants are spending a lot of time and money on data already—from lab tests, running tests, instrumentation and recording data—so I think the question is how much more can they do with it?”
Encoding Knowledge
Chronic, says it’s critical to recognize employees that help plants succeed through data-driven thinking. “In this era when everyone is placing a premium on employee retention and employee recognition, the more you can leverage information to empower employees, the better,” she says. “Too often with data, we think only about the process, but people make these decisions, and even small everyday decisions driven by data can have a large impact on the plant.”
Pedro Peña, lab and R&D director at CTE Global Inc., agrees that enabling personnel to make data-informed choices is smart management, especially when done in parallel with vendor support programs like CTE’s trademarked InSight data service, which helps ethanol producers “connect the dots” in their data libraries to optimize production. “Capitalizing on data requires expertise—statistical analysis, modeling, and the know-how to analyze information—and you’re ultimately relying on people to get it done,” Peña says. “But ethanol plants are dealing with the same workforce challenges everyone else is, so we’re stepping up with InSight to bridge that gap and help producers navigate their data.”
IFF has a similar data solutions approach, its trademarked Xcelis AI, a platform the company offers to its ethanol industry customers to help them harness the power of data and predictive modeling. Reese agrees that data fluency can be lost through employee turnover. “Every plant has exper-
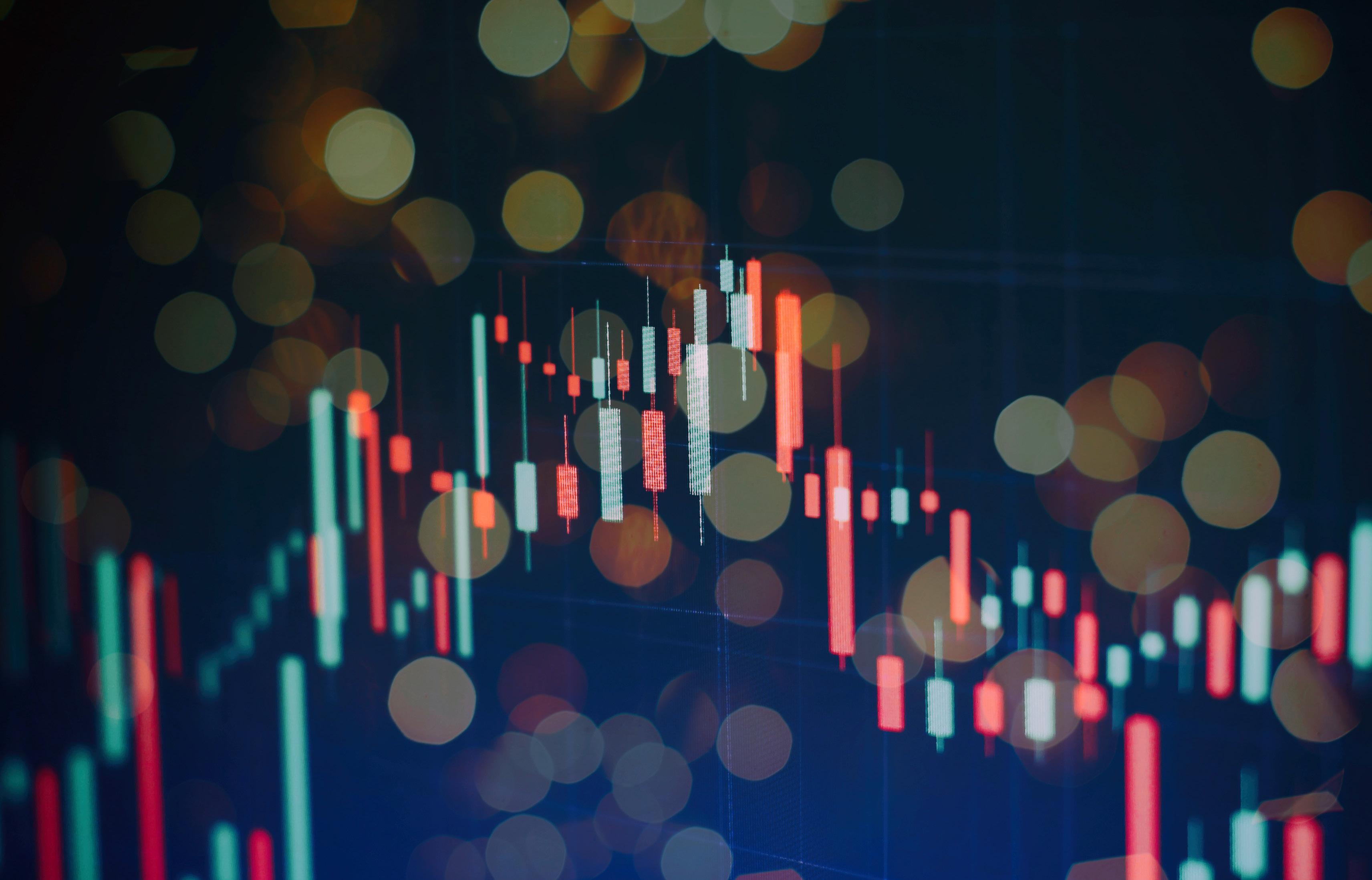
Peña
Pedro Peña
tise that tends to exit at different times,” he says. “But a sound data strategy like Xcelis AI can help encode and operationalize that process knowledge so that, even as you have turnover, that expertise remains built into your process. It’s so important not to lose that understanding and potential for optimization when a key person leaves.”
Data as a Service
With enzymes, yeast and antibiotic providers all offering to help ethanol plants understand and utilize data more effectively, Peña says producers are increasingly looking for analytical support that casts a wider net of process improvement potential. “Data is an area where we feel we can really help across the whole plant,” he says. “We’re always looking at what else we can do—even outside of enzymes—to help our customers do better. It’s more than just our products. It’s about helping them optimize, helping them troubleshoot, helping them identify areas for improvement.”
Peña says CTE is even conducting comprehensive plant audits to more fully uncover areas of potential improvement within its customers’ facilities. “Helping producers optimize is our calling card,” he says. “Anything we can do to help them run more efficiently, more consistently, more cost effectively, and ultimately, more profitably, we’re going to do. Data is critical, because it’s how we begin to understand how the plant is running.”
Likewise, Reese explains, Xcelis AI is a service that can mean different things to different IFF customers, from helping them select and implement a data software package to consulting services or customized support. “It’s part of our broader Xcelis approach,” he says. “We try to work with our customers as closely as possible to deliver whatever services and technologies they need to be successful.”
Ultimately, data analytics as a service is a vehicle for providers of fermentation products to meaningfully engage with customers on both plant optimization and product maximization. “If we can better understand how our customers operate, how our products influence their operations, than we can offer improved products and better understand how existing products are working,” Reese says. “Anytime we can do that, the customer benefits.”
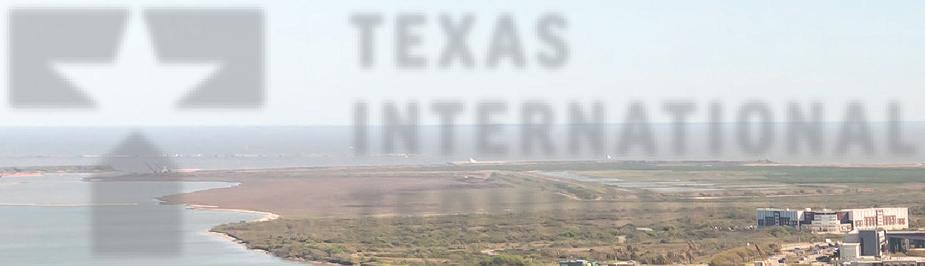
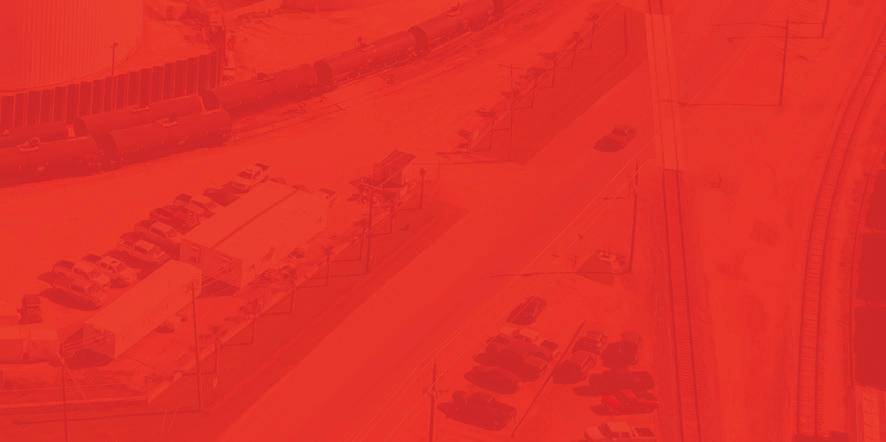


WE MOVE THE WORLD FORWARD.
RAIL, STORAGE AND MARINE CAPABILITIES
RAIL • UP and BNSF direct access • 160 railcar unloading spots, unload at 15,000 bph • Landing tracks capable of staging 4 unit trains • Unit train turn times of 24 hrs or less STORAGE • 2 million barrels of dedicated storage • Denaturant & bitrix blending • Foreign Trade Zone MARINE • 3 deep draft berths • Loading rate of 10,000 to 20,000 bph • 3 barge berths
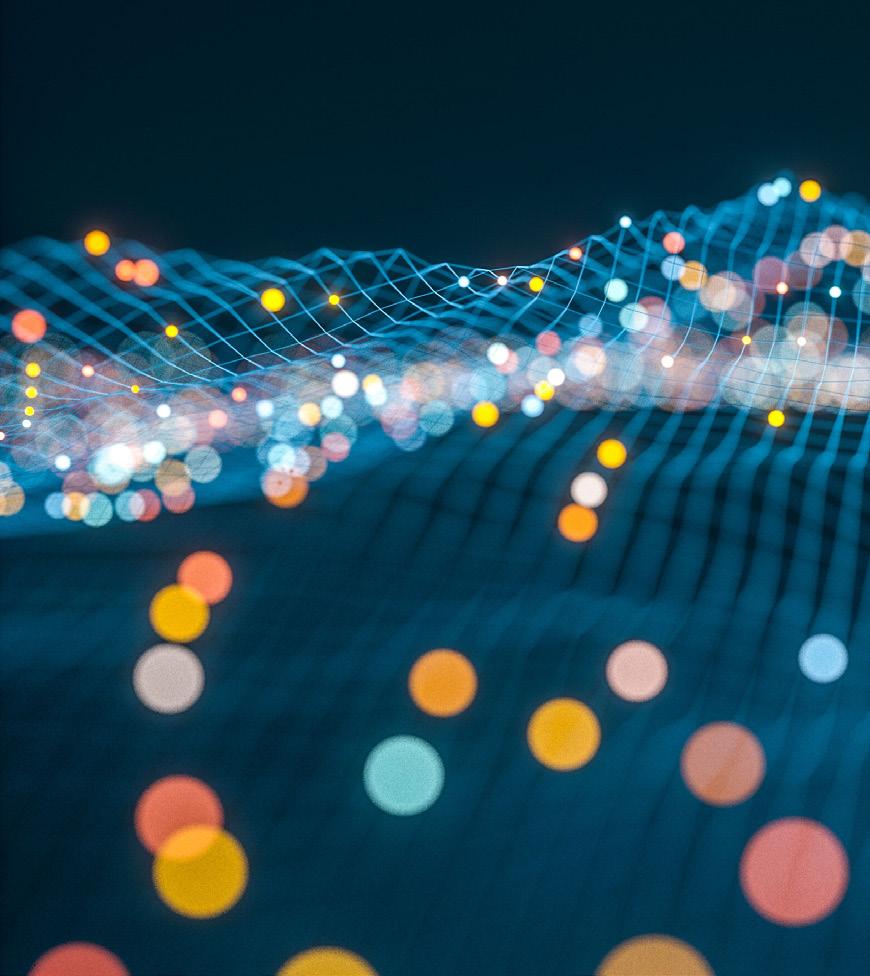
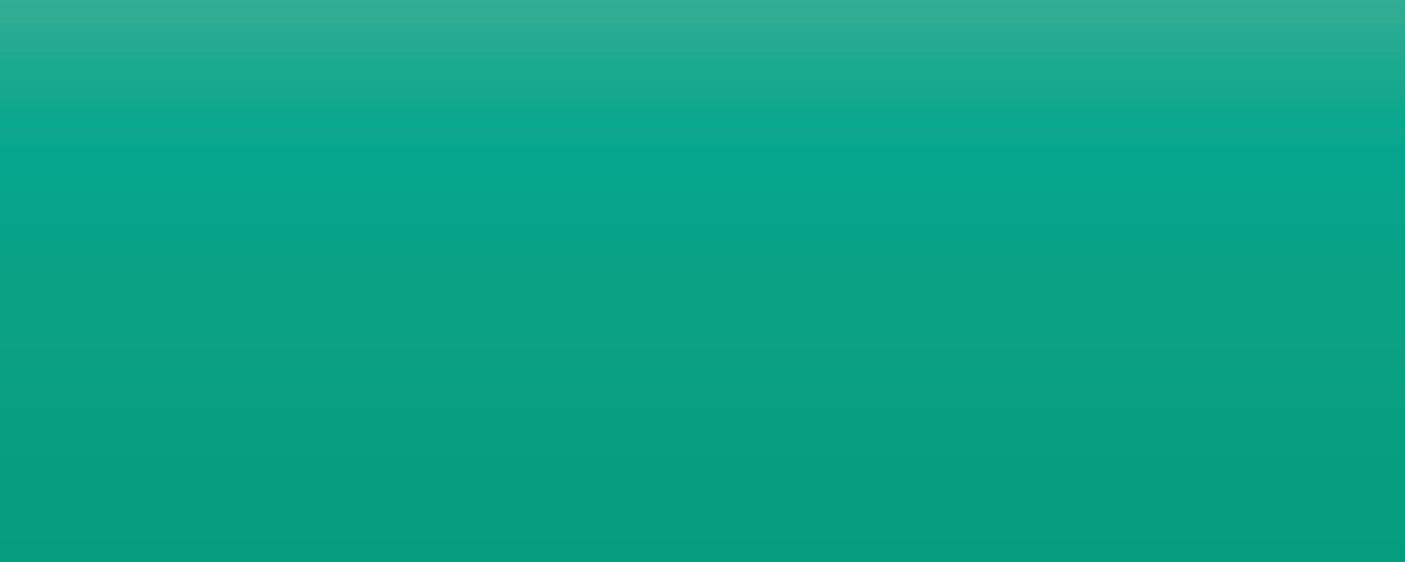
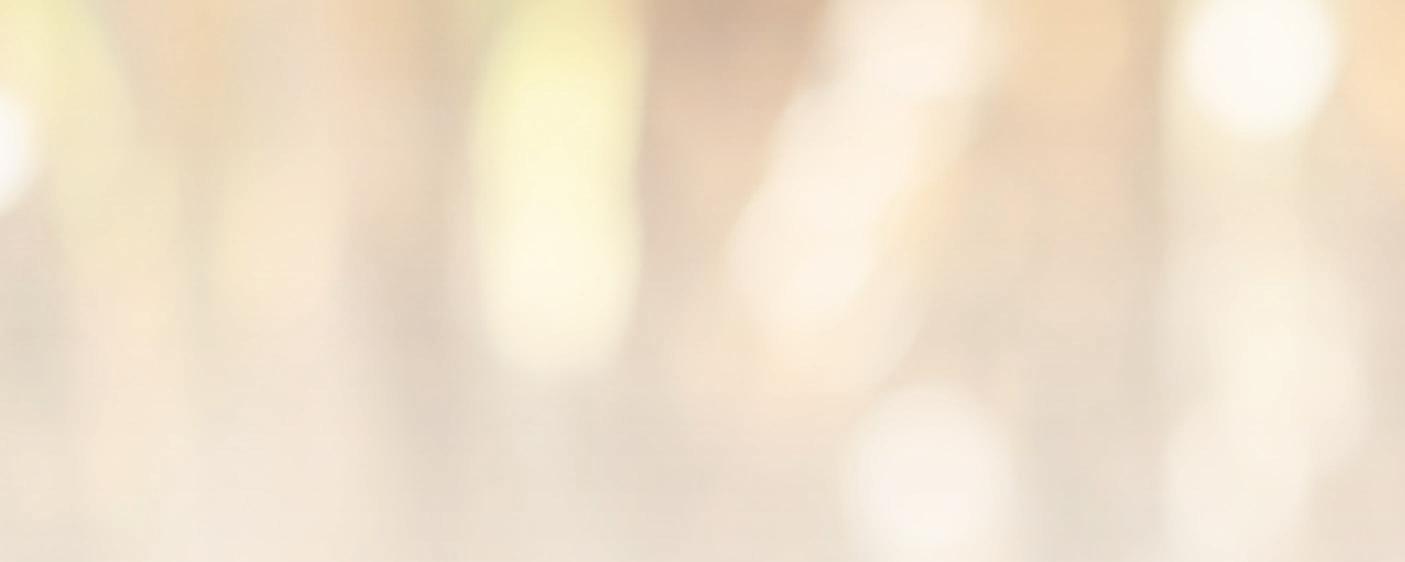
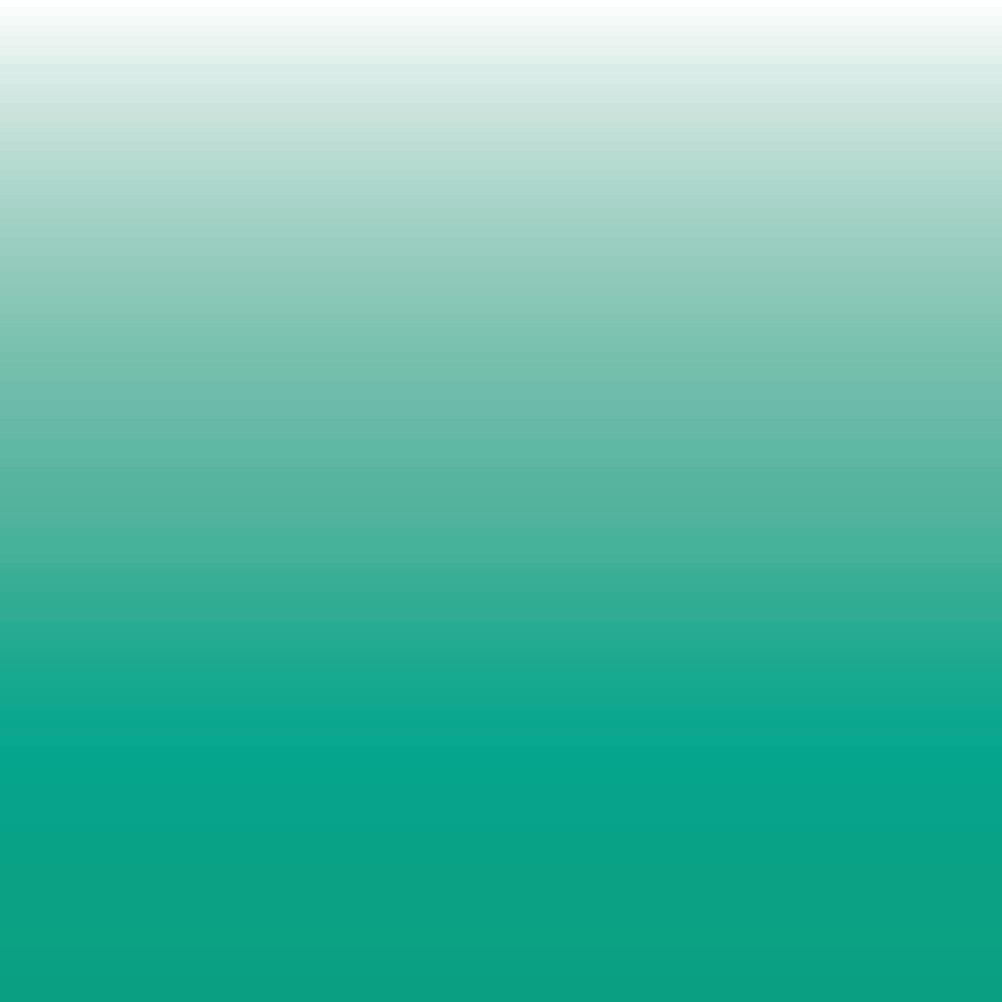
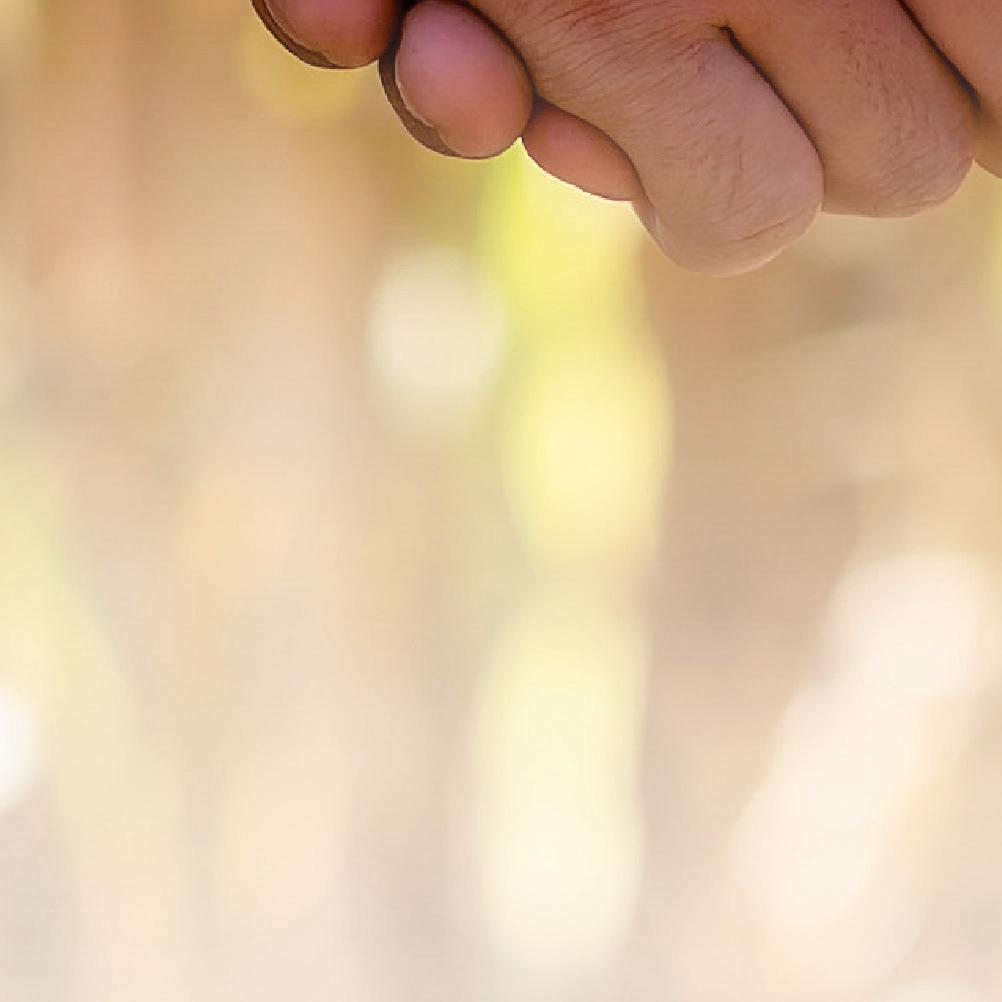
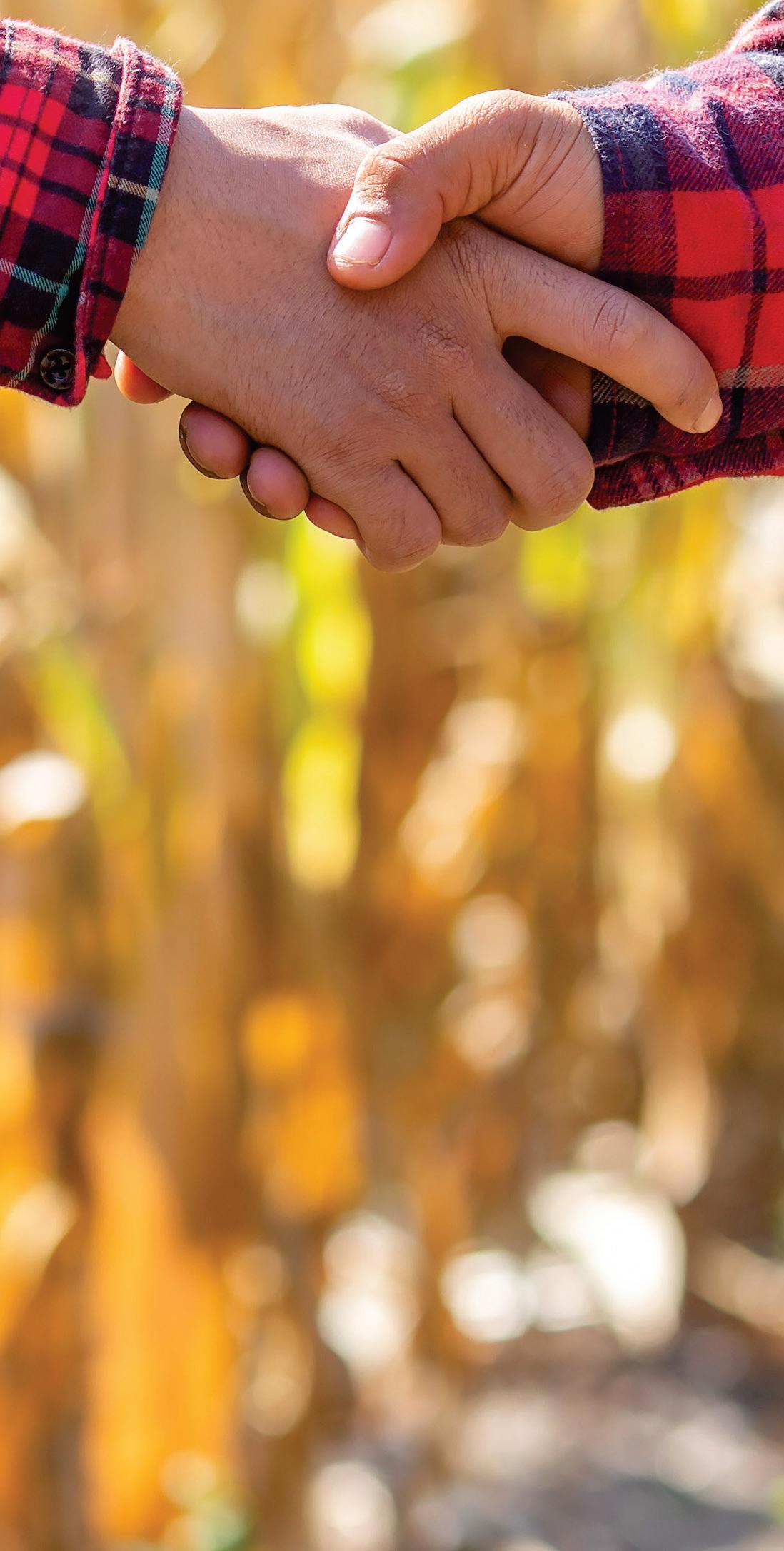


Focused solely on agriculture, the Agribusiness and Capital Markets department of AgCountry Farm Credit Services has the experience and expertise to be the complete solution for all your fınancing needs.
AgCountry.com | 877-811-4073
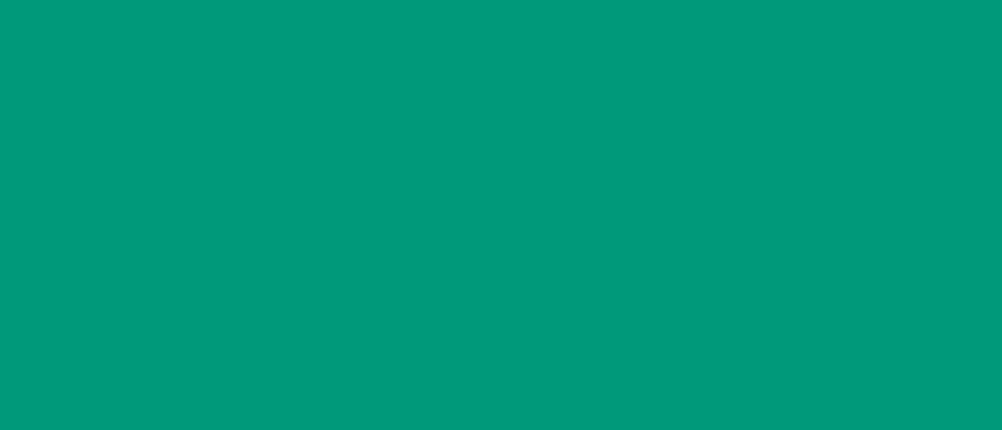

Reese says data analytics also de-risks product trials. “Rather than going into trials blind, if we can understand these plants better before we develop products, or as we’re developing products, we’re helping to de-risk the whole innovation process while potentially delivering improved products to our customers at a faster pace.”
Sexton says Lallemand’s technical services team also places a heavy emphasis on being available to help interpret process data for customers, plugging data into JMP, for example, before, during and after a product or process change. “I think producers appreciate that added confidence, knowing they’re not alone trying to figure out a difficult challenge,” he says.
Detectable through Data
As the ethanol industry incrementally achieves greater efficiencies, and improvement over time, gains of any kind are harder to uncover and pursue. Sexton says this makes data-driven approaches to innovation not just useful, but necessary to achieving the next hard-to-get process advancements. “More than 90%, maybe 95%, of the industry is now using a biotech yeast that has a glycerol reduction pathway allowing more ethanol to be made by the yeast at a higher yield,” he says. “Only through data are we able to make sure producers are getting the best performance out of these yeasts with the best possible yields.”
Peña agrees. “Most of the low-hanging fruit of optimization is gone,” he says. “It’s time to get on the ladder and see what we can reach, and what more we can squeeze out by leaning into plant data. And when
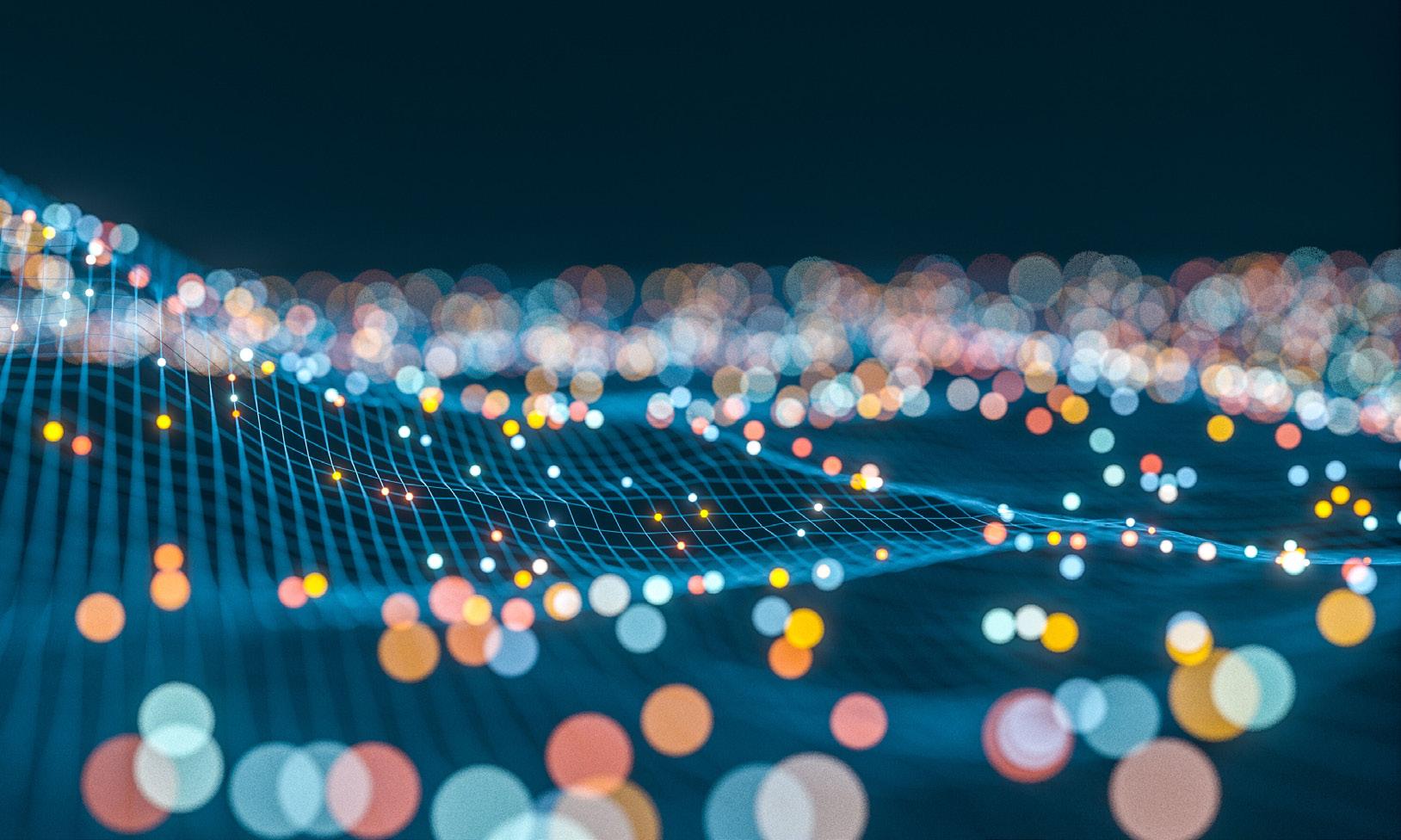

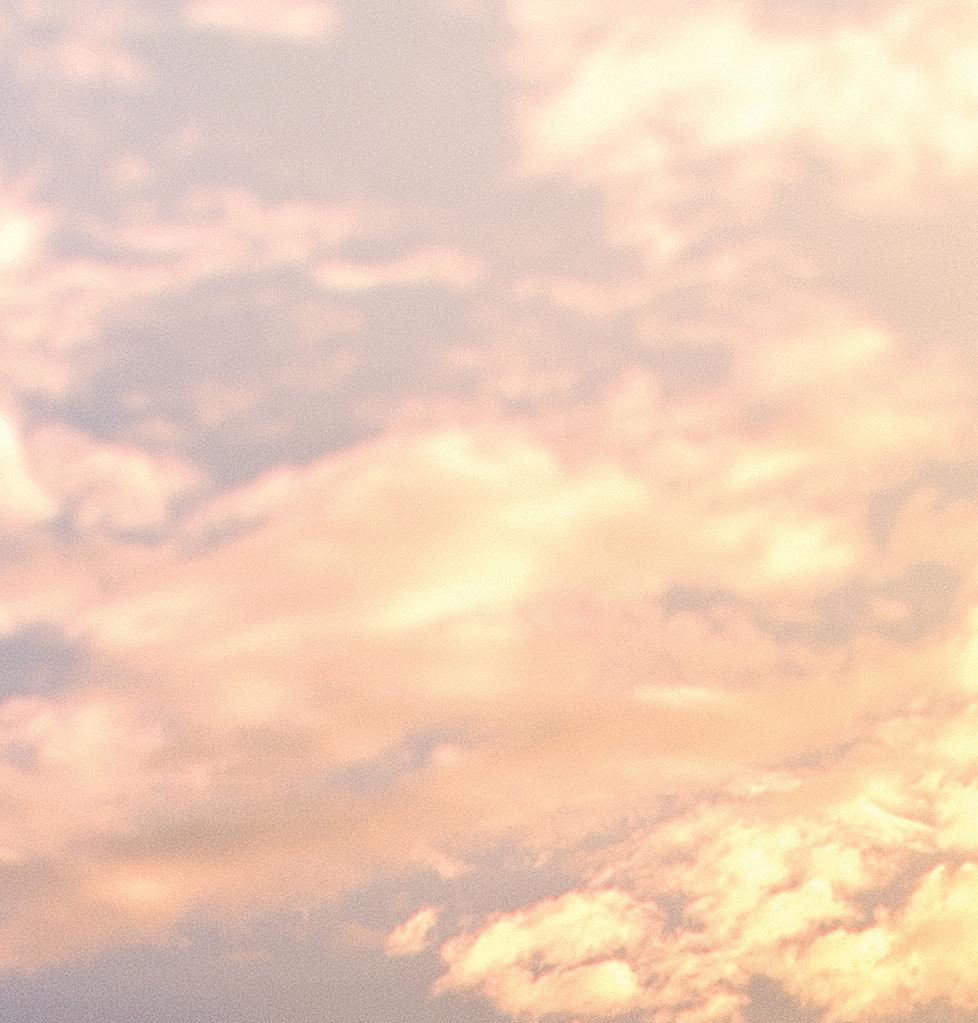
Reese
Joseph Reese
you’re up against theoretical maximum yield, it becomes a matter of not just hitting a number but doing it consistently. Can you do it day in and day out—99% versus 90% of the time. That’s the kind of fine-tuning we’re trying to get at with data.”
And Peña says producers sharing data among multiple facilities may ultimately benefit the most. “It will require a diversity of data, and more of an industrywide perspective, not just looking at the plant as an island, but looking at ethanol production data more broadly, more wholistically,” he says. “Producers that can do that will be able to squeeze out the most juice and get up the ladder a little faster, with less risk, and a little more efficiently.”
Chronic says that even though new efficiencies may be getting harder to achieve, even small improvements revealed through tiny variabilities in process data can make a big difference to a plant producing 50 to 100 million gallons of ethanol a year. “The great thing about eliminating significant process variability is that, as you tighten your process—and this is the beauty of statistics, too—there are still ways to mine out data, even when the variability is minute,” she says. “You can still see the nuances in differential and incremental changes. It’s not going to be the 15%, maybe not even the 1% variability that it once was, but it’s going to still be something they can leverage for powerful results.”
Reese agrees that ethanol producers have gotten very good at understanding and controlling the factors that contribute to yield—or yield loss—and it has become tougher to tease out the real effects in the data that drive yield. “So, by better engineering the data, by bringing it all together in one place, these more advanced analytics tools can help analyze for the smallest effects in the customers’ processes—effects that have been missed in the past,” he says. “The plants that are going to separate themselves from the competition in the future are those that will successfully implement these data-driven strategies to more deeply understand their processes. Even in a very well optimized environment, there will always be more levers you can pull to improve yield and profitability.”
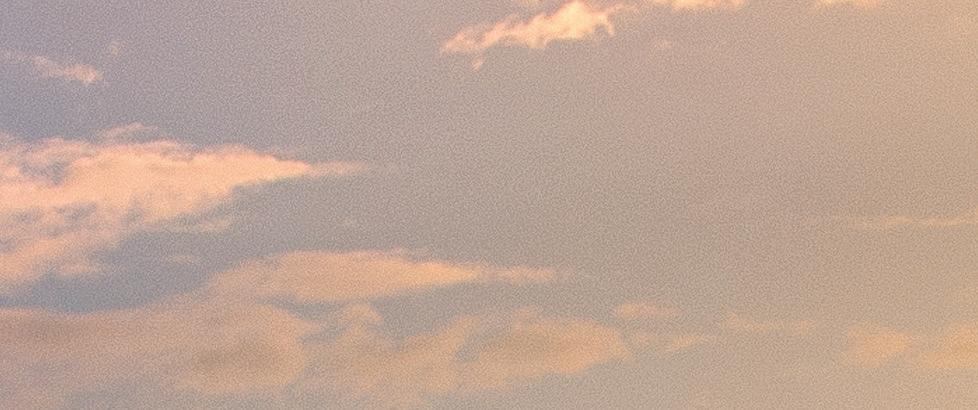
Author: Tom Bryan Contact: editor@bbiinternational.com
JUST 10 PAGES, BUT IT’S THE NEXT CHAPTER FOR YOUR ETHANOL PLANT.
What’s the right direction for the next generation of ethanol production? How can you find the right solution? What questions should you be asking? Fluid Quip o ers an objective guide to making the right decisions.
Download your free copy.