
4 minute read
DUST CONTROL
IMAGE 1 IMAGE 2

Example 1: Engineered transfer points and modular load zones: covered storage and transfer of wood pellets.
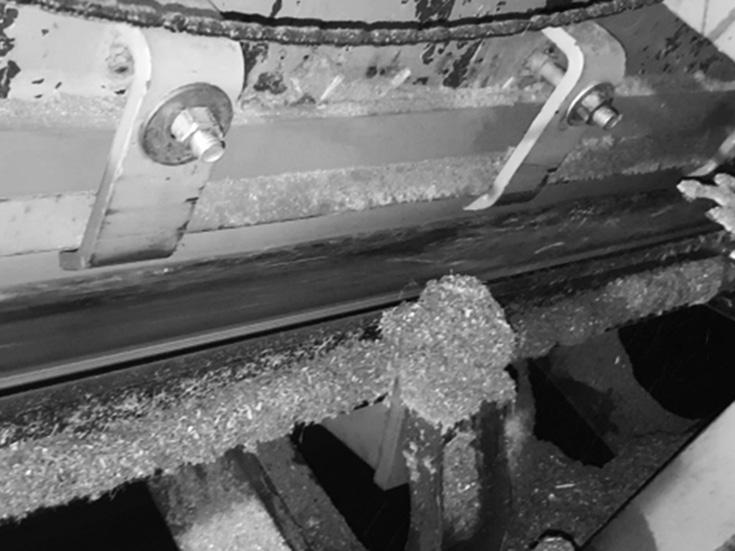
IMAGE 3
IMAGE 4 Example 2: Slider beds can act as a heat source. Coupled with spillage and dust due to uneven wear and sliding friction, the risk of fire and explosion is elevated.
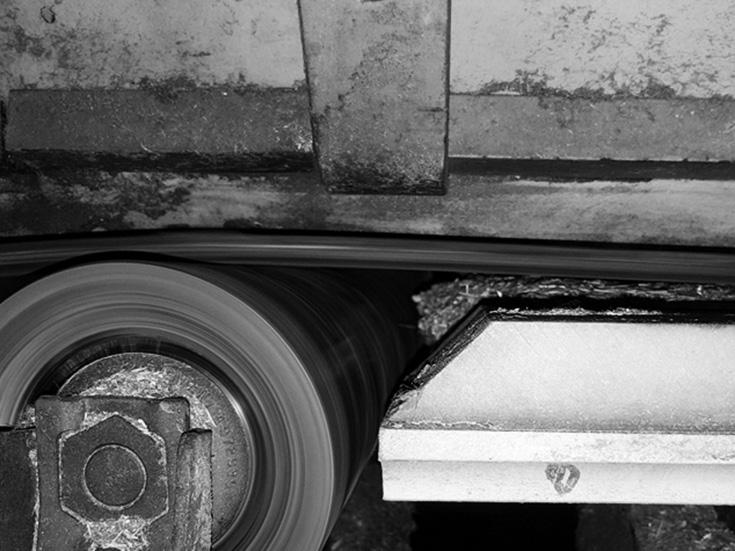
Controlling Combustible Dust and Spillage
BY GREG BIERIE
One of the primary issues at pellet mill facilities is controlling combustible dust and spillage. Personnel safety and regulatory compliance are also top of mind in the corporate safety culture. Increasingly, maintenance and operations personnel are making use of new tools and leading-edge technologies to ensure that their jobs can be performed efficiently and safely.
As a general statement, if maintenance is made easy to perform with minimal downtime, the corporate goals of maximum production can mesh perfectly with maintenance and operations goals to maximize reliability and minimize downtime.
Using a “toolbox” approach to total dust management and spillage control allows the pellet mill industry to address the problems at the source. This philosophy focuses on using safety by design in developing new technologies that are conceived by plant professionals, for use by plant professionals. If maintenance is easy to perform, it will get done. If problems are addressed at the source, the Band-Aid approach can be eliminated.
The problems and solutions that combine “safety by design” with robust products and systems to achieve compliance and improve performance include the following areas of focus: • Lower risk, increase safety, prevent spill-
age
• Reduce cleanup and transfer cost, improve material flow • Regulatory compliance with agencies, NGOs and local community
Project Examples
The following few examples of recent projects that address above issues.
In Example 1, improvements were made to alleviate issues with transfer points and modular load zones at a wood pellet transfer and storage facility. As can be seen in Image 1 and Image 2, a dramatic difference was achieved. No additional dust con-
IMAGE 5
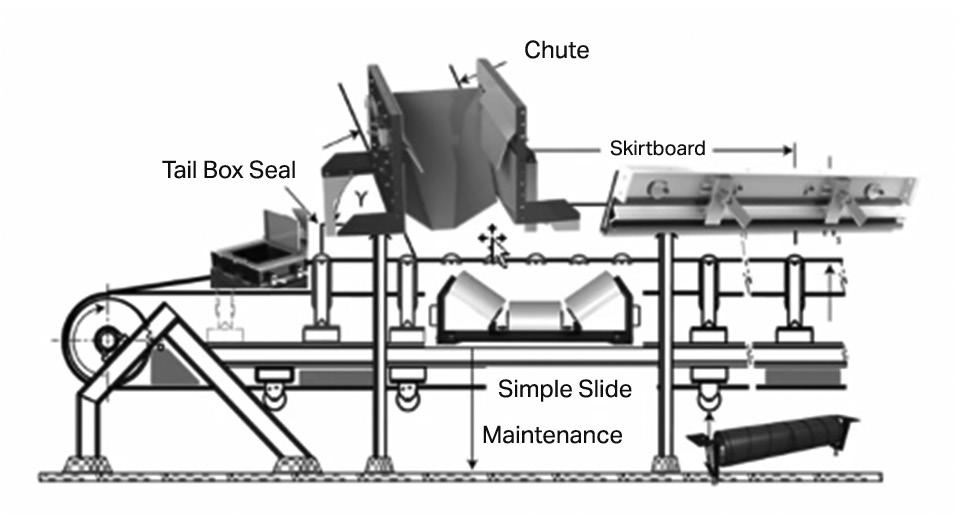
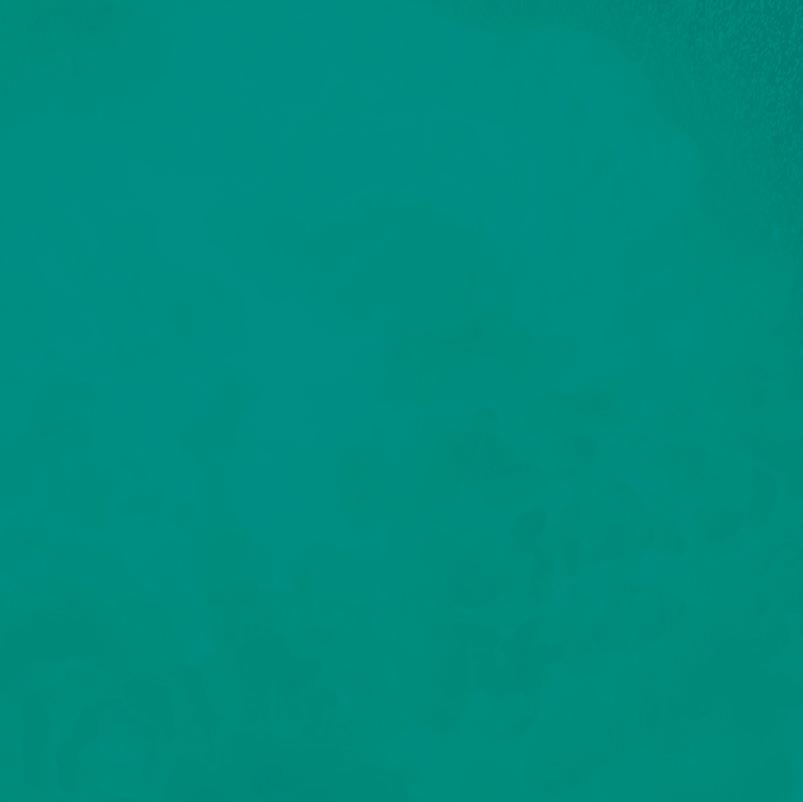
trol measures were necessary to eliminate the problem in this enclosed conveyor system. By controlling material flow and minimizing entrained air along with soft loading and center loading of wood pellets onto the receiving belt, the dust and risks of fire or explosion were reduced well below the acceptable level. Leading edge technologies were utilized to cure the problem at the source.
For Example 2, Image 3 and Image 4 demonstrate, at this facility, sliding friction and poor sealing was increasing fire risk at load zone areas using impact beds. The mill workers saw and smelled smoke to indicate a dangerous situation in which combustible material had built up on adjacent structure. The solution to this issue included many leading-edge technologies to cure the problems at the source. These included, but were not limited to, the MaxZone Plus—a system that acts as a modified load zone chute with an additional way to reduce dust and spillage at the load zone—and SureGuide Training Idlers, which are belt-centralizing return pulleys made of precision-turned components (see Image 5).
In conclusion, doing the same old thing will produce the same old results. New equipment should not be confused with new technology. The products and project results as shown above are due to adopting new technologies. The combination of these technologies solve the problems at the source. Safety by design aims to eliminate issues such as confined space entry required for service, ergonomics for and maintenance, and maintenance made easy so that it can be performed by one person in the field. In addition, rolling components replace sliding components that produce friction and heat, along with special foot patterns and slide-out rollers to make service simple and sealing secure. Modular componentry eliminates the need for hot work in construction, and all internal components are externally serviceable by one person. Material flow is controlled to minimize dust and spillage, and ensure proper belt loading.
Above all, regulatory compliance can be achieved, the corporate safety culture is enhanced, and the risk of fire or explosions from combustible dust is eliminated at the source.


Author: Greg Bierie Technology Specialist, Benetech Global bierieg@benetechusa.com www.benetechglobal.com
T +1 704 716 7022 T +49 2961 7405-0
ve d © REMBE® | All rights r eser
PROTECT YOUR PLANT!
Consulting. Engineering. Products. Service.
· Over 45 years of innovation in comdust explosion protection. · Venting and isolation to protect personnel and plant. · Customized indoor/outdoor protection for dust collectors and more.
Inc.
| Charlotte, NC 28217, USA | info@rembe.us | www.rembe.us