
7 minute read
FEEDSTOCK Understanding Ash Fusibility
Bulk powder flow testers can quantify biomass feedstock flow properties, yielding data that can help improve flowability and productivity.
Q&A: Biomass and Bulk Powder Flow Testing
BY JAMIE CLAYTON
What is the relevance of bulk powder flow testing for biomass?
Converting biomass into usable product involves steps such as storage, chute transfer, conveying, mixing and feeding/ discharge into a mill or grinder, for example. Effective bulk solids handling is therefore essential, with poor flowability routinely highlighted as a primary cause of operational problems. Poor flowability causes unplanned shutdowns and can limit handling rates, making it a major cause of inefficiency in biomass handling facilities. Bulk powder flow testing can quantify the flow properties of biomass feedstocks, providing insights that can help processors to improve flowability and work more productively. The inherent variability of biomass and the impact of moisture are undoubtedly complicating factors in biomass handling, but there is considerable scope to gain valuable information that can have a direct impact on processing efficiency.
How does bulk powder flow testing sit alongside other physical characterization techniques such as particle sizing?
Particle size is just one of many variables that impact bulk powder flow. Examples of others that are particularly relevant to biomass handling include particle shape, surface roughness, bulk density and moisture content. It’s quite easy to see the impact of these variables in practice and their effects are widely recognized. For example, bulk solids can be transformed from free-flowing to a solid-like mass by moisture ingress, and more regular-shaped particles tend to be associated with better flowability than elongated analogues with the propensity to mechanically interlock during transfer.
When a biomass feedstock doesn’t behave as required, the default may be to investigate whether changing particle size will improve things and to what extent, not least because particle size is relatively easy to measure. But as the preceding observations make clear, this approach is fundamentally flawed. It involves measuring just one of many influential variables as a proxy for the behavior of interest. Measuring bulk powder flow properties is more productive because it directly quantifies the behavior of interest. Such measurements support systematic investigation of the factors that can be manipulated to improve flowability and promote more robust optimization of the feedstock. For example, longer drying times may be a far more beneficial strategy than particle size reduction, but there is no scope to compare these options with particle size measurement alone.
What are the options when it comes to measuring powder flow?
Engineers and scientists have been devising techniques for measuring the flowability of bulk solids for decades, so there are plenty of commercial options to consider. The lowest cost, such as angle of repose,
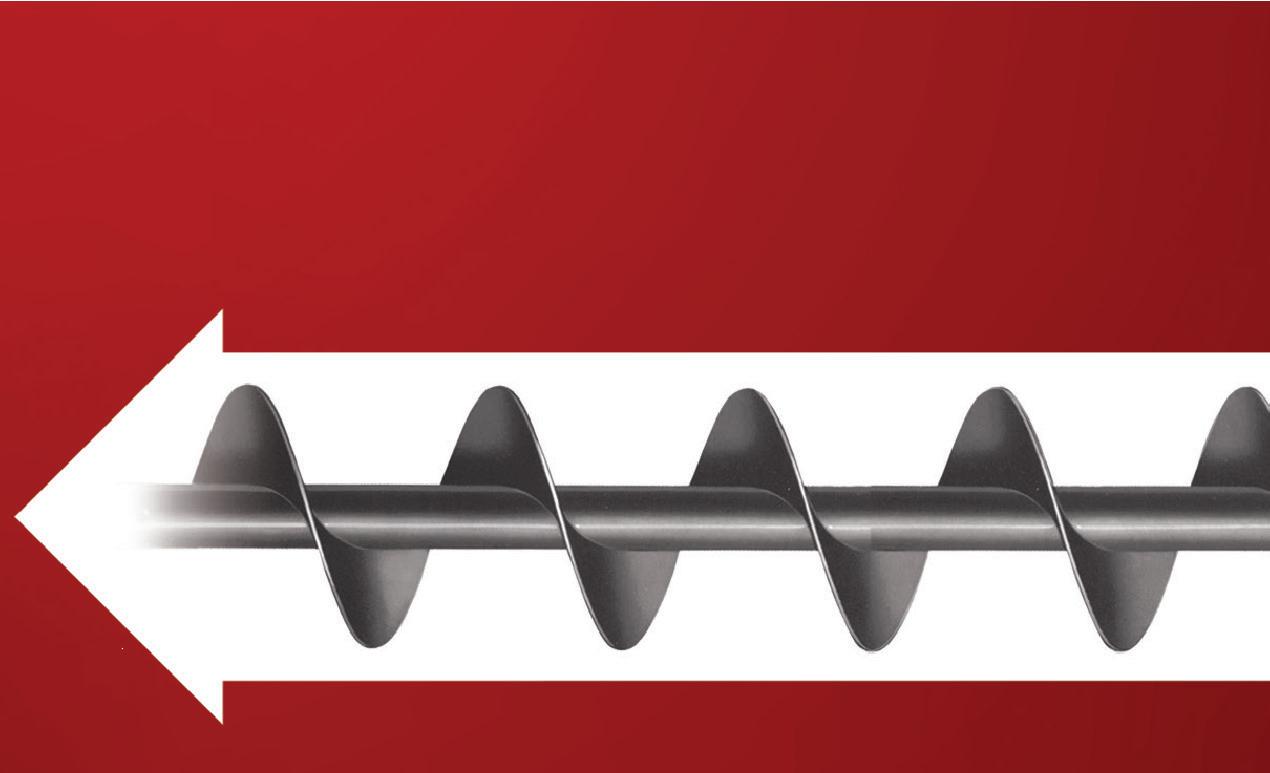
tapped density and flow through an orifice, involve very simple, manual tests, with the trade-off being poor repeatability and minimal insight. All these tests are somewhat dependent on operator technique, so there may be significant variability in the data, compromising sample differentiation. With flow through an orifice, there is also the danger of an uninformative “null” result—no flow. These techniques also offer no control over the test environment, so it is hard to relate the data to specific processes; notably, to determine the impact of in-storage consolidation or how the sample might behave when aerated, for example, in a pneumatic conveyor.
Shear cell testing was developed in the 1950s, and has the distinction of being the first scientific approach to bulk powder testing. It quantifies the ease with which a consolidated bulk transitions from the static to dynamic state, and generates parameters that are used for hopper design. This is a helpful technique for investigating the impact of storage and hopper discharge behavior, but it is less informative when it comes to determining how powders behave in low-stress regimes—for example, during gravitational transfer.
The 1990s saw the introduction of dynamic powder flow testing with what would become the FT4 Powder Rheometer, an instrument that quantifies flowability from measurements of the powder in motion. It became possible to test powders in a consolidated, moderately stressed, aerated and even fluidized state to gain information of relevance to a wide range of different processes. At the same time, this instrument’s ability to measure dynamic, shear and bulk powder properties increased awareness of the practical benefits of multifaceted powder testing. Today, those working at the forefront of bulk materials handling rarely, if ever, rely on a single number approach, instead measuring multiple parameters to piece together different quantifiers of flow behavior and form a complete picture.
In summary, modern options for powder testing range from the simple and manual to the more sophisticated and highly automated. There are corresponding differences in upfront costs, but it pays to be aware of the total cost of ownership; powder testing with some instruments can be manually intensive. The relevance of the resulting data also varies substantially.

What features should be looked for in a powder tester?
Picking up on the last point, the most important feature of a powder tester is its ability to generate information of value. Biomass samples are often fairly coarse and highly variable, so check whether the instrument can handle all the materials you are interested in. Then consider how the information generated might be used. What behavior do you need to understand? Powder properties measured under one set of conditions cannot be robustly extrapolated
Feeding, Conveying and Elevating Solutions
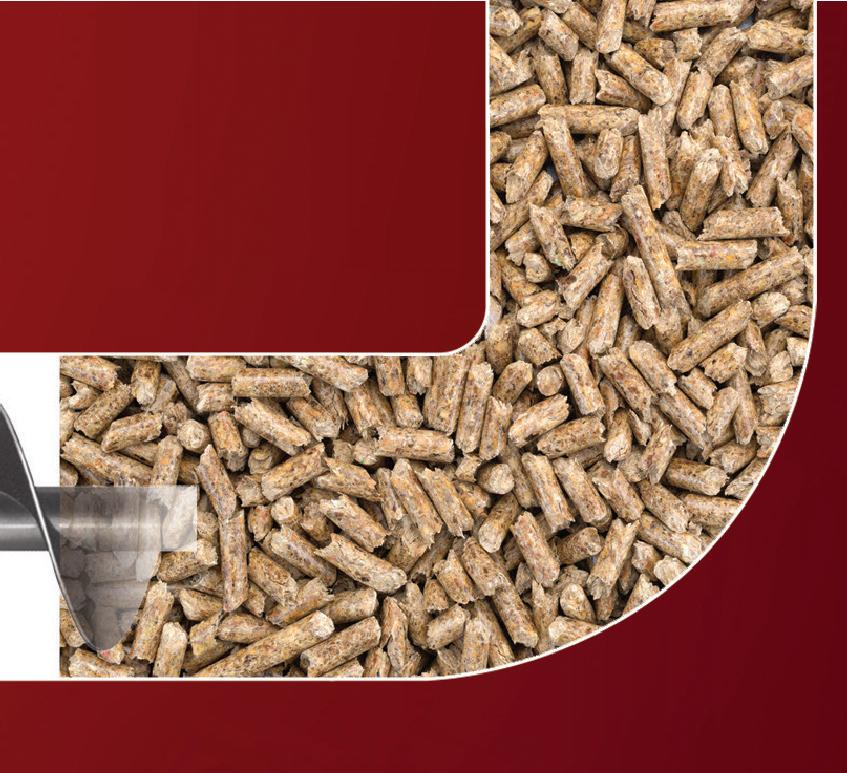
For the Wood Pellet Industry
Screw Conveyor Corporation has provided engineered material handling solutions since 1932. We focus on Screw Conveyors, Screw Feeders, Round and Flat Bottom Drag Conveyors, as well as Centrifugal and Continuous Bucket Elevators (both belt and chain). Visit screwconveyor.com to learn more about our capabilities. We look forward to working with you on your next engineered material handling solution!
700 Ho man St., Hammond, IN 46327-1894 Phone 219-931-1450
to another, so being able to measure under relevant test conditions will substantially increase the likelihood of generating useful data. Also consider practicality. How easy is it going to be to measure samples? How much training is likely to be required and how much ongoing effort? Automation can make a major difference to the day-to-day productivity of an instrument while simultaneously improving data integrity. Think about who will use the tester, how much effort will be involved and the likely payback in terms of information flow. Look for evidence that the instrument can deliver a solid return on investment by solving expensive problems.
What can be learned from bulk powder testing and differentiating biomass feedstocks with respect to pelleting energy consumption?
In this example, four biomass feedstocks were used to make pellets (Figure 2). The associated energy consumption varied considerably, but no robust correlation was observed with particle size, moisture content or particle shape (aspect ratio). Can bulk powder testing provide relevant differentiation? The data in Figure 3 shows that it can. Compressibility values rank the feedstocks in terms of the energy required for pelletization, since more compressible materials poorly transmit compressive forces, thereby consuming more energy.
What Insight can bulk powder testing provide?
Figure 1 shows two samples of cellulose-based biomass—one untreated the other post-acidification. These two samples are visibly different, but what does this mean for ease of processing? Can bulk powder testing provide any relevant insight? Data shows that it can. Repeatable values of basic flow integrity, a property that quantifies dynamic flow behavior (Figure 4) were successfully measured for both materials. These show that the untreated material presents greater resistance to flow than the treated material under low-stress, forced-flow conditions, as applied during processes such as blending. Both samples are highly permeable, but this test indicates that the treated material is less permeable and more sensitive to consolidation (applied normal stress). These differences are relevant to storage and hopper discharge behavior.
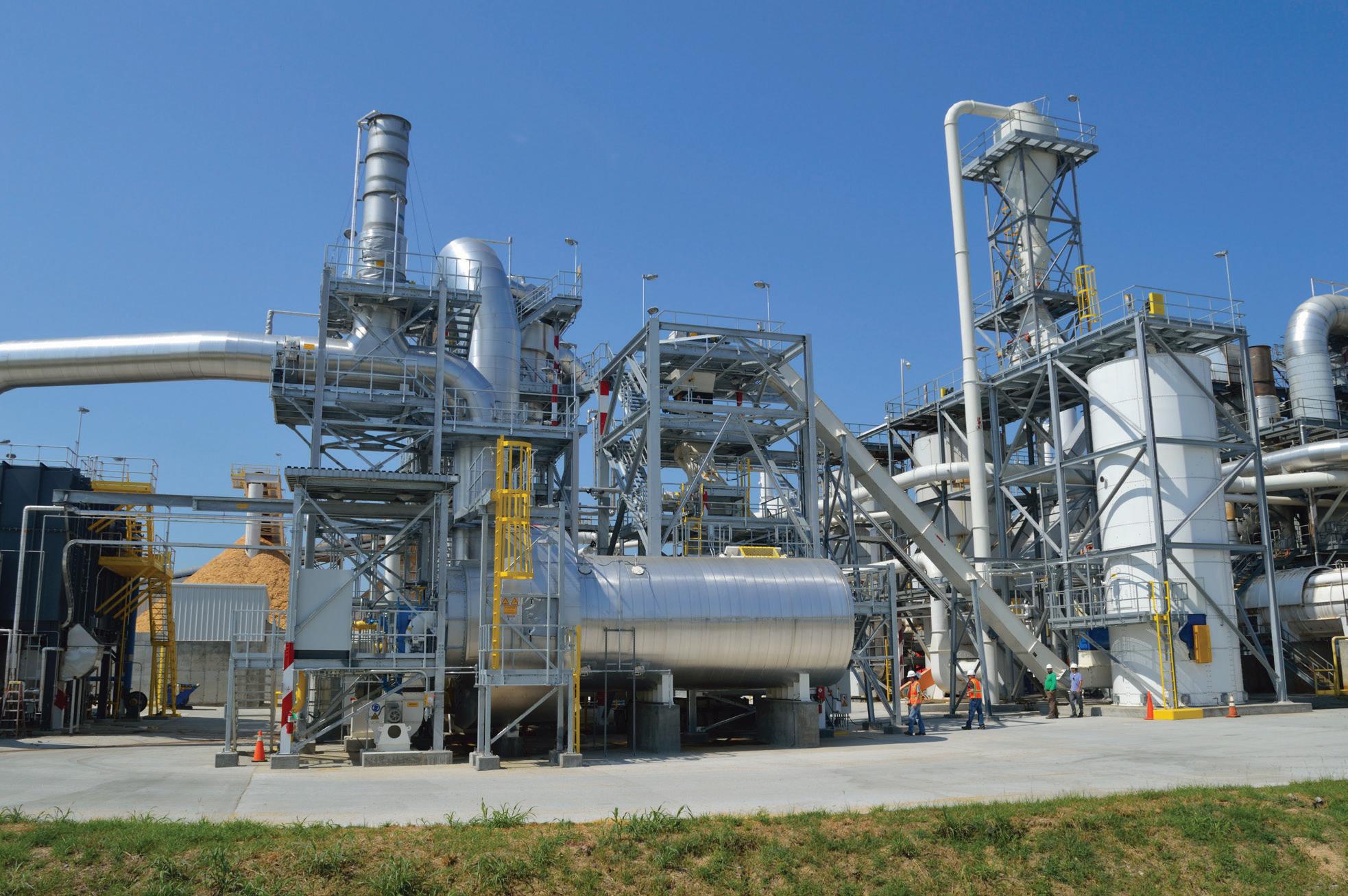
What are some last tips for just starting out with powder testing?
In my experience, those working with bulk solids, whatever their industry, ultimately conclude that bulk powder behavior, notably flowability, cannot be quantified with a single number. Therefore, it is advised to be to very realistic with respect to expectations if you are considering investing in instrumentation with limited capabilities, and avoid doing so if possible. Another recommendation is to check out a tester with some of your own samples. Bulk solids and powders vary enormously, so don’t rely on performance with a material that is very different from your own. Where possible, get some samples measured, because then you’ll be able to see whether the results highlight differences that you know are relevant. Finally, though many professional engineers and scientists have minimal knowledge of powder testing, it is easier to access useful information than you might think. Look for an instrument that is easy to use, backed by relevant application support and easy-to-digest literature, and you could be successfully troubleshooting your biomass feedstock in weeks. And the rewards can be substantial, particularly when it comes to solving long-standing problems.
Author: Jamie Clayton Operations Director, Freeman Technology www.freemantech.co.uk