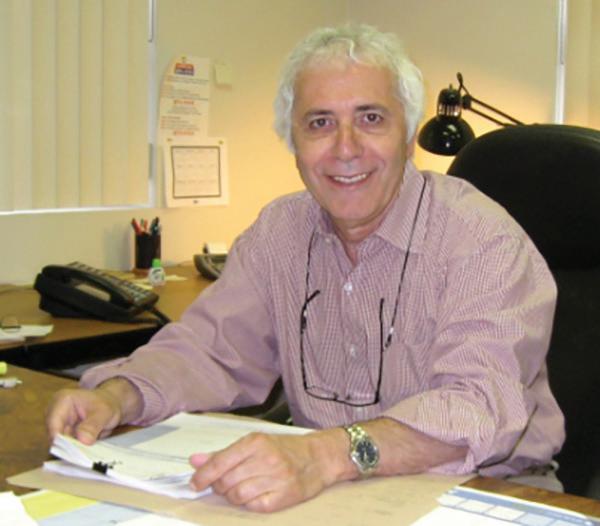
5 minute read
The Fiber Takers
BY TIM PORTZ
Alongside a working group of members, the Pellet Fuels Institute is updating some messaging documents that outline the societal, economic and environmental benefits of wood pellet production and use. This effort has included a thorough vetting of the myriad claims and benefits our organization has championed, trumpeted or touted over the course of the past decade. Those well acquainted with our sector have heard our story of rural jobs, localized energy expenditures and low-carbon heating before, and they are no less relevant today than they were when we started sharing them. Still, over the course of our efforts, our role as fiber takers continues to shine most brightly as an irrefutable, undeniable reality of our contribution to the larger forest products sector. Industry, including wood pellet manufacturing, will always have its detractors. Those detractors work tirelessly to poke holes in the various value propositions industry proponents bring forward, including the arguments proffered by the Pellet Fuels Institute. Fortunately, our annual expenditures and annual volumes of sawmilling and wood product manufacturing residuals are tracked and reported by the U.S. Energy Information Administration, and have been since 2016. The accumulated data tells a compelling story measured in billions of dollars spent on what otherwise might be considered waste.
When the EIA launched its Monthly Densified Biomass Fuel Report, it began tracking feedstock purchases by wood pellet manufacturers in four different categories: sawmill residuals, wood product manufacturing residues, other residuals and roundwood/pulpwood. Both tonnage and cost per ton are reported in each category every month. A deep dive into the data makes it clear that wood pellet manufacturing provides not only a home for an incredible volume of material, but also extends the overall value of wood via these ongoing residual purchases.
Consider the numbers from 2020 alone. Last year, wood pellet producers purchased 4.1 million tons of sawmill residuals worth $134 million, 4.6 million tons of wood product manufacturing residuals worth $171 million and 5.7 million tons of other residuals worth $172 million. Collectively, that’s 14.5 million tons of shavings, chips and sawdust worth nearly $500 million. 14.5 million tons can be difficult to picture. Instead, imagine a convoy of tractor trailers over 7,000 miles long. For reference, Anchorage is about 5,000 road miles from Miami. This imagined convoy, with trucks inching along bumper to bumper would thread all the across Canada and the U.S. and halfway back again. Most importantly, these materials are generated because of the manufacture of other, higher-value products, and they must go somewhere. Waste professionals constantly bemoan the general public’s struggle to grasp the concept of waste streams and what happens to them. These professionals often joke about the mythical place called “away,” where waste ultimately goes. The joke, of course, is that there is no “away,” and that these materials—whether they be food waste, standard municipal solid waste (MSW), sawdust or wood chips—must go somewhere. Typically, disposal of waste streams comes at a cost. For MSW, these costs come in the form of tipping fees. The Environmental Research & Education Foundation tracks the national average for tipping fees, and reported that in 2019, the nationwide average was $55.36 per ton. Imagine, for a moment, that instead of being purchased by wood pellet manufacturers, every ton of these manufacturing residuals had to be landfilled. At $55.36 per ton, the cost to wood product manufacturers would be a staggering $802 million. Because of the demand generated by wood pellet manufacturers, this potential $800 million expense is transformed into a $500 million revenue stream, a swing of over $1.3 billion.
As a sector, we need to make more of this compelling reality, and attract more people and more constituents to our various causes.
Wood pellet manufacturing is a vital piece of our country’s forest product sector. As fiber takers, we allow our upstream partners to focus on the manufacture of high-value forest products with the full confidence that consistent, reliable offtake partners stand ready to convert those materials into a low-carbon, cost-effective home heating solution relied upon by millions of Americans each winter.
Author: Tim Portz Executive Director, Pellet Fuels Institute tim@pelletheat.org www.pelletheat.org
Bulk Procurement Automation Reduces Risk
COVID-19 makes an easy case for automation, but the benefits extend well beyond mitigating risk during a pandemic. When it comes to bulk procurement of feedstock for pulp and paper mills, ethanol plants and pellet producers, CDCorp’s Bulk Procurement and Logistics System, or BPAL, offers a solution that removes risk from the raw material supply chain and creates long-term benefits that extend beyond the present moment. “Our original intentions were to build a system that would improve efficiency along the raw material supply chain so that businesses could focus more time and resources on growth development,” says Jay Shatilla, president of CDCorp. “With the pandemic, we see the added benefit of a contactless interface in reducing risks to human safety and keeping businesses operating efficiently during times of uncertainty.”
It’s no secret that automating manual processes generates costsaving benefits by reducing human resource allocations, lowering the occurrence of human error and building real-time operational and administrative efficiencies. CDCorp’s BPAL System was designed not only to deliver these benefits, but also to address and remove pain points specific to bulk procurement. “The BPAL System was born out of a clearly articulated need for increased efficiency across the raw material supply chain,” Shatilla says. “We’ve enhanced and expanded its features over the past 10 years in direct consultation with supply chain managers to understand and improve the day-to-day experience of people operating in this field.”
BPAL integrates hardware and software systems to reduce manual participation in bulk feedstock delivery while providing real-time remote management and administrative control functions. The system uses barcode readers and activation relays that allow for unmanned access and delivery Jay Shatilla, president, CDCorp. control stations. Through automated sequencing of entry and exit access control, traffic monitoring, inbound and outbound weigh scale registration, sample control, quality analysis and delivery point control, BPAL reduces the risk of human error and maximizes operational efficiency during delivery.
On the administrative side, BPAL’s user-friendly interface provides remote access to real-time reporting and information transfer, vendor, payment, contract management and feedstock delivery transaction reporting from all connected devices. CDCorp offers free consultations and on-site installation of its BPAL system.

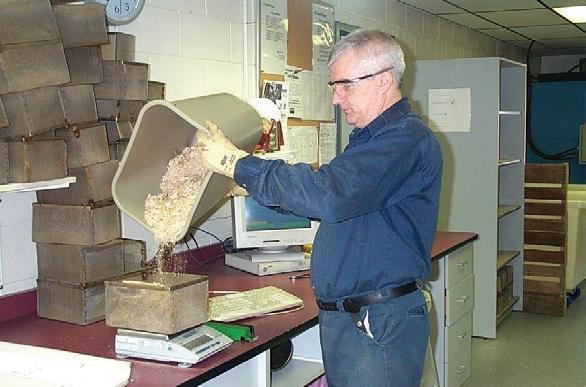
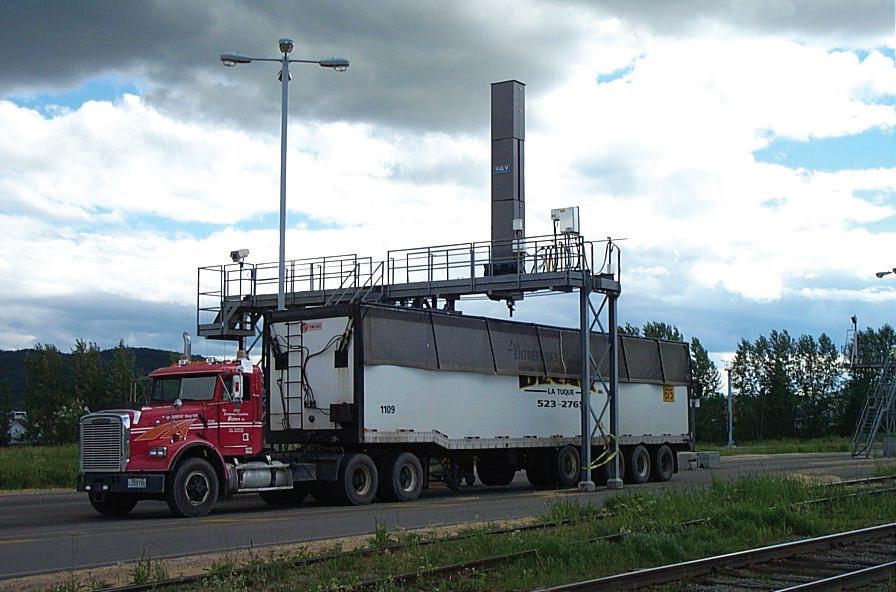

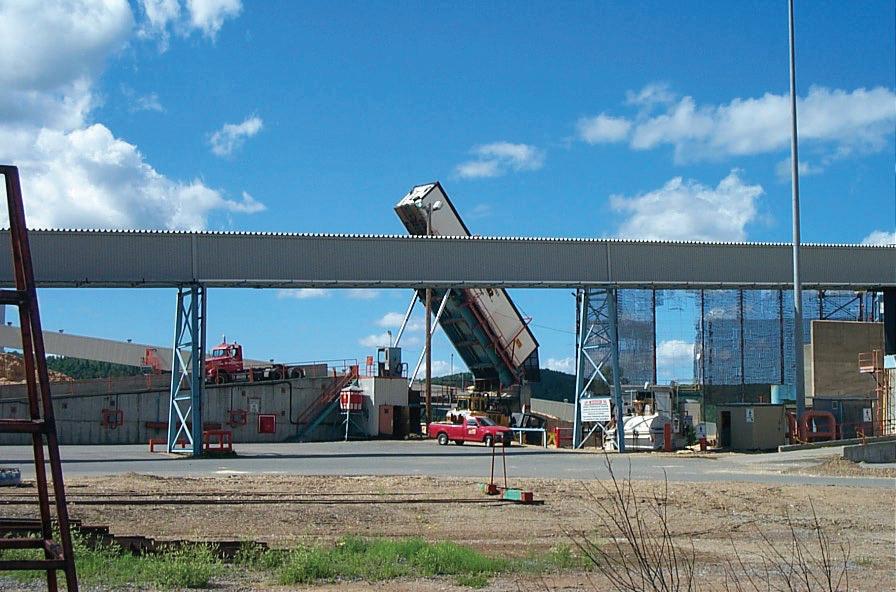
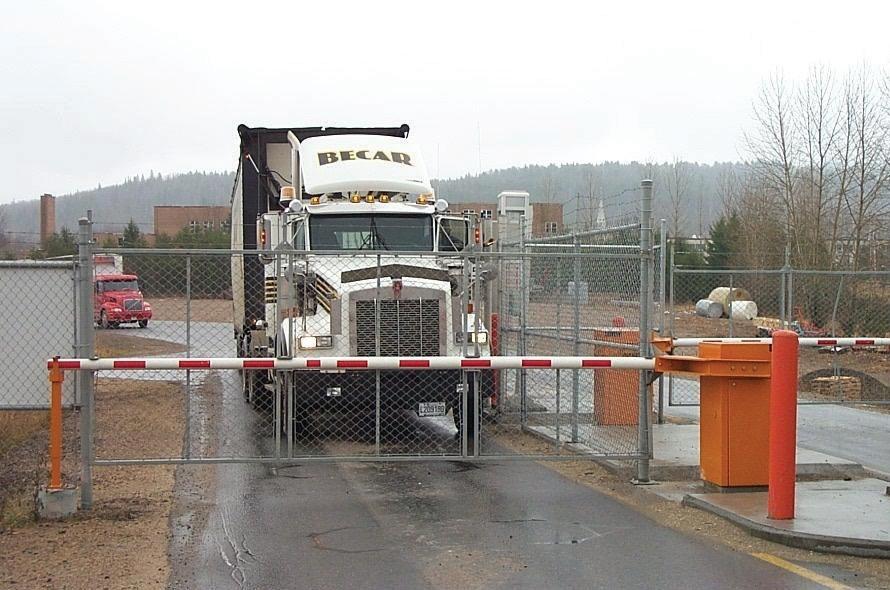