
39 minute read
BUSINESS BRIEFS
PEOPLE, PARTNERSHIPS & PROJECTS
Element shifts focus to high-protein animal feed
Element LLC in Colwich, Kansas, has been refocused to produce ANDVantage 50Y, a yeast-enriched 50% protein animal feed. The process utilizes three proprietary technologies from ICM: patented Selective Milling Technology, patented Fiber Separation Technology Next Gen and patentpending Thin Stillage Solids Separation System.
Element, a joint venture between ICM Inc. and The Andersons Inc., became fully operational in 2019 and oriented its pro-
Flint Hills Resources is now producing and delivering its trademarked NexPro protein ingredient from its Shell Rock, Iowa, ethanol plant. The company installed Maximized Stillage Co-Products technology at the 125 MMgy plant earlier this year, making it the second FHR plant to install MSC under license from Fluid Quip Technologies.
NexPro protein ingredient will be used in a variety of animal feed rations globally. duction to ANDVtantage 50Y after an operational pause in 2020. The feed, which will be marketed by The Andersons, has both higher protein and lower fiber than traditional ethanol coproducts.
“In addition to producing a high-quality combination of corn and yeast proteins, these processes deliver higher efficiencies and operational cost savings throughout the production process,” said ICM Presi-
FHR producing NexPro coproduct at second plant
dent Chris Mitchell. The product is made by extracting protein from an ethanol plant’s whole stillage. The process yields not only a 50% high-protein feed ingredient with premium market value, but also residual distillers grains and enhanced levels of distillers corn oil. NexPro will be sold locally, nationally, and internationally, competing against corn gluten meal, soy, corn protein concentrates and fishmeal.
Reach Producers
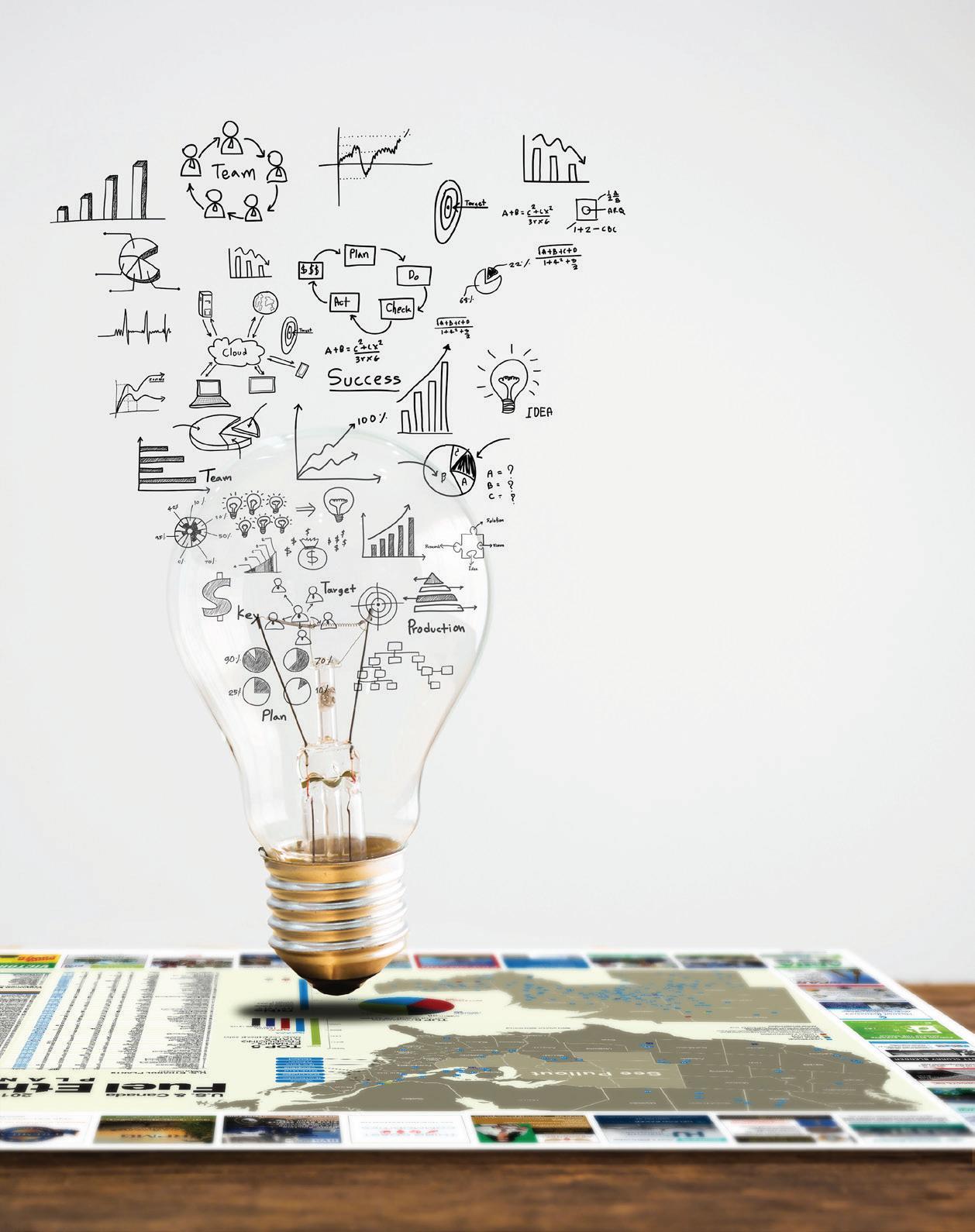
REACH 8,000 PROFESSIONALS
All Ethanol Producer Magazine subscribers All Ethanol Production Facilities All major Ethanol related events Distributed to all Fuel Ethanol Workshop & Expo attendees
Book Your Ad AD SPOTS LIMITED Summer 2021 Map Ad Deadline: Apr. 20, 2021 Mailed with the July 2021 Issue of EPM
PURCHASE A SPOT ON THE ETHANOL PLANT MAPS
Receive 6 Months FREE Online Advertising! Advertise now on Ethanol Producer Magazine’sU.S. & Canada Ethanol Plant Maps. It is the easiest and most cost-effective way to get your name, product and/or service in front of Ethanol Producers, as well as other ethanol professionals for 6 months at a time.
Need info on advertising opportunities? service@bbiinternational.com - 866-746-8385 EthanolProducer.com
Construction on cellulosic ethanol plant in Romania continues
Clariant is progressing on schedule with the construction of a cellulosic ethanol plant in southwestern Romania, according to the company. Despite the challenges of the COVID-19 pandemic, Clariant’s team has been able to ensure that the facility’s construction has carried on. To do so, the company has had to fully comply with all of Romania’s precautionary safety regulations.
The plant is being constructed on a 10-hectare plot of land in the town of Po-
Pacific Ethanol Inc. has closed on a $10 million deal with Liberty Basin LLC to sell 134 acres of land including a rail loop and grain handling assets at its Magic Valley ethanol plant in Burley, Idaho. Pacific Ethanol will retain the ethanol plant and terminal on the remaining 25 acres and has entered into agreements with the buyer for grain delivery. dari, where it has access to a secure regional supply of feedstock and the region’s existing logistic and industrial infrastructure.
Once operational, the facility will produce 50,000 metric tons of cellulosic ethanol annually from approximately 250,000 metric tons of straw. The plant’s construction is expected to be complete by the end
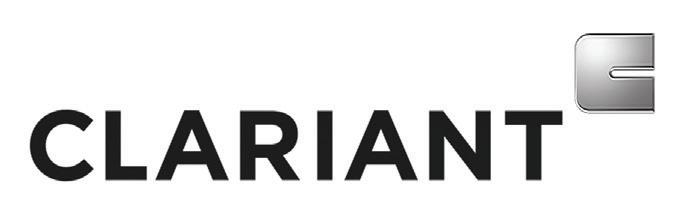
Pacific Ethanol sells Idaho grain handling facilities
of 2021.
“The sale of real estate and grain handling assets at our Magic Valley facility marks further progress in our strategic realignment around higher, more stable margins in specialty alcohols and essential ingredients,” said Pacific Ethanol’s CEO Mike Kandris, adding that the company will restart the facility after it is repositioned to produce higher-value products.
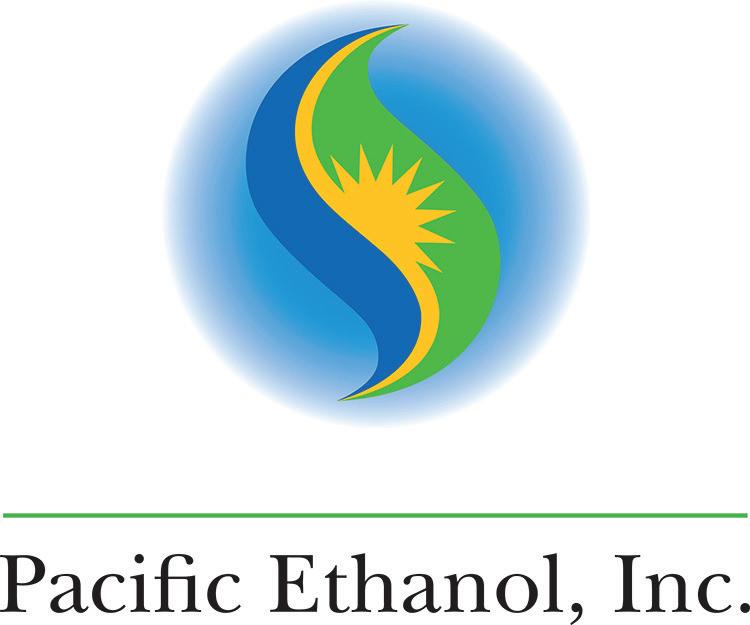


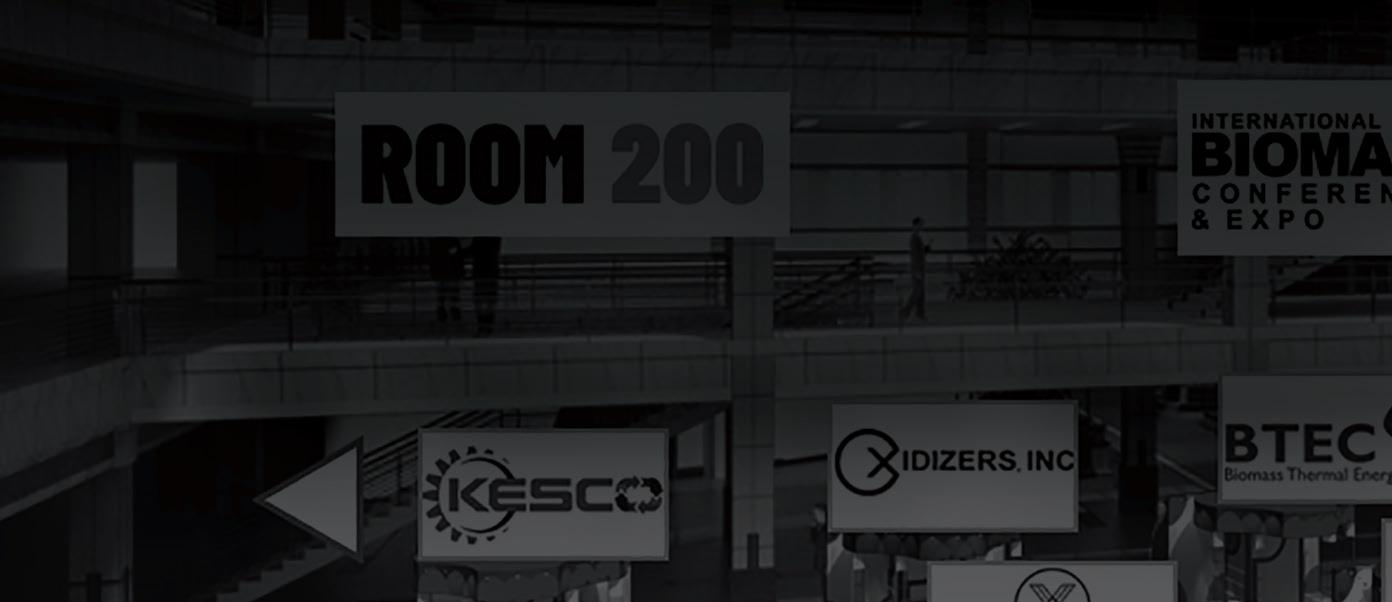

Capitalize onNew Opportunities, OvercomeNew Challenges
Get Educated & Network PELLETS BIOGAS & RNG
R E G I S T E R T O D A Y BIOMASS POWER BIOMASS THERMAL DENSIFIED BIOMASS WASTE-TO-ENERGY ADVANCED BIOFUELS BIOBASED CHEMICALS 14th Annual March 15:17, 2021
VIRTUAL EVENT BIOMASSCONFERENCE.COM



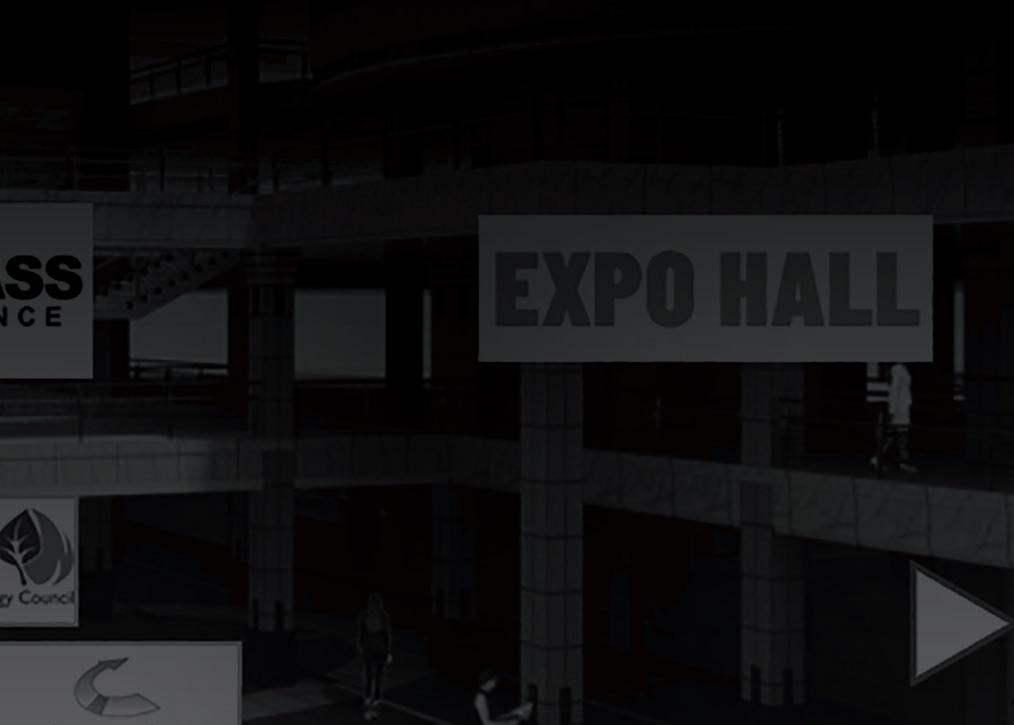
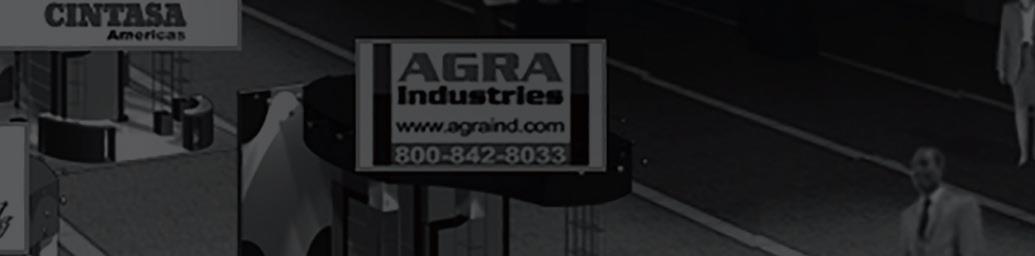
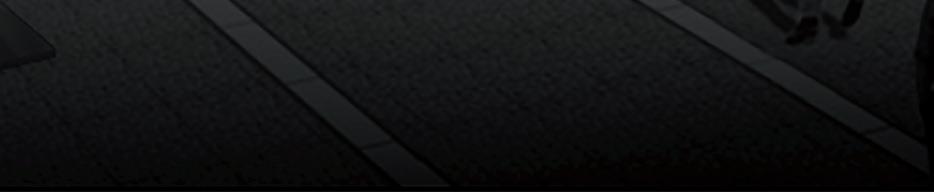
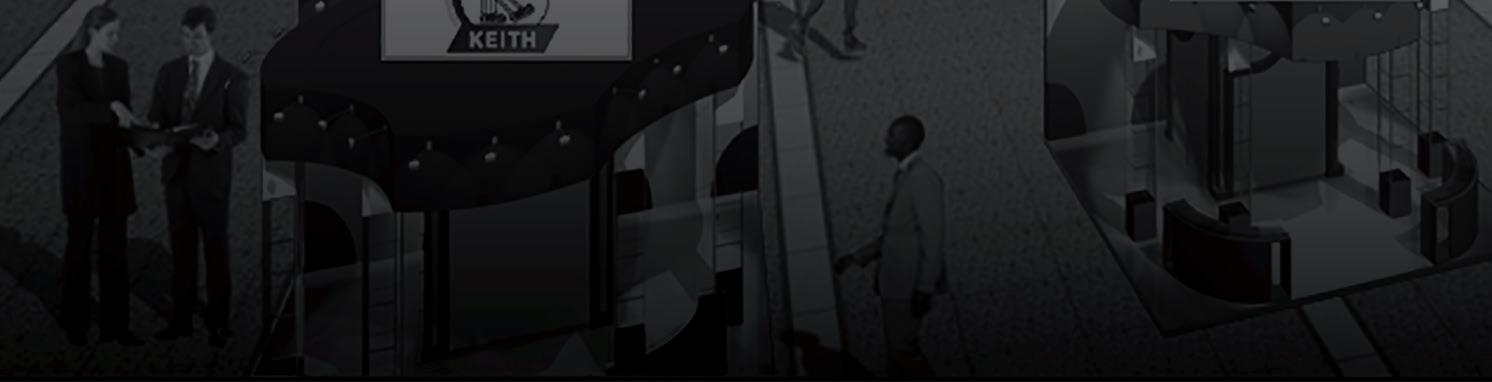


VIRTUAL EVENT
twitter.com/biomassmagazine 866-746-8385 service@bbiinternational.com
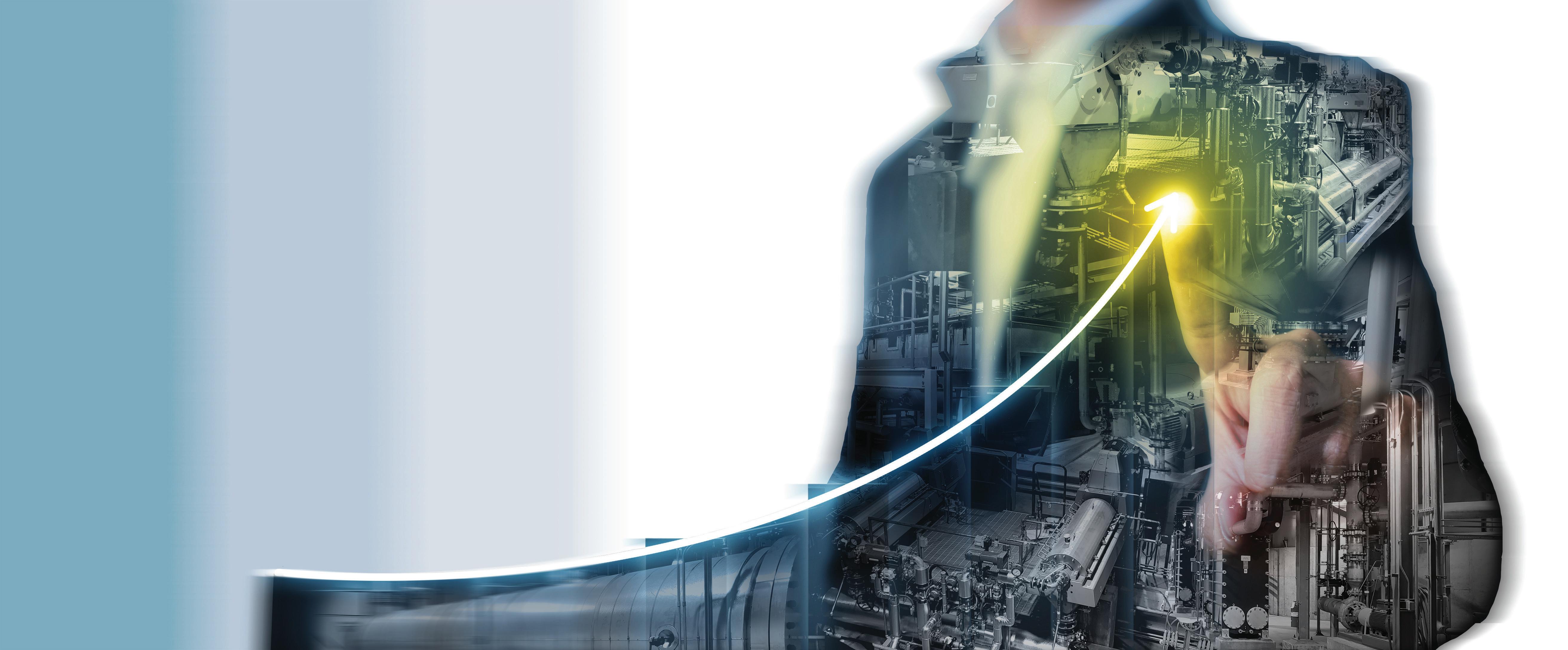
FIBER IN HAND: Novozymes has released a new platform of products to complement and enhance both in-situ and separate corn fiber conversion. The company's scientists are eager to continue releasing new, improved iterations. PHOTO: NOVOZYMES
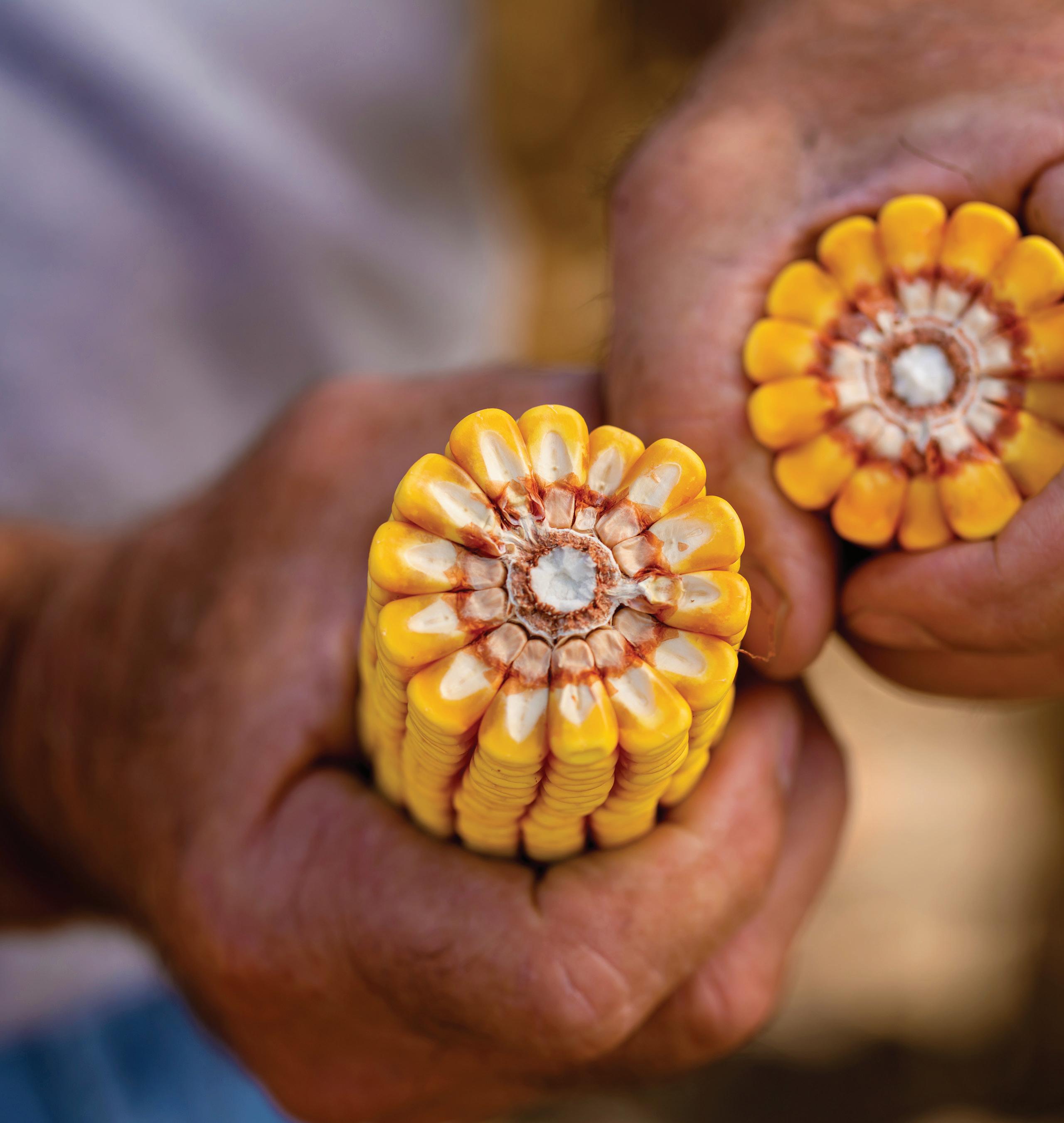
Novozymes has released a platform to help convert more fiber to ethanol, and looks ahead to higher conversion in future iterations. By Lisa Gibson
It’s the rallying call at Novozymes: “Fiber is the new starch.”
“It’s to work so hard that we don’t talk about fiber anymore— we don’t have to,” says Kalpesh Parekh, senior manager in business development for Novozymes. “It becomes so easy and so normal that it’s not special anymore. But to get to that point, it’s a lot of hard work.”
Novozymes has released its Fiberex platform, for in-situ and separate corn fiber processing: Fiberex F1 and Fiberex R1. The Fiberex platform reimagines ethanol, Parekh says. “This goes back to our customers’ needs. They’re looking to diversify their business and make it more sustainable.
“Fiberex is not a product, it’s a platform,” Parekh says. “And the idea is to consistently launch breakthrough solutions for new products, be it enzymes, be it organisms like yeast, or process pieces to work together to then convert fiber into ethanol.”
More than a decade of biomass conversion expertise has lent
Introducing the SYNERXIA ® Gem Collection
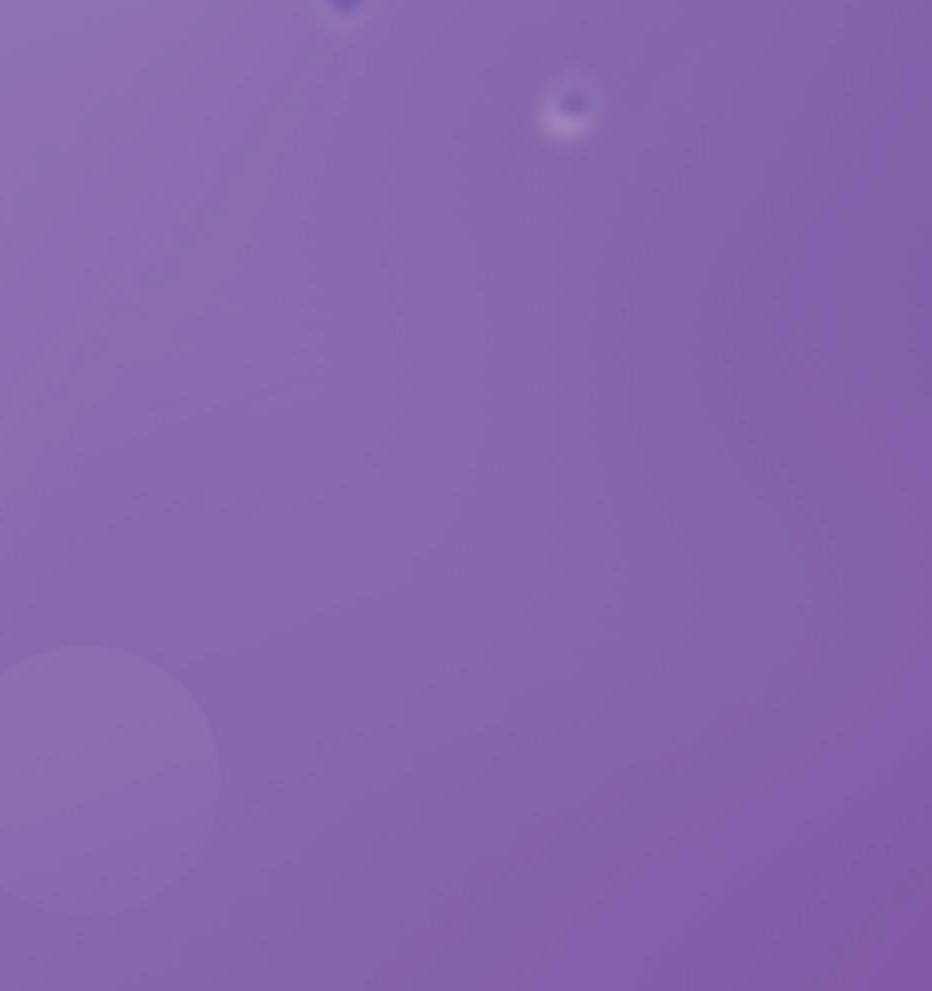
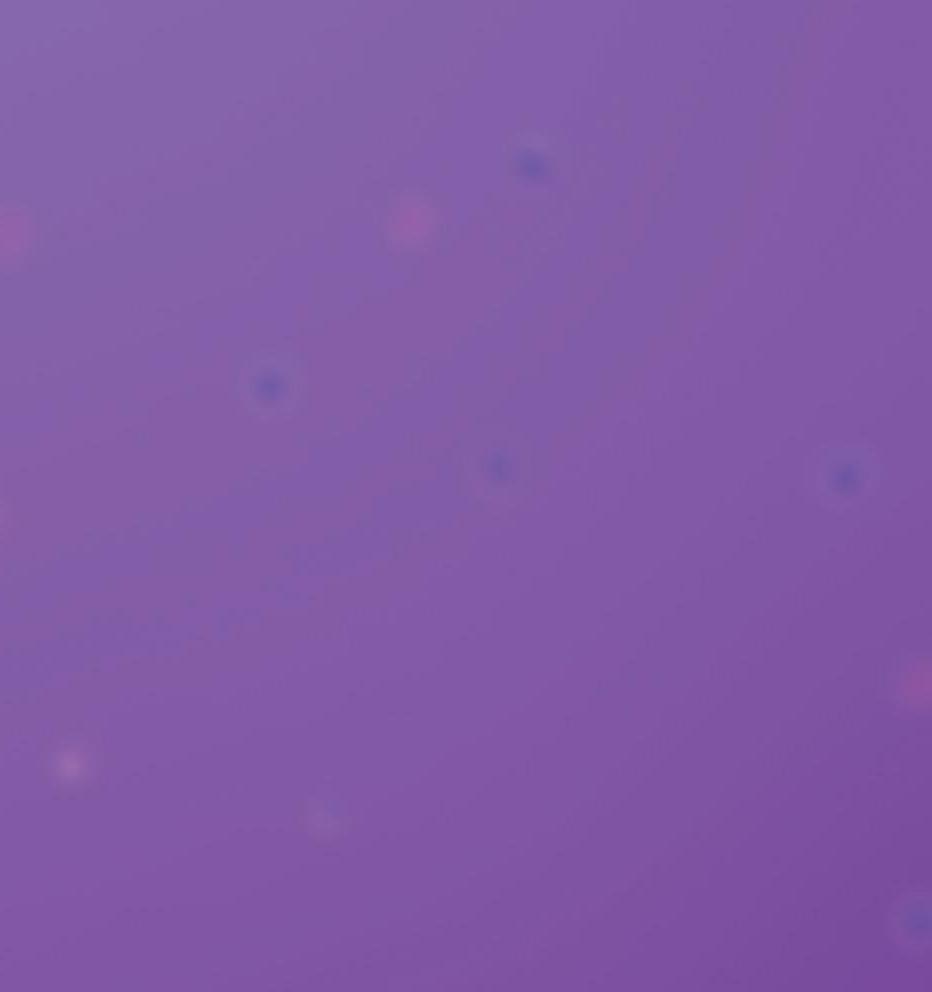
The next advancement in high-performance yeasts to make your plant shine.
www.xcelis.com
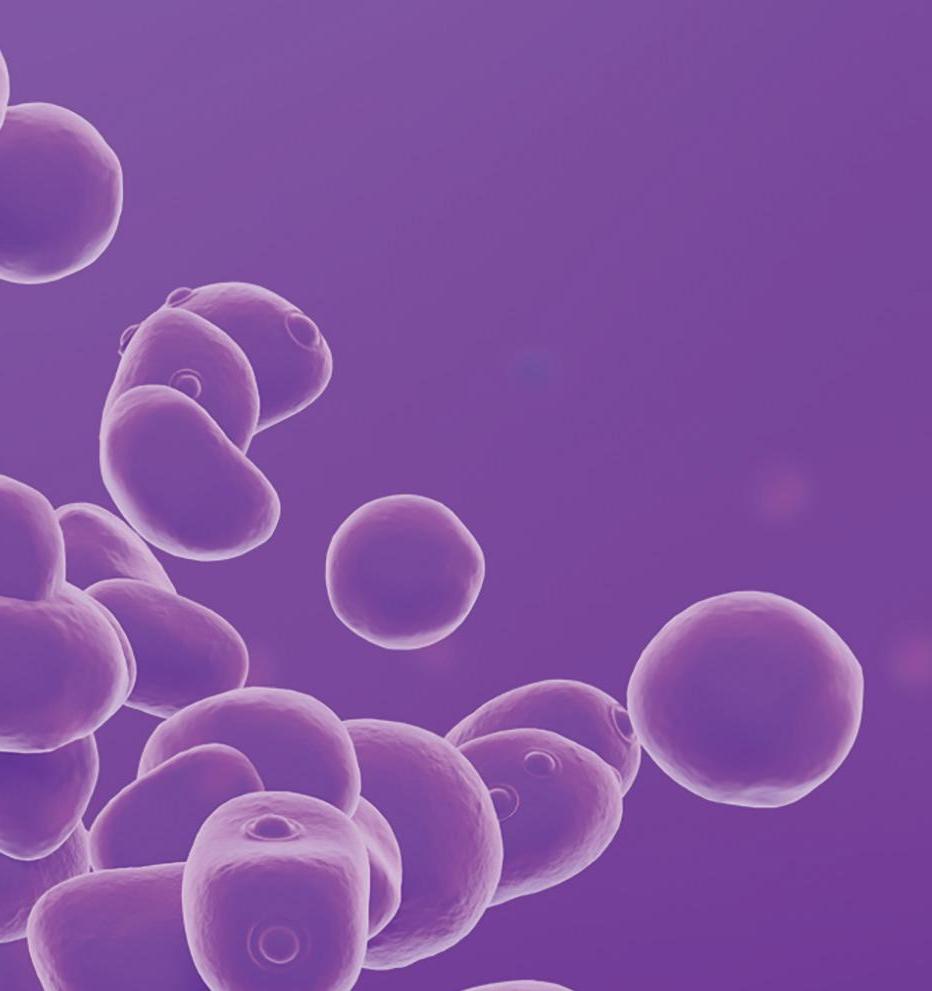
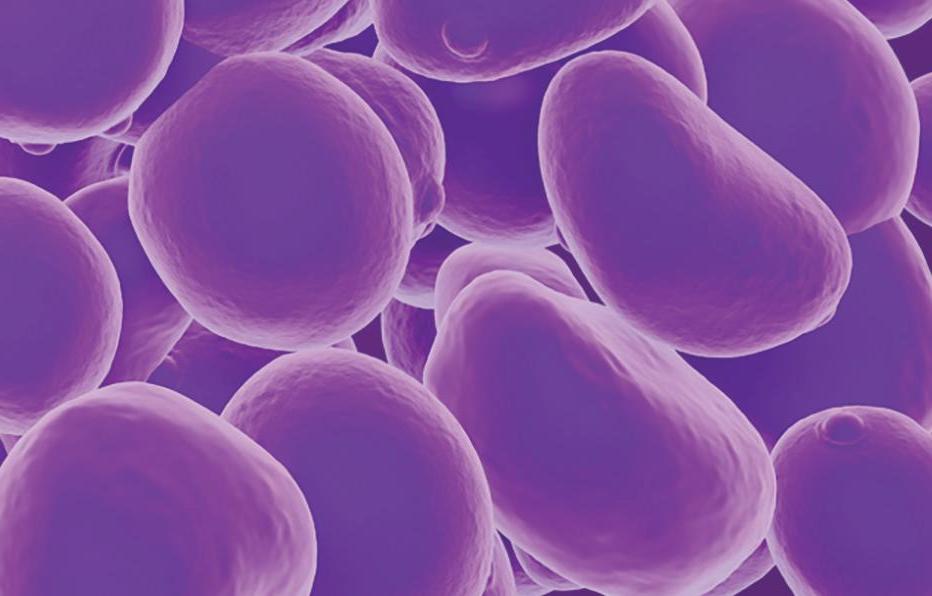

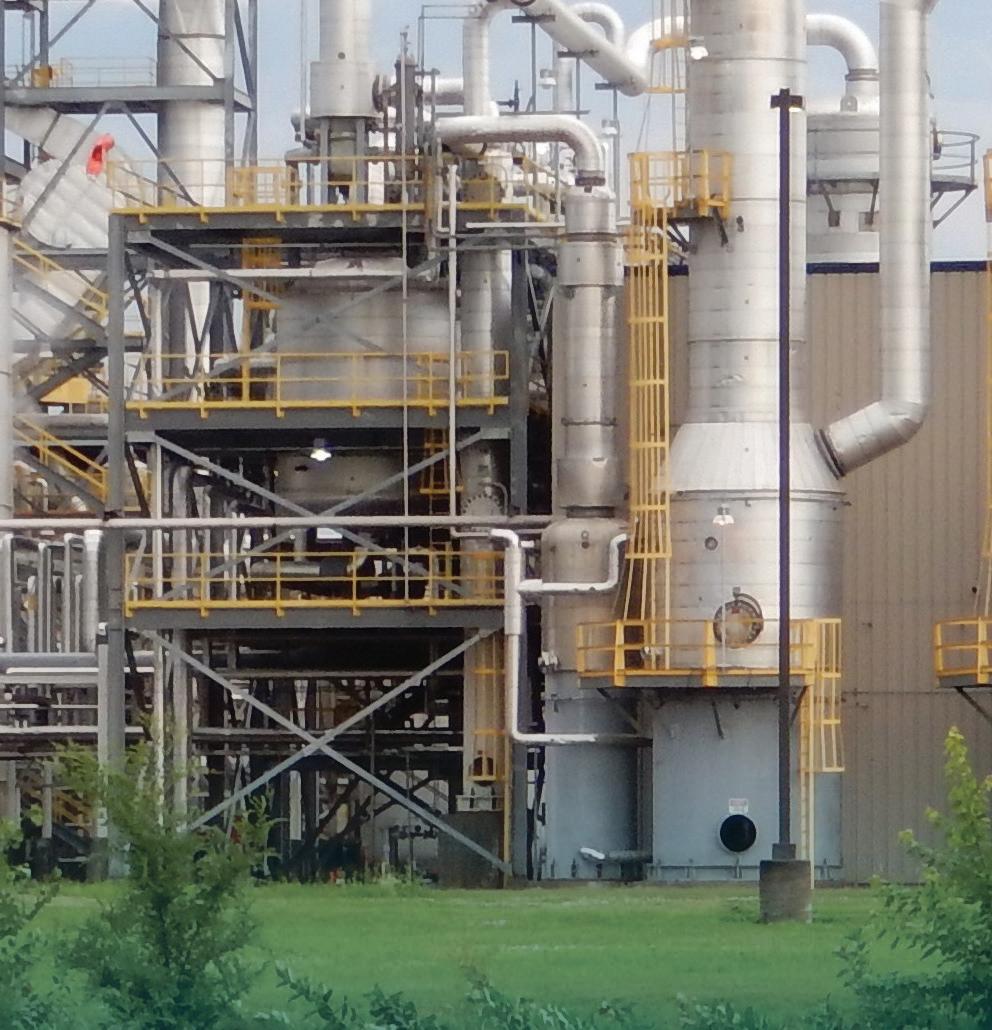
FIBER FLEXIBILITY: Fiberex enables drop-in and bolt-on fiber applications, diversifying into lowcarbon and high-value coproduct markets. SOURCE: NOVOZYMES
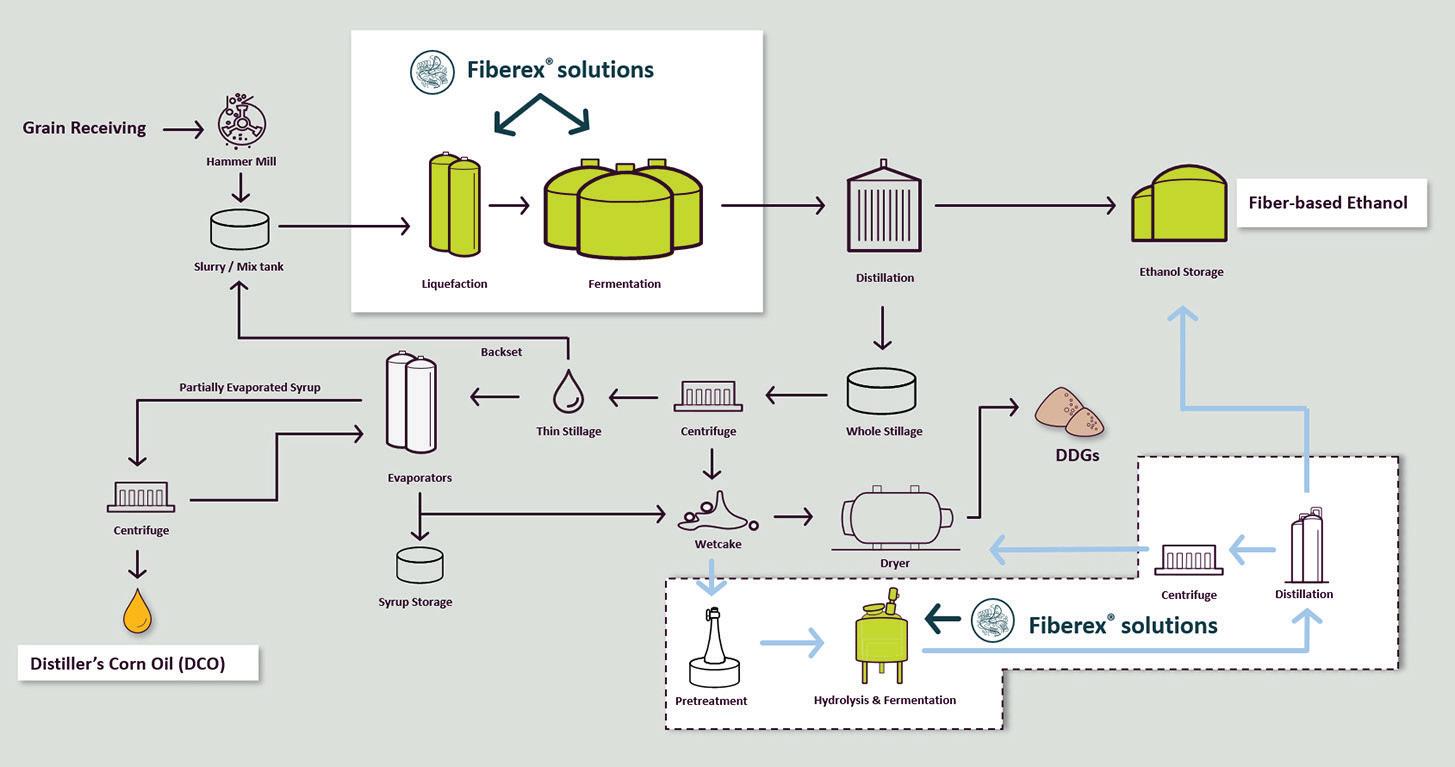
NEW INDUSTRY TOOL NOW AVAILABLE

‘State of the Industry’ Ethanol Data Hub
Explore Growth Energy’s new data hub presenting the latest information on America’s biofuel industry, with user-friendly tools to track and visualize important trends — from ethanol production and exports to U.S. blending.
Learn more at
GrowthEnergy.org/datahub
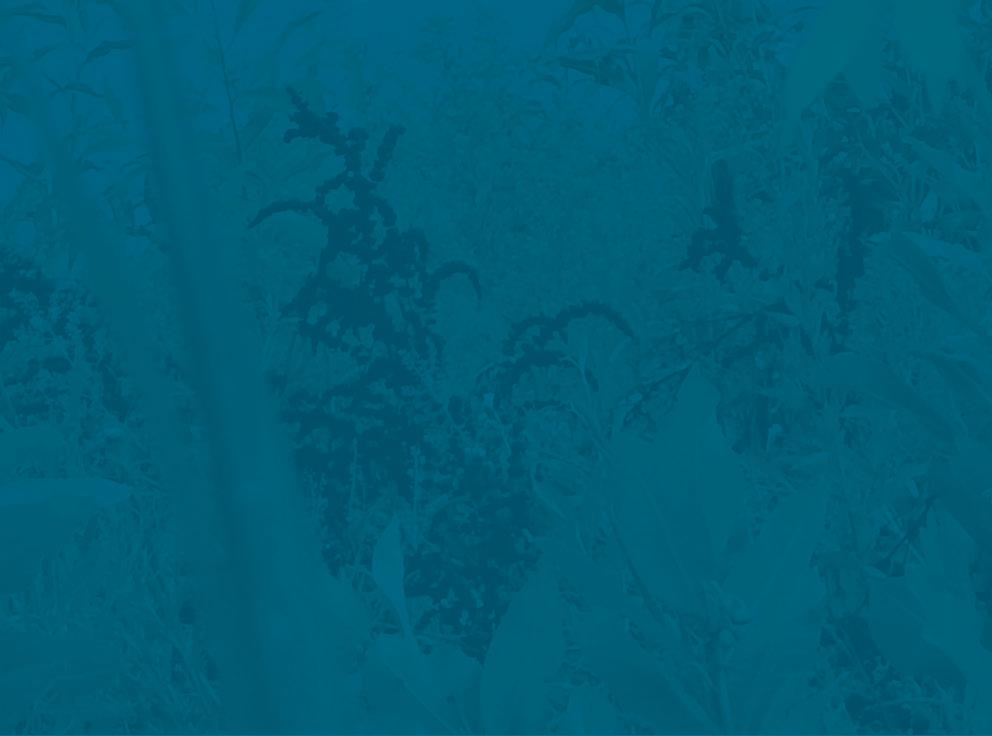
Novozymes research and development firepower to leverage. “We have learned a lot and now we are investing more in fiber-focused solutions to make tailormade products for fiber conversions.”
Brian Brazeau, Novozymes’ vice president for bioenergy, adds, “I would really characterize it as Novozymes even helping to lead the market. We have a long history of looking at complex substrates, biomass, how do we break that down and create value? How do we take our biological tools, apply them to this biological raw material and allow our customers to create value from that?”
The pandemic in 2020 followed 2019’s negative producer margins, and the ethanol industry has struggled, Brazeau says. “It’s really about us understanding that our customers have been hurting, have been looking at additional ways to create value. We do know how to develop microbes that break down complex materials like fiber, and help our customers create value from them.”
The Platform
Fiberex R1 is an enzyme for separate conversion. Because the product focuses specifically on conversion of pretreated fiber into ethanol, and uses the appropriate high dose of enzyme, the fiber conver-
'Fiberex is not a product, it’s a platform, and the idea is to consistently launch breakthrough solutions for new products, be it enzymes, be it organisms like yeast, or process pieces to work together to then convert fiber into ethanol.' Kalpesh Parekh, Novozymes
sion is near 6%. “It’s a cocktail of enzymes that works really well with pretreated corn fiber,” Parekh says.
Fiberex F1, for in-situ processing, reaches more than 2% fiber conversion.
Both iterations allow producers to do more with less, Parekh emphasizes. “The same kernel of corn—create more ethanol, create more corn oil, reduce energy consumption and create maybe a little bit more sustainable future for us.”
The holistic approach Novozymes takes is crucial for optimal performance.
“The yeast can’t work and do its job optimally if it’s developed and designed
CENTRIFUGE STATS: Ace Ethanol in Stanley, Wisconsin, has switched to Novozymes’ Fiberex R1 in its bolt-on D3MAX process. Here, an Ace employee checks the system. PHOTO: D3MAX LLC
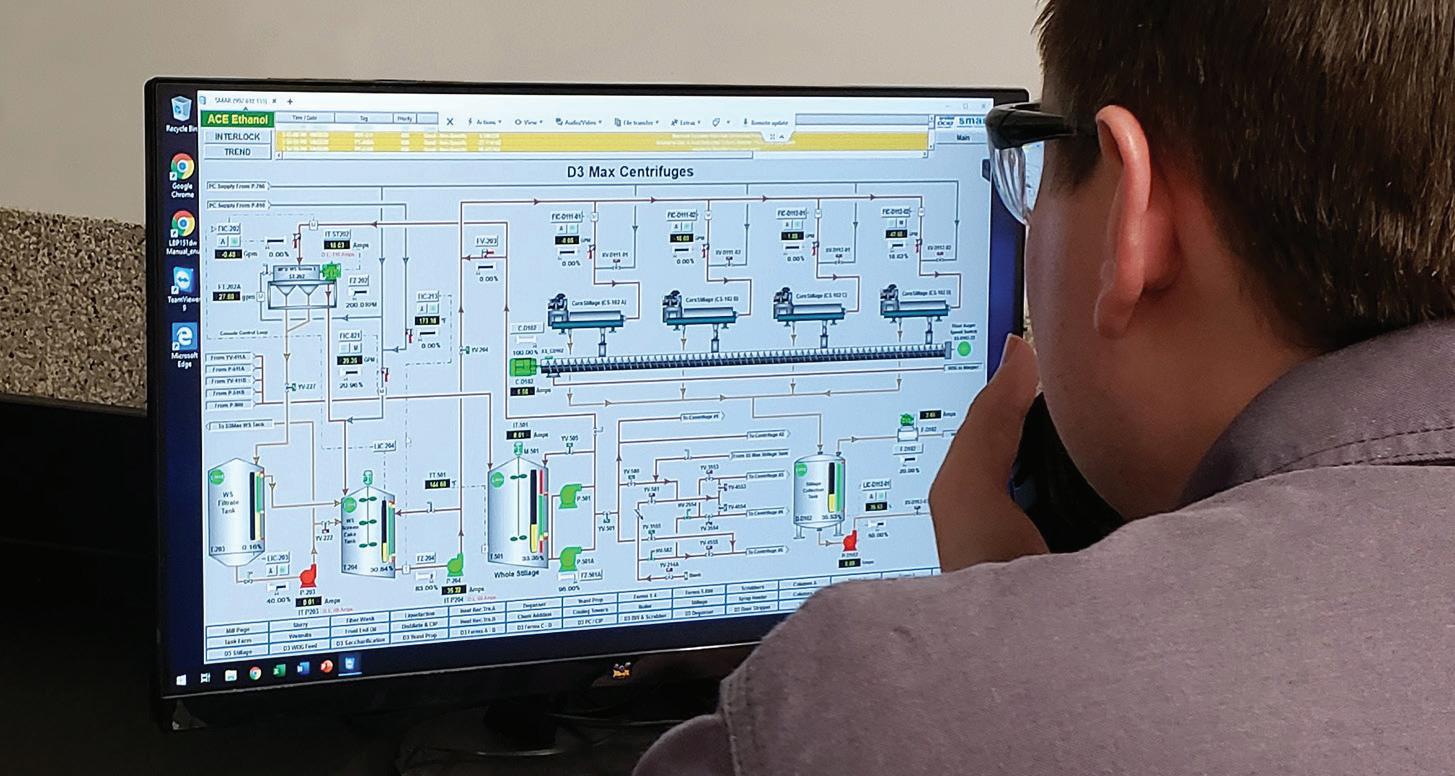
independently of the enzyme systems,” Brazeau says. “We’ve carried that thinking over.
“To create an optimal fermentation process to make ethanol, we need to link all these systems together. We’ve been a leader in thinking about how we do that and Fiberex is a good example of that.”
Ace Ethanol in Stanley, Wisconsin, recently switched to Fiberex R1 for its separate corn fiber conversion process, D3MAX. “They’re pretty happy about it.” Parekh says.
“The Novozymes enzyme will work better in our equipment,” says Mark Yancey, chief technology officer for D3MAX. “We expect better performance and are waiting on the data to confirm that.”
Brazeau says, “Our biology might marry well with a hardware or a processing technology to create value, and the advantage from our point of view, at least, is here is the additional value that an ethanol producer can create, which doesn’t require them to invest in any additional capital.”
D3MAX at Ace Ethanol started up in January 2020 and, through early December, had been online 310 out of 320 days. “Overall, the plant continues to perform very well,” Yancey says. “The online time is at 97 to 98%, so since Jan. 9 (2020), the first day of startup, we’ve only had a handful of days when the D3MAX plant was down. So, we’re extremely happy with that. It’s proven so far to be very reliable, which of course is a big plus for any kind of cellulosic process.”
Since startup, Ace has made modifications to the plant to correct some issues, including the optimized R1 for fiber conversion, Yancey says. Overall, the design and construction have worked well, he adds.
Since June, the D3MAX plant has made steady improvements to the amount of cellulosic ethanol produced. “Every month the amount of ethanol produced has gone up,” Yancey says. “The plant is now running at nearly 95% of design yield.”
The goal is 9,000 to 9,500 gallons per day, or a D3 lift of 6.5% or more. “We’re getting there.”
In-Situ R&D
Fiberex F1 is in use at a few plants, but Parekh is eager to continue releasing new iterations.
“We have heavily invested and continue to invest in in-situ fiber conversion because we realize that not everybody is able to invest in the capex,” he says. “So insitu fiber conversion is a big piece of what we do here.”
XCELIS® Yeasts SYNERXIA® SAPPHIRE
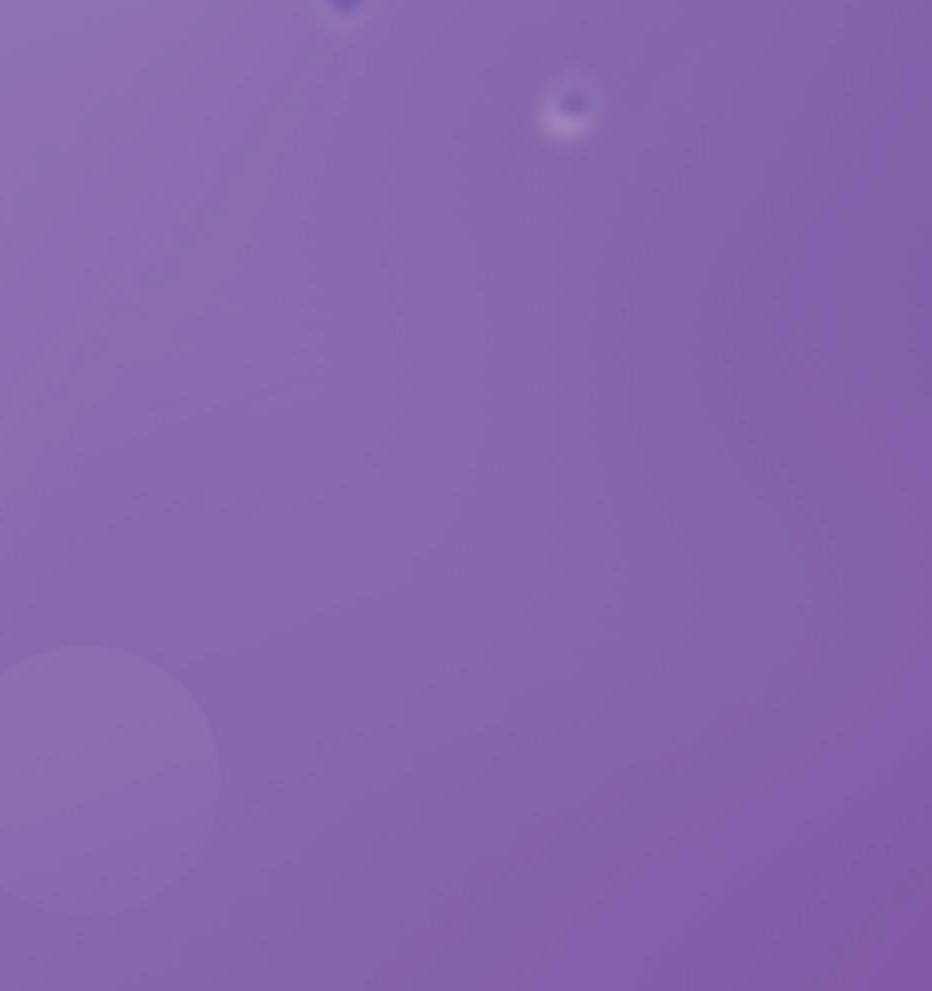
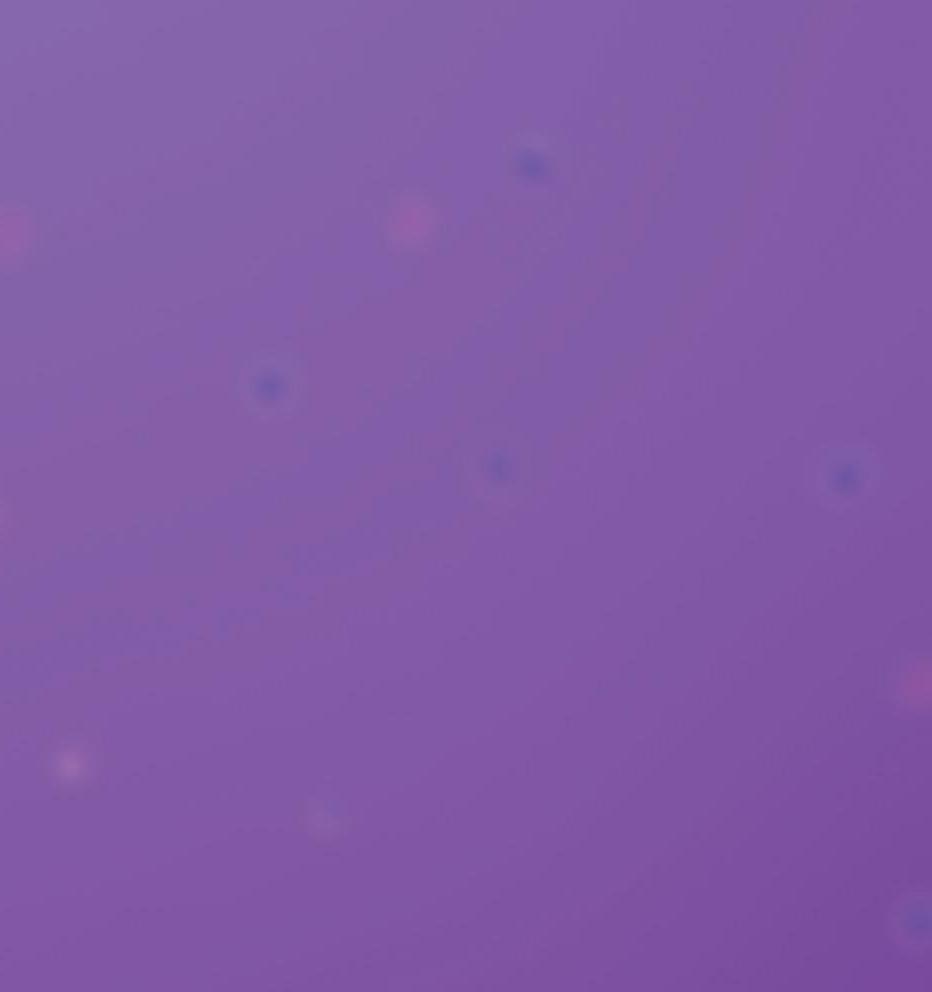
The most powerful combination of yield, robustness and enzyme expression in a yeast.
www.xcelis.com
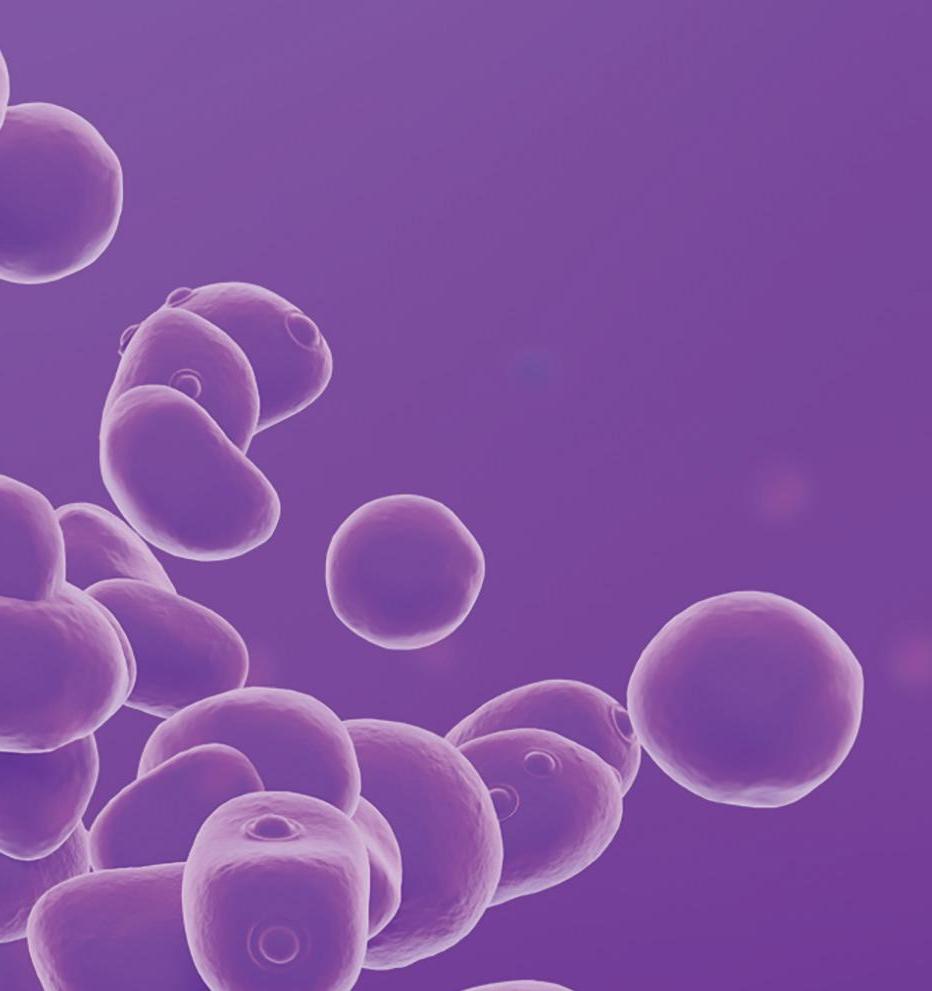
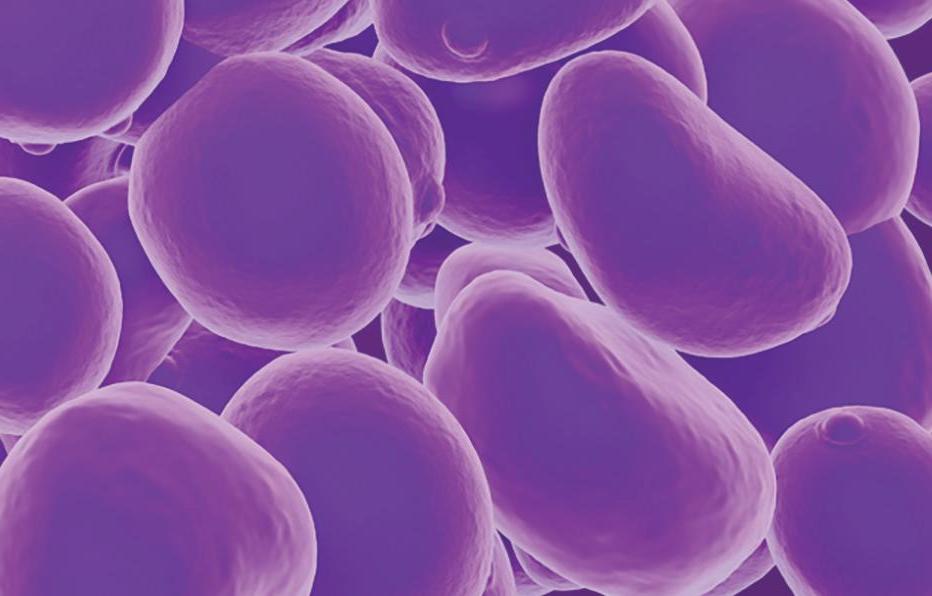

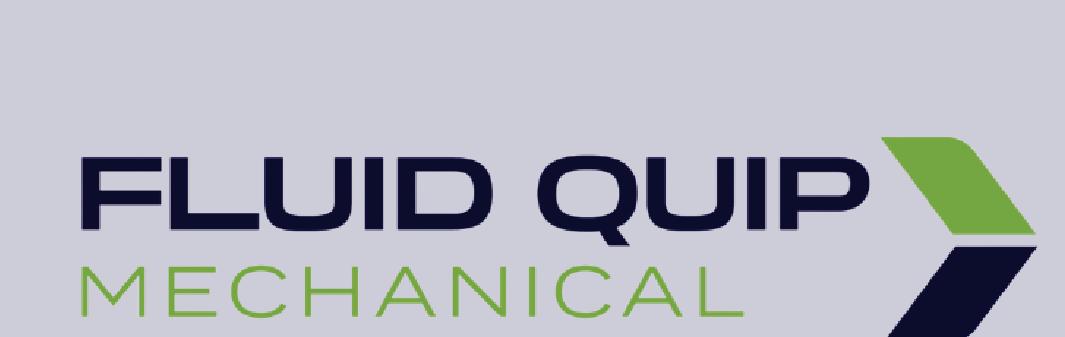
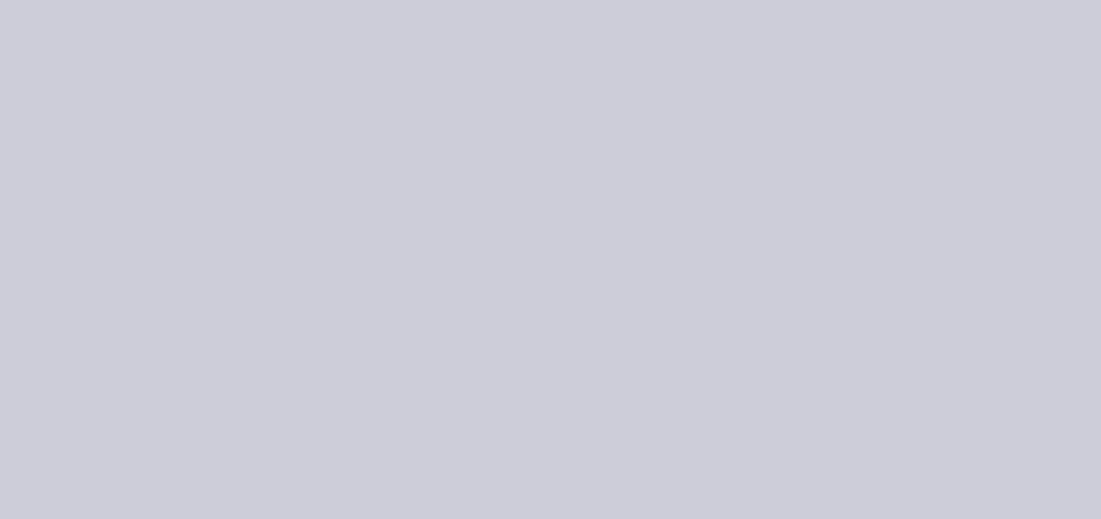



PLANT UPTIME IS IMPORTANT TO YOU, SO IT IS IMPORTANT TO US. Our full service team of experts have 20 years of ethanol plant maintenance reliability and uptime history. 24/7 support and ready access to a full inventory and all Fluid Quip equipment parts, ensures that you maintain your plant’s uptime status.


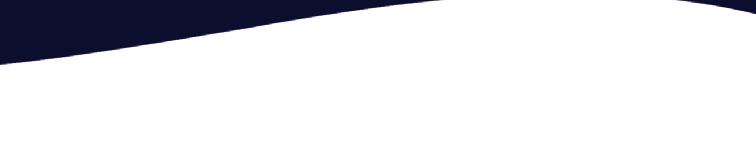

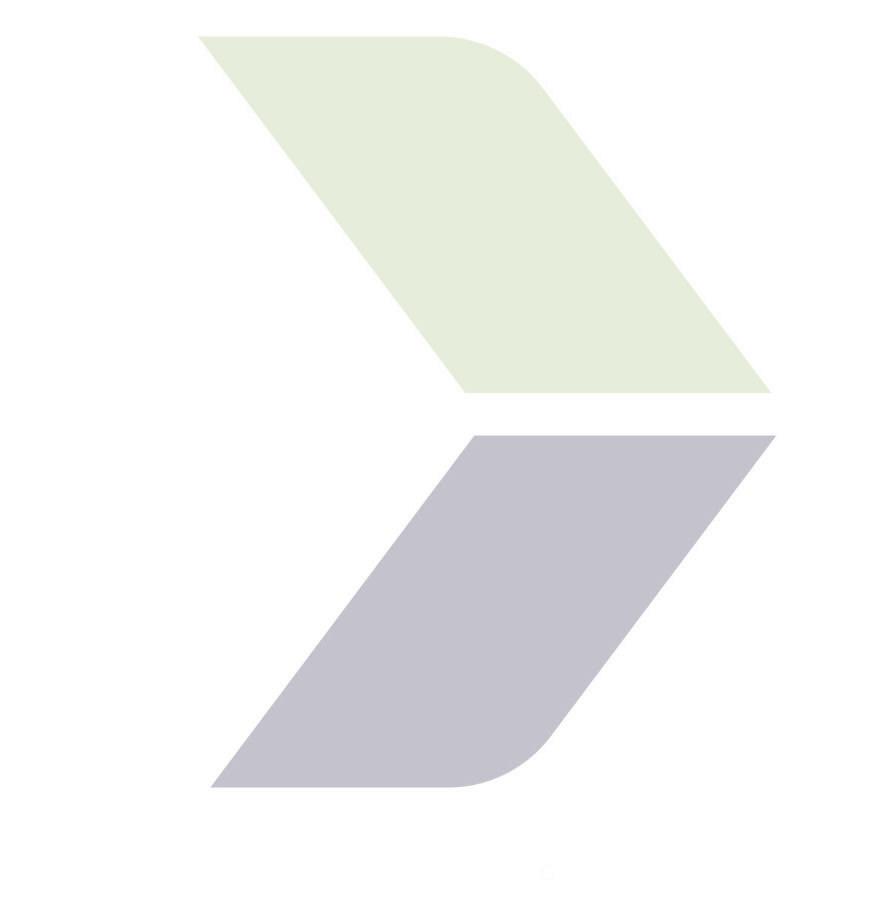

PARTS OEM Parts Warehouse $1 million+ on-hand inventory Fully stocked trucks Overnight/hot shot shipping
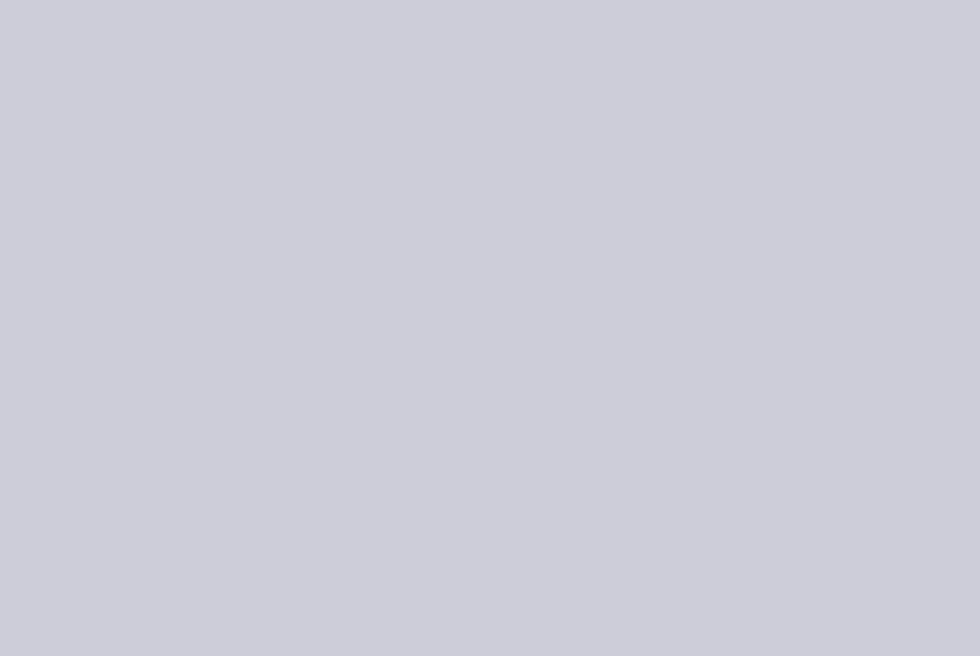
EQUIPMENT
SERVICE • Factory Trained & Certified • MSC™ Systems • SGT™ Grind Systems • FBP™ Fiber By-Pass Systems • MZSA™ Screens • Paddle Screens • Grind Mills • • Centrifuges Centrifuges


FluidQuipMechanical.com | 920-350-5823 | follow us on on Fluid Quip Mechanical is a division of Fluid Quip Technologies i .
Novozymes is working to include hemicellulases with its traditional cellulase products to open up the fiber matrix even more, boosting fiber conversion another 1.5%, Parekh says. The process also bumps corn oil production by up to 20%, he says. “That’s an immediate revenue gain for customers.”
Going forward, new iterations of the Fiberex platform are expected to cross 3.5% cellulosic ethanol. Parekh expects the next iteration to be released in 2021, with another in 2022. “We’ll soon become the new norm in terms of solutions for fiber conversion.
“The idea behind the platform is consistently launch new solutions that keep moving the ball forward in converting the most amount of fiber into ethanol. So Fiberex F1 is just a very small rung of the ladder and we’re quickly going to jump into the novel combinations of cellulases and hemicellulases, which would be the next Fiberex iteration.”

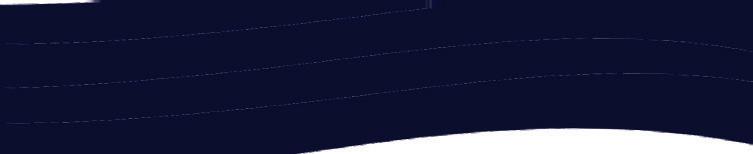
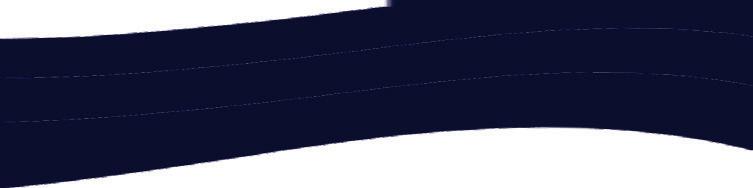
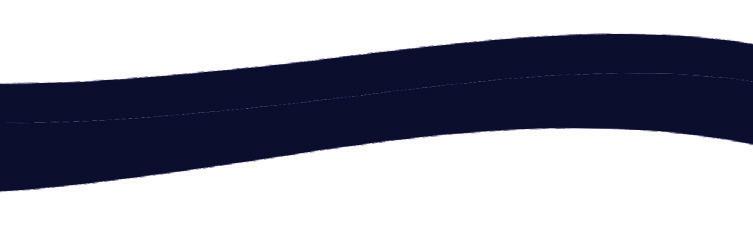
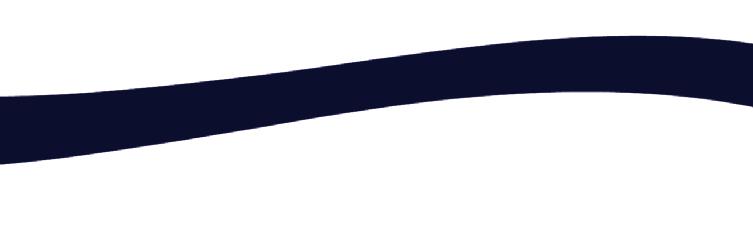
Navigating Certification
A vital piece of fiber solutions is proving cellulosic conversion to regulatory agencies like CARB. Parekh says Novozymes helps producers navigate that process, as well. “We know that the biology is only a piece of the puzzle. So we work really hard and seamlessly with engineering companies … and bring everybody at the table for the customer to make sure the process is as seamless as possible in moving forward with CARB.
“That’s another key part of the platform is our commitment to not only bring the best solutions out there, but to make business easier for our customers.”
Novozymes works closely with
BOLT-ON BOOST: D3MAX is running at nearly 95% of design yield at Ace Ethanol. Novozymes’ new Fiberex R1 will help the plant achieve a D3 lift of 6.5%. PHOTO: D3MAX LLC
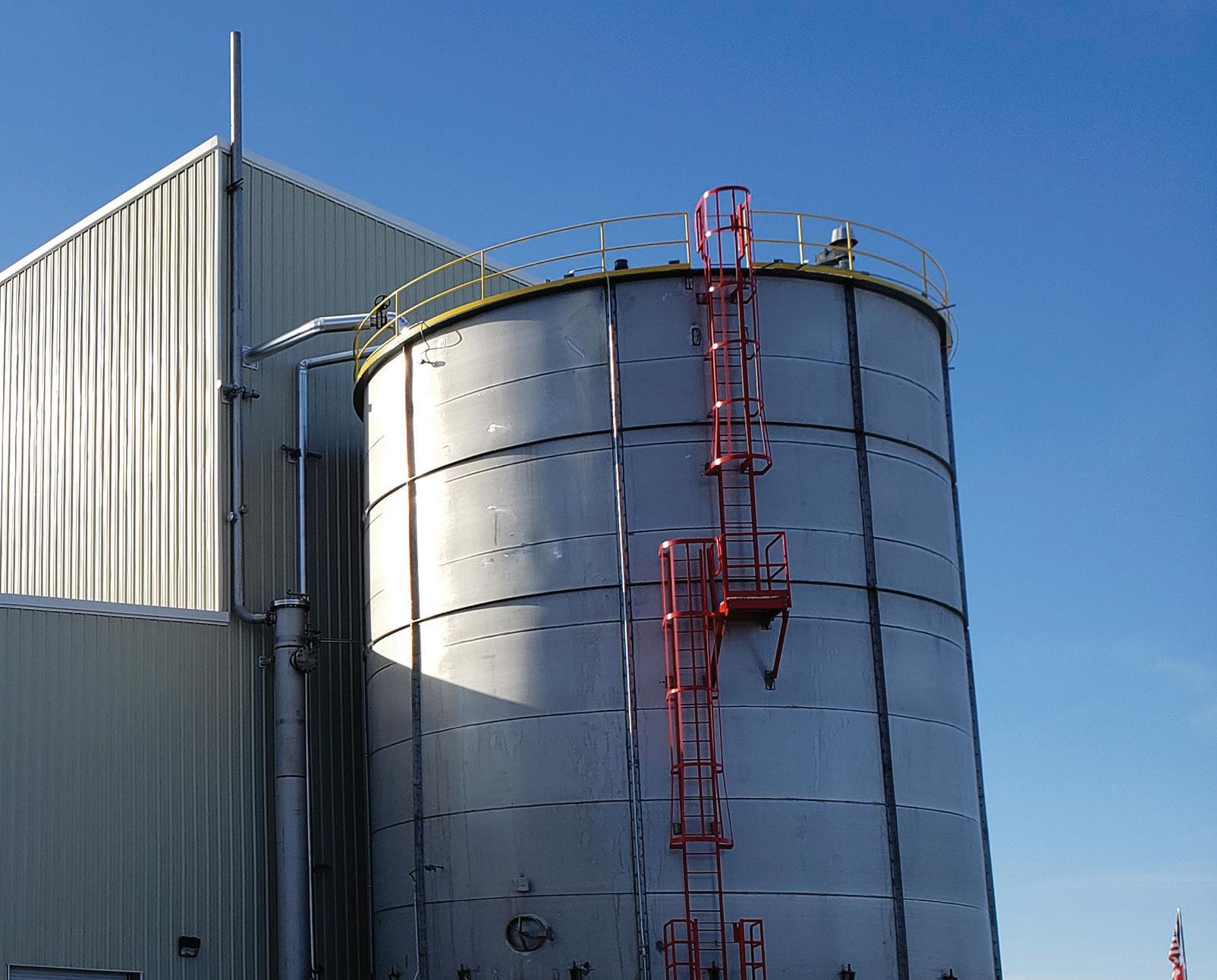
CARB, the U.S. EPA and others to make sure certifications and validations go smoothly. “We make sure there’s clarity and customers can do it easily,” Parekh says.
“Customers come to us and say, ‘this is a great solution but how do we make it work with CARB?’ So we coach them in that process as well.
“It’s really great when years of R&D and the right partnership approach with our customers works in favor of them and helps them diversify more and be more sustainable in terms of business.”
Parekh emphasizes the sustainability of fiber conversions. “One of the things I’m grateful for is the work of CARB, who have provided a great environment for fiber-based ethanol driving diversification in business and for our planet’s sustainability.
“We’re really thankful for California and Oregon’s carbon programs. Going forward hopefully it’ll happen in Washington, New York, Minnesota and other places as well. We’re thankful to these states and these regulatory bodies for creating an environment where we can create these new solutions and innovations.”
Ethanol producers are pioneers in sustainability and biotechnology, Brazeau says.
“The ethanol industry is an example of what biotechnology and agriculture can create. And we think about that very holistically—what are new biological tools that we can bring out to our ethanol-producing customers to help them continue to be pioneers in this space?”
Author: Lisa Gibson Editor, Ethanol Producer Magazine 701.738.4920 lgibson@bbiinternational.com
XCELIS® Yeasts SYNERXIA® RUBY
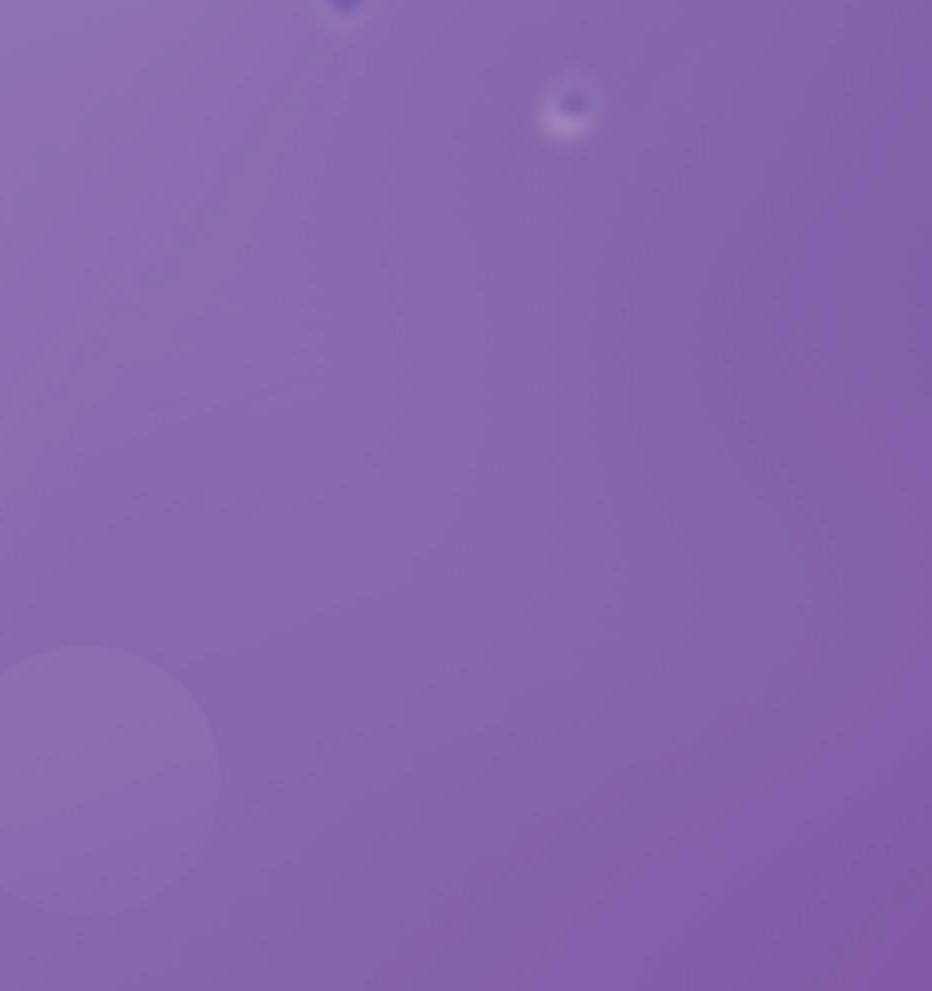
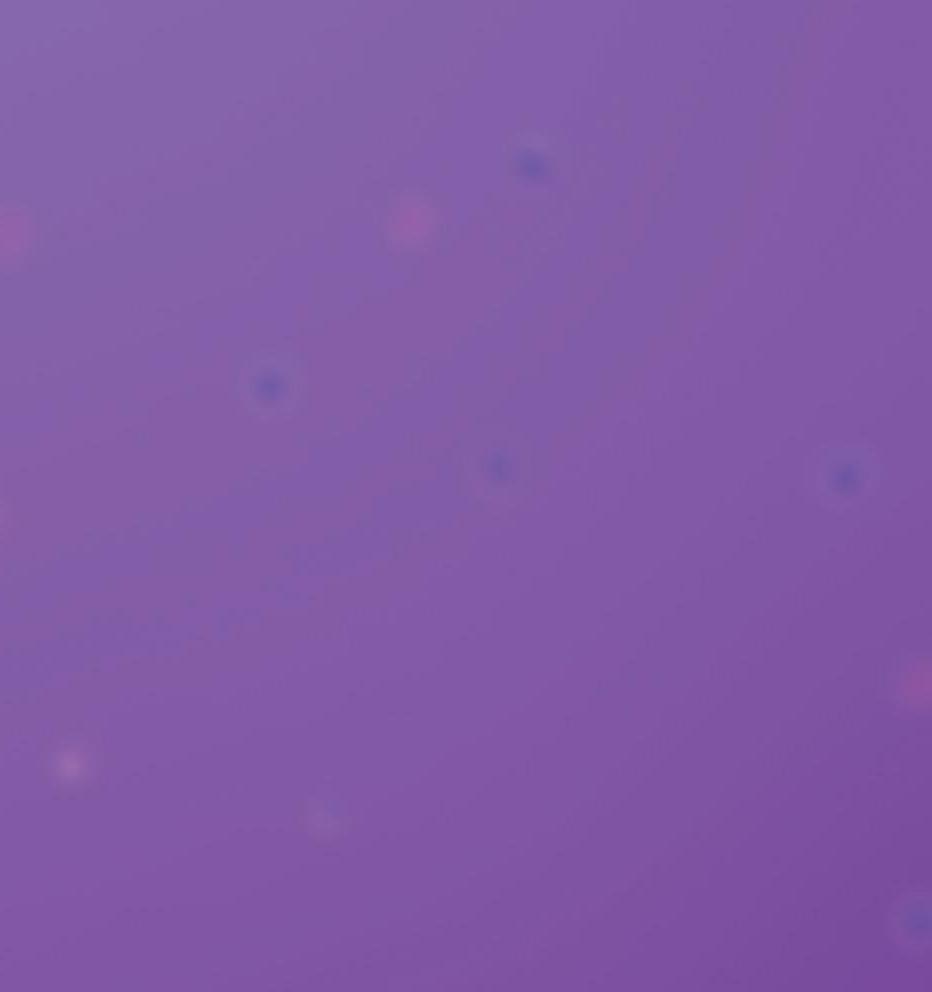
The new standard in high yield yeast driving plants to the peak of performance.
www.xcelis.com
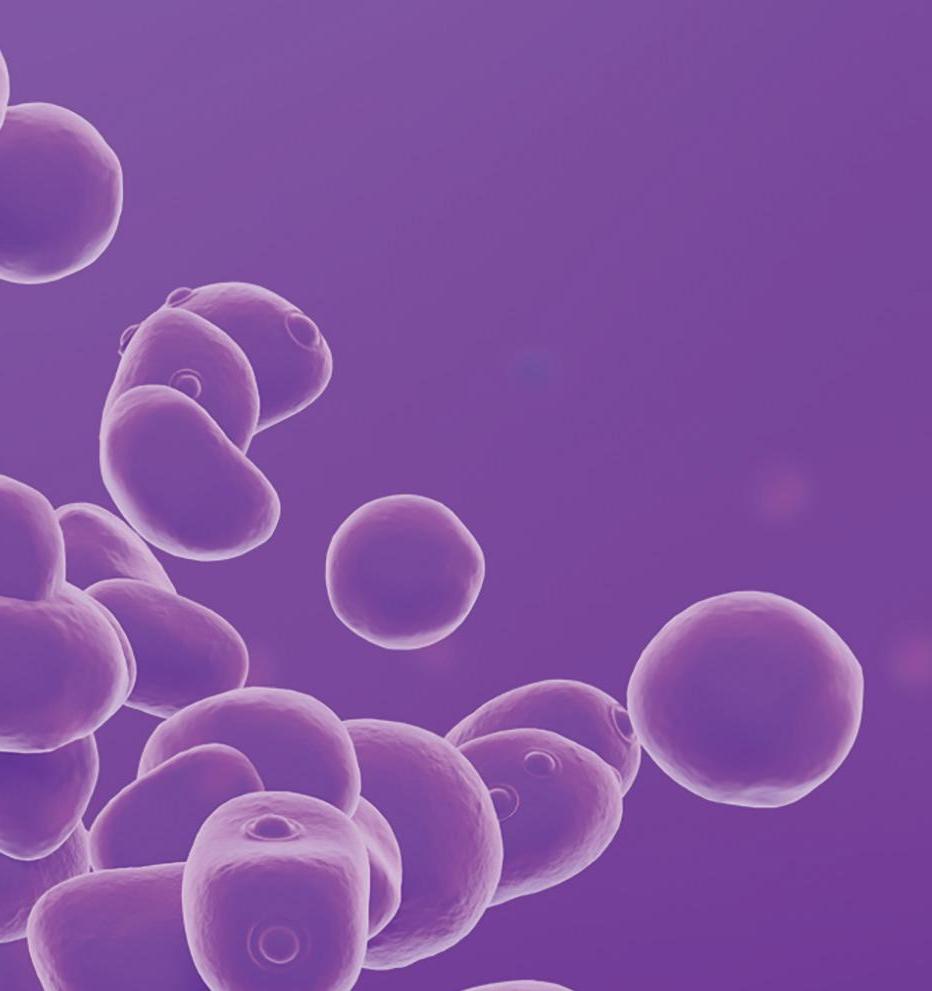
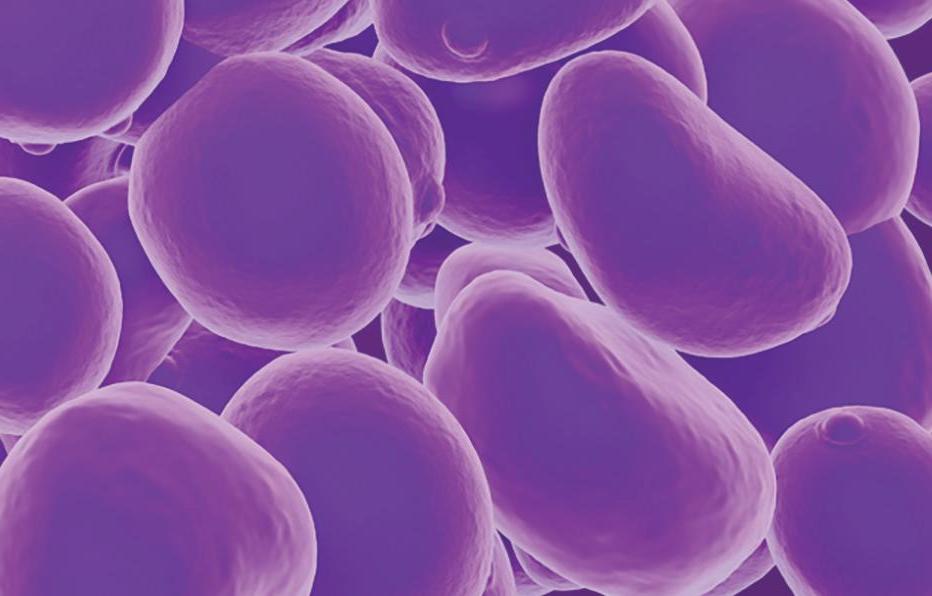

The NEXT STEP
Lallemand Biofuels &
Distilled Spirits’ new
Convergence platform merges its expertise in yield enhancement and enzyme expression. Other innovators have similar goals. By Lisa Gibson
Lallemand Biofuels & Distilled Spirits has released what company President Angus Ballard says is an enormous “step change” in the ethanol production process, on par with the emergence of genetically modified yeast.
LBDS’ Convergence platform marries its work in yield-enhancing yeast with glucoamylase production to provide optimal performance. TransFerm CV5 and Alcolase 146 work together to greatly reduce exogenous GA requirements, as well as enhance yield.
To date, yeast innovation has moved forward with “a little more yield, a little more robustness, a little more GA expression,” Ballard says. “Until now.”
“We have a technology now that the yeast can express levels of GA that literally were thought impossible. It’s literally a step change in the amount of exogenous GA required. Instead of needing truckloads of GA, it’s a small amount, it’s a tote of 1,000 liters that will last several weeks.
“That’s the exciting change.” Complementary Combination
Convergence is a combination of an external enzyme package, Alcolase 146, that complements the TransFerm CV5 yeast, with its yieldenhancing features and enzyme expression, says Matt Richards, director of application technology for LBDS. It’s the first time LBDS has been able to demonstrate such a significant level of yeast-produced enzyme in the ethanol production process, he adds.
“We’ve seen roughly 70% to complete displacement of the added enzyme in fermentation being provided by the yeast in the process,” Richards says.
“The exciting part is the displacement of the GA,” he adds. “The yeast produces both the GA and trehalase, so when coupled with Alcolase 146, we get the best performance. But in some cases, we have demonstrated complete replacement of a GA package with the yeast-made enzymes.”
Before Convergence, conventional dry yeasts from LBDS with a complete exogenous enzyme package were able to replace 25% to 45% of enzyme needs. “This is obviously a significant increase to that,” Richards says.


CLOSEUP: LBDS’s TransFerm CV5 doubles the enzyme expression of previous TransFerm products. PHOTO: LALLEMAND BIOFUELS & DISTILLED SPIRITS

BRINGING FERMENTATION FORWARD: Lallemand Biofuels & Distilled Spirits recently released Convergence, a combination of an enzyme-producing yeast and enzyme cocktail to improve yield and reduce the amount of exogenous enzyme needed in fermentation. PHOTO: STOCK PHOTO
GA works to break down the solubilized longer chain soluble starches, dextrins, into glucose for the yeast to ferment directly. “GA is really what needs to work to make sugars available to yeast for fermentation,” Richards says.
Trehalase splits the trehalose made by the yeast in fermentation. Without splitting, trehalose tends to build up and recycle in fermentation.
“Yeast can displace more of the overall cocktail by expressing more of the trehalase and glucoamylase, the two most important enzymes for the yeast to perform,” Richards says. hasn’t gotten much attention, as very high kinetics.
“There is this very small segment of the industry that is less interested in yield, but is very interested in output, very interested in fast kinetics and very interested in robustness because of their particular circumstance.” For those customers, Bio-Ferm EGA, coupled with Alcolase 146, still provides extraordinary levels of GA expression.
“We encourage customers to increase profitability with CV5, but some are interested in Bio-Ferm EGA,” Ballard says. “We have a couple plants running product and it’s
The Convergence platform includes another yeast that it’s not the primary offering, Ballard says. Bio-Ferm EGA is extremely robust, but is not a yieldenhancing strain. “It’s a very fast strain,” he says. “It’s a strain with proving to be very interesting as well.” Trehalase Train
Cargill also is focusing on trehalase expression, with its biocatalyst, an advanced Saccharomyces cerevisiae, according to Greg Poynter, principal biotechnologist for Cargill. The combination of its three main traits—glycerol reduction, GA and trehalase expression—allows producers to reduce enzyme costs while increasing yield through the reduction of byproducts, Poynter says.
“The third trait, a secreted trehalase enzyme, is what I feel differentiates our strain from the competitors,” Poynter says. “Through an extensive screening process, we identified several viable trehalase enzyme candidates and then engineered them into the yeast.”
The trehalase hydrolyzes trehalose, he explains. “Our solution results in a significant reduction in the overall DP2 sugars at the end of fermentation and a corresponding increase in ethanol titers.
“Cargill’s yeast would bring another competitive offering into the market with the added benefit of a secreted trehalase enzyme. The trehalase offers the same performance as commercial enzyme cocktails containing the trehalase, but with the advantage of having the yeast supplying the enzyme.” Cargill’s yeast has demonstrated between 2% to 4% yield
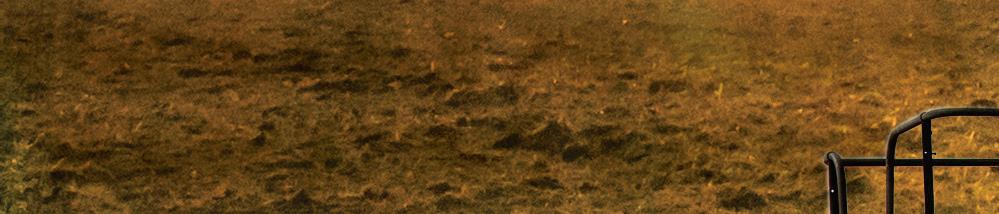
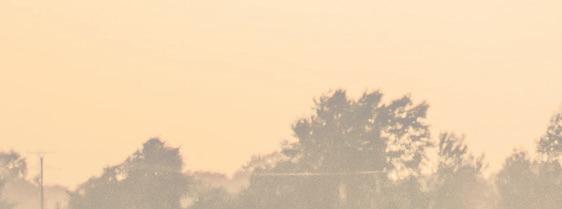
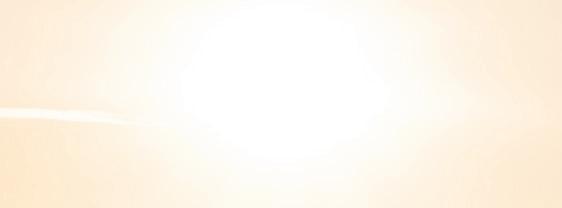
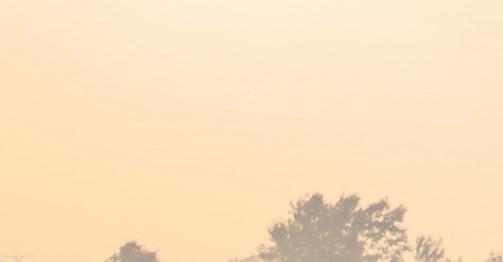
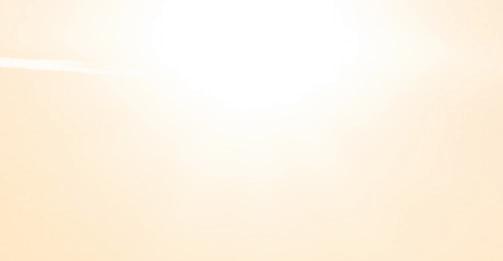

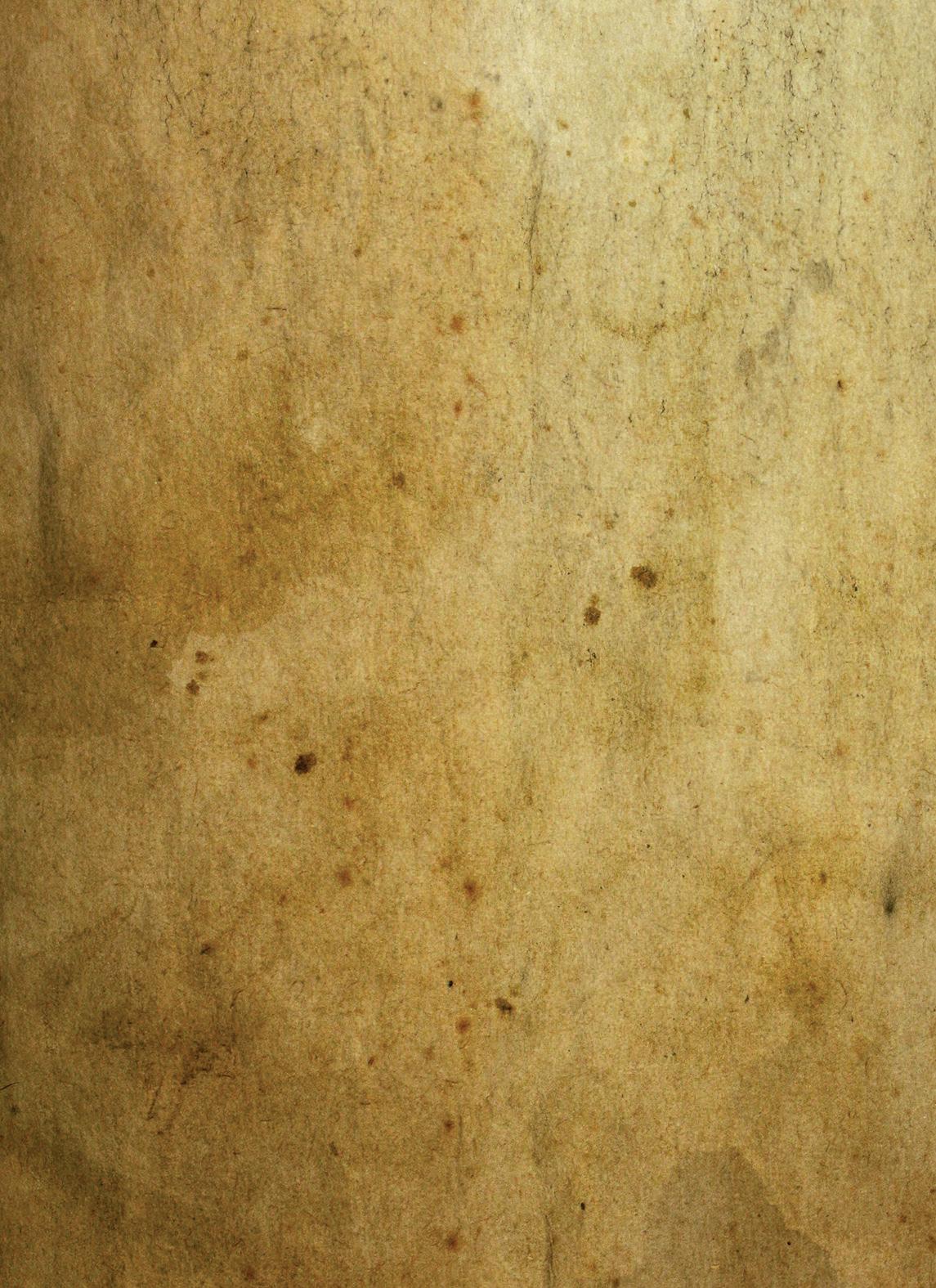
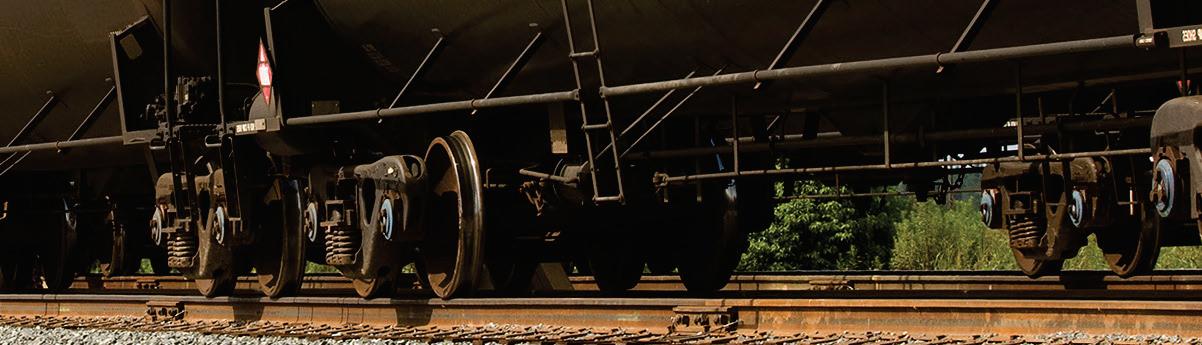
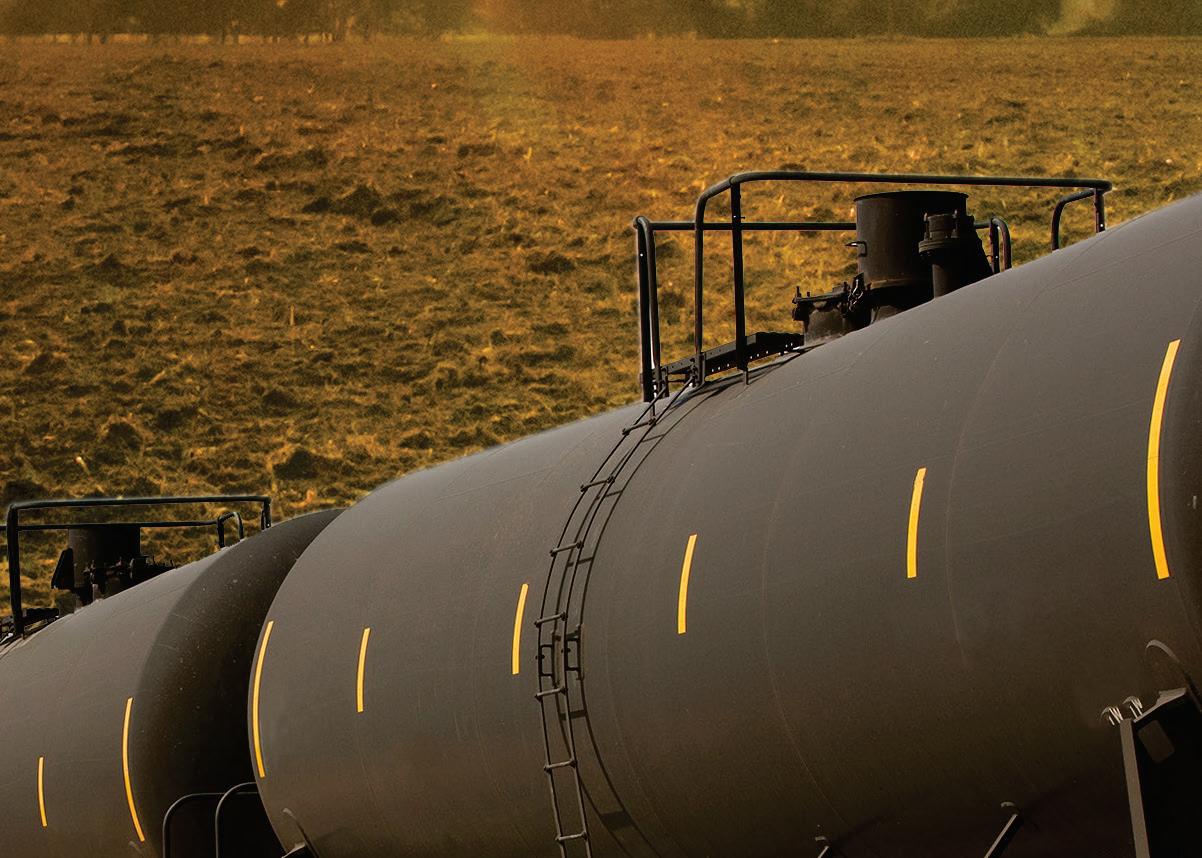

increase, depending on the mash and fermentation conditions. Cargill has been using its yeast developed in-house at its North American ethanol plants but is exploring options to release the technology to the broader ethanol industry, Poynter says.
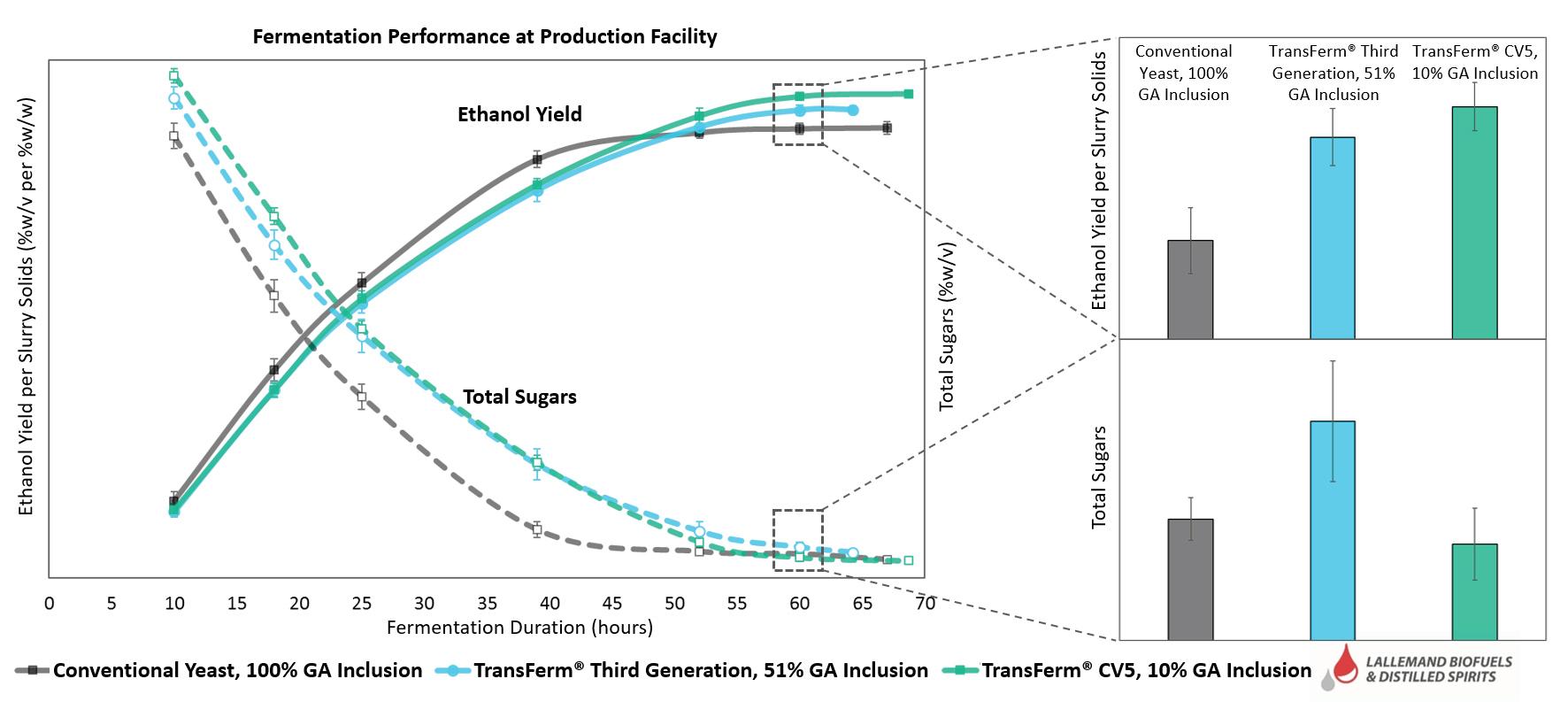
Glycerol Goals
Mickel Jansen, senior scientist in fermentation for DSM Advanced Yeast & Enzymes, says ethanol producers will always want yield enhancement and robustness of yeast. Looking forward, he says new strains will continue to innovate in those areas, but it’s crucial to pay attention to what the altered yeast do to the process.
“Biology has quite some astonishing powers and possibilities for opportunities,” he says. “That’s what we are exploring here, to the benefit of the customer, of course.”
The first wave of advanced yeast was related to glycerol reduction, the second was related to GA, and last was robustness, he says. Ballard says, looking back, those iterations seem almost rudimentary, considering how far development has come.
“Glycerol is still being produced and, for me, that’s kind of the ultimate (opportunity),” Jansen says. “It’s not zero. Can we get there?”
Glycerol is needed in the process for robustness, he says, but there’s more potential in getting more sugars for yeast to be converted. “I can see already some trends there. I expect that would happen more. I would not be surprised if it goes in that direction more.”
Cargill is on top of it. “Glycerol and trehalose represent the major byproducts in an ethanol fermentation, so those were the top targets for the strain development program,” Poynter says.
But, Jansen points out that, in an anaerobic environment, like fermentation, both yeast biomass and electrons are being produced. “The yeast can only compensate if it also makes glycerol,” he explains. “In that sense, it’s kind of a yield loss. The ones that offer a lower glycerol technology do have a certain metabolic pathway introducing the yeast that can partly circumvent that. … Making less glycerol makes higher yields.”
Poynter addresses that. “One of the challenges with glycerol reduction is that many of the solutions, while effective in reducing glycerol, negatively impact ethanol productivity. The modifications we have made to our strain brings the best of both worlds, reduction in glycerol without impacting productivity.”
Jansen adds that process control is crucial in partnership with an optimal yeast. “You cannot fully control your fermentation temp in the process. If you really want to squeeze out the best potential of every yeast, then also the best process control is needed.”
Process control and yeast control go hand-in-hand, he says. “You really have to also think about process control, not only what the yeast can control.”
Compelling Economics
Despite the tough couple of years producers have had, the timing is good for a new product, Ballard assures.
“In this case, the economics are so compelling it’s helped in our favor. And it’s a product that works very well without a lot of onsite tweaks.”
Richards agrees. “The robustness has really decreased the support requirement from the technical support service managers and the team has also really adapted to provide remote
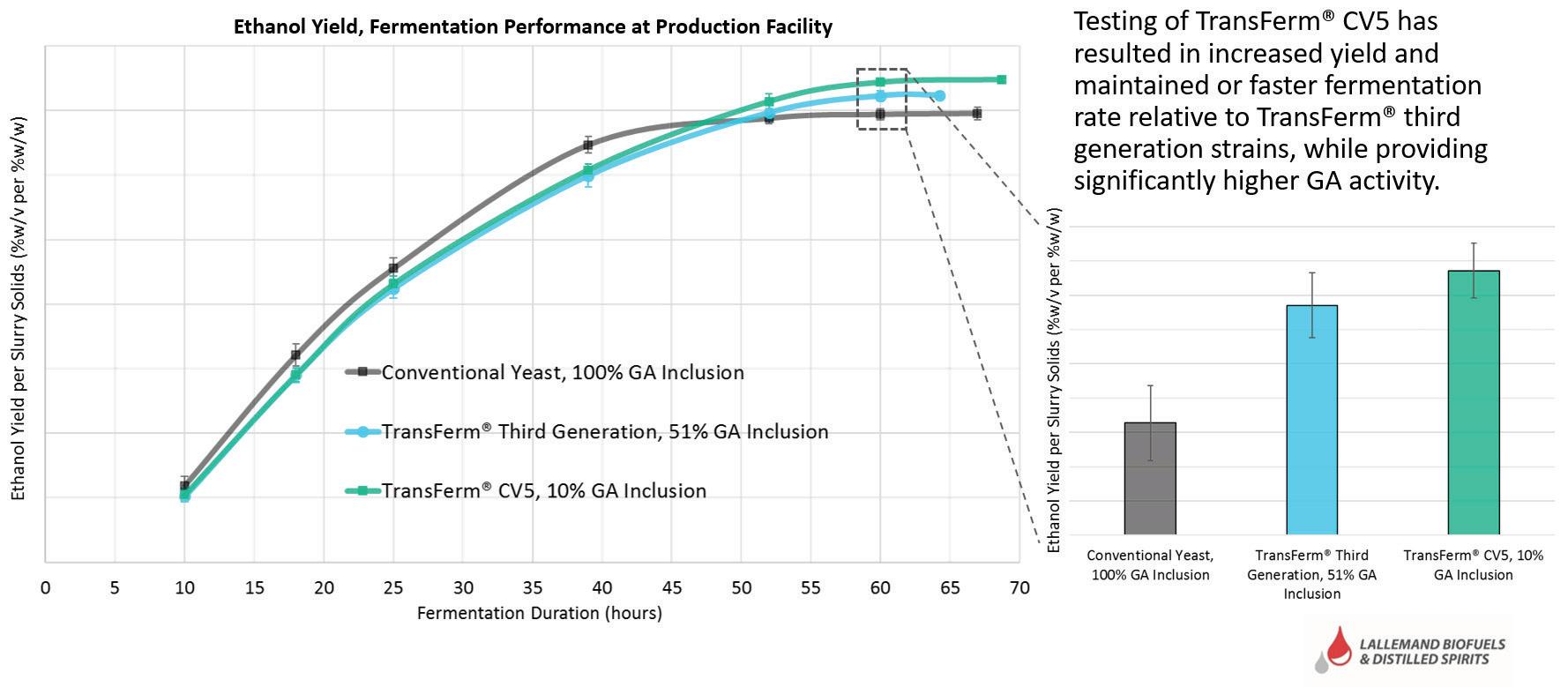
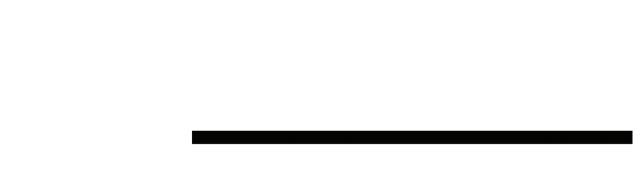
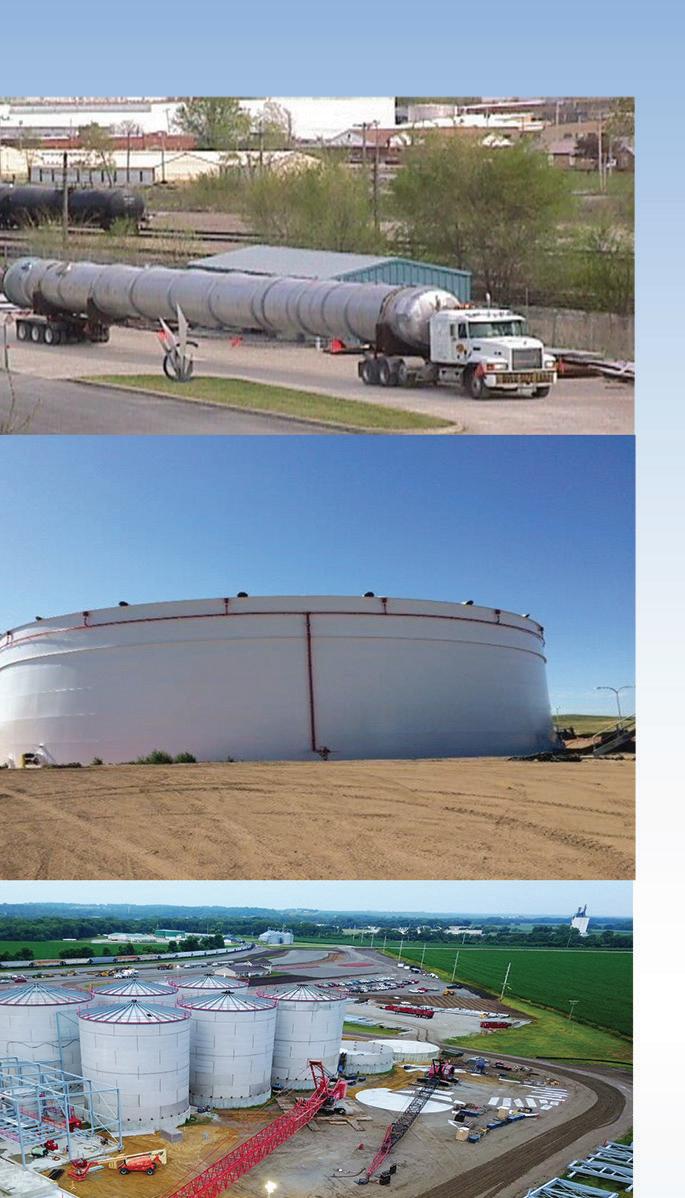
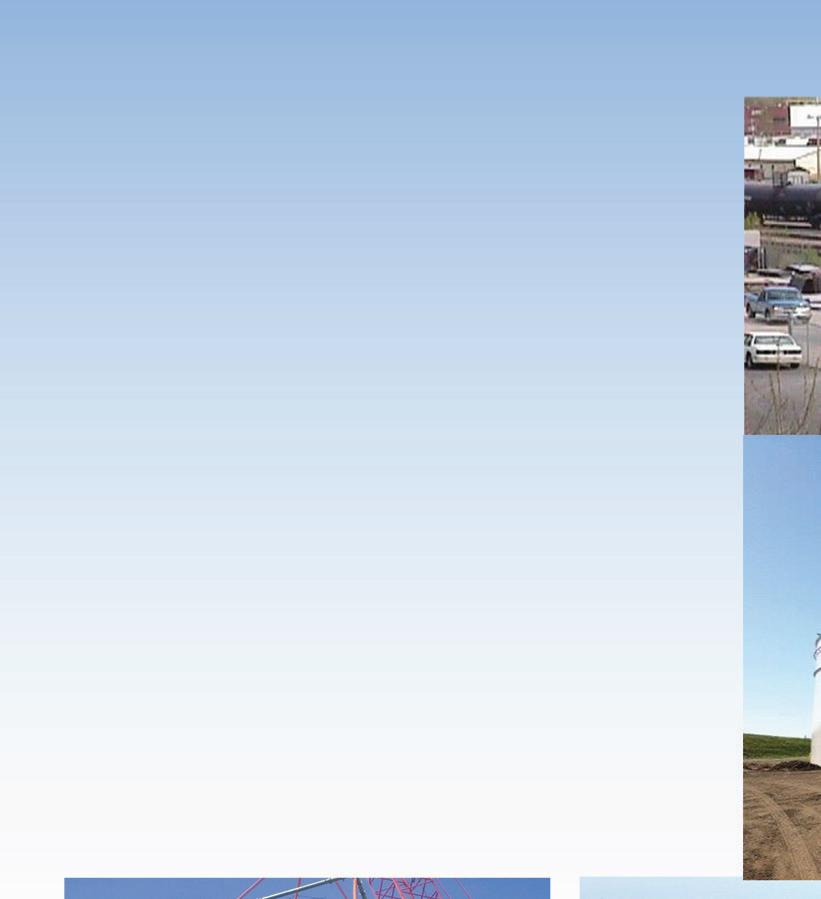

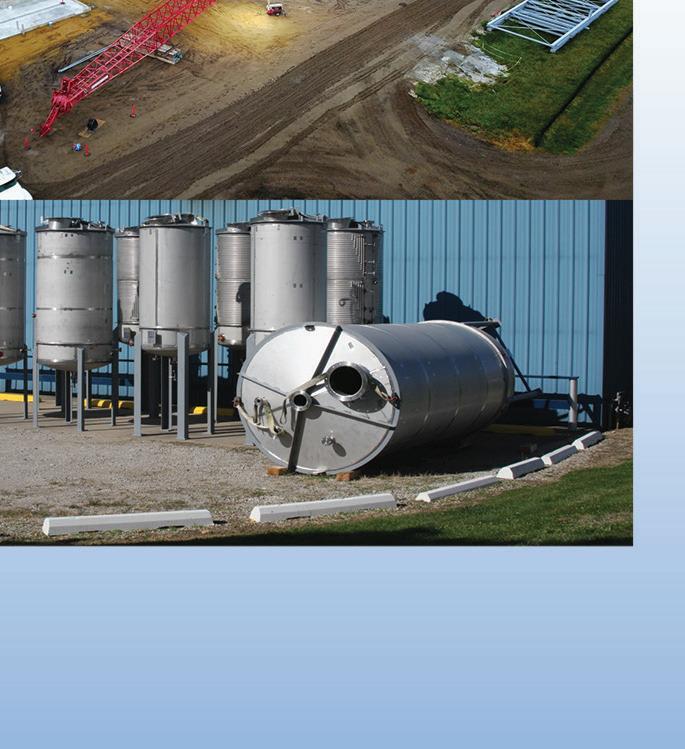


support, and on-site support where customers allow it.
“But with improved robustness and overall strong performance of this strain coupled with our existing knowledge in rolling out products, it’s been pretty smooth,” Richards says.
“What we’ve all learned during this pandemic is what can be done without being on-site, without being face to face,” Ballard says. “We’ve pivoted to ensure our team is able to provide the high level of technical support that is valued in the industry, but, very often, that has to be done virtually.”
“While we want to communicate on-site, the remote support has been pretty effective in helping these trials succeed,” Richards says. “It’s been good timing as far as the intro to the industry.”
One doesn’t find out the extent to which business can be done virtually, until forced to do it, Ballard says.
LBDS has plenty of plans for future iterations of its platforms, continuing to enhance yield and improve robustness.
“We’ll continue to work on different types of enzyme activity to help producers, in terms of some of their other goals with coproducts,” Richards says. “The next step is to continue to enhance yield where we can and overall improve fermentation rate and fermentation robustness.”
Ballard says, “I think it’s an exciting world, when you look into the future— what we can do with GM yeast. There are other enzymes we can express, and we still believe we can get more yield out of the process. So we have plenty of options to work on.”
Poynter says biotechnology has expanded by leaps and bounds over the past decade. “By leveraging these everexpanding capabilities, the yeast providers can significantly improve the process economics for ethanol producers by reducing costs and improving profit margins.”
Ballard always expresses appreciation for competition, helping to motivate innovation. “Competition has certainly been very active and there’s a lot of good products out there,” he says. “We’re very happy we’re currently winning the yield race. But the only way we’ll stay ahead is by continuing to innovate, so we’re continuing to do just that.”
Author: Lisa Gibson Ethanol Producer Magazine 701.738.4920 lgibson@bbiinternational.com

When ‘Best-of-Both’ Traits Shine The new glucoamylase-expressing yeasts within DuPont’s SYNERXIA® Gemstone Collection are both high yielding and fundamentally robust.
Both nature and physics rarely allow two desired but incompatible outcomes to occur in unison—like chasing optimal efficiency with maximum output—and, because of it, ethanol production is full of difficult tradeoffs. “Best-of-both” scenarios are infrequent in biological processes; when one goal is met, another is often partially forfeited.

Lee Robinson Application Scientist DuPont PHOTO: DUPONT
Until recently, high-yield, glucoamylase (GA)-expressing yeasts were subject to precisely that type of limitation. Producers in search of the highest yielding yeasts had to sacrifice some degree of robustness. Those seeking the pinnacle of robustness had to give up some degree of yield.
Now, scientists are producing those dual traits, jointly, with more success. DuPont Nutrition & Biosciences, building on years of success with its high-yield, GA-expressing yeasts, is making the previously divergent characteristics of high yield and superior robustness—packaged together—a reality.
“What we’ve seen in this industry is that you’re either going after yield or robustness,” says Lee Robinson, an application scientist at DuPont’s Applied Innovation Center in Cedar Rapids, Iowa. “There wasn’t much of a middle ground. The line between yield and robustness had to be walked with known consequences: engineering yeasts for yield came at the expense of robustness, and vice versa. But our newest line of yeasts from the XCELIS® platform, the SYNERXIA® Gemstone Collection, is changing that by creating a best-in-class combination of both yield and robustness.”
Robinson says DuPont began its latest journey to develop new yeasts with “good base genetics” that allowed its scientists to drive more robustness into the SYNERXIA® Gemstone Collection. “That’s where we really pushed hard,” he says. “We leveraged a set of very diverse genetic yeast backgrounds, and by mating our current high-yield yeast with an exceptionally robust yeast, we produced hybrid yeast strains with incredible genetic diversity.”
The resultant yeasts were then screened for performance under various stress conditions such as temperature and organic acid tolerance—“the type of stresses they would see at an ethanol plant,” Robinson says. “And after applying that stress and seeing what resulted, we were able to pick two winners.”
The selected pair of champion yeasts reside within a “bestof-both-worlds spectrum,” Robinson says, explaining that they are both high yielding and fundamentally robust. “We made sure we weren’t sacrificing either quality.”
The new yeasts within DuPont’s SYNERXIA® Gemstone Collection—SYNERXIA® RUBY and SYNERXIA® SAPPHIRE— are both available in dry and cream formats. While the two yeasts vary in their makeup and overall attributes, both have enhanced temperature and organic acid tolerance, along with GA-expression that dramatically reduces the need for additional glucoamylase.
When GA-expressing yeast are employed, very little standalone glucoamylase needs to be added to the process during saccharification. In fact, Robinson says, SYNERXIA® RUBY results in a 65% reduction in GA (relative to conventional yeast dosage) and SYNERXIA® SAPPHIRE results in an 80% reduction.
“With SYNERXIA® RUBY, which has DuPont’s patented high-yield, glycerol-reducing PKL pathway, we’ve also applied some additional, targeted genetic modifications that further enhance yield and provide an increase in robustness relative to its predecessor, SYNERXIA® THRIVE GX,” Robinson says. “So, the result is that SYNERXIA® RUBY is our highest-yielding yeast to date from the XCELIS® platform.”
SYNERXIA® SAPPHIRE is intended to fulfill a different but equally important customer need. “Where SYNERXIA® RUBY is for ethanol producers focused on the highest-yielding yeast possible, SYNERXIA® SAPPHIRE is best suited for customers that want significantly more yield than a conventional yeast but also superior robustness,” Robinson explains. “SYNERXIA® SAPPHIRE gives you assurance that you’re going to survive and thrive during the upsets that inevitably occur.”
Unlike SYNERXIA® RUBY, SYNERXIA® SAPPHIRE does not have the patented PKL pathway built into it, but contains many other yield-enhancing modifications. Furthermore, SYNERXIA® SAPPHIRE and SYNERXIA® RUBY do not share the same GA. “The glucoamylase in SYNERXIA® RUBY is similar to its predecessor, but SYNERXIA® SAPPHIRE has a new glucoamylase that has the potential to lower residual starch in fermentation with an enhanced ability to reduce the need for additional GA—and that’s how we get to an 80% reduction.”
Both products have gone through extensive plant trials, despite the unique challenges of doing so during the pandemic. “We have excellent data sets from multiple plants,” Robinson says. “Whenever you trial new yeasts, you’re never quite sure what will emerge, but we saw unique value in each yeast, and enough of a market segment for each product, to bring both of them forward together.”
ROAD TO 45Q: Detailed mandates, including a 2023 construction-start deadline, can sneak up on a carbon capture project and result in disqualification. A thorough understanding of the rules is crucial. PHOTO: CARBONVERT INC.
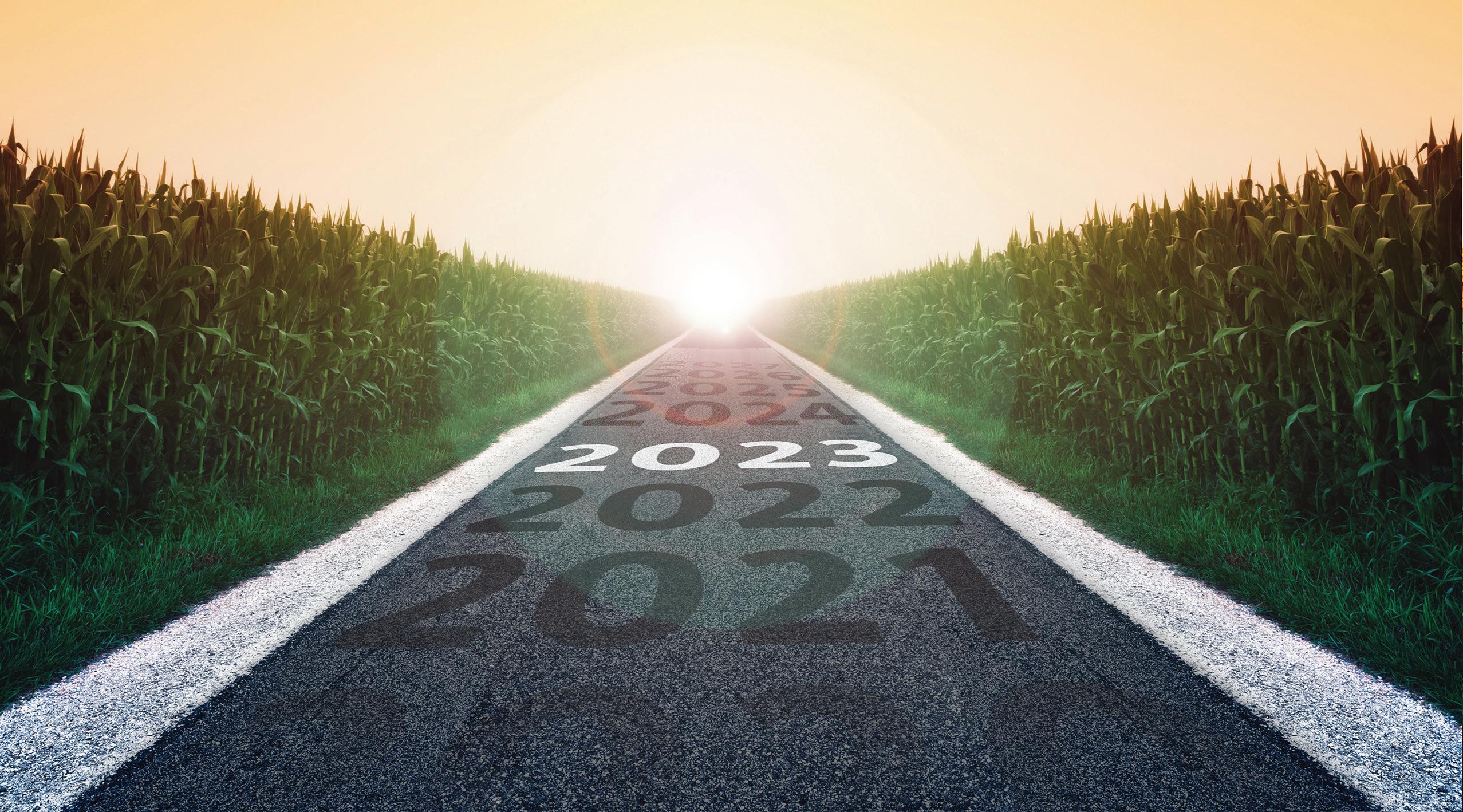
45Q: The Drive to Qualify
The road to qualifying for the 45Q tax credit can be confusing, with strict limitations on project phases and what constitutes start of construction. But, navigated properly, the credit is a promising opportunity. By Alex Tiller
Carbon capture and storage (CCS) presents a tremendous financial opportunity for many ethanol producers. Through CCS, producers can lower their carbon intensity (CI) score to increase profits through the California Low Carbon Fuel Standard market, with the potential for concurrent earnings from both 45Q tax credit transactions and sales in carbon credit markets. CCS also provides access to indirect economic benefits, namely the mitigation of enterprise risk from a future carbon tax and the improvement of commercial relationships with ESG sensitive lenders, investors and customers.
While the economic benefits of CCS can be numerous, producers will need to commit significant time and capital to pre-development. Proper due diligence is necessary to navigate the complexities of IRS Section 45Q tax credit rules. 45Q contains a litany of guide-
lines, timelines and limitations that require expertise and adherence to prevent inadvertent project disqualification.
Among the intricacies of 45Q is the determination of what qualifies as the start of construction. Despite its apparent simplicity, the start of construction is a complex milestone that serves as the primary pacing item for all other pre-development activities. In addition to a start timeline, certain mandates must be met to consider construction officially started.
It’s also essential to understand that there are many other guidelines, both written and unwritten, drawn from previous tax credit programs and guidance. Tax credit program complexity can become a barrier to entry for inexperienced emitters. Retaining specialized legal counsel with experience in closing tax credit investment transactions, also known as tax equity investments, is an efficient way to obtain this support. Additionally, as 45Q guidance develops over the coming months, ethanol producers will be forced to make critical decisions and investments, or risk missing out altogether.
Construction Clock
To qualify for the program, facility construction must begin by Dec. 31, 2023. Legislation proposed in December would extend the date for projects to begin construction to claim the 45Q tax credit for carbon dioxide sequestration by 10 years. It would also provide a direct pay elective for the full value of the tax credit.
With the current 2023 construction start date in mind, many steps need to fall into place before construction can begin.
Preliminary technical phase: The first phase includes, but is not limited to, acquiring internal funding and contracting with third-party providers, as well as conducting
feasibility studies, geologic characterization, and FEED studies for geologic storage. In addition, plan on conducting FEED studies for carbon capture, securing land and subsurface rights with owners, initiating LCFS and carbon registry documentation, construction permitting, and U.S. EPA permitting.
Project finance: About $30 million to $50 million will need to be secured, and the lender will seek certainty that an experienced tax equity investor stands ready to monetize all the tax credits generated from the new facility. Since 45Q is a relatively new incentive, the tax equity investor market is still evolving and is relatively unknown, which makes the financial modeling required to make a go/nogo decision for a project even more difficult.
Once these phases have been completed, a project will need to meet strict start-ofconstruction criteria.
Qualifying for Construction Start
There are two ways to establish that a project has begun construction before Dec. 31, 2023. The first is by incurring at least 5% of the project’s total cost and making continuous efforts to advance toward completion of the project thereafter. It’s a seemingly straightforward approach to meeting the start of construction deadline, but it comes with important caveats: • The total costs need to be calculated based on the project’s depreciable basis, including any tax credit structuring related basis step-up. Since there’s a chance the project cost overruns the budget, it is prudent to target about 7% as a rule of thumb. • The payment approach is only available when using the cash method for accounting, as opposed to the commonly used accrual method. • When purchasing components and equipment to meet the 5% threshold, delivery can be at the project site, the manufacturer’s factory or in transit, but steps should be taken to make it clear that the buyer has truly taken possession of the property. • If the project developer cannot establish that the 5% test is met based on its own costs, the rules permit it to look through the contractor’s costs if there is a binding written contract in place.
Another way to mark the start of construction is by performing what the IRS calls “physical work of a significant nature.” This test focuses on the nature of the work performed as opposed to the cost or amount. It requires a continuous program of construction, but potentially leaves the door open for an unfavorable IRS judgment that construction was not truly underway, as “significant” is not clearly defined. Key points to consider include: • A carbon dioxide emitter does not have to do the work itself if the work is performed under a binding written contract that is entered into before the work starts. • If properly designed and implemented, project developers can take credit for the characterization work that is performed adjacent to construction. • Physical work may not be deemed significant if it includes the manufacturing of components that are either in existing inventory or normally held in a vendor’s inventory. • Consistent with previous renewable energy tax credit guidance, the IRS has indi-
CONSTRUCTION CLOCK: To qualify for the 45Q tax credit, producers must start construction by Dec. 31, 2023. PHOTO: CARBONVERT INC.

cated that certain preliminary activities do not count (such as exploration, research, etc.), even if their cost is properly included in the basis of the property.
Before beginning the construction process, it is crucial to consult with professional and legal resources to determine which strategy best suits the project.
Simplifying A Project
Determining whether a plant is a viable candidate for CCS through feasibility studies could cost millions. That alone could be a barrier to entry for many producers. One viable option is using third-party experts to conduct all the upfront assessments while minimizing cash and cost outlay at the same time.
Given recent economic setbacks from the COVID-19 pandemic and questions surrounding the future of ethanol production, creditworthiness for host emitters poses a challenge for project execution. Project lenders are going to need production covenants to mitigate the risk of project fallout. Considering the shutdown of some ethanol plants in 2019, additional expected shutdowns due to COVID-19, and projected declines in U.S. motor gasoline demand, the risk aversion of lenders could lead to many unbankable deals for host emitters.
Many ethanol producers don’t have the excess cash or team bandwidth for in-house development. The capital-intensive process further hinders the feasibility of undertaking a carbon capture project alone. Fortunately, there are well known commercial approaches to exploiting similar opportunities through third-party project development and finance teams.
For years, the oil and gas, solar and wind industries have partnered with project hosts. These partnerships have provided stakeholders with the technical and financial expertise needed to successfully stand-up new projects and manage the complexities of the finance and tax credit markets.
In these arrangements, a third-party project developer contracts with a project host for the right to develop a project at their facility in exchange for mutually beneficial financial terms. The project developer provides a dedicated team with a vested interest in the project’s success, allowing the project host to focus on their core business. Plants entering into CCS investments will likely be required to enter take-or-pay agreements with lenders, which can limit the ability of plants to react dynamically to market conditions. Through diversification of projects and substantial financial expertise, thirdparty developers can limit this risk for plants.
For large ethanol producers, it might still make sense to build in-house competencies in CCS development. For many others, entering into CCS projects alone will be difficult, considering the financial and technical complexities that coincide. Partnering with experts and sharing in the upside of generated benefits could be the best course of action.
CCS allows host emitters to monetize waste emissions while promoting the development of sustainable infrastructure. Lower CI scores, 45Q and additional state or local incentives create enormous market potential for emitters to profit from decarbonization. With proper execution, CCS provides a promising growth opportunity for emitters.
Author: Alex Tiller President, Carbonvert Inc. 303.517.6608 alex@carbonvert.com
Rich Data, Real Relationships Enzyme provider CTE Global is raising the bar on service with madeto-order testing and contextual plant data analysis from a single lab.
For Pedro Peña, CTE Global Inc.’s Lab and R&D director, delivering the right enzymes to an ethanol producer is a process of discovery that couples plant data analysis with a genuine effort to understand the facility, the people who run it, and their goals. “It starts with those two things: establishing the data and making personal connections at the plant,” Peña tells Ethanol Producer Magazine. “You have to know your customers to understand their challenges, and tage,” Peña says. “It gives us the ability to see precisely where each of our customers stand, and it also enables benchmarking. Being able to do all this work under one canopy also accelerates new product development.”
CTE offers more than 20 different enzymes, both stand-alone and blended products, including half a dozen alpha-amylases tailored for liquefaction, a suite of glucoamylase blends for fermentation and saccharification, yeast and numerous specialty enzymes. CTE also provides food-grade enzymes for producers making alcohols for sanitizers or other consumer products. Knowing which products are best suited for each producer, Peña says, comes down to understand-

Pedro Peña, Ph.D. Lab and R&D Director CTE Global Inc. PHOTO: CTE GLOBAL INC.
ing the plant. “When you fold all the work in—the data, testing in the
lab, tech support in the field, understanding the customer’s goals— the answer is usually pretty evident,” he says. CTE recently expanded its suite of alpha-amylases to include two new products with thermostable characteristics. Peña explains that high heat boosts the solubility of starch, along with the viscosityhow their plant is running. The data is vital, obviously, but leverag- ment. ing those relationships—knowing exactly what your customers want “That’s what we’re shooting for with these new alphas,” he says. to achieve, and why—is the context that leads to real optimization.” “The industry is moving toward higher and higher starch conversion,
CTE’s dedication to customer service is the driving force be- and if you can run your liquefaction at higher temperatures, you’re hind its Data-Driven Strategies platform, aimed solubilizing the starch at significantly higher levat extracting maximum value from the production data it harvests for clients through laboratory testing and plant trials. “When we do a 'We’re helping our customers go after els than you would at lower temperatures. And anytime you can do that, you are increasing your opportunity to improve yield.” trial, whether it’s working with a customer for that undigested CTE’s AMYL-XT is a stand-alone enthe first time or the tenth, we perform an all-out starch, and also corn zyme with high heat tolerance, while the newer analysis of how the plant is running,” Peña says. The production data CTE generates for its customers is analyzed and parsed out in ways that are particularly useful to decision makers at fiber, so little or nothing is left behind. It’s about squeezing AMYL-XTP+, also a thermostable product, includes a beneficial protease. “With XTP+, we can break up that protein-lipid complex and free up oil, giving your corn oil coproduct yield the plant. “Most of our clients still use third- out as much value as a boost,” Peña says, explaining that a higherparty labs for testing, and those labs play an im- possible.' quality nitrogen environment for yeast growth portant role,” Peña says. “But we’re providing also results. “Happy yeast withstand stresses new value to producers by taking commonly and grow and populate better, so that, too, crerun tests, like starch, and separating the data out in ways that provide ates the potential for better yield.” actionable insight—like defining enzymatically-available starch from Recently, CTE launched a new line of blended specialty enresistant starch, or showing how much nitrogen a producer has from zymes, including cellulases and fungal alpha amylases, trademarked ammonia, urea or amino acids—information that sheds new light on by CTE as Complete™, designed to help ethanol producers finish optimizing their process.” challenging conversions. “We’re helping our customers go after that
One of CTE’s key assets is its ability to accommodate this work undigested starch, and also corn fiber, so little or nothing is left within a single lab. “Having our entire customer base, the testing and behind,” Peña says. “It’s about squeezing out as much value as posdata for all the plants we serve, under one roof, where we know the sible. With our Complete™ line of products, producers can now go methods are consistent day to day, month to month, is a huge advan- after that last bit of potential.” break of liquefaction, giving way to the potential for yield improve-