
10 minute read
PROCESS
POURING ON IMPROVEMENT
New and improved yeasts—more robust, flexible and effective than ever—are helping ethanol producers optimize today while adapting for tomorrow. By Matt Thompson
IMPROVEMENT
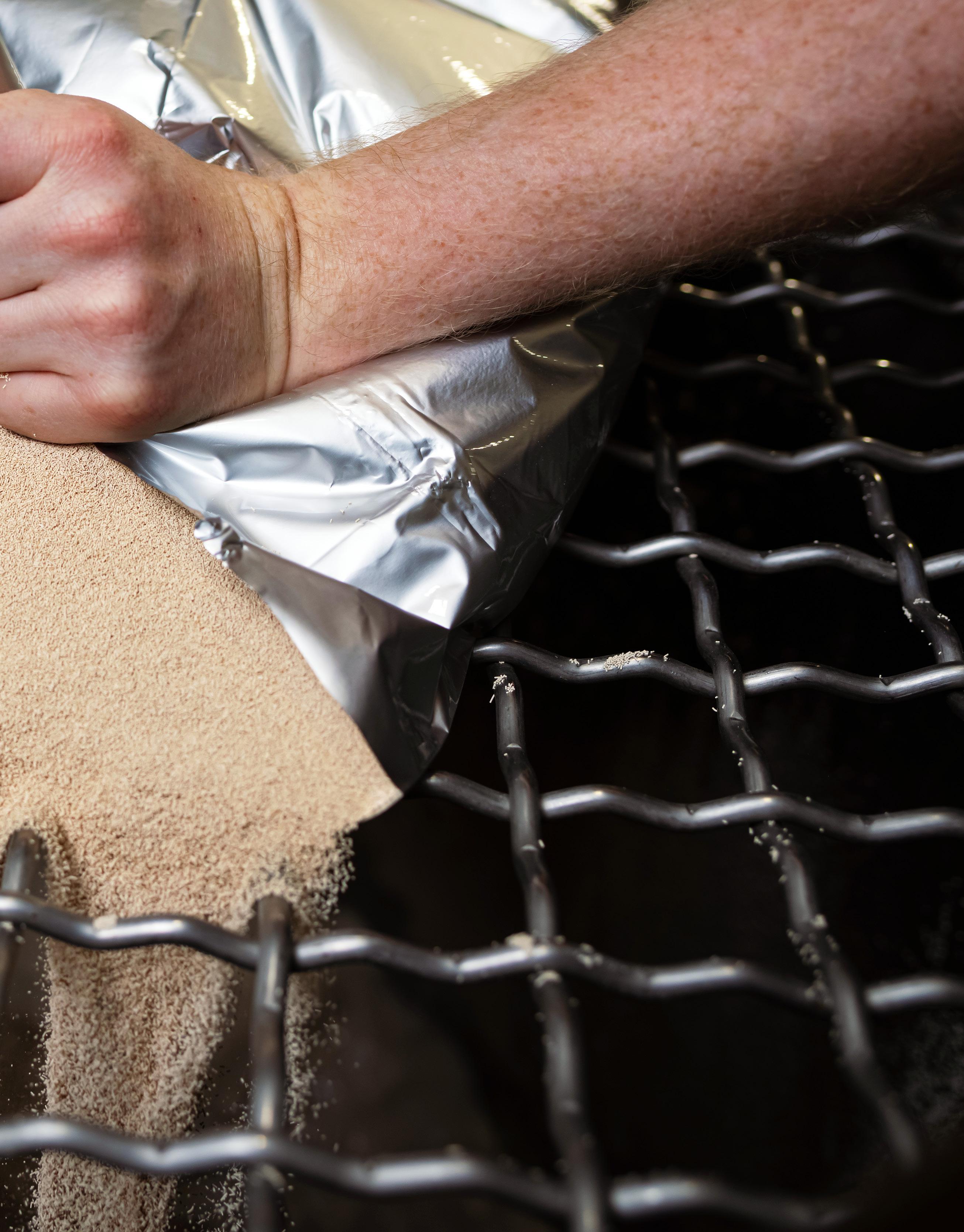
GRATE OPPORTUNITIES: Dry yeast is hand poured into a mix tank. Yeast developers like Novozymes say their research and product development is focused on creating value, optimizing yield and, ultimately, maximizing plant returns.
PHOTO: NOVOZYMES
Hans Foerster of IFF likens running an ethanol plant to managing an ecosystem. “There's
the influence of the larger environment, whether that's from your environmental regulators who say that you have certain constraints on your wastewater, or the financial constraints that the marketplace imposes,” he says. “There’s a lot that goes into running an ecosystem.”
And in the biological system of an ethanol plant, yeast is just one factor—albeit an important one—of process optimization. “I think if you look at top-tier producers, no matter what product they use, [yeast] is only one contribution to why they achieve the highest operational or financial performance,” Foerster says. “It has a lot more to do with the plant team and the systems and processes in place there. An advanced yeast can be part of that. But it’s a part. It certainly isn’t a substitute for those other elements.”
Matt Richards, director of application technology at Lallemand, says one of the roles yeast and enzymes play is to help reduce costs. “It's about creating value for the facility, both in terms of the primary product of ethanol, and now in terms of the coproducts as well, trying to ensure that the oil yields are [on target] and the protein is higher with less inert materials like cholesterol. It’s about reducing cost for the producers by allowing them to produce their exogenous or added enzyme doses,” he says.
For Robert Osborne, R&D manager for yeast application research at Novozymes, successful yeast innovation is about maximizing plant returns. “Our goal is to help our customers get the absolute maximum value out of their facility possible,” he says. “Our yeast strains are less reliant on urea. That's a differentiating characteristic of our product portfolio, resulting in a simpler process and one less expense for our customers.”
For Phibro, innovations in yeast are valuable in helping plant managers optimize for yield, throughput and many additional factors. “We’re now engaged in innovation in the yeast space. Our focus is on GA [glucoamylase] replacement with consistency and robustness,” says Stephanie Gleason, senior manager of technical services for Phibro Ethanol.
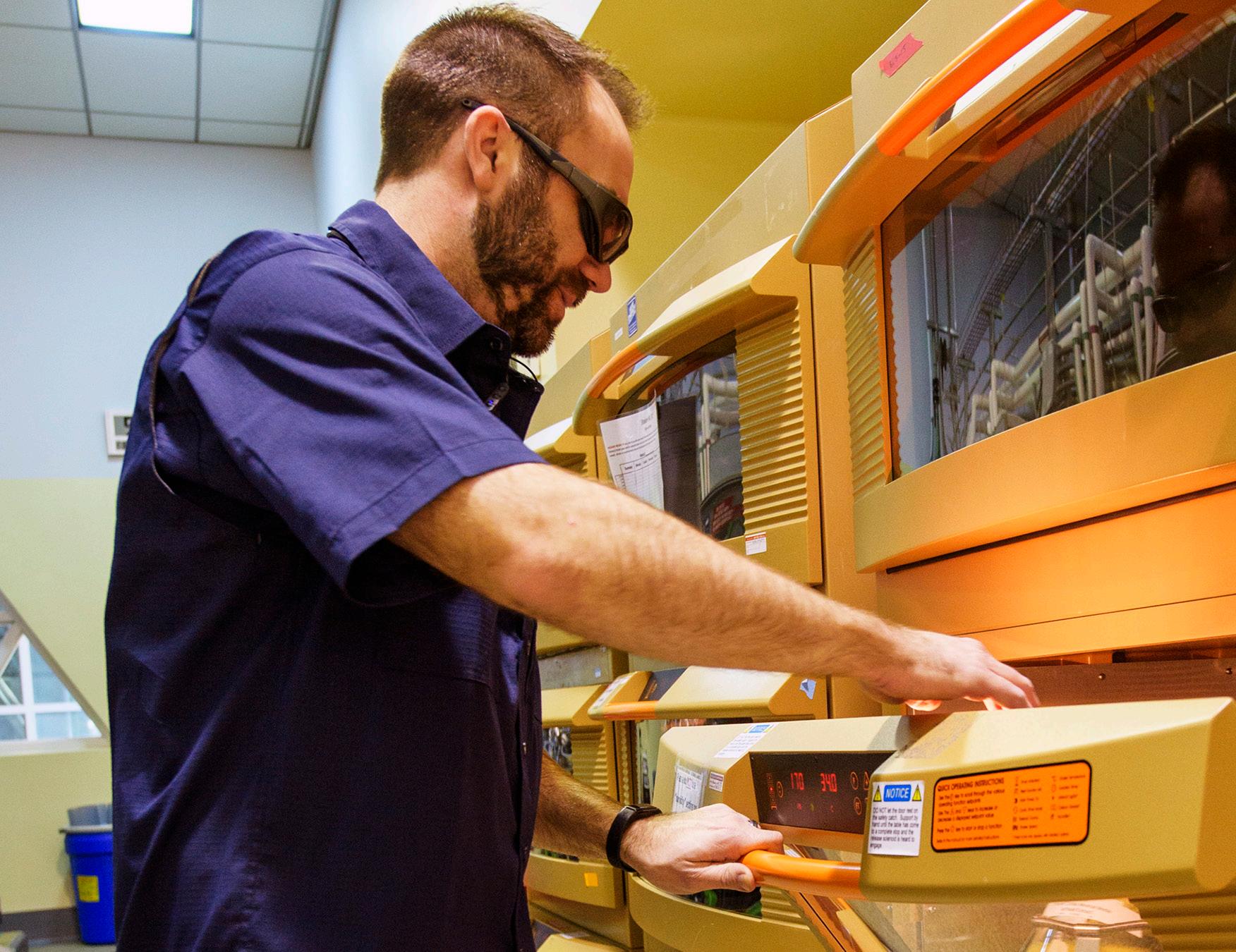
LAB FERM: Yeast fermentations are done in shaking incubators with the ability to program temperature profiles to optimize yeast performance and mimic the temperature profile observed in a customer’s plant.
PHOTO: IFF
Fit and Flexibility
All four companies say yeast has advanced quickly in recent years, and they have each contributed in different ways to those advancements.
Kevin Cox, director of bioenergy applied research at Novozymes, says there are three themes that describe the company’s recent yeast innovations: yield performance, robustness and enzyme expression.
“Recent advances in technology enable ethanol producers to maintain corn grind and gain higher ethanol titers, or decrease corn grind and get roughly the same ethanol output. This gives plant managers flexibility in their approach to ethanol production,” he says. “Right now, ethanol margins are quite good, so producers are able to make strong profits. From the perspective of yeast performance, Novozymes has put a big emphasis on robustness in our breeding and engineering programs to ensure our yeast products are able to maintain high ethanol yields and strong performance even when fermentations are challenged with heat stress or bacterial infections.
Lallemand has been working on faster fermentation, yeast expression and keeping an eye on high-protein coproducts. “For grain ethanol, it’s primarily trying to improve on the existing products that we have in terms of fermentation rate, the enzyme production capabilities of the yeast as well as continuing to try push ethanol yield and reduce glycerol to allow for higher protein coproducts,” Richards says.
Gleason says Phibro’s innovations in the yeast space give plant managers flexibility in how they run their plants. The company’s latest strain in its Kinetx yeast line
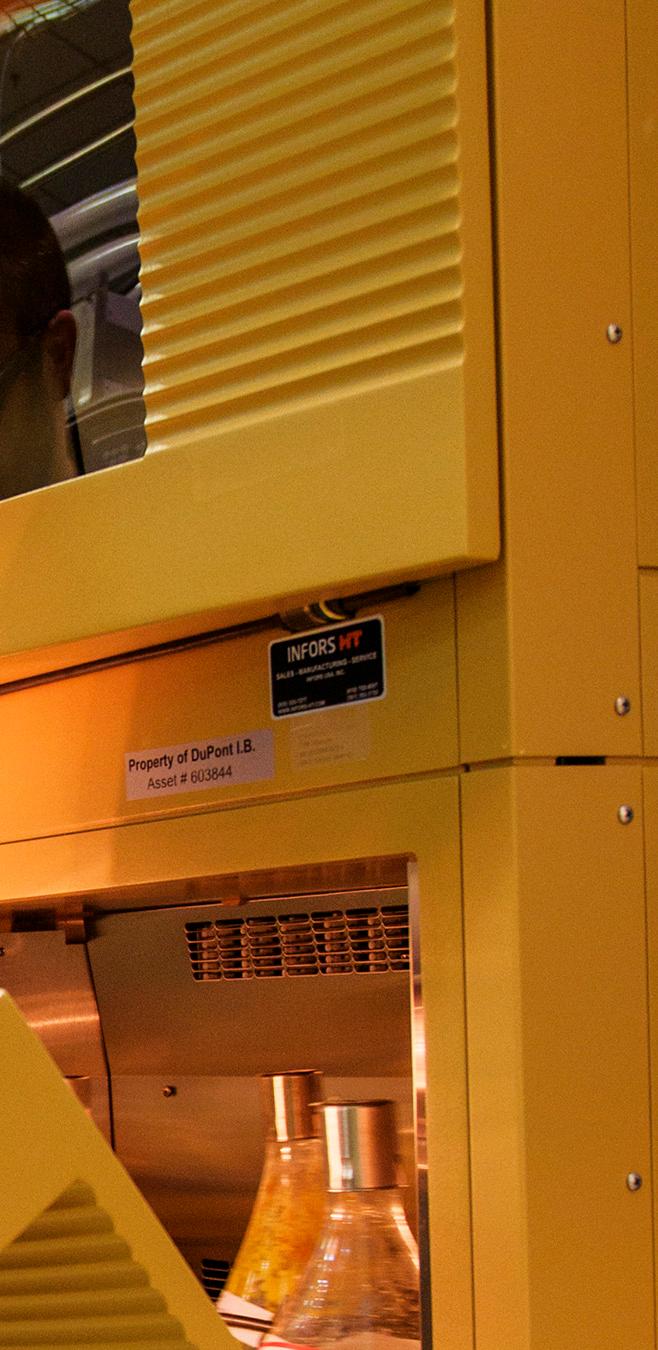

SPEED TO MARKET: Technology such as liquid handling robots are used to automate workflows in the lab, accelerating yeast innovation.
PHOTO: IFF
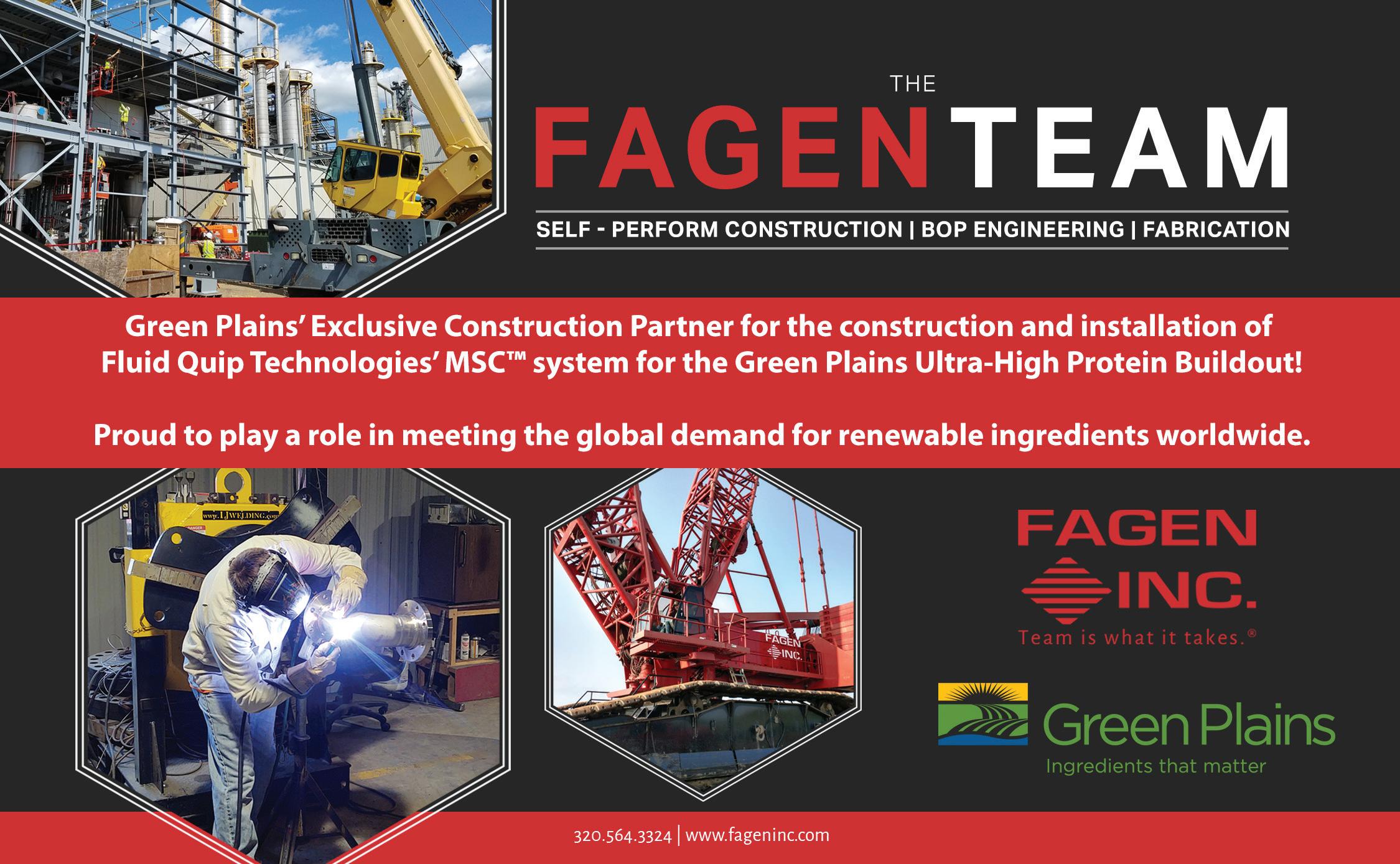
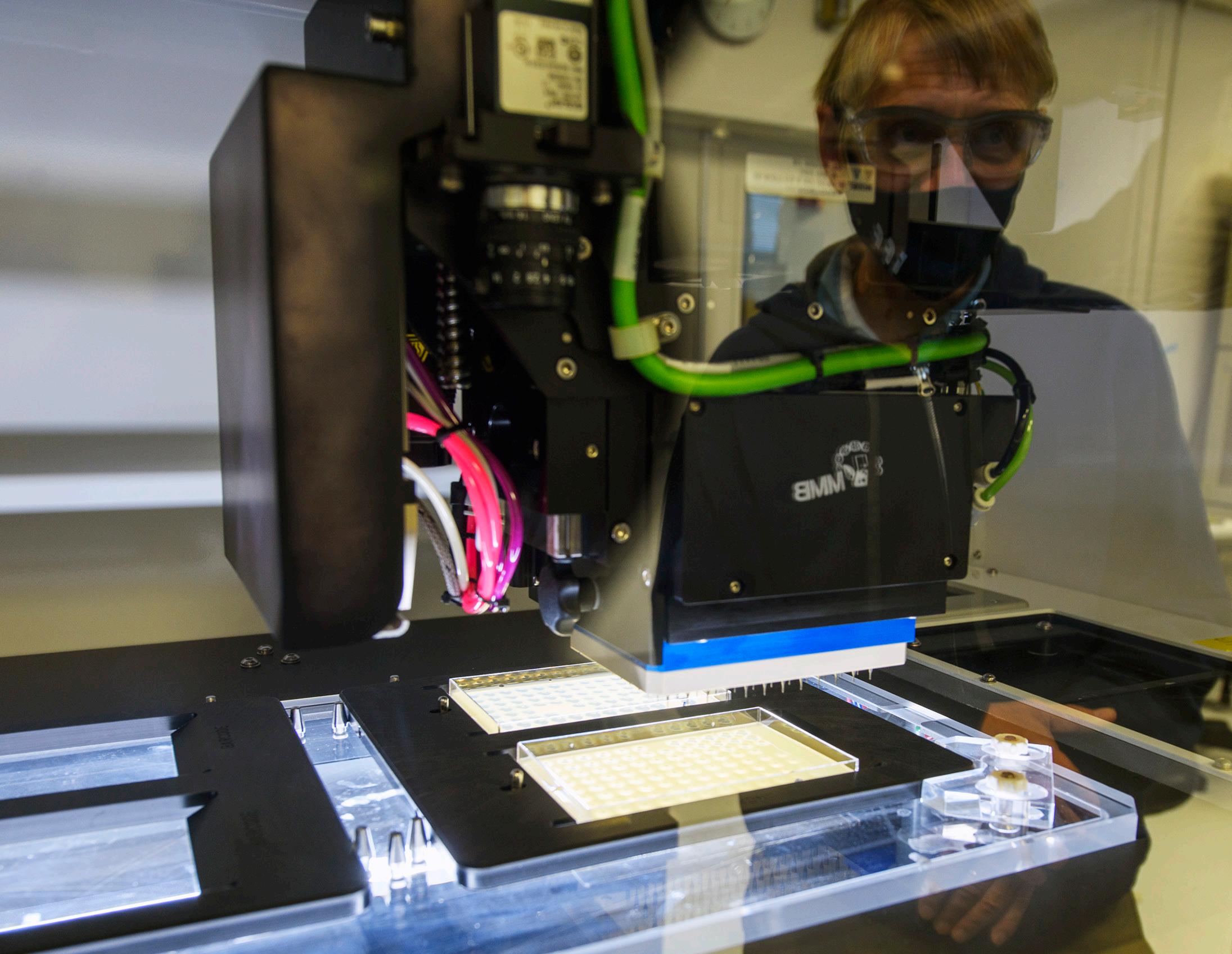
ON THE FIND: Automation is a critical tool in the process of screening and selecting new yeast strains.
PHOTO: IFF
does just that. “Whether they want to run for gallons or yield, the strain will push forward under whatever conditions they want to run,” she says. “We want to provide the customer with a super robust strain that will work under the conditions and how they want the plant to run.” The yeast also helps producers reduce costs by providing GA replacement, offsetting some of the enzyme that needs to be added to the system.
For IFF, a major focus has been robustness and a high titers ratio. “This yeast is capable of overcoming [infections and temperature excursions] and delivering 15%-plus w/v titers with very little glucose at drop,” Foerster says. “If you had asked us a decade ago, ‘Is that possible?’ I think most of our scientists would have said, ‘Possible, yes. Unlikely? Also yes.’ The fact that we've been able to make such progress is really a testament to their hard work guided by the insights from customers.”
Forester continues, “We've been investing in yeast engineering for over a decade now, and always with the aim of better fitting customer needs and learning stepby-step that those needs both change over time and are quite distinct plant to plant. Our yeast blends are one way that customers are adding fit and flexibility to their operations.”
Industry Input
Ethanol industry customers—namely plant managers and operators—play an important role in yeast development. Foerster says IFF’s yeast development teams go through a two-part process. The first is discovering new yeast traits, and the second is incorporating those traits and working with producers to test them in the marketplace.
“Producers play a critical role,” he says. “Often, as I’m thinking through this and looking back, they really provoke the scientific questions.” He gives an example of producers asking IFF if yeast could reduce residual starch. “They’re not going to come to us and say, ‘Can you alter this gene in the yeast?’ They’re going to come to us and say, ‘This is all great, but residual starch is what I’m being hammered on. Can you help with that?’”
Richards says producer input is critical to Lallemand’s process, too. He says the company receives valuable initial feedback from its customers, in terms of problems they hope yeast can solve and how their plants are operated. “That input helps drive R&D,” he says. “And then it’s being able to operate the plants under tighter tolerances that have been done in the past in order to ensure the new products work.”
He continues, “To generate yeast that have a specific purpose and are targeted at a specific goal, there’s a need to tighten parameters a bit, and that’s really where the second step comes in. For the operations staff, really putting in the effort, getting the knowledge, working on the training and understanding how the yeast perform in order to make those operational changes.”
The same holds true for Phibro, Gleason says. “Feedback really comes from our producers,” she says. “We look at what’s available in the market, and then what are the needs of our industry in that space. Do they want to run for yield? Or do they want to run for gallons, or do they want to run regardless of what the market conditions are and still get that performance.”
Cox and Osborne agree. “We definitely do not want to develop technology with blinders on,” Osborne says. “We don't want to be naive to think that we, as the technology provider, know more about how a plant operates than the actual plant operator. So, we very much pride ourselves with having the voice of the customer and working closely with major players in the ethanol industry. We absolutely want the feedback from the industry to help give us guidance on where to spend our energy and how to develop next-generation technologies.
Cox adds, “We definitely spend a lot of time visiting ethanol plants and talking directly with our customers. These dialogues are critical to help us build a good understanding of what innovation ethanol producers need and desire in the future.”
Unlocking What’s Next
Yeasts have experienced continuous advancements in traits like robustness and flexibility over the past several years, as well as technological advancements like embedding enzymes into yeast, and experts in the field expect advances to continue.
“Even though it’s one of the most studied organisms that exist on the planet, we’re still learning new things about how
systems inside those cells operate and interact, and therefore how their function can be improved,” Foerster says. “I feel comfortable predicting that even higher yields are possible. And producers have told us that it is crucial for them to be able to create new biorefinery products. Biofuels are at the industry’s core, but we are also working to deliver new animal feeds with superior value. Moreover, new innovations will make it possible for corn-based ethanol to have an even lower carbon intensity. I think all of those things, motivated by the ethanol producers’ thirst for innovation, make it much more likely that you’ll see continued yeast innovation.”
Gleason also foresees continuous improvement in the yield and robustness characteristics of yeasts, as well as more novel innovations that might redefine what’s possible with yeast. In her opinion, after developing a robust yeast strain that can help maximize yield, the ethanol industry would seek other areas in which yeast could play a role. “What is the next thing our industry would want? It’s to be able to do something else that would benefit the process. I can see that being the next big step in yeast innovation,” she says.
Osborne says Novozymes predicts a next generation innovation could be corn fiber substrate conversion. “The race is on to liberate C5 sugars from corn fiber to produce higher value ethanol while potentially tapping into low-carbon fuel credits,” he says. “I believe we’re on a path towards a biorefinery model, and plants will lead that evolution. Policy will also play a role, and we’re trying to keep our finger on the pulse. For example, if ethanol to sustainable aviation fuel advances, the ethanol production demands will increase. Thus, we’re trying to keep ourselves connected with ethanol producers and potential off-takers for advanced fuels and precursors to make sure we know where and how biology fits in. I think we’re going to see this rapidly evolve in the next three to five years, and it’s going to be exciting.
Cox agrees, adding that coproducts will also play a role in future yeast innovation. “As we see it, yeast is the key biotechnology tool in ethanol plants,” he says. “We can enable further substrate conversion and continue to push higher ethanol yields. We can enable coproduct improvement and enhancement. There is so much to go for. We're in position to pivot with the industry and we’re keeping our eyes on where things go knowing that yeast innovation will be the centerpiece of many of our innovation programs going forward.”
Osbourne adds, “We’re living in the middle of the DNA revolution. The rate at which we can pivot, engineer and produce products that deliver on our customers’ needs is exciting. We’ll be part of driving that conversation, but our customers will drive it as well.”
Author: Matt Thompson Contact: editor@bbiinternational.com
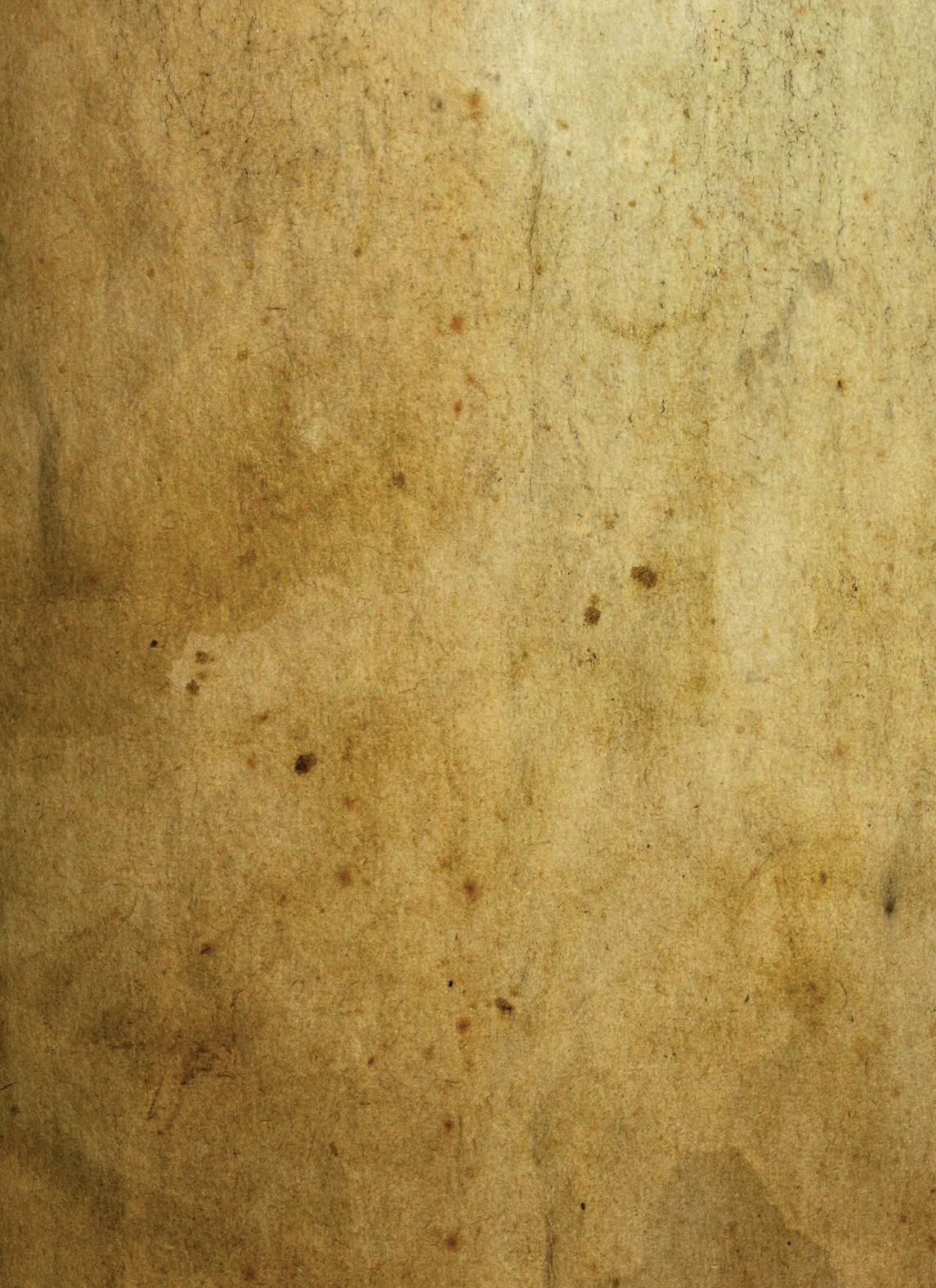
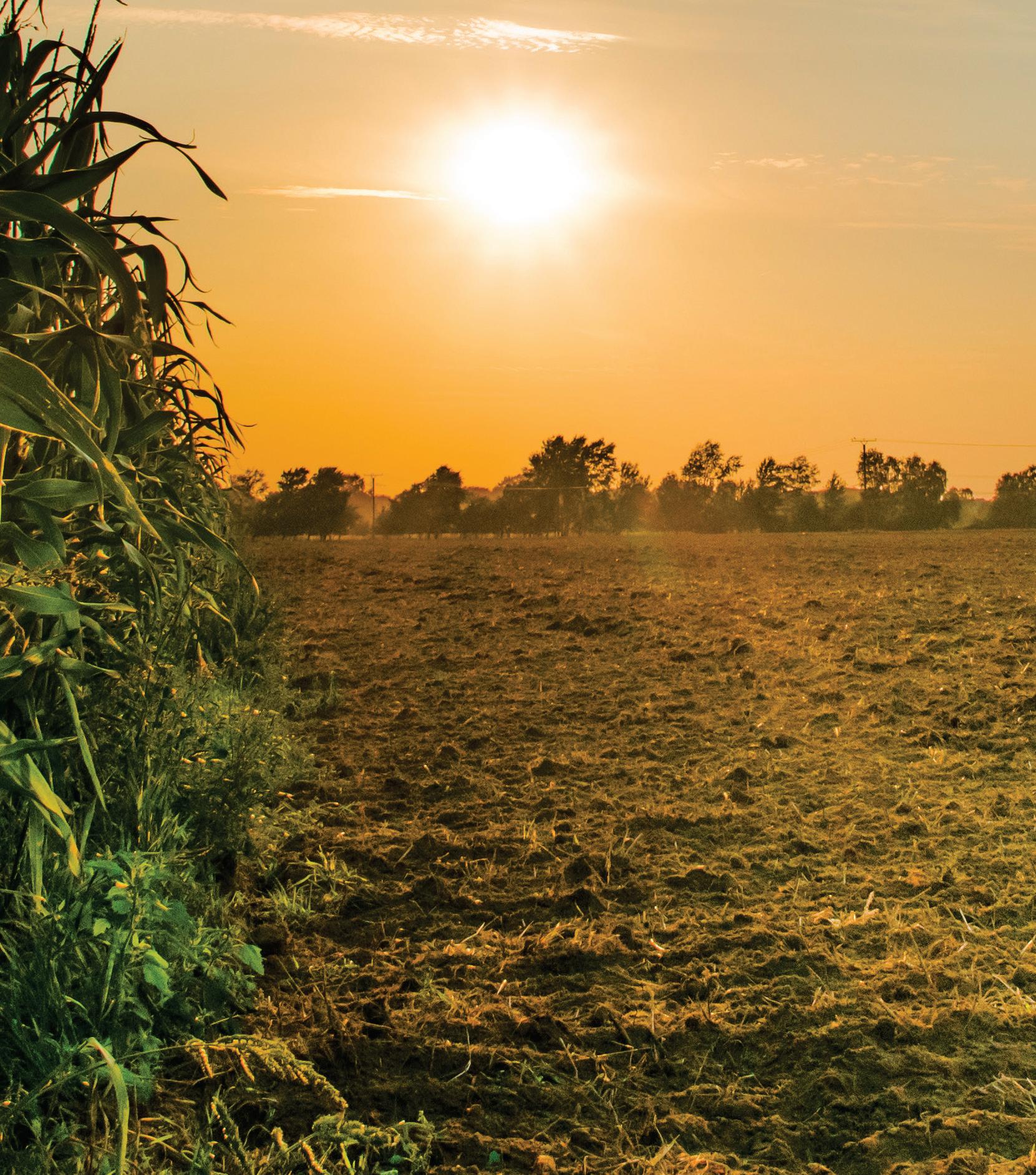
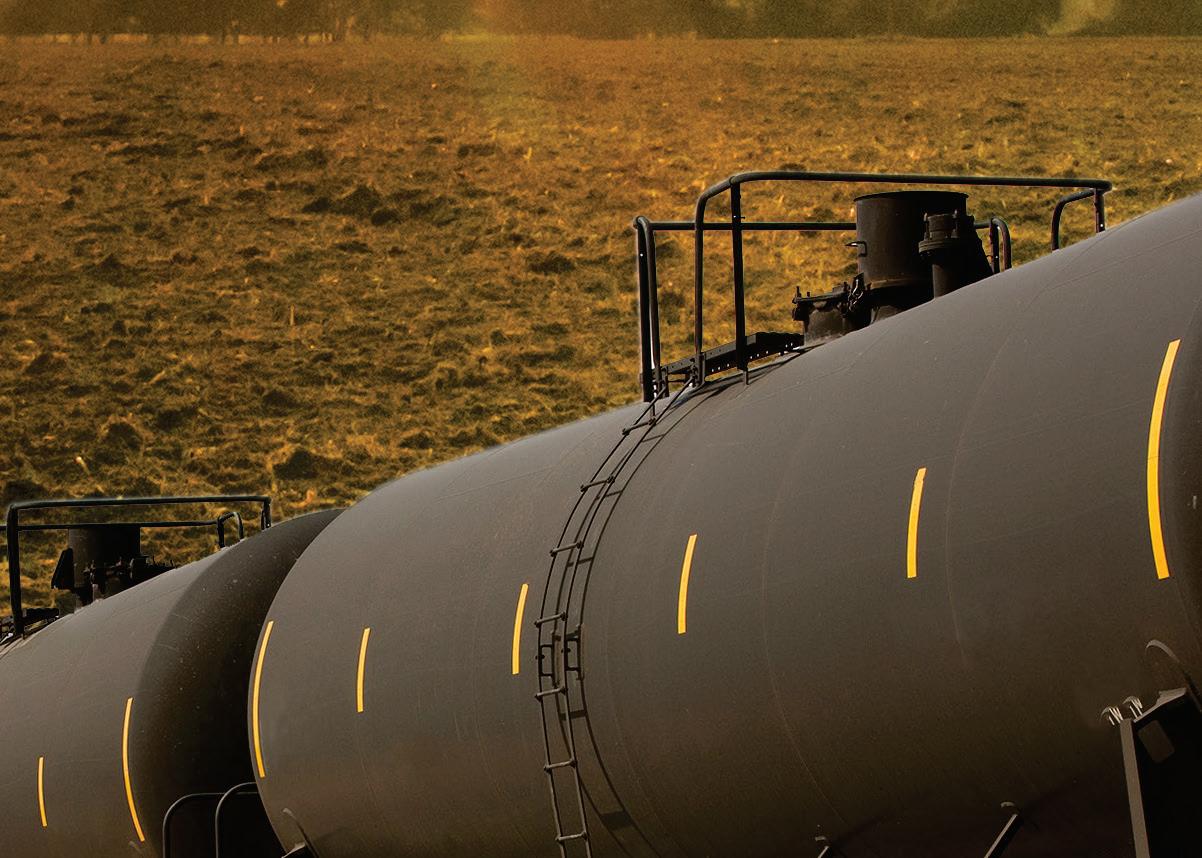
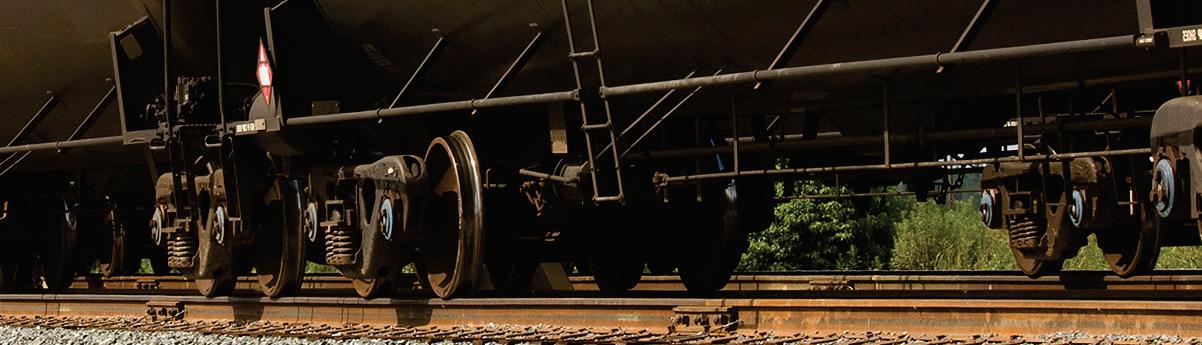

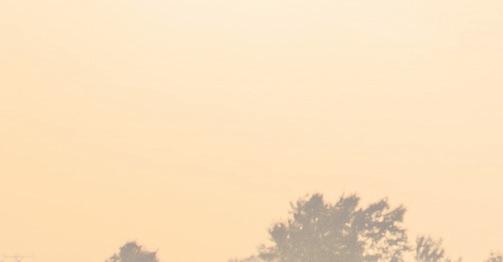
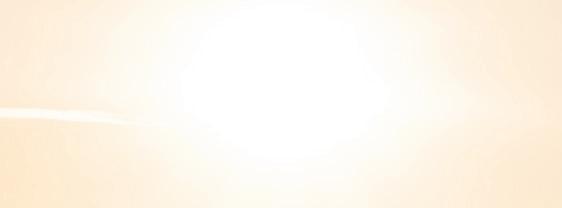
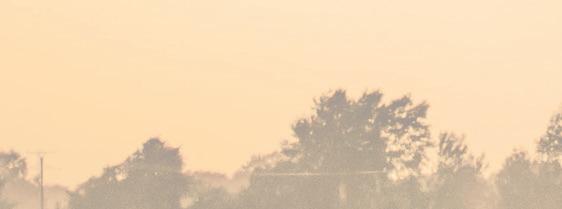
