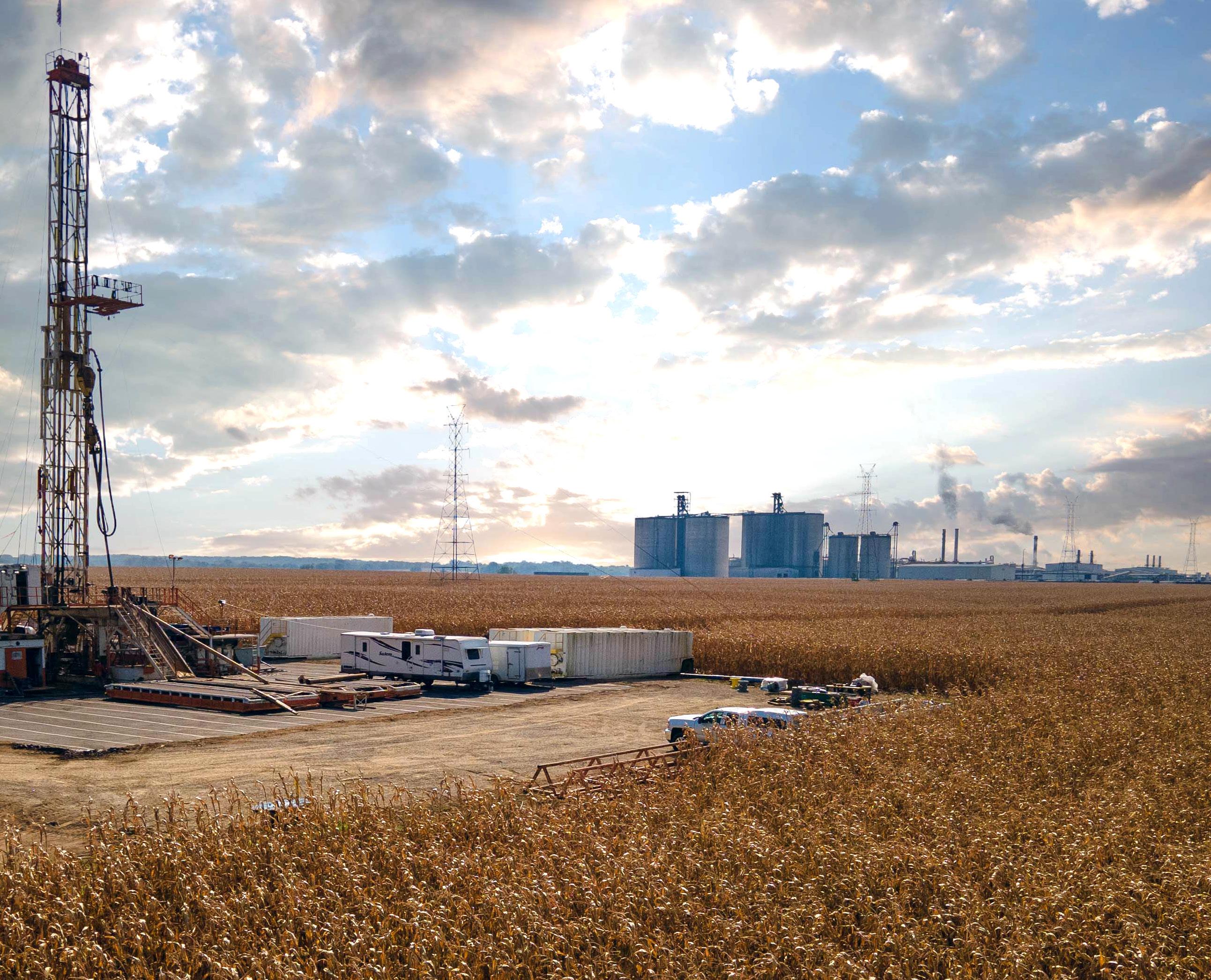
11 minute read
CARBON
SEQUESTERING IN PLACE
Pipeline aggregation of ethanol plant CO2 has captured industry attention, but stand-alone CCS projects might be uniquely positioned for early success. By Luke Geiver
Carbon capture and sequestration (CCS) projects are integrating into existing ethanol plants like never before. In the
past two years, numerous plants in the heart of ethanol-production country—spanning several Midwest states—have announced their intentions to implement CCS. A majority of the projects announced will rely on pipeline networks to take compressed CO2 from participating ethanol plants to alternative locations where the gas will be utilized for industrial purposes or, more likely, injected thousands of feet below the surface. In early May, Summit Carbon Solutions announced a successful $1 billion equity raise for its proposed CCS pipeline, which would link more than 30 ethanol plants into its system. But not every ethanol plant eyeing CCS is planning for pipelines.
A handful of plants are taking the steps—or already have—to explore the feasibility of capturing and storing CO2 onsite, or very close to the confines of the ethanol plant’s geographic footprint. Reviewing why and how those plants are approaching and dealing with the variables related to the process shows what it takes to sequester on location, autonomously. Putting CO2 Under Your Plant
Ethanol plants considering onsite CCS should remember that tried-and-true real estate mantra: it’s all about location, location, location. There’s a twist, however. It’s not so much about the surface location. The sequestration portion of CCS relies on the presence of a geologic formation capable of housing carbon gas molecules and trapping them. Every plant location is different in terms of the geologic formations below ground. In some areas, a suitable rock structure like sandstone or limestone may exist only 1,000 feet underground. In other cases, the target structure for CCS may be more than two miles down. The deeper the suitable formation, the costlier the upfront price.
While CCS projects using pipelines must overcome the challenge of gaining public and government buy-in for rightof-ways and multi-month installation, inplace sequestration projects must start with the well permitting process. From there, a permitted well can be drilled by a reputable drilling company. The core samples from the drill-out will reveal the geologic formations below the surface. Although the geology is generally already understood for most areas in ethanol country, the process still has to be undertaken to ensure exactly what lies beneath. If the test well shows favorable geology, it can be used as the injection well. Other injection points can be added, along with the compression equipment needed to take CO2 from its gas state into the liquid state needed for injection. A monitoring system must also be installed.
In California, progressive renewable energy producer Aemetis has undergone the early test well phase. The company has completed a study, led by globally recognized drilling contractor Baker Hughes, to evaluate the drilling site, perform an underground formation review and ensure the feasibility of drilling technology for the CCS injection projects. The company’s
CCS NEAR THE PLANT: In Illinois, Marquis Energy recently completed a 5,000-foot test well to determine the capacity available for carbon sequestration at the company’s planned industrial site near one of its ethanol plants.
PHOTO: MARQUIS
study showed that more than 2 million metric tons of CO2 per year could be injected at its Keyes ethanol plant site.
In late 2021, Marquis Energy began drilling a 5,000-foot test well to determine the capacity available for carbon sequestration at the company’s planned industrial site in Hennepin, Illinois. The site lies above the Mt. Simon sandstone formation. The porous nature of sandstone is well-suited for capturing and containing gas. A large part of CCS isn’t just about the formation the carbon will go into, but the formations around the storage area.
Carbon America, a vertically integrated CCS “super developer,” is helping two Colorado ethanol plants install CCS systems at their locations. At Sterling Ethanol LLC and Yuma Ethanol LLC, Carbon America will help each capture and store roughly 95 percent of the CO2 emissions generated through the fermentation process. Carbon America will build, own and operate the systems in northeastern Colorado.
Rex American Resources Corp.’s Illinois ethanol plant, One Earth Energy, drilled its first test well in December 2021. Working with the University of Illinois, the team at One Earth is trying to determine the feasibility of an onsite CCS well, including its size and scope.
In North Dakota, two ethanol facilities are leading the way to onsite sequestration. Near Underwood, Midwest AgEnergy Group (MAG) has been exploring the feasibility of a CCS well for its 70 MMgy Blue Flint ethanol plant. MAG is still testing the feasibility of the CCS system and currently working through the long-term planning stages of development.
And then there is Red Trail Energy. RTE is undergoing a historic effort to bring
WE CLEAN SILOS
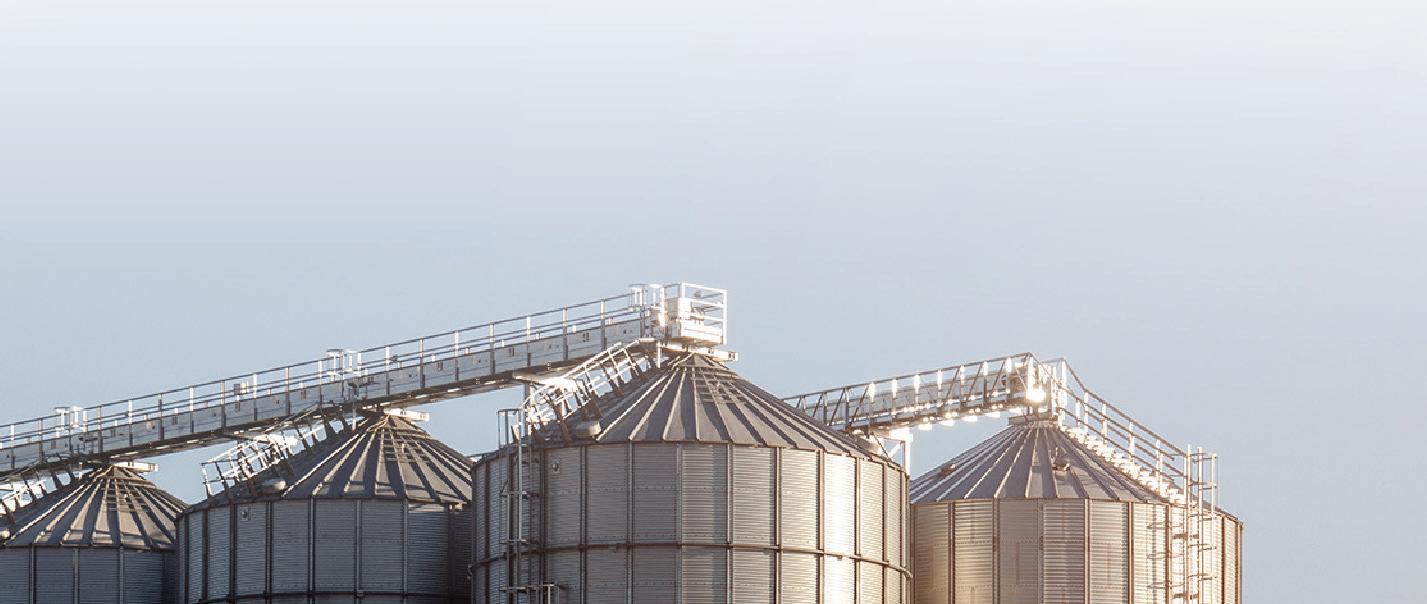
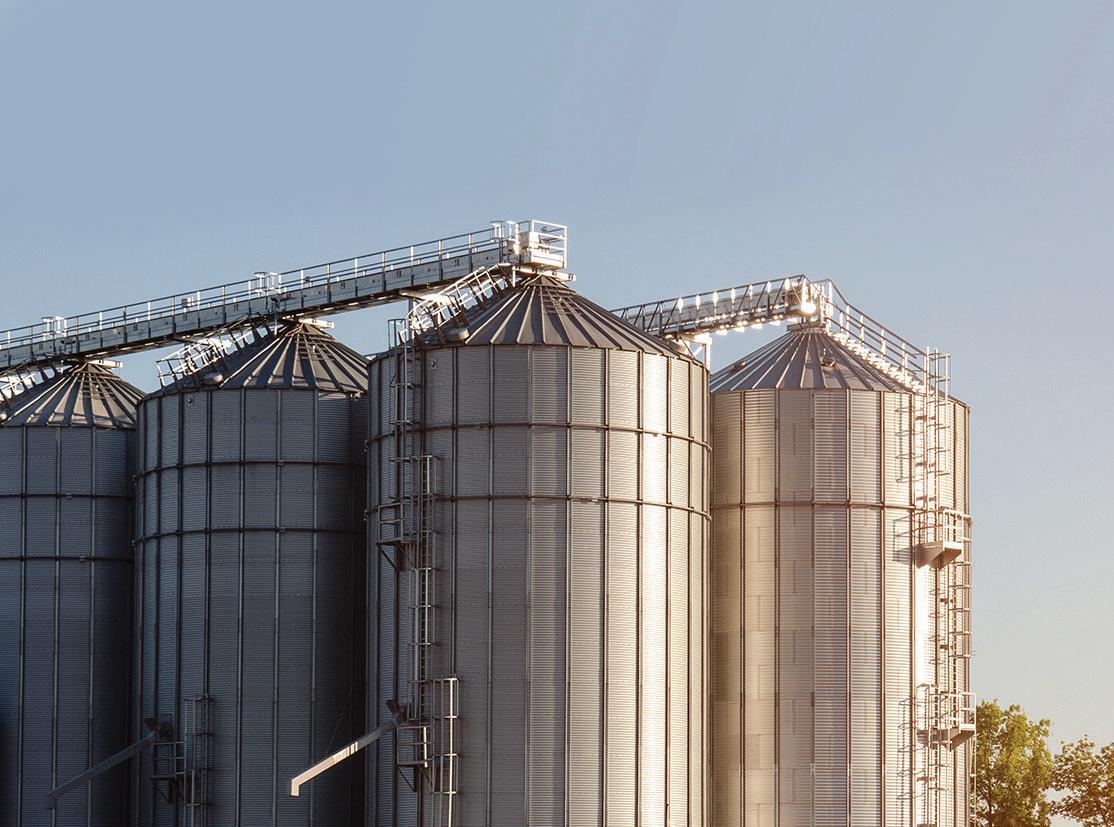
Why is Mole•Master™ the ethanol industry’s first choice for silo cleanout?

EXPERIENCE
#1 silo cleanout contractor, worldwide, for 35+ years.
TOTAL MATERIAL RECOVERY
Bulk storage and process vessels are restored to 100% of planned storage capacity with maximum ef ciency and minimum downtime.
RESTORED PRODUCTION
100% dry process, no mess, no mud and no expensive cleanup.
Mole•MasterTM crews are intensively trained to OSHA/MSHA standards and are ready to mobilize to your site, anywhere on earth.
www.molemaster.com
GOING FOR ZERO: In central North Dakota, Midwest AgEnergy Group is actively exploring the feasibility of carbon capture and sequestration at its 70 MMgy Blue Flint ethanol plant.
PHOTO: MAG
its own CCS system onsite at its ethanol production facility grounds. The project could be a blueprint for other ethanol plants considering the investment into CCS.
Red Trail Energy
Near Richardton, North Dakota, RTE was originally constructed as one of the first coal-fired ethanol plants in the nation. In 2016, the plant converted to natural gas. It produces more than 60 MMgy using roughly 23 million bushels of corn annually. In addition to the 2.8 gallons of ethanol produced from every bushel of corn, the plant makes 125,000 tons of dried distillers grains, 80,000 tons of modified-wet cake and 15 million pounds of distillers corn oil per year. The second-gen plant received a CO2 storage facility permit in October 2021.
RTE has already started constructing a capture facility adjacent to its ethanol plant that will push 180,000 metric tons of CO2 annually. Like the Marquis facility in Illinois, the RTE project will inject into sandstone. The formation, more than a mile below RTE, is known as the Broom Creek formation and is sealed by several layers of impermeable shales more than half-a-mile thick. The shale layers surrounding the Broom Creek formation protect groundwater and prevent CO2 from escaping, according to the University of North Dakota Energy and Environmental Research Center (EERC), a major partner working with RTE to make the project a success.
At the plant, the CO2 exhaust from the fermentation vessels is set to be captured and piped to a capture facility next door. That exhaust is compressed and dehydrated to purify the CO2. The rest of the exhaust, mainly water vapor and oxygen, is released into the atmosphere. Oxygen and water are both corrosive to the CO2 capture and injection components, including the flow line, wellhead tubing, fittings and monitoring components.
At the gas capture plant, CO2 is compressed from 1,500 psi into liquid CO2 (which flows like water). The compressor, according to EERC’s design team working on the project, acts
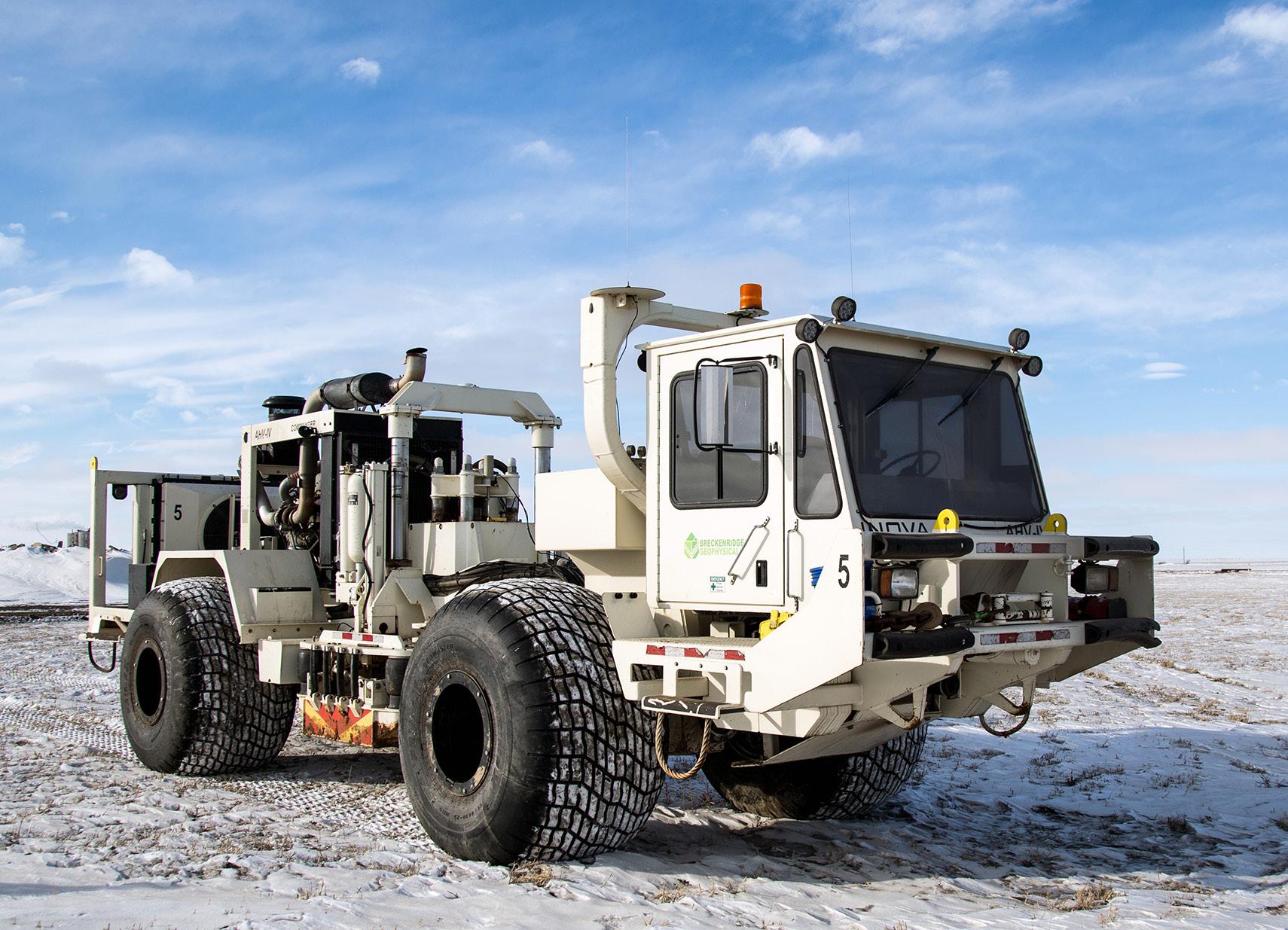
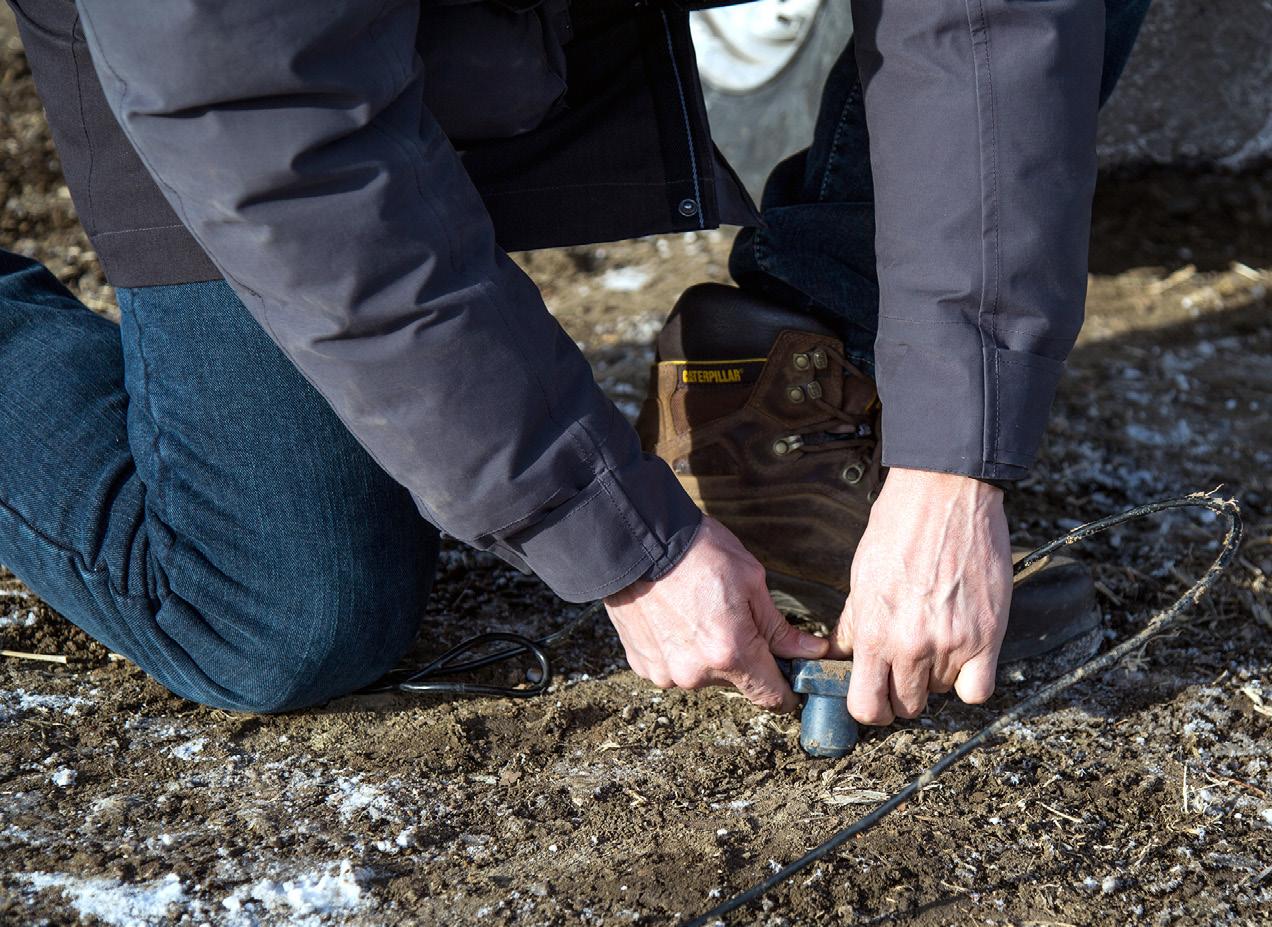
GROUND-LEVEL ANALYSIS: In North Dakota, Red Trail Energy recently completed a survey involving the use of vibroseis trucks (above left) that perform seismic recordings using battery-powered sensors and wi-fi transmitters placed at 165-foot intervals in a pattern surrounding the injection area (right).
PHOTO: EERC
like a water tower, providing the pressure for the downhill flow into the injection well. Real-time, continuous fiber-optics monitors the entire path of the CO2.
RTE has shown what it takes to make sequestering in place work. Collaborating with EERC and the North Dakota Industrial Commission, RTE was able to work through the process successfully. In addition to obtaining the appropriate permits for a process never done before, RTE was also able to perform a geologic survey to find out where the injected gas would go deep underground.
That survey involved a series of vibroseis trucks that perform seismic recordings using battery-powered sensors and wi-fi transmitters placed at 165-foot intervals in a pattern surrounding the injection area. The trucks drive around and over the
transmitters, stopping at intervals to vibrate the ground for one to two minutes (staying away from buildings or other infrastructure). The eight-square-mile survey was performed only after RTE had reached out to area landowners and the public, announcing the survey, requesting access to place sensors and to drive the vibroseis trucks in the area. Results from the survey data were ETHANOL PRODUCER_HALF PG AD used to determine the behavior of the CO2
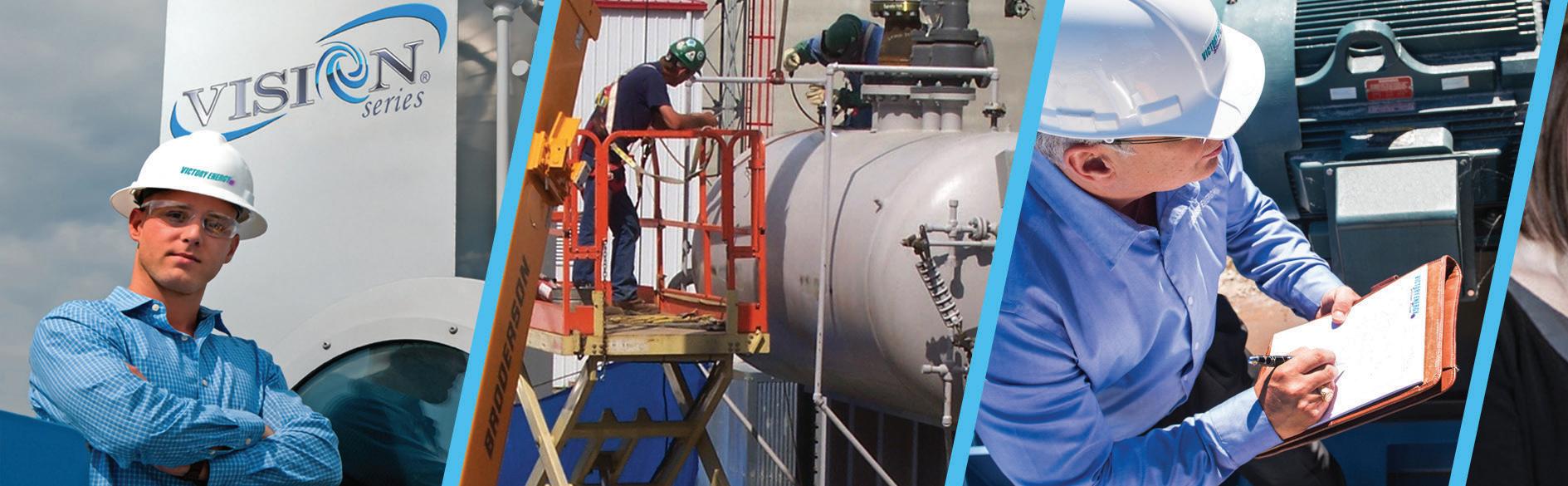
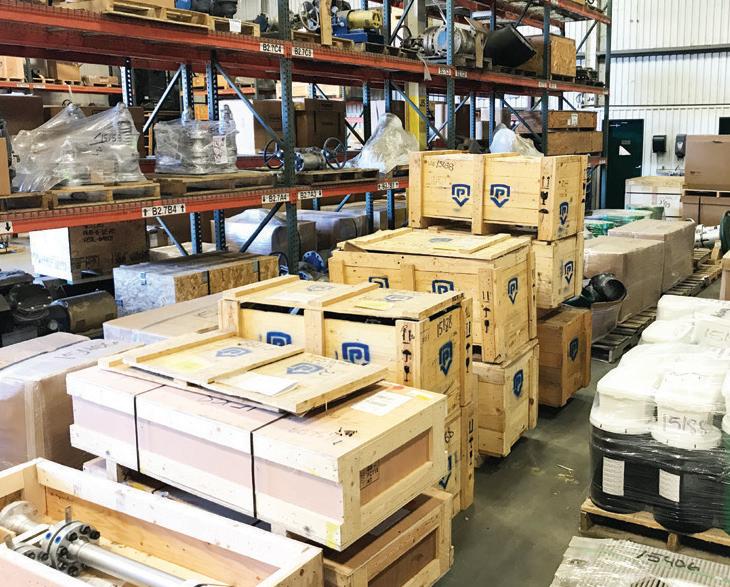
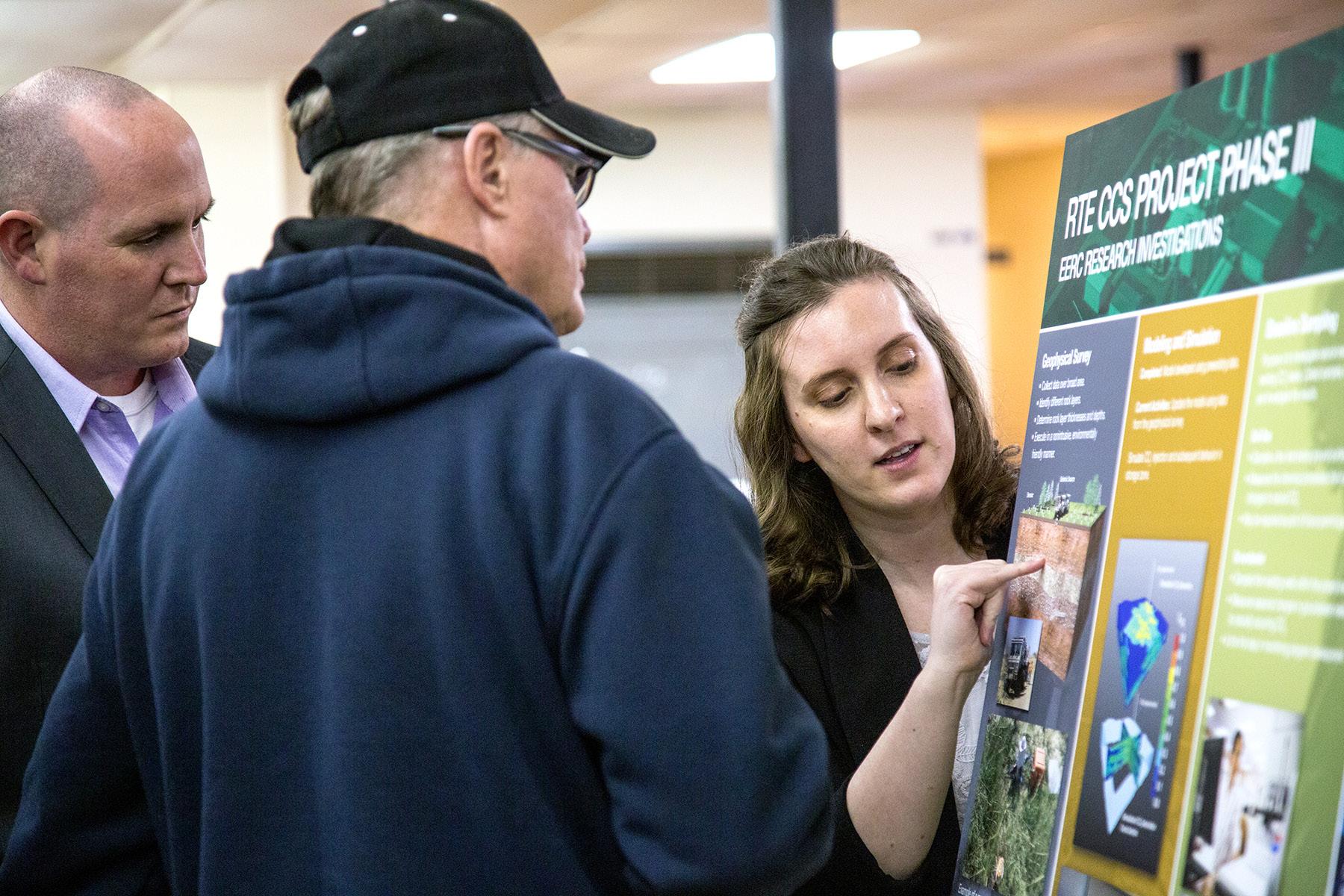
SHARING THE PLAN: EERC geophysics research scientist Amanda Livers explains Red Trail Energy's planned CCS project to an attendee of a recent community open house while the ethanol plant's COO, Dustin Willett, looks on.
PHOTO: EERC
once injected. The surveys are also used to create a monitoring system effective for long-term storage.
Dustin Willett, chief operation officer for RTE, says that although most CCS projects have some flexibility, the RTE project is designed specifically for permanent CO2 storage. The project has to be maintained and monitored (including periodic reporting) to ensure economic viability through credits from the California Low-Carbon Fuel Standard. Willett says the site will house just one injection well.
The work to obtain the permit for the injection well is a landmark, he says, adding that it could be used as a model for other states, and other ethanol plants, to follow in the future. But some things, Willett also says, must be obtained on an individual plant basis. “Many elements will never be turnkey or faster in the development of a successful project,” he says, “Core collection, subsequent laboratory analyses [and related] contingencies should be planned and expected, because every project has unique components ranging from geology to business structure.”
For RTE, the ethanol plant owns the CCS entity. From 2016 to 2021, the U.S. Department of Energy, via the EERC and North Dakota Industrial Commission’s Renewable Energy Program, provided funding to RTE for feasibility studies. “Establishing good partnerships and working relationships with program and regulatory agencies, and facilitating communication in the early stages, is crucial to project success,” Willett says.
In addition to the EERC, RTE also worked with other technical partners including Trimeric Corp. for engineering services, Schlumberger Carbon Services for drilling and geologic work, and Computer Modelling Group Ltd., for analysis of the geologic survey of where the injected CO2 would end up below ground.
RTE is currently awaiting a decision on its historic permit to greenlight the system. The company expects positive announcements and milestones later in 2022.


CCS On Your Site: Five Basic Steps
For ethanol plants looking into onsite CCS, the early process involves drilling, sampling and data collection.
1. Obtain Permits: Drill holes for geologic research requires drilling permits. Every state has a geologic division with forms or answers on what is needed.
2. Prepare the Drill Site: Pad preparation usually requires leveling a space of 400 feet by 400 feet. The drilling rig needs a flat, workable surface. Pads usually take two weeks to construct.
3. Drill the Hole: Well drilling in the modern age is a multi-step process. Each stage includes adding casing or using drilling mud and cement to ensure that the downhole effect doesn’t impact existing freshwater sources.
4. Gather Downhole Data: After the shaft is drilled out and core samples of rock are collected, wireline trucks with sensors lower line into the well to gather more data. All of this is standard practice.
5. Close the Hole: Following data collection, test holes or wells are sealed temporarily while data is analyzed.
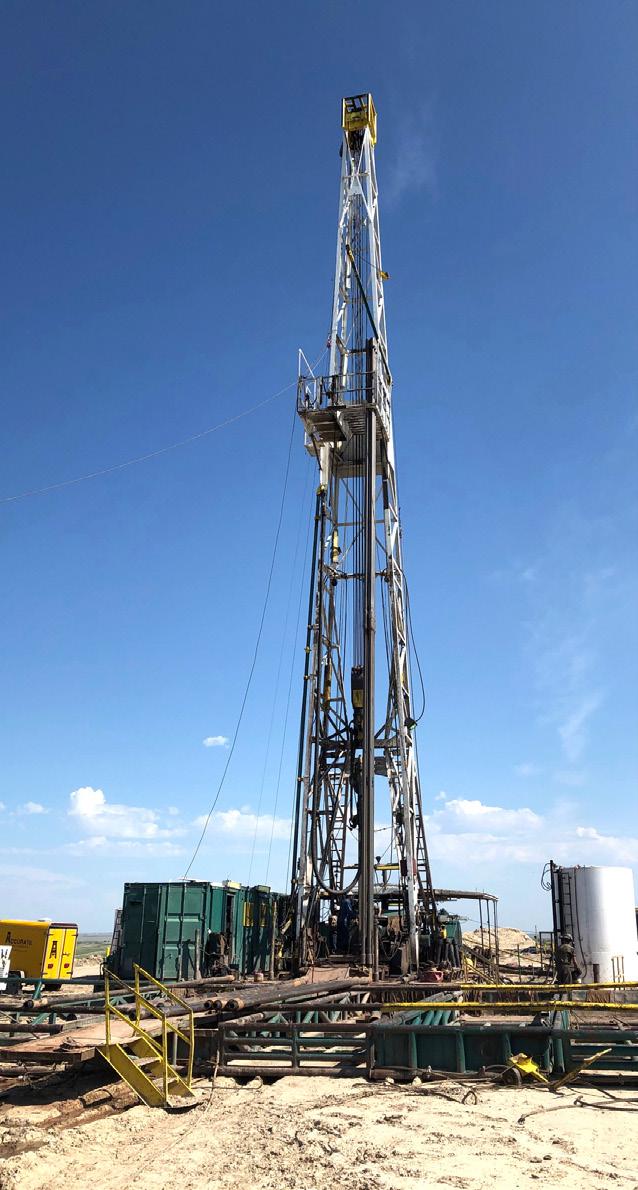
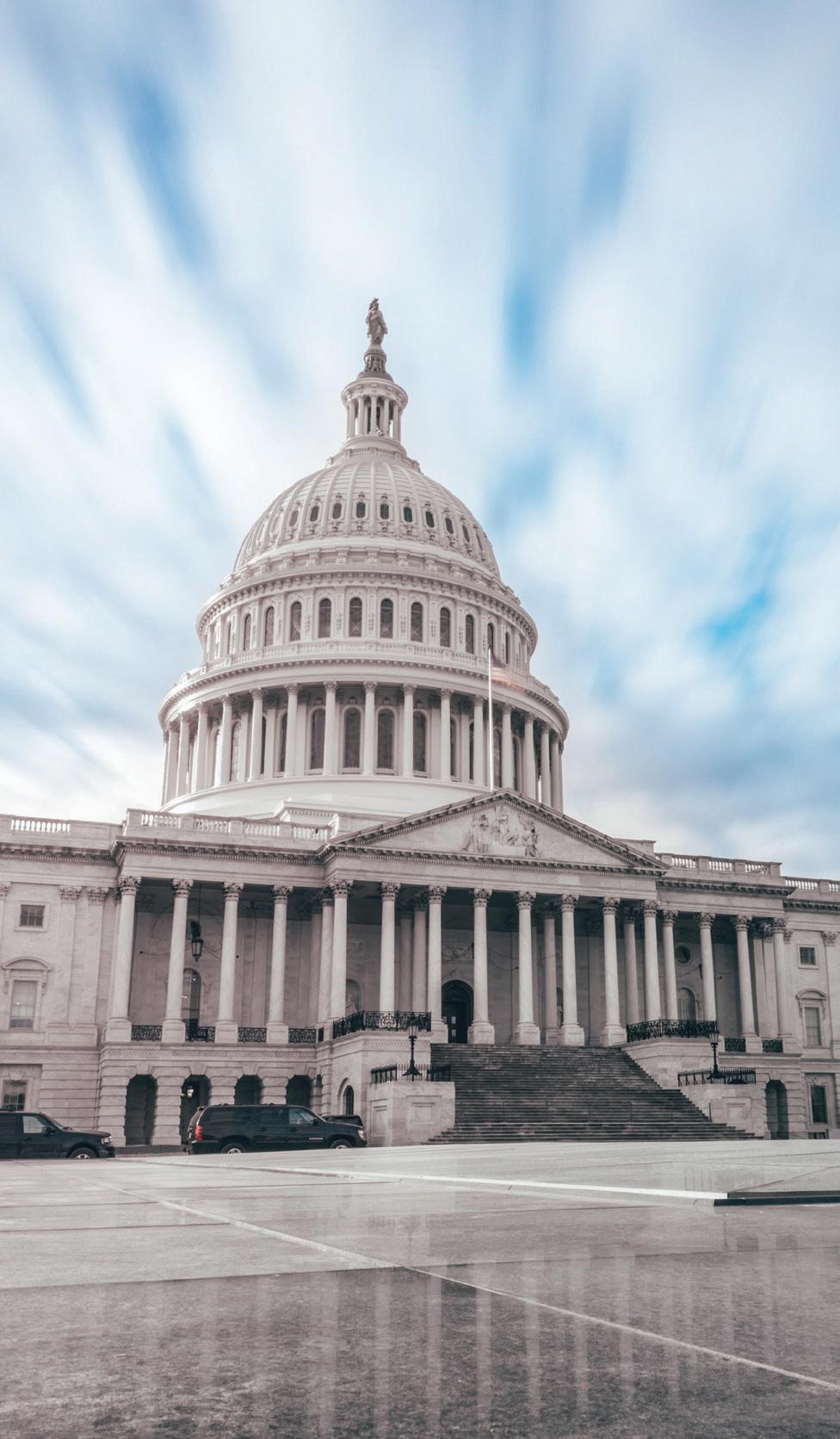
Costs for the completed project are still undetermined.
Equipment for the Job
While RTE awaits final approval to fully deploy its CCS system in North Dakota, the Summit Carbon Solutions pipeline project, backed by $1 billion in private equity, offers insight on who is out there to supply equipment.
Xebec Systems USA LLC (doing business as UECompression) specializes in electric motor driven high-speed reciprocating compression systems designed for the CO2 emitted from ethanol plants. Xebec is supplying equipment for the Summit pipeline. Greg Herman, a veteran of gas compression technology for Xebec, says the gas dictates special materials for construction and design. Herman says his team is well suited to work with ethanol producers because they understand the intricacies of the gas/equipment relationship.
“Our team works closely with project developers and their process engineering firm. Understanding the challenges presented by the corrosive gas, and building a reliable compressor, is paramount to the system operating as designed,” Herman says.

According to Herman, Xebec’s portfolio includes products for renewable natural gas in the agriculture markets, onsite generation of hydrogen and nitrogen as emerging fuel and feedstocks options, and gas upgrading or compression systems for CCS no matter where the CO2 ends up. Herman believes Xebec is a leader in the push to capture carbon in the ethanol space. “We will continue to look for processes and products,” he says, “to continue this movement.”
Author: Luke Geiver Contact: editor@bbiinternational.com