
6 minute read
PERFORMANCE
OPTIMAL INNOVATIONS: Advancements in cleaning technology, including data availability, enhance overall performance.
PHOTO: STOCK PHOTO
Advancements in Technology
Advanced CIP, dosing technology improvements and data analysis illustrate the significant impact cleaning strategies have on overall performance. By David Fowlie
As ethanol producers position themselves for continued success under challenging market conditions, the impact cleaning programs have on overall plant performance has become a major focus in their efforts to optimize profitability.
The introduction of advanced clean in place (CIP) and foulant prevention chemistries, implementation of more accurate and consistent dosing equipment, and a data-driven focus to measure the impact of CIP strategies on plant performance have fueled innovation in CIP management. Distinct Operational Units
Historically, ethanol plants widely adopted a standard cleaning approach utilizing commodity chemistries such as caustic and sulfamic acid to clean all sections of the plant. This approach does not take into account the distinct cleaning challenges
presented by different operational units within the plant or the specific cleaning goals of these operational units and their impact on overall plant performance.
The foulant challenges for different sections of the plant vary widely, requiring different approaches to control the rate and type of foulant formation. Producers are now approaching each plant operational unit as a unique environment to optimize CIP chemistry, duration and frequency.
For example, controlling fouling in the liquefaction mash flow through the mash banks presents very different challenges compared to the thin stillage process flow in the evaporators. Implementing a CIP program focused on controlling organic deposit buildup in the mash banks to positively impact fermentation kinetics, while applying a different CIP strategy to control both inorganic and organic fouling in the evaporators to optimize heat transfer, will result in the most positive impact on overall plant performance.
Prevention First
The introduction of advanced foulant prevention and cleaning formulations has provided plant management with a range of technology options for their CIP programs. The use of scale inhibitors, organic deposit control agents, detergent cleaners and oxidation agents optimizes CIP processes and addresses the specific challenges presented by different plant operational units.
Scale inhibitors and organic deposit control technologies help plant operations run more consistently for longer periods of time between CIP events, reducing the frequency and duration of CIP, leading to improved productivity and lower total CIP program costs.
The addition of an organic deposit control agent to plant mash banks can provide improved mash flow, lower liquefaction differential pressures and increase heat transfer to beer. The use of scale inhibitors to evaporator systems can reduce
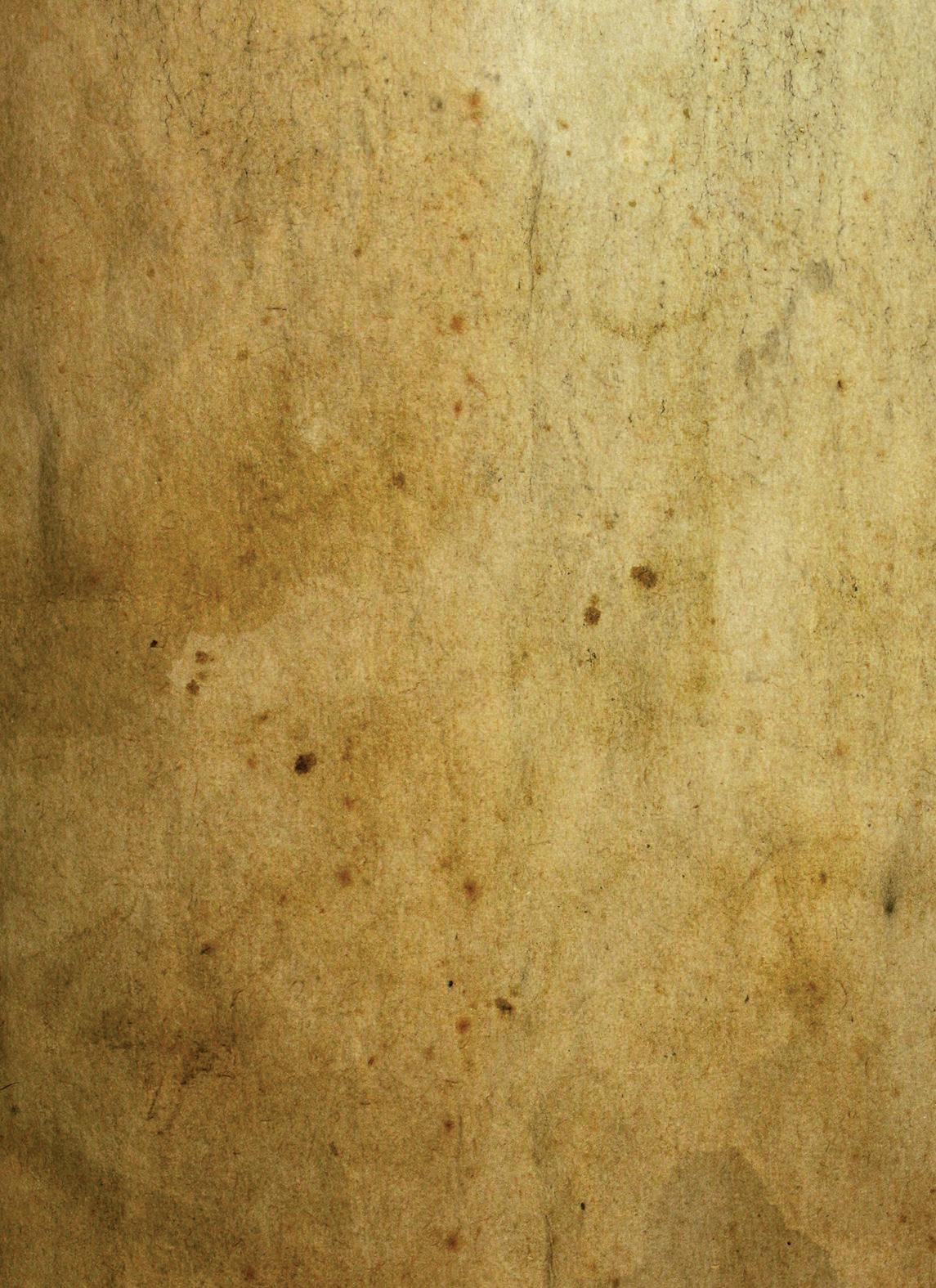
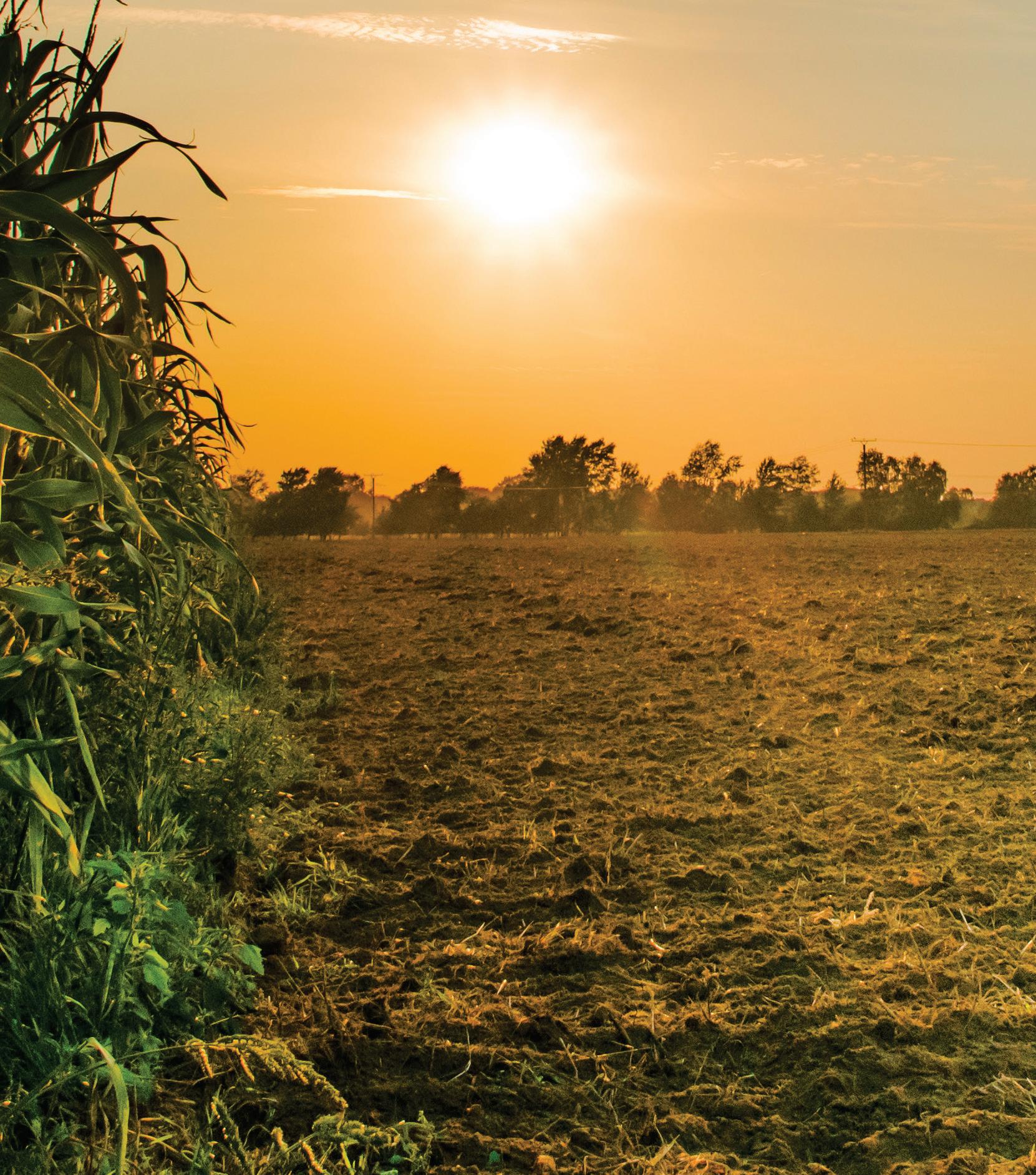
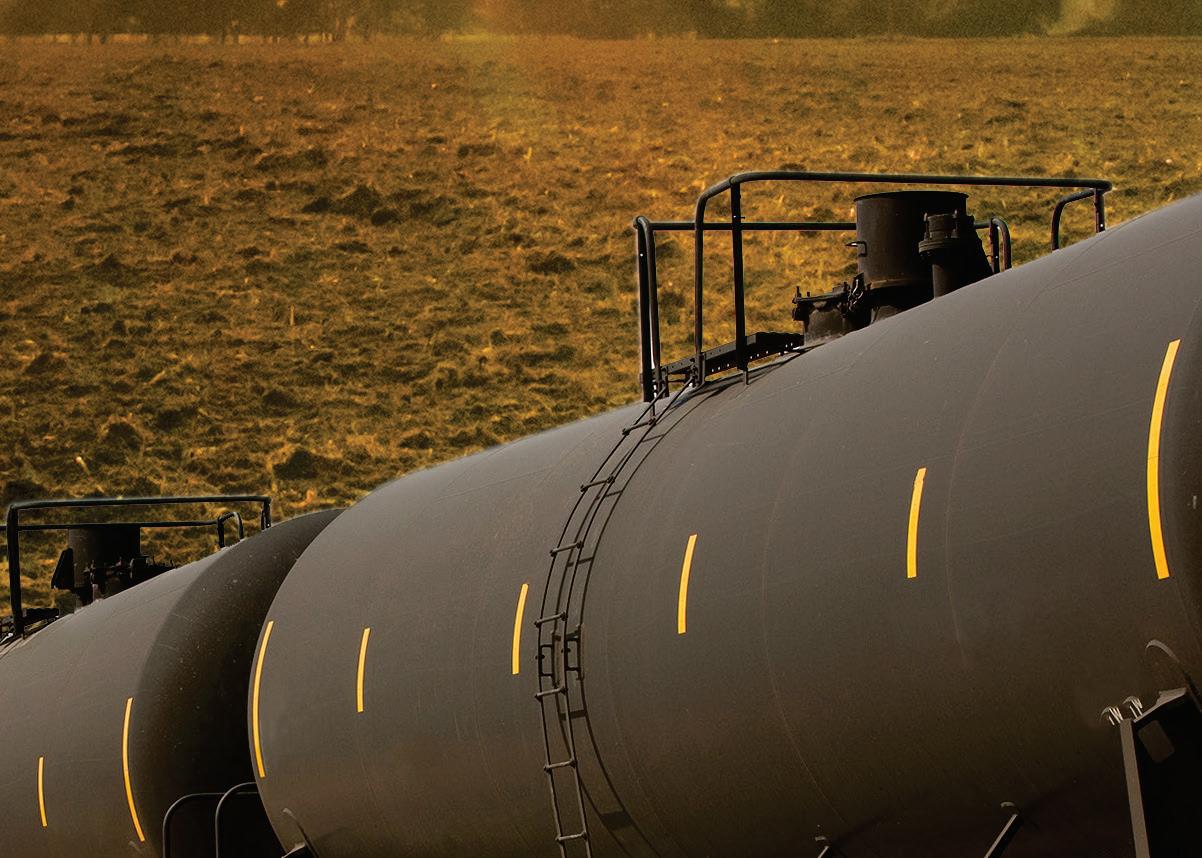

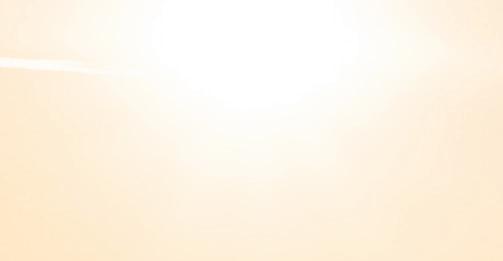
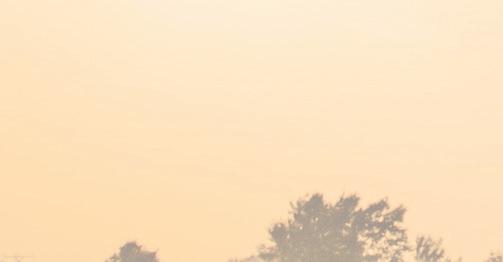



WE CLEAN SILOS
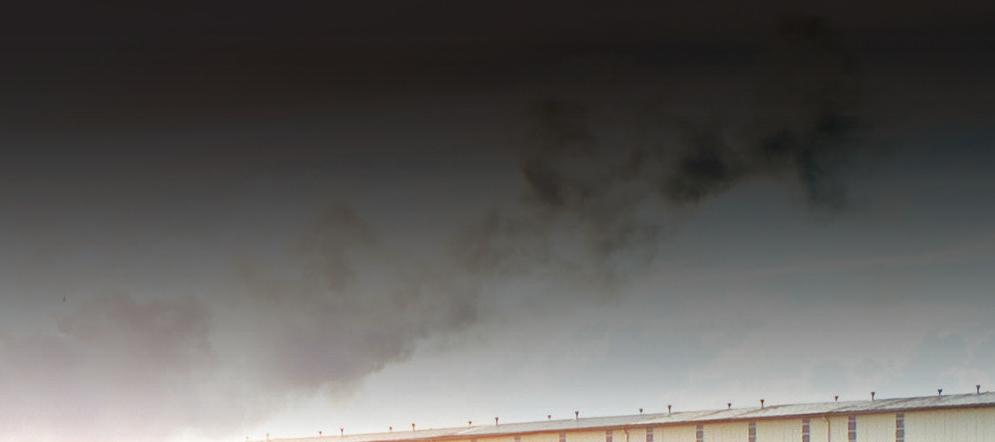
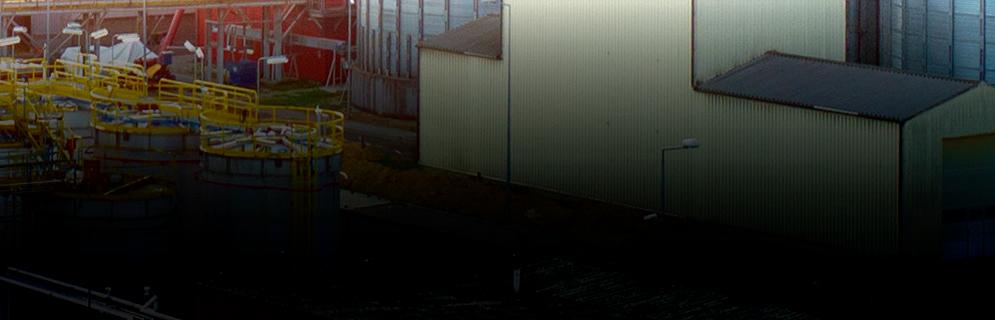
OUTAGE SERVICES

Bin Cleaning, Complete Cleanout and CSE Vacuum Services.
SAFETY
No hazardous human entry of con ned spaces. No chemicals or explosives used in the process.
TOTAL MATERIAL RECOVERY
Storage vessels are restored to 100% of planned storage capacity.
RESTORED PRODUCTION
100% dry process, no mess, no mud, and no expensive cleanup.
Intensively trained to OSHA/MSHA standards, Mole•Master ™ will mobilize to your site, anywhere on earth. the formation of inorganic scale, slowing the rate of pressure buildup within the evaporators. This can provide improved heat transfer and evaporator efficiency while reducing CIP frequency, duration and cost.
Adoption of detergent cleaners used either on their own or in combination with caustic- or acid-based CIP has had a significant impact on CIP efficiency. Detergent cleaners enhance the penetration of cleaning solutions into plant deposits and improve cleaning performance through chemical dissolution and physical cleaving of foulants from plant surfaces. These formulations provide potential cost savings through optimization of cleaning cycles, facilitate the reduction of required CIP concentrations, and help preserve the stability of CIP solutions to extend their service life.
As the industry has become more aware of the dynamics and challenges related to managing caustic-based CIP solution stability, more plants are choosing to eliminate caustic CIP and adopt a low pH CIP system. The use of low pH cleaning systems combining strong oxidizers, such as nitric acid, with detergent cleaners can provide a more effective CIP program at lower cost.
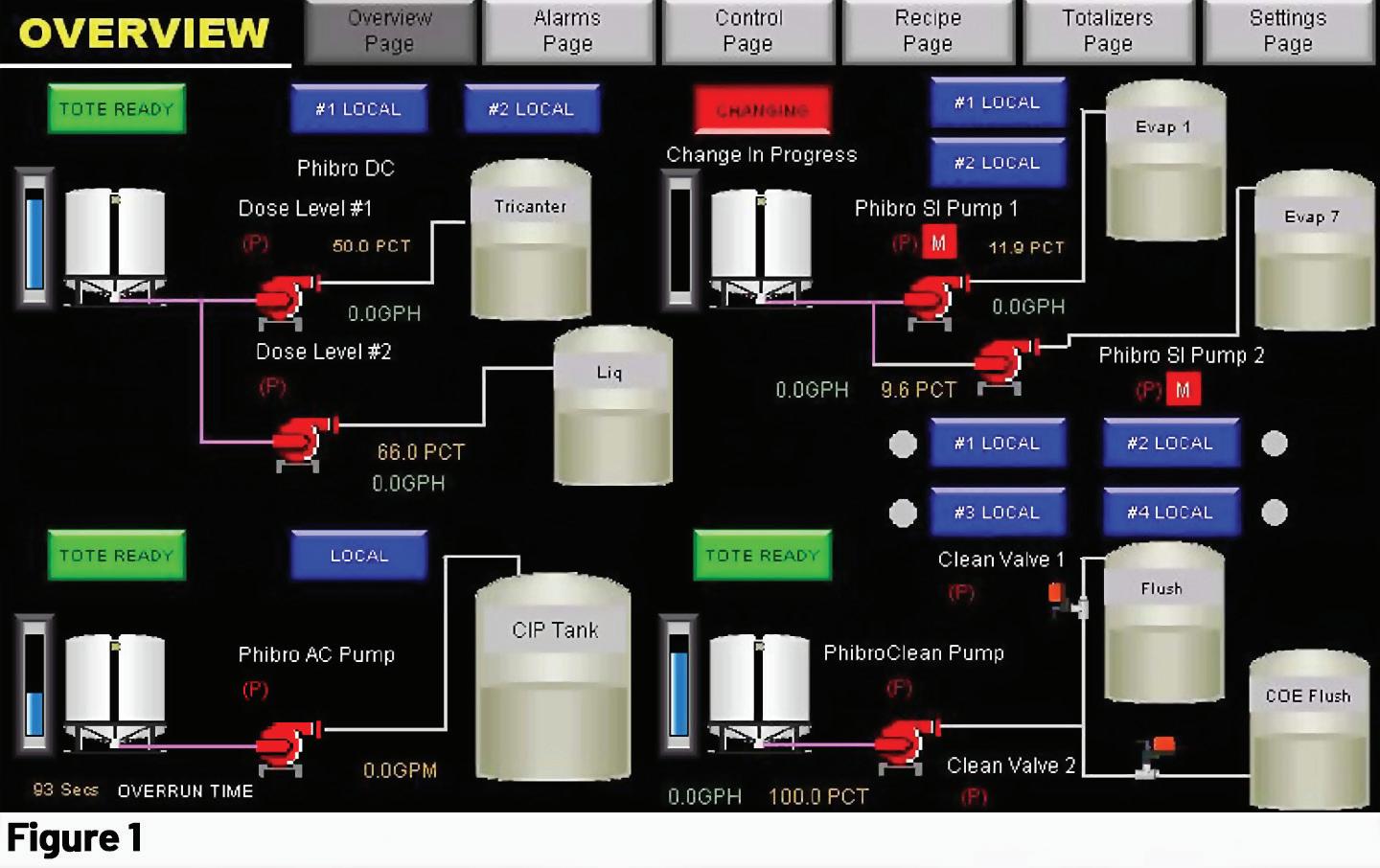

Equipment and Automation
Upgraded CIP dosing and control systems also have provided plant management with better tools to optimize their CIP programs. The use of more accurate dosing skids controlled with automated PLC systems capable of capturing program application details improves control and consistency.
Accurate tracking of CIP dosing inputs equips management teams with the ability to track CIP costs in real time and optimize programs based on application cost and performance. This more modern approach to applying CIP chemistries has created more scope for plants to improve CIP efficiency and optimize its impact on plant performance. (See Figure 1.)
Performance-Driven CIP

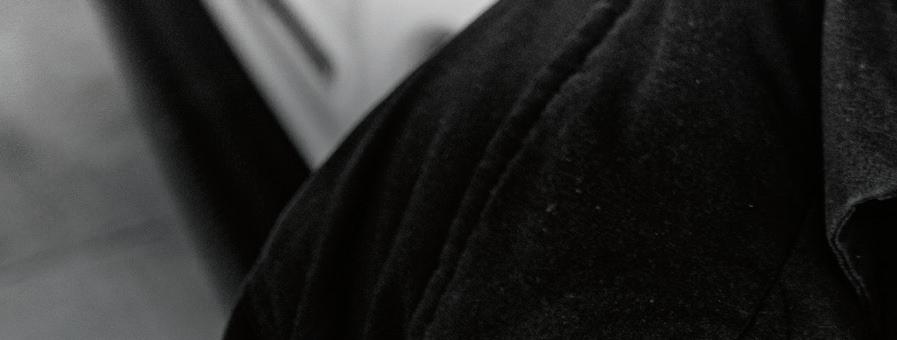

An effective CIP program will enhance fermentation performance, improve energy efficiency and help optimize plant yields, including ethanol, corn oil and protein. Plant management strategies increasingly rely on data tracking to measure the impact CIP programs have on plant performance.
The ability to track key performance indicators for specific plant operational units through data collection and analysis provides management with the tools needed to adopt a results-driven approach to optimizing CIP programs. This allows optimization of CIP chemistry, frequency and duration for each section of the plant.
As an example, data collected as shown in Figure 2, provides plant management with information regarding the rate of pressure buildup and heat transfer efficiency in their evaporator system. The data show a clear operational performance improvement as evidenced by a decrease in the rate of pressure buildup while using Phibro’s TCP system compared to previous performance while using an alternate evaporator cleaning system.
Data analysis can also be applied to determine the frequency and duration of cleaning events and equip plant management to make informed decisions on which areas of a plant require the most attention. Detailed analysis of plant operational parameters, such as delta lactic and acetic levels, heat exchanger and evaporator pressures, and corn oil and protein separation efficiency, can lead to optimized CIP and, therefore, optimized overall performance.
With continued focus on controlling costs and optimizing plant performance, the impact of CIP initiatives will continue to be a key feature of a successful plant management program. Optimizing CIP cost and performance will have a significant impact on the continued success and profitability of ethanol plant operations as the industry adopts more advanced technologies and CIP strategies.
Author: David Fowlie Product Manager, Processing Aids Phibro Ethanol Performance Group 704.430.9604 david.fowlie@pahc.com
TRUST, EXPERIENCE & DEDICATION
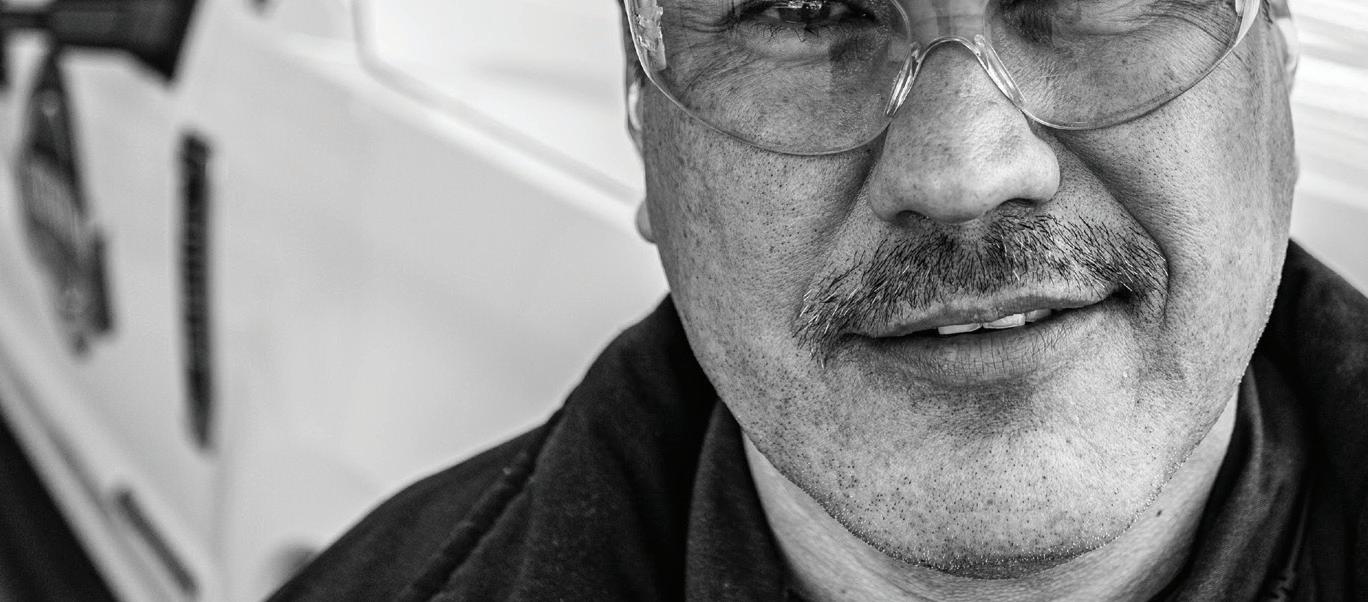
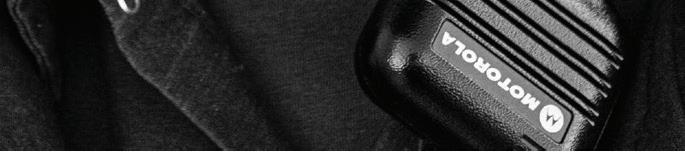
at’s why you chose PREMIUM.


.
(888) 54 9-18 69
HIBBING, MN | TRACY, MN | DUBUQUE, IA | STEVENS POINT, WI