
5 minute read
Victory Energy Operations, LLC
Aemetis closes on $35.5 million of EB-5 funding
Aemetis Inc. has closed on its $35.5 million Phase I EB-5 Program funded by 71 foreign investors. The EB-5 Program is authorized by the U.S. Immigration and Naturalization Act and designed to provide employment-based visa preferences for immigrant investors who deploy capital into U.S.-based projects that provide jobs for American workers.
Highwater Ethanol LLC, a 59 MMgy ethanol plant in Lamberton, Minnesota, has filed an 8-K with the U.S. Securities and Exchange Commission announcing an agreement with Nelson Baker Biotech Inc. for the installation of a system to produce 20 MMgy of hydrous USP-grade ethanol, which is used in the sanitizer market.
Aemetis closed its Phase I EB-5 Program with the issuance of 71 subordinated convertible promissory notes, raising $35.5 million of low-interest investment funds used to create both direct and indirect jobs at its high-grade alcohol and fuel ethanol plant in Keyes, California.
Aemetis Chairman and CEO Eric McAfee said the project exemplifies
The filing indicates Highwater and Nelson Baker executed the construction agreement on Aug. 26. The agreement includes design, engineering and construction management. Construction is expected to begin before November and reach
sound immigration policy that generates U.S. investment and creates jobs. He said the company has already launched a second phase of EB-5 funding with plans to issue
Highwater Ethanol invests in USP-grade alcohol production
$50 million in additional notes. completion in the second fiscal quarter of 2021.
Highwater Ethanol is among many U.S. ethanol plants venturing into high-end alcohol production, according to Ethanol Producer Magazine’s recent survey of U.S. producers (see page 16).

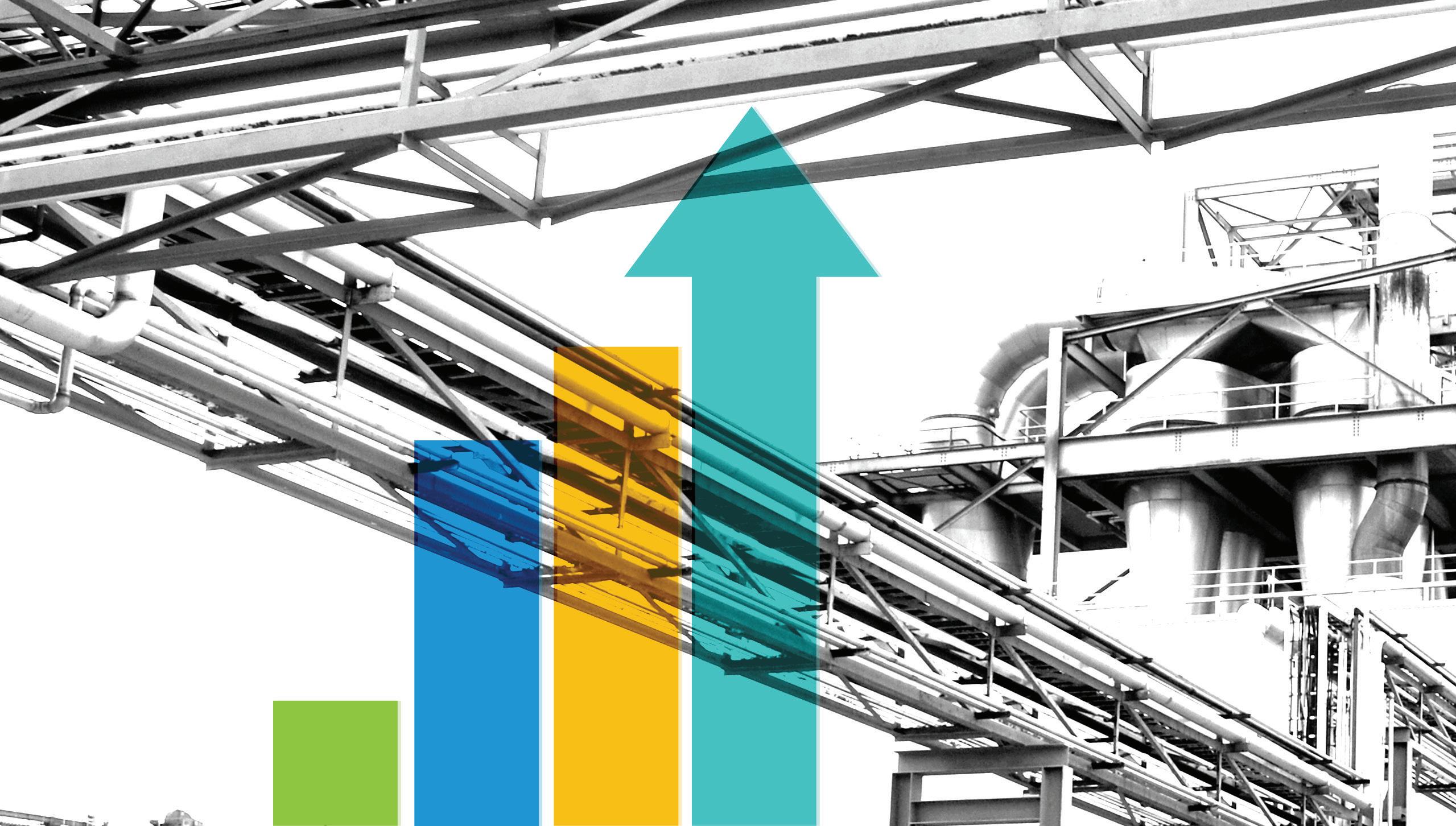
Since the COVID-19 pandemic slammed the ethanol industry in March of this year, almost 30% of producers recently surveyed by Ethanol Producer Magazine have drastically changed daily operations. Twenty-five percent said the economic downturn seriously affected operations and business. Still, almost 84% of respondents laid off only 1% to 5% of their staff.
EPM emailed a 23-question survey about the impacts of COVID-19 to CEOs and general managers of U.S. ethanol plants. Fortyfour completed the survey, providing a snapshot of experiences across the industry.
Production
Production slowdowns started as early as February for some, and as late as May for others. One producer didn’t slow production, but increased it, while another also maintained but “emptied the tanks” during the downturn.
Less than 10% of respondents lowered production by more than half of their pre-pandemic production volume; the majority—more than a third—lowered by 31% to 50%. Interestingly, 0 to 10% was the next most common reduction, at 28%. Results showed 12% lowered production by 11% to 20%; 16% lowered production by 21% to 30%; and 9% reported reductions of more than 50%.
U.S. Energy Information Administration data reports a sharp decrease in production of more than 35% from March to April (1.04 million barrels per day to 672,000).
As of the end of August, almost 32% of survey respondents said production had increased more than 50% since the low point. Twenty percent said production had only increased 0 to 10%; 16% reported an 11% to 20% increase; about 14% reported an increase between 21% and 30%; and 18% said production had increased 31% to 50%.
Daily Operations
While one-fourth of respondents said their operations were seriously affected by the COVID-19 slowdown, just 7% said they were severely affected—the only worse category. The others reported less negative effects. About one in five respondents said operations were somewhat seriously affected; a third of them said operations were moderately affected; and 16% reported no effect at all.
Thirty percent said drastic changes have been required in areas such as safety protocols, schedules and meetings. About 43% reported
Ethanol's Recovery Readout

A survey of ethanol plant CEOs and general managers shows the COVID-19 downturn had a substantial, but not lasting, impact on their operations. By Lisa Gibson
numerous changes were required; one-fourth reported few changes; and just 2% said the pandemic required no changes to operations.
More than 54% of respondents said they have produced hand sanitizer or other high-end commercial alcohols during the pandemic. Thirty-two percent said they have not; and 12% said they are considering it. More than 57% of those producing sanitizer or high-end alcohol said they will continue to produce it after the FDA guidance for ethanol in hand sanitizer expires. The remainder said they will not.
Expenses are being reduced in a several ways beyond decreasing production, including reducing hours, paying more attention to feedstock prices, minimizing travel and other expenses, shortening planned shutdowns, overtime reduction, reducing maintenance, freezing capital projects, lowering chemical usage, and negotiating price breaks with vendors. Some respondents also said they are reducing staff.
Those reported reductions have amounted to considerable savings, sometimes up to or more than $100,000 per month, as reported by three respondents. One producer said they’re saving about $34,000 per month, another $10,000 per month, and one facility reported that 90% of its expenses had been eliminated, presumably due to being idle. Many declined to give a dollar amount or percentage. Staff and Pay
About 84% of CEOs and general managers who took the survey said they only had to layoff or furlough 1% to 5% of employees. Approximately 10% of respondents said they laid off or furloughed more than 25% of their staff. About 3% reported 6% to 10%, mirroring the 11% to 15% range. No respondents said they laid off or furloughed 16% to 25% of their staff.
Morale has been affected, too. More than one-fifth of respondents said employee morale has been affected somewhat seriously; 47% reported moderate effects; 30% said morale has not been affected at all. Thankfully, no respondents reported severe blows to morale during the pandemic.
About 88% of respondents said no employees have voluntarily resigned over dissatisfaction during the pandemic, while about 12% said they have had voluntary resignations as a result of dissatisfaction. The resignations included operators, supervisors, receptionists and accountants. All respondents reporting voluntary resignations said they will replace those employees, though some must wait until the plants resume production. About 76% of respondents said they have not frozen hiring, while 24% said they have.
Similarly, about 62% said they have not suspended pay raises or