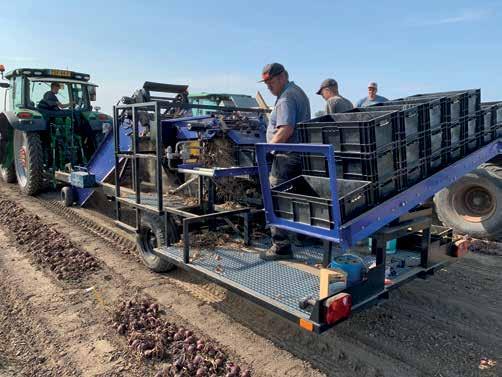
4 minute read
saving labour through innovation: i-team develops new machines for trial fields
Employees in De Groot en Slot’s Operations department were able to harvest the onions on the trial fields faster this year thanks to an improved lifter and a new loader. Production specialist John Brunen is enthusiastic about the machines. “They’re great examples of the ongoing development of innovations in breeding and production, with the goal of saving labour,” he says.
Brunen is one of the five members of the I-Team – De Groot en Slot’s Innovation Team. It consists of employees from the Breeding, Sales, Operations and Production departments. “If somebody comes up with a good idea for making improvements within the company that have to do with technology, the I-Team gets to work,” he says. “Every year, harvesting the test fields is a labour-intensive job that requires many hands. Casual workers are getting harder and harder to find, so we have to look at innovation for labour solutions where we can. These two machines are great examples of that.”
Every year, De Groot en Slot plants trial fields on farms all over the Netherlands. There, the Breeding department tests existing varieties and new hybrids. These are sown on plots around 5m in size, harvested, and judged. “In the busy harvest period we need a lot of people in a short space of time – 15 to 20 for the average test field,” Brunen says. “We noticed in the last couple of years it was getting harder and harder to find workers. And lifting and harvesting these plots is precise work. The onions need to be harvested separately in different crates. There absolutely can't be any mixing.”
Nonstop lifting Over the last year, the I-Team invested a lot of time and energy in obtaining an improved onion lifter and a new loader. The old lifter was difficult to clean, Brunen says. “Somebody always had to walk alongside to get the last onions off the belt. So you had to stop before you could start on a new field. We decided that needed to change.” With Edwin van Galen, an engineer with the Weevers agricultural machinery firm, the I-Team converted the existing lifter to work the trial fields nonstop, with no mixing. “Edwin had already built a similar machine for potatoes,” Brunen says. “We took that idea forward, and in the end our onion lifter was converted.”
The improved machine has a greatly expanded capacity. It removes the onions from the soil and places them on the ground. Special flaps on top of the machine distribute the onions over the whole machine. Additional sieving capacity has also been built in, as it had proved inadequate before. “We’re saving a ton of
research

labour and time with the improved machine,” Brunen says. “So we can harvest more test fields in a shorter time under favourable conditions, and the windrows are neater too.”
A new way of harvesting Developing the new onion loader was less straightforward. The members of the I-Team visited several mechanization firms and soon concluded that the machine they wanted didn’t exist. Finally they contacted Wouter Schoot Uiterkamp at SU-Tech, in the Dutch town of Lelystad, who had developed a similar machine for potatoes. “We saw videos of it on YouTube,” Brunen says. “We went to him with our requirements and ideas, and he gave us some constructive suggestions. Our basic requirements for the onion loader were that it needed to be labour-friendly and labour-saving and it had to work flawlessly. In the first test we could see that that had been achieved. After a few more modifications we had a highly efficient machine. It was developed within a year. It’s miraculous how fast it went.”
Harvesting the trial fields smoothly used to take 15 to 20 people; now it only takes seven. And De Groot en Slot’s employees, who supervise and assist in the process, have a better overview too. “If you have 20 people on a field, you can never be completely sure all the onions are going in the right crates,” Brunen says. “Now we have that overview, and we know for sure that everything’s being done correctly.” A major benefit is that the workers no longer have to do the heavy physical labour of gathering onions on their hands and knees, putting them in crates, and lifting the crates onto pallets. “Now the full crates only need to be pushed onto the pallets,” Brunen says. “The machine is fully approved for health and safety.”
Enthusiastic growers The onion loader proved itself on the test fields last season. De Groot en Slot originally intended to use the machine to harvest two or three of its Dutch test fields but ultimately used it on all of them, Brunen says with obvious satisfaction. “The machine performed beyond our expectations. Of course there are a few small areas for improvement. We conducted an evaluation with everyone involved. The I-Team and Wouter will use that to move forward.” The participating growers were enthusiastic about the new way of harvesting, Brunen says. “Now they can manage with their own employees. Farming a test field can be difficult, and it creates extra work. You’ve got to enjoy it to do it alongside your other activities. With these technical innovations, we're motivating growers to continue to work with De Groot en Slot.”