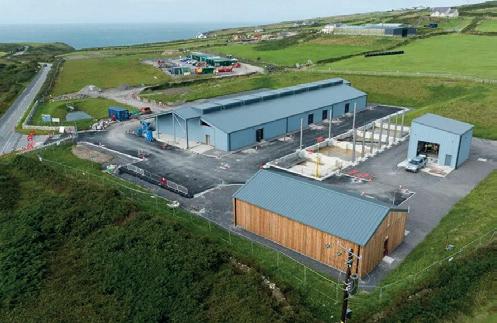
6 minute read
Official opening of Wales’s first Tidal Stream Energy Site
The First Minister of Wales, Mark Drakeford, officially opened the substation linked to Morlais tidal energy on Anglesey this week. The event, which is the culmination of more than ten years of work, marks not only a significant milestone for the project itself but for the tidal energy sector in Wales.
As part of this week’s Ireland Wales Forum, the First Minister will host the Irish Tánaiste, Micheál Martin TD (Deputy Prime Minister) and showcase the Morlais project as a key tidal stream development in Wales.
Morlais, off the west coast of Holy Island, is the largest consented tidal energy scheme in the UK. It is managed by Anglesey-based social enterprise, Menter Môn, who secured the Crown Estate lease for the 35KM2 zone of seabed in 2014. Since then, and having secured consent in 2021, work has been ongoing to put onshore infrastructure in place. The first tidal energy devices are expected to be deployed at sea in 2026.
The First Minister said: “Morlais is a groundbreaking project and a key part of our transition to a low carbon economy. It is an example of the type of development that will help Wales reach our net zero targets and underlines the importance of investing in clean energy infrastructure for our future generations.”
The County Council has been supportive of the Morlais project from its inception. The project, once operational, will ensure that the island leads the way in terms of tidal energy contributing to national net zero targets.”
Once operational the site has the potential to generate up to 240MW of low-carbon electricity. It is seen as a unique model within the sector – rather than producing electricity itself, Morlais will provide developers of tidal energy devices with the consent and infrastructure they need to supply electricity to the grid. Five developers have already agreed connection within the scheme and discussions with an additional five are at an advanced stage.
Gerallt Llewelyn Jones is a director with Morlais and has been at the heart of the project since its inception. He explains: “This is a huge day for us. We have faced many challenges along the way, but thanks to the determination of the team and support from partners and funders we can now look forward to the next phase in the scheme’s development.
“As a Menter Môn project, Morlais is rooted in our local community and the broader economic landscape. From day one we’ve been committed to advancing a more sustainable and renewable energy future and today’s achievement reflects our team’s dedication. I’m excited to see our efforts come to fruition as we get closer to generating electricity off the coast of Anglesey.”
Councillor Llinos Medi is Leader of the Isle of Anglesey County Council, Portfolio Holder
Economic Development and Lead Member for the Low Carbon Energy Programme on the North Wales Ambition Board.
Speaking at the event she said: “The County Council has been supportive of the Morlais project from its inception. The project, once operational, will ensure that the island leads the way in terms of tidal energy contributing to national net zero targets. It will also continue to provide significant local and regional economic benefits by creating jobs, enhancing skills and supply chain opportunities. It is also important to recognise that the Morlais project will be re-investing profits into those local communities that are accommodating the development.”
In line with the Menter Môn commitment to secure benefit to the north Wales economy, Ruthin-based Jones Bros Civil Engineering has been responsible for the construction of the substation officially opened by the First Minister. Working with other local companies, they also undertook the cabling work, connecting the scheme to the national grid. The project is funded by the European Regional Development fund through the Welsh Government. The Isle of Anglesey County Council, The Nuclear Decommissioning Authority and North Wales Growth Deal have also supported the project.
WCNW: To begin, tell us a little about yourself and your background.
I began in the paper industry as a trainee and junior commercial person in 1964 and that activity was as paper mill agent and a paper trader. I was appointed Director and shareholder in the trading business in 1974 being responsible for the importing and sourcing of paper from a variety of overseas mills. In 2009, we became a UK manufacturing business with the acquisition of Kruger’s UK operations in Disley and in Wales. From that initial acquisition, the business really started to become an established player in the UK paper hygiene market. We have since grown organically and through further acquisitions to become the largest British private & familyowned paper hygiene companies in the UK. Northwood is now a group of associated companies that provide the manufacturing, supply and transportation of disposable tissue products. Run by four shareholders, we are building and investing in the latest technology which is at the forefront of NPD in the paper industry. We are nimble in our approach to investment and decision-making, with no constraints by the city or institutional shareholders – we make our own decisions.
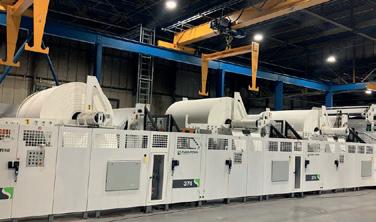
WCNW: What attracted you to the company?
From the early days in a junior commercial role, I have had a passion for paper and tissue product so it was a natural progression to build on this.
WCNW: What are your main responsibilities?
I am Chairman and founder of the Northwood Group and oversee the strategic direction of the business. I do this with a first-class senior management team which is complemented by my two sons Marc and Adam who are fully immersed in the Group activity and development.
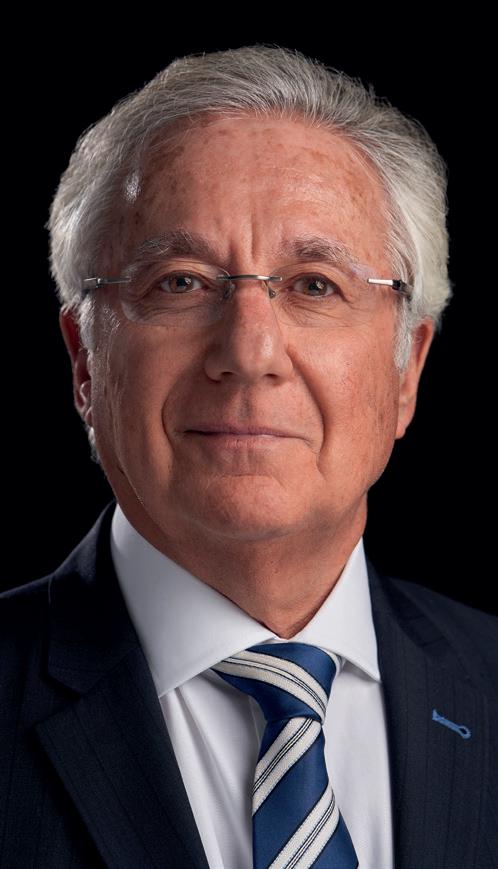
WCNW: What does a typical day involve?
I’m actively involved in the business on a daily basis. In regular contact with the senior management team, I like to think I can offer advice and assist with problem-fixing!
WCNW: Who are your target audience and what is the main aim of the organisation?
The Northwood business has many facets, including paper procurement, wastepaper recycling, Recycled Hygienic paper parent reel production, we have in the UK three paper mills Disley, Chesterfield and Lancaster we also operate a paper mill in Spain as well as our converting (paper processing) facility in Madrid. The UK converting businesses operate in both the away from home (AfH) and retail consumer sectors. Our AfH route to market is business to business. We deal with several national accounts and independent distributors that service customer in all areas of the market including, education, food service, office supplies, hospitality and the FM sector.
Our retail division services virtually all the national High Street grocery stores with Toilet Roll, Kitchen Towel and Tissues. We also serve a number of customers from independent cash and carry outlets to the discount stores which are growing in importance year on year.
WCNW: What projects are you currently working on?
As part of our strategy to grow our retail division, we have recently invested in a new manufacturing and warehousing site at Ellesmere Port. The site has undergone a significant investment with new machinery and is now fully operational. This site will become our facility of excellence in the production of consumer roll tissue products. We are in the trajectory to invest in excess of £18millon in this plant over the next three years.
WCNW: How have things gone so far?
In respect to the Ellesmere Port project, we have had some issues to overcome, but these have been managed efficiently by the management team. We have introduced state of the art processing machines which needs specialist skills to operate and we are fortunate that the catchment area in Ellesmere Port is able to provide the skillsets needed and new staff have adapted to the technology, and with tuition they are becoming experts in the production of Toilet Rolls Kitchen Towel to follow.
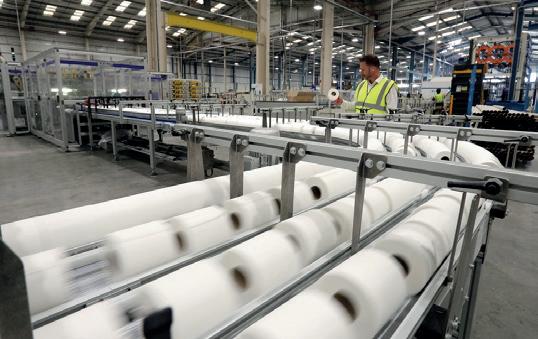
WCNW: Any difficulties? If so, how did you overcome them?
Like many other companies, our business has faced difficult challenges in recent years, Brexit, Covid, Ukraine and hyperinflation. We are an energy intensive business, with paper mills that work 24/7 365 days a year, and so we were affected by the rise in energy costs and have worked hard to minimise this impact on our customers. Investments have gone in to minimise the use of fossil fuels and to work towards greener production.
WCNW: Looking ahead, what are your main aims for the organisation and how would you like it to develop?
We are now one of only a small handful of companies in the UK market that is fully vertically integrated and sells as well as converts parent reels. We also have mill facilities to guarantee supply.
Our aim is to be the preferred supply chain partner for key organisations and retailers, involved in the disposable paper and tissue industries.
WCNW: How have businesses and individuals responded to what you’re offering?
I believe our customers have reacted very well to our strategy in recent years. We have a very loyal customer base, some of which have been with us for almost 30 years! We pride ourselves on making prompt decisions and responding quickly to customer needs. Our AfH business excels in driving our own value-added brands, some of which, such as our Whisper brand, have become very recognisable in the away from home market. Our retail division excels in delivering own label propositions for many high street grocery chains and we have established many excellent commercial partnerships over many years. As we continue to grow, we will never lose sight of the importance of relationships with our customer base.
WCNW: What are your career aims and aspirations? Is there anything else in particular you’d like to achieve in your lifetime?
We intend to make one significant, major investment and have already been granted planning permission to install a 100% virgin paper machine with 70,000 tonnes capacity. The group will then become selfsufficient in all parent reel requirements, fully supporting the converting expansion plan.
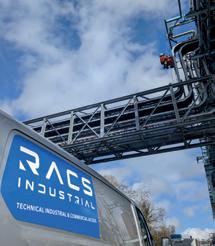
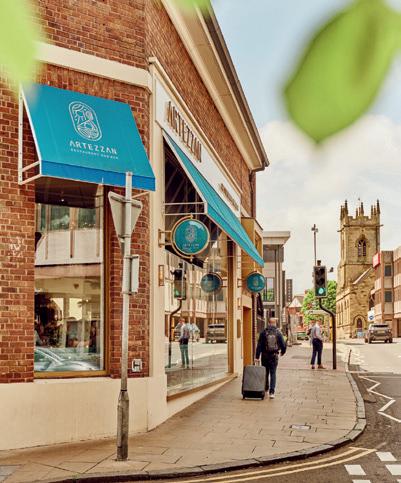
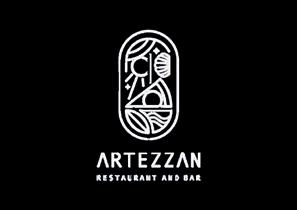