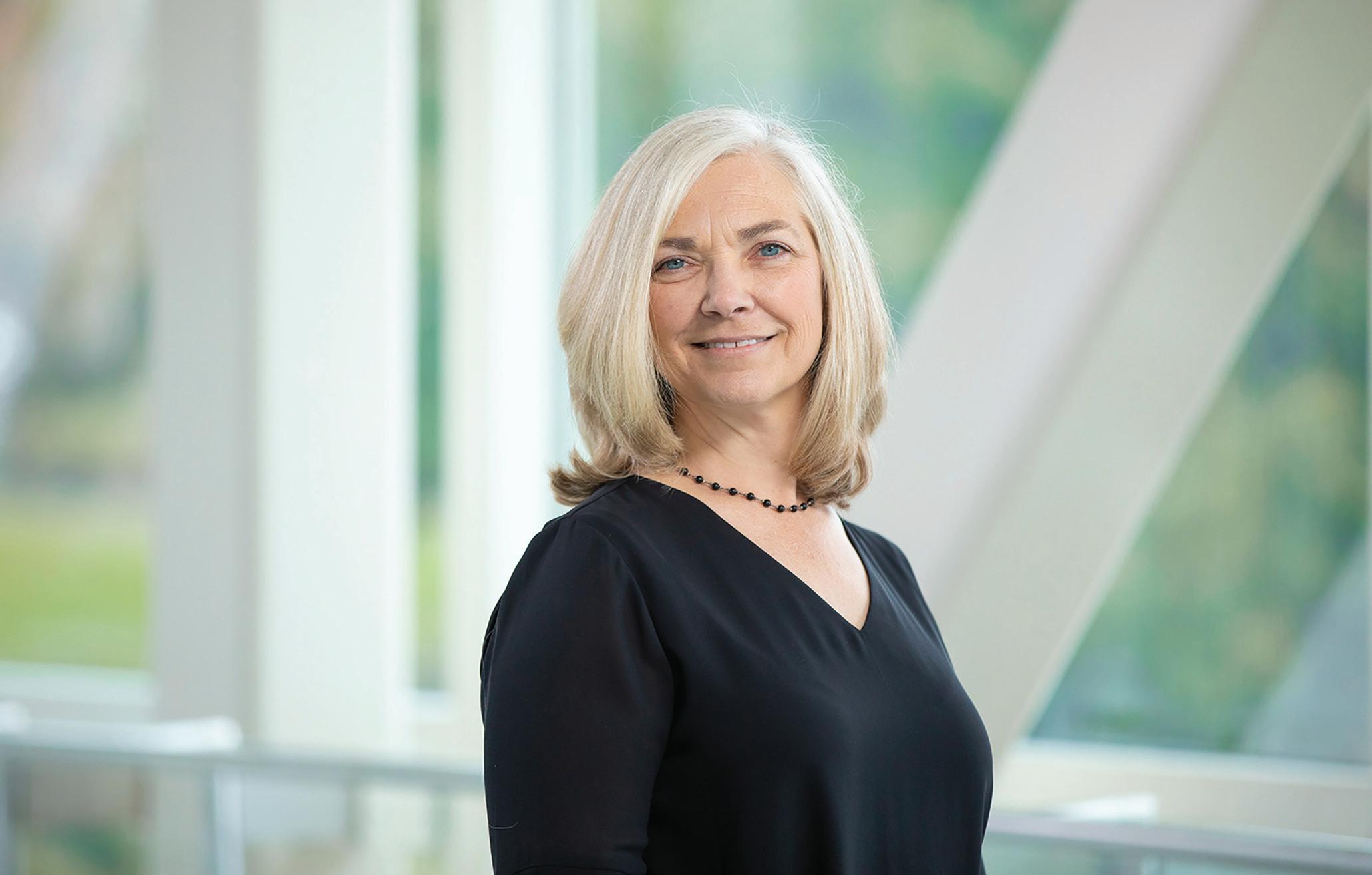
4 minute read
Before dirt is turned over
Brenda Landes
Photos courtesy of SFCS
Advertisement
Before Dirt is Turned Over By Brian Bongard
Before construction begins, there’s the architectural and design process; Roanoke’s SFCS describes.
How do big sophisticated projects like the new cutting-edge Science, Technology, Engineering and Math, (STEM) building at Virginia Western Community College, or the new Bioscience center at Blue Ridge Community College (BRCC) go from vision to reality? It brings to mind the old question, “How do you eat an elephant?” The answer being, “One bite at a time.” In the case of the 72,000 sq. ft, $37 million STEM building in Roanoke, it started with the vision of Dr Robert Sandel, long time President of VWCC. In a Campus News announcement, he said “We expect it to be a destination for students and industry partners who are interested in getting ahead in the region’s growing STEM-focused economy”.
But the more specific answer is that it takes a multitude of talented, hard-working people, from the presidents of the schools to the carpenters and bricklayers. Guided by a well-defined process, they work together to bring the vision to life. The process is important. The people create the magic. The 40,000 sq. ft, $16 million Bioscience building at BRCC was to be geared specifically toward educating skilled workers for the area’s health care systems.
Then the Virginia Community College System gets involved. They are the government hub
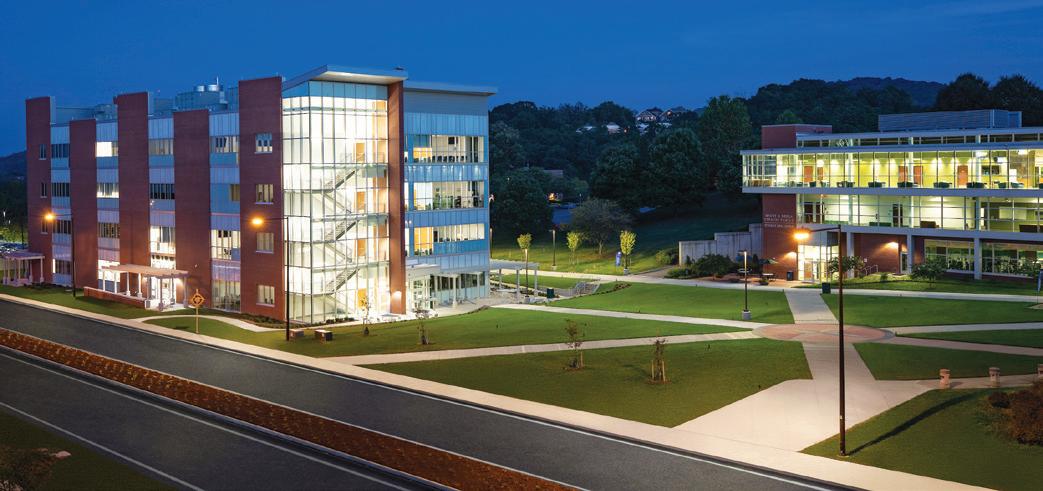

for these projects. For over 50 years they have been facilitating the process of moving projects from the vision, to the specifics. Wish lists get sorted through, priorities are set, compromises made, and then it boils down to what is feasible. Space requirements are translated to square feet, an equipment list is created, a budget is agreed upon, and an RFP (Request for proposal) is posted.
Brenda Landes is a team leader at SFCS Architects in Roanoke, which eventually landed the design contracts for both of these buildings. She offered some insights as to how the process goes. “SFCS tracks the RFP’s [request for proposal), but we also make an effort to build relationships with the community college people. We generally have some information about what projects are on the horizon before the RFP is publicly posted”.
From there, the selection process is defined with submitting firms given about 2-5 weeks to put together an initial 15-minute presentation. Landes notes that, “those few weeks involve a lot of late nights and overtime [with her team] to ask questions, develop answers, and put the presentation together.” Specialists are sometimes brought in to consult on a project. In these cases, it was HERA Laboratory planners on the VWCC STEM building, and Page SST Laboratory Planners on the BRCC Bioscience project.
A presentation is made to the selection committee, which develops a short list of three to five firms that are asked to return with a more detailed proposal. The committee then makes a final decision, usually within a couple weeks, and awards the contract.
A “Construction Manager at Risk,” is engaged at this point. Kjellstrom and Lee was the construction firm and Ryan Amos the point man for them on the Bioscience building. He said “our job is to consult in the design process on complex projects, in order to identify

SFCS t urns 100 Years Old

SFCS opened in Roanoke one-hundred years ago (1920) and now has offices in Charlotte, Philadelphia, and Louisville. In mid-February, the company (still headquartered in Roanoke) held its 35th annual “By Design” conference—a national event for CEOs, executive directors, administrators, board members, planners, marketers, building committee members, trustees of retirement communities and sponsors of senior housing. SFCS is an industry leader in the design of senior living spaces and communities.
gray areas and help save the client money. We are ‘At Risk’ because we sign a contract that ensures the building will be done on time at a guaranteed maximum price.” Adds Amos, “we could not have completed the project as quickly or as efficiently without collaborating with SFCS in the process. They were very attentive to getting any issues worked through and resolutions approved in order to keep the process moving forward”.
One more person brought in during construction is a 3rd party inspector. Hired by the client, they verify that all the details spelled out in the plans are up to spec as the project is built. For example, they would take concrete samples to test as the foundation is poured and ensure that windows and doors meet the requirements spelled out by SFCS.
There is usually a sprint to get to the finish line on time, which involves lots of inspections and punch lists of details to be handled. Ultimately, there is a Certificate of Occupancy issued. Ribbon cuttings, press releases, congratulations on jobs well done, and the buildings are ready to start enriching the minds of students - and contributing to the local economy. The vision has become a reality.