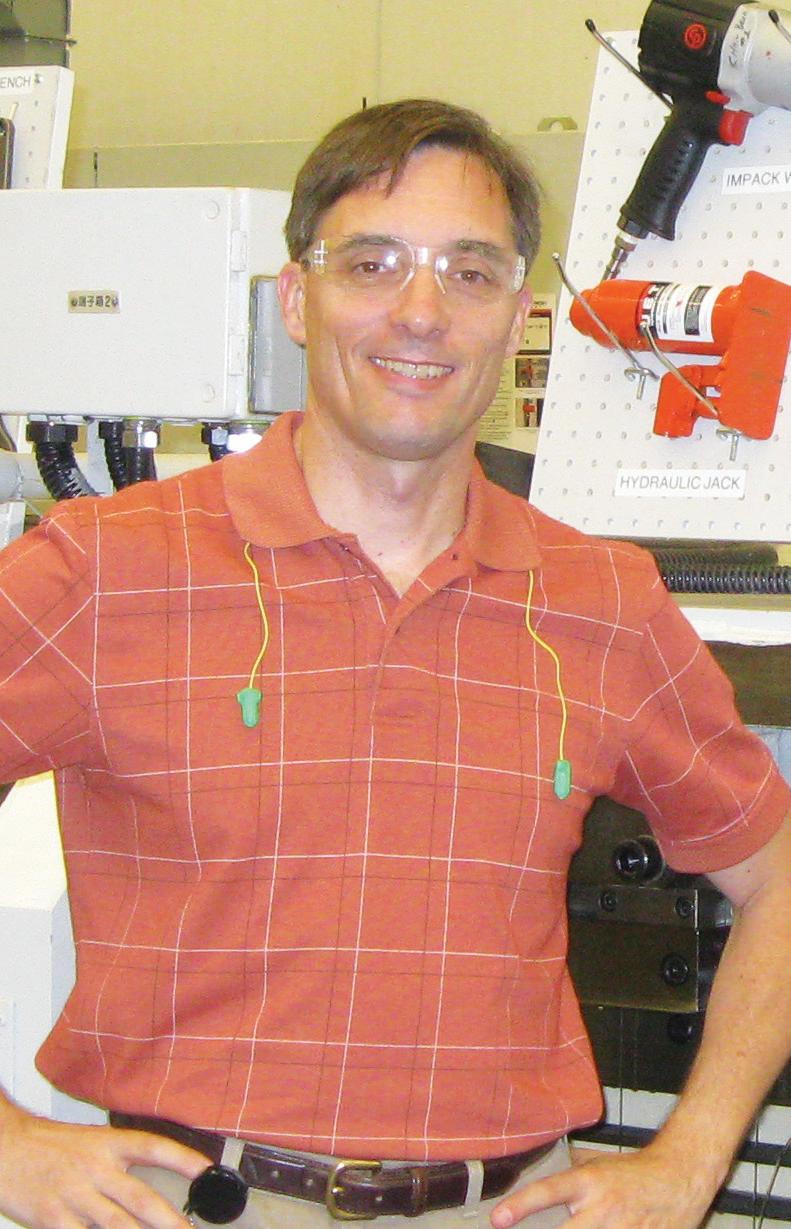
2 minute read
Business Operations
By Mike Leigh
Executive Summary:
Advertisement
During the pandemic this past year, you’ve probably noticed longer than normal delays and out-of-stock items when buying goods. A year ago, my wife and I ordered a couple mountain bikes. We’re still waiting for one of them.
Send your questions or comments to Mike@ OpXSolutionsllc.com
Inventory Management and JIT
Manufacturers are in a supply chain crisis. Demand is high for products, but the pandemic has severely disrupted the flow of parts and raw materials. The most highly visible impact has been a shortage of circuit cards used in automobiles and other modern devices. Without a reliable and resilient supply chain, organizations cannot promptly deliver their goods and services.
To compensate for supply chain disruptions, many organizations choose to keep extra inventory as a buffer. But excess inventory ties up free cash flow, takes up space capacity, and reduces productivity due to extra material handling and management.
After WWII, Toyota recognized the high cost of excess inventory and developed the concept of Just-In-Time (JIT). Simply stated, the JIT philosophy aims to eliminate excess inventory to improve efficiency, reduce costs, and provide product more quickly to the customer. I’ve heard and read many opinions this past year that blame the JIT concept for these supply chain disruptions. But these opinions fail to fully understand JIT.
JIT does not promote eliminating inventory. It promotes eliminating excess inventory. Excess inventory is inventory above what a company needs to ensure no disruptions in production. Toyota, and other organizations that fully understand this concept, do not reduce their inventory unless they have first developed reliable suppliers and have accounted for supply chain risk. For this reason, Toyota partners closely with their suppliers and, where possible, uses suppliers located close to their factories, thus reducing the risk of overseas shipments from other countries.
After the earthquake and tsunami in Japan several years ago, Toyota recognized the fragility of the circuit card supply chain. After the earthquake, they took actions to reduce their risk of this important component and increased their inventory of these parts. This does not go against the JIT philosophy. While US auto manufacturers have taken a big hit in sales due to the chip shortage, Toyota increased their US sales in Q3 and has surpassed GM so far in 2021.
After decades of chasing low-cost parts in low-cost countries overseas, the pandemic has put a spotlight on the risks of this supply chain strategy. I’m hopeful this will lead to developing a stronger domestic supply base and a resurgence in manufacturing in the US.